Выбор состава стержневой смеси, способа и оборудования для изготовления стержней
Стержни в процессе заливки испытывают большие термические и механические воздействия по сравнению с формой, поэтому к стержневым смесям предъявляются более жесткие требования. Прочность стержня в сухом состоянии и поверхностная твердость должны быть выше, чем у формы. Стержневые смеси должны иметь большую огнеупорность, податливость, небольшую гигроскопичность при формовке по-сырому.
Применим для изготовления стержней для отливки «Корпус» СоId-Box-Amin-процесс с уплотнением на пескострельном автомате.
СоId-Box-Amin-процесс разработан в США фирмой Ashland. Стержневая смесь содержит, мас. ч.: 100 кварцевого песка и 0,6…0,8 фенольной смолы с 0,6…0,8 полиизоцианата (связующая композиция). После уплотнения смеси в ящике пескодувным или пескострельным способом стержень продувается смесью паров низкокипящей жидкости – третичного амина (триэтиламина, диметилэтиламина) с воздухом, и стержень приобретает начальную прочность, которая составляет 60 % конечного ее значения. Время продувки 2…5 с, далее 10…20 с стержень продувают воздухом для его очистки от паров амина. Расход катализатора ≤ 1,5 г на 1 кг стержневой смеси. В результате взаимодействия компонентов связующего в присутствии катализатора (амина) образуется твердый полимер – полиуретан, который и обеспечивает высокую прочность стержня. Для подготовки, дозирования и подачи амина применяют специальные газогене-раторы, которые испаряют амин, смешивают его с воздухом и подают в стержневой ящик.
|
|
Смесь амина с воздухом после прохода через стержневой ящик направляется в нейтрализатор, где полностью нейтрализуется разбавленной серной кислотой с образованием водорастворимой соли – сульфата аммония. Степень очистки воздуха в этой системе близка к 100 %. Таким образом, весь тракт подачи амина полностью герметизирован, что обеспечивает безопасность процесса. После изготовления и зачистки стержни также окрашиваются противопригарной краской.
Приготовление смеси осуществляется в вихревом смесителе, а изготовление стержней происходит пескострельным способом. Схема пескострельной головки представлена на рисунке 2.
Рисунок 2 – Схема пескострельной головки стержневого ящика
Выбор типа литниковой системы
Литниковая система должна обеспечить спокойную, равномерную и непрерывную подачу металла в заранее определенные места отливки. Конструкция ЛС должна создавать условия, препятствующие засасыванию воздуха потоком металла. ЛС должна задерживать все неметаллические включения, попавшие в поток металла. Одной из важнейших функций ЛС является заполнение формы с заданной скоростью: при очень большой скорости заливки происходит размыв стенок формы и каналов самой ЛС, а при слишком медленной заливке – значительное охлаждение металла и образование спаев, неслитин, недоливов [5]. ЛС должна способствовать выполнению принципа равномерного или направленного затвердевания отливки. Она служит для частичного питания жидким металлом отливки в начальный момент ее затвердевания.
|
|
При литье сталей шлаки и плены удерживаются в разливочном ковше, поэтому для заполнения отливки «Корпус» расплавом применим простую литниковую систему. Литниковый ход будет располагаться в верхней опоке, питатели и зумпф в нижней. Подвод расплавленного металла будем производить в область фланца, что позволит создать равные условия заполнения и затвердевания обеих заготовок.
В виду того, что стальные сплавы обладают достаточно высокой усадкой (от 2% и более), то для утолщённых зон отливок применим прибыли, которые позволят скомпенсировать в процессе затвердевания заготовок объёмную усадку металла. Массивным узлами на отливках являются фланецы, поэтому на одну заготовку необходимо 2 прибыльные части.
Дата добавления: 2022-07-16; просмотров: 116; Мы поможем в написании вашей работы! |
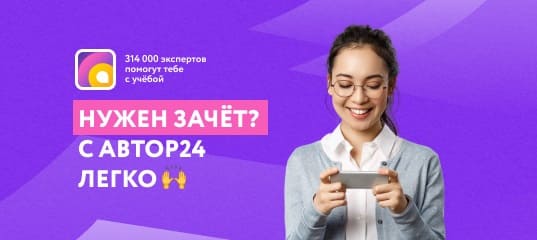
Мы поможем в написании ваших работ!