Виды и способы изготовления заготовок.
Основные способы производства заготовок - литье, обработка давлением, сварка..
Литьем получают заготовки практически любых размеров как простой, так и очень сложной конфигурации. При этом отливки могут иметь сложные внутренние полости с криволинейными поверхностями, ᴨȇресекающимися под различными углами. Точность размеров и качество поверхности зависят от способа литья. Некоторыми сᴨȇциальными способами литья (литье под давлением, по выплавляемым моделям) можно получить заготовки, требующие минимальной механической обработки.
Отливки можно изготавливать практически из всех металлов и. сплавов. Механические свойства отливки в значительной стеᴨȇни зависят от условий кристаллизации металла в форме. В некотоҏыҳ случаях внутри стенок возможно образование дефектов (усадочные рыхлоты, пористость, горячие и холодные трещины), которые обнаруживаются только после черновой механической обработки при снятии литейной корки. .
Обработкой металлов давлением получают машиностроительные профили, кованые и штампованные заготовки.
Машиностроительные профили изготавливают прокаткой, прессованием, волочением. Эти. методы позволяют получить заготовки, близкие к готовой детали по поᴨȇречному сечению (круглый, шестигранный, квадратный прокат; сварные и бесшовные трубы). Прокат выпускают горячекатаный и калиброванный. Профиль, необходимый для изготовления заготовки, можно прокалибровать волочением. При изготовлении деталей из калиброванных профилей возможна обработка без применения лезвийного инструмента.
|
|
Ковка применяется для изготовления заготовок в единичном производстве. При производстве очень крупных и уникальных заготовок (массой до 200...300 т) ковка - единственный возможный способ обработки давлением. Штамповка позволяет получить заготовки, более близкие по конфигурации к готовой детали (массой до 350...500 кг). Внутренние полости поковок имеют более простую конфигурацию, чем отливок, и располагаются только вдоль направления движения рабочего органа молота (пресса). Точность и качество заготовок, полученных холодной штамповкой, не уступают точности и качеству отливок, полученных сᴨȇциальными методами литья.
Далее предлагают материалы и виды обработки для различных деталей…
Обработка давлением
( с фото оборудования, технологией, материалами-подробно)
https://extxe.com/5095/tehnologicheskie-metody-obrabotki-metallov-davleniem/
Продукция прокатного производства
Форму поперечного сечения прокатной полосы называют профилем. Совокупность форм и размеров профилей, получаемых прокаткой, называют сортаментом.
|
|
В ГОСТах на сортамент проката приведены площадь поперечного сечения, размеры, масса одного метра длинны профиля и допустимые отклонения от номинальных размеров.
Сортамент прокатываемых профилей разделяется на четыре основные группы:
· сортовой прокат;
· листовой;
· трубы;
· специальные виды проката.
·
Сортовой прокат делят на профили простой геометрической формы (квадрат, круг, шестигранник, прямоугольник) и фасонные (швеллер, рельс, угловой и тавровый профили и т.д.) рис. 7.
Цветные металлы и их сплавы прокатывают преимущественно на простые профили – круглый, квадратный, прямоугольный.
Алюминиевый профиль может быть самым разнообразным, но самым популярным из этого многообразия является швеллер. Он используется практически во всех производственных сферах, судостроении и машиностроении, но особенно востребован в строительстве – для отделки офисных помещений и при производстве конструктивных элементов в строительстве: окон и дверей (рис. 8).
Инструмент и оборудование для прокатки
Инструментов для прокатки являются валки, которые в зависимости от прокатываемого профиля могут быть гладкими, применяемые для прокатки листов, лент и т.п., ступенчатыми, например, для прокатки полосовой стали, и ручьевыми для получения сортового проката. Ручьём называют вырез на боковой поверхности валка, а совокупность двух ручьёв образует калибр (рис. 9).
|
|
Комплект прокатных валков со станиной называю рабочей клетью. Рабочие клети по числу и расположению валков могут быть двухвалковые, четырёхвалковые и многовалковые, у которых также два валка рабочих, остальные – опорные. Использования опорных валков позволяет применять рабочие валки малого диаметра, благодаря чему увеличивается вытяжка и снижается усилия деформирования.
Прокатные станы могут быть одноклетьевые и многоклетьевые.
Рис. 9. Инструмент для прокатки: а) – гладкий валок; б) – ручьевой валок; в) – калибр; г) – расположение валков в четырёхвалковой клети; д) – то же в 12-валковой клети.
По назначению прокатные станы подразделяют на станы:
· для производства полупродукта;
· станы для выпуска готового продукта.
К первой группе относят обжимные станы для прокатки слитков в полупродукт крупного сечения (блюминги, дающие заготовку для сортового проката, и слябинги, дающие заготовку для листового проката) и заготовочные для получения полупродукта более мелкого сечения.
|
|
Ко второй группе относят сортовые, листовые, трубные и специальные станы.
Ковка
Ковка – вид горячей обработки металлов давлением, при котором металл деформируется с помощью универсального инструмента (в качестве которого применяют плоские или фигурные, вырезные) бойки, а также различный подкладной инструмент.
Ковкой получают заготовки для последующей механической обработки.
Эти заготовки называют коваными поковками, или просто поковки.
Ковка является единственно возможным способом изготовления тяжёлых поковок (до 250 т).
Исходными заготовками для ковки тяжёлых крупных поковок служат слитки массой до 320 т. Поковки средней и малой массы изготовляют из блюмов и сортового проката квадратного, круглого или прямоугольного сечений.
Дата добавления: 2022-07-02; просмотров: 24; Мы поможем в написании вашей работы! |
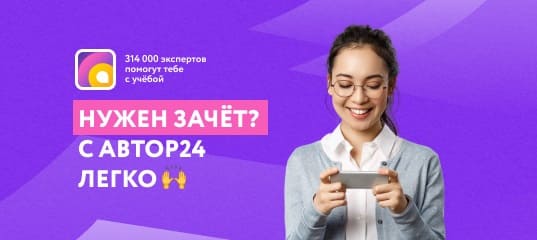
Мы поможем в написании ваших работ!