Применение в пищевой промышленности
Процесс дозирования широко распространен в отраслях пищевой промышленности: при производстве хлеба дозируются мука, вода, соль и другие добавки; при производстве овощных и закусочных консервов дозируются вкусовые добавки; пpи производстве синтетических моющих средств осуществляется дозирование различных ингредиентов, входящих в их состав.
Для получения смесей повышенного качества процесс дозирования происходит обычно непрерывно. При автоматизации процессов дозирования основное внимание уделяется регулированию соотношения расходов заданных рецептурой компонентов, при этом предъявляются повышенные требования к точности дозирования.
Дозирование может осуществляться по объему, например с помощью многокомпонентного насоса-дозатора, либо по массе с помощью весовых устройств.
Рассмотрим автоматизацию процесса дозирования по массе жидких компонентов при производстве маргариновой эмульсии.
При производстве маргариновой продукции предварительно готовится маргариновая эмульсия, в состав которой входят жировые и водно-молочные компоненты. Набор этих компонентов проводится в дозировочном отделении, куда они поступают соответственно из жирохранилища и молочного отделения. В жирохранилище каждый вид жировых компонентов находится в баках-емкостях, в которых поддерживается определенная температура, для того чтобы жиры находились в расплавленном виде и хорошо транспортировались по трубопроводам.
|
|
В молочном отделении приготавливается сквашенное молоко и пастеризуется поступающее свежее молоко, готовится раствор соли, кипяченая вода и т. п.
Дозирование - набор жировых и водно-молочных компонентов- осуществляется по определенной рецептуре по массе в баки, установленные на автоматических весах. После набора жировой и водно-молочной смеси одновременно проводится их слив в один из смесителей, откуда приготовленная маргариновая эмульсия поступает на дальнейшую обработку.
На рисунке приведена схема автоматического управления участком дозирования при производстве маргарина. Из ёмкостей / жирохранилища и VI молочного отделения (для упрощения на схеме показано по одной емкости) последовательно в баки IV и V, установленные соответственно на весахII и III, набирается по массе каждый входящий в рецептуру вид жиров и компонент водно-молочной смеси.
25.
Рисунок 9. Схема автоматического управления участком дозирования при производстве маргарина: I - ёмкость жирохранилища; II - весы жирового набора; III - весы водно-молочной смеси; IV - бак жирового набора; V - бак водно-молочной смеси; VI - ёмкость молочного отделения
|
|
Автоматизация участка выполнена с использованием комплектной системы автоматизированного дозирования жидких сред (САДЖС-2). В состав этой системы входят рычажно-механические весы // типа РС-2Ц13 с пределом взвешивания 2000 кг, с указателем циферблатным тина УЦК-400-3 ВД6 (2а, 26) с 6 задающими стрелками и сельсином-датчиком и с дистанционным циферблатным указателем типа УЦД-400-ЗВП6 (2в) ,с 6 задающими стрелками и сельсином-датчиком, а также весы /// типа РП-1Ц13 с пределом взвешивания 1000 кг и соответственно двумя указателями УЦК-400-ЗВД6 (За) и УЦД-400-ЗВП6 (36) со шкалами 0-500 кг.
В качестве запорной арматуры на линиях подачи компонентов на весы и слива с весов в смесители применены отсечные клапаны с поршневым пневмоприводом КОПП1 (56 -116; 176 - 206) и КОПП2 (126, 216). Управление клапанами осуществляется сжатым воздухом с помощью электропневматических вентилей типа ВВ-32Ш (5а - 12а, 17а - 21а).
Кроме весовых дозаторов жировых и водно-молочных компонентов, в состав системы входят два пульта управления, два шкафа, в которых расположены вентили ВВ-32Ш, и два местных щитка.
Пульты управления и дистанционные циферблатные указатели устанавливаются в помещении операторского (диспетчерского) пункта управления маргариновым цехом.
|
|
Система обеспечивает местный, дистанционный и автоматический режимы управления. В местном режиме управление производится переключателями с местных щитков, в дистанционном - переключателями с пультов управления. На пультах расположена световая сигнализация работы клапанов набора и слива компонентов, установки стрелки весов на «0» шкалы, окончания набора компонентов, готовности смесителя принять с весов набранные компоненты.
Системой предусмотрена аварийная световая и звуковая сигнализация перегрузки весов, нарушения рецептуры из-за не закрытия клапана подачи компонента, отсутствия подачи компонентов на весы и слива набранной порции с весов после поступления команды.
Система позволяет провести проверку массы отдельных компонентов, остановить дозирование с доработкой всего цикла набора. Обеспечена также защита весов от перегрузки.
Перед началом работы системы в автоматическом режиме выбирают программу для данного вида маргарина штекерами на программной плате пультов управления. Установка штекера обеспечивает соединение датчиков массы циферблатного указателя с определенными вентилями ВВ-32Ш, управляющий сигнал от которых поступает на определенные клапаны подачи компонентов.
|
|
Если набор в баки на весах окончен и один из смесителей готов принять очередную порцию, то открываются клапаны слива и компоненты поступают в смеситель.
Системой автоматизированного управления дозированием предусматривается также автоматический контроль уровня и температуры в ёмкостях жирохранилнща и молочного отделения. В качестве датчиков уровня используются гидростатические уровнемеры ПИГ-2 (1а, 13а). Сигналы от уровнемеров поступают на вторичные приборы ППВ1.3И (16, 136) с сигнальными устройствами. По достижении верхнего уровня в емкости электрический сигнал от ППВ-1.3И используется для блокировки соответствующих насосов; при нижних значениях уровня блокируется работа дозирующих устройств.
Контроль температуры продукта в ёмкостях осуществляется с помощью термопреобразователей сопротивления ТСП (4а), сигналы от которых поступают на многоточечный электронный мост КСМ-2 (46).
Вторичные приборы и сигнальные лампочки установлены на щитах жирохранилнща и молочного отделения.
В ёмкости, в которой происходит сквашивание молока, с помощью погружных датчиков ДПг и преобразователя П201 контролируется рН.
Смешивание (перемешивание) широко применяется в различных отраслях пищевой промышленности для равномерного распределения составных частей в смесях жидких, твердых и сыпучих компонентов. Так, например, в хлебопекарном производстве перемешивают различные виды теста, на маргариновых заводах смешивают различные компоненты маргариновой эмульсии, в консервном производстве - мясные и овощные фарши и т. д. Полученные однородные смеси должны обладать вполне определенными физико-химическими свойствами.
Для получения смесей используются смесители, где перемешивание происходит механическим, пневматическим, циркуляционным и поточным методами.
При автоматизации процессов смешивания наиболее простыми являются системы стабилизации расходов подаваемых в смеситель компонентов. Иногда при постоянстве расходов компонентов состав смеси будет отличаться от заданного, тогда вводятся корректирующие сигналы в систему управления по тем параметрам, которые определяют качество смеси.
Смешивание (перемешивание) применяется также для интенсификации массообменных, тепловых и химических процессов.
Автоматизация приготовления замеса.На спиртовых заводах, перерабатывающих крахмалистое сырье, большое значение отводится процессу приготовления замеса с требуемой концентрацией крахмалистых веществ.
Измельченное зерно поступает в смеситель замеса, где смешивается с водой, после чего замес направляется в отделение разваривания. Схема автоматизации приготовления замеса включает в себя систему стабилизации продуктового потока и контуры стабилизации основных режимных параметров.
Система стабилизации продуктового потока обеспечивает заданный расход муки в чан замеса с коррекцией по содержанию вводимого крахмала, подачу воды для замеса в определенном соотношении с расходом муки, стабильный расход замеса на производство с коррекцией по плотности замеса.
Расход муки, поступающей в чан замеса, измеряется расходомером типа РЦ-71 в комплекте со вторичным дифтрансформаторным прибором типа КСД-3. Сигнал, пропорциональный расходу муки, от вторичного прибора КСД-3 поступает на электропневмопреобразователь ЭПП, пневматический сигнал от которого поступает в камеру «переменная» вторичного прибора со станцией управления типа ПВ3.2 и пропорционально-интегральный регулятор ПР3.31. В камеру «программа» прибора ПВ3.2 поступает сигнал от функционального блока ПФ1.1, в котором формируется задание на расход муки по уровню массы в смесителе с ручной коррекцией по количеству вводимого крахмала. В блоке ПФ1.1 происходит алгебраическое суммирование сигналов, поступающих от пропорционального регулятора ПР2.8 и от задатчика вторичного прибора ПВ2.3. После сравнения параметра с заданием сигнал от регулятора ПР3.31 поступает на исполнительный механизм МИМ-К, сочлененный с шибером.
Вода для приготовления замеса подается в определенном соотношении с расходом сырья. Для измерения расхода воды используется ротаметр типа РПЖ, сигнал от которого поступает в камеру «переменная» вторичного прибора со станцией управления ПВ10.1Э и пропорционально-интегральный регулятор соотношения с коррекцией ПР3.34. На этот же регулятор поступает сигнал, пропорциональный расходу сырья, от ЭПП, а в камеру «коррекция» - корректирующий сигнал по концентрации сухих веществ (плотности) замеса от пропорционального регулятора ПР2.8. Выход регулятора ПР3.34изменяет положение регулирующего клапана, установленного на трубопроводе воды.
Для измерения плотности замеса используется устройство с пневмовыходом, разработанное ВНИИ продуктов брожения.
В качестве датчика для измерения расхода замеса применяется индукционный расходомер типа ИР-51, сигнал от которого поступает на электропневмопреобразователь ЭПП и затем на функциональный блок ПФ1.1. На этот же блок поступает корректирующий сигнал по плотности замеса от плотномера. От ПФ1.1 сигнал поступает на вторичный прибор со станцией управления ПВ10.1Э и пропорционально-интегральный регулятор ПР3.31. Выходной сигнал регулятора ПР3.31 поступает на пневмоэлектропреобразователь ПЭ-55М и на регулируемый тиристорный электропривод, сочлененный с плунжерным насосом замеса.
Системой автоматизации приготовления замеса предусмотрена также стабилизация температуры воды, поступающей в смеситель. Для измерения температуры в смесителе воды используется датчик температуры типа 13ТД, сигнал от которого поступает на вторичный прибор типа ПВ3.2 и пропорционально-интегральный регулятор IIP3.31, который управляет клапанами, установленными на трубопроводах подачи холодной и теплой воды.
Заключение
В заключении курсового проекта цели, поставленные в начале были выполнены в полном объеме.
Внедрение на предприятиях автоматических дозаторов сыпучих материалов позволяет повысить точность дозирования , в большей мере исключить ручной труд, обеспечить высокую производительность и надежность эксплуатации оборудования, увеличить выход продукции и ее качество.
Для получения смесей повышенного качества процесс дозирования происходит обычно непрерывно. При автоматизации процессов дозирования основное внимание уделяется регулированию соотношения расходов заданных рецептурой компонентов, при этом предъявляются повышенные требования к точности дозирования.
Список используемых источников:
1. Белов, М.П. Автоматизированный электропривод типовых производственных механизмов и технологических комплексов/ М.П. Белов, В.Л. Новиков, Л.Н. Рассудов.- М.: Издательский центр «Академия»,2007
2. Шабурова, Г.В. Практикум по оборудованию и автоматизации перерабатывающих производств / Шабурова Г.В.; Зимняков В.М., Курочкин А.А. – М.: КолосС,2004.
3. Проектирование автоматизированных систем: методические указания к выполнению самостоятельной работы для студентов специальности «Автоматизация технологических процессов и производств»/ Е.В. Ерофеева, Б.А. Головушкин. — М.: Иваново, 2008.
4. Системы управления электроприводом / В.М. Терехов, О.И. Осипов. — М.: Академия, 2005.
Дата добавления: 2022-01-22; просмотров: 119; Мы поможем в написании вашей работы! |
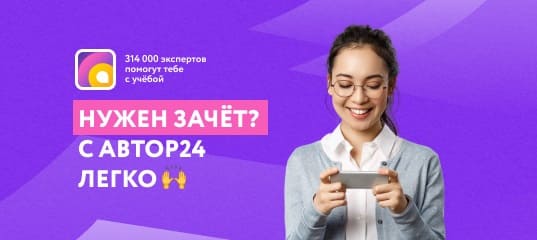
Мы поможем в написании ваших работ!