Классификация устройств дозирования сыпучих материалов испособов дозирования
Департамент внутренней и кадровой политики по Белгородской области
Областное государственное автономное профессиональное образовательное учреждение
«Белгородский политехнический колледж»
КУРСОВОЙ ПРОЕКТ
по МДК 02.01. Технология эксплуатации электронного оборудования и САУ
специальность 27.02.04 «Автоматические системы управления»
Студента группы № 44 Переверзева Данила Игоревича
(фамилия, имя, отчество)
Тема: Автоматизация управления дозированием сыпучих материалов
Руководитель проекта: ____________________________Васильева О.Н.
2019г
ОГАПОУ «Белгородский политехнический колледж»
Рассмотрено на заседании «Утверждаю»
предметно-цикловой комиссии Зам. директора по УР
специальных дисциплин Шевченко Т.А. _____________
Протокол №___ от__________2019 «___»_________________ 2019
Председатель ПЦК ___________
/Антропова О.С./
Задание на курсовой проект
Дисциплина:Технология эксплуатации электронного оборудования и САУ
Студент: Переверзев Данил Игоревич
Курс: 4 Специальность: 27.02.04 Автоматические системы управления
Тема:Автоматизация управления дозированием сыпучих материалов
|
|
Содержание:
I. Пояснительная записка
1. Титульный лист
2. Задание
3. Дозирование сыпучих материалов
4. Классификация устройств дозирования сыпучих материалов и способов дозирования
5. Обоснование функциональной схемы системы автоматизации процесса дозирования сыпучих материалов
6. Весовые дозаторы
7. Циклические дозаторы
8. Применение в пищевой промышленности
9. Заключение
10. Список использованных источников
II. Графическая часть
Лист 1 (формат А1)
Лист 2 (формат А1)
Список рекомендуемыхисточников:
Дата выдачи « » 2019
Дата сдачи « » 2019
Содержание
1. Дозирование сыпучих материалов. 5
2.Классификация устройств дозирования сыпучих материалов и способов дозирования 10
3. Обоснование функциональной схемы системы автоматизации процесса дозирования сыпучих материалов. 13
4. Весовые дозаторы.. 16
5. Циклические дозаторы.. 20
6. Применение в пищевой промышленности. 26
Введение
Дозирование сыпучих материалов является важным этапом цепочки технологических операций. Обычно дозирование осуществляется перед поступлением материала в дробилку для его измельчения. Параллельно с материалом для отделения примесей во входной канал дробилки добавляют воду и флотореагент. Правильное протекание процесса флотации возможно при определенном соотношении между расходами: материала, воды, флотореагента. Данная задача может быть решена при помощи автоматизации процесса дозирования сыпучего материала.
|
|
Дозирование сыпучих материалов
Функциональная схема процесса дозирования представлена на рисунке:
Рисунок 1.Функциональная схема процесса дозирования:
1 - приемный бункер; 2 - ленточный конвейер (дозатор); 3 - мотор-редуктор с асинхронным двигателем для вращения ролика ленты; 4 - приемный бункер дробилки;5 - концевые выключатели для контроля схода ленты (справа и слева);6 - вибрационный привод бункера;7 - датчик уровня материала;8 - датчик расхода воды; 9 - датчик расхода флотореагента;10 - датчик веса; 11 - датчик оборотов ленты; 12 - датчик скорости вала (энкодер); 13 - ультразвуковой датчик уровня флотореагента.
Технологическая схема, представленная на рисунке 1, состоит из приемного бункера, с помощью которого происходит подача сыпучего материала на ленточный конвейер.Лента приводится в движение мотор-редуктором. Дозатор состоит из весового транспортера с бортами, кожухами, подвесками для контрольных весов, формирующей воронкой, датчиков и электрооборудования. Материал, пройдя по ленте, поступает в приемный бункер дробилки. Параллельно с материалом в приемный бункер дробилки также подается вода и флотореагент. Соотношение их расходов должно поддерживаться строго определенным и зависит от заданной производительности дозатора по материалу. Вода и флотореагент служат для отделения примесей сыпучего материала в процессе его измельчения на последующем этапе.
|
|
Проведен анализ технологического процесса и выбраны средства автоматизации. В качестве электропривода ленты предлагается применить частотно-регулируемый ВЕСПЕР EI-7011-001H электропривод с управлением по U/ƒ — характеристике. Частотное регулирование обеспечивает высокое качество управления скоростью асинхронного двигателя.
Датчик уровня материала предназначен для выдачи сигнала о наличии материала в формирующей воронке. В зависимости от исполнения дозатора может быть применен емкостной датчик ДКЕ. Емкостные датчики контролируют наличие, отсутствие, а также уровень сыпучих материалов в резервуаре.
|
|
Вибрационный электропривод OLIMVE60/3 бункера необходим для того, чтобы материал, поступающий на ленту, не застревал в бункере.Концевые выключатели ВСКЛ для контроля схода ленты предназначены для сигнализации смещения ленты относительно продольной оси дозатора. Тензодатчик веса T2-0.1-C3 используется для измерения веса материала, находящегося на весоизмерительном участке ленты. Датчик оборотов ДО-01 ленты служит для определения количества полных оборотов ленты. Датчик скорости Siemens1XP8001-1 необходим для измерения скорости вращения быстроходного вала редуктора. Расходомер предназначен для измерения расхода воды или флотореагента.
Поплавковый датчик уровня ОВЕН ПДУ-И.250 служит для контроля уровня флотореагента в емкости. Выбраны также микродозаторфлотореагентаДарконт ООМ004 и регулируемый клапан с электроприводом ВАРИПАК 8013 и расходомер Метран-350-SFAдля регулирования расхода воды.
В качестве управляющего контроллера предложено использовать ОВЕН ПЛК 110-220-32-К с модулями аналогового ввода МУ-110И-8И и аналогового вывода МВ-110-224.8А. Для обеспечения человеко-машинного интерфейса выбрана операторская панель ОВЕН СП-270. Взаимодействие контроллера с панелью и модулями ввода-вывода осуществляется по интерфейсу RS-485.
Рассчитан автоматический регулятор производительности материала. Оценка эффективности его работы возможна с помощью компьютерного моделирования дозатора, как объекта управления.
Рисунок 2. Структурная схема системы управления дозатором с частотным электроприводом:
Gзад- заданная производительность; Kpc- пропорциональная составляющая регулятора; Tcp- интегральная составляющая регулятора;Kпч- передаточный коэффициент преобразователя частоты; Tпч- постоянная времени цепи управления преобразователя частоты; w- угловая скорость; β- модуль жесткости; Тэ- электромагнитная постоянная времени; Тм - электромеханическая постоянная времени; iред- передаточное число редуктора; R- радиус роликов; K- вес материала с датчика.
Коэффициенты передаточной функции АД рассчитаны по паспортным данным двигателя. Для моделирования выбран ПИ-регулятор по1.4 рекомендациям структур регуляторов для частотных электроприводов [5, с. 224]. При моделировании системы на вход ПЧ был подан сигнал задания Gзад=5т/ч (1,4 кг/с). Статический момент Мс принят равным 0,5Мном = 1,3 Н.м. На вход К подавался имитационный сигнал с датчика веса равный 100 кг.м. На рисунке 3 представлен график переходного процесса. Из рис.3 видно, что после выхода на установившуюся скорость вращения (через 0,4 сек от начала) производительность становится постоянной. Далее в момент времени t=1 сек сымитировано увеличение веса материала на ленте путем скачкообразного изменения сигнала Kсо 100 кг/с до 120 кг/с. В результате из рис.3 видно, что регулятор автоматически изменяя скорость вращения двигателя выровнял производительность G к заданном значению 1,4 кг/с. Время переходного процесса составило 0,4 сек, перерегулирование — 12 %, что является допустимым по регламенту.
Рисунок 3. График системы управления технологическим процессом
В данной статье рассмотрена задача автоматизации технологического процесса дозирования сыпучего материала с учетом расхода воды и флотореагента. Проведен выбор средств автоматизации. Составлена структурная схема и выполнено моделирование весового дозатора в программе компьютерного моделирования. Результаты моделирования показали, что при возмущающих воздействиях со стороны датчика веса в диапазоне ±20 %, производительность автоматически поддерживается регулятором с временем переходного процесса 0,4 сек и перерегулированием 12 %. Это свидетельствует о том, разработанный алгоритм управления может быть применен в системе управления дозатором.
Классификация устройств дозирования сыпучих материалов испособов дозирования
Современное развитие оборудования в сфере приготовления комбикормов ставит задачу организовать процесс производства с меньшим количеством единиц оборудования, меньшей протяженностью транспортных линийи, соответственно, снижение энергопотребления. Также обязательным условием является высокое качество выпускаемой продукции, эксплуатационнаянадежность оборудования при возрастающем уровне его автоматизации иобеспечение безопасности производства и комфортных условий труда дляперсонала.Качество конечного продукта в первую очередь зависит от точностидозирования компонентов кормовых смесей. Сыпучие материалы оченьтрудно точно дозировать вручную, поэтому на производствах применяютсяразличные типы дозаторов.
К настоящему времени разработано множество конструкций дозирующих устройств. Это связано с тем, что материалопоток обладает широкимдиапазоном физико-механических и технологических характеристик; крометого, к оборудованию часто предъявляются специфические требования в зависимости от особенностей процесса.
Классификацию типов дозаторов можно провести по трем признакам:
- по структуре работы цикла;
- конструктивным признакам;
- принципу работы.
По структуре рабочего цикла можно выделить дозаторы непрерывногодействия и дозаторы дискретного действия.
В осуществлении грузопотоков на предприятиях основную роль играют системы подъёмно-транспортных машин и оборудования. Для транспортирования груза, в основном применяются ленточные конвейеры. Ленточными конвейерами перемещают сыпучие кусковые материалы, штучные грузы, а также пластичные смеси бетонов и растворов.
Их широко применяют для непрерывного транспортирования различных материалов в горизонтальном или наклонном направлениях. Они обеспечивают высокую производительность (до нескольких тысяч тонн в час) и значительную дальность транспортирования (до нескольких десятков километров). В строительстве используют передвижные и стационарные ленточные конвейеры, перемещающие грузы на сравнительно небольшие расстояния.
Целью статьи является выявить основные и дополнительные машины и механизмы для комплексной механизации процесса транспортирования сыпучих грузов. В соответствии с целью, поставлены следующие задачи:
- изучить основные машины;
- изучить дополнительные машины;
- изучить главные параметры основных и дополнительных машин.
Основная машина в процессе транспортирования сыпучих грузов — ленточный конвейер. Эту транспортирующую машину характеризует длина транспортирования L и ее составляющие — длина горизонтальной проекции Lр и высота подъема материала Н, связанные между собой зависимостью:
Lр = L1·cos β; Н = L·sin β,
где α — угол подъема.
При транспортировании насыпных грузов минимальная ширина ленты должна удовлетворять условию:
- для рядового груза В = 2·а + 200 мм;
- для сортированного груза В = 2·a + 200 мм,
где a — размер типичного куска.
Рисунок 4. Схема ленточного конвейера
Дата добавления: 2022-01-22; просмотров: 56; Мы поможем в написании вашей работы! |
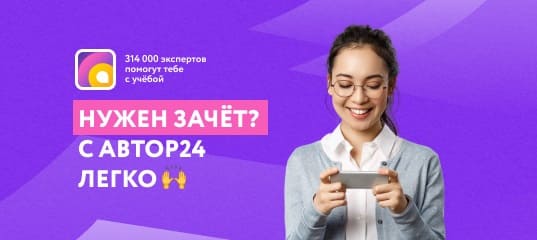
Мы поможем в написании ваших работ!