Обоснование функциональной схемы системы автоматизации процесса дозирования сыпучих материалов
Для обеспечения высокой надежности программно-аппаратный комплекс должен состоять как минимум из трех уровней. Нижний уровень содержит датчики и исполнительные механизмы. Средний уровень включает в себя управляющий контроллер. Верхний уровень представляет собой автоматизированное рабочее место оператора на базе персонального компьютера.
Технологический процесс дозирования требует максимальную точность дозирования при заданной производительности.
На входе регулятора веса, программно выполненного в контроллере, суммируются сигнал задания на вес, поступающий сигнал с нормирующего усилителя пропорциональный текущему весу. Выход регулятора веса является заданием на частоту преобразователя и, соответственно, скорости вращения мотор-редуктора шнекового питателя. По мере наполнения бункера разница между заданной и действительной массой в бункере уменьшается, что приводит к уменьшению скорости электропривода. Остановка двигателя осуществляется на небольшой скорости, что положительно сказывается на точности дозирования. После окончания работы первого шнека, вступает в работу второй и так далее, до заполнения бункера-дозатора. Как только бункер-дозатор заполнен и все шнеки выключены, поступает сигнал управления на фидерную сборку реверсивного пуска, которая включает двигатель задвижки и открывает ее. Вся отдозированная масса высыпается в бункер смеситель. Смеситель работает по заданному времени, как время смешивания закончилось, отключается двигатель смесителя и открывается задвижка бункера-смесителя. Также включается двигатель транспортера готовой продукции. Транспортер готовый продукции будет работать по заданному времени.
|
|
Исходя из функциональной схемы в процессе проектирования нужно выбрать следующее оборудование.
- Двигатели шнековых питателей;
- Преобразователь частоты;
- Пусковую аппаратуру;
- Тензо-датчики веса, датчики положения;
- Нормирующий суммирующий усилитель;
- Кабели, автоматические выключатели;
- Блоки питания;
- Контроллер, блоки релейной коммутации и компьютер.
При проектировании системы дозирования сыпучих материалов, необходимо правильно выбрать мощность двигателя и скорость вращения шнекового питателя.
По техническому заданию на проектирование известны параметры механизма и желаемая производительность системы. Производительность шнекового питателя прямо пропорциональна скорости вращения механизма и находится по формуле:
где D - внешний диаметр шнека;
d - диаметр вала;
S - шаг винта шнека;
n- скорость вращения шнекового питателя;
j- коэффициент производительности.
|
|
где D - внешний диаметр шнека;
Для того чтобы определить скорость вращения шнекового питателя, которая требуется для обеспечения заданной производительности системы, выражаем ее из формулы:
где К3 - коэффициент запаса, К3=1,1-1,3;
Для горизонтального шнека пассивная область целиком размещается на шнеке при условии S/D?1 и, следовательно, применима формула:
12. Тогда по формуле (2) рассчитываем скорость вращения шнекового питателя:
Секундная производительность
Удельный расход энергии
где =0,8- коэффициент трения;
L- длина шнека;
- насыпная объемная масса материала (кг/м3).
Расчетный момент сопротивления на валу
Весовые дозаторы
Весовые дозаторы непрерывного действия предназначены для выдачи постоянного количества материала в единицу времени. Например, дозаторы марки С-613 производительностью 7-30 т/ч служат для весового непрерывного дозирования инертных заполнителей бетона с максимальной крупностью до 40мм, на передвижных бетоносмесительных установках непрерывного действия, работающих на открытом воздухе. Это и определяет конструкцию дозатора с простой механической системой регулирования.
Рисунок 5. Весовой транспортер маятникового типа
|
|
Чувствительным элементом системы регулирования служит весовой транспортер маятникового типа, подвешенный на призменной подвеске. Изменение производительности дозатора Q преобразуется весовым транспортером в момент силы тяжести М и в угол поворота φ транспортера. С рамой весового транспортера связана заслонка, которая определяет величину слоя материала на ленте, а тем самым и производительность дозатора. Значение времени запаздывания таких дозаторов составляет от 5 до 30 сек, что сказывается на качестве приготовления смеси.
Однако колебания напряжения и частоты питающей сети, а также нагрузочного момента привода ленты приводят к значительной нестабильности скорости ленты и существенным ошибкам дозирования. Именно поэтому в настоящее время создается все большее число систем дозирования, в которых регулирование осуществляется непосредственно по расходу. Принцип действия таких дозаторов основан на компенсации отклонения расхода от заданного.
Расход получается умножением сигналов, пропорциональных массе материала и скорости ленты конвейера. Управляющее воздействие осуществляется путем изменения скорости ленты. В качестве примера подобных систем управления может быть рассмотрен дозатор С-781, предназначенный для дозирования цемента и других пылевидных материалов.
|
|
Автоматический регулятор такого дозатора включает в себя: весовой ленточный транспортер, являющийся чувствительным элементом; преобразователь, преобразующий изменение веса материала в электрический сигнал или сигнал другого типа; регулятор и регулирующий орган или исполнительный механизм, обеспечивающий поддержание постоянства подачи материала питателям.
Здесь постоянство соотношения подачи материалов обеспечивается за счет регулирования скорости приводных двигателей. Это достаточно точная система, но требует в приводе двигатели постоянного тока.
Лента весового конвейера приводится в движение через редуктор от двигателя. Вибропитатель с постоянной производительностью подает на ленту дозируемый материал. Действующее от массы усилие на ленту конвейера передается через рычажную систему на уравновешивающую часть. Отклонение рычага с уравновешивающим грузом от заданного положения вызывает соответствующее перемещение плунжера индуктивного датчика. От него сигнал через электронную аппаратуру передается электромагнитному вибропитателю.
Производительность вибропитателя можно изменять, повышая или понижая напряжение в обмотках его электромагнитов. Можно менять при необходимости наклон лотка, скорость движения ленты, положение уравновешивающего груза.
Наиболее важными особенностями непрерывных дозаторов, рассматриваемых как системы автоматического регулирования расхода сыпучих материалов, является способ управления.
Способ регулирования характеризуется видом информации о текущем значении расхода.
При этом существенным является уравнение:
Q = s γ h V υ,
определяющее зависимость между расходом Q питателя, массой материала на ленте конвейера и скоростью ленты υ (γ — насыпная плотность материала, s и h — соответственно ширина конвейерной ленты и высота слоя материала на ней).
Существует большое количество различных модификаций дозирующих устройств, в которых скорость ленты конвейера принимается постоянной (например, рассмотренные ранее дозаторы С-613 и С-313), а измеряемый сигнал от массы материала на ленте — пропорциональным значению расхода. Дозаторы такого типа называются дозаторами с регулированием по массе. Общим для всех вариантов управления является наличие нерегулируемого привода скорости ленты конвейера.
Принцип управления, основанный на поддержании неизменного среднего значения массы материала на ленте конвейера, осуществляется по косвенному параметру. Такое управление эффективно только в том случае, если косвенный параметр полностью характеризует процессы, происходящие в объекте.
Рассмотренные выше схемы непрерывного дозирования могут быть упорядочены по критерию минимума ошибки дозирования. Наименьшими потенциальными возможностями обладают дозаторы с управлением по массе. В первую очередь это вызвано нестабильностью скорости привода и инерционностью регулятора.
Повышения качества дозирования можно добиться за счет применения дозаторов с управлением по производительности. Дальнейшее улучшение динамических параметров дозаторов непрерывного действия требует усложнения структуры системы управления.
Можно предполагать, что если управляющее воздействие, пропорциональное сигналу ошибки, подавать не только на привод ленты конвейера, но и на питатель, т.е. управлять одновременно скоростью ленты и производительностью питателя, то можно еще более снизить ошибку дозирования.
Для реализации такой структурной схемы необходимо, чтобы сигнал, пропорциональный управляющему воздействию (скорости ленты), оказывал влияние также и на высоту слоя материала на ленте конвейера, и тем самым уменьшал влияние возмущающего воздействия. Принципиальная схема такого дозатора может иметь следующий вид:
Рисунок 6. Принципиальная схема непрерывного дозатора
Циклические дозаторы
Наряду с дозаторами непрерывного действия в различных технологических процессах широко используются дозаторы периодического действия. Это весовые устройства, которые состоят из ковша, загрузочных устройств, весового механизма и аппаратуры управления. Усилие от ковша, подвешенного на призменных или упругих опорах, передается через систему рычагов на главное коромысло. Главное коромысло связывается с циферблатным указателем массы. Весовой механизм имеет также рецептурные коромысла, снабженные передвигающимися гирями дляустановки значения отмериваемой дозы.
Циферблатный указатель массы оборудован поворотным диском с расположенными на нем датчиками, фиксирующими степень загрузки весового ковша. При заполнении бункера стрелка циферблатной головки, вращаясь, поочередно заставляет срабатывать датчики поворотного диска.
Рисунок 7. Принципиальная схема весового дозатора АВДЦ-425:
аэрационный питатель 1; весовой ковш 2; рычажная система 3; циферблатный указатель 4.
При включении питателя происходит заполнение ковша, который через рычажную систему вращает стрелку циферблатной головки до замыкания соответствующего контакта на указателе массы. При этом включаются пневмоцилиндры закрытия впускного затвора, и поступление материала в весовой бункер прекращается. Отдозированная таким образом порция материала выгружается из бункера самотеком при включении пневмоцилиндра открытия выпускного затвора. Рассмотренный дозатор циклического действия оснащен простейшей системой управления с минимально необходимым набором функциональных элементов, реализующих процесс набора заданной дозы. Объектами управления (ОУ) в системе служат питатели разнообразных типов.
Управляемый параметр — масса дозируемого веществаG — определяется ковшом с рычажной подвеской (ВБ) и циферблатным указателем массы (Ц), которые выполняют роль чувствительного элемента. Циферблатный указатель выполняет функцию сравнения текущего значения массы с заданием G3.
Исполнительный механизм (ИМ) с регулирующим органом (РО) включаются в работу кратковременно, отсекая подачу материала питателем. Дозатор обладает системой управления дискретного действия с кратковременным восстановлением контура обратной связи, по которому передается воздействие на изменение управляющего параметра — расхода питателя.
Недостатки такого способа управления очевидны:
Перемещение стрелки, фиксирующей изменение массы материала в бункере, испытывает на себе сильное влияние динамического усилия от столба материала, подаваемого питателем, а также от ускорений, получаемых бункером в процессе его заполнения. Система управления по окончании цикла дозирования фиксирует наряду с истинной еще и фиктивную массу, значение которой не может быть откорректировано по линии обратной связи.
Для повышения точности автоматическое управление весовым периодическим дозированием должно осуществляться по специальному алгоритму, учитывающему влияние процесса истечения материала, а также количество материала, поступающего в бункер дозатора после подачи сигнала на закрытие затвора питателя в каждом цикле дозирования.
Рисунок 8.Функциональная схема дозатора циклического действия
Устройства для дозирования сыпучих материалов попринципу подачи материала можно разделить на непрерывныеи дискретные дозаторы. Непрерывные дозаторы подаютматериал непрерывно и равномерно.
Количество отдаваемогоматериала определяется либо скоростью, либо временемподачи. К дозаторам непрерывного действия можно отнестиконвейерные или шнековые.
Дискретные дозаторы подают материал порциями черезпромежутки времени. Количество отдаваемого материаларегулируется путем изменения количества порций в единицувремени или величиной самой порции. К дозаторам дискретногодействия можно отнести ковшовые, стаканные, шлюзовые,бункерные и прочие подобные им. Принцип непрерывнойподачи материала позволяет добиться более точногодозирования и более равномерного смешивания компонентов ипоэтому представляется более предпочтительным. Ксожалению, серьезным недостатком непрерывных дозаторов —конвейерных и шнековых — является их громоздкость иналичие механического привода и движущихся частей. Сложныймеханизм невозможно эксплуатировать при высокихтемпературах или в агрессивной среде, а абразивный характерматериала серьезно уменьшает срок службы и делает болеедорогой эксплуатацию. Дискретные дозаторы хотя и являютсяменее прецизионными, однако имеют гораздо более простуюконструкцию, проще обслуживаются и надежно работают привысоких температурах и в агрессивных средах.
Задачауправлениярасходомсыпучегоматериалаявляетсявесьматипичнойдляавтоматизации производственныхпроцессовизмельчения,смешивания,растворения,дозированияидр.Известномножество разработок систем автоматического регулирования (САР) разнообразных сыпучих материалов. В их основе лежит прямоеизмерениерасходасыпучегоматериаласиспользованиемтехилииныхфизическихявлений.Кчислу современных средств измерения расхода различных твердых веществ и их смесейс гранулометрическим составом от1нмдо0,1мотносятся,например,SolidFlow,MaxFlow,DensFlow,ClampFlow.Величинапогрешности измерения указанных расходомеров достигает 3…5 %. Это вынуждает искать другой способ получения информации о величине расхода сыпучего материала, не требующий использованиярасходомеров.Новозможнолиэто?Да,внекоторыхслучаяхможнопостроитьСАРрасхода сыпучего материала, используя косвенный параметр, находящийся в прямой корреляции с величиной расхода, тем более, что часто не требуется высокая точность его измерения.
Вкачествеисполнительныхустройств(ИУ)всистемахуправлениярасходомсыпучихматериаловшироко применяютсяразнообразныепитатели(барабанные,ленточные,вибрационные,лопастные,шнековыеидр.).В числе их недостатков следует также отметить:
- большие первоначальные денежные затраты на создание САР из-за необходимости наличияв канале управления преобразователя частоты(ПЧ) напряженияэлектродвигателя;
- онипостоянноиспользуютэнергиюэлектрическоготокаприсвоейработе,тоестьдлянихсвойственны значительныеденежныерасходыиприэксплуатации;
- необходимостьрасходомераиПЧобусловливают снижение надежности САР.
Альтернативойпитателямявляютсяподбункерные(подсилосные)задвижки,кчислудостоинствкоторых относятся:простотаконструкции,высокаянадежностьидолговечность,небольшаястоимостьсозданияСАР(в вариантеотсутствиявнейрасходомера),оченьмаленькие,буквальномизерные,эксплуатационныерасходы. ИменноиспользованиевсоставеИУвкачестверегулирующегооргана(РО)подбункерных(реечныхлибо винтовых)задвижекипозволяетприпостроенииСАРрасходасыпучегоматериалаиспользоватькосвенный параметр, коррелированный с текущей величиной расхода. Основная часть. В качестве косвенного параметра, находящегося в прямой корреляции с текущей величиной расходасыпучегоматериала,можноиспользоватьодинизгеометрическихпараметровзадвижки–величину линейногоперемещениязатворарегулирующегооргана–шибера.Обозначимкоординатуположенияшибера через«а»(м).Подбункерныезадвижкиимеютквадратнуюформуотверстиясосторонойb,черезкотороеи движетсясамотекомсыпучийматериал,еслиa>0.
Сторонаквадрата,тоестьширинаотверстияшироко используемыхзадвижек,0,2b0,5,м;b=const.Параметраоднозначноопределяетстепеньоткрытия задвижки. ЭкспериментальноустановленазависимостьвеличинырасходаQсыпучегоматериалаотвеличиныа открытия задвижки при различных величинах b и различных видах сыпучих зернопродуктов.
Дата добавления: 2022-01-22; просмотров: 82; Мы поможем в написании вашей работы! |
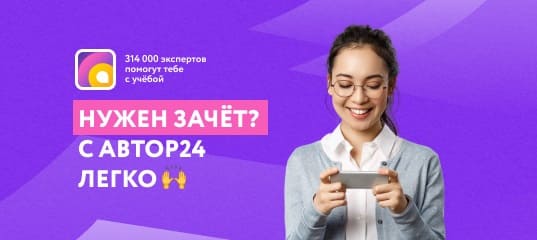
Мы поможем в написании ваших работ!