Выполнение основных операций.
Типовые и групповые технологические процессы (ТП).
Типизацией ТП называется такое направление в ходе изучения и построения технологий, которое заключается в классификации деталей, разбивке их на группы, имеющие конструктивно-технологическую общность и в комплексном решении всех вопросов, возникающих в каждой классифицированной группе.
Сущность идеи – чем больше деталей будет изготовлено по данной технологии, тем ниже будет себестоимость изготовления деталей применительно к данному ТП.
Трудоемкость составления типового ТП является весьма высокой. И этими вопросами занимаются научно – исследовательские отраслевые институты.
Идея типизации ТП принадлежит А.П.Соколовскому, и нашла своё отражение в ЕСТД.
Данная идея имеет два направления:
1.разбивка деталей по конструктивному признаку и составление ТП на выбранную группу.
2.подбор деталей по подобию обрабатываемых поверхностей.
Реализацией обоих этих направлений возможно применительно к массовому производству. Поскольку в нашей промышленности заводы массового производства составляют только 20%, то типизация ТП наиболее актуальна для серийного и мелкосерийного производства. Применительно к серийному производству наиболее подходящей оказалась идея групповой обработки деталей (идея С.М. Митрофанов), которая явилась в дальнейшем развитием типизации ТП.
Эта идея основана на классификации деталей по видам обработки с выделением из всей совокупности деталей таких групп деталей, которые требуют одинаковое оборудование, общих приспособлений и одинаковую настройку станка.
|
|
|
Групповые технологии могут быть применимы как на отдельных операциях, так и при обработке партии или групп деталей, имеющих общую последовательность выполняемых операций.
Классификация деталей:
Групповой метод основан на классификации деталей по видам обработки, т.е. создаются группы деталей, которые обрабатываются на револьверных станках, на станках автоматах, фрезерных, сверлильных и т.д.
В свою очередь каждый класс разбивается на группы с учетом точности обработки, габаритов деталей и общности ТП.
При проектировании групповых ТП составляется комплексная деталь, включающая в себя все поверхности деталей группы.
ТП составляется для комплексной детали, и он является групповым для всех деталей, входящих в группу.
Комплексная деталь – реальная или условная деталь, содержащая в своей конструкции все элементы (поверхности) деталей, входящих в группу.
|
|
Комплексная деталь является конструктивно – технологическим представителем деталей группы.
Под основными элементами детали понимают поверхности, определяющие конфигурацию детали и основные технологические задачи, решаемые при их обработке.
Основные элементы служат главным признаком при отнесении конкретной детали к той или иной группе.
Поверхности или элементы комплексной детали необходимо индексировать по определённой схеме, так чтобы все поверхности деталей входящих в группу были ею охвачены.
При разработке группового ТП исходят из следующих изображений:
1. последовательность всех технологических операций и переходов должна обеспечивать обработку всех поверхностей детали группы;
2. технологическая оснастка должна быть приемлемой для обработки всех деталей группы, т.е. быть унифицированной и обеспечивать увеличение производительности обработки.
Последовательность выполнения работ при составлении группового ТП:
1.разбивка детали на группы
2.создание комплексной детали и разработка группового ТП и наладки
3.проектирование групповой оснастки
4.модернизация оборудования
5.перепланировка участка для обеспечения прямоточного технологического потока
|
|
6.проведения технического нормирования
Для группового ТП изготавливается групповая оснастка и групповая наладка.
Групповая наладка – наладка станка, обеспечивающая обработку всех деталей группы при небольших переналадках или без них.
Особенности составления групповых ТП при обработке на токарных станках:
1.сокращается универсальность станка и автоматизируются вспомогательные переходы
2.автоматизируются переключение оборотов и подач
3.станок оснащается групповой оснасткой (цанги, план шайбы и т.д.)
4.используются многоместные оправки и резцедержатели
5.для обработки фасонных поверхностей используют копировальные устройства с набором копировальных линеек в виде суппорта
Групповая технология применяется в мелкосерийном и серийном производстве, где используется универсальное оборудование, поэтому его необходимо модернизировать под групповую технологию.
Особенности группового ТП при обработке на многорезцовых токарных станках:
1.применяют сменные резцовые блоки, настройка которых производится вне рабочей зоны, что снижает на 40-50% время на установку и регулировку резцов.
2.применяют поворотные резцовые блоки для каждой рабочей позиции.
|
|
Особенности группового ТП для сверлильных станков:
1.производится унификация установочных элементов в приспособлении
2.применяются поворотные столы и унифицированные кондукторы
3.применяются шпиндельные головки с выдвижным и фиксированным положением шпинделя
4.для сверления и расточки отверстий применяют агрегатные станки.
Техническое нормирование при групповом ТП:
В мелкосерийном и единичном производствах из-за большой номенклатуры применение технически обоснованных норм и техническое нормирование невозможно.
При применении групповых ТП серийность как бы увеличивается и становится возможным техническое нормирование.
Нормирование осуществляется на комплексную деталь, нормирование деталей входящих в группу берется в процентном отношении к комплексной детали. И хотя технические нормы также будут приблизительны, но все же более точно отражают истинную трудоёмкость, по сравнению с опытно-статическими нормами, применяемыми в мелкосерийном и единичном производствах.
Особенности группового ТП:
1.станки оснащаются необходимой оснасткой согласно ведомости группового ТП
2.станок и деталь закрепляются за одним рабочим
3.производится четкое оперативное планирование на участке с целью своевременного обеспечения рабочего места заготовками, инструментом, приспособлениями и т.д.
Применение группового ТП позволяет повысить производительность труда на:
1. револьверных операциях на 40-50%
2. токарных на 20-30%
3. фрезерных и сверлильных на 20-30%
Время на переналадку сокращается на:
1. револьверных на 40-50%
2. фрезерных на 80%
3. токарных на 20-30%
Принципиальное отличие групповой и типовой технологии:
1. Типовая технология характеризуется общностью последовательности и содержания операций ТП, т.е. технологическим и конструктивным подобием детали.
2. Групповая технология характеризуется общностью оборудования и технологической оснасткой, необходимой для выполнения данной операции или полного изготовления детали.
3. Типовая технология предпочтительна для массового и крупносерийного производства.
4. Групповая технология предназначена для серийного и мелкосерийного производства.
Комплектность документов и правила оформления документов на типовые и групповые ТП регламентирована ГОСТ 3.1121-84.
ОЦЕНКА ТЕХНИКО-ЭКОНОМИЧЕСКОЙ ЭФФЕКТИВНОСТИ ТП:
ТЕХНИКО-ЭКОНОМИЧЕСКИЕ ПОКАЗАТЕЛИ ТП:
Технико-экономическая эффективность вновь разрабатываемых и существующих ТП оценивается технико-экономическими показатели:
1.Наиболее характерными из них является себестоимость детали, которая определяется:
,
где M – стоимость материала,
P – основная з/плата производственных рабочих
R – цеховые накладные расходы
2.Цеховая себестоимость (обработки)
3.Норма времени на обработку всей детали
где - время обработки на одной операции
4.Основное технологическое время по всем операциям обработки детали:
5.Коэффициент использования станка по основному технологическому времени:
или
для станка автомата (в идеале)
6.Коэффициент загрузки станка
,
где Ср – расчетное количество станков, необходимых для обработки детали
Спр – принятое количество станков
7.Степень автоматизации производства:
,
где - количество автоматизированных станков
- общее количество станков, используемых в производстве
8.Выпуск продукции в рублях, тоннах или штуках на одного рабочего, характеризует производительность труда.
9.Выпуск продукции на единицу оборудования, характеризует уровень использования оборудования.
10.Выпуск продукции на единицу площади, характеризует эффективность использования площади.
Оценивать технико-экономическую эффективность ТП следует по комплексу параметров, главным из которых является себестоимость выпускаемой продукции.
Оценка экономической эффективности производится путем сравнения разрабатываемого ТП с ТП передовых предприятий, выпускающих аналогичную продукцию.
ТЕХНИКО-ЭКОНОМИЧЕСКОЕ СРАВНЕНИЕ ВАРИАНТОВ ТП. СТРУКТУРА СЕБЕСТОИМОСТИ ДЕТАЛИ:
Себестоимость детали:
,
1.
где Q и - вес материала заготовок и отходов (к одной детали в [кг])
Sк и Sотх – цена одного кг материала заготовки и отходов
2. ,
,
где Ропер. – основная з/плата за выполнение одной операции
Sn – з/плата в единицу времени для данного разряда
S1 – ставка для 1-ого разряда
Kn – разрядный коэффициент
Т.О. - стоимость обработки
3. в серийном производстве для машиностроения цеховые накладные расходы в % от Р.
для механических цехов автопроизводства
для основного производства
Цеховые накладные расходы для данной операции (одной операции):
где Аст – амортизация станка
Lст – затраты на малый ремонт, осмотр и проверку станка, отнесенные к одной операции
Апр – амортизация приспособления и его ремонт
J – затраты на инструмент
Е – затраты на силовую электроэнергию
D – доплаты и начисления на основную з/плату
Z – другие цеховые расходы, несвязанные или мало связанные с конкретными ТП и оборудованием (затраты на эксплуатацию помещения, на вспомогательные материалы (ветошь, масла), з/плата вспомогательных рабочих, административно-технического персонала и конторского персонала, а также отопление, освещение, вода и др. Эти затраты мало связаны с изменением ТП и считаются постоянными).
1) Доля ежегодных Аст амортизационных начислений оборудования на одну операцию рассчитывают:
где - число годовых процентов от балансовой стоимости станка, отчисляемых на амортизацию;
для двухсменной работы
Sст – балансовая стоимость станка
Fд – действительный фонд времени работы станка в одну смену
m – число смен работы станка
- коэффициент загрузки станка по времени
- штучное время на выполнение одной операции
2) Lст – годовой
где годовые отчисления от балансовой стоимости станка
3)
(приспособления служат 3…5 лет)
где N – число обработанных приспособлении деталей
Sпр – стоимость приспособления
- коэффициент годовых отчислений, от стоимости приспособления
- затраты на ремонт приспособления на период его эксплуатации, от стоимости приспособления
4)
где - затраты на производство инструмента
- затраты на заточку режущего инструмента
5)
Sk – цена 1 кВт электроэнергии
W – потребляемая электроэнергия на одну операцию
КПД электродвигателя
Ny – установленная мощность электродвигателя
- коэффициент загрузки электродвигателя по мощности
- коэффициент потери электроэнергии в сети, отнесенное к основному времени
- основное время
6) D начисляется в процентах к основной з/плате производственных рабочих и начисляется от суммы в процентах от основной и дополнительной з/платы
или
где Ропер – з/плата основных производственных рабочих за одну операцию
- доплата от основной з/платы
- начисления на основную и дополнительную з/плату
7) Z – остальные цеховые расходы берутся в процентах от основной з/платы
где в зависимости от вида цеха
ПУТИ ПОВЫШЕНИЯ ТЕХНИКО-ЭКОНОМИЧЕСКОЙ ЭФФЕКТИВНОСТИ ТП:
1. Рациональная организация рабочего места, позволяющая уменьшить подготовительно-заключительное и вспомогательное время на операциях.
2. Применение режимов обработки, позволяющих максимально использовать мощность станка и возможности инструмента.
3. Максимальное снижение за счет применения механизированных и автоматизированных станков и приспособлений.
4. Применение фасонного инструмента и копировальных устройств.
5. Многостаночное обслуживание.
6. Применение специальных станков, агрегатных и станков с ЧПУ.
7. Применение САПР ТП для ускорения составления ТП.
8. Применение типовых и групповых ТП.
Все эти мероприятия позволяют снизить затраты на проектирование, обработку, лучше использовать оборудование и производственные площади, и снизить себестоимость обработки.
ТИПОВЫЕ ТЕХНОЛОГИИ:
ОБРАБОТКА ВАЛОВ АД:
Классификация валов, конструкция валов, технические условия на валы и материалы:
Детали класса валов весьма разнообразны по конструкции, габаритам, весу, служебному назначению, но с конструктивной и технологической точки зрения все валы можно классифицировать по следующим группам:
1.Ступенчатые
2.Цельные
3.Сборные
4.Пустотелые
5.С прямолинейной осью
6.Коленчатые
Рассмотрим валы с прямолинейной осью. К ним относятся валы турбин, компрессоров, турбонасосов, агрегатов, редукторов и распред. валы.
Валы АД работают в сложных узлах при больших нагрузках и высоких температурах, к ним предъявляют жесткие требования по прочности и весу.
Необходимость уменьшения веса и обеспечения равнопрочности вала по сечениям, приводят к усложнению их формы.
Валы пустотелые, тонкостенные при большой длине, наиболее сложны в изготовлении валы турбин и компрессоров, турбонасоса, агрегата.
Поверхности этих валов представляют собой сочетание гладких, сферических, резьбовых, шлицевых поверхностей, а также могут иметь зубчатые венцы.
На валах могут быть отверстия, просверленные наклонно или под прямым углом к оси для подвода масла к подшипникам.
На фланцах валов также могут быть отверстия для крепления к ним дисков.
Форма отверстий валов задается из условий равнопрочности, поэтому они имеют сложную форму, сочетание цилиндрических и радиальных поверхностей.
Тяжелые условия работы валов обусловлены назначением жестких требований к ним.
ТУ на валы:
Точность
· рабочих шеек валов 5-6 квалитет
· не рабочих поверхностей 8-10 квалитет
Отклонение формы шеек:
· рабочих поверхностей 0,005-0,020
· нерабочих поверхностей 0,010-0,040
Точность осевых отверстий 8-10 квалитет
Точность сопрягаемых отверстий 5-6 кв.
Точность резьбы 5-6 кв.
Биение шеек относительно друг друга 0,01-0,04
Относительное биение рабочих и нерабочих шеек 0,05-0,2
Шероховатость
· рабочих поверхностей 1,25-0,16
· нерабочих поверхностей Rz 20 Ra 1,25
Валы статически и динамически балансируют.
Материалы валов:
Из высоколегированных конструкционных сталей:
38ХМЮА (азотирование на h=0,6…0,9 мм
40ХНМА с закалкой до HRc=65 ед.)
12ХН3А (рабочие поверхности
18ХН3А цементируют на h=0,7…1,2 мм
18ХН4А с последующей закалкой до
HRc=58 ед. для обеспечения
предела прочности
)
Термоулучшаемые валы после закалки (40ХНМА) имеют твердость HRc=38…42 ед.
Для ракетных двигателей одноразового использования применяют менее легированные стали – 38ХА, СТ45.
ПОСТРОЕНИЕ ТП:
Заготовки на валы получают на молотах, прессах и горно-ковочных машинах. Разъем штампов может быть вдоль и перпендикулярно оси.
РИС
Заготовки авиавалов проверяются по первой группе контроля (на 70-75 мм длиннее для отрезки образцов на мех. испытания), припуска на обработку задаются z=6-15 мм на сторону.
В цеха заготовки поступают в нормализованном состоянии, с твердостью HB 90-270 ед. (нагрев 100 АС3 и охлаждение на воздухе).
После изготовления заготовки на валы с них снимают окалину – травлением (глубина поверхностных дефектов должна быть не более половины припуска на обработку ).
Этапы механической обработки валов:
1.Черновая (обдирка)
2.Чистовая
3.Отделочная
Черновой этап предназначен для обеспечения равномерности припуска на последних операциях и для выявления подповерхностных дефектов. Его проводят на высоких режимах обработки со снятием большей части припуска на неточных, но мощных станках.
При чистовой обработке снимают меньший припуск на меньших режимах для обеспечения заданной точности и частоты обработки. Применяются многорезцовая обработка, копировальные устройства.
Цель: Обеспечить минимальную величину припуска, окончательно обработать и устранить дефекты 1-ого этапа.
На окончательном этапе обеспечиваются скорость, заданная чистота и точность обработки.
Наибольший удельный вес на третьем этапе занимаемой операции:
- шлифование
- хонингование
- полирование и др.
На окончательном этапе часто получают резьбы, мелкие шлицы и другие поверхности, которые могут быть повреждены, если их обрабатывать раньше.
Желательно, чтобы на последних этапах в первую очередь обрабатывались внутренние поверхности, для того, чтобы принять их за базы и обеспечить концентричность внутренних и наружных поверхностей. Это не делается в том случае, если внутрь запрессовывают подшипник скольжения.
Место т/о в ТП обработки валов:
Термоулучшаемые валы (закалка + высокотемпературный отпуск) можно подвергать т/о как до, так и после первого этапа.
В первом случае сокращается технологический цикл. Во втором – появляется опасность непрокаливания вала, если большая величина припуска на обработку.
Место т/о для цементируемых валов определяется способом защиты от цементации.
В авиапромышленности применяют три способа защиты от цементации:
1. меднение нецемнтируемых поверхностей
2. оставлением припуска на цементируемых поверхностях.
3. комбинация первого и второго, применяют в том случае, когда недопустимо повышение твердости нецементируемых поверхностей.
При применение первого и третьего способа защиты ??? меднение цементацию, закалку и отпуск проводят перед чистовой обработки, но после того как цементируемые поверхности подготовлены под окончательную обработку.
При втором способе – защитный цикл удлиняется, т.к. деталь дважды направляется в термический цех, поэтому применяется редко.
Примерный план обработки валов:
1.Валы термоулучшаемые:
Термообработка – нормализация
Подрезка торцев и зацентровка
Обточка наружных поверхностей под люнет если вал длинный.
Черновой этап:
1) сверление осевого отверстия
2) отрезка образцов для испытания
3) растачивание отверстий и протачивание центровых фасок
4) обработка наружных поверхностей
5) т/о (закалка + отпуск)
6) восстановление баз (центровочных фасок)
7) шлифование шеек под люнет, если вал длинный
Чистовой этап:
1) растачивание фасок
2) обтачивание наружных фасок
3) фрезерование канавок, лысок и т.д.
4) сверление радиальных отверстий
Окончательный этап:
1) полирование отверстий
2) растачивание или шлифование участков отверстий с высокой точностью
3) шлифование наружных поверхностей
4) нарезание шлицев
5) нарезание резьбы
6) полирование наружных поверхностей
7) окончательная отделка наружных поверхностей и окончательный контроль.
Закалку валов с диаметром меньше 50 мм с небольшим припуском проводят до первого этапа.
Если вал в длине меньше 500 мм, то их не зацентровывают, а черновой этап начинают с подрезки торца и обработки отверстий.
Обработка валов цементируемых:
1.1 т/о –нормализация
1.2 1.2 подрезка торцев и зацентровка
1.3 проточка шеек под люнет, если валы длинные.
Черновой этап.
1.Сверление осевого отверстрия
2.Отрезка образцов для испытания (для валов 1-й категории контроля)
3.Растачивание отверстий и протачивание
4.Обработка наружних поверхностей
5.Шлифование цементуемых поверхностей, отверстий
6.Шлифование наружных цементуемых шеек, поверхностей, валов. Гальваническая операция: меднение – меднение нецементуемых поверхностей.
7.Цементация, закалка и отпуск.
8.правка и зачистка центральных фасок и базовых поверхностей
9.шлифование шеек под люнет, если вал длинный.
Чистовой этап.
1.Растачивание отверстий.
2.Обтачивание нецементуемых наружных поверхностей.
3.Нарезание шлиц, протачивание выкружек.
4.Сверление радиальных отверстий.
Окончательный этап.
1.Полирование отверстий
2.Шлифование цементированных участков отверстий
3.Шлифование нар-ых цем-ых шеек.
4.Шлифование шлицев.
5.Нарезание резьбы
6.Полирование наружных поверхностей
7.Чистовая отделка наружных рабочих поверхностей.
ВЫПОЛНЕНИЕ ОСНОВНЫХ ОПЕРАЦИЙ ПРИ ОБРАБОТКЕ ВАЛОВ.
Подрезка торцев и зацентровка-на токарных станках общего назначения или на фрез.-центровочных станках ФЦ1, ФЦ2.
Крупные валы зацентровывают дрелью по разметке.
В крупносерийном произ-ве подрезание торцев и зац-ка-на фрез. Станках-МР77, МР78
Обточка отв-ий на коротких валах-на ток. револьверных станках с одновременой обработкой наруж-х поверхностей, при этом достигается их высокая концентричность.
Отверстия на длинных валах обрабатыв-ся на гориз. сверлильных станках для глуб. сверления.
Обточка наружных поверх-й может производиться на монгорезцовых ст.авт-х и полуавт-х. На серийных станках на 1К62ПУ, 1А616ПУ.
Шлифование валов для обеспечения заданной точности. При шл-ии нар-х поверх-й за базу принимают внутрин. Поверх-ти или спец-ные центровые пробки, которые запрессовываются в отв-ие.
Обработка сферических поверхностей валм производиться спец-м заправленным по радиусу абразивным кругом, либо чашечным кругом.
РИС
Нарезание резьбы в конце последнего этапа путем ее фрезер-я с послед-м шлифованием, либо сразу вышлифовывают. Фрезерованием получ. резьбу-ч. фр.
Контроль валов:
1.наружные поверхности скобами
2.внутринние-пробками
3. резьбовые - резьбовыми калибрами.
ОБРАБОТКА ДИСКОВ, ТУРБИН, КОМПРЕССОРОВ И ТУРБО-НАСОСНЫХ АГРЕГАТОВ.
КОНСТРУКЦИЯ, ТУ И МАТЕРИАЛЫ.
Диски ГТД работают в крайне тяжелых условиях.Диски турбин-до 2000°С и испыт-ют напряжение s=5000 кгс\см2, поэтому их изг-т из высокопрочных и жаропрочных сталей ЭИ-437Б(ХН77ТЮР), ЭИ-698, ВД
В большинстве случаев их делают толстостенными, без отв-ий, чтобы не снизить прочность.
На внешней окр-ти утолщенного обода прорезают прямые или косые пазы для установки лопаток.
РИС
Диски центрируются с валами по пояскам с натягом. Крутящий момент от диска к валу передается через штифты, запрессованные в отверстие вала и диска, просверливаются вместе.
Диски осевых компрессоров работают в менее сложных условиях, при низких t-рах их делают из менее жаропрочных сплавов. 18ХНВА,ЭИ415, ЭИ395, ЭИ461, ВТ3-1, ВТ-9, АК4-1, АК6-1, и из пласмасс.
Диски компрессора часто имеют отверстия и утолщенную ступицу. На ободе диска имеются пазы чаще в виде ласточкина хвоста или укороченной елки для крепления лопаток. Ось пазов под лопатки бывает скошенной относительно оси диска на 15-20°.
Диски центрируются с цапфами и между собой по центр-щим пояском и торцевым шлицам. Соединяется с помощью радиальных штифтов или центральным стержнем-болтом.
Диски компрессора имеют более сложную форму по сравнению с дисками турбин.
РИС
Диски ТНА раб-т в таких же условиях как и диски К. и в агрессивных средах. Их изготавливают из жаропрочных сплавов типа : ЖС1, 30ХГСА, ВЛР20, ЭИ787(ХН35ВТ-Ю), ЖС3, ЖС6К.
Эти диски могут отливаться заодно с лопатками или пазами под лопатки, или с приварными лопатками. Диски могут быть ступенчатыми с развитым ободом. Пазы под лопатки: Т-образные, кольцевые, елочные. Соединение вала с диском может быть разъемным и неразъемным. Разъемное осущест-ся штифтами или резьб-ми дисками. При неразъемном соединении вал приваривается к диску шовной сваркой или сваркой по конусам. Сварка дисков и вала осуществляется оплавлением встык или диффузионной сваркой в вакууме.
РИС
ТОЧНОСТЬ ОБРАБОТКИ ДИСКОВ.
Посадочные и лабиринтные пояски-6-8 IT
Диаметры наруж. И внутр. Поверхностей – 8-11 IT
Допуск на ширину паза ласточкин хвост-0,02-0,03 мм
Допуск на елочн. Пазы 0,02-0,03 мм
Допуск на Т-образные пазы - 0,03 мм
Точность расположения:
1. биение наружного диаметра и торцев до 0,05 мм
2. разность шагов зубьев в замке до 0,02 мм
3. разность окружных шагов – 0,2-0,3 мм
4. перекос оси паза на L~100 мм –0,1-0,2 мм
5. смещение одной стороны паза относительно другой до 0,02 мм
Шерох-ть поверх-ти дисков Rа 1,25
посадоч-х и центр-щих поясков Rа 1,25
нерабочих цилиндрич-х пов-й Rа 2,5
в елочном пазу основание паза Rа 2,5
боковые поверхности Rа 1,25
Диски балансируются стат-ки, а в роторе динамически.
Диски компрессора анодируются, оксидируются.
Диски ТНА еще и пассивируют.
ПОСТРОЕНИЕ ТП.
Заготовки дисков Т и К штампуют в закрытых штампах на молотах и мощных прессах.
Диски ТНА малых диаметров отливают с лопатками, а больших диаметров -штампуют. Припуск на обр-ку на сторону – 5-6 мм. Все заготовки на диски клеймят с указанием марки мат-ла, №плавки и № диска.
Стальные заготовки на диски поставляют в мех. Цеха в нормальном состоянии с указанием тв-ти и протравленные.
В сопроводительном сертификате указывают механические св-ва.
Микроструктура заг-к на изломе образцов не должна иметь долокинов, усадочных рыхлот, пузырей, трещин, расслоений, мет-их и неметал-х включений, видимых невооруженым взглядом.
На поверх-ти ободронной з-ки не олно быть пленок, заковок, трещин, инородных включений, нарушающих сплошность мат-ла.
Под поверхностные дефекты выявляются – ультразвуком.
Заг-ки дисков ТНА вместет с лопатками получ-т по выплавляемым моделям по 8-12 IT, шер-тью Rа=2,5, Rz=40
Лопатки на таких дисках не обрабатываются, а собст-но диски обрабатыв-я по обычной схеме.
Мех-ая обработка дисков как и валов делится на черновой , чистовой и отделочные этапы.
Окончательная отделка дисков – полирование – выполняется перед нарезанием пазов или перед окончательным контролем.
Обработка дисков начинается с подрезки одного из торцев чистотой Rа 2,5 под у\зв. контроль.
Затем обтачивают кругом с оставленым припуском 2…3 мм. После черновой обр-ки диск подвергают закалки, отпуску или старению с проверкой качество металла на мех-ие св-ва по 2 или 1-й группе контроля. В процессе т\о диск коробится до 1 мм, что необх-мо учитывать припуском на послед-ю операцию.
При чистовой обр-ки необх-мо обес-ть концентричность всех цилиндр-х поверх-й для уменьшения дисбаланса относительно посадочного диаметра.
Фасонные, цил-ие пов-ти диска обраб-ся по контуру или по программе на ЧПУ.
В крупносерийном производстве для обеспечения концент-ти торцы диска обр-ся одновременно на спец-х станках с центр-ым приводом.
Пазы под лопатки протягиваются на вертикальных или гор-ых протяж-х станках. Торцевые шлицы диска компрессора фрезируют или протягивают круговыми протяжками. Прецензионные отверстия в дисках сверлят или разверт-т совместно с фланцами валов. Анодирование и оксид-ие дисков производят после окончательного контроля.
ПРИМЕРНЫЙ ПЛАН ОБРАБОТКИ ДИСКОВ.
1.обдирка заг-ки кругом с ост-ем припуска на сторону до 3 мм и подрезка одного из торцев с Ra2,5 для УЗК
2.УЗК
3.т\о-закалка + отпуск или старение
4.первая предварительная обработка диска кругом
5. вторая предварительная обработка диска кругом
6. чистовая обр-ка диска кругом
7. полирование торца диска с 2-х сторон и внутренние поверхности под травление
8. травление и промывка
9. сверление и развертывание отв-й в основании паза для фиксации лопатки (для дисков турбин)
10.фрезерование паза на торце диска для его фиксации при протягивании пазов под лопатки
11. протягивание и контроль пазов на образце и ложном диске (для дисков турбин)
12. протягивание пазов и контроль (типа елки или ласточ. хвоста)
13. слесарная обработка пазов и скосов
14. шабрение торцев и диска компрессора с прилеганием краске не менее 80%
15. чистовая проточка базовых полок и торцев с 2-х сторон по очереди (для дисков с торцевыми шлицами)
16. свер-ие отв-й в пазах для штифтов (фиксация лопаток)
17. фрезер-е торцевых шлицев для компрессора с 2-х сторон по очереди. Срезание фрезой одного шлица для фиксации диска.
18.полиров-е диска и окончат-й контроль
Выполнение основных операций.
1.токарная обработка диска производиться на ток.карус-х ст-х
2.елочные пазы протяг-т на гор-х и верт-х протяж-х ст.
3.лопатки отлитые за одно с диском обра-т электро-физич-ми или электро-хмикотерм. Обр. или фр. На ЧПУ. Лопатки у дискам ТНА иногда приваривают.
4. Контроль – все диски контролируются мех-м способом, оптикомех-м (просвечивают на экран при увеличении 50 раз)
елочные пазы – путем наложение световой тени на чертеж с увеличением в 50 раз.
Ширину пазов в дисках елочного профиля проверяют с помощью валика и калибров. В пазах ел-го профиля угловой клин проверяют угломером.
Обработка лопаток АД
Лопатки АД подразделяются:
1.Рабочие вращ-ся
2. Неподвижные: Направл-е
Спрямляющие
Сопловые
Лопатки АД бывают:
1. сплошные
2. с каналом для охлаждения
3. пустотелые
По способу изготовления лопатки АД делятся на: деформируемые (кованные, прессованные, чеканные, литые, сварные, паяные)
Перо лопаток имеет сложн. пространственную форму с постоянным или переменным профилем по высоте.
Сечения профиля могут быть повернуты относительно друг друга который может достигать 60о.
РИС
Перо сопловых лопаток турбин имеет сечение сопловых лопаток пост. или изм-ся по величине и углу закрутки до 100
У ТНА – ЖРД – перо лопаток сложного профиля с закруткой или без закрутки.
Перо лопаток компрессора имеет более сложную форму у 1 ступеней и больший угол закрутки до 600
Замок лопаток ГТД могут иметь форму елки, ласточкин хвост, Т-образное, вильчатое, грибовидное, бульбовидное строение.
Хвостовик (замок) елочного профиля у лопаток турбин.
У ТНА – бульбовидные.
Остальные бывают у компрессора.
Приварные лопатки не имеют замковой части.
Поверхности лопаток из Al сплавов подвергают хромовому анодированию.
А остальные лопатки покрываются хромом или никелем.
Для повышения жаростойкости сопловых лопаток рабочих турбин, их перо покрывают жаростойкими эмалями, алитируют или хромируют.
Лабиринтные канавки на торцах лопаток, протачивают в сборе с дисками для повышения точности.
Тех. Условия на лопатки
1. Отклонение формы профиля по корыту и спинке 0,01-0,03мм – для лопаток из деформир-ых сплавов и 0,25 для литых.
2. Отклонения максимальной толщины профиля от номинала не более 0.2 мм.
3. Допуск на толщину вых.кромки 0,1-0,4мм.
4. Допуск на угол закрутки пера в поперечном сечении 15/
5. Смещение контуров корыта и спинки, в направлении перпендикулярном к плоскости симметрии замка допускается для рабочих лопаток турбины 0,2-0,6мм.
Для лопаток компрессора 0,1-0,4
6. Допуск на толщину стенки пера, щелей и перемычек литых пустотелых лопаток 0,3мм
Шероховатость пера лопатки
Ra 0.63, Ra 1.25
Дата добавления: 2018-02-15; просмотров: 532; Мы поможем в написании вашей работы! |
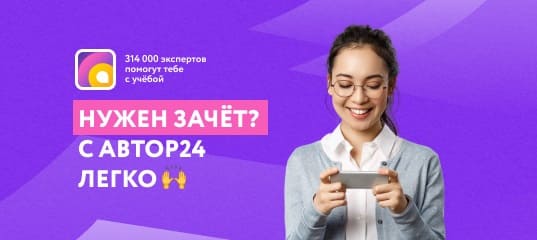
Мы поможем в написании ваших работ!