Теоретические основы и технология эксплуатационной обкатки
Поступающие в эксплуатацию машины после их изготовления или ремонта должны пройти эксплуатационную обкатку в целях приработки трущихся поверхностей деталей, создания условий минимальной скорости изнашивания. Такая скорость изнашивания определяется наличием в процессе работы стабильной прочной масляной пленки на поверхности трения при жидкостном или гидродинамическом режиме смазывания. Этот режим характеризуется коэффициентом трения (отношением силы трения к нагрузке, направленной по нормали к поверхности касания) 0,002.. .0,01. При полужидкостном режиме смазывания коэффициент трения увеличивается до 0,01 ... 0,20, при граничном — до 0,05 ... 0,40.
Неприработанные детали обычно отличаются непараллельностью поверхностей трения, значительной волнистостью, шероховатостью, микронеровностями, недостаточной площадью контакта. В связи с этим в процессе работы появляются большие удельные нагрузки, вызывающие повышенные механические потери, увеличение коэффициента трения, температуры деталей, уменьшение вязкости смазочного материала, а значит
и толщины масляной пленки. Это может привести к полужидкостному, граничному режиму смазывания и даже к работе деталей с несмазанными поверхностями. В результате наблюдаются задиры и значительный приработочный износ до конца приработки поверхностей трения. Особенно большой приработочный износ происходит после перекомплектовки деталей при обезличенном ремонте узлов и агрегатов.
|
|
В процессе правильной эксплуатационной обкатки в течение 30...60 ч (заводскую обкатку машины проводят после сборки на заводе-изготовителе или на ремонтном предприятии) поверхности трения становятся более параллельными, постепенно уменьшается их волнистость, шероховатость, высота микронеровностей, увеличивается площадь контакта. В результате резко уменьшаются удельные нагрузки, механические потери, коэффициент трения, стабилизируемся нормальная температура, вязкость, толщина масляной пленки. Таким образом, после эксплуатационной обкатки детали начи-
22
нают работать в благоприятных стабилизированных условиях. Правильная обкатка отличается достижением стабилизированных
условий работы деталей при малом приработочном их износе. В том случае, если стабилизированные условия работы появились после большого приработочного износа, ресурс деталей и сопряжений значительно сокращается. Особенно это заметно на перекомплектованных при обезличенном ремонте соединениях, ресурс которых в результате послеремонтной приработки обычно сокращается на 20 процентов и более.
|
|
Приработочный износ характеризуется показателем приработки П [формула (1.1)]. Обычно эта величина колеблется в пределах 0 .. 0,07uп, где и п
— предельный износ.
Приработочный износ деталей после обезличенного ремонта увеличиваетя, как правило, в 1,5.. 2 раза.
В целях достижения стабилизированных условий работы деталей при небольшом приработочном их износе в процессе эксплуатационной обкатки придерживаются основного принципа: обеспечение постепенного возрастания нагрузок: тяговых, скоростных, температурных и т, п.
Например, при эксплуатационной обкатке трактора вначале работают на нем без нагрузки, в течение 1,5... 2 ч, затем с 25% нагрузкой в течение 4,5... 6 ч, с 50% нагрузкой в течение последующих 9... 12 ч, наконец, с 75% нагрузкой в течение 15... 20 ч. При каждой нагрузке трактор работает на различных передачах.
Во время обкатки особенно внимательно следят за работой дизеля, состоянием температурного режима работы систем, за показаниями контрольных приборов. Периодически прослушивают и осматривают дизель, трансмиссию, ходовую систему и др.
Нагрузку создают путем агрегатирования трактора боронами, культиваторами, сеялками и другими машинами, не требующими больших тяговых усилий. После обкатки трактора проводят соответствующее ТО.
|
|
23
Обоснование периодичности технического обслуживания и допускаемых значений параметров машин
Существует несколько критериев (показателей), по которым устанавливают периодичность ТО:
по максимальной производительности машины; по среднему значению наработки между отказами; по минимальным удельным издержкам; по минимальной вероятности отказа и др.
Метод определения периодичности ТО по максимальной производительности основан на том,что с течением времени в результатеразрегулированиями износа соединений производительность машины (мощность двигателя) уменьшается.
Геометрически это можно представить в виде наклонной прямой, характеризующей уменьшение мощности, под определенным углом к оси времени (абсцисс). При Техническом обслуживании показатели восстанавливают. Чем чаще выполняют техническое обслуживание, тем Меньше снижается мощность двигателя, тесно связанная с производительностью машины.
Однако по мере увеличения числа технических обслуживании растет простой машины в течение периода работы —- tтo, вызванный восстановлением мощности двигателя.
|
|
В этом случае существует оптимальный интервал времени моеду обслуживанием tмопт.
Недостаток такого метода заключается в, том, что он не учитывает рассеивание случайной скорости снижения мощности или производительности однотипных машин.
Определение периодичности ТО по среднему значению наработки между отказами устраняет этот недостаток путем учета как среднейнаработки Тор, так и среднего квадратического ее отклонения σ. Если принять
в качестве периодичности ТО среднее значение наработки, то 50% машин к этому моменту окажет, то есть обслуживание окажется поздним. В этой связи есть необходимость проводить ТО раньше
24
ка величину, равную среднему квадратическому отклонению
наработки между отказами: | |
tм = Тcp - σ. | (2.1) |
При нормальном законе распределения наработки между отказами, не-50; а 13,5% машин откажут, остальным же будут предупредительно проведены операции ТО. Естественно, такой метод является приближенным, так как в одних случаях, когда издержки, вызванный устранением последствий отказа, велики, периодичность окажется завышенной, а когда малы — заниженной.
Метод обоснования периодичности ТО по критерию. минимума удельных издержек устраняет упомянутый недостаток.Кроме того,этотметод позволяет одновременно устанавливать допускаемое значение параметра, зависящее от периодичности. Ведь, изменяя периодичность» необходимо в обязательном порядке изменять и соответствующее допускаемое значение параметра.
Функция оптимизации периодичности контроля и, при необходимости, восстановления параметра, а также его допускаемого значения в простейшем случае имеет вид
где А, С, В — соответственно средние издержки на устранение последствий отказа с учетом потерь от простоя машины, на предварительное восстановление параметра и на его контроль, руб.; Q(D, t M )—вероятность отказа по параметру в зависимости от его допускаемого отклонения D от номинального значения и межконтрольной наработки t м . Эту вероятность определяют в течение средней фактически используемой наработки (ресурса) до отказа или восстановления, зависимой также от D и t M , величины — Тср (D, t м ) в ед.наработки; К п (D, in)— число проверок составной части измерения параметра втечение Тср (D, tM).
Первое слагаемое в фигурных скобках равно вероятным удельным издержкам на устранение последствий отказа, второе слагаемое — удельным издержкам на предупредительное восстановление параметра, третье—: на измерение параметра. Изменяя технические требования D и t м , устанавливают искомый минимум издержек. При этом D и t M будут оптимальными.
25
Рис. 2.1. Влияние допускаемого отклонения и межконтрольной наработки параметра на вероятности отказа и предупредительной замены элемента
Рассмотрим расширяющийся пучок прямых, характеризующих отклонение параметра (производительность, мощность, расход газов, прорывающихся в картер двигателя, и др.) от номинального его значения со случайной скоростью изнашивания (рис. 2.1). Пересечение пучка прямых с ординатой и п , соответствующей предельному отклонению, формирует непрерывную плотность распределения наработки между отказами составной части по параметру. При наличии допускаемого отклонения параметра D случайная величина наработки становится дискретно непрерывной. Дискретность появляется вследствие замены (регулирования или другого
26
восстановления номинального значения параметра) составной части с отклонением параметра больше D в момент контроля tм, 2tм, 3tм и т. д. Составные части должны были отказывать в интервалах t M... t(1), 2tм … t(2), 3tм... t(3). Однако после контроля (диагностирования) при техническом обслуживании их предупредительно заменяют или ремонтируют.
Составные части, отклонения параметров состояния которых меньше допускаемого, отказывают далее по достижении предельного отклонения вследствие относительно большой скорости изменения параметра (изнашивания). Вероятность отказа таких составных частей соответствует заштрихованным площадям, ограниченным кривой распределения наработки между отказами φ(t) и интервалами t(1)…2tм, t(2)…3tм, а также штриховыми линиями изменения параметра.
По мере увеличения D и приближения ее к и п вероятность предупредительной замены уменьшается, а вероятность отказа (заштрихованная площадь) растет. При допускаемом отклонении зазора, равном предельному, вероятность отказа становится равной единице, а степень использования наработки между отказами составляет 100%.
Таким образом, изменяя периодичность контроля или межконтрольную наработку t м и D, можно увеличить или уменьшитьвероятность отказа, расход запасных частей в 2... 3 и более раз, тем самым управлять техническим состоянием машин согласно функции (2.2).
Анализируя график на рисунке 2.1, можно вывести формулу вероятности отказа в зависимости от технических требований tм и D при линейном изменении параметра. Если плотность распределения ресурса — φ(t) то вероятность отказа в i-м эксплуатационном периоде
где из подобия треугольников | (2.3) | |
ti-1= (Uп/D) (i — 1)tM; i = 1, 2, ...n1. | (2.4) |
При i=1 величина ti-1 = 0. Отказы наблюдаются при условии, что верхний предел интеграла (2.3) больше нижнего. С увеличением i эта разность убывает. Послед-
27
ний эксплуатационный период, в котором будет наблюдаться отказ,
(2.5) Здесь квадратные скобки указывают на то, что следует брать целую
часть числа.
Вероятность отказа составной части по параметру в зависимости от его допускаемого отклонения и периодичности контроля
(2.6)
В случае универсальной степенной функции изменения параметра (1.2) при Z(t)=0 (рассматриваются плавные кривые)
(2.7)
При нормальном распределении ресурса и <х=1
(2.8)
где F 0 — индекс нормированной и центрированной функции нормального распределения наработки между отказами при D=uп; T 0 , σ 0 — параметры распределения этой функции — среднее значение и среднее квадратическое отклонение наработки в единицах t м .
Число проверок составной части в течение наработки ГСр (D, 4 Ы ) определяют по формуле
(2.9) Для облегчения расчетов обычно используют номограммы или таблицы, по которым определяют члены функции (2.2). На рисунках 2.2, 2.3
и 2.4 даны номограммы для определения вероятности отказа Q(D, t м ), средней фактически используемой наработки T cp (D,t м ) и оптимальных периодичности контроля и допускаемого значения параметра составной части при гладких кривых изменения параметра, описываемых степенной функцией (1.2) при Z(t)=Q. В целях универсальности номо-
28
Рис. 2.2. Номограмма для определения вероятности отказа элемента за срок его службы в зависимости от допускаемого отклонения и межконтрольной наработки его параметра состояния
Рис. 2.3. Номограмма для определения фактически используемого ресурса элемента в зависимости от допускаемого отклонения и межконтрольной наработки его параметра состояния
29
Рис. 2.4. Номограмма для определения оптимальных допускаемого отклонения и межконтрольной наработки параметра состояния элемента
30
грамм исходные и выходные данные представлены в безразмерном виде: D 0 = D/u n ; v = σ/T cp ; T 0 =T CP /t M ;
T 0 (D,t M ) = T cp (D,t M )/t м ; А0=А/С; В 0 = В/С, | (2.10) |
где v — коэффициент вариации наработки между отказами (ресурса) составной части по параметру при D = u п .
Для определения абсолютной оптимальной периодичности /мопт используют отношение
t м опт = Т ср /Т 0 , | (2.11) |
где Т0 находят по номограмме на рисунке 2.4.
Для определения абсолютного оптимального значения параметра (переход от нормированного в единицах uп отклонения к абсолютному значению) используют выражение
1Ъопт=|Пн±(/>ооптЫп+ЛП|, (2.12)
где ПDопт, Пн — оптимальное допускаемое и номинальное значения параметра, ед.
параметра; П — показатель, характеризующий приработку составной части, ед.
Знак « + » применяют, когда параметр с течением времени увеличивается, знак «—» — когда параметр составной части уменьшается. Прямые скобки в (2.9) и (2.12) указывают на то, что следует брать в первом случае целую часть, а во втором положительную величину результата.
Абсолютное оптимальное допускаемое значение диагностического параметра ПDопт при линейной его зависимости от структурного вычисляют по формуле
ПDопт = а + bПDопт , | (2.13) |
где а и b — коэффициенты, характеризующие связь диагностического параметра со структурным.
При пользовании номограммой для определения вероятности отказа соблюдают условие
Q(D0<0,5α)=Q(D0 = 0,5α). | (2.14) |
Средние издержки на устранение последствий отказов | |
A=C + C 3 + K н t доп C ч.с l+t п C ч.n , | (2.15) |
где С3—затраты на поиск и доставку запасных частей к месту устранения последствий отказа или доставку машины к месту ре-
31
Дата добавления: 2021-04-24; просмотров: 117; Мы поможем в написании вашей работы! |
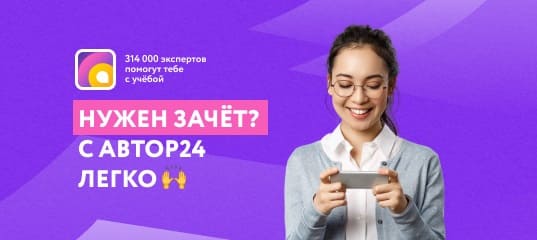
Мы поможем в написании ваших работ!