Высокоэнергетические методы штамповки
Последние десятилетия характеризуются быстрым развитием производства крупногабаритных машин и механизмов. Изготовление элементов конструкций размерами 3–10 м потребовало создания новых беспрессовых методов штамповки ввиду ограниченных возможностей механических и гидравлических прессов.
В качестве таких методов были созданы и применены на практике высокоэнергетические методы формообразования под действием импульсивных нагрузок, создаваемых взрывом брезантных взрывчатых веществ, газовых смесей, давлением испаряющихся сжиженных газов, высоковольтным электрическим разрядом в жидкости, мощными импульсами магнитного поля.
Особенностью высокоэнергетических импульсных методов штамповки является высокая скорость деформирования в соответствии с высокими скоростями преобразования энергии. Поэтому высокоэнергетические методы штамповки именуются высокоскоростными методами. Они получили преимущественное применение при изготовлении крупногабаритных деталей типа днищ, полусфер, оболочек и других, изготовляемых малыми сериями, когда использование прессов и штампов становится технически нецелесообразным и экономически невыгодным.
Импульсные методы обработки металлов имеют место в самых разнообразных процессах штамповки: при вытяжке, листовой формовке, формоизменении трубчатых заготовок, вырубке и пробивке отверстий, резке труб и проката, объемной штамповке, калибровке и поверхностном упрочнении металла, прессовании, сварке разнообразных металлов, запрессовке и развальцовке труб, различных сборочных операциях.
|
|
Взрывная штамповка основана на деформации заготовки давлением ударной волны, образующейся при взрыве брезантных взрывчатых веществ (ВВ), при этом время деформации детали исчисляется миллисекундами.
Взрывная штамповка получила преимущественное применение для обработки крупных деталей (1,5–8 м) при толщине материала свыше 2 мм. Достоинством ее является высокая экономическая эффективность в результате резкого снижения капитальных затрат и сокращения сроков и стоимости подготовки производства. Другое преимущество – возможность штамповки деталей из высокопрочных сплавов.
В зависимости от размеров и формы деталей взрывная штамповка осуществляется следующим образом: при больших габаритах деталей – в бассейнах с водой или бронекамерах; при небольших размерах деталей – в наземных установках.
Наряду со взрывной штамповкой применяют способ формовки высоковольтным электрическим разрядом в воде. Энергия, необходимая для электрического разряда, накапливается в высоковольтной конденсаторной батарее (35–40 кВ). Накопленная энергия (от 30 до 120 кДж) создает между электродами мгновенный разряд длительностью 10-5 с, что приводит к мгновенному испарению некоторого объема воды и расширению образовавшегося пара, который вызывает ударную волну в жидкости, в результате чего происходит деформация заготовки.
|
|
Электрогидравлическая штамповка имеет ряд преимуществ перед взрывной штамповкой: 1) лучшую управляемость процессом за счет варьирования количества импульсов и месторасположения разрядных контуров: 2) возможность изменения энергии и осуществления многократного разрядного импульса; 3) размещение электрогидравлических установок в производственных помещениях.
Электрогидравлической штамповкой осуществляют вытяжку, листовую формовку, отбортовку, растяжку полых деталей, пробивку отверстий, развальцовку труб и т. п. Наиболее перспективно применение электрогидроимпульсной штамповки для изготовления крупногабаритных деталей размерами от 400´400 до 1300 ´1800 мм. Электрогидравлической обработке подвергаются различные, в том числе труднодеформируемые, металлы и сплавы.
Установки для штамповки высоковольтным электрическим разрядом состоят из источника питания, включая высоковольтный трансформатор с выпрямительным устройством, конденсаторной батареи, разрядника и технологической установки, состоящей из матрицы, прижимного устройства, электродов, вакуум-насоса.
|
|
Магнитно-импульсная штамповка (МИШ) основана на мгновенном разряде электроэнергии, накопленной в конденсаторной батарее, через соответствующий индуктор, являющийся рабочим органом. При этом в цепи индуктора протекает импульс тока, а в окружающем индуктор пространстве возникает импульсное магнитное поле высокой напряженности. Это магнитное поле индуцирует вихревые токи противоположного направления в металлической заготовке, помещенной вблизи индуктора. При взаимодействии мощного поля индуктора с индуцированным в заготовке током и его магнитным полем возникают электромеханические силы взаимодействия, стремящиеся оттолкнуть заготовку от индуктора и вызывающие ее деформацию. МИШ получила довольно широкое применение в промышленности при выполнении различных операций листовой штамповки: вытяжки, вырубки, пробивки отверстий, отбортовки, развальцовки труб, запрессовки штуцеров, обжатия труб и наконечников на тросах, сборки трубчатых деталей с оправками и т. п. Этот способ имеет ряд преимуществ перед другими высокоэнергетическими методами:
|
|
· повышенную точность штампуемых деталей; сравнительно
высокую производительность процесса; возможность точного дозирования мощности импульсного разряда путем применения конденсаторов различной емкости, автоматизации и встраивания магнитно-импульсных установок в производственный процесс;
· возможность выполнения сборочных операций, а также де-
формирования заготовок за несколько разрядных импульсов, причем первые импульсы служат для разогрева заготовки и повышения ее пластических свойств.
Магнитно-импульсные установки конструктивно просты, не имеют движущихся и трущихся частей и поэтому надежны в эксплуатации.
Холодная штамповка, применявшаяся вначале только в крупносерийном и массовом производствах, в настоящее время получила широкое распространение в мелкосерийном производстве, в серийном производстве с неустойчивой, часто изменяющейся номенклатурой деталей и даже при изготовлении опытных деталей. Это стало возможным в результате применения универсальных или простых и дешевых штампов и внедрения штамповки по элементам.
Внедрение холодной штамповки в мелкосерийном производстве взамен малопроизводительной ручной обработки приводит к значительному экономическому эффекту, заключающемуся в резком снижении трудоемкости по сравнению с ручной обработкой деталей, в уменьшении расхода материала и снижении массы штампуемых деталей, в увеличении производительности и снижении себестоимости деталей.
В мелкосерийном производстве получили применение следующие процессы листовой штамповки: 1) на универсальных переналаживаемых штампах, предназначенных для изготовления подобных однотипных деталей разных размеров; 2) по элементам на универсальных быстропереналаживаемых штампах; 3) на координатно-револьверных пробивных прессах; 4) на прорезных прессах и обрабатывающих центрах; 5) на универсально-сборных штампах;
6) полиуретаном.
Универсальные штампы давно применяются в серийном и мелкосерийном производствах и предназначены для отрезки, пробивки, надрезки, обрезки и гибки деталей, различающихся своими размерами. На этих штампах изготовляют детали из полосы, ленты, прутка и профильных заготовок.
Рис. 38. Схема штамповки по элементам
Метод штамповки по элементам, разработанный заслуженным изобретателем РСФСР В.М. Богдановым, заключается в том, что контур штампуемой детали расчленяется на простейшие элементы (прямые участки, закругления, пазы, скосы, отверстия и т. п.), выполняемые на заготовке последовательно при помощи набора различных штампов, каждый из которых может штамповать один или группу элементов контура (рис. 38).
В мелкосерийном производстве штамповка по элементам универсальными штампами позволяет отказаться от изготовления ряда специальных штампов, что дает большую экономию и значительно сокращает сроки подготовки производства. В случае изменения размеров деталей вместо переделки штампов требуется лишь переналадка универсальных штампов.
При листовой штамповке в условиях мелкосерийного производства осуществляется штамповка на координатно-револьверных пробивных прессах деталей типа плат, панелей, шасси приемников с большим числом отверстий и пазов разных форм и размеров. Изготовление таких деталей на координатно-револьверных пробивных прессах заключается в последовательной штамповке отверстий или других элементов при помощи набора сменных штампов, устанавливаемых в револьверной головке пресса. Обрабатываемая заготовка подается на рабочую позицию при помощи координатного устройства, управляемого вручную или автоматически при помощи программного управления. Координатно-револьверный пресс позволяет штамповать не только отверстия, но и наружные элементы листовых деталей: пазы, срезы, закругления, ребра жесткости, жалюзи, а также неглубокую отбортовку.
Дата добавления: 2021-07-19; просмотров: 129; Мы поможем в написании вашей работы! |
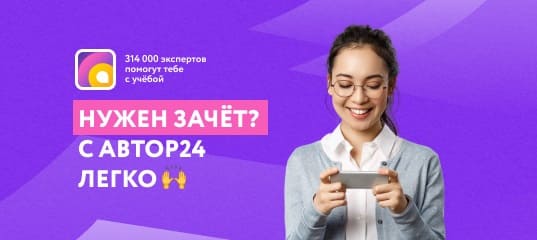
Мы поможем в написании ваших работ!