Рекомендации по проектированию чертежа поковки на процессы объемной штамповки
Проектирование поковок
12.11.2018
Источник : https://extxe.com/1383/proektirovanie-pokovok/
Содержание
1. Обработка металлов давлением в современном машиностроении
2. Прокатка
3. Ковка
4. Горячая объемная штамповка
5. Выдавливание
6. Рекомендации по проектированию чертежа поковки на процессы объемной штамповки
7. Вальцовка
8. Штамповка на радиально-обжимных и ротационно-ковочных машинах
9. Раскатка и накатка
10. Калибровка
11. Листовая штамповка
12. Высокоэнергетические методы штамповки
Обработка металлов давлением в современном машиностроении
В современной металлообрабатывающей промышленности обработка металлов давлением является одним из основных способов формообразования деталей машин различного назначения. Примерно 90 % стали и более 55 % цветных сплавов, выплавляемых в России, подвергаются обработке давлением.
Все процессы обработки металлов давлением основаны на способности металлических материалов в твердом состоянии устойчиво изменять форму и размеры под действием приложенных внешних сил, т. е. пластически деформироваться. Обработка металлов давлением существенно отличается от других видов обработки, так как в процессе пластической деформации металл не только приобретает требуемую форму, но и меняет свою структуру (форму и размеры зерен, характер распределения неметаллических включений, возникновение направленности макроструктуры) и физико-механические свойства.
|
|
Несмотря на многообразие процессов обработки давлением, их можно объединить в две основные группы – процессы металлургического и машиностроительного производства.
К первой группе относятся прокатка, прессование и волочение, т. е. процессы, в основе которых лежит принцип непрерывности технологического цикла. Продукцию металлургического производства (листы, полосы, ленты, периодический и профильный прокат, трубы, профили, проволоку и т. п.) используют как заготовку в кузнечно-штамповочных и механических цехах и как готовую продукцию для создания различного рода конструкций.
Во вторую группу входят ковка, объемная штамповка (горячая и холодная), листовая штамповка и специальные виды обработки давлением (калибровка, раскатка кольцевых деталей, редуцирование, обкатка, раздача и т. д.). Эти процессы обеспечивают получение заготовок изделий (деталей) и готовых деталей, не требующих последующей механической обработки. Возможность использования высоких, сверхвысоких скоростей деформирования, небольшое число необходимых, относительно несложных технологических операций обусловливают кратковременность технологического процесса, высокую производительность и сравнительно низкую себестоимость получаемой продукции. Кованые и штампованные заготовки (поковки) отличаются высокими механическими свойствами, что обеспечивает надежность и долговечность выпускаемой продукции, поэтому наиболее ответственные, тяжело нагруженные детали машин изготавливают из заготовок, полученных ковкой или штамповкой.
|
|
Как указывалось ранее, все процессы обработки металлов давлением основаны на возможности материалов пластически деформироваться. Поэтому обработке давлением могут подвергаться, как правило, те металлы и сплавы, которые обладают необходимым запасом пластичности, обеспечивающим деформирование без нарушения сплошности материала, т. е. без его разрушения. Пластичность не является неизменным, наперед заданным свойством материала – на нее оказывает влияние ряд факторов: химический состав материала, температура и скорость деформации, форма очага деформации и т. п. Создавая соответствующие условия деформирования, можно получить требуемую технологическую пластичность.
В зависимости от температуры и скорости деформации различают холодную и горячую деформации.
Холодная деформация происходит при таких температурноскоростных условиях, когда в материале протекает только один процесс – упрочнение (или наклеп) металла. В этом случае образуется волокнистая структура, резко повышается прочность и снижается пластичность материала. При холодной деформации может возникнуть преимущественная ориентация кристаллографических осей зерен, образуется так называемая текстура, что является причиной повышения анизотропии механических свойств материала.
|
|
Различают два вида анизотропии:
1. начальную (или исходную), существующую до деформирования и объясняющуюся анизотропией свойств монокристаллических материалов; поликристаллические материалы (к ним относятся большинство металлов, подвергаемых обработке давлением) могут быть изотропными вследствие большого числа монокристаллических, хаотично расположенных зерен;
2. вторичную (или деформационную), изменяющуюся или заново возникающую в процессе деформации.
Анизотропия, возникающая в процессе деформации, может оказывать как полезное, так и вредное влияние на свойства материала. Анизотропия механических свойств листовых материалов способствует образованию «фестонов» при получении деталей глубокой вытяжкой, хрупкому разрушению рекристаллизованного тугоплавкого листового металла и другим видам дефектов. Однако механическая анизотропия может противодействовать хрупкому разрушению конструкций; направленность магнитных свойств материалов для трансформаторных сердечников, возникающая в результате прокатки трансформаторной стали, а также зависимость штампуемости листового материала от текстурного упрочнения свидетельствуют о полезном влиянии анизотропии.
|
|
Горячая деформация осуществляется при таких температурноскоростных условиях обработки, когда в материале протекают одновременно два процесса: наклеп и рекристаллизация (упрочнение и разупрочнение), причем скорость разупрочнения равна или выше скорости упрочнения. При горячей деформации улучшаются все механические свойства материала: и прочностные, и пластические, особенно повышается ударная вязкость. После горячей деформации, как правило, микроструктура равноосная, мелкозернистая, макроструктура волокнистая. Образование волокнистой макроструктуры при горячей деформации – полезное явление, особенно при изготовлении ответственных деталей (турбинных дисков, валов, роторов и т. п.). Используя определенные операции ковки (например, осадку, протяжку), можно получить макроструктуру, совпадающую с направлением максимальных напряжений в детали при ее эксплуатации.
Современное машиностроение в условиях развивающейся технической революции характеризуется быстрым ростом масштабов производства и производительности труда при все более строгой оптимизации применяемых конструктивных и технологических решений.
Оптимизация конструктивных и технологических решений, в свою очередь, дает толчок к созданию так называемого конструктивного и технологического множества, без чего невозможен выбор оптимальных решений в разнообразных условиях производства.
Поэтому насыщение производства большим числом новых и совершенствование существующих технологических процессов является характерным условием развития современного машиностроения. Особенно ярко это обстоятельство проявляется в области обработки металлов давлением, для которой в настоящее время насчитывается около 400 способов объемного формообразования.
Рассмотрим основные способы получения штучных заготовок.
Прокатка
Во многих случаях, когда требуются высокие прочность и пластичность, применяют заготовки из сортового и специального проката. В процессе прокатки нагретые до температуры деформирования литые заготовки подвергают многократному обжатию в валках прокатных станов, в результате чего значительно повышается плотность материала за счет «залечивания» литейных дефектов – пористости, микротрещин и т. п. Это придает заготовкам из проката высокие прочность и герметичность даже при небольшой их толщине. При поперечно-винтовой прокатке в винтовых калибрах непрерывное формообразование осуществляется путем перемещения обрабатываемого тела между вращающимися валками, на поверхности которых по винтовой линии нарезаны ручьи (рис. 9). В результате этого длинная цилиндрическая заготовка, двигаясь непрерывно, деформируется на небольшом участке в относительно короткие тела вращения заданной конфигурации. Таким способом получают, в частности, шары.
Исходным материалом для изготовления мельничных шаров служат прутки круглого поперечного сечения из углеродистой стали диаметром на 1–3 мм меньше диаметра шара, а для получения заготовок шаров подшипников качения – прутки из стали ШХ15.
Передний конец предварительно нагретой заготовки толкателем подается в непрерывно вращающиеся валки. Высота винтовой реборды валков от начала калибра плавно увеличивается, вследствие чего заготовка, захваченная валками, продвигаясь вдоль оси калибра, постепенно обжимается, приобретая форму шара, соединенного перемычкой с остальной заготовкой. Затем шар отделяется
от заготовки и обкатывается в калибре. При этом поверхность шара проглаживается, а остаток перемычки закатывается и из валков выбрасывается полностью сформованный шар.
Рис. 9. Схема поперечно-винтовой прокатки
Прокатанные заготовки шаров имеют точную форму, а их диаметры изменяются в пределах 0,2–0,3 мм. Точные размеры, хорошее качество поверхности и малая глубина обезуглероженного слоя позволяют сократить припуск на шлифование шаров до 0,5–0,7 мм на сторону.
Прокаткой в винтовых калибрах можно получать не только шары, но и другие тела вращения, например втулки, иглы для игольчатых подшипников.
Прокатка цилиндрических изделий в винтовых калибрах находит применение и при получении заготовок, используемых в автоматических линиях, особенно для изделий из хрупких или очень пластичных материалов, когда традиционные способы резки мерных заготовок не могут обеспечить ровные торцы в заготовках.
Круглые изделия с переменным по длине диаметром применяются во многих отраслях машиностроения. К таким изделиям относятся полуоси, валы, шпиндели и т. п. Обычные способы изготовления заготовок этих деталей токарной обработкой или штамповкой вызывают большие потери металла (до 25–35 %) в стружку или на заусенцы и в то же время являются малопроизводительными. Наиболее целесообразным способом получения заготовок для таких деталей является поперечно-винтовая прокатка на трехвалковых станах. Этот способ состоит в том, что три приводных валка 1 (рис. 10) вращают заготовку 2, которая принудительно перемещается в осевом
направлении со значительным натяжением, создаваемым натяжным устройством через свободно вращающийся патрон 3, захватывающий передний конец заготовки.
Во время прокатки валки сближаются и разводятся на требуемый размер гидравлической следящей системой в соответствии с заданным профилем сменной копировальной линейки или путем числового программного управления по заранее заданной программе.
На трехвалковых станах можно получать прокат, имеющий любую форму, состоящую из соосно расположенных цилиндрических, конических, сферических или других поверхностей вращения. Трехвалковые станы имеют сравнительно малые установочные мощности, занимают меньше производственной площади, проще в эксплуатации и при ремонте.
Рис. 10. Схема стана для поперечно-винтовой прокатки профилей круглого сечения
По сравнению с другими способами получения аналогичных деталей поперечно-винтовая прокатка профилей переменного сечения имеет следующие преимущества:
· экономию металла до 15–30 %;
· возможность полной механизации и автоматизации процесса получения заготовок, начиная от загрузки заготовок в приемную часть нагревательного устройства до получения готового периодического проката;
· переход от одного профиля заготовки к другому без замены вал-
ков, только за счет смены копира или программы (это позволяет прокатывать широкий сортамент заготовок при малом парке инструмента);
· простоту в переналадке стана к выпуску нового типоразмера проката (это дает возможность использовать способ для получения заготовок в условиях мелкосерийного производства);
· низкую стоимость и малый расход инструмента при изготовлении
деталей по сравнению со штамповкой.
Примеры параметров сортаментов сталей и примеры их обозначения приведены в прил. 7.
Ковка
Ковка возникла еще в бронзовый век, когда вручную получали сначала изделия из меди, а затем из самородного метеоритного железа. С развитием металлургии бронзы и железа ковка получила широкое распространение. В настоящее время область применения ковки сокращается, но в ряде случаев ковка по-прежнему остается наиболее экономичным способом получения деформированных заготовок.
При ковке формоизменение происходит вследствие течения металла в стороны, перпендикулярные к движению деформирующего инструмента-бойка. Применяемый при ковке инструмент создает значительное сопротивление течению металла при деформировании, что и отличает ковку от других видов обработки давлением, причем это течение ограничено лишь трением на контактной поверхности инструмент – деформируемый металл.
Применение ковки для получения заготовок объясняется рядом ее преимуществ по сравнению с другими видами обработки:
1. возможность изготовления крупногабаритных поковок массой несколько сотен тонн, получение которых другими способами невозможно, причем при обработке таких поковок используется сравнительно маломощное оборудование, так как обработка ведется деформированием отдельных участков заготовки;
2. применение универсального оборудования и универсальной оснастки позволяет получать поковки широкого ассортимента;
3. в процессе ковки значительно улучшается качество металла, повышаются его механические свойства, особенно пластичность и ударная вязкость.
Основные недостатки ковки следующие: низкая производительность, значительная трудоемкость изготовления поковок, особенно на прессах; большие напуски, припуски и допускаемые отклонения размеров поковки, что приводит к увеличению объема механической обработки и расхода металла.
Ковка является рациональным и экономически выгодным процессом получения качественных заготовок с высокими механическими свойствами в условиях мелкосерийного и единичного производств. Ковкой изготавливают самые разнообразные поковки, масса которых находится в пределах от нескольких десятков граммов до сотен тонн. Наиболее ответственные детали, такие как валы и диски турбин, роторы, коленчатые валы судовых двигателей, барабаны котлов высокого давления и т. п., к которым предъявляются высокие требования по качеству металла и механическим свойствам, изготавливают из поковок.
Ковка осуществляется при температурах горячей деформации, поэтому для такого вида обработки применяют все стали и сплавы, используемые при обработке металлов давлением. Шероховатость поверхности поковок, полученных ковкой, не превышает Rz = 80–
320 мкм. При использовании подкладных штампов шероховатость
поверхности поковок может быть доведена до Rz = 80/40 мкм. Коэффициент весовой точности поковок не превышает 0,3–0,4, что вызывает большой объем механической обработки. Поэтому в условиях мелкосерийного производства целесообразно применять несложные подкладные штампы, групповую или секционную штамповку. Для снижения расхода металла при партиях более 30–50 поковок одного наименования рекомендуется применять подкладные открытые или закрытые штампы (рис. 11). В этом случае возможно получение без напусков поковок относительно сложной формы с припусками и допусками примерно на 15–20 % ниже, чем при ковке на универсальном инструменте. Подкладные штампы можно применять для получения поковок массой до 150 кг, но преимущественно подкладные штампы применяют для поковок массой до 10–15 кг.
Как видно из данных, приведенных на рис. 11, применение подкладного штампа позволило повысить коэффициент весовой точности и улучшить качество поковки за счет более рационального
распределения металла, уменьшить объем механической обработки и снизить стоимость получения готовой детали.
Рис. 11. Поковки, получаемые ковкой (а) и в подкладных штампах (б)
Горячая объемная штамповка
Этот способ наиболее распространен для получения качественных заготовок. Горячей объемной штамповкой получают заготовки для ответственных деталей автомобилей, тракторов, сельскохозяйственных машин, железнодорожных вагонов, самолетов, металлообрабатывающих станков, швейных машин и т. д. Более 65 % массы всех поковок и до 20 % массы деталей большинства машин изготавливаются из заготовок, полученных горячей объемной штамповкой. Этот способ штамповки наиболее эффективен при массовом, крупносерийном и серийном производствах деталей массой от нескольких граммов до нескольких тонн (примерно до 3 т). Наиболее целесообразно изготовление штамповкой поковок массой не более 50–100 кг.
По сравнению с ковкой горячая объемная штамповка имеет следующие преимущества:
· поковки, изготавливаемые штамповкой, имеют более сложную форму и лучшее качество поверхности; шероховатость поверхности Rz = 20–80 мкм, а при применении холодной калибровки Rz = 1,6–10 мкм;
· поковки можно получать со значительно меньшими допусками, чем при ковке, а при точной штамповке допуски можно довести
до долей миллиметра и подвести под классы точности, получаемые при обработке резанием; припуски снижаются в два-три раза (как правило, механической обработке подвергаются только сопрягаемые поверхности);
· значительно повышается производительность труда (десятки
и сотни поковок в час);
· за счет наличия в конструкции штамповочного оборудования выталкивателей штамповочные уклоны значительно меньше, чем при получении штамповок на молотах.
К недостаткам горячей объемной штамповки относятся:
· ограничения по массе получаемых поковок;
· дополнительный отход металла в заусенец, масса которого составляет от 10 до 30 % от массы поковки;
· для горячей объемной штамповки требуются бо́льшие усилия
деформирования, чем для ковки;
· инструмент (штамп) является более сложным и дорогим, чем универсальный инструмент (штамп) для ковки.
Горячая объемная штамповка подразделяется на различные виды в зависимости от типов штампа, оборудования исходной заготовки, способа установки заготовки в штампе и т. п. Остановимся только на факторах, которые определяют конфигурацию поковки и точность ее изготовления, т. е. на типах штампов и оборудования.
В зависимости от оборудования имеются следующие виды объемной штамповки: на штамповочных паровоздушных молотах двойного действия, кривошипных горячештамповочных прессах (КГШП), горизонтально-ковочных машинах (ГКМ), гидравлических прессах, высокоскоростных молотах и на специальных машинах (ковочные вальцы, горизонтально-гибочные машины – бульдозеры, ротационно-обжимные и радиально-обжимные машины, электровысадочные машины, раскатные машины).
Для изготовления одних и тех же деталей применяют различное оборудование, при этом можно значительно изменять конфигурацию поковки, размеры припуска и допуска, напуски и точность изготовления.
В зависимости от типа штампа штамповка подразделяется на следующие виды: в открытых штампах (рис. 12, а); в закрытых штампах (рис. 12, б); в штампах для выдавливания.
Перечисленные типы штампов применяют практически при штамповке на всех типах оборудования. Вид штампа определяет течение металла, т. е. конфигурацию поковки, поэтому данную классификацию штамповки можно считать основной.
Рис. 12. Схема открытой (а) и закрытой (б) штамповки
Штамповка в открытых штампах характеризуется тем, что штамп в процессе деформирования остается открытым (рис. 13, а). Зазор между подвижной и неподвижной частями штампа является переменным, в него затекает (выдавливается) металл при деформировании, образуя заусенец, т. е. технологический припуск, размеры которого рассчитывают при проектировании технологии в зависимости от размеров поковки. Основное назначение этого заусенца
– компенсация колебаний исходных заготовок по массе. Этот тип штампа можно применять для деталей любой конфигурации. Однако наличие заусенца увеличивает расход металла, кроме того, для обрезки заусенца необходимо применение специальных обрезных прессов и штампов.
При штамповке в закрытых штампах штамп в процессе деформирования остается закрытым, т. е. металл деформируется в закрытом пространстве (рис. 13, б). Зазор между подвижной и неподвижной частями штампа в процессе деформирования остается постоянным и незначительным по размеру – он только предохраняет штамп от
заклинивания. Отсутствие заусенца сокращает расход металла, отпадает необходимость в обрезных прессе и инструменте. Однако этот тип штампа применяется для сравнительно простых деталей, в основном тел вращения. Кроме того, отсутствие заусенца вызывает необходимость использовать точные заготовки из калиброванного проката или предварительно механически обработанные.
Рис. 13. Схема расположения волокон металла при открытой (а) и закрытой (б) штамповке
Рис. 14. Схемы штамповки выдавливанием: а – прямое; б – обратное; 1 – пуансон; 2 – матрица; 3 – поковка; 4 – выталкиватель
Сопоставляя качество макроструктуры поковок, отштампованных в открытых и закрытых штампах, необходимо отметить, что при закрытой штамповке макроструктура более качественная, так как процесс образования поковки в полости штампа протекает без на
рушения сплошности волокон, при обрезке заусенца после открытой штамповки волокна оказываются перерезанными, что снижает прочность детали.
Значения припусков и допусков на размеры поковок приведены в прил. 6.
Выдавливание
Штамповка в штампах для выдавливания – наиболее прогрессивный технологический процесс горячей штамповки. При использовании штампов для выдавливания значительно снижается расход металла (до 30 %), повышается коэффициент весовой точности, поковки получаются точные, максимально приближающиеся по форме и размерам к готовым деталям, производительность труда увеличивается в 1,5–2,0 раза.
Для выдавливания наиболее целесообразны следующие типы поковок: стержень с фланцем, клапаны двигателей, полые детали типа стаканов и т. п. Схемы штамповки в штампах для выдавливания приведены на рис. 14, где стрелками указано течение металла. Этим способом можно получать детали из углеродистых и легированных сталей, алюминиевых, медных и титановых сплавов. Поковки, изготовленные выдавливанием, имеют высокое качество поверхности, плотную микроструктуру. Точность поковок может соответствовать 12-му квалитету точности. Это достигается в результате тщательной подготовки исходных заготовок под штамповку, а также высокой точности изготовления и наладки штампов использованием специальных смазок.
Основное преимущество процесса выдавливания перед штамповкой в открытых штампах – получение поковок с точными размерами и чистой поверхностью.
Основные недостатки – высокие удельные усилия деформирования, большие энергозатраты на реализацию процесса и низкая стойкость штамповой оснастки.
Выбор штампа – открытый, закрытый или для выдавливания определяется, во-первых, конфигурацией и сложностью детали, во-вторых, ее массой и материалом, в-третьих, характером производства. Следует учитывать также и существенные различия в макроструктуре материала поковок, полученных в различных штампах. Макроструктура материала детали определяет ее прочность и долговечность, поэтому указанное обстоятельство должно учитываться при выборе технологического процесса получения штампованной заготовки.
Рекомендации по проектированию чертежа поковки на процессы объемной штамповки
При разработке чертежа детали, получаемой горячей объемной штамповкой, необходимо учитывать реализацию всех возможностей этого процесса. Прежде всего это относится к качеству поверхности. Следует также принимать во внимание требования, предъявляемые особенностями процесса объемной штамповки, к геометрической форме и размерам детали. В некоторых случаях необходимо проверить возможность и рациональность изменения конструкции отдельных ее элементов (без ущерба для качества и эксплуатационных характеристик) для упрощения конфигурации поковки в целях облегчения заполнения полости ручья штампа.
Общие конструктивные требования к деталям, изготавливаемым горячей объемной штамповкой, следующие.
1. Сопряжения необрабатываемых поверхностей должны быть оформлены радиусами, которые необходимы как для улучшения условий заполнения металлом полостей штампа (внутренние радиусы), так и для повышения стойкости штампов (наружные радиусы). Радиусы регламентированы ГОСТ 7505–74*.
2. На необрабатываемых поверхностях, перпендикулярных к плоскости разъема штампа, следует предусматривать штамповочные уклоны, необходимые для свободного удаления поковки из полости штампа. Штамповочные уклоны зависят от типов штампа и оборудования и должны быть в пределах от 1 до 10°.
3. При штамповке на прессах штамповочные уклоны уменьшаются, так как конструкция прессов позволяет применять специальные приспособления-выталкиватели, предназначенные для принудительного извлечения поковки из полости штампа. При штамповке
на горизонтально-ковочных машинах благодаря наличию подвижной разъемной матрицы штамповочные уклоны еще меньше.
Допускаемые отклонения размеров поковок на необрабатываемые поверхности назначают в соответствии с ГОСТ 7505–74*.
Рис. 15. Схема упрощения конструкции поковки: а – ликвирующих сплавов за счет разделения детали; б – за счет объединения двух деталей в одной поковке (S – толщина реза)
Для упрощения конструкции поковки, повышения и улучшения условий заполнения гравюры штампа в отдельных случаях целесообразно разделять деталь на две или большее число частей, штампуемых порознь, которые впоследствии соединяются сваркой или иным способом (рис. 15, а), в других случаях, наоборот, целесообразно объединение различных деталей в одну (рис. 15, б).
К важным технологическим требованиям, предъявляемым к конструкции штампуемых деталей, относится возможность правильного выбора плоскости разъема штампа. Деталь технологична для горячей объемной штамповки, если ее конструкция обеспечивает легкое из
влечение поковки из полости штампа без существенного упрощения формы детали за счет дополнительного металла – напуска. Влияние
положения плоскости разъема на форму поковок дано на рис. 16. Двойной штриховкой показаны объемы металла, необходимые для упрощения формы детали и обеспечения получения качественной поковки. При изменении плоскости разъема штампа необходимо оценивать объем заусенца, удаляемого после штамповки, и напуски, назначаемые для упрощения формы поковки.
Рис. 16. Влияние положения плоскости разъема на форму поковок
В некоторых случаях положение плоскости разъема определяется макроструктурой поковки. Например, при штамповке шестерен плоскость разъема штампа всегда должна быть перпендикулярна к оси детали. В этом случае макроструктура получается одинаковой у всех зубьев шестерни и обеспечивает их высокую прочность. На рис. 17 показан выбор положения разъема штампа по условиям работы детали.
Рис. 17. Схема к выбору плоскости разъема с учетом условий работы детали
Если деталь работает на срез по линии а-а, то волокна металла должны располагаться перпендикулярно к линии среза (положение плоскости разъема II-II). Положение плоскости разъема I-I в данном случае нежелательно.
При выборе плоскости разъема штампа необходимо учитывать условия захвата и базовые поверхности при механической обработке. При прочих равных условиях правильный разъем штампа должен обеспечивать зажим поковки по цилиндрической части и одинаковый припуск вдоль направления обработки резанием, т. е. напуски должны быть расположены по «черным» необрабатываемым поверхностям поковки.
Отступление от технологических требований, предъявляемых к конструкции штампованных деталей, неизбежно приведет к увеличению себестоимости заготовок из-за повышения затрат на материалы, механическую обработку и процента брака.
При разработке чертежа поковки пользуются ГОСТ 7505–74*, данные которого распространяются на штампуемые детали массой
до 400 кг, изготовляемые горячей объемной штамповкой из черных металлов на различных видах штамповочного оборудования.
Припуски на механическую обработку предусматривают в том случае, если качество поверхностного слоя поковки не удовлетворяет требованиям, предъявляемым к готовой детали. Припуски назначают либо по всей поверхности детали, либо на отдельные ее элементы, допускаемые отклонения – на все размеры поковки, независимо от наличия и назначения припуска. Допускаемые отклонения на размеры штампованных поковок двусторонние, несимметричные и включают все отклонения от номинальных размеров поковки. Причины этих отклонений следующие: недоштамповка по высоте; износ и неполное заполнение гравюры штампа; поверхностные дефекты материала; колебания объема исходной заготовки; неравномерная усадка материала при охлаждении.
При определении припусков и допускаемых отклонений размеров необходимо определить массу поковки, категорию материала и группу сложности поковки.
Различают две категории материала: M1 – углеродистая и легированная сталь с содержанием углерода до 0,45 % и легирующих элементов до 2 %; М2 – легированная сталь, за исключением указанной в группе M1.
Группу сложности поковки определяют в зависимости от отношения объема поковки Vпок к объему фигуры в виде цилиндра или
прямоугольного параллелепипеда Vфиг, описанного вокруг поковки,
т. е. С = Vпок /Vфиг.
ГОСТ 7505–74* предусматривает четыре группы сложности поковок в зависимости от величины С: первая группа при 0,63 £ С £ 1,0; вторая – при 0,32 £ С < 0,63; третья – при 0,16 £ С << 0,32; четвертая
– при С < 0,16.
Чем выше группа сложности поковки, тем менее технологична деталь, больше потери металла при механической обработке, ниже точность поковки.
Все пересекающиеся поверхности поковки сопрягаются по радиусам, все острые кромки на поверхности поковок необходимо закруглять. Если радиусы закругления не назначены или приняты недостаточными, то в местах их расположения в штампе возникает большая концентрация напряжений, что приводит к быстрому разрушению штампа. Значения наружных радиусов устанавливают в пределах 1–8 мм в зависимости от массы поковок (до 200 кг). Практически достаточно, чтобы значения для этих радиусов были на 0,5–1 мм больше нормального припуска на механическую обработку поковки, независимо от того, к каким сопрягаемым поверхностям относятся эти радиусы – механически обрабатываемым или нет. Внутренние радиусы закруглений примерно в три раза больше соответствующих наружных радиусов.
Практика штамповки показала, что конструктивные элементы поковок из цветных сплавов отличаются от таких же элементов стальных поковок. Припуски и допускаемые отклонения размеров на поковки из цветных сплавов рекомендуется назначать по ОСТ или ведомственным нормалям, например по ОСТ 3-4026–78.
Штампованные поковки из алюминиевых и магниевых сплавов, подвергаемые очистке поверхности травлением, должны изготавливаться с той же точностью, что и поковки, не подвергающиеся механической обработке.
На поковки из титановых сплавов, поверхности которых не подлежат механической обработке, а поверхностный слой металла удаляется травлением, устанавливают дополнительный припуск 0,5 мм. Если же поверхности штампованных поковок подлежат механической обработке, то дополнительный припуск на травление не назначается.
На конфигурацию поковок, получаемых горячей объемной штамповкой, на их точность, объем последующей механической обработки и себестоимость большое влияние оказывает не только тип штампа, но и вид применяемого оборудования.
Разница в принципе воздействия этих машин на деформируемый материал является определяющей. Ударный характер работы штамповочного молота исключает возможность использования выталкивателей, что приводит к значительному расходу металла на штамповочные уклоны и на компенсацию возможного смещения половин штампа относительно друг друга. Производительность труда при штамповке на молотах невысокая, процесс трудно поддается комплексной автоматизации.
Штамповка на кривошипных горячештамповочных прессах имеет ряд технологических и эксплуатационных преимуществ по сравнению со штамповкой на молотах. К ним относятся:
· достаточно высокая точность поковок (особенно по высоте);
· при штамповке на молоте пределы допусков 0,8–1,0 мм, а при штамповке на КГШП – 0,2–0,5 мм;
· существенная экономия металла и сокращение объема механической обработки за счет снижения припусков (в среднем на 20– 30 %) и штамповочных уклонов (в два-три раза);
· форма поковки более близка к форме готовой детали (рис. 18);
· повышение производительности труда в среднем в 1,4 раза; возможность полной автоматизации процесса;
· КПД прессов в три раза выше, чем у молотов; снижение себестоимости изготовления поковок примерно на 10–30 %.
Штамповку на молотах в основном применяют при серийном и крупносерийном производствах поковок массой 0,01–1000 кг, штамповка на КГШП наиболее целесообразна при крупносерийном и массовом производствах деталей сложной формы массой до нескольких сот килограммов.
При оценке эффективности горячей объемной штамповки следует учитывать стоимость штамповой оснастки, так как значительная доля затрат падает на стоимость штампов (в зависимости от характера производства составляет 10–60 % стоимости поковок).
Рис. 18. Схема расположения припусков на механическую обработку при штамповке на молоте (а) и прессе (б)
Молотовые штампы изготовляют цельноблочными, массивными, что приводит к значительному расходу дорогостоящей, сложнолегированной стали; прессовые штампы требуют меньше материала, но сложнее в механической обработке. Затраты на штамповую ос
настку зависят от стойкости штампов: чем больше выпуск поковок и чем больше стойкость штампов, тем меньше затраты на штампы.
Особенность конструкции гидравлических прессов обеспечивает неударный характер работы, однако они значительно тихоходнее, дороже и менее производительны, чем штамповочные молоты. Поэтому гидравлические прессы вместо штамповочных молотов применяют только там, где не может быть использован молот: при штамповке крупных штамповок, для которых масса падающих частей самых мощных молотов оказывается недостаточной; малопластичных сплавов, не допускающих больших скоростей деформирования; при различных видах штамповки выдавливанием, где требуется большой ход рабочего инструмента; для штамповки поковок цилиндрической формы типа втулок, стаканов и очень сложных форм в разъемных матрицах. Применение разъемных матриц позволяет получать поковки, по форме и размерам приближающиеся к конфигурации готовых деталей, без заусенца и штамповочных уклонов. Точность размеров таких поковок может достигать 11–12-го квалитетов. Коэффициент использования металла увеличивается с 0,2 до 0,6, трудоемкость механической обработки уменьшается на 15–20 %.
Фрикционные винтовые прессы по принципу воздействия на деформируемый металл занимают промежуточное положение между прессом и молотом; их применяют для мелких и средних поковок типа колпачков и стаканчиков, типа стержня с утолщением, например винты и болты, а также для штамповки сложных поковок, требующих разъемных матриц, в частности корпусов вентилей, тройников деталей трубопроводов.
На фрикционных прессах штампуют поковки из черных и цветных металлов, преимущественно малопластичных, медных и магниевых сплавов. Винтовые фрикционные прессы – тихоходные малопроизводительные машины, поэтому их применение ограничено при крупносерийном производстве.
Кривошипные горячештамповочные и винтовые прессы применяют для получения точных поковок шестерен с готовым профилем зуба. Освоены и внедрены в производство технологические процессы штамповки шестерен с прямым и спиральным профилем зуба, с модулем 5 мм и выше. Штамповка конических и цилиндрических
шестерен с готовым профилем зуба имеет место в следующих случаях: для получения готовых шестерен без последующей механической обработки по зубу с параметром шероховатости поверхности Rz = 4–20 мкм, применяемых в сельхозмашиностроении, угольной промышленности и т. д., шестерен с готовым профилем зуба, требующих только чистовой обработки. Припуск по профилю зуба принимают равным 0,6 мм на сторону, а по наружному конусу или диаметру цилиндрической шестерни – 1,5 мм на сторону.
Штампованные шестерни с готовым профилем зуба имеют ряд преимуществ перед шестернями, изготавливаемыми механической обработкой:
1. статическая прочность таких шестерен в среднем на 50 % выше обычных, так как у штампованных зубьев волокна металла расположены вдоль контура зуба, а у фрезерованных зубьев они перерезаны; это увеличение прочности зубьев позволяет снизить массу и удешевить стоимость машины путем снижения габаритов или замены легированных сталей обычными конструкционными;
2. значительно снижаются расход металла (в среднем на 25– 45 %) и общая трудоемкость изготовления шестерен.
Широкое применение для горячей объемной штамповки, особенно для операций высадки, получили горизонтально-ковочные машины (ГКМ), представляющие собой механический пресс, расположенный в горизонтальной плоскости. Кроме главного деформирующего ползуна имеется ползун, движение которого перпендикулярно движению главного ползуна, осуществляющего смыкание и размыкание блока матриц. В отличие от штампов молотовых и прессовых штампы для ГКМ имеют два взаимоперпендикулярных разъема и могут быть открытыми и закрытыми. Наличие двух разъемов в штампе создает лучшие условия для выполнения высадочных работ и позволяет получать поковки, как правило, без штамповочных уклонов. Поковки, получаемые на горизонтально-ковочных машинах, обычно имеют форму тел вращения. Типичные образцы поковок, штампуемых на ГКМ, приведены на рис. 19. Данные машины позволяют производить высадку конусов на длинных (до 3 м и более) прутковых и трубных заготовках; получать изделия типа стержня или трубы с головкой значительного объема путем после
довательной высадки с последующим набором металла головки (рис. 20); штамповать осадкой в торец изделия сложной формы, для изготовления которых необходимо применение разъемных матриц; получать поковки с отверстиями из прутковой заготовки без отходов металла на просечку отверстия.
Рис. 19. Типы поковок, штампуемых на ГКМ
Припуски и допускаемые отклонения размеров поковок, штампуемых на ГКМ, определяют по ГОСТ 7505–74* с учетом тех же факторов, что и при штамповке на молотах или прессах. Поскольку ГКМ обладают меньшей жесткостью, чем кривошипные горячештамповочные прессы, поковки, изготавливаемые на них, по размеру припусков и допусков ближе к молотовым, чем к прессовым.
Рис. 20. Схема многоручьевой высадки стержневой детали на ГКМ (I–IV – последовательность операций)
Штамповочные уклоны на участках поковки, формуемых в полости пуансона: наружные – 15’–1°, внутренние – 30’–2°. Для участков, формуемых в матрице, наружные уклоны не предусматриваются, а внутренние составляют 1–5°.
Наружные радиусы закруглений принимают равными размеру припуска на механическую обработку, внутренние – в 1,5–2 раза большими.
При сопоставлении штамповки на горизонтально-ковочных машинах со штамповкой на молотах и прессах необходимо учитывать, что номенклатура поковок для этих машин резко ограничена, масса их сравнительно небольшая (обычно 30–50 кг), стойкость штампов ниже, чем у молотов и прессов, стоимость горизонтально-ковочных машин примерно в 1,5 раза выше стоимости кривошипных прессов той же мощности. Однако достигаемая экономия металла, возможность получения более сложных и точных поковок, исключение предварительной операции резки прутков на штучные заготовки делают этот способ экономически целесообразным (рис. 21).
Рис. 21. Формы поковок при штамповке на ГКМ (а), молоте (б) и прессе (в); 1 – деталь; 2 – припуск на механическую обработку
Все возрастающие требования к экономии материалов, к разработке таких технологических процессов получения заготовок, когда механическую обработку применяют только как доводочную операцию, вызвали появление процессов точной или малоотходной горячей объемной штамповки. Точная горячая объемная штамповка относится к прогрессивным технологическим процессам, обеспечивающим экономию металла, сокращение трудоемкости при механической обработке, повышение качества и надежности деталей. Для более широкого внедрения точной штамповки уже на стадии разра
ботки изделий конструкторы должны стремиться к тому, чтобы при проектировании деталей предусмотреть больше необрабатываемых поверхностей, даже если при этом несколько повысится стоимость поковок. При точной штамповке размерная точность для стальных поковок может достигать 12–14-го квалитетов, параметр шероховатости поверхности Rz = 20–40 мкм, штамповочные уклоны до 1°.
При наличии необрабатываемых поверхностей наиболее полнореализуется преимущество штампованных деталей с их благоприятно ориентированной для условий эксплуатации макроструктурой, плавно огибающей контуры детали и исключающей надрезы, неизбежные при механической обработке.
Использование машин узкого назначения вместо универсальных при производстве заготовок позволяет во многих случаях значительно снизить трудоемкость, сократить сроки изготовления и улучшить качество деталей. Ниже в общих чертах рассмотрим специализированные процессы, нашедшие за последнее время наибольшее распространение в кузнечно-штамповочном производстве.
Штамповку на горизонтально-гибочных машинах применяют для получения заготовок из сортового или полосового материала больших габаритов. Она может осуществляться как в горячем, так и в холодном состоянии. Как правило, изделия, получаемые гибкой, не подвергаются механической обработке, поэтому при конструировании деталей в чертеже следует предусмотреть все необходимые требования для обеспечения точности формы и размеров детали:
· по возможности избегать гибки на ребро;
· обеспечивать внутренние радиусы изгиба максимально возможными;
· незначительные отклонения размеров в результате искажения проката в местах изгиба не учитывать и в чертеже не указывать.
Горизонтально-гибочные машины позволяют осуществлять гибку П-образных (рис. 22, а), дугообразных (рис. 22, б) и круглых (рис. 22, в) деталей.
Рис. 22. Схемы гибки на бульдозерах и получаемые профили
Вальцовка
Вальцовка представляет собой разновидность процесса прокатки, когда деформирование штучной заготовки производится в секторных штампах ковочных вальцов. Ковочные вальцы относительно просты по конструкции и в эксплуатации, высокопроизводительны. Из мерных заготовок круглого, квадратного или прямоугольного поперечного сечения вальцовкой изготавливают фасонные заготовки удлиненной формы, переменного сечения и, как правило, с прямолинейной осью. Вальцовку применяют для изготовления заготовок под дальнейшую штамповку на прессах или молотах, а также для получения готовых поковок и как отделочную операцию.
Вальцовкой в массовом и крупносерийном производствах изготавливают мелкие и средние поковки переменного сечения и различной формы (например, гаечные ключи, плоскогубцы, звенья транспортеров и т. п.). Поковки получают в «ленте» по несколько штук, расположенных в длину и соединенных между собой заусенцем. Параметр шероховатости поверхности таких поковок Rz = 40–320 мкм,
производительность процесса оценивают тысячами штук в смену.
Отделочную вальцовку применяют для получения профильных заготовок, например турбинных лопаток с припуском на рабочую поверхность до 0,2–0,15 мм, параметром шероховатости поверхности до Rz = 6,3–3,2 мкм. Обычно такую вальцовку проводят в холодном состоянии, причем получаемые заготовки имеют окончательные размеры по толщине и профилю. Отделочная вальцовка
дает значительный эффект: снижаются расход металла в среднем на 35 %, трудоемкость на 20 %, себестоимость на 35 %.
Рис. 23. Схема вальцовки: а–в – стадии вальцовки; 1 – подающий схват; 2, 3 – секторные штампы
Дата добавления: 2021-07-19; просмотров: 88; Мы поможем в написании вашей работы! |
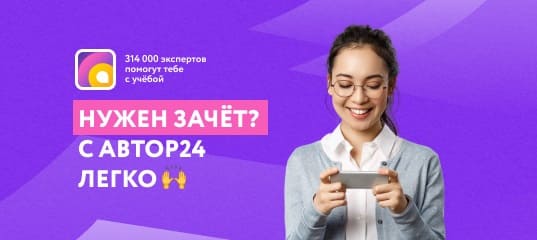
Мы поможем в написании ваших работ!