Штамповка на радиально-обжимных и ротационно-ковочных машинах
Штамповку на радиально-обжимных и ротационно-ковочных машинах осуществляют как в горячем, так и в холодном состоянии, обрабатывая осесимметричные детали с вытянутой осью.
Ротационное деформирование как метод точной обработки изделий получило применение в производстве сравнительно недавно, чему способствовало появление специализированных радиальнообжимных и ротационно-ковочных машин с программным управлением. Изделия, изготовляемые на этом оборудовании, имеют широкий диапазон размеров диаметра: от 0,15 мм (для прутка) до 600 мм (для трубной заготовки). Эскизы деталей, получаемых ротационным деформированием, приведены на рис. 24.
На радиально-обжимных и ротационно-ковочных машинах можно изготавливать ступенчатые и удлиненные поковки и изделия из жаропрочных и малопластичных сталей и сплавов, сплавов на основе алюминия, а также из металлокерамики и металлопорошков; получать отверстия малых диаметров на относительно большой длине; производить сборочные операции.
Точность и шероховатость поверхности поковок зависят от качества изготовления и геометрии инструмента, режимов обработки. При удовлетворительном сочетании всех факторов можно получить параметры шероховатости поверхности: Rz = 0,4–1,6 мкм при холодной и Rz = 2–6,3 мкм при горячей обработке. В этих случаях обжатие позволяет одновременно заменить точение и шлифование. Точность обработки при холодном обжатии соответствует 6–8-му, при горячем – 11–13-му квалитетам.
|
|
Рис. 24. Эскизы деталей, получаемых ротационным деформированием
В процессе ротационного обжатия улучшается структура металла, повышаются его механические свойства. Повышение прочности изделий после обжатия предопределяет применение этого вида обработки в тех случаях, когда затруднено выполнение термической обработки.
Сущность процесса состоит в следующем: прутковая заготовка подвергается обжатию бойками, движущимися навстречу друг другу, движение бойков у разных конструкций машин осуществляется по-разному; число бойков также может быть различным: два, три, четыре (рис. 25). Число обжатий у различных машин колеблется от нескольких сот до нескольких тысяч в минуту.
Основным преимуществом данного вида обработки является получение поковок высокой точности с высокой чистотой поверхности. Дальнейшая механическая обработка, за исключением шлифования (в целях достижения необходимой точности) и последующих доводочных операций, является в большинстве случаев излишней.
Прочность изделий увеличивается примерно на 30 %. Процесс позволяет значительно экономить металл. Так, при переводе изделий типа ступенчатых валов со штамповки или механической обработки на горячее обжатие экономия металла достигает 40–60 %. Производительность (по сравнению с токарной обработкой) возрастает в четыре-пять раз. Поэтому перевод изделий с обработки резанием на ротационное обжатие во всех типах производства, кроме единичного, всегда является экономически целесообразным.
|
|
Рис. 25. Схемы ковки на ротационно-ковочной (а) и ротационно-обжимной (б) машинах: 1 – бойки; 2 – поковка; Е – ход бойков
Раскатка и накатка
Процесс раскатки кольцевых заготовок получил значительное распространение в промышленности для получения заготовок колец сложного профиля, с поднутрениями, буртами, выточками и т. д.
Раскатка не является самостоятельным процессом обработки металлов давлением, так как исходные заготовки для раскатки обычно получают штамповкой, ковкой, литьем или из труб. Раскатку осуществляют как в горячем, так и в холодном состоянии. В соответствии с габаритными размерами применяемого оборудования раскатке подвергают заготовки с наружным диаметром от 40 до 2000 мм при высоте обрабатываемого обода до 180 мм. На рис. 26 показаны схемы раскатки кольцевых заготовок, на рис. 27 – типы колец, получаемых раскаткой. Допуск на наружный диаметр кольца принимают +0,01d, на внутренний диаметр – 0,022d, но не более 6 мм. Параметр шероховатости поверхности Rz = 10–3,2 мкм. Основные преимущества процесса раскатки следующие: возможность получить более сложный профиль и более точные размеры, чем при штамповке; обеспечить в заготовке тангенциальное расположение волокон металла, что значительно увеличивает надежность изделий; обеспечить значительную экономию металла, повышение коэффициента весовой точности до 0,7–0,75, сравнительно высокую производительность процесса (250 шт./ч крупных и 500 шт./ч мелких поковок), снижение трудоемкости механической обработки на 20–30 %.
|
|
Рис. 26. Схемы раскатки: 1 и 2 – соответственно опорный и обжимной ролики; 3 – раскатываемое кольцо; 4 и 5 – ограничительные ролики
Рис. 27. Типы колец, получаемых раскаткой
Недостаточная производительность (в ряде случаев и точность) шлицефрезерования обусловила возникновение новых методов об
разования шлицев, в частности пластическим деформированием накаткой, т. е. превращением гладкой поверхности заготовки в ребристую определенного профиля. Этот процесс комбинированный, заготовки под накатку получают либо штамповкой, либо ковкой, в некоторых случаях заготовкой может служить пруток.
|
|
Диаметр заготовки под накатку определяют опытным путем. Основным оборудованием являются специальные станы, действующие по принципу поперечной прокатки, с принудительным вращением заготовки и пары накатных валков (рис. 28). Такой способ накатки в основном используют для горячей накатки зубьев колес, шлицев на валах и крупной резьбы. Мелкую резьбу накатывают в механических цехах плоскими плашками или роликами на резьбонакатных станках.
Штучная накатка зубчатых колес универсальна и при использовании соответствующей оснастки позволяет изготовлять цилиндрические и конические колеса с зубьями прямыми и спиральными.
Цилиндрические зубчатые колеса диаметром менее 150 мм при модуле не более 3 мм рациональнее обрабатывать стопками. На таком же принципе основано изготовление зубьев шестерен непосредственно от прутка. Зубья наносятся накаткой на поверхность прутка, который в дальнейшем режется на мерные заготовки по высоте; механической обработкой изготавливают отверстия. Накаткой можно получать зубья модулем 8–15 мм на колесах диаметром до 600 мм. Особенно выгодно получать зубья накаткой для крупномодульных шестерен, когда достигают значительной экономии металла.
Рис. 28. Схемы накатки: а – штучных заготовок; б – от прутка; 1 – деформирующий инструмент; 2 – заготовка
Предварительная механическая обработка перед накаткой заключается в обработке посадочного отверстия, торцов и наружного диаметра, что позволяет получить профиль накатанного зуба по всем размерам с точностью по 8-му квалитету с параметром шероховатости поверхности Rz = 0,8–6,3 мкм. На полученных накаткой зубьях, окончательные размеры которых должны соответствовать 6-му квалитету, предусматривают припуск (на последующее шлифование или шевингование) по 0,2–0,25 мм на сторону.
Применение пластического деформирования (накатки) вместо механической обработки дает значительное снижение трудоемкости изготовления зубчатых колес, так как производительность накатки выше зубонарезания в 40–50 раз. Например, использование одного стана даст возможность заменить примерно 80 единиц зуборезного оборудования и высвободить до 70 станочников.
Благоприятное расположение волокон после накатки повышает механические характеристики зубчатых колес, в частности, их износоустойчивость увеличивается на 50–70 %.
Стоимость колес с накатанными зубьями получается ниже стоимости фрезерованных примерно на 15–20 %. При этом можно рассчитывать, что освоение накатки заготовок без предварительной обработки снизит трудоемкость их изготовления на 40–45 %, а тем самым и стоимость зубчатых колес, и расширит область применения этого способа.
Калибровка
Калибровка относится к отделочным операциям обработки металлов давлением (рис. 29). Цель калибровки – повышение точности размеров всей поковки или отдельных ее участков. При калибровке достигают улучшения поверхности и снижения колебаний массы поковки. Калибровку целесообразно применять в крупносерийном и массовом производствах для снижения, а в некоторых случаях и для полного устранения механической обработки. Точность и чистота поверхностей поковок, подвергаемых калибровке, не ниже, чем фрезерованных, а иногда и шлифованных деталей. Кроме того, после калибровки возможно повышение механических свойств и стойкости деталей при эксплуатации за счет наклепа.
По технологическим признакам калибровку можно разделить на плоскостную, объемную и комбинированную.
Плоскостная калибровка (чеканка) служит для получения точных вертикальных размеров на одном или нескольких участках поковки, ограниченных горизонтальными плоскостями (рис. 29, а). Плоскостная калибровка производится в холодном состоянии на специальных чеканочных кривошипно-коленных прессах.
Для получения положительных результатов калибруемые поковки должны удовлетворять следующим требованиям: под калибровку должен быть предусмотрен припуск; для низких поковок (до 10 мм) номинальный припуск на размер рекомендуют 0,3–0,6 мм в зависимости от диаметра или ширины обжимаемого участка; с увеличением толщины поковки припуск увеличивается примерно до 0,5–1,0 мм.
Допуски на размеры поковок под калибровку рекомендуют от
+(0,3 + 0,4) до +(0,8 + 1,0) мм соответственно приведенным ранее предельным значениям номинальных припусков. Припуски и допуски для плоскостной чеканки предусмотрены ГОСТ 7505–74*: точность поковок после штамповки должна быть повышенной; горизонтальные размеры поковок, подлежащих калибровке, следует назначать меньше номинальных, чтобы компенсировать их увеличение после калибровки.
По точности получаемых размеров поковок после калибровки различают грубую калибровку с допуском ±(0,1 + 0,25) мм, повышенной точности с допуском ±(0,05 + 0,1) мм и после двукратной калибровки – высокую точность с допуском ±0,025 мм. Параметр шероховатости поверхности после калибровки достигает Rz = 1,6– 6,3 мкм, т. е. он такой же, как при шлифовании.
Объемная калибровка служит для уточнения размеров поковки в разных направлениях. Точность объемной калибровки ниже, чем плоскостной.
Рис. 29. Схемы калибровки: а – плоскостная; б – объемная; 1 – поковка; 2, 3 – элементы штампа
Можно обрабатывать поковки как в холодном, так и в горячем состоянии (рис. 29, б).
Комбинированная калибровка является сочетанием операций объемной и плоскостной. В начале обработки в результате объемной калибровки поверхности поковок становятся гладкими, далее отдельные плоские элементы поковок подвергают плоскостной чеканке для получения точных размеров между соответствующими плоскостями.
Следует отметить, что при применении таких операций, как калибровка, раскатка, накатка зубьев, отделочная вальцовка, можно всегда значительно снизить объем механической обработки, уменьшить себестоимость продукции, повысить производительность труда и качество получаемой продукции.
Листовая штамповка
Это один из видов холодной обработки металлов давлением, при котором листовой материал деформируется в холодном или подогретом состоянии.
Листовой штамповкой изготовляют мелкие детали часов и приборов; детали средних размеров, металлическую посуду, металлические консервные банки, части велосипедов и мотоциклов, различные заглушки, крышки, кронштейны, диски; крупные облицовочные детали автомобилей, автобусов, тракторов – кузова, крылья, двери, крыши, детали корпусов самолетов и вагонов и, наконец, очень крупные и тяжелые толстолистовые детали – днища паровых котлов и резервуаров, детали корпусов морских судов и т. д.
Сваривая листовые штампованные детали, создают сложные и ответственные части машин, например штампосварные станины прессов и металлорежущих станков, сложные штампосварные кузова автомобилей, части аппаратов химического производства, речных и морских судов.
Основные преимущества листовой штамповки:
· возможность изготовления прочных, легких и жестких тонкостенных деталей или изделий простой и сложной формы, получить которые другими способами невозможно или затруднительно;
· высокая производительность и экономное расходование металла;
· широкие возможности автоматизации и роботизации производственных процессов;
· взаимозаменяемость деталей и высокая чистота поверхности.
По сравнению с горячей штамповкой холодная листовая штамповка имеет следующие преимущества: нет операции нагрева металла, поверхностный слой металла не окисляется, изделия получаются более точными по размерам и с меньшей шероховатостью поверхности.
По сравнению с обработкой резанием холодная штамповка позволяет сократить расход материала, так как материал не отделяется в стружку, снизить трудоемкость изготовления деталей и повысить производительность труда. Одновременно холодная обработка давлением обеспечивает упрочнение обрабатываемого материала, что позволяет делать детали более легкими. Эти же преимущества позволяют заменять литые детали штампованными. Кроме того, преимущество холодной штамповки по сравнению с литьем заключается в том, что холодноштампованные изделия почти не требуют механической обработки.
Операции листовой штамповки подразделяют на разделительные, когда одна часть металла отделяется от другой; формоизменяющие, при которых без разрушения заготовок изменяется их форма; комбинированные (сочетаются разделительные и формоизменяющие переходы обработки); штампосборочные, при которых механически соединяют отдельные листовые штампованные детали.
Для изготовления деталей листовой штамповкой применяют разнообразные металлические и неметаллические материалы. Металл для листовой штамповки выпускают в виде лент, полос и листов, сортамент которых указан в соответствующих стандартах, например ГОСТ 82–70 «Сталь прокатная широкополосная универсальная». При выборе материала для листовой штамповки необходимо учитывать эксплуатационные свойства получаемых деталей и способность материала к обработке давлением.
Из углеродистой стали обыкновенного качества штампуют детали, несущие малые нагрузки, бытовые изделия. Из качественной углеродистой стали изготовляют детали с повышенными требованиями к прочности и качеству поверхности. Во многих отраслях машиностроительной промышленности широкое применение находит качественная конструкционная сталь марок 05кп, 08кп, Юкп, 15кп и др. Эта сталь отличается высокими пластическими свойствами и хорошей свариваемостью.
Горячекатаную листовую сталь общего назначения, поставляемую со слоем окалины, штампуют относительно редко, так как окалина, покрывающая листы, является причиной быстрого изнашивания пуансонов и матриц. Используется эта сталь при изготовлении грубых строительных конструкций, товарных вагонов, некоторых сельскохозяйственных машин и т. д.
Декапированная тонколистовая сталь толщиной 0,25–3,0 мм имеет хорошую штампуемость. Из нее изготовляют посуду, бытовые изделия, а также детали, не несущие значительных нагрузок и не предназначенные для полирования, хромирования, никелирования.
По точности толщины листа сталь подразделяется на три группы: А – высокая точность, Б – повышенная точность, В – обычная точность.
По способности к вытяжке в холодном состоянии различают листы трех групп вытяжки: ВГ – для весьма глубокой, Г – для глубокой, Н – для нормальной.
Низкоуглеродистая холоднокатаная стальная лента может быть особо мягкой (ОМ), мягкой (М), полумягкой (ПМ), пониженной твердости (ПТ) и твердой (Т); по точности изготовления – Н (нормальной точности), ВШ (повышенной точности по ширине и толщине).
Черную отожженную полированную жесть изготовляют толщиной 0,18–0,55 мм, а белую жесть – 0,21–0,55 мм. Из черной жести штампуют тонкостенные детали бытовых изделий, подвергающиеся затем окраске. Из белой жести изготовляют консервные банки, тару для упаковки, пищевых продуктов, некоторые тонкостенные детали, поверхности которых должны быть защищены от коррозии.
Оцинкованную сталь, выпускаемую толщиной 0,88–1,5 мм, применяют для штамповки изделий различного назначения.
Ответственные детали штампуют из легированных конструкционных сталей, таких как 10Г2А, 12Г2А, 20ХГСА, 25ХГСА и др. Эти стали обладают хорошей способностью к штамповке в отожженном состоянии и хорошо свариваются.
Детали с повышенной коррозионной стойкостью штампуют из коррозионно-стойких сталей (например, марок 12Х18Н9, 10X13 и др.).
Помимо указанных в листовой штамповке используются стали специального назначения, например электротехнические, пружинные.
По качеству материала листовая и полосовая сталь разделяется на сорта, изготовляемые из сталей различных марок:
· листовая углеродистая сталь – из марок стали обыкновенного качества по ГОСТ 380–71*;
· листовая углеродистая качественная сталь – из марок качественной стали по ГОСТ 1050–74**;
· листовая низколегированная сталь – из марок стали по ГОСТ 19282–73;
· листовая легированная конструкционная сталь – из марок легированной стали по ГОСТ 1542–71*;
· листовые высоколегированные стали и сплавы (коррозионностойкие, жаростойкие и жаропрочные) по ГОСТ 5632–72*.
В автомобильной, химической и пищевой промышленности вместо коррозионно-стойких и жаростойких сталей используют холоднокатаную стальную полосу (08кп), диффузионно-хромированную
в вакууме. Сталь обладает хорошими пластическими свойствами и повышенной стойкостью во многих реактивных средах при повышенной температуре. Стальные полосы с полимерным покрытием (металлопласт) применяют в химической, автомобильной, пищевой, радиотехнической, авиационной промышленности. Металлопласт обладает стойкостью против коррозии, износоустойчивостью, хорошими электроизоляционными и звукоизоляционными свойствами.
Из цветных металлов, применяемых для листовой штамповки, наибольшее распространение получили алюминий, медь, никель, магний, титан и их сплавы.
Алюминий и его сплавы находят широкое применение в самолетостроении, автомобильной промышленности, при изготовлении различных деталей приборов, бытовых изделий и т. д. Распространены следующие марки алюминия: А1-А3, АД, АД1 и Д1, Д6, Д16.
Из медных листов и лент марок M1–М3 штампуют в основном детали электротехнической аппаратуры. Латуни находят применение при штамповке деталей часов, радиодеталей, посуды и т. д. Штампуют главным образом латуни марок Л62, Л68, J170. Из других сплавов меди для штамповки применяют бронзы.
Никель марок h2–Н3 и его сплавы – мельхиор и нейзильбер
– используют для изготовления химической посуды, приборов, деталей часов, ювелирных изделий.
Сплавы магния МА1 и МА8 с повышенной коррозионной стойкостью применяют для штамповки самых разнообразных изделий: деталей мотоциклов, велосипедов, прицепов и других средств передвижения, электротехнического и электронного оборудования и т. д. Титан все шире используют в штамповочном производстве для изготовления ответственных деталей в авиационной промышленности и в ряде других отраслей (главным образом сплавы титана марок ВТ-1, ВТ1-00, ВТ5, ВТ6, ОТ4).
Из неметаллических материалов штамповкой получают прокладочные детали, изоляционные и декоративные. Наибольшее применение находят следующие неметаллические материалы: пластмассы (гетинакс, текстолит, органическое стекло, винипласт, целлулоид и др.), резина, материалы на основе бумаги (картон, фибра), материалы минерального происхождения (слюда, миканиты).
Из других неметаллических материалов штампуют также фетр, кожу, войлок, прессшпан.
Основным требованием, предъявляемым к материалам, применяемым при изготовлении деталей листовой штамповкой, является их пригодность к штамповке и последующей эксплуатации. Выявление этой пригодности материала к той или иной штамповочной операции весьма сложно и требует проведения ряда испытаний.
Технологические процессы листовой штамповки могут быть рациональными лишь при условии создания технологичной конструкции или формы детали, допускающей наиболее простое и экономичное изготовление. Поэтому технологичность листовых штампованных деталей представляется важной предпосылкой прогрессивности технологических процессов и экономичности производства.
Основные показатели технологичности листовых холодноштампованных деталей – наименьший расход материала, минимальное число и низкая трудоемкость операций, отсутствие последующей механической обработки, наименьшее количество требуемого оборудования и производственных помещений, минимальное число оснастки при сокращении затрат и сроков подготовки производства, увеличение производительности отдельных операций и цеха в целом. Общий результативный показатель технологичности – наименьшая себестоимость штампуемых деталей.
При конструировании деталей, предназначенных для изготовления их способами листовой штамповки, необходимо учитывать технологические требования к конструкции листовых штампованных деталей; основные из них следующие:
1. механические свойства листового материала должны соответствовать не только требованиям прочности и жесткости изделия, но также процессу формоизменения и характеру пластических деформаций; применять для формоизменяющих операций более пластичный, хотя и менее прочный материал, так как в процессе холодной штамповки происходит его упрочнение, значительно увеличивающее характеристики прочности материала;
2. создавать легкие и облегченные конструкции деталей, применяя для увеличения жесткости штамповку ребер жесткости, отбортовку, загибку, закатку кромок и т. д., а также замену тяжелых
стандартных прокатных профилей более легкими – гнутыми из листового металла;
1. конфигурация детали или ее развертки должна обеспечивать наивыгоднейшее использование листового металла – применение малоотходного или безотходного раскроя. Если отход неизбежен, то желательно придать ему конфигурацию, соответствующую другой детали, или использовать его вторично;
2. широко применять технологичные штампосварные конструкции взамен литых, кованых или клепаных;
3. использовать штамповочные методы для сборки отдельных деталей путем расклепки, отбортовки, полой высадки, загибки кромок и лапок, закатки шва и т. п.
Кроме указанных общих требований к конструкции штампованных деталей существуют специфичные требования, присущие отдельным операциям листовой штамповки.
Основные технологические требования к конструкции плоских деталей, получаемых вырубкой или пробивкой:
1. избегать сложных конфигураций с узкими и длинными вырезами контура или очень узкими прорезями (b > 2S, где b – ширина прорези; S – толщина листовой заготовки);
2. выполнять сопряжения сторон наружного контура с закруглениями лишь при вырубке детали по всему контуру; для возможности применения безотходного раскроя следует, наоборот, допускать сопряжения сторон под прямым углом;
3. избегать вырубки длинных и узких деталей постоянной ширины при b > 3S, заменяя вырубку расплющиванием проволочной заготовки;
4. не следует располагать отверстия в заготовке, подлежащей гибке, близко к радиусу закругления детали; наименьшее расстояние от края отверстия до загнутой полки «а» должно составлять а ³ r + 2S, где r – радиус изгиба;
5. в вытянутых деталях, имеющих отверстия в дне или фланце, пробиваемые после вытяжки, расстояние от стенки детали до края отверстия С ³ r + 0,5S, где r – радиус закругления дна или фланца;
6. наименьшее расстояние между отверстиями при одновременной их пробивке L = (2f3)S.
При проектировании гнутых деталей необходимо учитывать технологические требования к конструкции изогнутых листовых деталей:
1. минимально допустимые радиусы изгиба следует применять лишь при конструктивной необходимости; в большинстве случаев можно применить увеличенные радиусы гибки: r ³ S (для толстых заготовок еще бо́льшие);
2. в случае гибки пластичных металлов (стали 10, 20) с малым радиусом закругления линию изгиба желательно располагать поперек волокон проката;
3. при гибке твердых малопластичных материалов (бронза, сильно наклепанная латунь, лента пружинной стали и др.) линию изгиба следует располагать обязательно поперек волокон проката; наименьший радиус изгиба берется в пределах 2S–4S;
4. для увеличения жесткости гнутых деталей и устранения упругого пружинения рекомендуется штамповка ребер жесткости поперек угла изгиба;
5. наименьшая высота отгибаемой полки h ³ 3S;
6. в случае многооперационной гибки необходимо предусматривать технологические базы для фиксирования заготовок на операциях.
При проектировании деталей, получаемых вытяжкой или формовкой, следует учитывать следующие технологические требования:
1. избегать весьма сложных и несимметричных форм вытягиваемых деталей, использовать их лишь в случае явной конструктивной необходимости;
2. радиусы закруглений фланца должны быть больше, чем радиусы закруглений у дна; сопряжение стенок с дном без радиуса закругления может быть выполнено путем дополнительной калибровки или при штамповке весьма толстых заготовок;
3. избегать глубоких вытяжек с широким фланцем, требующих большого числа операций;
4. полуоткрытые несимметричные формы полых деталей нужно проектировать, учитывая возможность спаренной вытяжки с последующей разрезкой на две детали;
5. в прямоугольных коробках избегать острых углов в плане и у дна детали, кроме случаев изготовления коробок методом холодного выдавливания;
6. при вытяжке полых деталей сложной конфигурации предусматривать те или иные технологические базы для фиксирования заготовок на операциях.
Анализ технологичности деталей проводится обязательно с учетом конкретных производственных условий и масштаба производства. При массовом производстве штампуемых деталей основными показателями при оценке технологичности являются расход материала и трудоемкость изготовления. Действительно, при изготовлении деталей сотнями тысяч или миллионами единиц эти факторы приобретают решающее значение. Уменьшение трудоемкости изготовления может быть достигнуто совмещением операций, применением сложных штампов-автоматов, автоматических линий. Связанное с этим удорожание производства оказывает малое влияние на себестоимость продукции, так как затраты распределяются на большое число штампуемых деталей.
При мелкосерийном производстве на себестоимость продукции большое влияние оказывает стоимость штампа. Поэтому экономически целесообразно применять штамповку в универсальных штампах со сменными пуансонами и матрицами. В этом случае технологический процесс расчленяют на ряд отдельных простых операций. Для оснащения штампов изготовляют только относительно простые пуансоны и матрицы. Это позволяет осуществлять штамповку с малыми затратами на оснастку.
К разделительным операциям листовой штамповки относятся отрезка, разрезка, обрезка, надрезка, вырубка, пробивка, проколка, зачистка.
В разделительных операциях листовой штамповки отделение одной части заготовки от другой осуществляется относительным смещением частей в направлении, перпендикулярном к плоскости заготовки. Это смещение в начальных стадиях характеризуется пластическим деформированием, но завершается обязательно разрушением. Для уменьшения искажений заготовки, вызываемых пластическими деформациями, стремятся локализовать очаг деформации, чему способствуют уменьшение радиусов скругления рабочих кромок инструмента, уменьшение зазора между пуансоном и матрицей, а также применение специальных разделительных операций.
Обычная вырубка и пробивка листового материала дают неровную, слегка криволинейную и шероховатую поверхность среза. В ряде случаев изготовления штампованных деталей повышенной точности требуется гладкая и перпендикулярная поверхность среза с параметром шероховатости поверхности Rz = 1,6–3,2 мкм.
В таких случаях применяют способы чистой вырубки, имеющие
значительные преимущества по сравнению с механической обработкой резанием и дающие гладкую полированную поверхность среза, перпендикулярную к поверхности изделия, при повышенной точности изготовления.
Сущность этих способов заключается в применении матрицы с закругленными режущими кромками (рис. 30, а), пуансона больше матрицы (рис. 30, б), или прижима, имеющего клиновидное ребро (рис. 30, в). Последний способ является новым, прогрессивным. В результате смещения некоторого объема металла клиновым ребром в сторону пуансона в зоне реза создается напряженное состояние объемного сжатия, которое способствует устойчивости пластической деформации и увеличивает пластические свойства материала заготовки. Этим способом изготовляют детали точного приборостроения толщиной 1,5–15 мм. Параметр шероховатости
поверхности среза Rz = 1,6–3,2 мкм.
Раскрой листового металла на штучные заготовки и полосы является первой операцией, связанной с потерями металла в виде обрезков и неиспользуемых отходов. В то же время экономия металла и уменьшение отходов в холодной листовой штамповке имеют весьма важное значение, особенно в крупносерийном и массовом производствах, так как при больших масштабах производства даже незначительная экономия материала на одном изделии в итоге дает значительный экономический эффект.
Рис. 30. Схемы процессов вырубки: а – обычной; б – пуансоном больше матрицы; в – точной с клиновым прижимом
При листовой штамповке экономия металла может быть получена наиболее целесообразным раскроем листов на штучные заготовки или полосы с наименьшими отходами; экономным раскроем полос и расположением вырубаемых деталей на полосе; уменьшением потерь металла на перемычки; применением так называемого безотходного и малоотходного раскроя; повышением точности расчета размеров заготовок и уменьшением припусков на обрезку; использованием отходов для изготовления других деталей; предупреждением появления брака штампуемых деталей.
Различные способы раскроя полосового материала по экономичности и технологическим отходам разделяют на три вида: раскрой с отходами, малоотходный и безотходный раскрои.
Оценку экономичности того или иного типа раскроя производят посредством определения коэффициента раскроя:
Кр = (f0np)/(Bh),
где f – площадь поверхности детали, м2; h – шаг вырубки, м;
0
В – ширина полосы, м; np – число рядов раскроя.
При штамповке из полосы или ленты коэффициент раскроя определяют по формуле
Ки = fn/LB,
где f – площадь детали, м2; п – число фактических деталей, получаемых из полосы; L – длина полосы или ленты, м; В – ширина полосы или ленты, м.
Если в операциях разделения листового материала стремятся к максимальной локализации очага деформации, то при формоизменяющих операциях сосредоточение деформации в одном месте недопустимо, так как формоизменяющие операции осуществляются без разрушения материала. При формоизменяющих операциях стремятся получить заданную величину деформации, чтобы заготовка приобрела требуемую форму. Если этого не удается достичь за один ход пресса, технологический процесс разбивают на переходы, число которых зависит от сложности детали, материала заготовки, применяемого оборудования.
При проектировании технологических процессов, в которых применяются операции гибки, технологам приходится определять размеры заготовки, минимальные радиусы изгиба, углы пружинения, условия гибки без калибровки, с калибровкой.
Одной из основных технологических характеристик при гибке является минимально допустимый радиус изгиба (радиус пуансона). Минимально допустимые радиусы изгиба должны соответствовать пластичности металла и не допускать образования трещин на наружной поверхности металла.
При снятии деформирующих усилий после гибки происходит упругая разгрузка, в результате чего размеры детали изменяются. Последеформационная упругая деформация при гибке носит название «пружинение». Для получения точных размеров гнутых деталей необходимо учитывать значения угла пружинения.
Для компенсации пружинения применяют различные способы: увеличивают углы подгибки на угол пружинения, используют гибку с калибровкой (подчеканкой), специальные штампы с компенсатором.
Вытяжка является основной из формоизменяющих операций. Вытяжку изделий из тонколистового материала в большинстве случаев производят в холодном состоянии. Вытяжку из толстолистового материала, а также из малопластичных металлов осуществляют с подогревом заготовок.
По характеру деформации различают: 1) вытяжку без утонения стенок; 2) вытяжку с утонением. В первом случае вытяжка происходит без заранее обусловленного изменения толщины материала стенок изделий: во втором случае процесс вытяжки осуществляется за счет изменения поперечного сечения: уменьшения диаметра и толщины стенок изделия.
Основными рабочими инструментами для вытяжки служат матрица и цилиндрический пуансон. При опускании пуансона плоский кружок-заготовка вытягивается, проталкивается пуансоном через матрицу и превращается в полый цилиндр. Различают три основных способа вытяжки.
1. Вытяжка полых деталей путем превращения плоского фланца в цилиндрическую или коробчатую форму при создании во фланце плоского напряженного состояния. Сюда относится вытяжка цилиндрических, овальных, коробчатых и других деталей с вертикальными или слегка наклонными стенками.
2. Вытяжка сферических, криволинейных и сложной формы деталей в штампах с вытяжными ребрами. В этом случае под прижимом преобладают растягивающие напряжения и деформации, а в остальной части деформируемой заготовки возникает напряженное состояние двухосного растяжения.
3. Вытяжка эластичной матрицей и фрикционная вытяжка, создающие заталкивание заготовки, в результате чего снижаются растягивающие напряжения в очаге деформации и облегчается процесс вытяжки.
При первом способе вытяжки наиболее благоприятные условия деформирования заключаются в максимально возможном уменьшении сопротивления плоского фланца деформированию. Этого достигают путем применения металла пониженной прочности, отжигом заготовки, нагревом фланца, вытяжкой без прижима, эффективным смазыванием. В результате снижаются растягивающие напряжения в опасном сечении, улучшается условие прочности этого сечения и становится возможной более глубокая вытяжка.
При втором способе вытяжки в штампах с вытяжными ребрами значительная часть заготовки вначале находится вне контакта с рабочими частями штампа и легко образует гофры и морщины. Для их предотвращения приходится создавать повышенные радиальные растягивающие напряжения и искусственно увеличивать сопротивление деформируемого металла путем перетягивания его через вытяжные ребра. При этом значительно возрастают растягивающие напряжения в опасном сечении и ухудшается условие его прочности. Для того чтобы в данном случае создать благоприятные условия деформирования и избежать разрыва, надо обеспечить условие прочности опасного сечения, что возможно лишь при применении металла повышенных прочности и упрочняемости при достаточно высокой пластичности.
Третий способ вытяжки обладает наиболее благоприятными условиями деформирования, так как в этом случае прочность опасного сечения позволяет получить значительную степень деформации. Таким образом, для рассмотренных способов вытяжки необходимо выбирать металл с различными механическими свойствами или в различном состоянии: при первом способе вытяжки – повышенной пластичности при пониженной прочности (стали 08-10 в отожженном состоянии или нормализованием состоянии с дрессировкой); при втором – повышенной прочности при достаточно высокой пластичности (стали 08-10, 12Х18Н9Т); при третьем – без повышенных механических свойств.
Процесс вытяжки характеризуется коэффициентом вытяжки, который определяется по формуле:
К = DИlDЗ,
где DИ – диаметр получаемого изделия или полуфабриката, м;
DЗ – диаметр заготовки, м.
Коэффициенты вытяжки должны быть разными для деталей различной геометрической формы, а также для различной относительной толщины материала, от которой зависит большая или меньшая степень устойчивости фланца заготовки.
Оптимальные значения коэффициентов вытяжки цилиндрических деталей без фланца зависят от относительной толщины заготовки.
При разработке конструкции детали, получаемой вытяжкой листового материала, необходимо стремиться к тому, чтобы деталь можно было бы получить за наименьшее число переходов. В процессе вытяжки, как и при любой холодной пластической деформации, все металлы подвергаются упрочнению или наклепу, сопровождаемому повышением сопротивления деформированию и прочностных характеристик и понижением пластичности металла. На складе полуфабрикатов с недельным, а иногда и более длительным сроком хранения пооперационных заготовок процесс старения металла приводит к значительному снижению пластичности материала заготовки или полуфабриката. Все это вызывает необходимость применения межоперационного отжига.
Обычные способы вытяжки применяют почти во всех отраслях промышленности. Однако в ряде случаев они недостаточно рациональны и эффективны. Например, не всегда приемлема многооперационность процесса вытяжки деталей сложной формы, для которых требуется большое число штампов. В результате работы по дальнейшему улучшению и интенсификации процесса глубокой вытяжки созданы и освоены особые способы вытяжки.
Обратная вытяжка (с выворачиванием) – это объединение двух или более операций вытяжки, выполняемых за один рабочий ход (рис. 31). При этом каждая последующая вытяжка осуществляется в направлении, обратном предыдущему. Обратную вытяжку применяют в целях сокращения количества штамповочных операций.
Рис. 31. Схема вытяжки с выворачиванием
Последовательную вытяжку в ленте (рис. 32) выполняют при изготовлении полых деталей и осуществляют на многопозиционных штампах. Для предотвращения разрывов ленты коэффициент вытяжки принимают несколько большим, чем при обычной вытяжке. Так, в случае вытяжки деталей из низкоуглеродистых сталей и латуней для первой операции коэффициент вытяжки берут равным 0,68–0,72, а для второй операции – 0,80–0,85. Этот способ значительно повышает производительность штамповки.
Рис. 32. Схема штамповки по ленте
Вытяжку с утонением (рис. 33) применяют для изготовления тонкостенных деталей, при этом длина вытягиваемой детали увеличивается за счет уменьшения толщины стенок.
Обычно утонение стенок за один проход не превышает 30–35 % начальной толщины, что обеспечивается соответствующим выбором зазора между пуансоном и матрицей. При вытяжке с утонением толщина дна изделия не изменяется. Эту операцию можно осуществлять через несколько матриц, расположенных последовательно одна за другой.
Рис. 33. Схема вытяжки с утонением
Вытяжку резиной (рис. 34) выполняют резиновой подушкой (пуансоном) в жесткой матрице или жестким пуансоном в резиновой матрице. Оба способа применяют для получения полых деталей из тонколистового материала. Резиновую подушку заключают в металлическую обойму. Штампы для вытяжки резиной просты, так как изготовлять нужно лишь один деформирующий элемент (пуансон или матрицу), другой заменяется резиной. Необходимость создания высоких удельных давлений и быстрое изнашивание резины ограничивают область применения этого способа. Он используется в основном в условиях мелкосерийного и индивидуального производств.
Рис. 34. Схема вытяжки резиновой подушкой (пуансоном): 1 – контейнер с резиной; 2 – заготовка; 3 – матрица
При гидравлической вытяжке (рис. 35) полые детали цилиндрической, конической, сферической или другой формы получают надавливанием на заготовку непосредственно жидкостью или жидкостью, заключенной в эластичную (резиновую) оболочку. Этот способ особенно эффективен при изготовлении деталей сложной формы, так как при гидравлической вытяжке отпадает необходимость в изготовлении металлического пуансона и пригонки его к матрице. Недостаток гидравлической вытяжки – возможность значительного утонения металла в отдельных зонах, так как силы трения между заготовкой и матрицей приводят к возникновению больших растягивающих напряжений.
Рис. 35. Схема гидравлической вытяжки
Рис. 36. Схема отбортовки
Отбортовку подразделяют на два основных вида (рис. 36): отбортовка отверстий – образование бортов вокруг предварительно пробитых отверстий; отбортовка наружного контура – образование невысоких бортов по наружному криволинейному краю заготовок.
Отбортовку отверстий широко используют в штамповочном производстве, заменяя операции вытяжки, с последующей вырубкой дна. Особенно большую эффективность дает применение отбортовки отверстий при изготовлении деталей с большим фланцем, когда вытяжка затруднительна и требует нескольких переходов.
Геометрические размеры отбортовки определяют исходя из равенства объемов заготовки и детали. Обычно высота борта бывает задана чертежом детали.
Отбортовку лучше производить при большом зазоре между пуансоном и матрицей или при значительно увеличенном радиусе закругления матрицы. Такая отбортовка характеризуется большим радиусом закругления, но малой цилиндрической частью борта; ее применяют для увеличения жесткости конструкции при малой ее массе (например, при отбортовке крупных отверстий и окон в авиационных, транспортных, судостроительных конструкциях и т. д.).
Отбортовку с малым радиусом закруглений и большой цилиндрической частью борта можно применять лишь для небольших отверстий под резьбу, при запрессовке осей или когда конструктивно необходимо иметь цилиндрические отбортованные отверстия.
Успешное выполнение отбортовки зависит от чистоты среза деформируемой кромки. При наличии заусенцев по краю отверстия неизбежно образование трещин и разрывов.
Степень деформации при отбортовке отверстий определяют соотношением между диаметром отверстия (D) в заготовке и диаметром борта (d) или так называемым коэффициентом отбортовки К0 = d/D.
Величина К0 зависит от вида и свойств материала и отношения толщины заготовки к диаметру пробитого отверстия D = (S/d). Для стали с содержанием углерода 0,1 % при D, равном от 3 до 9, К0 = 0,60/0,45, а при D, равном от 67 до 100, К0 = 0,23/0,20.
В различных отраслях промышленности (электро-, радиотехника, приборостроение) применяют штамповку деталей, имеющих отверстия с высокими цилиндрическими стенками. В данном случае применяют операцию отбортовки с утонением стенок, так как при простой отбортовке для образования высокого цилиндрического борта не хватало бы площади заготовки. При этом обычно достигают значительной экономии металла (рис. 37).
Рис. 37. Схема отбортовки с утонением
Отбортовка с заданным утонением материала является более целесообразной вследствие большей устойчивости пластической деформации металла и отсутствия разрыва и трещин, так как в процессе утонения возникает более благоприятное напряженное состояние за счет появления значительных сжимающих напряжений. Это позволяет вести отбортовку при смягченных «неопасных» коэффициентах отбортовки, а высоту борта получить за счет максимально допустимого утонения материала. Производственный опыт показывает возможность утонения за одну операцию до S = (2,0/2,5)Si, где Si – толщина материала в отбортованной части.
В некоторых неответственных случаях допускается изготовление рваного борта путем проколки материала гвоздеобразным пуансоном. Этот способ отбортовки применяют для соединения деталей из тонкого материала (до 0,6 мм) взамен соединения заклепками, а также для получения отверстий с загнутыми кромками.
Дата добавления: 2021-07-19; просмотров: 191; Мы поможем в написании вашей работы! |
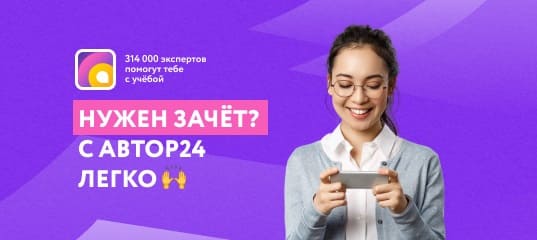
Мы поможем в написании ваших работ!