Гидроусилители КАУ-30Б и РА-60Б
Гидроусилители КАУ-30Б и РА-60Б, установленные в цепях управления вертолетом, снимают усилия с командных рычагов управления. На вертолете в цепях продольного, поперечного давления и управления общим шагом установлены три гидроусилителя КАУ-30Б, а в цепи путевого управления - РА-60Б. Схема установки гидроусилителей - необратимая. Все четыре гидроусилителя силовыми цилиндрами шарнирно устанавливаются в опорах с подшипниками, закрепленных шпильками на общем кронштейне, расположенном на картере главного редуктора ВР-14. Входные качалки жесткой проводкой соединяются с органами управления, а исполнительные штоки гидроусилителей КАУ-30Б продольного поперечного управления посредством тяг связаны с качалками продольно поперечного управления, КАУ-30Б управления общим шагом - с рычагом общего шага автомата перекоса: исполнительный шток РА-60Б - с качалкой сектора путевого управления.
Гидроусилитель КАУ-30Б в режиме ручного управления работает по гидромеханическому принципу, а в командном режиме - по электромеханическому принципу.
Основные технические данные КАУ-30Б
Рабочее давление жидкости МПа(кгс/см2).. 4,5±0,3...6,5 (45 – 65)
Максимальное усилие, развиваемое гидроусилителем при давлении в ГС 65 кгс/см2 и скорости штока, равной нулю, кгс (Н), не менее . 17 000 (1700)
Ход исполнительного штока, мм:полный. 74±2
рабочий. 70 (по 35 от нейтрального положения)
|
|
Ход распределительного золотника ручного управления, не более, мм. 1,2
Зона нечувствительности распределительного золотника, не более, мм. 0,2
Ход головки от нейтрального положения при комбинированном управлении, мм . ±6
Средняя скорость движения исполнительного штока при ручном управлении под переменной нагрузкой 0...+- 15 000 Н, мм/с, не менее 60
Допустимые утечки жидкости по уплотнениям подвижных соединений:
при работе, не более, см3/ч 0,4
при стоянке, не более, см3/сут 2
Рабочее напряжение питания микровыключателей и обмоток управления
реле, В 27±10%
Питание потенциометра ИПБ 45-1:напряжение, В 36±8
частота тока, Гц 400±8
Масса, кг 12
Основные составные части гидроусилителя КАУ-30Б (рис. 8.14): цилиндр, исполнительный шток с поршнем, шлиц-шарнир, узел входной качалки, узел головки (корпус головки, четыре штуцера для подачи жидкости из ОГС, ДГС и слива, фильтры, клапан включения систем, распределительный золотник ручного управления (РЗРУ), распределительный золотник комбинированного управления (РЗКУ) с управляющим золотником, редукционный клапан, клапан автоматического управления, цилиндр комбинированного управления, клапаны кольцевания силового цилиндра и цилиндра комбинированного управления, клапан включения комбинированного управления, стопор, поляризованное реле РЭП-8Т, бесконтактный потенциометр ИПБ-45-1, механизм возврата головки).
|
|
Рис. 8.14. Принципиальная схема работы гидроусилителя КАУ-30Б:
1,5 — фильтры; 2 — клапан включения питания от ОГС и ли ДГС; 3 — управляющий золотник; 4 — головка; 6 — редукционный клапан; 7,17 — дроссели; 8— распределительный золотник комбинированного управления; 9 — толкатель; 10-пружина; 11 — поляризованное реле; 12 — якорь поляризованного реле; 13 — штепсельный разъем; 14 — клапан кольцевания полостей силового цилиндра; I5 — распределительный золотник ручного управления; 16 — клапан кольцевания цилиндра комбинированного управления; 18 — клапан включения комбинированного управления; 19 — цилиндр комбинированного управления; 20 — шлиц-шарнир; 21 — силовой цилиндр; 22 — исполнительный шток; 23 — индукционный бесконтактный потенциометр ИПБ-45-1; 24 — механизм возврата головки в нейтральное положение; 25 — поршень комбинированного управления; 26 — стопор; 27 — наконечник для тяги управления; 28 — входная качалка.
|
|
Работа гидроусилителя КАУ-30Б возможна в трех режимах - ручного управления, комбинированного управления, „жесткой тяги".
Режим ручного управления гидроусилителя КАУ-30Б осуществляется при работающей ОГС и отключенном автопилоте, а также в случае питания гидроусилителей от ДГС. В этом режиме КАУ-ЗОБ работает как силовой следящий гидропривод.В исходном положении стопор фиксирует головку относительно исполнительного штока, так как сигнальное давление от выключенного крана ГА-192 не подводится. Якорь поляризованного реле РЭП-8Т находится в среднем положении, поэтому РЗКУ располагается в нейтральном положении, перекрывая рабочими поясками каналы подвода Т и С жидкости в полости цилиндра комбинированного управления. Клапан кольцевания цилиндра комбинированного управления сообщает обе полости цилиндра между собой. РЗРУ находится в нейтральном положении, закрывая рабочими поясками каналы Г и Д подвода жидкости в полости силового цилиндра.Жидкость подводится от работающей ОГС или ДГС к соответствующему штуцеру нагнетания I и IV, далее проходит к средней расточке РЗКУ по каналу А к редукционному клапану, создающему пониженное стабилизированное давление. Одновременно жидкость проходит в полость пружины клапана кольцевания силового цилиндра и создает дополнительное усилие к усилию пружины на удержание шариков клапана в закрытом положении, а также поступает к средней расточке РЗРУ.При отклонении командного органа в соответствующем направлении добустерная цепь управления вызывает отклонение входной качалки гидроусилителя и полный ход РЗРУ на 1,2 мм например вправо. Средняя расточка РЗРУ соединяет канал А с каналом Г и Н подачи в левую полость силового цилиндра, что вызывает под действием давления жидкости перемещение поршня с исполнительным штоком и головкой вправо и отклонение забустерной цепи управления рулевой поверхностью. Из правой полости силового цилиндра жидкость сливается через каналы М, Д, Б, штуцер слива соответствующей ГС. Но так как командный орган продолжает отклоняться, то РЗРУ вновь смещается вправо, и устанавливается определенное кольцевое окно, пропускающее жидкость в левую полость силового цилиндра, а также второе окно - сливное, сообщающее правую полость силового цилиндра с каналом слива Б. Если пилот остановит командный орган управления, то, поскольку жидкость с некоторым запаздыванием поступает в левую полость (давление распространяется со скоростью звука, а каналы имеют определенную протяженность), поршень с исполнительным штоком и головкой передвигается вправо до тех пор, пока каналы Г и Д не закроются рабочими поясками РЗРУ. Обе силовые полости заперты - рулевая поверхность зафиксирована. При перемещении РЗРУ влево гидроусилитель работает аналогично. РЗРУ соединяет при этом канал А с В, М и правой полостью силового цилиндра, а левая полость каналами Н, Г, Б соединена со сливом.
|
|
Режим комбинированного управления гидроусилителя КАУ-30Б - это режим автоматической стабилизации соответствующего параметра полета, установленного пилотом, в пределах 17% рабочего хода исполнительного штока гидроусилителя по командам автопилота. При этом КАУ-30Б работает одновременно как гидроусилитель ручного управления и как рулевая машина автопилота. Данный режим возможен только при работающей ОГС и включенное соответствующем канале автопилота. В исходном положении детали находятся в тех же позициях, что и при ручном управлении, только жидкость поступает в гидроусилитель от штуцера нагнетания ОГС. В полете, пилот установил необходимый режим полета, снял с помощью электромагнитных тормозов ЭМТ-2М усилие загрузочных механизмов, с ручки циклического шага, отпустил кнопку „Фрикцион" на ручке „шаг-газ", включил соответствующие каналы автопилота.Ручка управления при комбинированном режиме работы гидроусилителей остается неподвижной.
Подключаются гидроусилители к автопилоту тремя электромагнитными кранами ГА-192 при нажатии кнопок-ламп с зелеными светофильтрами на пульте управления автопилотом, располагающемся на центральном пульте.
При открытии электромагнитного крана жидкость поступает к штуцеру V гидроусилителя и по каналу поступает к клапану включения комбинированного управления, отжимает его поршень, который передвигает стопор в положение, при котором головка кинематически не связана с исполнительным штоком. Одновременно жидкость от этого канала смещает клапан кольцевания цилиндра комбинированного управления на разобщение обеих полостей цилиндра между собой.
Сигналы с датчиков автопилота, фиксирующие углы отклонения, угловую скорость относительно соответствующих осей вертолета, отклонения по высоте и скорости полета, поступают на вход агрегата управления автопилота раздельно по каждому каналу, суммируются, преобразуются, усиливаются и подаются в виде тока на обмотки поляризованного реле. Если режим полета, заданный пилотом, сохраняется, то якорь поляризованного реле находится в нейтральном положении, а элементы КАУ-ЗОБ занимают исходное положение. При отключении вертолета от заданного пилотом режима полета автопилот выдает преобразованный и усиленный сигнал рассогласования на соответствующую обмотку поляризованного реле. Если для восстановления исходного режима полета посредством отключения рулевой поверхности необходимо перемещение исполнительного шток вправо, то якорь поляризованного реле отклонится вправо, переместит вправо толкатель с управляющим золотником который увеличивает скорость слива жидкости из полости к и уменьшает из полости Л РЗКУ перемещается вправо под действием разности давлений жидкости, подводимой под пониженным давлением от редукционного клапана через дополнительный фильтр, - жидкость из канала А поступает под рабочим давлением в канал С и в конечном счете в левую полость цилиндра комбинированного управления. Вследствие этого головка смещается относительно неподвижного поршня комбинированного управления и РЗРУ влево, из правой полости цилиндра жидкость сливается по каналу через РЗКУ в канал Б. При этом открывается канал Г, и жидкость из канала А под рабочим давлением через РЗРУ поступает каналом Н в левую полость силового цилиндра, что вызывает перемещение поршня с исполнительным штоком вправо, отклонение рулевой поверхности, возвращение вертолета на режим, установленный пилотом. Такое положение сохраняется до тех пор, пока не восстановятся заданные параметры полета вертолета. В этот момент сигнал рассогласования достигает нуля. Якорь поляризованного реле становится в нейтральное положение, РЗКУ возвращается в исходное (нейтральное) положение, запираются обе полости цилиндра комбинированного управления, создается гидростопор, в результате чего головка совершает заключительное движение совместно с исполнительным штоком до тех пор, пока каналы Г и Л не закроются рабочими поясками РЗРУ что обеспечит гидростопорение исполнительного штока с поршнем, а значит и рулевой поверхности. Перемещение исполнительно штока КАУ-ЗОБ по сигналам стабилизации от автопилота ограничено 17% его рабочего хода, так как ход головки (т.е. исполнительного гидромотора рулевой машины автопилота) возможен на 12 мм. Такое ограничение для гидроусилителей КАУ-30Б, установленных в цепях продольного, поперечного управления и управления общим шагом, выбирается из условия обеспечения безопасности полета в случае отказа автопилота.Когда пилот переходит на ручное управление и отключает соответствующие каналы автопилота, жидкость из гидроусилителя сливается через штуцер у, через выключенный электромагнитный кран ГА-192 в бак ОГС. Поршень клапана включения в комбинированный режим возвращается своей пружиной в исходное положение, а стопор фиксирует головку относительно штока при совмещении их отверстий с помощью механизма возврата. Одновременно клапан кольцевания цилиндра комбинированного управления своими пружинами возвращается также в исходное положение, и обе полости цилиндра между собой сообщаются. Якорь реле РЭП-8Т, РЗКУ занимают исходное (нейтральное) положение.
Режим работы гидроусилителя КАУ-30Б „жесткая тяга" возможен при неработающих ОГС и ДГС. Все элементы гидроусилителя занимают исходное положение, рассмотренное ранее при режиме ручного Управления, только жидкость не поступает и не сливается через штуцера I, II, I II, IV. Шарики клапана кольцевания силового цилиндра прижаты к своим седлам только усилием пружины. При отклонении командного органа управления пилотом происходит перемещение входной качалки до упора, передача управляющего усилия на головку далее через стопор на исполнительный шток. Если отклонение входной качалки до упора вызывает перемещение в влево, исполнительный шток смещается также влево. Жидкость из левой (уменьшающейся по объему) полости силового цилиндра вытесняется по каналу Н к шарику клапана кольцевания силового цилиндра, отжимает его, проходит к среднему каналу у РЗРУ и далее через каналы Д, В, М поступает в правую (увеличивающуюся по объему) полость силового цилиндра. Пилот непосредственно за счет своей мускульной энергии управляет рулевой поверхностью, а КАУ-ЗОБ в режиме „жесткой тяги" обеспечивает кинематическую связь цепи управления, при этом предотвращается образование гидрозамка в полостях силового цилиндра.
Гидроусилитель РА-60Б (рис. 8.15), установленный в цепи путевого управления, по своей конструкции в основном идентичен гидроусилителю КАУ-30Б.
Рис. 8.15. Принципиальная схема работы гидроусилителя РА-60Б:
1...24 — см. рис. 8.10; 25 — микровыключатель; 26 — поршень комбинированного управления; 21 — пружинный упор узла микровыключателей; 28 — стопор; 29 — винтовой упор; 30 — плунжер; 31 - кронштейн; 32 — двуплечая качалка пружинных упоров; 33 — скоба; 34 — вилка; 35 — входная качалка; 36 — наконечник для тяги управления; I, II, III,IV — каналы, соединенные с трубопроводами нагнетания ОГС, слива ОГС, слива ДГС, нагнетания ДГС соответственно; V- канал подвода жидкости для включения гидроусилителя в комбинированный режим управления.
Конструктивными отличиями гидроусилителя РА-60Б являются наличие механизма перегонки, установка микровыключателей управления электромагнитным тормозом ЭМТ-2М путевого управления, измененный профиль лысок на РЗРУ и увеличенный до 2,1 мм ход РЗРУ.
Механизм перегонки включает в себя удлиненное плечо входной качалки, жесткую вилку, пружинные упоры (качалка, два плунжера, пружина), два винтовых упора. Винтовые упоры вворачиваются и стопорятся в отверстиях на скобе, связанной со штоком гидроусилителя. Два плунжера с пружиной, расположенной между ними, установлены внутри расточки качалки, подвешенной с помощью болта на кронштейне, соединенном с головкой. Качалка пружинных упоров жесткой вилкой подсоединяется к удлиненному плечу входной качалки.
Два микровыключателя устанавливаются с помощью стоек на головку гидроусилителя. Пружинные упоры узла микровыключателей размещены внутри корпуса, закрепленного на кронштейне скобы.
Гидроусилитель РА-60Б может работать в режимах ручного и комбинированного управления, „жесткой тяги" и „перегонки". Три первые режима работы аналогичны рассмотренным ранее для гидроусилителя КАУ-30Б.
Режим „перегонки" - режим автоматической стабилизации угла курса вертолета, установленного пилотом, в пределах 17...100 % рабочего хода исполнительного штока гидроусилителя РА-60Б по командам от автопилота. Расширение диапазона автоматической стабилизации параметров полета до максимально-возможного значения для РА-60Б обусловлено относительно безопасными последствиями при отказе автопилота, а также необходимостью -автоматической стабилизации в больших пределах в связи со значительными отклонениями параметров при внешнем возмущении (боковой ветер). Когда пилот установит необходимый курс вертолета, снимет усилие с пружины загрузочного механизма включением механизма ЭМТ-2М и освободит педали, микровыключатели под гашетками включат автоматически стабилизацию вертолета по курсу с помощью автопилота - начинается работа гидроусилителя РА-60Б в режиме комбинированного управления, который аналогичен рассмотренному для КАУ-30Б.В случае необходимости восстановления исходных параметров -полета (заданного пилотом угла курса), когда якорь поляризованного реле отклоняется, например, вправо под действием управляющего сигнала от автопилота, РЗКУ передвигается вправо.Жидкость под рабочим давлением движется из канала А по каналу С в левую полость цилиндра комбинированного управления. При этом головка смещается влево относительно штока и неподвижного РЗРУ, что вызывает сообщение канала А через средний канал у РЗРУ с каналами Г и Я. Жидкость поступает в левую полость силового цилиндра, в результате чего исполнительный шток с поршнем передвигается вправо. Это передвижение осуществимо в комбинированном режиме до тех пор, пока поршень комбинированного управления не упрется в упор цилиндра, что свидетельствует о том, что комбинированный режим управления завершен и дальнейшее поддержание открытыми каналов подачи жидкости в полости силового цилиндра за счет смещения головки относительно неподвижного РЗРУ невозможно. И если якорь реле РЭП-8Т по-прежнему отклонен вправо, что свидетельствует о неполном восстановлении заданного пилотом режима, то наступает режим „перегонка". Но как только поршень комбинированного управления должен стать на упор, левый пружинный упор механизма перегонки коснется левого винтового упора, верхнее плечо качалки пружинных упоров отклонится вправо, а нижнее - влево. Это вызовет отклонение удлиненного плеча входной качалки влево, а РЗРУ - вправо, и каналы, по которым жидкость поступала в левую полость силового цилиндра, остаются открытыми. Исполнительный шток продолжает перемещаться с постоянной скоростью в том же направлении, и автоматическая стабилизация режима полета продолжается до тех пор, пока на вход привода не поступит сигнал стабилизации обратного знака. Поскольку в режиме „перегонки" передвигается входная качалка вместе с головкой и исполнительным штоком, это вызывает перемещение добустерной цепи управления и педалей, которые были неподвижны в режиме комбинированного управления. Одновременно с началом режима «перегонки» происходит касание правым микровыключателем пружинного упора и замыкается цепь питания электромагнитного тормоза ЭМТ-2М путевого управления, который снимает нагрузку с педалей, создаваемую пружинным загрузочным механизмом. Это предотвращает травмирование ног пилота при смене знака стабилизации. Когда пилот берет управление на себя посредством нажатия на гашетки педалей, отключается стабилизация вертолета по курсу, но происходит коррекция от автопилота по угловой скорости рыскания вертолета при комбинированном режиме управления гидроусилителя в малых диапазонах. При снятии ног с гашеток происходит автоматическое включение стабилизации по углу курса для удержания вертолета на новом курсе.
8.4. ТЕХНИЧЕСКОЕ ОБСЛУЖИВАНИЕ ГИДРОСИСТЕМЫ ВЕРТОЛЕТА
При оперативном обслуживании в соответствии с видом подготовки по регламенту осуществляется:
- контроль уровня масла в гидравлическом баке по масломерному стеклу и дозаправка при необходимости;
- внешний осмотр гидроусилителей КАУ-30Б, РА-60Б, агрегатов, трубопроводов, шлангов гидросистемы, проверка их крепления, герметичности, отсутствия внешних механических повреждений;
- проверка плавности перемещения исполнительных штоков гидроусилителей КАУ-30Б и РА-60В в полном диапазоне отклонения ручек циклического шага и „шаг-газ", педалей при включенных основной и дублирующей гидросистемах.
При периодическом обслуживании согласно действующему регламенту производится:
- проверка герметичности и работоспособности основной и дублирующей гидросистем от наземной гидроустановки;
- снятие, осмотр, замена фильтроэлементов гидроусилителей КАУ-30Б, РА-60Б;
- проверка зарядки гидроаккумуляторов азотом с помощью приспособления;
- визуальный контроль качества масла АМГ-10;
- осмотр и проверка кронштейна крепления гидроусилителя к корпусу вала несущего винта главного редуктора на предмет отсутствия механических повреждений, трещин, а также момента затяжки гаек крепления опор гидроусилителей.
Проверка уровня масла АМГ-10 в гидробаке производится при отсутствии давления в системе и проверяется уровень в баках ОГС и ДГС по масломерным стеклам (уровень должен быть между нижними и верхними рисками). При количестве масла на уровне, равном или ниже нижней риски, следует произвести дозаправку гидравлической системы. В случае заметного снижения уровня масла в гидробаке после предшествующего оперативною обслуживания следует проверить зарядку гидроаккумуляторов азотом с помощью приспособления с манометром, так как вероятно разрушение резиновой диафрагмы гидроаккумулятора. При заправке гидравлической системы по указателю манометра ДИМ-100 (УИ1-100) при включенных источниках переменного и постоянного тока следует убедиться, что в ОГС и ДГС отсутствует давление. При наличии остаточного давления в системе нужно снизить его до нуля: включить гидросистему и произвести отклонение командных органов управления. Заправку системы осуществляют маслом АМГ-10, предварительно отстоявшимся в стеклянной таре не менее суток, до нормального уровня 22 л только закрытым способом посредством наземной гидроустановки типа УПГ-250 (УПГ-300, УПГ-250 ГМ, ЭГУ-3). Для этого следует предварительно убедиться в чистоте фильтров тонкой очистки гидроустановки, отсутствии механических частиц, воды в масле АМГ-10 в гидроустановке, открыть перекрывные краны 630600. Шланг нагнетания наземной гидроустановки через специальный переходник подсоединить к бортовому клапану всасывания ОГС Для этого нужно предварительно убедиться в чистоте наконечника нагнетания и протереть клапан всасывания чистой салфеткой, а затем включить наземную гидроустановку, контролируя уровень масла по масломерным стеклам баков ОГС и ДГС. При достижении уровня масла верхних рисок по масломерному стеклу (это соответствует примерно 20 л масла в гидробаке) гидроустановку выключить, перекрывные краны 630600 закрыть. В случае заправки масла в „сухую" ОГС или ДГС необходимо удалить воздушные пробки из системы через всасывающий шланг гидронасоса НШ-39М (отвернув гайку на 2...5 ниток резьбы) и через специальный шланг с наконечником (подсоединенным к бортовому клапану всасывания соответствующей гидросистемы), сливая масло в емкость до появления струи без воздушных пузырьков. После чего следует проверить работоспособность ОГС и ДГС от наземной гидроустановки и уровень масла в гидробаках и дозаправить при необходимости гидросистему. В исключительных случаях при отсутствии гидроустановки для заправки гидросистемы разрешается заправка гидросистемы открытым способом через заливную горловину гидробака с использованием воронки с сеткой, батистового или шелкового фильтра. О проделанной работе обязательно делается запись в формуляре вертолета.
При отсутствии масла АМГ-10 в гидросистеме запрещаются работы с прокруткой трансмиссии для предотвращения выхода из строя гидронасосов НШ-39М ОГС и ДГС (масло АМГ-10 в насосах смазывает рабочие детали).
Для слива масла из гидросистемы необходимо выполнить подготовительные операции, открыть краны 630600 и подсоединить шланги наземной гидроустановки к бортовым клапанам всасывания и нагнетания ОГС и ДГС, включить установку. При достижении рабочего давления 4,5±3...6,5 МПа (45+3...65 кгс/см2) в ОГС поработать органами управления в течение 3...10 мин, выполнив 4...5 переключений с ОГС на ДГС. После этого следует выключить наземную гидроустановку, стравить давление в гидросистеме до нуля, отсоединить шланги от бортовых клапанов всасывания и нагнетания. Затем поочередно нужно слить масло из ОГС и ДГС в чистую емкость через батистовый или шелковый фильтр с предварительным подсоединением к бортовым клапанам всасывания специального шланга с наконечником. Полный слив масла из трубопроводов нагнетания производится после отжатия бортового клапана нагнетания латунным или дюралюминиевым стержнями.В случае обнаружения в слитом масле АМГ-10 механических частиц, воды следует заправить в гидросистему свежее масло АМГ-10, произвести прокачку системы и слив масла, а затем окончательно заправить свежее масло в гидросистему. В случае слива масла АМГ-10 после останова двигателей подключение гидроустановки не производить.
Для визуального контроля качества масла АМГ-10 в гидросистеме необходимо после выполнения подготовительных работ и открытия кранов 630600 (краны после окончания работ закрыть и законтрить) подключить наземную гидроустановку, создать рабочее давление в гидросистеме и произвести отклонение органов управления в течение 18... 10 мин на ОГС, а затем 3...5 мин - на ДГС» Затем следует слить масло АМГ-10 около 0,5...1,0 л поочередно из ОГС и ДГС через соответствующие бортовые клапаны всасывания в емкости, а затем аналогично из гидробака ОГС и ДГС по 0,3...0,5 л в чистую стеклянную тару и убедиться в отсутствии механических частиц, воды, помутнения масла. В противном случае слить 0,5... 1 л масла в емкость и повторно взять пробу. При повторном обнаружении в масле АМГ-10 механических частиц, воды, помутнения масло в гидросистеме заменить. После взятия проб дозаправить гидросистему. Пробу масла АМГ-10 можно брать после останова двигателей.
Для проверки работоспособности гидросистемы от наземной гидроустановки необходимо:
- обеспечить требуемую чистоту наконечников шлангов установки и штуцеров бортовых клапанов всасывания и нагнетания, открыть краны 630600; включить источники питания постоянного тока (напряжением 27 В ± 10 %) и однофазного переменного (36 В, 400 Гц);
- подсоединить шланги наземной гидроустановки к соответствующие штуцерам бортовых клапанов всасывания и нагнетания гидросистемы;
- включить оба АЗСГК-10 „Гидросист основн." и „Гидросист. дублир." переключатели ЛПГ-15К „Гидросист основн." и „Гидросист. дублир.", проконтролировать показания манометров по их указателям УИ 1-100;
- включить наземную гидроустановку и убедиться, что давление в ОГС возрастает и при давлении (3,5±0,16) МПа [(35±1,6) кгс/см2] загорится зелено табло „Основная включена", а давление в ДГС равно нулю. Если давление в ДГС достигло (2,5±0,16) МПа [(25±1,б) кгс/см2] быстрее, чем в ОГС, и давление в ОГС будет равно нулю, то включить ее с помощью кнопки „Откл. дублир." на средней панели электропульта. При рабочем давлении в ОГС (4,5±0,3...6,5 МПа [(45±3...65| кгс/см2)] произвести отклонение (10 циклов за минут; органов управления, перемещении которых должно быть плавным, без усилий и заеданий, рывков, вибраций;
- проверить герметичность ОГС при работе гидроусилителей (допускаются утечки по подвижным уплотнениям не более 0,4 см3/ч, а при стоянке вертолета - до 2 см3/сут при давлении рабочей жидкости не более 0,15 МП (1,5кгс/см2));
- выключить переключатель ОГС и отклоняя органы управления, зарегистрировать момент падения давления ОГС до (3,5±0,16) МПа (35±1,6) кгс/см2 когда погаснет табло „Основная включена", а при (3±0,5) МПа. (30±5) кгс/см2 включится в работу ДГС и давление ней будет нарастать. При давлении ДГС (2,5+0,16) МПа [(25±1,6) кгс/см2 загорается красное табло „Дублир.включена"; при достижении рабочего давления в ДГС (4,5±0,3...6,5 ) МПа [(45±3...65 ) кгс/см2] проверить плавность хода органов управления, герметичность ДГС; включить выключатель ОГС, но давление в ОГС не возрастает; нажать кнопку „Откл. дублир." и удерживать ее до тех пор, пока давление в ОГС не достигнет (3,5±0,5) МПа [(35±5) кгс/см2], а давление в ДГС не упадет до нуля (табло „Основная включена" загорится, а „Дублир. включена" - погаснет), и отпустить кнопку. Давление в ОГС быстро нарастает и при перемещении органов управления изменяется в пределах (4,5±0,3..., 6,5) МПа [(45±3...65) кгс/см2]; выключить наземную гидроустановку и методом „стравливания" проверить давление зарядки азотом гидроаккумулятора (давление падает плавно до (3+0,2) МПа f(30±2) кгс/см2], а затем резко до нуля). В случае несоответствия давления в гидроаккумуляторе техническим условиям проверить зарядку с помощью приспособления с манометром.Аналогично проверяют зарядку азотом гидроаккумулятора ДГС, для чего предварительно выключают ОГС, включают наземную гидроустановку и создают давление в ДГС (4,5±0,3...6,5) МПа [(45±3...65) кгс/см2], выключают наземную гидроустановку, АЗС и выключатели ОГС, ДГС, отключают источники питания. Отсоединяют шланги от бортовых клапанов всасывания и нагнетания, устанавливают заглушки, закрывают и контрят краны 630600.
8.КОНТРОЛЬНЫЕ ВОПРОСЫ И ЗАДАНИЯ.
1. Каково назначение гидравлической системы вертолета?
2. Как осуществляется контроль за работой гидросистемы в эксплуатации?
3. Где размещены агрегаты гидросистемы вертолета?
4. Назначение и конструкция фильтров гидросистемы вертолета. Чем объяснить различие в их конструкции?
5. Используя рисунок , проследите изменение положения узлов агрегата ГА-74М/5 при запитывании и обесточивании катушки электромагнита. К каким последствиям это приведет?
6. Используя рисунок 9.10, проследите изменение положения узлов агрегата ГА-59/1 при изменении давления в основной гидросистеме. К каким последствиям это приведет? Ответ поясните, используя также рисунок 9.1.
7. Используя рисунок 9.17, проследите изменение положения узлов агрегата КАУ-30Б при: - падении давления в основной гидросистеме;- падении давления в основной и дублирующей гидросистеме включении автопилота;- перемещении летчиком командных рычагов в кабине.
8. Какие существуют отличия в конструкции агрегатов КАУ-30Б и РА-60Б, чем объяснить их наличие?
9.СИСТЕМА ОТОПЛЕНИЯ И ВЕНТИЛЯЦИИ
Вертолет оборудован системой отопления и вентиляции, которая обеспечивает подачу подогретого или атмосферного воздуха в кабины вертолета с целью поддерживания в них нормальных температурных условий. Система отопления и вентиляции обеспечивает обогрев ног пилотов, обдув передних стекол и блистеров кабины экипажа, а также фильтра-отстойника воздушной системы вертолета.
9.1. ОБЩИЕ СВЕДЕНИЯ
В систему отопления и вентиляции вертолета (рис. 9.1) входят: обогреватель КО-50 8, правый и левый отопительные короба 10 и 13, распределитель 9, соединительные трубы 14, короб 15 обдува передних стекол и блистеров, заслонки 18 подачи воздуха к ногам летчика, заслонки 2 и 4 управления системой обогрева и вентиляции, рукоятка 6 управления заслонками распределителя.
Керосиновый обогреватель КО-50 установлен с внешней стороны правого борта фюзеляжа перед правым подвесным топливным баком и закрыт специальным капотом-обтекателем. Обогреватель притянут лентами к кронштейнам, которые, в свою очередь закреплены к каркасу фюзеляжа при помощи тяг и вильчатых болтов. Керосиновый обогреватель может работать в режиме отопления или в режиме вентиляции.
В режиме отопления вентилятор 7 обогревателя забирает воздух из атмосферы через воздухозаборник капота обогревателя или для ускоренного прогрева из грузовой кабины через отверстие в правом борту фюзеляжа. Заслонка 4 воздухозаборника вентилятора обогревателя и заслонка 2 забора воздуха из кабины кинематически связаны между собой и управляются рукояткой 5, которая установлена на правом борту между шпангоутами №2 и 3. Если заслонка 4 открыта, воздух из атмосферы через сетку 3 поступает в обогреватель 8. При ускоренном прогреве кабин (рециркуляция) открыта заслонка 2. В этом случае вентилятор 7 засасывает воздух из грузовой кабины и подает его в обогреватель. Кроме крайних положений заслонок 2 и 4, их можно устанавливать в промежуточные положения, при этом воздух одновременно забирается как из атмосферы, так и из грузовой кабины. От вентилятора холодный воздух подается параллельно в калорифер и камеру сгорания, куда одновременно через форсунку подается топливо. Сгорая, топливовоздушная смесь горячими газами нагревает стенки калорифера, а продукты сгорания отводятся за борт в атмосферу. Холодный воздух, циркулируя по каналам калорифера, нагревается от его стенок и подается в распределитель 9, где разделяется на два потока: один из них подается в грузовую кабину, другой — в кабину экипажа. В распределителе установлены две заслонки 21, кинематически связанные между собой дифференциальным механизмом 20. В зависимости от положения заслонок нагретый воздух может подаваться либо в грузовую кабину, либо в кабину экипажа, либо в обе кабины одновременно в разных регулируемых пропорциях.
Рис.9.1. Схема расположения агрегатов системы отопления и вентиляции кабин вертолета:
1,3— сетки; 2, 4— заслонки; 5— рукоятка управления заслонками воздухозаборника и забора воздуха из грузовой кабины; 6— рукоятка управления заслонками распределителя; 7— вентилятор обогревателя; 8— обогреватель КО-50; 9— распределитель; 10— правый короб;.11— фильтр-отстойник воздушной системы; 12— раструб обогрева фильтра-отстойника; 13— левый короб; 14— соединительные трубы; 15— короба обдува передних стекол и блистеров; 16— трубопровод; 17— рукоятка управления заслонкой патрубка подачи воздуха к ногам летчика; 18—заслонка патрубка подачи воздуха к ногам летчика;. 19— передний патрубок; 20— дифференциальный механизм; 21— заслонка распределителя; 22— вильчатый болт; 23— кронштейны; 24— тяга
На обогрев грузовой кабины нагретый воздух поступает в правый отопительный короб 10, откуда по соединительным трубам 14, проложенным под полом грузовой кабины, в левый отопительный короб 13. В кабину экипажа из распределителя 9 воздух подается по гибкому трубопроводу 16.
Отопительные короба 10 и 13 изготовлены из листового дюралюминия и имеют теплоизоляционный слой. Между коробами и внутренней обшивкой фюзеляжа также проложены теплоизолирующие прокладки. В стенках правого и левого коробов имеются отверстия для выхода теплого воздуха, размеры и размещение которых обеспечивают равномерное распределение его по всей грузовой кабине.
В задней части левого отопительного короба выведен патрубок, заканчивающийся раструбом 12, через который теплый воздух подается на обогрев фильтра-отстойника 11 воздушной системы. Трубопровод 16, подающий воздух в кабину экипажа, проложен под полом грузовой кабины и кабины экипажа и соединен с передним патрубком 19. От патрубка гибкие соединительные магистрали подходят к левому и правому патрубкам с заслонками 18, через которые воздух подается к ногам пилотов. Расход воздуха через заслонки можно регулировать поворотом рукояток 17. У бортов кабины ответвления трубопровода заканчиваются коробами 15, подведенными к каркасу остекления кабины. Из этих коробов воздух направляется на передние стекла и блистеры через отверстия в стенках.
В режиме вентиляции открывается заслонка 4, а заслонка 2 закрывается, после чего включается вентилятор 7 обогревателя без подачи топлива в последний. В этом случае воздух поступает из атмосферы через воздухозаборник и подается (без подогрева) в выходной распределитель 9 и далее в кабины по тем же каналам, что и в режиме отопления. Вытяжная вентиляция кабин транспортного вертолета осуществляется через заслонку и жаберные щели, установленные на левой грузовой створке.
9.2. КЕРОСИНОВЫЙ ОБОГРЕВАТЕЛЬ КО-50
Керосиновый обогреватель КО-50 предназначен для подогрева воздуха, поступающего в кабины вертолета.
Основные технические данные
Номинальная теплопроизводительность на земле при перепаде температур воздуха 130°С и напряжении 27 В, ккал/ч не менее 50000
Применяемое топливо керосин Т-1, ТС-1, Т-2
Давление топлива на входе в насос, кгс/см2 .не более 0,3...1,3
Давление топлива за насосом, МПа (кгс/см2) 0,2 + 0,05(2 + 0,5)
Расход топлива, кг/ч не более 8,7
Расход воздуха через обогреватель при напряжении 27 В и давлении за обогревателем 100 мм вод. ст., кг/ч 1760
Потребляемая электрическая мощность при напряжении 27 В, кВт 2,5
Высотность, м до 5000
Масса обогревателя, кг не более 47,5
В комплект керосинового обогревателя КО-50 (рис.9.2) входят: обогреватель, вентилятор, топливная коробка, два пневмореле, блок управления регулятора температуры, электромагнитный клапан, два приемника температуры, задатчик температуры, агрегат зажигания, два датчика температуры, два термопереключателя и термовыключатель.
Рис. 9.2. Керосиновый обогреватель КО-50:
1,3—термопереключатели; 2— термовыключатель; 4— датчик температуры; 5— обогреватель;6—вентилятор; 7— топливная коробка; 8— пневмореле; 9— приемник температуры; 10— пусковая катушка; 11—электромагнитный клапан; 12—задатчик температуры; 13— блок управления регулятора температуры; 14 — высоковольтный привод
Обогреватель (рис. 9.3) состоит из камеры сгорания и калорифера, изготовленных из жаропрочной стали. Камера сгорания обеспечивает сгорание топливовоздушной смеси и состоит из конуса и цилиндра с вваренным дном. В передней части конуса по окружности расположены круглые и щелевые отверстия для лучшего завихрения топочного воздуха и смесеобразования. В конусной части камеры сгорания установлены топливная форсунка с перепуском и запальная свеча.
Подогреватель топлива установлен на кожухе обогревателя.
Рис. 9.3. Обогреватель
1— кожух; 2— топливная форсунка; 3— камера сгорания; 4— калорифер; 5— подогреватель топлива; 6— запальная свеча; 7— выхлопной патрубок
Калорифер предназначен для нагрева холодного воздуха, поступающего от вентилятора в кабины вертолета. Он состоит из цилиндра с приваренным кольцом и переходниками (газоходами), соединяющими камеру сгорания с калорифером. К внешнему цилиндру калорифера приварен выхлопной патрубок, отводящий продукты сгорания в атмосферу. Для улучшения теплоотвода поверхности цилиндров камеры сгорания и калорифера имеют сферические штампованные выпуклости, расположенные в шахматном порядке. В передней части обогревателя установлен воздухозаборник с дефлектором, состоящий из каркаса и приклепанной к нему обшивки с обтекателем
Запальная свеча СД-96 обеспечивает воспламенение топливовоздушной смеси в камере сгорания обогревателя. Воспламенение осуществляется искродуговым разрядом тока высокого напряжения от пусковой катушки зажигания КП-4716. Зазор между электродами свечи – около 4 мм.
Вентилятор (рис. 9.4) предназначен для продува воздуха через обогреватель и подачи топочного воздуха в камеру сгорания.
Рис. 9.4. Вентилятор
1— направляющий аппарат; 2— рабочее колесо; 3— спрямляющий аппарат; 4— электродвигатель; 5— шпонка; 6— гайка
В комплект вентилятора входят электродвигатель МВ-1200, направляющий аппарат,рабочее колесо и спрямляющий аппарат. Электродвигатель установлен на фланце спрямляющего аппарата, рабочее колесо крепят на носке вала электродвигателя гайкой и фиксируют от проворачивания шпонкой, а направляющий аппарат соединен винтами со спрямляющим аппаратом. Спрямляющий аппарат, рабочее колесо и направляющий аппарат изготовлены из алюминиевого сплава. К фланцу спрямляющего аппарата крепится переходник, соединяющий вентилятор с обогревателем.
Топливная форсунка (рис. 9.5) предназначена для распыла топлива, поступающего в камеру сгорания обогревателя, а также перепуска части топлива в бак при работе обогревателя на режиме пониженной теплопроизводительности. В резьбовую расточку корпуса 3 форсунки ввернуты переходник с соплом 1 и втулка 6 с фильтром 2. Втулка имеет два штуцера 4 и 5, соединенные с каналами для подвода и перепуска топлива. Топливо подводится к форсунке и через фильтр и сопло подается в камеру сгорания, а при перепуске через штуцер 5 частично отводится из форсунки в топливную коробку и далее в бак.
Рис. 9.5. Форсунка с перепуском
Подогреватель (рис. 9.6) топлива обеспечивает подогрев керосина, подаваемого в камеру сгорания перед запуском обогревателя для достижения лучших условий запуска. Подогрев осуществляется спиралью 3, вмонтированной в стальном корпусе 2. Внутри корпуса установлен чувствительный элемент, состоящий из медной трубки 4 и стержня 5, изготовленного из инвара.
Рис. 9.6. Подогреватель топлива
При подаче питания на спираль топливо, проходя через подогреватель, нагревается и при достижении заданной температуры стержень 5 чувствительного элемента через рычажное устройство 6 воздействует на кнопку микровыключателя 1, который обесточивает спираль 3 подогревателя топлива.
Топливная коробка предназначена для фильтрации топлива, поддержания постоянного давления его перед форсункой, открытия и закрытия доступа топлива в камеру сгорания и перепуска части топлива из форсунки при работе обогревателя на пониженной теплопроизводительности. Для надежного топливопитания керосинового обогревателя КО-50 и отключения питания в экстренных случаях в магистрали подвода топлива от правого подвесного топливного бака к топливной коробке обогревателя установлены электромагнитный кран 610200А и топливный насос 748А.
Топливная коробка (рис. 9.7) имеет две рабочие линии. Линия подачи топлива от насоса 748А к форсунке состоит из топливного фильтра 2, регулятора 6 давления, электромагнитного топливного клапана 1, трубопроводов и соединительной арматуры. Перепускная линия, имеющая две магистрали на входе и одну на выходе, состоит из двух электромагнитных топливных клапанов 5,7, жиклера 4 большого расхода топлива, жиклера 3 малого расхода топлива, трубопроводов и соединительной арматуры.
Рис. 9.7. Топливная коробка
Корпус топливной коробки изготовлен из нержавеющей листовой стали, состоит из двух половин и соединен после монтажа агрегатов винтами.
Электромагнитные клапаны 772 предназначены для открытия или закрытия рабочих линий топливной коробки. Каждый клапан (рис. 9.8) состоит из корпуса 7, катушки 5, сердечника 3, якоря 6, пружины 4, колпака 2 и контакта 1. Корпус имеет два резьбовых отверстия под штуцера подвода и отвода топлива. На корпусе совместно с колпаком 2 закреплены катушки 5, один конец обмотки которой припаян к сердечнику 3, а другой выведен к контакту 1. Якорь 6 прижат к седлу корпуса 7 пружиной 4 через штифт, обеспечивая герметичность между полостями входа и выхода.
Рис. 9.8. Электромагнитный клапан 772:
Электромагнитные клапаны открываются по сигналам, поступающим от блока управления в зависимости от температуры воздуха в кабине, на входе и выходе из обогревателя.
Жиклеры, установленные на входе в электромагнитные топливные клапаны 5 и 7(рис. 9.7), обеспечивают дозировку перепускаемого топлива. Они отличаются один от другого размером проходного отверстия. Жиклер 3 имеет отверстие диаметром 0,36 ± 0,01 мм, жиклер 4— 0,47 ± 0,01 мм.
Регулятор давления 773Н-2С предназначен для поддерживания постоянного давления топлива величиной 0,16 ± 0,01 МПа (1,6 ± 0,1) кгс/см2, подаваемого к форсунке. Регулятор состоит из корпуса 6 (рис. 9.9), крышки 5, мембраны 1, пружины 3, штока 2, седла 7, клапана 9 с пружиной, регулировочного винта 4, штуцера подвода топлива с сетчатым фильтром 8 и штуцера отвода топлива.
Рис. 9.9. Регулятор давления 773Н-2С:
Усилиями со стороны редукционной пружины 3 шток 2 удерживает клапан 9 в открытом положении. Топливо, поступающее через штуцер входа и фильтр, проходит в каналы седла 7 клапана и через штуцер выхода подается к электромагнитному клапану. При повышении давления топлива больше расчетного мембрана 1 регулятора, прогибаясь, сжимает пружину 3. Клапан 9 под действием своей пружины перемещается вверх и прикрывает доступ топлива в рабочую полость регулятора, и следовательно, в магистраль подвода топлива к форсунке. При понижении давления топлива в рабочей полости регулятора пружина 3, воздействуя на мембрану 1 и шток 2, открывает клапан 9 для поступления топлива к форсунке. Регулирование давления топлива осуществляется винтом 4.
Топливный фильтр 774 обеспечивает очистку топлива, поступающего к форсунке от загрязнения. Фильтр (рис. 9.10) состоит из корпуса 6, крышки 5, стакана 3, фильтроэлемента 4, чашки 2 и пружины 1.
Рис. 9.10. Топливный фильтр:
Стакан совместно с чашкой, пружиной и фильтроэлементом установлен в центральной расточке корпуса и закрыт крышкой, вворачиваемой в корпус. Топливо через штуцер входа и отверстия в чашке поступает во внутреннюю полость фильтра и далее через полость, образованную стаканом и фильтроэлементом, подается к штуцеру выхода.
Пневмореле являются блокирующими элементами в системе подачи топлива к форсунке и предназначены для включения электромагнитного клапана 772 линии подачи топлива к форсунке при наличии напора за вентилятором и его отключения при отсутствии напора. Корпус пневмореле состоит из верхней и нижней частей, которые соединены между собой винтами. Между фланцами частей корпуса зажата мембрана, изготовленная из капронового волокна и соединенная с верхним и нижним дисками штифтом и чашкой. В верхней части корпуса с помощью скобы установлен микровыключатель с клеммами для подсоединения электропроводов. В нижней части корпуса смонтирована пружина, упирающаяся в чашку и втулку, установленную на регулировочном винте, который после тарировки контрится к скобе и закрывается крышкой. Принцип работы пневмореле основан на изменении мембраны при наличии напора в ее рабочей полости и включения цепи питания электромагнитного клапана.
Блок управления регулятора температуры предназначен для преобразования изменения сопротивления датчиков температуры в электрическое напряжение и подачи сигнала на электромагнитные клапаны 772 перепуска топлива из форсунки.Блок управления установлен в схеме автоматического регулятора температуры, служащего для поддержания заданной температуры воздуха в кабинах вертолета путем подачи сигналов на клапаны в зависимости от температуры в кабинах вертолета и на входе и выходе из обогревателя. Блок управления работает совместно: с двумя приемниками температуры типа П-9Т, установленными в разных точках кабины и соединенными параллельно; с двумя датчиками температуры, установленными на входе и выходе воздуха из обогревателя; с задатчиком температуры; с двумя топливными клапанами 772, изменяющими подачу топлива в камеру сгорания обогревателя.
Приемники температуры П-9Т установлены на потолочной панели в кабине фюзеляжа и служат в качестве датчиков для подачи сигнала на блок управления регулятора температуры. Каждый приемник температуры имеет вентилятор с электродвигателем Д-60Г, который засасывает воздух из кабины и подает его на обдув датчика для уменьшения его инерционности.
Задатчик температуры предназначен для задания нужной температуры воздуха в кабинах вертолета. Он представляет собой потенциометр, установленный в корпусе и снабженный ручкой управления со шкалой, проградуированной от 10 до 30°C.
Термовыключатель предназначен для автоматического отключения вентилятора при падении температуры воздуха на выходе из обогревателя 50 °С.
Термопереключатели предназначены соответственно для отключения подачи топлива в обогреватель при достижении температуры воздуха на выходе обогревателя 175 °С и отключения свечи СД-96 при достижении температуры воздуха на выходе из обогревателя 40
°С.
По конструкции термовыключатель и термопереключатели аналогичны и отличаются только температурой срабатывания.
Система зажигания предназначена для воспламенения топливовоздушной смеси в камере сгорания обогревателя, состоит из агрегата зажигания КВ-112 и свечи СД-96. Агрегат зажигания обеспечивает получение высокого напряжения, необходимого для работы свечи.
Керосиновый обогреватель может работать в режиме обогрева и на вентиляционном режиме. В режиме обогрева предусмотрено автоматическое и ручное регулирование температуры воздуха в кабинах.
Процесс работы обогревателя (рис. 9.11) в режиме обогрева (образование и зажигание смеси, электропитание, топливопитание и сохранение безопасной температуры воздуха) происходит автоматически. При этом температура воздуха поддерживается постоянной в зависимости от положения задатчика температуры в пределах от 10 до 30°С.
Ручной режим обеспечивает работу обогревателя на максимальном и среднем режимах теплопроизводительности.
Максимальный режим теплопроизводительности рекомендуется устанавливать при температуре наружного воздуха ниже —13°С, а средний режим — в пределах температур от — 13 до +15°С.
Работа обогревателя в вентиляционном режиме обеспечивает вентиляцию кабин в теплое время года. Режим рециркуляции служит для успешного запуска обогревателя и быстрого прогрева кабины вертолета в зимних условиях.
Керосиновый обогреватель рекомендуется включать при температуре наружного воздуха + 10°С и ниже на земле и в воздухе при работающих двигателях на всех режимах полета, кроме режима самовращения несущего винта. Основным режимом работы обогревателя КО-50 является автоматический.
Перед запуском обогревателя сливают топливо из дренажного бачка, включают АЗС ОБОГРЕВАТЕЛЬ, ПОДОГРЕВАТЕЛЬ, НАСОС, ТЕРМОМЕТР, задатчик температуры устанавливают в положение + 30°С, а переключатель АВТОМАТ — РУЧНОЙ ставят в положение АВТОМАТ. При этом открывается электромагнитный топливный клапан 26 подачи топлива от насоса ЭЦН-40 и включается насос 748А.
Для запуска обогревателя при включенном переключателе на 2...3 с нажимают кнопку ЗАПУСК КО-50. Тогда ток от переключателя поступает на контакты реле, которое срабатывает, и через контактор питание подается на спираль подогревателя. При этом загорается желтое сигнальное табло ПОДОГРЕВ ТОПЛИВА. При подогреве топлива до заданной температуры + 70 ± 5 °С чувствительный элемент подогревателя через рычажное устройство воздействует на кнопку микровыключателя, который замыкает цепь реле. В этом случае размыкается контактор и обесточивается спираль подогревателя, желтое сигнальное табло гаснет. Через реле замыкается цепь пусковой катушки и свечи, и одновременно загорается желтое сигнальное табло ЗАЖИГАНИЕ, сигнализирующее о включении свечи. Кроме этого, при срабатывании реле через контактор подается питание на электродвигатель вентилятора. От напора, создаваемого вентилятором, замыкаются пневмореле, открывается топливный клапан, обеспечивая доступ керосина к форсунке обогревателя.
Топливо от насоса ЭЦН-40 через электромагнитный клапан поступает в топливный насос, который под давлением (0,2 + 0,05) МПа [(2 + 0,5) кгс/см2] подает его в топливный фильтр. Отфильтрованное топливо поступает в регулятор давления, который поддерживает постоянное давление (0,16 + 0,01) МПа [(1,6 + 0,1) кгс/см2] на выходе.
Рис. 9.11. Принципиальная схема работы керосинового обогревателя КО-50:
1, 33 — переключатель; 2, 3, 5, 6, 32 — реле; 4, 34 — контакторы; 7, 28 — фильтры; 8 — вентилятор; 9, 19, 37 — сигнальные табло; 10 — пусковая катушка; 11 — электрическая свеча; 12 — форсунка; 13 — термовыключатель; 14, 16 — термопереключатели; 15 — датчик температуры; 17—подогреватель топлива; 18 — микровыключатель подогревателя топлива; 20 — пневмореле; 21, 22, 23 — электромагнитные топливные клапаны; 24 — регулятор давления топлива; 25 — топливный фильтр; 26—электромагнитный топливный кран 610200А; 27 —топливный насос 748А; 29 — блок управления регулятора температуры; 30 — задатчик температуры; 31 — приемник температуры; 35 — выключатель; 36 — пусковая кнопка
Из регулятора топливо через электромагнитный клапан и подогреватель поступает в форсунку и далее в камеру сгорания. После открытия электромагнитного клапана загорается зеленое сигнальное табло ОБОГРЕВАТЕЛЬ РАБОТАЕТ НОРМАЛЬНО, сигнализирующее о подаче топлива в камеру сгорания.
Одновременно воздух от работающего вентилятора через трубу перепуска воздуха поступает в камеру сгорания. Происходят смесеобразование и зажигание топливовоздушной смеси. Образующиеся в камере сгорания нагретые газы движутся по изолированным газоходам калорифера к выхлопному патрубку, отдавая тепло через стенки калорифера холодному воздуху, поступающему из атмосферы под напором вентилятора и проходящему по воздушным каналам калорифера.
При достижении температуры воздуха на выходе из обогревателя 40°С срабатывает термопереключатель, размыкается реле, гаснет желтое сигнальное табло, отключается свеча и агрегат зажигания. Это означает стабилизацию процесса горения.
В случае необходимости изменения температуры воздуха в кабинах ручку управления задатчика температуры переводят на отметку нужной температуры. Сигнал с задатчика температуры поступает на измерительный мост блока управления регулятора температуры. Блок управления срабатывает и выдает сигнал на электромагнитные клапаны линии перепуска топлива в бак. При выдаче сигнала блоком управления на закрытие клапанов все топливо, подходящее к топливной коробке, поступает через форсунку в камеру сгорания. Происходит сгорание большего количества топливовоздушной смеси, и температура воздуха на выходе из обогревателя повышается. При выдаче сигнала с блока управления на открытие клапанов часть топлива из форсунки поступает через перепускную линию в бак. Происходит сгорание меньшего количества топливовоздушной смеси, и температура воздуха на выходе из обогревателя понижается.
В случае повышения температуры воздуха на выходе из обогревателя до 175°С срабатывает термопереключатель, отключаются подача топлива и зеленое сигнальное табло. Обогреватель выключается, но вентилятор продолжает работать, удаляя продукты горения из камеры сгорания и охлаждая калорифер. При дальнейшем понижении температуры воздуха на выходе из обогревателя и достижении ее 50°С срабатывает термопереключатель и выключается электродвигатель вентилятора.
При работе обогревателя на ручном режиме переключатель АВТОМАТ — РУЧНОЙ устанавливают в положение РУЧНОЙ и нажимают пусковую кнопку. Дальнейший процесс запуска и работы обогревателя аналогичен работе КО-50 в автоматическом режиме, но автоматической регулировки заданной температуры в кабинах при этом не будет. В ручном режиме теплопроизводительность обогревателя регулируется переключателем РЕЖИМЫ. В режиме полной подачи все топливо поступает на форсунку, а в режиме средней подачи часть топлива сливается из форсунки через линию перепуска в бак. В первом случае обогреватель работает на полной теплопроизводительности 50000 ккал/ч, во втором — на пониженной теплопроизводительности 32000...40000 ккал/ч. Полную подачу рекомендуется ставить при запуске обогревателя в ручном режиме, а затем полную и среднюю подачу изменять в зависимости от температуры наружного воздуха.
Перед выключением обогревателя рекомендуется за 2 мин переключить его на режим рециркуляции для продувки его кабинным воздухом с целью удаления влаги.
При работе подогревателя в вентиляционном режиме включаются АЗС ОБОГРЕВАТЕЛЬ и выключатель ВЕНТИЛЯТОР. В этом случае вентилятором обогревателя воздух без подогрева подается в систему вентиляции. При необходимости перехода с автоматического управления на ручное или наоборот обогреватель выключают на 10...15 мин с целью его охлаждения и затем переключают на работу в другом режиме.
9.3. ТЕХНИЧЕСКОЕ ОБСЛУЖИВАНИЕ СИСТЕМЫ ОТОПЛЕНИЯ
Техническое обслуживание системы отопления и вентиляции заключается в контроле состояния агрегатов, воздухопроводов и трубопроводов этих систем. При этом обращают внимание на крепление и контровку агрегатов и воздухопроводов, выполняют работы по проверке исправности агрегатов с их демонтажем.
Воздухопроводы не должны иметь коррозии, проколов, надрывов, потертостей, а патрубки и короба — трещин, вмятин. Зазоры между воздухопроводами и элементами конструкции должны быть не менее 3 мм.
К трубопроводам подвода топлива к обогревателю КО-50 предъявляются такие же требования, что и к трубопроводам топливной системы. Ослабление крепления трубопроводов и воздухопроводов в колодках и хомутах, а также нарушение контровки не допускаются. Трубопроводы должны быть герметичны и не иметь трещин, глубоких потертостей и коррозии. Зазор между трубопроводами должен быть не менее 3 мм, а между трубопроводами и другими деталями не менее 5 мм.
Для обеспечения надежности запуска и работы КО-50 периодически снимают свечу и промывают в бензине. При наличии на контактах нагара свечу помещают на 10... 15 мин в бензин, промывают с помощью кисти и просушивают. После монтажа свечи во втулку к ней подсоединяют проводник от пусковой катушки и визуально проверяют интенсивность искры при напряжении источника питания 27В ± 10%, которая должна быть устойчивой. Зазор между лапками и центральным электродом свечи должен быть равен 3..3,5 мм.
Форсунку после снятия с КО-50 разбирают, ее детали промывают в керосине, продувают сжатым воздухом под давлением 0,15...0,2 МПа (1,5...2 кгс/ см2). После сборки форсунку проверяют на герметичность. Для этого на штуцер перепуска и отверстие сопла устанавливают заглушки. Через штуцер подвода топлива к форсунке под давлением от насоса 748А в течение 5 мин подается керосин. Утечка через соединения форсунки не допускается. После снятия заглушки из сопла в форсунку вновь подают топливо в течение 5 мин с проливом в емкость. Подтекание керосина на торцовой поверхности сопла, за исключением момента пуска и отсечки топлива, не допускается.
Расход топлива через форсунку определяется путем подачи к ней керосина через топливную коробку под давлением 0,2 МПа (2 кгс/см2) и сбора его в мерную емкость. Расход должен быть в пределах 168...172 см3/мин.
Для проверки конуса распыла топлива через форсунку ее устанавливают в вертикальное положение и альвейером создается давление керосина, поступающего к форсунке до (0,16 ± 0,01) МПа [(1,6 ± 0,1) кгс/см2] в течение 10 мин. Конус распыла должен быть симметричным относительно оси форсунки в двух взаимно перпендикулярных плоскостях без наличия крупных капель.
Для осмотра жиклеров магистрали перепуска топлива из форсунки необходимо отвернуть накидные гайки трубопроводов на электромагнитных клапанах. Вывернуть жиклеры, осмотреть их, промыть в чистом бензине, продуть сжатым воздухом и установить на место.
При контроле фильтра топливной магистрали керосинового обогревателя следует отсоединить трубопроводы подвода топлива к фильтру и форсунке, слива топлива из форсунки и топливной коробки, вскрыть топливную коробку и снять крышку сетчатого фильтра. Проверить состояние фильтра на отсутствие повреждения сетки и целостности уплотнительных колец, промыть фильтр в бензине и продуть воздухом под давлением не более 0,15...0,2 МПа (1,5...2 кгс/см2).
После обслуживания агрегатов, установленных в топливной коробке, следует проверить герметичность соединений топливной системы в коробке под давлением 0,25 МПа (2,5 кгс/см2). Подтекание топлива устраняется подтягиванием резьбовых соединений.
С целью повышения надежности работы КО-50 периодически проверяют техническое состояние калорифера и камеры сгорания обогревателя. Для этого следует снять капот обогревателя, отсоединить высоковольтный провод от свечи и электропровод от подогревателя топлива, а также отсоединить трубопроводы подвода топлива к подогревателю, отвода топлива из линии перепуска и от дренажного штуцера. Разъединив хомуты, снять резиновый переходник, а затем и обогреватель, предварительно отсоединив трубопроводы от выхлопного патрубка и форсунки. Снять с подогревателя втулку со свечой, трубопроводы перепуска и топочного воздуха. Отвернуть гайки, снять кожух с калорифера и осмотреть калорифер на отсутствие прогаров и трещин. Допускается дальнейшая эксплуатация калорифера с трещинами размером 5 х 1 мм при суммарной площади до 100 мм2. В случае наличия трещин больших размеров калорифер заменяют. После контроля калорифера и камеры сгорания производят монтаж агрегатов, коммутаций и подогревателя на место согласно предусмотренной технологии.
После выполнения работ по контролю состояния обогревателя КО-50 проверяют его работу. Для этого запускают обогреватель на автоматическом режиме и контролируют его работу в течение 2...3 мин. После выключения КО-50 его осматривают на предмет отсутствия течи топлива и надежности крепления частей, агрегатов, трубопроводов и соединительной арматуры, подвергавшихся демонтажу. Затем проверяют работу обогревателя в ручном режиме.
9.4. КОНТРОЛЬНЫЕ ВОПРОСЫ И ЗАДАНИЯ
1. Для чего предназначена система отопления и вентиляции вертолета?
2. Какие основные агрегаты входят в состав системы отопления и вентиляции вертолета?
3. В какие отсеки вертолета система отопления и вентиляции осуществляет подачу воздуха?
4. В чем отличие работы система в режиме отопления, в режиме вентиляции, при ускоренном прогреве кабин вертолета?
5. Как осуществляется регулирование температуры воздуха в кабинах вертолета? Какие агрегаты принимают участие в регулировании температуры в кабинах вертолета?
6.Какие основные агрегаты входят в состав обогревателя КО-50, каково их назначение?
10.ОБОРУДОВАНИЕ ВЕРТОЛЕТА
Оборудование вертолета является его составной частью и включает оборудование кабины экипажа и грузовой кабины, систему отопления и вентиляции, оборудование вертолета специальными устройствами в зависимости от его варианта и назначения, транспортное оборудование, авиационное и радиоэлектронное оборудование.
10.1 ОБОРУДОВАНИЕ КАБИНЫ ЭКИПАЖА
Кабина экипажа (рис. 10.1) является отсеком, в котором размещены сиденья экипажа, командные рычаги управления вертолетом, его системами и оборудованием, приборы и устройства, обеспечивающие контроль за работой систем и агрегатов вертолета и двигателей, а также аппаратура авиационного и радиоэлектронного оборудования.
На верхнем электропульте расположены: левая и правая панели автоматов защиты сети (АЗС), средняя, правая и левая панели, правый и левый электрощитки, правая и левая боковые панели. Верхний электропульт установлен на верхней жесткости потолка кабины. Для удобства осмотра и монтажа оборудования, а также устранения неисправностей панели и щитки могут быть откинуты на петлях, расположенных внизу, а сверху их крепят винтовыми замками.
Приборные доски с помощью специальных кронштейнов, склепанных из дюралюминиевых профилей и листов, закреплены к полу кабины.
В задней части кабины установлены сиденья для пилотов и бортмеханика
Сиденья пилотов установлены на полу кабины между шпангоутами № 3Н и 4Н.
Рис. 10.1. Общий вид кабины:
1— щитки управления фарами; 2, 22 — левая и правая приборные доски; 3, 20— светофильтры; 4, 19— вентиляторы; 5, 17 — левая и правая боковые панели электропульта; 6, 16— левый и правый электрощитки; 7, 15— левая и правая панели электропульта; 8, 13 — плафоны; 9, 14 — абонентские аппараты; 10, 12 — левая и правая панели АЗС; 11 — средняя панель электропульта; 18 — щиток предохранителей; 21— компас КИ13К; 23—пульт автопилота
Для крепления сидений (рис. 10. 2) на полу кабины закреплены болтами кронштейны 11, выполненные из магнитного сплава. Каждое сиденье состоит из чашки 1 и спинки 3, изготовленных из дюралюминиевых листов, склепанных между собой и подкрепленных штампованными профилями. Сиденье к кронштейнам 11 крепится при помощи литой рамы 8, направляющих 7 и двух стоек 9 с раскосом. Рама 8 изготовлена из магниевого сплава и закреплена на профилях спинки 3 болтами. Во втулках 13 рамы имеются отверстия для прохода направляющих, по которым сиденье может перемещаться по высоте на 160 мм и фиксироваться в одном из пяти различных положений фиксаторами 15. В левом нижнем приливе рамы 8 смонтирован стопорный механизм, состоящий из фиксатора 15, пружины и поводка 14 с рукояткой 16. Направляющие 7 рамы изготовлены из хромансилиевых труб, хромированы и полированы, при помощи болтов 2 соединены с траверсой 5. Снизу в направляющие вварены узлы для крепления их к кронштейнам 11, а спереди имеется пять радиальных отверстий под фиксатор 15. Траверса 5 изготовлена из магниевого сплава, имеет отверстия в приливах для установки направляющих рамы и проушины под болты 4 для крепления стоек 9. Стойки с раскосом изготовлены из хромансилиевых труб, в концы которых вварены узлы для крепления к проушинам траверсы 5 и к кронштейнам 11 болтами 10. К проушинам рамы и траверсы укреплены две пружины 6, при помощи которых сиденье можно перемещать вверх, вниз сиденье перемещается от веса пилота. В продольном направлении положение сиденья можно изменить, переставив крепление направляющих в кронштейнах 11. Для этого в кронштейнах имеются три отверстия с расстоянием между крайними из них 65 мм.
Рис .10.2. Сиденье пилота:
Для обеспечения удобного подхода к оборудованию, расположенному на этажерках, сиденья легко можно снять, вынув шпильки 12. Сиденья снабжены привязными ремнями 17, а также мягкими спинками из поролона, обтянутого текстовинитом.
Сиденье бортмеханика установлено в дверном проеме входа в кабину экипажа между шпангоутами № 4Н и 5Н. Сиденье подвешено к правой боковой стенке этажерки. В рабочем положении оно дополнительно опирается на кронштейны и стопорится шариковыми фиксаторами, а в откинутом положении его удерживают пружины, смонтированные у кронштейнов навески сиденья. Сиденье снабжено привязными ремнями поясного типа с замками, позволяющими быстро отсоединить ремни, а также использовать их в качестве страховочного пояса при погрузочо-разгрузочных работах с бортовой стрелой.
Поверхности бортовых панелей и потолка кабины экипажа покрыты теплозвукоизоляцией, состоящей из двухслойных матов, которые крепятся к каркасу клеем и самонарезными винтами. Пол кабины покрыт нейлоновым ворсовым ковром, изготовленным на латексной основе, который крепится пружинными кнопками.
За сиденьями пилотов на крышках этажерок винтами с анкерными гайками закреплены санитарные аптечки и сумки из повинола, предназначенные для хранения карт и мелкого имущества.
10.2 ОБОРУДОВАНИЕ ГРУЗОВОЙ КАБИНЫ
В грузовой кабине расположены сиденья на 24 чел.: на левом борту - два двухместных и два трехместных сиденья, на правом - одно двухместное и три трехместных сиденья, на кожухе, закрывающем тяги управления на стенке шпангоута № 5Н, - одноместное откидное сиденье. Кроме этого, крышки двух инструментальных ящиков на грузовых створках используются в качестве одноместных сидений.
Сиденья откидного типа (рис 10.3)выполнены съемными, клепаной конструкции; панели изготовлены из листового дюралюминия и сверху склеены дублером, состоящим из слоев поролона и повинола. Сиденья закреплены шарнирно, с внутренней стороны они опираются на кронштейны бортовых панелей, а с наружной - на пол грузовой кабины через раму, связанную с бортовой панелью подкосом. В откинутом положении сиденья прижимаются к бортовым панелям спиральными пружинами, укрепленными к подкосу и бортовой панели. Сиденья оборудуются общими съемными спинками и привязными ремнями.
Рис. 10.3. Схема размещения сидений в грузовой кабине
Внутренняя отделка грузовой кабины состоит из потолочных и бортовых отделочных панелей, а также отделочных рамок проемов окон. Потолочные отделочные панели имеют каркас, склепанный из дюралюминиевых профилей и обтянутый серым повинолом. Каркас бортовых панелей выполнен из фанеры, поверх которой наклеен поролон с подслоем повинола. Панели крепятся винтовыми замками, а бортовые панели - винтами с самоконтрящимися гайками. В потолочных панелях имеются отверстия под плафоны освещения и лючки со сдвижными крышками для установки лямок крепления санитарных носилок.
Окна грузовой кабины закрываются светомаскировочными шторами. В зимний период между шпангоутами № 13 и 14 навешивается легкосъемная утеплительная штора, изготовленная из капроновой ваты толщиной 15 мм, простеганной вместе с двумя облицовочными слоями клеенчатого капронового полотна.
ТРАНСПОРТНОЕ ОБОРУДОВАНИЕ
Транспортное оборудование вертолета включает бортовую стрелу с электролебедкой ЛПГ-150М и такелажно-швартовочное оборудование.
На вертолете предусмотрена установка бортовой стрелы с электролебедкой, которая служит для погрузки в кабину мелких грузов массой до 150 кг. Погрузка может производиться как при стоянке вертолета на земле, так и при висении вертолета на небольшой высоте. Бортовая стрела расположена снаружи фюзеляжа около верхнего переднего угла проема сдвижной двери грузовой кабины. Размещение бортовой стрелы и ее агрегатов показано на рис. 10.4.
Рис.10.4. Схема установки бортовой стрелы с электролебедкой ЛПГ-2:
1— кронштейн; 2— консоль; 3, 6— ролики; 4— направляющая троса; 5— сектор консоли; 7— коробка с крышкой; 8— фиксатор; 9— трос электролебедки; 10— карабин; 11— коробка КУЛ-2 управления электролебедкой; 12—пульт ПУЛ-1 управления электролебедкой; 13— ролик; 14— ручка аварийного привода электролебедки; 15— электролебедка ЛПГ-2
Бортовая стрела состоит из кронштейна, консоли, карабина, роликов, фиксаторов, сектора консоли и коробки с концевыми выключателями. Подтягивание и опускание груза с помощью стрелы осуществляется электролебедкой ЛПГ-2, которая закреплена двумя болтами на полу грузовой кабины с правой стороны между шпангоутами № 1 и 2. Дистанционное управление лебедкой осуществляется с пульта управления ПУЛ-1А.
Рис.10.5. Бортовая стрела:
Кронштейн 1 стрелы (рис.10.5) литой из магниевого сплава; он имеет две площадки, которыми с помощью болтов крепится к фитингам шпангоута № 1. На кронштейне двумя болтами на шариковых подшипниках 2 закреплена консоль бортовой стрелы. Консоль сварной конструкции изготовлена из стали 30ХГСА и состоит из подкоса 4, трубы 8, кронштейнов 6 и 10 крепления роликов, сектора 18, ручки 17 и скобы 5 для крепления карабина в нерабочем положении стрелы. В походном и рабочем положениях консоль стопорится фиксатором 19, входящим в соответствующий паз сектора 18. Кроме двух пазов, по краям сектора имеется два выступа, ограничивающие угол поворота консоли в пределах 90°. Фиксатор состоит из втулки 20, пружины 21 и ручки 22, расположенной внутри грузовой кабины. Поворот стрелы осуществляется вручную с помощью ручки 17.
Трос электролебедки проходит через систему роликов 3, три из которых установлены на кронштейнах в кабине, а три — на самой стреле. На конце троса установлены пружина 12 и груз 14, который фиксируется защелкой 13. К грузу болтом закреплен карабин 15 (наличие груза обеспечивает натяжение троса при выпуске его лебедкой), на грузе винтом закреплен трос заземления 16 с грузиком. С целью исключения скручивания троса лебедки при подъеме и опускании грузов между крюком подцепки груза и тросом лебедки установлен вертлюг. На кронштейне крепления концевого ролика установлена коробка 11 с концевым выключателем, обеспечивающим выключение электролебедки в момент нажатия пружины 12 на выключатель при крайнем верхнем положении карабина.
Дата добавления: 2021-06-02; просмотров: 1817; Мы поможем в написании вашей работы! |
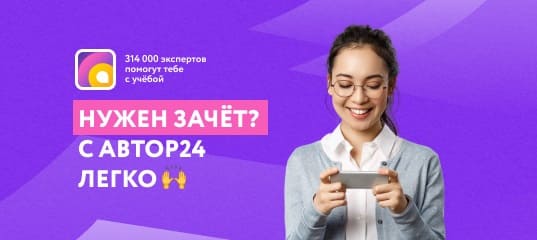
Мы поможем в написании ваших работ!