Массовые и центровочные данные
Государственное образовательное учреждение
высшего профессионального образования
Сибирский государственный аэрокосмический университет
имени академика М. Ф. Решетнева
КОНСТРУКЦИЯ И ТЕХНИЧЕСКАЯ ЭКСПЛУАТАЦИЯ
ВЕРТОЛЕТА МИ-8
«Планер и его системы».
Учебное пособие
для бакалавров, магистров по направлению подготовки 160900 и студентов специальностей 160901, 16903
всех форм обучения
Красноярск 2010
УДК 629.735.45. (022).171.2
ББК39.52 м8
Печатается по решению методической комиссии ИГА
Конструкция и техническая эксплуатация вертолета Ми-8.
часть 1.Планер вертолета и его системы:учебное пособие для бакалавров по направлению подготовки 160900. – испытания и эксплуатация авиационной техники, студентов специальностей 160901– техническая эксплуатация летательных аппаратов и двигателей, 16903- техническая эксплуатация авиационных электросистем и пилотажно- навигационных комплексов всех форм обучения /сост. В.А.Лавренов, В.Л.Медведев; Сиб. гос. аэрокосмич. ун- т. - Красноярск,. 2010 г. 180 стр.
86 иллюстр.
В настоящем учебном пособии приведены основные данные и эксплуатационные характеристики вертолета Ми-8, описана конструкция планера и его систем. Рассмотрены правила по уходу за ними и приведены методы их технического обслуживания и эксплуатации.
Пособие предназначено для бакалавров, магистров и специалистов по специальности 160901,160903.изучающих конкретную авиатехнику на старших курсах.
|
|
ОГЛАВЛЕНИЕ
Условные обозначения 4
Введение 5
1. Общая характеристика вертолета
1.1. Общие сведения 7
1.2. Основные данные 8
1.3 Контрольные вопросы и задания 10
2. Фюзеляж 10
2.1 Общие сведения 10
2.2 Носовая часть фюзеляжа 12
2.3 Центральная часть фюзеляжа 16
2.4 Хвостовая балка 22
2.5 Концевая балка 23
2.6 Стабилизатор 25
|
|
2.7 Техническое обслуживание фюзеляжа 26
2.8 Контрольные вопросы и задания 30
3. Шасси
3.1 Общие сведения 31
3.2 Основная опора шасси 32
3.3 Передняя опора шасси 37
3.4 Хвостовая опора 39
3.5 Техническое обслуживание шасси 41
3.6 Контрольные вопросы и задания 45
4. Воздушная система
4.1 Общая характеристик воздушной системы 46
4.2 Агрегаты воздушной системы 48
4,3 Техническое обслуживание воздушной системы 52
4.4 Контрольные вопросы и задания 53
5. Трансмиссия
5.1 Общие сведения 53
5.2 Промежуточный редуктор 54
|
|
5.3 Хвостовой редуктор 57
5.4 Хвостовой вал трансмиссии 59
5.5 Тормоз несущего винта 61
5.6 Техническое обслуживание трансмиссии вертолета 62
5.7 Контрольные вопросы и задания 66
6. Несущий и рулевой винты
6.1 Общие сведения о несущем винте 67
6.2 Рулевой винт 77
6.3 Техническое обслуживание несущего и рулевого винтов. 81
6.4 Контрольные вопросы и задания 91
7. Управление вертолетом
7.1 Общие сведения 92
7.2 Автомат перекоса 93
7.3 Проводка управления 96
7.4 Продольно-поперечное управление 99
7.5 Путевое управление 101
|
|
7.6 Пружинный механизм загрузки и электромагнитный
тормоз ЭМТ-2М 105
7.7 Объединенное управление 107
7.8 Управление остановом двигателей и
тормозом несущего винта 112
7.9 Техническое обслуживание системы управления вертолетом 114
7.11 Контрольные вопросы и задания 117
8. Гидравлическая система
8.1 Общие сведения 117
8.2 Работа гидросистемы 120
8.3 Агрегаты гидросистемы 123
8.4 Техническое обслуживание гидросистемы вертолета 142
8.5 Контрольные вопросы и задания 146
9. Система отопления и вентиляции
9.1 Общие сведения 147
9.2 Керосиновый обогреватель КО-50 149
9.3 Техническое обслуживание 160
9.4 Контрольные вопросы и задания 161
10. Оборудование вертолета
10.1 Оборудование кабины экипажа
10.2 Оборудование грузовой кабины 162
10.3 Транспортное оборудование 166
10.4 Устройство для внешней подвески грузов 171
10.5 Шарнирно-маятниковое устройство внешней
подвески грузов 174
10.6 Техническое обслуживание оборудования 176
10.7 Контрольные вопросы и задания 178
Заключение 179
Литература 180
Условные обозначения:
АЗС автомат защиты
БЗ блокировочный золотник
ВНА входной направляющий аппарат
ВС воздушная система
ВШ вертикальный шарнир
ВУ выходное устройство
ГС гидравлическая система
ГЦ гидроцилиндр
ГШ горизонтальный шарнир
ДГС дублирующая гидравлическая система
ДТБ дополнительный топливный бак
ЗК запорный клапан
ИР измеритель режимов
КБ концевая балка
КВД камера высокого давления
КНД камера низкого давления
КС камера сгорания
НВ несущий винт
НЧФ носовая часть фюзеляжа
ОГС основная гидравлическая система
ОМР ограничитель максимального расхода топлива
ОШ осевой шарнир
ПВД приемник воздушного давления
ПЗУ пылезащитное устройство
ПКРТ пульт контроля регулятора температуры
ПОС противообледенительная система
ПР промежуточный редуктор
ПТБ подвесной топливный бак
РВ рулевой винт
РЗКУ распределительный золотник комбинированного управления гидроусилителя
РЗРУ распределительный золотник ручного управления гидроусилителя
РК ручка коррекции
РТБ расходный топливный бак
РУД рычаг управления двигателем (на насосе-регуляторе)
РШГ рычаг "шаг — газ"
СПЛЛ сигнализация повреждения лонжерона лопасти
СВ стартер воздушный
СКВ система кондиционирования воздуха
ТС топливная система (вертолета)
ХБ хвостовая балка
ХР хвостовой редуктор
ЦОСЛ центробежный ограничитель свеса лопасти
ЦЧФ центральная часть фюзеляжа
ВВЕДЕНИЕ
Созданный в конструкторском бюро под руководством М. Л. Миля многоцелевой вертолет Ми-8, прототип которого совершил первый полет в 1960 г., морально и физически устарел. Основными причинами, приведшими к уменьшению диапазона его применения и производительности, явились недостаточные экономичность и мощность двигателей ТВ2-117, несовершенное авиационное и радиоэлектронное оборудование.
Во второй половине 70-х годов конструкторское бюро имени М. Л. Миля создало вертолет Ми-17 с двигателями ТВ3-117, который явился дальнейшим развитием вертолета Ми-8Т и широко экспортировался в зарубежные страны. Позднее на его базе были созданы вертолеты Ми-8МТВ с двигателями ТВЗ-117ВМ и Ми-8АМТ. Для военной авиации параллельно был создан специальный вариант вертолета Ми-8МТ.
В 1973 г. совершил первый полет вертолет-амфибия Ми-14, способный взлетать и садиться на водную и земную поверхность, отличающийся от вертолета Ми-8МТ конструкцией нижней части фюзеляжа, выполненной в виде лодки, наличием дополнительного хвостового поплавка, двух передних и двух основных убирающихся опор шасси, установкой специального оборудования.
Вертолет Ми-8МТВ наряду с максимальной преемственностью конструкции вертолета Ми-8Т имеет ряд существенных отличий. К ним относятся:
уменьшение массы конструкции фюзеляжа за счет изготовления обшивки в основном из сплава Д16АМ с меньшей толщиной листов при одновременной постановке усиливающих кольцевых накладок по усиленным шпангоутам центральной части фюзеляжа (ЦЧФ), хвостовой балки (ХБ), концевой балки (КБ), а также дополнительном усилении подкосами шпангоута №7 ЦЧФ;
расположение на правой бортовой панели ЦЧФ между шпангоутами № 3 и 4 аварийного люка;
изменения стояночного обжатия амортизаторов и авиашин в связи с увеличением максимальной взлетной массы вертолета до 13 000 кг и изменением диапазона допустимых эксплуатационных центровок вертолета;
постановка в воздушную систему редукционного клапана УП-25/2 вместо ПУ-7;
кардинальная доработка силовой установки (использование более мощных и экономичных основных двигателей ТВЗ-117ВМ с электронными регуляторами и вспомогательной силовой установки АИ-9В, обеспечивающей воздушный запуск основных двигателей и резервное энергоснабжение вертолета;
доработка задней сферической опоры и переднего пояса крепления двигателя;
размещение эффективного пылезащитного устройства с воздушно- и электротепловой противообледенительной системой (ПОС);
обеспечение принудительного воздушного охлаждения генераторов переменного тока, гидронасосов, воздушного компрессора, маслорадиаторов;
доработка концевого отсека и левой боковой створки отсека главного редуктора, капотов в соответствии с установкой двигателя АИ-9В и второго генератора
изменения в топливной системе низкого давления, обеспечивающей топливопитание двигателей ТВЗ-117ВМ, АИ-9В, обогревателя КО-50;
выполнение маслосистемы двигателя с раздельной откачкой масла из двигателя в маслорадиатор, из коробки верхних приводов, центрального привода, первой опоры и при срабатывании перепускного клапана маслоагрегата - в маслобак;
обеспечение защиты от пожара отсеков основных двигателей, обогревателя, главного редуктора и АИ-9В (в системе имеются два огнетушителя с пироголовками вместимостью по 4 л каждый);
применение на вертолете главного редуктора ВР-14, согласующего частоты вращения свободных турбин двигателей (15 000 мин-1) и несущего винта (192 мин-1) на номинальном режиме работы для эффективного использования мощности двигателей;
установка на КБ рулевого винта (РВ) тянущего типа с доработанными лопастями, что в целом позволило расширить диапазон путевой управляемости вертолетом и получить максимальную тягу РВ -8700 Н (870 кгс);
введение в систему управления вертолетом дополнительно цепи управления перенастройкой частоты вращения несущего винта (НВ), а в путевое управление - системы подвижного упора СПУУ-52, обеспечивающего автоматическое ограничение шага РВ до 80 % максимального его значения в условиях низких температур и повышенного давления окружающего воздуха во избежание перегрузки хвостовой трансмиссии вертолета;
замена дозатора на дроссель в магистрали подвода рабочей жидкости к гидроупору в гидросистеме вертолета.
Вышеперечисленные конструктивные решения позволили существенно улучшить летные и массовые характеристики, повысить производительность полетов вертолета.
Вертолет Ми-8АМТ - модифицированный вариант вертолета Ми-8МТВ. Его предполагается использовать с внешней подвеской для транспортировки грузов общей массой до 4000 кг, а также со съемной модульной стрелой грузоподъемностью 300 кг и электролебедкой ЛПГ-300. В транспортной кабине размещены 27 откидных сидений, установлено более современное авиационное и радиоэлектронное оборудование.
1.ОБЩАЯ ХАРАКТЕРИСТИКА ВЕРТОЛЕТА
1.1 ОБЩИЕ СВЕДЕНИЯ
Вертолет Ми-8МТВ предназначен для пассажирских и грузовых перевозок, а также проведения специальных авиационных работ в труднодоступной местности. Вертолет (рис. 1.1) спроектирован по одновинтовой схеме с пятилопастным несущим и трехлопастным рулевым винтами. На вертолете установлены два турбовинтовых двигателя ТВЗ-117ВМ с взлетной мощностью 1470 кВт (2000 л. с.) каждый, что обеспечивает возможность полета и посадки при отказе одного из двигателей и переходе работающего двигателя на чрезвычайный режим с мощностью 1617 кВт (2200 л. с).
Вертолет эксплуатируется в следующих вариантах:
транспортном, предусматривающем перевозку грузов массой до 4000 кг или 24 пасс;
санитарном, обеспечивающем перевозку 12 лежачих больных и сопровождающего медработника;
с внешней подвеской, предназначенной для перевозки крупногабаритных грузов вне грузовой кабины массой до 3000 кг;
перегоночном (с двумя дополнительными баками), обеспечивающем максимальную дальность полета.
Проведены испытания по перевозке на подвеске грузов массой до 4000 кг.
В необходимых случаях на любом из вариантов может быть установлен дополнительный бак.
Рис. 1.1. Общий вид вертолета
Вертолет снабжен электролебедкой, позволяющей с помощью бортовой стрелы поднимать (опускать) грузы массой до 150 кг, а также при наличии полиспаста затягивать в грузовую кабину грузы массой до 3000 кг.
1.2 ОСНОВНЫЕ ДАННЫЕ
Геометрические данные
Длина вертолета, м:
без несущего и рулевого винтов 18,219
с вращающимися несущим и рулевым винтами 25,262
Высота вертолет, м:
без рулевого винта. 4,756
с вращающимся рулевым винтом 5,521
Ширина фюзеляжа, 2,500
Габаритные размеры кабины экипажа, м 2,15x2,05x1.7
Клиренс, м 0,445
Стояночный угол вертолета 3°42'
Диаметр несущего винта, м. 21,294
Диаметр рулевого винта, м 3,908
Угол наклона оси несущего винта вперед 30'
Расстояние от конца лопасти до хвостовой балки на стоянке, м. 0,45
лощадь стабилизатора, м2 2
Длина грузовой кабины, м
без грузовых створок. 5,34
с грузовыми створками 7,82
Ширина грузовой кабины, м: на полу. 2,06
Максимальная 2,34
Высота грузовой кабины, м. 1,8
Размер сдвижной двери, м 0,82x1,4
Размер блистеров, м 0,75x0,75
Габаритные размеры аварийного люка,м 0,7x1
Расстояние между силовыми балками пола, м. 1,52
Размер аварийного люка-окна, 0,46x0,7
Колея погрузочных трапов, м 1,5+0,2
Колея шасси, м 4,510
База шасси, м. 4,281
Размер колес, мм :
передних опор 595x185
основных 865x280
Массовые и центровочные данные
Взлетная масса, кг:
максимальная 13 000
нормальная 11100
Коммерческая нагрузка вертолете, кг:
Полная 4000
на внешней подвеске 3000
Масса пустого вертолета, кг 7085
Масса снаряженного вертолета
(без дополнительных топливных баков), кг 7523
Допустимая центровка загруженного
вертолета, мм:
передняя. +370
задняя -95
Центровка пустого вертолета, мм -13
Для обеспечения безопасности маршрутных полетов устанавливается гарантийный запас топлива не менее минимального 140 кг. Невырабатываемый остаток топлива 20 кг.
Летные данные
Практический потолок, м:
с нормальной взлетной массой 6000
с максимальной взлетной массой 4800
Статический потолок, м:
с нормальной взлетной массой 3980
Приборная скорость при массе11100кг на высоте 100 м., км/ч 230
Приборная скорость при массе11100кг на высоте 6000 м., км/ч 100
Минимальная приборная скорость, км/ч 60
Наивыгоднейшая скорость набора высоты 6000 м , км/ч: 90
Время набора высоты с максимальной взлетной массой,мин.
1.3 КОНТРОЛЬНЫЕ ВОПРОСЫ И ЗАДАНИЯ
1. Какова история создания вертолета Ми-8МТВ.
2. Какие основные различия вертолетов Ми-8МТВ и Ми-8Т?
3. Перечислите основные геометрические данные вертолета Ми-8МТВ.
4. Перечислите основные летные данные вертолета Ми-8МТВ
5. Назовите основные массовые и центровочные данные вертолета Ми-8МТВ
6. В каких вариантах эксплуатируется вертолет.
2. ФЮЗЕЛЯЖ
Фюзеляж предназначен для размещения экипажа, оборудования, коммерческой нагрузки, а также взаимной связи основных составных частей вертолета.
2.1 ОБЩИЕ СВЕДЕНИЯ
Основные части планера вертолета и технологические разъемы представлены на рис.2.1.
Силовая схема фюзеляжа полумонокок, то есть в конструкции фюзеляжа имеются усиленные и нормальные шпангоуты, силовые балки стрингеры и рабочая обшивка.
Фюзеляж, имеющий три конструктивных разъема, включает носовую, центральную части фюзеляжа, хвостовую и концевую балки, что существенно улучшает технологичность при производстве, эксплуатации и ремонте фюзеляжа.
Рис. 2.1 Основные элементы планера вертолета
1 - передняя стойка шасси; 2 - носовая часть фюзеляжа; 3, 22 -сдвижные блистеры; 4 - крышка люка для выхода к силовой установке; 5 - капот обогревателя КО-50; 6, 18 - главные стойки шасси; 7, 19 - подвесные топливные баки; 8 - капот; 9 - рама крепления главного редуктора; 10 - хвостовая балка; 11, 14 - правая и левая половины стабилизатора; 12- килевая балка; 13- обтекатель; 15- хвостовая опора; 16, 17- грузовые створки; 20- сдвижная дверь; 21- центральная часть фюзеляжа; 23-крышка люка для аварийного покидания вертолета; 24- обтекатель антенны изделия ДИВ-1; 25- погрузочные трапы; 26- щитки; 27- створка задней двери; 28- входной трап
Фюзеляж, состоящий из силового набора усиленных, нормальных шпангоутов, продольных балок, стрингеров и гладкой работающей обшивки, собирается из отдельных панелей. Обшивка панелей соединена с каркасом клеесварным методом, а в местах стыковки панелей друг с другом - внахлест с помощью многорядных заклепочных швов.
НЧФ своим шпангоутом № 5Н стыкуется с № 1 ЦЧФ, которая в свою очередь шпангоутом № 23 стыкуется со шпангоутом №1 ХБ, соединенной своим шпангоутом № 17 с № 1 КБ. Все эти соединения производятся с помощью болтов.
В конструкции фюзеляжа специально предусмотрены двери, люки, блистеры для аварийного покидания вертолета (рис. 2.2). Два сдвижных блистера НЧФ, сдвижная дверь, люк-окно, крышка люка на правой грузовой створке ЦЧФ имеют механизмы аварийного сброса. Дополнительные люки - люк с крышкой выхода к силовой установке на потолке НЧФ и люк с крышкой для внешней подвески на полу ЦЧФ.
Рис. 2.2 Схема расположения блистеров, дверей, люков для покидания вертолета при аварийных ситуациях:
1— сдвижные блистеры; 2 — аварийный люк — окно не правой бортовой панели; 3 — люк с крышкой выхода к силовой установке; 4 — люк с крышкой на правой грузовой створке; 5 — люк с крышкой для внешней подвески; 6 — сдвижная дверь для входа в грузовую кабину.
Основными материалами, применяемыми при изготовлении фюзеляжа, являются листовой плакированный дюралюминий Д16АМ, дюралюминий Д16А, упрочненный дюралюминий В95, алюминиевые сплавы АК-6 и АК-8, магниевый сплав МЛ5Т, титановый сплав ОЧТ, стали ЗОХГСА, ЗОХГСНА.
2.2. НОСОВАЯ ЧАСТЬ ФЮЗЕЛЯЖА
Носовая часть фюзеляжа предназначена для размещения экипажа, командных органов управления, приборного оборудования и создания единых аэродинамических обводов фюзеляжа.
Силовая схема НЧФ - полумонокок. Поперечный набор НЧФ (рис. 2.3) состоит из пяти шпангоутов № 1Н...5Н. Шпангоуты № 1Н...ЗН имеют нижние и верхние балки и неполные боковины, которые замыкаются на раме остекления. Шпангоуты № 4Н и 5Н имеют форму замкнутого кольца, состоящего из нижней, верхней балок и двух боковин клепаной конструкции.
Рис 2.3 Носовая часть фюзеляжа:
1 — этажерка для радиоэлектронного оборудования; 2 — крышка люка выхода к силовой установке; 3 — штампованная жесткость; 4 — стенка шпангоута № 5Н; 5 — сдвижной блистер;: 6 — ниша для аккумуляторной батареи; 7 — кронштейны крепления сиденья пилота; 8 — панель пола; 9—лобовое стекло фонаря; 10, 11— короба под аккумуляторы; 12— люк.
Шпангоут № 5Н имеет стенку, подкрепленную горизонтальными и вертикальными уголковыми профилями, которой отделяется кабина экипажа от грузовой кабины. По оси симметрии в шпангоуте № 5Н выполнен проем, окантованный прессованным уголком с резиновым профилем, для входной двери. Дверь, изготовленная из листового дюралюминия, подвешена справа на петлях и имеет замок с двусторонней ручкой, два замка-задвижки, оптический микроглазок и мягкую спинку откидного сиденья бортового техника. К передней поверхности стенки шпангоута № 5Н крепятся этажерки для монтажа оборудования. Продольный набор состоит из стрингеров уголкового типа, балок, шпампованных местных жесткостей. Обшивка НЧФ выполнена гладкой из листов дюралюминия Д16АМ толщиной 0,8 мм.
Основными технологическими панелями НЧФ являются панели пола, потолка, левая и правая бортовые панели со сдвижными блистерами, фонарь с остеклением, стыковочный шпангоут № 5Н.
Панель пола склепана из нижних балок шпангоутов, продольных балок, стрингеров настила пола и наружной обшивки. Силовой набор соединен уголковыми профилями и дополнительно усилен специальными профилями и диафрагмами. В настиле имеется ряд отверстий для прохода элементов командных органов управления (педалей, ручек циклического шага, ручек "шаг - газ"), электропроводки к приборным доскам и центральному пульту, патрубков системы отопления и вентиляции, а также люк доступа к узлам крепления, зарядному клапану передней амортизационной стойки и усиливающие накладки в местах крепления органов управления.
В наружной обшивке находятся люки под установку двух фар МПРФ-Ш для монтажа и осмотра элементов управления, агрегатов воздушной системы, системы отопления и вентиляции.
Потолочная панель склепывается из верхних балок шпангоутов № 1Н...5Н, местных штампованных жесткостей, стрингеров, подкрепляющих профилей, диафрагм, обшивки.
Рис. 2.4. Люк выхода к силовой установке:
1— петли крепления крышки люка; 2— упор; 3— кронштейн; 4— вилка; 5— регулировочная муфта; 6— вал; 7— защелка; 8— крюк; 9— ручка; 10— ребро; 11— штифт; 12— пружина; 13— кнопка
Между шпангоутами № 3Н...4Н установлен люк (рис. 2.4.) для выхода к силовой установке. Крышка люка - клепаной конструкции и навешивается на двух петлях к шпангоуту № 3Н. Во избежание попадания влаги внутрь кабины снаружи по периметру крышки выполнен желобок. В крышке имеются два смотровых окна, остекленные органическим ориентированным стеклом. Для герметизации в закрытом положении по периметру крышки изнутри крепятся профилями резиновые прокладки. Крышка запирается со стороны кабины ручкой-фиксатором.
Бортовые панели изготовлены из боковин шпангоутов, штампованных жесткостей, стрингеров, подкрепляющих профилей, обшивки.
Литые рамы из магниевого сплава и штампованные жесткости образуют рамы проемов для сдвижных блистеров. По задней и передней кромкам проемов находятся резиновые герметизирующие профили, а сверху снаружи приклепаны желобки для стока влаги. В верхней части рамной заделки проемов с внутренней стороны установлены механизмы аварийного сброса блистеров.
Рис 2.5.Сдвижной блистер
1—пружина; 2—запирающий штырь; 3—кронштейн; 4—ручка аварийного сброса; 5—верхний направляющий профиль; 6—наружный направляющий профиль; 7—штырь; 8—трос ;
9— нижний направляющий профиль; 10— сальник; 12, 15 —ручка; 13— рычаг; 14—выпуклое органическое стекло .
Сдвижной блистер (рис 2.5)конструктивно выполнен из литой из магниевого сплава рамы с вставленным выпуклым ориентированным органическим стеклом, которое прижимается на винтах с гайками внешней облицовкой из дюралюминия через резиновую уплотнительную прокладку. На блистере установлена внутренняя ручка с рычагом, связанным тросом с запирающим штырем. Левый блистер открывается только изнутри, а правый - изнутри и снаружи ручкой с замком под ключ. На левом блистере закреплен визуальный сигнализатор обледенения.
На левой бортовой панели между шпангоутами № 4Н и 5Н расположены два люка, закрывающие ниши под два аккумулятора. Крышки запираются винтовыми замками, а в горизонтальном открытом положении удерживаются тягами.
На левой панели установлены лючки под заземление и лючок для розеток подключения аэродромного питания, аэронавигационный огонь БАНО-45, приемник ПВД.
На правой бортовой панели установлены люк с жабрами для охлаждения выпрямительных устройств, аэронавигационный огонь БАНО-45, приемник ПВД.
Фонарь кабины, обеспечивающий необходимый обзор экипажу, состоит из каркаса и остекления. Каркас собран из специальных дюралюминиевых профилей, штампованных жесткостей, литых рам, облицовочных рамок. Два лобовых стекла изготовлены из триплекса с электрообогревом и имеют стеклоочистители с механизмами ЭПК-2Т-60, остальные стекла - из органического ориентированного стекла СО-95 толщиной 3...4 мм. Стекла устанавливаются в литые из магниевого сплава рамки на резиновых профилях и поджимаются облицовочными рамками на винтах с герметизацией герметикам ВИТЭФ-1 по внешней и внутренней поверхностям.
2.3. ЦЕНТРАЛЬНАЯ ЧАСТЬ ФЮЗЕЛЯЖА
Силовая схема центральной части фюзеляжа (ЦЧФ) - полумонокок. Поперечный набор каркаса ЦЧФ (рис. 2.6) -шпангоуты № 1...23, из которых шпангоуты № 1, 2А, 7, 10, 13, 23 - усиленные, остальные - нормальные. ЦЧФ собирается из отдельных панелей: бортовых, потолочной, грузового пола, заднего отсека.
В ЦЧФ между шпангоутами № 1 и 13 располагается грузовая кабина, № 13... 21 - задний отсек с грузовыми створками. Сверху потолочной панели между шпангоутами № 1...7 находятся двигатели ТВЗ-117ВМ, между № 7...10 -главный редуктор ВР-14, в надстройке между шпангоутами № 10...13 - расходный топливный бак, под капотами концевого отсека между шпангоутами № 10...13 размещены панель гидроагрегатов и отсек вспомогательной силовой установки АИ-9В, между шпангоутами № 16...21 в надстройке - радиоотсек.
Шпангоуты № 1, 23 - стыковочные и выполнены кольцевой формы с уголковым сечением, в стенке которого по периметру имеются отверстия под болты стыковки с НЧФ и ХБ соответственно.
Шпангоут № 2А - усиленный. Он склепан из листового дюралюминия, прессованных профилей и в местах установки силовых узлов подкреплен вертикально расположенными профилями, а по углам - фитингами.
Усиленные шпангоуты № 7 и 10 состоят из верхних и нижних балок и боковин. Верхние балки и боковины отштампованы из алюминиевого сплава АК-6 и имеют двутавровое сечение. Верхняя балка - разъемная по вертикальной плоскости симметрии, стыкующаяся в этой зоне болтами по фланцевым поверхностям, нижними частями соединяется с боковинами (на шпангоуте № 7 - с помощью фрезерованных гребенок и пар болтов, на шпангоуте № 10 - фланцами и вертикально расположенными болтами).
Нижняя балка имеет двутавровое сечение и склепана из стенки с подкрепляющими стойками и уголковых профилей. Стыковка нижних балок с боковинами осуществлена болтами через стыковочные фитинги из материала АК-6, закрепленные на концах балки.
Для увеличения жесткости шпангоута № 7 боковины с нижней балкой соединены дополнительно подкосами, соответственно подстыкованными к кронштейнам в зоне стрингера № 18.
Шпангоут № 13 склепан из листового дюралюминия и прессованных уголковых профилей. Кольцо основной части имеет верхнюю балку, боковины двутаврового сечения, соединенные между собой встык накладками с помощью заклепок.
Нижняя балка, собранная из трех отштампованных профилей на болтах, имеет швеллерное сечение и склепана по фитингам с боковинами. К нижней балке дополнительными фитингами и накладками крепится наклонный шпангоут № 13А, замыкающий грузовую кабину и окантовывающий грузовой люк.
Рис. 2.6. Центральная часть фюзеляжа:
1 - узел крепления амортизатора передней опоры; 2 — сдвижная дверь; 3 — левая бортовая панель; 4 — потолочная панель; 5 — узел крепления спецфермы; 6 — узел крепления амортизатора главной опоры; 7 — задний отсек; 8 — грузовые створки; 9,10 — узлы крепления заднего подкоса и подкоса-полуоси главной опоры; 11, 12, 13, 14 — узлы крепления подвесного топливного бака; 15 — панель грузового пола; 16 — узлы крепления вильчатого подкоса передней опоры;
а — отверстие под отводящий патрубок ресивера — распределителя обогревателя КО-50; б - отверстие под патрубок забора воздуха к обогревателю из грузовой кабины; в — отверстие под патрубок подвода воздуха в кабину экипажа
Верхняя арка отштампована из листового дюралюминия и имеет просечки для прохода стрингеров. Нормальные шпангоуты имеют Z-образное сечение. Верхние балки, боковины отштампованы из листового дюралюминия, соединены между собой встык накладками на заклепках, усиливаются гнутым профилем по внутреннему контуру, а по внешнему имеют просечки для прохода стрингеров. Нижняя балка клепаная. Она имеет двутавровое сечение и соединяется фитингами из материала АК-6 с боковинами с помощью заклепок.
Дополнительный шпангоут № 11А клепаной конструкции устанавливается в зоне размещения последних узлов крепления подвесных топливных баков увеличенной емкости.
Продольный набор каркаса ЦЧФ включает стрингеры из уголковых дюралюминиевых профилей, которые располагаются симметрично относительно продольной вертикальной плоскости, от которой и идет нумерация стрингеров. Для усиления панели пола установлены пять продольных балок. Для местного усиления конструкции панелей используются дополнительные жесткости.
Обшивка ЦЧФ выполнена из листов дюралюминия Д16АМ толщиной 0,8... 1 мм. Обшивка бортовых панелей, имеющих вырезы под окна фюзеляжа, имеет максимальную толщину. Обшивка при стыковке панелей соединяется внахлест многорядными заклепочными швами, а также усиливается приклепанными специальными лентами толщиной 2...3 мм в зоне усиленных шпангоутов № 1, 3А, 7,10,13.
Панель грузового пола склепана из нижних балок шпангоутов № 1...13, стрингеров, продольных балок, настила и наружной обшивки.
Настил выполнен из рифленого листа 388АМ-1, а наружная обшивка - из листового дюралюминия Д16АМ толщиной 0,8 мм. Средняя часть настила панели усилена поперечными профилями. Дополнительное соединение панели пола с бортовыми панелями осуществлено продольными уголковыми профилями на заклепках. Вдоль бортом установлены 27 швартовочных узлов, а место их крепления на шпангоутах и балках усилено штампованными кронштейнами и фитингами из АК-6. На шпангоуте № 1 посередине крепится узел крепления полиспаста для затягивания груза в кабину электролебедкой, а между шпангоутами № 1 и 2 справа -штампованный фитинг для крепления плиты под основание лебедки и кожух роликов и тросов лебедки.
На пороге проема под сдвижную дверь имеются два гнезда для установки съемного входного трапа.
Слева и справа на полу между шпангоутами №5 и 10 могут размещаться съемные ложементы под дополнительные топливные баки. В настиле имеется ряд монтажных, технологических и эксплуатационных лючков для доступа к агрегатам систем.
Между шпангоутами № 7с и 10с и стрингерами № 28 располагается люк для выхода удлинительного троса внешней тросовой подвески. Вырез под люк усилен двумя диафрагмами между шпангоутами №7и8, 9и10и двумя балками - между стрингерами № 28. Внешняя обшивка толщиной 1,5 мм имеет по периметру выреза пластмассовую окантовку для предотвращения износа троса.
Крышка люка - двойная и склепана из листового дюралюминия с ребрами жесткости Верхняя крышка, навешанная на петлях, соединяется со стороны противоположного ребра двумя регулируемыми тягами с нижней крышкой, подвешенной на двух кронштейнах, и имеет два запорных устройства и ручку для открытия.
Потолочная панель включает в себя верхние балки шпангоутов № 1...13, стрингеры № 1...6, местные жесткости, обшивку, склепанные между собой. Стрингеры у усиленных шпангоутов разрезаются и крепятся к зубчатым лентам. Нормальные шпангоуты имеют просечки для прохода стрингеров. Обшивка потолочной панели выполнена из листов титанового сплава марки ОЧТ толщиной 0,6 мм.
На панели по оси симметрии за шпангоутом № 8 размещен люк для подхода к редукционному клапану маслоагрегата главного редуктора ВР-14. У шпангоута № 9 имеются два отверстия под угольники пожарных кранов, между шпангоутами № 11 и 12 - люк под топливный насос 463Б. На обшивке панели имеются желоба и отверстия под дренажные трубопроводы для стока воды.
Бортовые панели склепаны из боковин шпангоутов, стрингеров, дополнительных усиливающих профилей и обшивки.
Задняя часть панелей заканчивается боковинами наклонного шпангоута № 13А.
На левой бортовой панели имеется пять круглых окон с выпуклыми стеклами из органического ориентированного стекла толщиной 3...4 мм. Стекло первого окна, находящегося на входной сдвижной двери, выполнено плоским. Окна № 2 и 5, откидывающиеся внутрь на двух верхних петлях, в закрытом положении фиксируются двумя запорными устройствами рычажного типа, которые расположены в нижней части окна.
На правой бортовой панели находятся пять круглых окон, из которых № 1, 2, 5 открываются внутрь.
Между шпангоутами № 3 и 4 установлен аварийный люк-окно (рис 2.7). Проем под него окантован профилями из дюралюминия. Крышка люка-окна склепана из рамки и обшивки. В крышке выполнено откидывающееся окно. Крышка люка-окна фиксируется двумя нижними штырьками в гнездах нижней части проема, а в верхней - запирающими штырями, которые входят в отверстия кронштейнов на крышке.
Между шпангоутами № 1 и 3 сделан проем под сдвижную дверь, окантованный профилями из дюралюминия и имеющий в верхней части желоб для стока воды и узлы для веревочной лестницы.
Рис 2.7 Аварийный люк-окно на правом борту грузовой кабины
1. – рычаг; 2. – крышка; 3 . – наружная ручка аварийного сброса; 4. – кронштейн; 5. – петля навески окна; 6. – откидывающееся окно;7. – запорное устройство;8. – штырьки
Рис 2.8 Сдвижная дверь
1- пружинный фиксатор; 2- пружина; 3,4- внутренняя и наружная ручки аварийного сброса двери; 5- трос;6- стекло;7- внутренняя ручка; 8- пружина; 9-щеколда; 10- наружная ручка; 11- верхняя направляющая; 12- шарики; 13- запирающий штырь;14- полозок;15-кронштейн;16- ролик
Сдвижная дверь склепана из каркаса, внешней и внутренней обшивок, установлена на верхней и нижней направляющих и может по ним сдвигаться назад. В верхнюю направляющую в виде П-образного профиля на шариках в ленточных сепараторах устанавливается полозок с кронштейнами, которыми через запирающие штыри соединяется с дверью. Дверь в открытом положении удерживается пружинным фиксатором, установленным снаружи на борту фюзеляжа. В закрытом положении дверь запирается замком, расположенным в средней части передней кромки. Для аварийного сброса двери в верхней части последней имеется штыревой механизм с внешней и внутренней ручками, который тросовой проводкой сблокирован с запирающим замком.
Между шпангоутами № 1-2 находятся отверстия под патрубок забора воздуха к обогревателю КО-50 в режиме работы «Рециркуляция», а у шпангоута № 5 - окно для отводящего патрубка ресивера-распределителя КО-50.
Задний отсек обеспечивает плавность аэродинамических обводов ЦЧФ в зоне соединения с ХБ и состоит конструктивно из надстройки и створок грузового люка. Надстройка клепаной конструкции, включающая в себя верхние арочные части шпангоутов, стрингеры, наружную обшивку, плавно переходит в ХБ и заканчивается шпангоутом
№ 23. В нижней части надстройки между шпангоутами № 16... 18 выполнен люк для обеспечения доступа из грузовой кабины в радиоотсек и ХБ при техническом обслуживании.
Створки грузового люка создают плавность переходов от грузовой кабины к надстройке в задней части ЦЧФ, закрывают проем грузового люка, увеличивают объем грузовой кабины.
Створки склепываются из штампованных жесткостей и обшивки. В нижней части створок шарнирно подвешиваются откидывающиеся щитки, удерживаемые резиновыми амортизаторами в открытом положении для увеличения прохода при загрузке через грузовой люк. Открытие и закрытие створок производится вручную. Створки в открытом положении фиксируются подкосами, а в закрытом - штырями у шпангоута № 13А и запираются продольным и поперечным замками.
Герметичность створок по стыкуемым поверхностям обеспечивается постановкой по периметру створок резиновых профилей. Внутренняя ручка замка створок имеет дополнительное устройство, что предотвращает открытие створок на стоянке снаружи.
На левой боковой панели верхнего электропульта установлено красное табло «Створки открыты», связанное с микровыключателем АМ-800К на шпангоуте № 13А и сигнализирующее, в каком положении находятся створки.
В нижней части створок размещены инструментальные ящики. На левой створке располагаются две кассеты сигнальных ракет, люк с жабрами вентиляции, переносной огнетушитель, кронштейны крепления ложементов санитарных носилок.
На правой створке имеется люк для аварийного покидания вертолета, который закрывается крышкой, имеющей механизм аварийного сброса (ручка, два запирающих штыря с пружинами). При сбросе необходимо ручку выдернуть вниз. При этом штыри выйдут из отверстий в кронштейнах крышки, а пружинные толкатели сбросят крышку наружу.
На левой грузовой створке могут располагаться погрузочные трапы, которые в рабочем положении фиксируются в гнездах на нижней балке шпангоута № 13 для погрузки и выгрузки колесной техники или иных грузов.
2.4. ХВОСТОВАЯ БАЛКА
Хвостовая балка предназначена для выноса рулевого винта из зоны возмущенного воздушного потока от несущего винта, создания момента от силы тяги рулевого винта для парирования реактивного момента несущего винта и обеспечения необходимой управляемости вертолета. Силовая схема ХБ -полумонокок.
Поперечный набор ХБ (рис. 2.9) включает шпангоуты № 1...17. Стыковочные шпангоуты № 1 и 17 имеют кольцевую форму и уголковое сечение, выполнены из прессованных дюралюминиевых профилей, усиливаются по периметру зубчатыми лентами. В стенках шпангоутов просверлены отверстия под стыковочные болты. Остальные шпангоуты — нормальные, имеющие Z-образное сечение и просечки для прохода стрингеров.
Шпангоуты № 2, 6, 10, 14 имеют местное усиление в верхней части и справа по полету в связи с установкой опор Задней жесткой части хвостового вала трансмиссии и кронштейнов под текстолитовые колодки четырех тросов управления рулевым винтом.
Шпангоуты № 12 и 13 справа между стрингерами № 3...9 усиливаются накладками и профилями. Шпангоуты № 11, 14 и зона между ними усилены диафрагмами и профилями из дюралюминия. Это вызвано установкой коробки блока роликов на шпангоутах № 12 и 13 при разносе тросов системы путевого управления для повышения ее живучести.
Продольный набор включает 26 стрингеров (вверху по оси симметрии - стрингер № 1 и далее отсчет стрингеров производится в обе стороны вниз), изготовленных из прессованных уголковых профилей и усиленных на левом и нижнем сводах ХБ.
Обшивка ХБ выполнена из листов Д16АМ толщиной 0,8 мм. Обшивка левого свода между шпангоутами № 8... 17 и правого до стрингера № 6 имеет толщину в 1 мм, остальная -толщину 0,8 мм. По шпангоутам № 12 и 13 обшивка усилена внешними усиливающими накладками. Стыковка листов обшивки осуществлена по стрингерам и шпангоутам внахлест с подсечкой. Слева и справа в обшивке между шпангоутами № 13 и 14 сделаны вырезы с усилением обшивки наружными накладками из листового Д16АМ. Сверху в обшивке выполнены два лючка с крышками для осмотра и смазки шлицевых шарниров хвостового вала трансмиссии, два выреза под строевые огни, вырезы под проблесковый маяк и датчик курсовой системы. Снизу обшивки сделан вырез между шпангоутами № 2...6 под блоки доплеровского измерителя путевой скорости и угла сноса, а также между шпангоутами №7, 8, 11 и 12 расположены приемная и передающие антенны радиовысотомера.
На шпангоутах № 13 и 14 по бокам размещены по два узла навески стабилизатора. На шпангоуте № 15 по бокам снизу установлены два узла крепления подкосов хвостовой опоры, а на шпангоуте № 17 снизу - узел крепления амортизатора хвостовой опоры.
Рис. 2.9. Хвостовая балка:
1 - шпангоут; 2 - кронштейн направляющих колодок тросов; 3 - опора хвостового вала; 4,6- узлы навески стабилизатора; 5 — накладка; 7,8 — узлы крепления амортизатора и подкоса хвостовой опоры.
2.5. КОНЦЕВАЯ БАЛКА
Концевая балка совмещает ось рулевого винта с плоскостью вращения несущего винта для уравновешивания моментов сил относительно продольной оси вертолета, а также улучшает путевую устойчивость вертолета.
Силовая схема КБ - полумонокок. Концевая балка (рис. 2.10) состоит из килевой балки и обтекателя.
Поперечный набор состоит из шпангоутов № 1...9, из которых № 1, 2, 3, 9 -усиленные.
Шпангоут № 1 - стыковочный, изготовленный штамповкой из алюминиевого сплава, имеет уголковое сечение. В стенке его выполнены отверстия под стыковочные болты.
Шпангоут № 2 выполнен усиленным в связи с изломом оси КБ на угол 43° 10' относительно оси ХБ.
Шпангоут № 3, изготовленный из листового дюралюминия, усилен отштампованным из алюминиевого сплава кронштейном, к которому четырьмя болтами крепится промежуточный редуктор трансмиссии. Шпангоут № 9 дополнительно усиливается специальной лентой, так как к нему крепится болтами нижним фланцем картера хвостовой редуктор.
Продольный набор килевой балки включает стрингеры и лонжерон. Стрингеры выполнены из уголковых прессованных профилей. Лонжерон, усиливающий конструкцию килевой балки в зоне стыковки с обтекателем, склепан из стенки и уголковых профилей. В стенке лонжерона имеется люк для подхода к промежуточному редуктору
Рис. 2.10. Концевая балка:
1 — кронштейн; 2 — шпангоут № 9; 3, 7 — несъемная и съемная части обтекателя; 4 — лонжерон; 5 — контурный огонь; 6 — антенна изделия 020М; 8 — люк с жабрами; 9 — килевая балка.
Обшивка килевой балки выполнена из листов дюралюминия Д16АТ различной толщины (между шпангоутами № 1...3 толщина 3 мм; между № 3...8 -0,8 мм; № 8...9 - 1 мм).
Обшивка по шпангоуту № 3 усилена наружной накладкой - лентой, а справа между шпангоутами № 7...9 имеется наружный усиливающий штампованный профиль. Сверху на обшивке килевой балки имеются два лючка с жабрами для охлаждения промежуточного редуктора, осмотра и смазки шлицевых соединений хвостового вала трансмиссии, заливки масла в промежуточный редуктор, замера угла излома оси хвостового вала трансмиссии, а также два лючка для осмотра концевой шарнирной части хвостового вала трансмиссии. Справа на обшивке килевой балки у шпангоута № 2 имеется лючок с крышкой для контроля уровня масла в промежуточном редукторе по масломерному стеклу.
Обтекатель увеличивает площадь килевой поверхности КБ для улучшения путевой устойчивости вертолета и состоит из верхней несъемной и нижней съемной частей. Каркас обтекателя КБ включает в себя шесть штампованных стрингеров, шесть нервюр и стыковочные ленты. Каркас склепан с обшивкой из Д16АТ. В нижней части обтекателя расположен люк, в крышке которого выполнены жабры для выхода охлаждающего промежуточный редуктор воздуха. На обтекателе установлен световой маяк ХС-39 и антенны изделия 020М. Съемная часть крепится к поясам лонжерона килевой балки винтами с самоконтрящимися гайками, а несъемная часть - стыковочными лентами на заклепках.
2.6. СТАБИЛИЗАТОР
Стабилизатор предназначен для улучшения продольной устойчивости вертолета в полете и особенно на переходных режимах. Стабилизатор имеет фиксированный угол установки, равный минус 3е. Аэродинамический профиль стабилизатора - симметричный NACA -0012. Обе половины стабилизатора (рис. 2.11), симметрично расположенные относительно ХБ, конструктивно выполнены аналогично и состоят из лонжерона, семи нервюр, диафрагмы, хвостового стрингера, обшивки концевого обтекателя.
Лонжерон склепан из стенки с отбортованными отверстиями и уголковых дюралюминиевых профилей. В корневой части лонжерон усилен накладкой по поясам и стенке, а в передней части — диафрагмой, что существенно облегчает восприятие изгибающего, крутящего моментов, поперечной силы от аэродинамической подъемной силы. Накладка имеет фланец для стыковки с другой половиной с помощью болтов.
Носовые и хвостовые части нервюр отштампованы из листового дюралюминия и приклепаны к поясам лонжерона. На хвостовых частях нервюр имеются зиги с отверстиями для прошивки полотняной обшивки АМ-100-ОП хвостового отсека.
Хвостовой стрингер, приклепанный к хвостовикам нервюр, увеличивает жесткость хвостовой части.
Обшивка носовой части выполнена из листового дюралюминия Д16А толщиной 0,8 мм, приклепанного к полкам носовых частей нервюр и поясам лонжерона. Полотняная обшивка хвостовой части заклеена по швам зубчатыми лентами.
Рис. 2.11. Стабилизатор:
1- штырь-болт; 2 - лонжерон; 3 - серьга навески; 4 - фланец; 5 - нервюра; 6 - лобовая обшивка; 7 - кронштейн крепления канатика лучевой антенны; 8 - противофлаттерный груз; 9 - концевой обтекатель; 10 - пистон с дренажным отверстием; 11 - обшивка хвостовой части; 12 - хвостовой стрингер; 13— дюралюминиевый лист; 14— диафрагма.
На передней части нервюры № 7 закреплен корпус с противофлаттерным грузом массой 0,2 кг, который закрывается съемным концевым обтекателем из стеклоткани, а также узел крепления канатика лучевой антенны.
На носке нервюры № 1 закреплена скоба с серьгой, которой половина стабилизатора с помощью болта соединена с ответным узлом на шпангоуте № 13 ХБ. Ось-болт на фитинге, отштампованном из алюминиевого сплава и установленном на лонжероне у нервюры № 1, соединяется с узлом на шпангоуте № 14 ХБ. Узлы навески стабилизатора защищены специальными чехлами.
2.7 ТЕХНИЧЕСКОЕ ОБСЛУЖИВАНИЕ ФЮЗЕЛЯЖА
Техническое обслуживание фюзеляжа в основном сводится к дефектации обшивки основных частей фюзеляжа, проверки надежности крепления узлов силовых элементов конструкции, состояния остекления фонаря носовой части и остекления грузовой (пассажирской) кабины, периодической проверке направляющих и замков фиксации дверей, створок, блистеров, аварийных люков и крышек и их смазке.
При оперативном обслуживании в соответствии с видами подготовки выполняются следующие работы:
внешний осмотр обшивки носовой, центральной частей фюзеляжа, хвостовой и концевой балок на предмет отсутствия коррозии, трещин, вмятин, пробоин, хлопунов, ослабления и обрыва заклепок;
контроль состояния остекления носовой и центральной частей фюзеляжа на отсутствие трещин, царапин, рисок, коррозии на литых магниевых профилях рамы остекления, механических повреждений прижимных рамок и нарушения герметичности уплотнения;
проверка надежности крепления обтекателя и крышек люков концевой балки;
контроль стабилизатора на отсутствие механических повреждений обшивки лакокрасочного покрытия, загрязнения дренажных отверстий, а также состояния узлов навески стабилизатора, затяжки болтов, их контровки, винтов крепления концевого обтекателя;
проверка чистоты дренажных отверстий на фюзеляже;
контроль плавности хода, фиксации сдвижных блистеров НЧФ, сдвижной двери ЦЧФ, установки ручек аварийного сброса и контровки сдвижных блистеров, входной двери, люка-окна, люка на правой грузовой створке, а также состояния их герметизации;
проверка люка выхода к силовой установке на отсутствие механических повреждений, нарушения герметичности, надежности запорного замка.
При периодическом обслуживании согласно периодичности работ по действующему регламенту производится:
проверка состояния шпангоутов № 10 ЦЧФ в зоне крепления комбинированных узлов амортизаторов главных опор шасси на предмет отсутствия трещин каркаса хвостовой и концевой балок, стабилизатора и узлов его крепления;
осмотр зоны стыка хвостовой балки с центральной частью фюзеляжа, концевой балкой и проверка моментов затяжки гаек болтов крепления хвостовой и концевой балок;
контроль состояния фитингов и опор хвостового вала трансмиссии, кронштейнов под направляющие колодки тросов управления рулевым винтом;
проверка работоспособности механизмов аварийного сброса блистеров, сдвижной двери, шока-окна, люка на правой грузовой створке.
Большие нагрузки, действующие на обшивку, детали и узлы фюзеляжа в полете и при посадке вертолета, являются основной причиной возникновения усталостных трещин, ослабления заклепок, появления, зазоров в соединениях.
На фюзеляж оказывают вредное воздействие солнечные лучи, пыль, грязь, влага, атмосферные осадки, вызывающие коррозию металлических деталей, разрушение защитных покрытий, неметаллических соединений и остекления. Особо опасными являются местапопадания под обшивку кислот, щелочей, бензина, масла и других вредно действующих жидкостей и их паров.
Внешними признаками начала коррозии являются потускнение поверхности, появление темных пятен, а в дальнейшем возникновение раковин, которые, постепенно увеличиваясь, проникают в глубь металла. Коррозия алюминиевых сплавов проявляется наличием на поврежденных участках пятен серовато-белого цвета, коррозия магниевых сплавов -выпучиванием лакокрасочного покрытия и появлением рыхлого солевого налета грязно-белого цвета, а остальных деталей - возникновением на их поверхности коричневато-красного налета.
Обработка пораженных коррозией участков сводится к удалению продуктов коррозии и защите этих участков лакокрасочным покрытием. В случае невозможности восстановления лакокрасочного покрытия при низких температурах на зачищенную поверхность наносят смазку ЦИАТИМ-201.
Дефекация обшивки и узлов фюзеляжа производится на предмет выявления трещин, пробоин, глубоких вмятин, царапин, нарушения лакокрасочного покрытия, ослабления заклепанных швов и болтовых соединений.
Трещины, пробоины, глубокие вмятины и деформация каркаса и обшивки фюзеляжа не допускаются. В этом случае эксплуатация вертолета не разрешается без ремонта поврежденных мест.
Царапины, забоины и поверхностная коррозия глубиной от 0,1 - 0,2 мм устраняются зачисткой с последующим восстановлением лакокрасочного покрытия.
Допускаются плавные вмятины глубиной не более 5 мм на площади до 50 см2 без образования хлопунов. Риски возможны только в пределах плакирующего слоя. Вмятины без трещин и вытяжки материала выравнивают при помощи деревянного молотка и поддержки. При образовании хлопуна с внутренней стороны обшивки приклепывают уголковый профиль жесткости. Деформация, трещины, глубокие вмятины и коррозия силового набора фюзеляжа не допускаются. Ослабление заклепок крепления обшивки обнаруживается по отставанию краски вокруг головки заклепки, темно-серому налету вокруг головок заклепки наличию вибрации при простукивании обшивки деревянным молотком вокруг заклепки. Заклепки, имеющие ослабление или обрыв головок, заменяют. При этом диаметр вновь устанавливаемых заклепок должен быть на 0,5 мм больше старых. Если ослабление заклепок превышает 10% их общего числа, приходящихся на данный отсек, необходимо тщательно проверить обшивку и силовой набор данного отсека в целях выявления причин, вызвавших ослабление заклепок. Небольшие трещины на обшивке засверливают по концам сверлом диаметром 2 мм, затем на место, где находится трещина, ставят накладку и восстанавливают лакокрасочное покрытие.
При повреждении лакокрасочного покрытия обшивки вертолета на суммарной площадки до 15% его общей поверхности старое покрытие на поврежденной части удаляют и наносят новое, а при повреждении ЛПК больше 15% новое покрытие наносят, полностью.
Особое внимание при дефектации фюзеляжа уделяется состоянию остекления фонаря носовой части. На остеклении не допускается больших трещин, пробоин, царапин, рисок и помутнений. Мелкие царапины и помутнение на стеклах удаляют путем полировки. Перед полировкой поверхность стекла очищают от пыли и пятен мягкой фланелью или ватой, смоченной в мыльной воде, а затем протирают чистой сухой салфеткой. На тампон из специальной гигроскопической ваты наносят небольшое количество пасты ВИАМ-1, и стекло полируют до полного удаления царапин и помутнений. Во избежание искажения видимости полируют площадь, несколько превышающую площадь поврежденного участка. При этом следует добиваться плавных переходов на полируемой поверхности. Поверхность оргстекла после полировки должна быть прозрачной и не должна отличаться от остальных участков.
Трещины на остеклении кабины экипажа длиной до 60 мм засверливают по концам сверлом диаметром 3...4 мм, подготавливают заплату из органического стекла толщиной на 1...2 мм более ремонтируемого. Углы заплаты закругляют, а кромки стачивают на конус с плавным переходом к верхней плоскости пластины. Ремонтируемую поверхность и заплату обезжиривают, а затем на них наносят клей, приготовленный растворением опилок органического стекла в дихлорэтане, уксусной или муравьиной кислоте из расчета 2..5 г опилок на 100 г растворителя. Заплату накладывают на ремонтируемый участок и выдерживают в течение определенного времени.
При наличии трещин длиной более 60 мм и пробоин диаметром более 50 мм, а также при возникновении дефектов на лобовых стеклах кабины экипажа, выполненных из силикатного стекла, стекла заменяют.
При техническом обслуживании осматривают болты стыковки хвостовой балки с центральной частью фюзеляжа и концевой балкой и их стыковочных шпангоутов, проверяют момент затяжки гаек стыковочных болтов, контролируют состояние силового набора каркаса фюзеляжа и надежность навески стабилизатора.
Контроль состояния болтов стыковки частей фюзеляжа производится на предмет отсутствия ослабления болтов и надежности контровки их гаек. При проверке момента затяжки гаек болтов их необходимо расконтрить и согласно правилам произвести их затяжку. Момент затяжки гаек болтов крепления хвостовой балки к центральной части фюзеляжа должен быть: для болтов диаметром 10 мм-(2,9±0,29) кгс/м, для болтов диаметром 12 мм-(4,3±0,43) кгс/м. Момент затяжки гаек болтов крепления концевой балки к хвостовой должен быть: для болтов диаметром 10 мм-(2,7 ±0,27) кгс/м, для болтов диаметром 12 мм- (3,3±0,33) кгс/м. После проверки момента затяжки гайки следует законтрить.
На стыковочных шпангоутах не допускаются трещины, вмятины, глубокие забоины и коррозия.
При осмотре силового набора каркаса фюзеляжа обращается особое внимание на отсутствие трещин и ослабление заклепочных швов в зоне крепления узлов к силовым шпангоутам № 7, 10 и 13, а так же повреждение резьбы болтов и ослабление гаек крепления узлов. В случае необходимости эти участки осматривают с помощью лупы 7-кратного увеличения. Аналогичные требования предъявляются и при осмотре состояния шпангоутов № 2, 6, 10, 13, 14 хвостовой балки и № 2, 3, 9 концевой балки. Необходимо обратить внимание на отсутствие трещин, ослабление и обрыв кронштейнов опор хвостового вала трансмиссии, которые не допускаются.
Стабилизатор проверяют на предмет целостности его обшивки, отсутствия трещин на лонжероне и соединительных накладках, ослабления болтов и нарушения контровки гаек крепления половин стабилизатора по стыковочным фланцам.
Дефектация входных дверей, сдвижных блистеров, грузовых створок, люков и крышек предусматривает выявление их целостности, отсутствие деформаций, исправности устройств навески и замков, плавности перемещения подвижных частей и наличия, при необходимости контровки.
Особое внимание при выполнении любого вида технического обслуживания на вертолете обращают на чистоту заправочных и сливных точек систем вертолета, надежность закрытия крышек заливных горловин емкостей, сливных кранов и крышек лючков для подхода к ним. При возникновении дефектов ремонтируют поврежденные части или их заменяют.
Подвижные части элементов конструкции фюзеляжа периодически смазывают смазкой ЦИАТИМ-201 с предварительной протиркой их бензином.
При обслуживании фюзеляжа необходимо предохранять его обшивку от ударов инструментом, стремянками, подвижными наземными средствами. Для защиты обшивки фюзеляжа от воздействия атмосферных явлений при длительной стоянке вертолета его необходимо зачехлить.
2.8 КОНТРОЛЬНЫЕ ВОПРОСЫ И ЗАДАНИЯ
1. Для чего предназначены основные части фюзеляжа: носовая часть, центральная часть, хвостовая балка, концевая балка, стабилизатор?
2. Как конструктивно выполнено остекление фонаря носовой части фюзеляжа?
3. Какова причина усиления шпангоутов №№ 1, 3а, 7, 10, 13 центральной части фюзеляжа?
4. Какие мероприятия реализованы для повышения прочности панелей пола и потолка центральной части фюзеляжа вертолета Ми-8МТВ?
5. Через какие выходы может быть осуществлено аварийное покидание вертолета?
6. Какие продольные элементы жесткости применены в конструкции фюзеляжа вертолета?
7. Как осуществляется регулирование угла установки стабилизатора вертолета?
8. Как осуществляется усиление конструкции стабилизатора в его корневой части?
9. Какие мероприятия реализованы на вертолете Ми-8МТВ для облегчения погрузо-разгрузочных работ?
3 ШАССИ
3.1. ОБЩИЕ СВЕДЕНИЯ
Шасси обеспечивает нормальное стояночное положение вертолета, восприятие и гашение энергии ударов при посадке вертолета, перемещении по земле. Шасси вертолета (рис. 3.1) выполнено по трехточечной схеме и имеет дополнительно хвостовую предохранительную опору.
Передняя опора, включающая в себя однокамерный жидкостно-газовый амортизатор и вильчатый подкос, имеет рычажную подвеску спаренных нетормозных самоориентирующих колес.
Основные опоры образованы двухкамерными жидкостно-газовыми амортизаторами, подкосами, неориентирующимися колесами с тормозными устройствами. Основные опоры воспринимают и поглощают основную часть энергии удара, так как располагаются вблизи центра тяжести вертолета.
Хвостовая опора, представляющая собой совокупность подкосов, жидкостно-газового однокамерного амортизатора, пяты, предотвращает касание хвостовой, концевой балками и рулевым винтом поверхности земли при посадке с большими положительными углами тангажа.
Основные технические шасси приведены в табл. 3.1.
Таблица 3.1
Параметр | Передняя стойка | Главная стойка | Хвостовая опора |
Тип колес | К2-116 | КТ-97/3 | — |
Размеры колес, мм | 595 х 185 | 865 х 280 | — |
Начальное давление пневматических устройств, МПа (кгс/см2) | 0,45 + 0,05(4,5 + 0,5) | 0,55 + 0,05(5,5+0,5) | — |
Объем АМГ-10, см3 | 2080 | 3510 | 300 |
в том числе: | |||
в камере низкого давления | — | 1110 | — |
в камере высокого давления | — | 2400 | — |
Начальное давление азота в амортизаторах, МПа (кгс/см2) | 3,2 + 0,1(32+1) | — | 2,7 + 0,1(27+1) |
в том числе: | — | ||
в камере низкого давления | — | 2,6+0,1(26+1) | — |
в камере высокого давления Полный ход штока амортизатора, мм | — 165 | 6,0+ 0,1(60+1) 360 | — 200 |
в том числе: | |||
камеры низкого давления | — | 120 | — |
камеры высокого давления | — | 240 | — |
Рис 3.1. Шасси:
1- колесо основной опоры; 2- амортизатор основной опоры; 3, 6, 7,12 - карданы; 4 - амортизатор хвостовой опоры; 5- подкосы хвостовой опоры; 8,9 задний подкос и подкос-полуось опоры; 10 - вильчатый подкос передней опоры; 11- колеса передней опоры; 13- амортизатор передней опоры; а – сферическое гнездо под установку гидроподъемника; б- проушины для крепления тросового буксировочного приспособления; в, г – проушины для крепления швартового приспособления;
3.2. ОСНОВНЫЕ ОПОРЫ ШАССИ
Обе основные опоры шасси аналогичны по конструкции.Силовая схема основной опоры ферменная пирамидальная. Составные ее части - двухкамерный амортизатор, подкос-полуось, задний подкос, колесо. Амортизатор верхней проушиной крепится через кардан к комбинированному узлу на шпангоуте № 10 ЦЧФ нижними проушинами - через кардан ответному узлу сверху на подкосе-полуоси, который в верхней части вилкой стыкуется с узлом в нижней части шпангоута № 11 ЦЧФ. Задний подкос нижней вилкой состыкован с задней проушиной подкоса-полуоси, верхней проушиной - через кардан с узлом на шпангоуте № 13.
Амортизатор основной опоры (рис. 3.2) обеспечивает восприятие и гашение энергии удара при посадке, перемещение по неровностям аэродрома, гашение поперечных колебаний вертолета типа «земной резонанс». Амортизатор образован камерой низкого давления (КНД), камерой высокого давления (КВД), переходником.
Основные составные части КНД: цилиндр, шток с удлинительной трубой, верхняя букса, нижняя букса с клапаном торможения, стяжная гайка с сальником, буферное кольцо, ограничительная гайка, зарядный клапан с трубкой уровня, шлиц-шарнир, детали уплотнения и крепления.
Рис. 3.2. Амортизатор основной опоры шасси:
I, II — камеры низкого и высокого давления, 1,7,10,12 — буксы; 2 — диффузор; 3, 9 — клапаны торможения; 4 — упорная втулка; 5, 8,11,14 — гайки; 6, 30 — цилиндр КВД; 13 — уплотнительное кольцо; 15 — сальник; 16 — буферная втулка; 17 — амортизационное резиновое кольцо; 18 — стопорное кольцо; 19 — проушина крепления амортизатора к фюзеляжу; 20,23,24 — дно; 21,25 — трубки уровня жидкости; 22,31 — штоки КНД и КВД; 26 — профилированная игла; 27 — стопорный винт; 28 — штуцер слива жидкости; 29 — проушина крепления амортизатора к подкосу-полуоси; 32 — цилиндр КНД; 33 — шлиц-шарнир; 34 — микровыключатель АМ-800К включения гидроупора; а, б — зарядные клапаны КНД и КВД.
Работа амортизатора
Когда вертолет при посадке касается поверхности авиашинами, то они в первоначальный момент и воспринимают удар, а затем первой обжимается КНД. При этом жидкость из нижней полости цилиндра вытесняется в полость штока, сжимая азот, а также отжимает клапан торможения вверх и проходит через кольцевое отверстие, осевые отверстия в верхнем буртике нижней буксы в увеличивающуюся в объеме кольцевую полость между штоком и цилиндром
Рис 3.3 Работа амортизатора основной опоры
а- принципиальная схема амортизатора; б- работа КНД при прямом ходе; в- работа КНД при обратном ходе; г - работа КВД при прямом ходе;1- цилиндр КВД; 2- шток КВД; 3- цилиндр КНД; 4- шток КНД; 5,8- центральные отверстия; 6,11- осевые отверстия в буксе; 7, 10- клапаны обратного торможения; 9 - отверстия в буртике буксы: 12 – игла.
В конце прямого хода ограничительный буртик на штоке упрется через буферное кольцо, втулку в стяжную гайку, и нагрузка через цилиндр КНД и переходник передастся на шток КВД, который переместится вниз и вызовет уменьшение объема жидкостной полости. Вследствие этого жидкость проходит через центральное отверстие в диффузоре, которое по мере обжатия амортизатора уменьшается профилированной иглой, в верхнюю полость штока, сжимая газ, а также через осевые отверстия в нижней буксе при отжатом вверх клапане торможения и поступает в увеличивающуюся в объеме кольцевую полость между штоком и цилиндром.
В нормальных условиях посадки, при правильной зарядке амортизатора КВД не должна полностью обжиматься, касаясь ограничительным буртиком на штоке стяжной гайки, так как усилие от возросшего давления газа уравновешивает действие внешней нагрузки.
При обратном ходе КВД под действием давления сжатого газа жидкость из полости штока вытесняется через отверстие в диффузоре в увеличивающуюся в объеме полость жидкости в цилиндре, в которую из уменьшающейся кольцевой полости между цилиндром и штоком также выдавливается жидкость через отверстия клапана торможения с большим гидросопротивлением.
Обратный ход КВД ограничивается упорной втулкой на штоке при касании его упорной гайкой на цилиндре.
Обратный ход КНД происходит при отрыве вертолета от поверхности земли или при колебаниях типа «земной резонанс». В этом случае жидкость из верхней полости под действием сжатого газа вытесняется через центральное калиброванное отверстие в нижней буксе в нижнюю жидкостную увеличивающуюся полость, в которую также поступает жидкость из кольцевой уменьшающейся полости между штоком и цилиндром. При этом клапаном торможения закрывается кольцевое отверстие, и жидкость проходит через осевые отверстия с большим гидросопротивлением в нижнем буртике нижней буксы.
Таким образом, кинетическая энергия удара при прямом ходе КНД и КВД расходуется на преодоление гидравлических сопротивлений, вызванных перетеканием жидкости, механическим трением при перемещении штока относительно цилиндра, сжатием газа. На обратном ходе КВД и КНД потенциальная энергия сжатого газа затрачивается на преодоление гидравлического сопротивления
при перетекании жидкости, механического трения между элементами на штоке и цилиндре.
Подкос-полуось изготовлен из хромансилевой трубы, на одном конце которой приварена вилка для крепления к фюзеляжу, а на другом имеется изогнутый переходник с фланцем для крепления корпуса тормоза колеса. Во внутреннее отверстие переходника запрессовывается и дополнительно фиксируется болтом на конических втулках полуось колеса с посадочными поверхностями под внутренние обоймы конических роликовых подшипников и наружной резьбой на конце под стяжную гайку. На переходнике имеются проушины: сверху - для крепления амортизатора, спереди - для буксировочного приспособления, сзади - для крепления заднего подкоса.
Задний подкос сварен из хромансилевой трубы, имеет в верхней части проушину для крепления к фюзеляжу и переходник под штуцер подвода (отвода) воздуха из воздушной системы. В нижней части подкоса расположена вилка для крепления к подкосу-полуоси, проушина для буксировочного приспособления, пробка для слива конденсата. Внутренняя полость подкоса используется в качестве бортового баллона для сжатого воздуха воздушной системы. На левом подкосе на тройнике рядом с штуцером подвода (отвода) воздуха установлен зарядный клапан, используемый для подзарядки пневматиков колес воздухом при отсутствии аэродромных баллонов со сжатым воздухом.
Колесо основной опоры шасси (рис. 3.4) состоит из барабана, тормозного устройства, деталей установки на полуоси. Барабан отлит из магниевого сплава за одно целое с ободом, ступицей, несъемной ребордой. В ступице имеются расточки под конические роликовые подшипники. С внутренней стороны на барабане установлен на болтах тормозной чугунный барабан. Для монтажа пневматика внешняя реборда сделана съемной. Она состоит из двух полуколец, стянутых пластинами на винтах, и фиксируется от осевого смещения буртиком, а от проворачивания - тремя шпонками.
Рис. 3.4. Колесо основной опоры шасси:
I — крышка сальника; 2 — болт; 3 — гайка; 4 — войлочный сальник; 5 — щиток; 6 — конический роликовый подшипник; 7 — барабан колеса; 8, 19 — болты; 9 — корпус тормоза; 10 — барабан тормоза; 11 — регулировочный винт; 12 — пневмоцилиндр; 13 — тормозная колодка; 14 — возвратные пружины; I5 — отверстия для замера зазора между тормозными колодками и барабанами; 16, 17 — конические шестерни; 18 — регулировочный валик; 20 — анкерный валик; 21 — распорная втулка; 22 — полуось
Пневматик состоит из покрышки и камеры с зарядным вентилем. Покрышка включает в себя каркас в виде нескольких слоев корда, протектор, кольца из стальных тросов, завулканизированных в бортах покрышки.
Тормозное устройство состоит из тормозного барабана, корпуса, двух тормозных колодок с фрикционными накладками, двух воздушных цилиндров, двух разжимных рычагов, двух возвратных пружин и двух регулировочных устройств. Корпус и тормозные колодки отлиты из магниевого сплава. Тормозные колодки шарнирно подвешены на анкерных валиках к корпусу, закрепленному на фланце подкосе-полуоси болтами, а противоположные концы колодок через регулировочные устройства (регулировочные валики, винты, конические шестеренки) связаны с разжимными рычагами, соединенными со штоком пневмоцилиндров. При торможении колес воздух из воздушной системы поступает в воздушные цилиндры, в результате чего поршни через штоки поворачивают разжимные рычаги, которые через регулировочные винты прижимают колодки с фрикционными накладками из материала ферродо к тормозному барабану. В этом случае возникает тормозной момент, передающийся через колодки на корпус тормоза. При растормаживании воздух из пневмоцилиндров стравливается в атмосферу через редукционный ускоритель воздушной системы и колодки оттягиваются возвратными пружинами от тормозного барабана. Внутренняя полость барабана и тормозное устройство с внешних сторон закрыты защитными щитками. Колесо устанавливается на полуоси с помощью конических роликовых подшипников, распорной регулируемой втулки, сальников, стяжной гайки с контровочным болтом.
3.3. ПЕРЕДНЯЯ ОПОРА ШАССИ
Силовая схема передней опоры балочно-подкосная. Передняя опора включает в себя амортизатор с рычажным механизмом, вильчатый подкос, два не тормозных колеса.
Амортизатор передней опоры (рис. 3.5) с рычажным механизмом состоит из цилиндра, штока, плунжера, верхнего и нижнего кулачка механизма самоориентации колес, двух направляющих букс, зарядного клапана с трубкой уровня, деталей уплотнения и крепления, поворотного кронштейна, рычага с осью колес, шатуна.
Работа амортизатора
При касании колес поверхности осевая нагрузка, действующая на амортизатор, вызывает перемещение цилиндра с плунжером вниз, и жидкость из нижней полости штока вытесняется через калиброванное отверстие в плунжере в верхнюю полость, сжимая азот.
Обжатие амортизатора (в нормальных условиях эксплуатации вертолета) на прямом ходе прекращается вследствие уравновешивания внешней нагрузки действием давления газа в конце прямого хода. Под действием этого давления на обратном ходе жидкость выталкивается через центральное отверстие в плунжере в нижнюю полость штока.
При прямом ходе амортизатора кинетическая энергия удара затрачивается на преодоление гидравлического сопротивления, которое вызвано перетеканием жидкости, механическим трением между цилиндром, штоком, плунжером, и сжатие газа.
При обратном ходе амортизатора потенциальная энергия сжатого газа расходуется на преодоление гидравлического сопротивления, механического трения, подъем вертолета. Если пренебречь разностью скоростей обжатия и распрямления амортизатора, то соответственно при прямом и обратном хоре количество энергии, рассеянной амортизатором, примерно одинаково.
Рис. 3.5. Амортизатор передней стойки шасси:
1—зарядный клапан, 2— гайка крепления плунжера; 3—проушина крепления амортизатора; 4 — хвостовик плунжера; 5 — пробка слива; 6 — трубка; 7 — стопорное кольцо; 8 — цилиндр; 9 — плунжер; 10 — верхняя букса; 11— поршневое кольцо; 12 — поршень плунжера; 13 — проушина крепления подкоса; 14—проушина для швартовки; 15—шток; 16 — упорное кольцо; 17 — втулка; 18 — нижняя букса; 19 — поворотный кронштейн, 20 — нижний кулачок; 21—втулка крепления буксировочного приспособления; 22 — гайка; 23 — рог поворотного кронштейна; 24 — указатель; 25 — чехол; 26 — шатун; 27 — рычаг; 28 — ось
Когда амортизатор обжат, верхний кулачок механизма самоориентации колес на штоке выходит из контакта с нижним неподвижным кулачком на цилиндре, что и позволяет вертолету разворачиваться на земле самостоятельно или при буксировке. При отрыве колес от поверхности, когда амортизатор распрямляется, шток перемещается вниз с верхним кулачком, который скользит по профилированной поверхности нижнего кулачка до упора, вращается вместе со штоком, разворачивающим через шатун рычаг с колесами, и ставит последние в линию полета. Это и обеспечивает минимальное лобовое сопротивление в полете и готовность к посадке (особенно по самолетному).
Колеса передней опоры (рис. 3.6) в основном аналогичны колесам основных опор, отличаясь тем, что не имеют тормозных устройств. Колеса устанавливаются на оси на конических роликовых подшипниках с помощью распорной втулки, стяжной гайки с контровочным винтами. Подшипники закрываются фетровыми сальниками, а внутренняя полость барабана - защитными щитками
Рис. 3.6. Колесо передней стойки шасси:
1 — роликоподшипник; 2 — гайки крепления колес; 3 — крышка;
4 — вентиль; 5 — реборда; 6 — барабан; 7,9 — щиток; 8 — болты;
10 — сальник; 11 — распорная втулка; 12 — ось колес; 13 — упорное кольцо.
3.4. ХВОСТОВАЯ ОПОРА
Силовая схема хвостовой опоры - ферменная пирамидальная. Составные части хвостовой опоры - амортизатор, два подкоса, пята.
Цилиндр амортизатора (рис. 3.7) выполнен из легированной стали и технологически состоит из трех частей. В верхней части цилиндра установлена бронзовая букса с резиновыми фторопластовыми уплотнительными кольцами и стяжная гайка с фетровым сальником. Шток имеет хромированную внешнюю рабочую поверхность. В нижней его части на резьбе установлена бронзовая букса с калиброванным центральным отверстием, а в верхней части - зарядный клапан, буртик ограничения прямого хода и проушина для крепления амортизатора к хвостовой балке. Между нижней и верхней буксами находится втулка из алюминиевого сплава для ограничения обратного хода.
При прямом ходе амортизатора кинетическая энергия удара расходуется на преодоление гидравлического сопротивления, вызванного перетеканием жидкости через центральное отверстие в нижней буксе из нижней полости в верхнюю полость штока, на сжатие газа, на преодоление механического трения между штоком и цилиндром.
При обратном ходе потенциальная энергия сжатого газа расходуется на преодоление гидравлического сопротивления, механического трения, подъем ХБ и КБ. Жидкость при этом вытесняется из верхней полости в нижнюю через центральное отверстие в нижней буксе.
Рис. 37. Амортизатор хвостовой опоры:
1 — цилиндр; 2, 4 — нижняя и верхняя буксы; 5 — сальник 6 — гайка; 7 — шток; 8 — зарядный клапан.
Подкосы образованы трубами из алюминиевого сплава. Верхней частью подкосы ушковыми болтами через узлы демпферов соединены с ответными узлами на шпангоуте № 15 ХБ.
Узел демпфера состоит из корпуса, внутренней, внешней обойм, резиновой втулки, вильчатого болта. Демпферы, как и резиновые демпфирующие кольца в проушине штока, предотвращают передачу вибраций хвостовой опоры на ХБ.В нижней части подкосы трубчатыми заклепками соединены со стаканами стального сварного узла, как и с корпусом демпфера. К сварному узлу сверху через сферический подшипник болтом крепится цилиндр амортизатора.
Пята, отштампованная из алюминиевого сплава, осью на двух бронзовых втулках установлена на сварном узле и прижимается рычажной пружиной к переднему упору узла.
3.5. ТЕХНИЧЕСКОЕ ОБСЛУЖИВАНИЕШАССИ
При оперативном обслуживании в соответствии с видами подготовки по действующему регламенту выполняются следующие работы:
-осмотр амортизаторов передней, основных, хвостовой опор и их подкосов на предмет отсутствия механических повреждений, коррозии на их элементах, течи из-под резиновых уплотнительных элементов по штокам амортизаторов, нарушения контровки гаек болтов крепления;
-внешний осмотр колес передней и основной опоры на предмет отсутствия механических повреждений, коррозии на барабанах, сдвига покрышки относительно барабана, порезов, проколов, расслоения, вспучивания, износа протектора покрышки, а также проверка контровки гаек крепления колес на оси и наличия колпачка на зарядном вентиле пневматика;
-проверка правильности зарядки пневматиков воздухом по стояночному обжатию пневматиков, а амортизаторов - жидкостью и газом (передней опоры - по стояночному обжатию, главных опор - по выходу штока камеры высокого давления).
При периодическом обслуживании согласно регламенту необходимо:
-проверить уровень масла АМГ-10 в амортизаторах передней, основных и хвостовой опор;
-перебрать колеса передней и основных опор; проверить состояние и работоспособность тормозных колес основных опор;
-замерить зазор в микровыключателях АМ-800К механизмов включения гидроупора в цепи продольного управления.
Дозарядка азотом амортизаторов опор шасси производится следующим образом:
Вертолет на гидроподъемниках поднимают до отрыва колес от поверхности земли. Проверка начального давления азота в амортизаторах передней опоры, камер высокого и низкого давления амортизаторов основных опор производится с помощью приспособления с манометром (рис. 3.8), устанавливаемого с помощью накидной гайки на резьбовую часть зарядного клапана (рис. 3.9). При этом устанавливают заглушку на штуцер подсоединения шланга, закрывают вентиль стравливания, рукоятку штока плавно поворачивают от руки. В этом случае начальное давление соответственно должно быть 3,2 МПа (32 кгс/см2), 6,0 МПа (60кгс/см2), 2,6 МПа (26 кгс/см2).
Рис.3.8 Приспособление для проверки давления и зарядки амортизатора шасси:
1- шток, 2-игла стравливания, 3-манометр, 4 - заглушка, 5 - корпус, 6 – пробка.
Если давление меньше указанного, то нужно произвести дозарядку амортизаторов до нормы азотом из исправного аэродромного баллона с помощью шланга предварительно подсоединенного к штуцеру на приспособлении с манометром при закрытом вентиле стравливания и утопленном штоке приспособления), открыв вентиль баллона и поворачивая рукоятку штока для открытия зарядного клапана амортизатора и контролируя давление по манометру.
В конце зарядки следует перекрыть вентиль баллона, вывернуть шток приспособления рукояткой, стравить давление из шланга, отсоединить шланг, приспособление, проверить герметичность зарядного клапана. Затем нужно опустить вертолет с подъемников и проверить соответствие техническим требованиям выходов штоков камеры высокого давления амортизаторов основных опор, обжатия амортизатора передней опоры.
Рис. 3.9. Зарядный клапан
1- корпус; 2- резиновое кольцо; 3- распорная втулка; 4- шток; 5- пружина; 6- направляющая втулка; 7- гайка; 8- заглушка; 9- тросик
Для дозаливки амортизаторов передней, основных опор шасси АМГ-10 следует:
-поднять вертолет на гидроподъемниках до отрыва колес от поверхности земли;
-стравить поочередно давление из камеры высокого и низкого давления соответствующего амортизатора основных опор с помощью приспособления с манометром, а для амортизатора передней опоры - дополнительно посредством шланга, выведенного за борт и подсоединенного к приспособлению;
-вывернуть зарядные клапаны на соответствующем амортизаторе, обжать плавно полностью амортизатор и убедиться, что уровень масла АМГ-10 находится на высоте среза торна трубки уровня, В противном случае трубку (или поочередно трубки - для основных опор) снять, предварительно выпустив шток (штоки для основных опор);
-дозаправить масло АМГ-10 через воронку до уровня зарядного штуцера, выдержать в течение 90 мин для отстоя пены от растворенного в масле азота, вставить трубку (трубки) уровня, плавно обжать амортизатор до упора для удаления излишков масла;
-установить зарядные клапаны с уплотнительными шайбами, установить на зарядный клапан приспособление с манометром, распрямить амортизатор;
-произвести зарядку амортизатора азотом до соответствующего начального давления от аэродромного баллона со сжатым азотом с помощью шланга.
После зарядки нужно отсоединить шланги и приспособление, проверить герметичность зарядных клапанов, установить колпачки, опустить вертолет с подъемников.
Для дозаливки масла в амортизатор хвостовой опоры следует его снять с вертолета, а затем стравить давление азота, вывернуть зарядный клапан. Масло АМГ-10 следует дозалить в амортизатор до уровня отверстия зарядного штуцера в обжатом положении, выдержать 90 мин, а затем установить зарядный клапан, распрямить амортизатор и зарядить азотом до начального давления (3,5±0,3) МПа((35+3) кгс/см2] при вертикальном положении амортизатора.
После часовой выдержки снизить давление азота до 2,7+0,1МПа, проверить герметичность зарядного клапана, установить на него колпачок, подсоединить амортизатор к вертолету. При неполном выходе штока перед зарядкой азотом разрешается предварительно подавать азот в амортизатор хвостовой опоры до давления 0,1...0,3 МПа (1...3 кгс/см2).
Проверка правильности зарядки пневматических устройств колес шасси заключается в контроле обжатия пневматиков.
При правильной зарядке пневматиков колес главных стоек шасси обжатие их у незагруженного вертолета не должно превышать: (45+10) мм, при массе вертолета 11100...12000 кг- (70+10) мм. Обжатие пневматических устройств передних колес шасси у незагруженного вертолета не должно превышать (30+10) мм, при массе вертолета 11100...12000 кг- (45+10) мм. Если обжатие пневматических устройств колеc шасси не соответствует указанным выше величинам, то требуется проверить давление воздуха в них. Для этого следует поднять вертолет на гидроподъемники и приспособлением (рис.3.10.) проверить давление в пневматических устройствах по манометру. При наличии давления в пневматических устройствах меньше требуемого их дозаряжают воздухом как от бортового, так и от аэродромного баллонов.
Рис. 3.10 Приспособление для проверки давления и зарядки пневматиков колес:
1 - манометр; 2 - запорная игла; 3-корпус; 4 - пружина; 5 - стакан; 6 - игла; 7 - пробка; 8 - заглушка
С этой целью на зарядный штуцер устанавливают приспособление и подсоединяют к нему предохранительный клапан или понижающий редуктор. Если зарядку выполняют от бортового баллона (задние подкосы главных стоек шасси), необходимо к штуцеру бортового баллона подсоединить наконечник и зарядный шланг. Другой конец шланга соединить со штуцером предохранительного клапана и плавным поворотом рукоятки крана наконечника подать воздух на зарядку пневматических устройств.
Контроль зарядки следует вести по манометру приспособления (в случае чрезмерной подачи воздуха предохранительный клапан срабатывает). По окончании операции закрыть кран наконечника и, отвернув на несколько витков зарядный шланг у приспособления, стравить давление воздуха. Снять шланг, приспособление и наконечник и, установив заглушки на штуцера колеса и баллона, опустить вертолет с гидроподъемников.
Зарядку пневматического устройства колеса от аэродромного баллона выполняют в той же последовательности. При перезарядке колес стравливание излишнего давления производят иглой приспособления.
Для обеспечения надежной работы колес периодически при сезонном техническом обслуживании их перебирают и смазывают подшипники колес. Для этого вертолет устанавливают на гидроподъемники, отворачивают гайку крепления колеса и его со всеми деталями демонтируют.
После разборки колеса проверяют состояние покрышки барабана, сальников, подшипников, все снятые детали промывают нефрасом, проверяют давление воздуха в пневматическом устройстве. Установленное на корпус сальника войлочное кольцо должно выступать по окружности на одинаковую по высоте величину и быть плотно установленным в кольцо барабана колеса.
При дефектации деталей колес шасси следует обращать внимание на состояние беговых дорожек, роликов и сепаратора подшипников. Не допускаются неравномерное изнашивание дорожек, подгорание буртиков и роликов. На тормозной рубашке не должно быть трещин, выходящих на внешний торец рубашки или проходящих на всю глубину чугунного слоя. На распорной втулке не допускаются нарушения контровки резьбового соединения и смятия торцов втулки. Пружинное полукольцо должно плотно входить в паз.
На рабочих поверхностях фрикционных накладок допускается неограниченное число мелких трещин. Трещин, проходящих через всю толщину фрикционных накладок, не должно быть.
Расстояние от рабочей поверхности тормозной накладки до головок заклепок должно быть не менее 0,5 мм. Замасленные фрикционные накладки зачищаются шкуркой, а накладки, имеющие недопустимый износ, заменяются. Подшипники колес после промывки смазывают смазкой НК-50.
При монтаже колеса гайку крепления затягивают до отказа и контрят специальным болтом. Не разрешается ослабление гайки крепления колеса, так как зазор в подшипниках регулируется распорной втулкой. После монтажа колес главных стоек шасси необходимо проверить герметичность тормозной и воздушной системы путем постановки на защелку рычага тормоза на 5...6 мин и степень торможения колес. Давление в системе тормозов не должно падать. При приложении усилия к колесу руками оно не должно поворачиваться.
Демонтаж и контроль состояния деталей колес передней стойки аналогичны работам по колесам главных стоек шасси.
Смазка шарнирных соединений подвижных элементов шасси обеспечивается согласно карте смазки путем зашприцовки или набивки смазки рукой. В качестве смазки применяют ЦИАТИМ-201.
3.7 КОНТРОЛЬНЫЕ ВОПРОСЫ И ЗАДАНИЯ
1. Почему крепление амортизатора, полуоси, заднего подкоса главной стойки шасси выполнено шарнирным?
2. С какой целью в камеры высокого и низкого давления амортизатора главной стойки шасси установлены клапаны торможения на обратном ходе?
3. Каково назначение букс амортизаторов? Есть ли принципиальная разница в конструктивном исполнении нижних и верхних букс?
4. Почему амортизаторы передней стойки и хвостовой опоры не имеют клапанов торможения на обратном ходе?
5. С какой целью подвеска колес передней стойки выполнена рычажной?
6. Почему крепление шатуна передней стойки выполнено шарнирным?
7. Почему на зарядные штуцеры КВД и КНД установлены трубки, почему эти трубки изогнуты под прямым углом?
8. Как с помощью визуального контроля можно определить: правильно ли заряжены амортизаторы, пневматики?
9. Почему выход штока амортизатора зависит от веса вертолета?
4. ВОЗДУШНАЯ СИСТЕМА
Воздушная система (ВС) предназначена для торможения колес основных опор шасси и подзарядки пневматиков колес при эксплуатации на необорудованных площадках.
4.1 ОБШАЯ ХАРАКТЕРИСТИКА ВОЗДУШНОЙ СИСТЕМЫ
Технические данные воздушной системы
Рабочее давление в контуре питания
ВС, мПа (кгс/см2) 4...5+0,4
(40...50+4)
Вместимость бортовых баллонов, л 10
Максимальное давление за клапаном
УП 25/2, МПа (кгс/см2) 1,1 (11)
Максимальное давление в магистрали торможения, МПа (кгс/см2)
3,3+0,3 (33+3)
Воздушная система (рис. 4.1) состоит из контура питания и контура потребления (торможения).
Рис.4.1. Принципиальная схема воздушной системы
1- редукционный клапан УП-25/2; 2- редукционный ускоритель; УПО-3/2М; 3 - манометр МА-60К,4- манометр НТМ-100; 5- воздушный компрессор АК-50Т1; 6- бортовые воздушные баллоны; 7- тормоза колес; 8- автомат давления АД-50; 9- обратный клапан636100М; 10,13- прямоточные фильтры723900-4АТ; 11- бортовой зарядный штуцер723900-4АТ; 12- фильтр-отстойник 5565-10
Контур питания (баллонно-компрессорной схемы) включает в себя: бортовые баллоны (задние подкосы основных опор); бортовой зарядный штуцер 3509С50; прямоточный воздушной фильтр; прямоточный воздушный фильтр 723900-6; два обратных клапана 686100М; фильтр-отстойник 5565-10; автомат давления АД-50; воздушный компрессор АК-50Т1; трубопроводы, шланги, манометр НТМ-100 (или МВУ-100).
Контур потребления (торможения) включает в себя: редукционный клапан УП-25/2; редукционный ускоритель УПО3/2М; четыре воздушных цилиндра тормозных устройств колес основных опор шасси; трубопроводы, шланги, манометр МА-60К.
Зарядка ВС может быть произведена от аэродромного баллона со сжатым воздухом на земле или от бортового компрессора АК-50Т1 при работающей трансмиссии.
При зарядке от аэродромного баллона воздух через шланг со специальным переходником под бортовой зарядный штуцер поступает к прямоточному воздушному фильтру 723900-4, где очищается от твердых частиц, проходит обратный клапан (второй обратный клапан не пропускает воздух в магистраль компрессораАК-50Т1) и далее через автомат давления АД-50 - в бортовые баллоны.
Когда давление в бортовых баллонах достигнет 50+0,4 МПа (50+4 кгс/см2), автомат давления АД-50 сообщает источник давления с атмосферой, ограничивая тем самым предельное давление в контуре питания.
В случае зарядки ВС от компрессора АК-50Т1, который при работающем главном редукторе ВР-14 подает воздух к фильтру-отстойнику, очищенный от конденсата воздух следует через автомат давления АД-50 к бортовым баллонам. При давлении в магистрали бортовых баллонов 5,0+0,4 МПа (50+4 кгс/см2) автомат давления АД-50 соединит магистраль от компрессора АК-50Т1 с атмосферой и компрессор переведется на холостой режим работы.Если давление в контуре питания упадет до 4,0 МПа (40 кгс/см2), АД-50 переключит компрессор вновь на подзарядку бортовых баллонов. Давление воздуха в контуре питания контролируется по манометру НТМ-100 (МВУ-100).
При торможении, когда пилот нажимает гашетку на левой ручке циклического шага, через тросовую проводку нажимной рычаг воздействует на редукционный клапан УП-25/2, который понижает давление воздуха, поступающего из контура питания, до управляющего давления 0...0,11 МПа (0...11 кгс/см2), подаваемого к редукционному ускорителю УПОЗ/2М. Ускоритель срабатывает под воздействием УП-25/2, редуцирует давление воздуха из контура питания до необходимого давления торможения 0...3,3±0,3 МПа (0...33±3 кгс/см2) и подает его в пневмоцилиндры тормозных устройств колес. Давление воздуха в контуре торможения контролируется по манометру МА-60К.
Когда гашетка отпускается, воздух из управляющей полости УПО3/2М стравливается в атмосферу через редукционный клапан УП-25/2, в результате чего воздух из пневмоцилиндров стравливается в атмосферу через редукционный ускоритель, что приводит к растормаживанию колес.
4.2АГРЕГАТЫ ВОЗДУШНОЙ СИСТЕМЫ
Воздушный компрессор АК-50Т1 (рис. 4.2) обеспечивает сжатие и подачу воздуха в контур питания ВС.
Основные технические данные АК-50Т1
Тип двухступенчатый одноцилиндровый
Диаметр цилиндра I ступени, мм. 46
Диаметр цилиндра II ступени, мм 40
Ход поршня, мм. 20
Частота вращения эксцентрикового вала, мин-1:
Минимальная 1450
Максимальная 2009
Подача при частоте вращения
1450 мин-1, м3/ч 0,96
Составные части компрессора АК-50Т1: разъемный картер, эксцентриковый валик с подшипниками и шатуном, ступенчатый поршень с кольцами, цилиндры I и II ступеней, впускной, перепускной и нагнетающий клапаны, фильтр.
Компрессор установлен на крышке приводов правого борта главного редуктора ВР-14.
Рис. 4.2. Схема работы компрессора АК-50ТЗ:
I - всасывание и нагревание; II - предварительное сжатие и перепуск воздуха
1 - эксцентриковый валик; 2 - поршень; 3 - нагнетающий клапан; 4 - перепускной клапан; 6 - всасывающий клапан; 7 - цилиндр первой ступени; 8 - цилиндр второй ступени; 9 - картер
Автомат давления АД-50 (рис. 4.3) предназначен для ограничения предельного давления 5,0+0,4 МПа (50+4 кгс/см2) в контуре питания при зарядке от бортового или наземного источника и переключения компрессора АК-50Т1 на рабочий режим с режима холостого хода при падении давления в контуре питания 4 МПа (40 кгс/см2).
Автомат давления АД-50 включает основные составные части: корпус, поршень с редукционной пружиной, иглу с гайкой и двуплечим рычагом, фиксатор с роликом, обратный клапан, фильтр. Автомат давления расположен на панели воздушных агрегатов по левому борту между шпангоутами № 12 и 13 ЦЧФ.
Рис. 4.3. Схема работы автомата давления АД-50:
а- при зарядке воздушной системы; б- при переводе источника зарядки на холостой ход 1- корпус; 2- редукционная пружина; 3- поршень; 4- обратный клапан; 5- фильтр; 6- гайка; 7- игла; 8- рычаг иглы; 9- фиксатор
Редукционный клапан УП-25/2. редуцирует давление воздуха, поступающего из контура питания, до давления 0 - 1,1 МПа (0...11 кгс/см2), необходимого для управления редукционным ускорителем. Основные составные части УП-25/2: корпус, поршень с направляющей гильзой, пружиной, анероидной мембраной, толкатель с редукционной пружиной, клапан впуска с пружиной и соединительной иглой, клапан выпуска с пружиной и направляющей гильзой, детали крепления и уплотнения. В исходном положении, когда на толкатель не действует осевое усилие, клапан впуска закрыт и разобщает магистраль высокого давления с управляющей полостью. Клапан выпуска прижат к своему седлу, но поршень своей пружиной отжат от клапана выпуска, что обеспечивает сообщение через открытый клапан выпуска управляющей полости с атмосферой.
При торможении, когда толкатель под действием осевого усилия перемещает поршень, который садится на клапан выпуска (управляющая полость разобщается с атмосферой), который отходит от своего седла и через соединительную иглу открывает клапан впуска, воздух из контура питания проходит в управляющую полость редукционного ускорителя. В этой полости установится постоянное давление, которое обусловлено ходом толкателя, зависящего от усилия нажатия на гашетку управления на левой ручке циклического шага. При полном ходе толкателя предельное управляющее давление достигнет 1,5 МПа (15 кгс/см2). В конце цикла редуцирования клапаны впуска и выпуска закрываются, а управляющая полость разобщена с атмосферой и контуром питания. При растормаживании, когда осевое усилие с толкателя снимается, клапаны впуска и выпуска и поршень занимают исходное положение. В этом случае воздух из управляющей полости стравливается в атмосферу через осевое и радиальные отверстия в толкателе.
Редукционный ускоритель УПО3/2М (рис. 4.4) редуцирует давление воздуха, поступающего из бортовых баллонов, до давления торможения 0...(3,3±0,3) МПа [0...(33±3) кгс/см2] под действием управляющего давления от редукционного клапана УП-25/2 и подает его к пневмоцилиндрам тормозных устройств колес. Составными частями редукционного ускорителя являются разъемный корпус с четырьмя штуцерами, поршень с направляющей пружиной и двумя резиновыми мембранами, клапан впуска с пружиной, клапан выпуска, детали крепления и уплотнения.
УПО3/2М находится под полом НЧФ у шпангоута № ЗН (рядом с УП-25/2).
Рис. 4.4. Редукционный ускоритель УПО-3/2
1,10,14,15- штуцеры; 2- болт; 3- крышка; 4- ступенчатый поршень; 5,7- резиновые мембраны; 6- кольцо; 8- корпус; 9- клапан выпуска; 11- направляющая; 12- клапан впуска; 13- пружина
Прямоточные воздушные фильтры 723900 (рис. 4.5) очищают сжатый воздух от механических примесей (фильтр 723900-4АТ очищает воздух, поступающий в ВС при зарядке, а 723900-6АТ дополнительно фильтрует воздух, подающийся к УП-25/2 и УПОЗ/2М).
Рис. 4.5 Воздушный фильтр 723900
1- корпус; 2- штуцер; 3- гайка; 4- уплотнительное кольцо; 5- упорная шайба; 6- фетровый диск; 7- латунная сетчатая шайба; 8- валик
Составные части фильтра: корпус со штуцером входа, крышка со штуцером выхода, гайка, фильтрующий пакет (фетровые диски и латунные сетчатые шайбы), две упорные шайбы, валик, уплотнительное кольцо.
Фильтр 723900-4АТ расположен на панели по левому борту (шпангоуты № 12, 13 ЦЧФ), а 723900-6АТ - под полом между шпангоутами № 5Н НЧФ и 1 ЦЧФ.
Фильтр-отстойник 5565 1 (рис. 4.6) очищает воздух, поступающий от компрессора в ВС, от воды, масла, других примесей в инерционном поле. Фильтр состоит из стального цилиндрического корпуса, отражательного стакана, крана (с контргайкой) слива отстоя. Штуцер подвода располагается ниже штуцера отвода очищенного воздуха. Фильтр-отстойник размещен в отсеке главного редуктора слева у шпангоута № 10 ЦЧФ.
Рис. 4.6. Фильтр-отстойник 5565-10
1- отражательный стакан; 2- корпус; 3- кран слива отстоя
Обратные клапаны 636100М позволяют двигаться воздуху только в одном направлении. Составными частями клапана являются корпус со штуцером выхода, штуцер входа, седло, поршень с пружиной и резиновой шайбой, уплотнительное резиновое кольцо. Клапаны крепятся на панели воздушных агрегатов, слева у шпангоутов № 12 и 13 ЦЧФ.
Бортовой зарядный штуцер 3509с50 обеспечивает зарядку бортовых баллонов от аэродромного источника сжатого воздуха. Он состоит из корпуса, штуцера, крышки, уплотнительного резинового кольца и находится слева у шпангоутов № 12 и 13 ЦЧФ.
Трубопроводы контура питания изготовлены из стальных (12Х18Н10Т) трубок, остальные - из АМг2М. Подсоединение трубопроводов к бортовым баллонам и тормозам колес выполнено гибкими бронированными шлангами сечением 4x14 мм.
4.3 ТЕХНИЧЕСКОЕ ОБСЛУЖИВАНИЕ ВОЗДУШНОЙ СИСТЕМЫ
При оперативном обслуживании в зависимости от видов подготовки по регламенту осуществляется: внешний осмотр состояния, герметичности и крепления агрегатов, трубопроводов, шлангов воздушной системы; проверка зарядки и герметичности воздушной системы; слив конденсата из фильтра-отстойника.
При периодическом обслуживании по действующему регламенту производится снятие, контроль, замена или промывка фильтра компрессора АК-50Т1, слив конденсата из бортовых баллонов (при сезонном обслуживании).
Для снятия, осмотра и промывки фильтра АК-50Т1 следует вынуть пакет фильтра из корпуса фильтра, предварительно отвернув болт стяжного хомута, сняв грибообразную крышку и стопорную пружину фильтра; демонтированные детали промыть в бензине Б-70 и просушить. Войлочный фильтроэлемент промывают в ванночке, прополаскивают и встряхивают без обжатия. Последующую просушку производят, обдувая его сжатым воздухом под давлением 0,15...0,2 МПа (1,5... 2,0 кгс/см2). Затем следует убедиться в чистоте полости под фильтром, а в случае загрязнения - протереть смоченной в бензине салфеткой. Для проверки работоспособности клапана выпуска необходимо открыть клапан нажатием на шток, а затем убедиться, что клапан закрывается без заеданий. После этого нужно установить снятые детали на место в обратной последовательности.
При сливе конденсата из бортовых баллонов ВС необходимо:
-стравить давление воздуха из контура питания ВС посредством периодического нажатия на гашетку на левой ручке циклического шага. При этом воздух стравливается в атмосферу через редукционный ускоритель УПОЗ/2М. Для быстрого стравливания можно отсоединить шланг подвода воздуха от тормозного устройства одного из колес, который подсоединяется обратно после уменьшения давления до нуля;
-расконтрить и отвернуть сливную пробку на одном из задних подкосов основных опор шасси и слить конденсат, а затем продуть внутреннюю полость подкоса сжатым воздухом под избыточным давлением 0,1...0,15 МПа (1...1.5 кгс/см2) от аэродромного баллона через шланг, подсоединенный к бортовому зарядному штуцеру;
-установить на место пробку и законтрить. Аналогичную работу выполняют для другого заднего подкоса;
-произвести зарядку ВС сжатым воздухом и проверить герметичность соединений, расстыкуемых при сливе конденсата, посредством мыльной пены (допустимо появлению не более 50 пузырьков воздуха в 1 мин).
Для слива конденсата из фильтра-отстойника необходимо открыть левую боковую створку капота редукторного отсека и открыть кран фильтра-отстойника. Слив конденсата определяют по шипению воздуха и видимым парам и каплям воды, удаляемым под давлением. После удаления конденсата кран фильтра-отстойника закрыть и застопорить контргайкой.
4.4 КОНТРОЛЬНЫЕ ВОПРОСЫ И ЗАДАНИЯ
1. Как осуществляется зарядка сжатым воздухом ботовых воздушных баллонов?
2. Какие фильтры применены в воздушной системе вертолета?
3. Какие изменения в составе воздушной системы проведены по сравнению с Ми-8Т?
5. ТРАНСМИССИЯ ВЕРТОЛЕТА
Трансмиссия предназначена для передачи мощности от двигателей на несущий, рулевой винты, некоторые вертолетные агрегаты, обеспечения наивыгоднейшей частоты и необходимого направления их вращения.
5.1. ОБЩИЕ СВЕДЕНИЯ
Основные агрегаты трансмиссии (рис. 5.1): главный редуктор ВР-14, промежуточный и хвостовой редукторы, хвостовой вал трансмиссии, тормоз несущего винта, вал привода вентилятора.
Главный редуктор ВР-14 согласовывает частоту вращения несущего винта с частотами вращения двигателей для эффективного использования их мощности, а также обеспечивает привод вертолетных агрегатов.
Частота вращения входных валов редуктора-15 000 мин-1
Частота вращения несущего винта на номинальном режиме -192 мин-1
Габаритные размеры, длина-1200 мм:,ширина- 880 мм:, высота-1760 мм:
Масса сухого редуктора, не более, кг 842,5
Конструкция главного редуктора и его системы будут рассмотрены во второй части учебного пособия «Силовая установка вертолета Ми-8».
Сейчас рассмотрим только его кинематическую схему и более подробно изучим другие составные элементы трансмиссии.
Рис. 5.1. Кинематическая схема трансмиссии:
а, г — главные приводы от деятелей; б, д — муфт свободного хода; в — привод вентилятора; е — привод несущего винта; ж — барабан тормоза несущего винта; з — хвостовой вал трансмиссии; и — концевая шарнирная; часть хвостового вала трансмиссии; к — привод рулевого винта; л —резервный; м — привод насоса НШ-39М дублирующей гидросистемы; н — привод компрессора АК-50Т1; п — привод маслоагрегата; p — привод генератора; c, т — приводы датчиков счетчиков оборотов; у — привод насоса НШ-39М основной гидросистемы; ф — привод генератора; 1, 2, 7— зубчатые колеса первой ступени редукции-привода несущего винта; 3, 4, 5, 6— зубчатые колеса привода вентилятора; 8, 9 — зубчатые колеса второй ступени редукции привода несущего винта; 10 — ведомое (колоколообразное) зубчатое колесо; 11- промежуточное зубчатое колесо; 12 — нижний (малый) зубчатый венец двойного зубчатого колеса замыкающего звена третьей ступени редукции привода несущего винта; 13 — верхний (большой) зубчатый венец двойного зубчатого колеса; 14 — сателлит; 15 — ведущее зубчатое колесо дифференциала третьей ступени привода несущего винта; 16,17 — зубчатые колеса привода рулевого винта; 13, 19 — зубчатые колеса промежуточного редуктора; 20, 21 — зубчатые колеса хвостового редуктора; 22...28 — зубчатые колеса приводов агрегатов правого борта; 29 — ведущее зубчатое колесо приводов агрегатов; 31...43 — зубчатые колеса приводов агрегатов левого борга; 30, 34, 35 — зубчатые колеса привода генератора.
5.2. ПРОМЕЖУТОЧНЫЙ РЕДУКТОР
Промежуточный редуктор (ПР) обеспечивает изменение направления вектора вращающего момента, передаваемого хвостовым валом, на угол 450 в соответствии с изгибом концевой балки.
Основные технические данные ПР
Передаточное отношение 1,0
Номинальная частота вращения валов, мин-1 2594
Применяемое масло летом ТСТИП, зимой смесь по объему 2/3ТСТИП + 1/3 АМГ-10
Объем заливаемого масла, л 1,3
Температура масла в редукторе, °С:
допустимая для запуска без подогрева (для разжиженного масла) -30
максимально допустимая 110
Масса редуктора (без масла), кг 24,4±0,5
Составные части ПР (рис. 5.2): картер, узлы ведущего и ведомого валов.
Картер, отлитый из магниевого сплава МЛ-5, имеет две расточки под установку узлов ведущего и ведомого валов, сзади - фланец для крепления ПР; справа устанавливается масломерное стекло и магнитная пробка, сверху -лабиринтный суфлер и масломерный щуп, снизу - отверстие под датчик температуры П-1, технологическая заглушка. Антикоррозионная защита картера - пропитка внутренних поверхностей эмалью БТ-538, а наружных - дополнительная грунтовка и окраска.
Узел ведущего вала включает в себя стакан, вал с коническим зубчатым колесом, шлицевый фланец, два роликовые радиальные и шариковый радиально-упорный подшипники, детали уплотнения и крепления. Стакан отлит из магниевого сплава. Вал изготавливается заодно с ведущим коническим зубчатым колесом и устанавливается с помощью подшипников в расточках со стальными гильзами в стакане и диафрагме картера. Уплотнение по наружной поверхности шлицевого фланца осуществляется с помощью двухступенчатого лабиринтного уплотнения (ответная маслосгонная резьба нарезана на стакане и гильзе передних подшипников) и фетрового сальника. Внутреннее отверстие в носке вала заглушено развальцованной заглушкой из алюминиевого сплава.
Узел ведомого вала аналогичен по конструкции узлу ведущего вала, но технологически они не являются взаимозаменяемыми.Зазор в коническом зацеплении регулируется в заводских условиях постановкой регулировочно-уплотнительных прокладок соответствующего осевого размера между фланцем стакана и картером.
Смазка трущихся деталей производится методом разбрызгивания. Ведущее колесо, погруженное в масляную ванну, захватывает масло, которое обильно смазывает зубчатое зацепление и ближайшие роликовые подшипники и разбрызгивается. Частицы масла оседают в верхних масляных карманах, из которых по каналам поступает на подшипники качения.
Рис. 5.2. Промежуточный редуктор:
1,4- шлицевые фланцы; 2,3 -стаканы; 5,8- ведомое и ведущее коническое колесо; 6-картер; 7-крышка; 9-пробка отверстия под датчик температуры масла; 10- запорный клапан; 11- магнитная пробка; 12- лабиринтный суфлер; 13- масломерное стекло.
Полости между первыми и вторыми ступенями лабиринтных уплотнений наклонными каналами соединены с нижней полостью картера, куда стекает после смазки рабочих деталей масло.
Промежуточный редуктор крепится четырьмя болтами диаметром 12 мм к специальному кронштейну на шпангоуте № 3 КБ.
5.3. ХВОСТОВОЙ РЕДУКТОР
Обеспечивает привод рулевого винта с оптимальной частотой и необходимым направлением вращения.
Основные технические данные хвостового редуктора:
Передаточное отношение 0,432
Номинальная частота вращения ведомого вала, мин-1 1120
Применяемое масло : летом – ТС ТИП , зимой - смесь по объему 2/3 ТС ТИП + 1/3 АМГ-10
Объем заливаемого масла, л 1,7
Температура масла в редукторе, °С:
допустимая для запуска без подогрева -30
максимально допустимая 110
Масса редуктора (без масла), кг 58,7+0,5 -0,8
Составные части ХР (рис. 5.3): картер, узлы ведущего вала, вала рулевого винта, механизм изменения шага рулевого винта, детали уплотнения и крепления.
Картер и крышка ведомого вала отливаются из магниевого сплава МЛ5.
Рис. 5.3. Хвостовой редуктор
1- ведущий вал; 2- шариковый подшипник; 3- маслоуплотнительная гильза; 4- резиновая манжета; 5- втулка; 6- стакан; 7-ведомое зубчатое колесо; 8- крышка картера; 9- ведомый вал; 10- шток управления рулевым винтом; 11- регулировочное кольцо; 12- суфлер; 13- картер; 14-стакан; 15- крышка; 16- звездочка; 17- ходовой винт; 18- шлицевая гильза; 19- ведущее зубчатое колесо
Картер имеет в нижней части -фланец крепления и датчик температуры П-1; справа по полету - заглушка на отверстии монтажа механизма изменения шага РВ; сверху - лабиринтный суфлер; на передней и задней поверхностях - магнитные пробки и масломерные стекла.
Крышка центрируется относительно картера цилиндрическим буртиком и крепится фланцем посредством шпилек, а между крышкой и фланцем устанавливается регулировочно-уплотнительная прокладка.
Узел ведущего вала включает стакан, ведущий и полый валы, ведущее коническое зубчатое колесо, шариковый закрытый подшипник ведущего вала, шариковый радиально-упорный и два роликовых радиальных подшипника полого вала, детали уплотнения и крепления. Валы, зубчатое колесо изготавливаются из легированной стали и оксидируются. Полый вал устанавливается на спаренных роликовом и шариковом подшипниках в стакане, а на роликовом - в расточке картера.
Ведущий вал опирается с помощью шарикового закрытого подшипника в стакане, а противоположным хвостовиком эвольвентными шлицами центрируется относительно полого вала. Стакан центрируется цилиндрическим поясом в нижней расточке картера и крепится шпильками через регулировочно-уплотнительную прокладку.
Выбивание масла из картера через осевое отверстие ведущего вала предотвращается постановкой торцовой заглушки на верхний хвостовик полого вала, маслоуплотнительной втулки с армированной резиновой манжетой, работающей по полому валу, и маслосгонной резьбой, предотвращающей проникновение масла в полость между валами при повреждении или износе манжеты. При нарушении герметичности этого уплотнения масло вытекает через калиброванное контрольное отверстие внизу стакана.
Узел ведомого вала состоит из крышки, вала РВ, ведомого зубчатого колеса, двух двухрядных шариковых радиально-упорных, роликового радиального подшипников, деталей крепления и уплотнения.
Венец со спиральными зубьями, диск и ступица ведомого зубчатого колеса изготовлены как одно целое. Ступица ведомого зубчатого колеса, устанавливаемая на двухрядном шариковом и роликовом подшипниках соответственно в расточках крышки и картера, внутренними шлицами центрируется с валом РВ.
Вал рулевого винта со стороны вывода опирается на двухрядном шариковом подшипнике в расточке крышки и фланцем соединяется болтами со ступицей втулки рулевого винта. Уплотнение вала рулевого винта со стороны вывода - двухступенчатое лабиринтное и с помощью фетрового сальника.
Механизм изменения шага РВ включает составные части: стакан, звездочку-гайку, два шариковых подшипника, ходовой винт, шток, шлицевую гильзу, детали крепления и уплотнения.
Ходовой винт фиксируется на штоке сегментной шпонкой и гайкой, а шток - шлицевой гильзой относительно стакана от проворачивания.
При проворачивании звездочки-гайки цепью, связанной комбинированной проводкой с педалями, ее вращательное движение преобразуется в поступательное движение штока, который передает осевое управляющее усилие через двухрядный шариковый подшипник на ползун узла поводка втулки РВ. В случае выдвижения штока
шаг РВ увеличивается, при втягивании уменьшается.
Смазка рабочих деталей происходит методом разбрызгивания. Ведущее и ведомое зубчатое колеса, находящиеся в масле, захватывают масло, разбрызгивают его и смазывают находящиеся вблизи роликовые подшипники. Спаренные, подшипники полого вала находятся в масляной ванне, а остальные смазываются маслом, поступающим из верхних маслоуловительных карманов по наклонным каналам. Масло после смазки стекает в нижнюю полость картера.
Суфлирование внутренней полости редуктора с атмосферой осуществляется через суфлер лабиринтного типа. Крепление хвостового редуктора производится девятью болтами к шпангоуту № 9 концевой балки.
5.4. ХВОСТОВОЙ ВАЛ ТРАНСМИССИИ.
Хвостовой вал трансмиссии обеспечивает передачу вращающего момента от главного редуктора на рулевой винт. Хвостовой вал горизонтальным участком соединяет главный и промежуточный редукторы, а наклонным -промежуточный и хвостовой редукторы. Составными частями хвостового вала являются передняя шарнирная, передняя жесткая, средняя шарнирная, задняя жесткая, задняя шарнирная и концевая шарнирная части.
Передняя шарнирная часть (рис. 5.4) состоит из трубы и двух шлицевых шарниров.
Шлицевый шарнир образован шлицевыми стаканом и наконечником. Наконечник узким шлицевым поясом сочленяется с широким шлицевым поясом стакана. Осевая фиксация стакана относительно буртика наконечника осуществляется с помощью стяжной гайки, двух амортизационно уплотнителъных колец, двух пар полуколец.
Внутри наконечника развальцована заглушка из алюминиевого сплава. Наконечник запрессовывается в трубу и дополнительно фиксируется двумя коническими болтами, которые после затяжки гайки расклепываются. Труба изготовлена из стали 40ХНМА-Ш, и внешняя поверхность ее оксидируется. Шлицевые шарниры позволяют компенсировать угловые смещения (перекосы). Передняя шарнирная часть стыкуется впереди через барабан тормоза несущего винта со шлицевым фланцем привода рулевого винта с помощью четырех болтов, а сзади - с передним фланцевым наконечником передней жесткой части.
Рис. 5.4. Хвостовой вал
1 - барабан тормоза; 2, 18 - шлицевые стаканы; 3, 11 - гайки; 4 - заглушка; 5 -конусный болт; 6-наконечник муфты; 7 - труба хвостового вала; 8 - резиновое кольцо; 9 - фланец муфты;10-болт; 12 - упорное кольцо; 13 - опора вала; 14 - резиновая обойма; 15 - шариковый подшипник; 16 - фланцевый наконечник; 17 - полукольца; 19 - шлицевый наконечник
Передняя жесткая часть состоит из двух труб, переднего и заднего фланцевого наконечника, соединенных между собой с натягом коническими болтами. Между трубами и наконечниками устанавливаются внутренними обоймами три подшипника закрытого типа, с помощью которых передняя жесткая часть устанавливается через резиновые обоймы в опорах на шпангоутах № 12, 16, 20 ЦЧФ. Передняя жесткая часть задним фланцевым наконечником соединяется со шлицевым шарниром средней шарнирной части.
Средняя шарнирная часть состоит из трубы, переднего шлицевого шарнира, заднего шлицевого шарнира со шлицевой втулкой. Шлицевая втулка подстыкована к стакану заднего шлицевого шарнира и соединяется со шлицевым поясом переднего наконечника задней жесткой части. Такое сочленение позволяет компенсировать термические расширения хвостового вала и фюзеляжа (изготовленных соответственно из стали и дюралюминия, имеющих различные коэффициенты линейного расширения), а также при изгибе ХБ в полете.
Задняя жесткая часть, состоящая из трех труб, переднего шлицевого, заднего фланцевого наконечников, устанавливается на четырех подшипниках закрытого типа через резиновые обоймы в опорах на шпангоутах № 2,6,10,14 ХБ. Задний фланцевый наконечник соединяется со шлицевым шарниром задней шарнирной части с помощью четырех болтов.
Задняя шарнирная часть аналогична передней шарнирной части и задним шлицевым шарниром стыкуется со шлицевым фланцем промежуточного редуктора. Концевая шарнирная часть аналогична средней шарнирной части и нижним шлицевым шарниром соединяется со шлицевым фланцем на ведомом валу промежуточного редуктора, а дополнительной шлицевой втулкой - с ведущим валом хвостового редуктора. Все шарнирные части компенсируют угловые смещения (перекосы), а средняя и концевая шарнирные части -дополнительно и осевые смещения.
Вдоль труб вала нанесены красные метки для контроля вала на скручивание. Шлицевые шарниры смазываются маслом ТСТИП, а шлицевые соединения средней шарнирной и задней жесткой частей, концевой шарнирной части с ведущим валом хвостового редуктора - смазкой СТ (НК-50) при сборке. Общая масса хвостового вала (57± 1,0) кг.
5.5. ТОРМОЗ НЕСУЩЕГО ВИНТА
Тормоз несущего винта (рис. 5.5) обеспечивает сокращение при необходимости времени останова несущего винта после выключения двигателей и стопорение трансмиссии на земле. Тип тормоза - колодочный. Основные составные части тормоза - кронштейн, колодки, барабан, разжимной рычаг, распорный и упорный пальцы, шарнирное звено, регулировочные винты и возвратная пружина.
Рис. 5.5 Тормоз несущего винта
1, 18 - тормозные колодки; 2 - болт крепления разжимного рычага; 3 - фрикционная накладка; 4- разжимной рычаг; 5 - упорный палец; 6, 14 - шарнирные звенья; 7- кронштейн; 8 - стержень; 5 - тормозной барабан; 10, 12, 15, 19, 23 - пружины; 11 - фланец привода рулевого винта;13 - винт; 16 - трос управления; 17 - заклепка; 20 - распорный стержень; 21 – регулировочный винт; 22-барашковаягайка
Кронштейн отлит из алюминиевого сплава и шестью шпильками крепится к среднему корпусу главного редуктора со стороны привода хвостового вала. К хромансилевым колодкам с Т-образным сечением приклепаны заклепками из латуни Л6Г фрикционные накладки из материала ферродо. Колодки через шарнирное звено подсоединены к упорному пальцу, а противоположными концами соединяются с регулировочными винтами. Барабан находится между фланцами привода хвостового вала на ВР-14 и передней шарнирной частью.
При торможении, когда трос передает управляющее усилие от ручки управления в кабине пилотов на разжимной рычаг, происходит поворот последнего относительно оси его подвески на одной из колодок и перемещение распорного пальца, который прижимает противоположную колодку к барабану.
После этого рычаг начинает под действием управляющего усилия поворачиваться относительно распорного пальца, и к барабану прижимается вторая колодка. Тормозной момент с колодок передается через шарнирное звено на упорный палец и далее на кронштейн и картер редуктора. Шарнирное звено создает равномерность прилегания фрикционных поверхностей к барабану, что обеспечивает максимальную эффективность торможения и равномерность износа фрикционных накладок.
Когда управляющее усилие снимается, колодки оттягиваются от барабана возвратной пружиной, являющейся одновременно стопором для регулировочных винтов.
При правильной регулировке радиальный зазор между фрикционными накладками и барабаном в расторможенном положении должен быть равномерным по всей поверхности тормозной колодки и составлять 0,2...0,5 мм.
5.6. ТЕХНИЧЕСКОЕ ОБСЛУЖИВАНИЕ ТРАНСМИССИИ ВЕРТОЛЕТА
При оперативном обслуживании выполняются работы:
внешний осмотр главного редуктора ВР-14, переходников крепления редукторной рамы к среднему корпусу картера, поддона и крышек приводов на отсутствие трещин, коррозии; проверка уровня масла в главном, промежуточном и хвостовых редукторах по масломерным стеклам и дозаправка при необходимости соответствующими маслами; контроль герметичности уплотнений промежуточного, хвостового редукторов.
В соответствии с определенными видами подготовки по действующему регламенту производится;
- внешний осмотр хвостового вала трансмиссии на отсутствие скручивания (определяется по прямолинейным продольным меткам на валу), механических повреждений, коррозии на всех элементах вала, подтекания смазки из подшипников и сдвига защитных шайб, а также резиновых втулок в опорах вала; проверка исправности и надежности крепления тормоза несущего винта.
При периодическом обслуживании осуществляются в соответствии с периодичностью работ по регламенту следующие работы:
-снятие, осмотр, промывка и установка на место маслофильтра главного редуктора, магнитных пробок главного, промежуточного и хвостового редукторов;
-проверка момента затяжки гаек болтов крепления промежуточного, хвостового редукторов, редукторной рамы Вр-14 к фюзеляжу, прицепных подкосов к основным, подкосов к переходникам, переходников к картеру главного редуктора, гаек крепления агрегатов на ВР-14, а также гаек болтов стыковки фланцевых соединений карданного вала привода вентилятора и хвостового вала трансмиссии, отсутствия ослабления конусных болтов хвостового вала;
-замер радиального биения хвостового вала на всех участках, излома в сочленениях, бокового зазора в шлицевых шарнирах;
-наружный контроль хвостового вала и проверка отсутствия повышенного зазора между резиновыми втулками и поверхностью опор, а также снятие и проверка исправности игольчатых подшипников карданного вала привода вентилятора;
-проверка зазора между колодками и барабаном тормоза несущего винта.
Состояние хвостового вала на отсутствие скручивания проверяют наружным осмотром изнутри хвостовой балки по прямолинейности красной линии, нанесенной на трубах частей вала. При обнаружении непрямолинейности красной линии какого-либо участка хвостового вала этот участок заменяют. Простукиванием медным молоточком проверяют отсутствие ослабления гаек в соединениях участков валов между собой и со шлицевыми наконечниками муфт. Ослабленные гайки конусных болтов необходимо подтянуть тарированным ключом с моментом 14...17 Н-м (1,4...1,7 кгс·м) и расклепать концы болтов со стороны гаек.
В процессе осмотра подшипников опор хвостового вала используют бортовое освещение и переносную лампу. При осмотре подшипников особое внимание обращают на отсутствие подтекания смазки, надежность крепления защитных шайб, отсутствие смещения и деформации резиновых обойм подшипников. Участок хвостового вала с дефектами подшипников заменяют. При смещении или проворачивании резиновой обоймы необходимо расконтрить и отвернуть гайки болтов крепления нижней половины опоры, совместив красные метки на обойме и кронштейне, становить резиновую обойму на место, смазать ее касторовым маслом и затянуть гайки. Трещины и срез заклепки крепления опор подшипников хвостового вала не допускаются. При обнаружении среза заклепок проверяют биение в смежных пролетах относительно опоры со срезанными заклепками. Если биение хвостового вала не превышает 0,45 мм, то старую опору можно приклепать на место, увеличив диаметр заклепок на 0,5 мм по сравнению с ранее используемыми.
В шлицевых муфтах хвостового вала с помощью приспособления (рис.5.6)
Рис. 5.6. Приспособление для проверки бокового зазора в шлицевых муфтах хвостового вала
1,2,3- винты; 4- хомут; 5- рычаг; 6- стойка; 7- гайка; 8- зажим; 9- индикатор
проверяют боковой зазор. Хомут 4 приспособления устанавливают на гайку стакана шлицевой муфты у главного редуктора и закрепляют стойкой 6 так, чтобы последняя находилась от головки конусного болта на расстоянии 15...20 мм. На стойку 6 устанавливают зажим 8 с индикатором 9 и перемещением индикатора в зажиме, а также вращением хомута 4 на гайке 7 стакана добиваются положения, указанного на рисунке, а предварительный натяг по индикатору должен быть 0,7...1,2 мм, после чего винтами 1 2, 3 хомут окончательно затягивают.
Ось конусного болта должна быть перпендикулярна оси ножки индикатора. При заторможенной трансмиссии лопасть рулевого винта отводят вращением до прекращения изменения показаний стрелки индикатора приспособления, после чего стрелка устанавливается против деления 0 шкалы индикатора.
После этого лопасть рулевого винта отводят по направлению против вращения и определяют показание индикатора. Аналогично проверяют величину бокового зазора во всех остальных шлицевых муфтах. Если в процессе проверки бокового зазора в шлицевых муфтах хвостового вала его величина превысит 0,6 мм, шарнирную часть хвостового вала с этим шарниром следует замерить.
При температуре наружного воздуха ниже 5° С перед замером боковых зазоров шлицевые муфты необходимо подогреть до температуры 25...30° С.
Проверку излома хвостового вала ведут специальным приспособлением (рис.5.7.)
Рис. 5.7. Приспособление для проверки соосности хвостового вала:
1,5,8- винты; 2- гайка стакана шлицевой муфты; 3- обойма; 4- ось поворота рычага; 6- рычаг; 7- индикатор на незагруженном вертолете.
Вертолет должен быть установлен на ровной площадке против ветра, скорость которого не должна превышать 5 м/с.
Для замера величины излома обойму 3 приспособления надевают на гайку 2 стакана шлицевой муфты и стягивают винтами 1. На рычаге 6 приспособления винтом 8 закрепляют индикатор 7 часового типа и путем перемещения рычага вокруг оси 4 создают предварительный натяг в 1,1...1,2 мм с фиксацией этого положения винтом 5.
Вращая трансмиссию за лопасть несущего винта, необходимо зафиксировать максимальное отклонение стрелки и установить на этом месте деление 0 шкалы индикатора. Повернуть трансмиссию на величину, соответствующую полному обороту хвостового вала, и проверить величину излома, которая не должна превышать 1 мм.
При большей величине излома проверить отсутствие деформации шпангоутов, на которых установлены опоры, разрушение резиновых обойм подшипников в опорах и деформации хвостовой балки.
При осмотре кронштейна крепления гидроусилителей необходимо обратить внимание на отсутствие на нем трещин, коррозии и царапин, а также проверить надежность крепления гидроусилителей и контровку гаек.
Коррозию и царапины глубиной до 0,1 мм зачищают шкуркой с последующим покрытием поврежденного участка лаком. Поскольку агрегаты трансмиссии являются высоконагруженными элементами, при выполнении технического обслуживания обязательно проверяют моменты их затяжки тарировочными ключами.
Шарниры шлицевых муфт хвостового и карданного валов привода вентилятора смазывают маслом для гипоидных передач через их пресс-масленки посредством рычажно-плунжерного шприца. Шлицевые соединения хвостового вала и вала привода вентилятора смазывают смазкой НК-50 путем набивки ее вручную. Остальные места, применяемые масла и способы смазки указаны на рис 5.8
Рис. 5.8.Точки смазки агрегатов трансмиссии:
1 — заправочная горловина маслобака двигателя; 2,4 — шарниры вала привода вентилятора; 3 — шлицевое соединение вала рабочего колеса и вала привода вентилятора; 5 — заправочная горловика главного редуктора; 6, 7, 8, 9, 11, 12, 14, 17 — шлицевые шарниры хвостового вала; 10, 15 — шлицевые соединения соответственно средней шарнирной, задней жесткой частей и концевой шарнирной части с ведущим валом хвостового редуктора; 13 — картер хвостового редуктора; 16 — картер промежуточного редуктора; 18 — подшипники ротора вентилятора,
Обозначение марки смазки: Б - масло Б-ЗВ; МГ - смазка ТСТИП; СТ - смазка НК-50;
0 - смазка ОКБ-122-7.
5.8 КОНТРОЛЬНЫЕ ВОПРОСЫ И ЗАДАНИЯ.
1. Перечислите основные агрегаты трансмиссии. Где они установлены? Каково их назначение?
2. Каково назначение и принцип работы муфт свободного хода?
3. Из каких основных частей состоит картер главного редуктора ВР-14, прокомментируйте их конструкцию?
4. Какова конструкция вала несущего винта главного редуктора ВР-14, чем вы объясните особенности его конструкции?
5. По каким параметрам контролируется состояние масла внутри хвостового редуктора?
6. Какие конструктивные мероприятия обеспечивают уплотнение масляной полости хвостового редуктора?
7. Какие предприняты конструктивные мероприятия для обеспечения смазки подшипников ведомого вала хвостового редуктора?
8. Какие части хвостового вала имеют жесткое соединение, как обеспечивается жесткость в соединении?
9. Как осуществляется регулировка зазора между барабаном и тормозной колодкой тормоза несущего винта?
10. К каким последствиям может привести увеличенный боковой зазор в шлицевых муфтах хвостового вала? Поясните выводы.
6.НЕСУШИЙ И РУЛЕВОЙ ВИНТ.
Несущий винт (НВ) предназначен для создания на всех режимах полета подъемной, движущей сил, моментов продольного и поперечного управления.
6.1 ОБШИЕ СВЕДЕНИЯ О НЕСУШЕМ ВИНТЕ
Несущий винт (НВ) предназначен для создания на всех режимах полета подъемной, движущей сил, моментов продольного и поперечного управления.
Дата добавления: 2021-06-02; просмотров: 787; Мы поможем в написании вашей работы! |
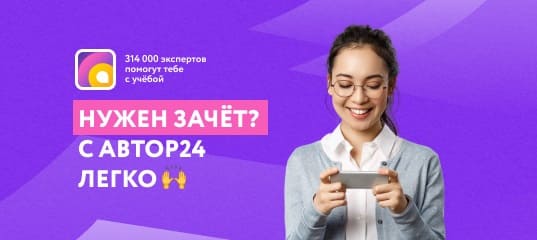
Мы поможем в написании ваших работ!