Основные технические данные НВ
диаметр винта, м2 1,294
Площадь, сметаемая НВ, м2 356,0
Коэффициент заполнения 0,0777
Удельная нагрузка на ометаемую площадь, кгс/ м2 31-36,5
Разнос горизонтальных шарниров, мм 220
Разнос вертикальных шарниров, мм 507
Диаметр втулки НВ, мм 1744
Высота втулки НВ, мм 321
Смещение середины проушины вперед, мм 45
Угол поворота горизонтального шарнира 5о 41 ' 9 ''
Коэффициент компенсации взмаха 0,5
Угол взмаха лопасти (максимальный) 25°±30'
Угол свеса лопасти:
при упоре на скобу 4°
при упоре на собачку центробежного ограничителя
свеса лопасти 1о40'20''
Угол поворота лопасти относительно вертикального шарнира:
вперед (по вращению) 13°±15'
|
|
назад (против вращения) 10°±10'
Масса втулки (сухая), кг 610,525
комплекта НВ, кг 1310,525
Несущий винт состоит из втулки и пяти лопастей.
Втулка НВ обеспечивает передачу вращающего момента с вала НВ главного редуктора на лопасти, а подъемной силы лопастей - в обратном направлении, создавая наивыгоднейшие условия работы для лопастей.
Основные составные части втулки НВ: корпус втулки, пять узлов горизонтальных, вертикальных, осевых шарниров, пять гидродемпферов вертикальных шарниров с компенсационной системой, пять центробежных ограничителей свеса лопасти, детали установки и крепления на валу НВ
Корпус втулки устанавливается эвольвентными шлицами на валу НВ ВР-14 и центрируется нижним бронзовым конусным кольцом, разрезным по радиусу, и верхним стальным конусным кольцом, разрезным по диаметру и охватывающим гайку крепления втулки НВ.
Рис. 6.1. Втулка несущего винта:
1, 10, 19, 31, 39, 58, 62, 66, 81- гайки; 2- верхний конус; 3- компенсационный бачок гидродемпферов; 4, 17, 25, 40- пробки, 5,50 - корпус втулки; 6- скоба; 7, 8, 11, 12, 13, 18, 20, 22, 23, 28, 33, 34, 41, 51, 61, 64, 68, 69, 71, 72, 73- кольца; 9- цапфа осевого шарнира; 14, 65- шпонки; 15, 44, 54, 56, 67- пальцы; 16, 76- крышки; 21, 38, 63- манжеты; 24, 30, 59, 70, 74, 77, 80- подшипники; 26- распорная втулка; 27- роликовый подшипник; 29- корпус осевого шарнира; 32- стопорная пластина; 35, 41- пружины; 36- шайба; 37- заглушка; 43, 55, 82- пресс-масленки; 45- собачка центробежного ограничителя свеса лопасти; 46- нижний упор; 47- нижний конус; 48, 49- пластины контровочные 52- серьга; 57- гидравлический демпфер; 60- кронштейн; 75- валик рычага поворота лопасти; 78, 79- распорные втулки; 83- рычаг поворота лопасти; 84- болт; 85 - втулка.
|
|
Гайка омеднена и имеет внутреннюю резьбу с малым углом подъема и большим числом витков. Контрится гайка тремя штифтами, установленными между коронок гайки и входящими в тело вала НВ, зафиксированными от выпадания под действием центробежных сил пластинами на винтах, которые в свою очередь контрятся попарно проволокой.
Сверху на корпусе втулки имеются отверстия под установку шпилек крепления компенсационного бачка и пять заливных отверстий с пробками, а в нижней части - отверстие под штифт фиксации хомута узла поводка автомата перекоса и пять сливных отверстий с пробками.
|
|
На проушинах, расположенных равномерно по окружности, сверху расположены постоянные упоры ограничения взмаха, снизу - постоянный упор (может меняться при ремонте) ограничения свеса лопасти. Проушины корпуса втулки и проушины скоб образуют горизонтальные шарниры.
Горизонтальные шарниры (ГШ) предотвращают опрокидывание вертолета относительно продольной оси на режимах косого обтекания НВ и разгружают лопасти от изгибающих моментов в их корневых частях. В состав ГШ входят два игольчатых подшипника, палец, детали крепления и уплотнения. В игольчатом подшипнике находится 43 иглы размером 6,5x60 мм. Наружные обоймы подшипников зафиксированы гайками, вворачиваемыми с торцов в отверстия проушин корпуса втулки и имеющими армированные резиновые манжеты. Между наружными обоймами находятся два бронзовых и стальное упорные кольца. Последнее располагается и между внутренними обоймами. Уплотнение внутренней полости ГШ обеспечивается манжетами, работающими по хромированным кольцам (между внутренними обоймами подшипников и проушинами скобы), и резиновыми уплотнительными кольцами под хромированными кольцами и гайками. Палец, проушиной соединенный через серьгу с корпусом упора гидродемпфера, внутри пустотелый, но герметично заглушён с торцов и зафиксирован от проворачивания сегментной шпонкой относительно проушины скобы. Стяжная гайка, наворачиваемая на палец, контрится пластинчатым замком. Для предотвращения утечки масла через уплотнения при повышении давления внутри шарнира в заливное отверстие устанавливается компенсатор давления с пальчиковой диафрагмой, внутренняя полость которой сообщена с атмосферой. Разворот оси ГШ против вращения связан с необходимостью обеспечения одинаковой нагрузки на игольчатые подшипники при воздействии результирующей от силы лобового сопротивления и центробежной силы лопасти. Радиальные нагрузки при маховых движениях лопасти в вертикальной плоскости воспринимаются игольчатыми подшипниками, осевые нагрузки от проушин скобы передаются через хромированные кольца, внутренние обоймы соответствующих подшипников, упорные кольца на корпус втулки НВ. Масло из полости в корпусе втулки НВ поступает на смазку игольчатых подшипников.
|
|
Вертикальный шарнир (ВШ), образованный проушинами скобы и головной частью цапфы осевого шарнира, обеспечивает разгрузку лопасти в корневой части лопасти от изгибающего момента, действующего в плоскости вращения. Конструктивно ВШ выполнен в основном аналогично ГШ. В верхней крышке на пальце установлен компенсатор давления с пальчиковой диафрагмой, а снизу на пальце сливная пробка. Масло из внутренней полости пальца через радиальные отверстия в пальце и внутренних обоймах подшипников поступает на трущиеся детали подшипников. Для удаления под давлением воздушных пробок из масляной полости на упорах головной части цапфы шарнира установлены пресс-масленка и контрольный клапан.
Осевой шарнир (ОШ) позволяет изменять углы установки-лопасти. ОШ образован корпусом и цапфой. При сборке на хвостовик цапфу последовательно устанавливав стяжная гайка с двумя резонов манжетами, хромированное кольцо маслоотражатель, шариковый радиальный подшипник, распорная втулка, двухрядный упорный подшипник, упорная гайка со стопорным замком. Изнутри в корпусе располагаются регулировочное кольцо, тарельчатые пружины. Стяжная гайка заворачивается на внутреннюю резьбу корпуса и контрится пластинчатым замком. На корпусе сверху находится заливная пробка, снизу магнитная проб контрольный стаканчик; на боковой поверхности крепится рычаг поворота лопасти, на внешней торцовой гребешка крепления лопасти.
В осевом отверстии цапфы устанавливаются заглушка и компенсатор давления сильфонного типа, а к проушинам в головной части крепят кронштейны для установки цилиндра гидродемпфера ВШ. Упоры на головной части цапфы ОШ, касаясь упоров на скобе, ограничивают предельные углы поворота лопасти относительно ВШ. Радиальные нагрузки при изменении углов установки лопастей воспринимаются шариковыми подшипниками, а центробежная сила лопасти - через двухрядный роликовый упорный подшипник передается на цапфу ОШ и далее через ВШ, скобу, ГШ на корпус втулки НВ.
Центробежный ограничитель свеса лопасти (рис.6.2) (ЦОСЛ) предотвращает касание лопастью хвостовой балки при неработающих двигателях и малых частотах вращения. Механизм центробежного ограничителя свеса (ЦОСЛ) состоит из противовеса 1, собачки 6, тяги 4, пружины 3, пальцев 2 и 5 и деталей крепления.
Рис.6.2 Механизм центробежного ограничителя свеса
Противовес устанавливается внутри скобы на горизонтальной оси, а собачка с помощью пальца и подшипника скольжения на проушинах снизу скобы. При частоте вращения НВ менее (95±3) мин-1 за счет усилия пружины собачка своим упором касается упора на скобе, и угол свеса лопасти минимальный (1°40'). Когда частота вращения возрастает свыше указанной, противовес за счет центробежной силы проворачивается, преодолевая усилие пружины, и упор собачки начинает выходить из соприкосновения с упором корпуса. При частоте вращения НВ, равной (108±3) мин-1, он полностью выйдет, и максимальный угол свеса ЦОСЛ станет 4°,что необходимо для обеспечения требуемой продольной и поперечной управляемости вертолетом.
Гидравлический демпфер ВШ (рис. 6.3) стабилизирует колебания лопасти относительно ВШ, воспринимая и поглощая часть кинетической энергии колебаний. Составные части гидродемпфера: Цилиндр с крышкой и направляющими буксами, шток с поршнем, восемь перепускных клапанов, узел упора, серьга, компенсационная система, детали крепления и уплотнения. Цилиндр цапфами установлен на игольчатых подшипниках на двух кронштейнах, связанных с цапфой ОШ. На резьбе хвостовика штока закреплен корпус упора с резиновым амортизатором, соединенный с серьгой пальцем через бронзовую втулку, а серьга связана с пальцем ГШ шарнирно на игольчатых подшипниках.
Уплотнение по штоку обеспечивается резиновыми кольцами, находящимися между фторопластовыми кольцами. Резиновый гофрированный чехол, закрепленный на корпусе упора и цилиндре, защищает шток от загрязнения. Компенсационные клапаны шарикового типа (два основных и один промежуточный) установлены в расточке прилива на крышке. Полость между клапанами соединена через штуцер и шланг с компенсационным бачком. Компенсационный бачок, имеющий литой из сплава АЛ9 корпус и колпак из органического стекла, установлен на корпусе втулки НВ.
Рис. 6.3. Гидравлический демпфер.
1,14, 19 - бронзовые втулки; 2-палец; 3,13, 20, 28 - уплотнительные кольца; 4 - заглушка; 5, 6, 7 - шарики компенсационного клапана; 8, 27 - клапаны; 9- пробка; 10 - стакан; 11 - шток; 12 - штуцер; 15 - корпус перепускного клапана; 16- конус перепускного клапана; 17 - пружина; 18 - гайка; 21 - чехол; 22 - амортизатор; 23 - корпус упора; 24 - цилиндр; 25 - цапфа; 26 - поршневые кольца; 29 - болт; 30 - крышка
Лопасть в полете совершает колебательные движения относительно ВШ под действием переменной по величине результирующей от силы лобового сопротивления лопасти и проекции кориолисовой силы. Избыток кинетической энергии при этом затрачивается на преодоление трения между штоком, поршнем и цилиндром, а также гидравлического сопротивления при перетекании жидкости через перепускные клапаны. Клапаны открываются при избыточном давлений масла АМГ-10 в полостях цилиндра свыше 2 МПа (20 кгс/см2); четыре клапана перепускают жидкость в одном направлении, четыре в противоположном. Усилие на штоке гидродемпфера на стабилизированном этапе работы приблизительно равно 1500 кгс (при частоте вращения около 192 мин-i). упор с резиновым амортизатором смягчает удар цилиндром в начале раскрутки НВ.
Масло АМГ-10 из бачка под действием центробежных сил и гидростатического давления поступает малыми дозами в полость пониженного давления в цилиндре через открытый соответствующий компенсационный клапан. Одновременно пузырьки воздуха удаляются в компенсационный бачок, который сообщен с атмосферой калиброванным отверстием.
При неработающем гидродемпфере обе его полости соединяются с кольцевой расточкой между компенсационными клапанами, что позволяет удалить воздух из полостей гидродемпфера и излишки жидкости при повышении температуры.
Виброгаситель (маятниковый гаситель вибрации) (рис.6.4) установлен на некоторых вертолетах с целью уменьшения уровня вибраций ряда систем и агрегатов, повышения эксплуатационной надежности авиационного и радиоэлектронного оборудования вертолета, а также для улучшения условий работы экипажа.
Рис. 6.4. Виброгаситель
Виброгаситель состоит из кронштейна 15, ступицы 3 и пяти маятников 7.
Кронштейн 15 выполнен в виде конусного диска, в нижней части которого выполнены расточка для центрирования относительно корпуса втулки несущего винта и пять приливов с отверстиями под пальцы крепления виброгасителя. К верхнему фланцу кронштейна с помощью шпилек крепится ступица 3 виброгасителя. С наружной стороны кронштейна 15 выполнена кольцевая полость, которая совместно с закрепленным к ней колпаком из оргстекла образует компенсационный бачок 14 для питания гидродемпферов.
При установке виброгасителя компенсационный бачок с втулки винта снимают.
Ступица 3 имеет пять рукавов с отверстиями по концам для монтажа на бифилярных подвесках пяти маятников 7. Каждая бифилярная подвеска представляет собой две роликовые связи, свободно посаженные в отверстии маятника и рукава ступицы. Для этого в отверстия маятников и рукавов ступицы запрессованы втулки 9 и 13. Сочленение маятника со ступицей выполнено посредством двух одинаковых наборов, каждый из которых состоит из болта 4, трех роликов 5, 10 и 11 и двух специальных шайб 12. Снаружи подвеска с маятником закрывается обтекателем 8. Для предотвращения повреждения обтекателя при работе маятника внутри обтекателя установлены ограничители 6. Виброгаситель к втулке 19 несущего винта крепят специальными полыми пальцами 18, ввернутыми в отверстия корпуса втулки. На пальцы насажены заливные горловины 17 с пробками 16 для заправки маслом горизонтальных шарниров. Для защиты токосъемника противообледенительного устройства несущего винта на верхней части диска ступицы 3 закреплен металлический зонт 2 с колпачком 1. Центрирование кронштейна 15 производится переходником 20, закрепленным к втулке болтами 21.
При вращении несущего винта происходит плавная раскачка маятников. Возникающие при этом инерционные силы масс маятников оказывают сопротивление переменным нагрузкам в плоскости вращения, действующим на втулку несущего винта со стороны лопастей. Подбор массы маятников и угла их установки (36° ±30') по отношению к оси рукавов втулки несущего винта приводит к тому, что внешние переменные по величине и направлению силы в основном уравновешиваются за счет динамической реакции маятников.
Лопасть несущего винта, (рис. 6.5) создающая подъемную аэродинамическую силу, имеет прямоугольную форму в плане с хордой 520 мм. Аэродинамические профили лопасти (рис. 6.5) следующие: между сечениями 0...1 -NACA-230; между 2...3 - NACA-230-12; между 4...22 на участке 0...50 % хорды -NACA-230-11 с увеличением ординат на 1 мм, на участке 50...95 % хорды увеличение ординат происходит по линейному закону до нуля. Начальные углы установки лопасти в сечениях 1...4 - 5" и далее изменяются по линейному закону до 0е в сечении 22. Относительная толщина профиля лопасти в процентах от хорды: в корневом сечении 13,0 %, в концевом сечении - 11,38 %. Масса лопасти- 135 кг.
Рис. 6.5. Лопасть несущего вита:
а — общий вид лопасти; б — корневая часть лопасти; в — типовое сечение лопасти; г — концевая часть лопасти; 1 — штепсельный разъем; 2 — комлевый наконечник; 3 — зарядный вентиль; 4 — крышка; 5 — сигнализатор давления; 6 — болт; 7 — лонжерон; 8 — хвостовой отсек; 9 — лампа контурного огня; 10 — законцовка; И — узел балансировочных пластин; 12 — заглушка; 13 — резиновый вкладыш; 14 — прижим; 15 — винтовой упор; 16 — противофлаттерный груз; 17 — резиновый уплотнительный вкладыш; 18 — сотовый заполнитель.
Лопасть выполнена цельнометаллической, и основными ее частями являются: лонжерон, комлевый наконечник, 21 хвостовой отсек, законцовка, балансировочные грузы, противообледенительное устройство, система сигнализации повреждения лонжерона.
Лонжерон основной силовой элемент, воспринимающий изгибающий и крутящий моменты, поперечную силу, действующие на лопасть. Лонжерон изготавливается из алюминиевого сплава АВТ1 и имеет наружную поверхность, обработанную под аэродинамический профиль с учетом установки нагревательных элементов и наклепанную на глубину 0,3...0,4 мм для увеличения усталостной прочности. К комлевой части лонжерона девятью сквозными и двенадцатью несквозными болтами во втулках крепится своим щеками стальной комлевый наконечник. При этом во внутренней полости установлен текстолитовый вкладыш во избежание деформации лонжерона при затяжке болтов. Комлевый наконечник гребенкой с помощью двух болтом крепится к ответной гребенке на корпусе ОШ.
Для поперечной противофлаттерной балансировки лопасти в носке лонжерона в концевой его части установлены в резиновой оболочке (для предотвращения вибраций и развития фреттинг-коррозии восемь противовесов длиной 400 мм и массой 1 кг каждый. Они же одновременно обеспечивают и продольную балансировку лопасти для уменьшения изгибных колебаний, а винтовой упор в районе последнего отсека предотвращает их осевой сдвиг под действием центробежных сил. Дополнительно продольная балансировка обеспечивается пластинами, установленными на шпильках с внешней стороны концевой заглушки под передней съемной частью законцовки. В съемной части законцовки имеется вырез, закрытый оргстеклом, для обеспечения видимости контурного огня. Задняя часть законцовки - несъемная.
Четыре секции нагревательных элементов (две сверху и по одной снизу и на носке) изготовлены из нержавеющей стали и помещены в изолирующий пакет из шести слоев стеклоткани и поверхностного антиабразивного резинового слоя.
На расстоянии 5 м от конца лопасти крепится антиабразивная оковка из нержавеющей стали с нанесенным слоем полиуретана толщиной 0,8... 1,0 мм.
Герметизация внутренней полости лонжерона обеспечивается корневой заглушкой, а также концевым герметизирующим узлом, состоящим из концевой заглушки с направляющими, прижима и резинового вкладыша.
На корневой заглушке находится зарядный вентиль колпачком и штепсельный разъемы переменного (для противообледенительного устройства) и постоянного (для лампы контурного огня) тока.
Рис. 6.6 Сигнализатор давления воздуха:
1- колпачок; 2- корпус ; 3- чувствительный элемент
Система сигнализации повреждении лонжерона - пневматическая визуальная с помощью сигнализатора давления (рис 6.6).
Сигнализатор давления состоит в корпуса с колпачком из органического стекла, чувствительного элемент анероидного типа с красным сигнальным пояском, бронзовой гайки с направляющей и заглушкой. Корпус на герметике вворачивается в резьбовое отверстие на задней стенке лонжерона корневой части.
Давление воздуха, закачиваемого через зарядный вентиль ручным насосом, в лонжероне на 0,015 МПа (0,15 кгс/см2) больше, чем давление начала срабатывания.
Давление гелия внутри анероида при температуре +15 0С составляет 0,105 МПа (1,05 кгс/см2). При повреждении лонжерона, когда давление в лонжероне стравливается через трещину и станет меньше давления гелия в анероиде, последний разжимается и красный сигнальный поясок появляется в поле зрения лица, производящего оперативное техническое обслуживание.
Каждый из хвостовых отсеков образован двумя нервюрами, хвостовым стрингером, обшивкой и сотовым заполнителем. Сотовый заполнитель получается склеиванием из алюминиевой фольги толщиной 0,04 мм, фрезерованием под аэродинамический профиль и дальнейшим растягиванием. Нервюры из авиаля толщиной 0,4 мм приклеены к задней стенке лонжерона. Обшивка из авиаля толщиной 0,3 мм огибает хвостовой текстолитовый стрингер, приклеивается к сотовому заполнителю и отбортовывается впереди в продольную канавку на полках лонжерона. На отсеках 16, 17 установлены триммерные пластины для изменения моментных характеристик лопасти при регулировании несущего винта на соконусность.
6.2. РУЛЕВОЙ ВИНТ
Рулевой винт (РВ) обеспечивает создание силы тяги, момент которой относительно центра масс вертолета уравновешивает реактивный момент НВ и создает управляющий путевой момент, а также улучшает путевую устойчивость вертолета.
Основные технические данные РВ
Тип винта изменяемого шага толкающий
Диаметр винта, м 3,908
Направление вращения.по часовой стрелке, если смотреть со стороны РВ
Ометаемая площадь, м2 12
Коэффициент заполнения 0,135
Коэффициент компенсации взмаха 1,0
Установочные углы лопастей:
минимальный -6°50+1о10
максимальный 23
максимальный, ограниченный СПУУ-52 17°21'±25'
Угол отклонения лопастей от нейтрального положения в кардане:
к КБ 10°±10'
от КБ 12°
Форма лопасти в прямоугольная
Профиль NACA-230M
Хорда лопасти, мм.- 305
Масса , кг 13,85
Масса комплекта винта со смазкой, кг . 122,8
Рулевой винт состоит из втулки и трех лопастей.
Втулка РВ (рис. 6.7) включает основные части: ступицу, общий горизонтальный шарнир, три узла осевых шарнира, узел поводка.
Ступица является базовой деталью, на которой устанавливаются остальные элементы втулки РВ. Ступица восемью болтами крепится к ведомому валу хвостового редуктора. Внутри ступицы нарезаны эвольвентные шлицы, по которым ответными шлицами перемещается ползун, а также имеются две направляющие бронзовые буксы. На внешней поверхности устанавливается ограничитель взмаха, на шлицах -траверса, гайка с пластинчатой контровкой и пресс-масленка. На фланце ступицы расположен клапан предельного давления.
Общий горизонтальный шарнир (типа кардан) состоит из основных деталей: траверсы, корпуса кардана, корпуса втулки, четырех роликовых конических подшипников, деталей .уплотнения и крепления. Узел кардана позволяет втулке наклоняться на угол +80 -100. Корпус кардана устанавливается на цапфах траверсы с помощью двух конических роликовых подшипников. Внутренние обоймы на цапфах фиксируются гайкой, наружные - в стаканах, установленных в расточках корпуса кардана. Уплотнение полостей подшипников обеспечивается резиновыми манжетами и крышками. Корпус втулки в свою очередь посредством двух конических роликовых подшипников устанавливается на двух цапфах кардана, оси которых перпендикулярны оси цапф корпуса кардана.
Осевой шарнир образован корпусом и цапфой, а дополнительными его элементами являются стяжная упорная гайка, упорное кольцо, роликовые однорядный и двухрядный упорные подшипники, роликовый радиальный подшипник. На корпусе имеется гребенка для крепления лопасти НВ, прилив для установки рычага поворота лопасти, а также масляный бачок, корпус которого изготовлен из полиамида. Корпус бачка крепится винтом к корпусу ОШ. На нем имеются два отверстия с пробками, используемыми при заправке и сливе масла. Контрольный стаканчик изготовлен из органического стекла, с помощью которого определяются объем и качество масла в ОШ.
Двухрядный роликовый подшипник имеет ролики размером 12x12 мм, оси которых расположены под углом 32'± 6 к линии радиусов, а беговыми дорожками являются торцовые цементированные поверхности упорной и стяжной гаек. Роликовый радиальный подшипник имеет насыпные ролики 7,5x7,5, внутренней обоймой которого является поверхность упорной втулки и расточка на стяжной гайке. Однорядный роликовый подшипник обеспечивает предварительный натяг упорного двухрядного роликового подшипника с помощью регулировочного кольца. Уплотнение полости ОШ создается резиновыми манжетой, кольцами и заглушкой из алюминиевого сплава, развальцованной в осевом отверстии цапфы ОШ.
Узел поводка, позволяющий совместно с узлами осевых шарниров и механизмом изменения шага рулевого винта хвостового редуктора изменять углы установки лопастей РВ, состоит из ползуна, поводка, трех тяг поворота лопастей, трех рычагов поворота лопастей.Внутри носка ползуна устанавливается наружная обойма двухрядного шарикового подшипника, которая фиксируется крышкой относительно ползуна. Внутренняя обойма подшипника через промежуточную втулку устанавливается на штоке механизма изменения шага РВ и поджимается гайкой с пластинчатым замком. На крышке расположена пресс-масленка, а на поводке - клапан предельного давления. Поводок установлен на внешней поверхности ползуна и фиксируется от проворачивания тремя штифтами, а от осевого сдвига - гайкой с пластинчатой контровкой.
Поводок своими тремя рычагами соединяется шарнирно с помощью сферических подшипников и болтов с тягами поворота лопастей. Тяга поворота лопасти регулируется по длине и состоит из вилки, стрежня и ушкового наконечника. Вилка тяги посредством двух шариковых подшипников и болта сочленяется с рычагом поворота лопасти.Рычаг выполнен в виде валика, установленного эксцентрично относительно оси ОШ в расточке прилива корпуса ОШ на двухрядном шариковое и игольчатом подшипниках.
Рис. 6.7. Рулевой винт:
1 — ползун; 2,12 — бронзовые втулки; 3 — ступица; 4 -ограничитель взмаха; 5, 11, 14,31, 36, 45, 49 — гайки различного назначения; 6,32, 46, 48,50 — роликовые подшипники; 7,38,41 — регулировочные кольца; 8,33,37—стаканы подшипников; 9,17,40,43 — армированные резиновые манжеты; 10 — пресс-масленка; 13 — резиновый чехол; 15 — гайка-крышка; 16,27 — шариковые двухрядные подшипники; 18 — поводок; 19 — тяга поворота лопасти; 20—сферический подшипник; 21, 25 — болты; 22 — масляный бачок; 23 — контрольный стакан; 24 — пробки; 26 — колпачковая гайка; 28 — валик; 29 — игольчатый подшипник; 30 — крышка; 34 — корпус кардана; 35 — траверса; 39 — стопорная пластина; 42, 44 уплотнительные резиновые кольца; 47 — упорное кольцо; 51 — регулировочное кольцо упорного подшипника; 52 —корпус осевого шарнира; 53 — корпус втулки; 54 — комлевый наконечник; 55 — сотовый заполнитель; 56 — лонжерон;57 — противообледенительное устройство; 58 — оковка; 59 — шпилька; 60 — балансировочные пластины; 61 — съемная часть законцовки; 62 — концевая нервюра; 63 — несъемная часть законцовки; 64 — хвостовой отсек; 65 — хвостовой стрингер.
При отклонении вперед правой педали управляющее усилие через комбинированную проводку передается на механизм изменения шага РВ, шток выдвигается и перемещает ползун с поводком, который в свою очередь перемещает три тяги поворота лопастей. Через рычаги поворота лопастей происходит разворот корпусов ОШ на увеличение положительных углов установки лопастей - тяга РВ возрастает.
Лопасть РВ - цельнометаллическая, имеющая прямоугольную форму в плане, включает в себя основные части: лонжерон, комлевый наконечник, хвостовой отсек, законцовку, противообледенительное устройство, балансировочный груз.
Лонжерон, изготовленный из алюминиевого сплава АВТ1, имеет поверхностное упрочнение наклепом для повышения усталостной прочности после обработки под аэродинамический
профиль.
К задней стенке лонжерона в комлевой части на клее-пленке ВК-3 приклеен силовой клык из сплава АК6, дополнительно закрепленный к лонжерону двумя втулками.
Комлевый наконечник из стали 18Х2Н4МА крепится к лонжерону восьмью сквозными болтами во втулках и приклеен клеем МПФ-1.
Вдоль носка лонжерона проложены две секции нагревательных элементов из стали, помещенных в пакет из пяти слоев стеклоткани, приклеенной к лонжерону и закрытых сверху одним слоем стеклоткани и абразивостойкой резины ВР-3а. По передней кромке установлена оковка из нержавеющей стали. На концевой поверхности лонжерона установлены две шпильки под крепление балансировочных пластин. Для герметизации внутренней полости в комлевой части с торца в лонжерон вклеен резиновый вкладыш с нанесенным по контуру герметикам.
Законцовка имеет несъемную часть, приклепанную к концевой нервюре и съемную часть из нержавеющей стали, крепящуюся к лонжерону на четырех винтах.Обшивка хвостового отсека выполнена толщиной 0,4 мм из двух слоев стеклоткани, склеенной с сотовым заполнителем клеем-пленкой ВК-3, с концевой нервюрой из авиаля толщиной 0,4 мм, по задней кромке - с хвостовым стрингером.Хвостовой стрингер усилен и связан с концевой нервюрой и силовым клыком.
6.3 ТЕХНИЧЕСКОЕ ОБСЛУЖИВАНИЕ НЕСУЩЕГО И РУЛЕВОГО
ВИНТОВ.
Несущий винт является одним из самых ответственных агрегатов вертолета, от надежности которого во многом зависит безопасность полетов. Поэтому техническое состояние втулки и лопастей винта контролируется при выполнении всех видов технического обслуживания вертолета.
При контроле на втулке несущего винта проверяют надежность крепления агрегатов и элементов конструкции втулки, контровки болтов и гаек, герметичность шарниров втулки и компенсационного бачка гидродемпферов. При наличии течи масла из-под пробок шарниров ее устраняют подтяжкой пробок или заменой уплотнительных прокладок. Обнаружив подтекание масла, необходимо проверить уровень масла в шарнирах и при необходимости дозаправить их.
Забоины на деталях втулки глубиной до 0,2 мм, а также налет коррозии удаляются шлифовальной шкуркой с последующим нанесением бесцветного лака. При обнаружении трещин на корпусе втулки, серьге, цапфе и на корпусе осевого шарнира втулку заменяют. На центробежных ограничителях свеса лопастей не должно быть наклепа и выработки на собачках и упоре. Выработка вкладышей упоров ограничителей свеса лопастей, вызывающая нарушение угла свеса, не допускается.
При выполнении обслуживания втулки проверяют моменты затяжки элементов крепления серьги и кронштейна гидродемпфера, рычагов поворота лопастей и гайки крепления втулки на валу несущего винта. Проверяя момент затяжки гайки крепления пальца серьги, необходимо, расконтрив ее, ослабить на половину оборота, после чего затянуть тарированным ключом с моментом 60...80 Н·м и вновь законтрить. Момент затяжки болтов крепления кронштейнов гидродемпферов должен быть 45...60 Н·м (4,5...6 кгс·м), а болтов крепления рычагов поворота лопастей 100...110 Н·м (10...11 кгс·м), причем затяжку болтов в этих случаях проверяют по диагонали.
Особое внимание следует обратить на состояние лопастей несущего винта. Контролируя состояние лопастей, проверяют отсутствие вспучивания и отставания обшивки хвостовых отсеков в местах приклейки к сотовому заполнителю, лонжерону, нервюрам и хвостовым стрингерам. Лопасти, имеющие вспучивание и задиры обшивки, трещины и пробоины хвостовых отсеков, без выполнения ремонта к эксплуатации не допускаются. При наличии на обшивке царапин без обнажения металла, плавных вмятин без разрыва металла глубиной до 2 мм и площадью до 100 см2 не более двух на каждой стороне отсека разрешается дальнейшая эксплуатация лопастей. Допускаются к ремонту отсеки с пробоинами величиной 20 х 20 мм, расположенными не ближе 20 мм от стенки лонжерона и 10 мм от нервюр и заднего стрингера, причем количество указанных пробоин должно быть не более двух на отсеках 2...10 и не более одной остальных отсеках. Допускается эксплуатация лопастей с трещинами, абразивным износом и повреждениями резины без оголения лент нагревательных элементов и металла лонжерона, если они не нарушают нормальной работы несущего винта. Стальная противоабразивная оковка не должна иметь существенных повреждений. Разрешается эксплуатация лопастей при нарушении склейки оковки на одном ее лепестке до 8 см2, не выходящей на кромку, с общей площадью на оковку до 50 см2, вмятины глубиной до 1 мм без сквозного пробоя оковки, а также незначительный абразивный износ оковок или полиуретанового покрытия. При осмотре комлевых наконечников следует обращать внимание на отсутствие трещин, механических и коррозионных повреждений в местах сопряжения проушин и в зоне болтов крепления щек наконечника к лонжерону, которые не допускаются. Фретинг-коррозия в местах сочленении комлевых наконечников с втулкой несущего винта характеризуется бурым налетом и является результатом трения сочлененных деталей. Ослабление и проворачивание болтов крепления комлевых наконечников к лонжерону, а также нарушение контровки не допускаются. Задние кромки хвостовых отсеков лопастей не должны иметь искривления со стрелой прогиба более 5 мм. На концевых обтекателях лопастей не допускаются трещины, пробоины, вмятины глубиной более 2 мм и ослабление винтов крепления обтекателей. При выполнении регламентных работ проверяют исправность системы сигнализации повреждения лонжеронов лопастей несущего винта. Проверку рекомендуется выполнять в тени для соответствия температуры воздухом лонжероне и наружного воздуха. Для проверки отворачивают колпачок и манометром (рис.6.8.)
Рис. 6.8. Замер давления воздуха в лонжероне лопасти.
1- манометр; 2- наконечник манометра; 3- колпачок;4- сигнализатор давления воздуха; 5- зарядный вентиль
замеряют давление воздуха в полости лонжерона лопасти. При этом красный поясок сигнализатора не должен быть в поле зрения. Нажатием на стержень золотника стравливается давление воздуха из лонжерона до начала появления красного пояска сигнализатора, после чего давление начала срабатывания сигнализатора замеряют манометром. Затем с помощью ручного насоса РН-6С в лонжероне создается давление на 0,15 кгс/см2 , превышающее давление начала срабатывания, из расчета 60...70 качков повышают давление на 0,1 кгс/см2. Затем проверяют герметичность золотника мыльным раствором, и колпачок устанавливают на место. Аналогичным образом проверяют сигнализаторы других лопастей. При выполнении этой работы следует учитывать, что накачивание воздуха в лонжерон до давления более 0,8 кгс/см2 не допускается, а при температуре ниже -40° С давление в лонжеронах должно выдерживаться не ниже 0,25 кгс/см2, так как в случае повреждения лонжерона вблизи комля стравливание давления будет незначительным ввиду отсоса воздуха к концу лонжерона центробежными силами.
Наиболее качественный контроль состояния лопастей возможен при их демонтаже. В этом случае тщательно проверяют лонжерон лопасти на отсутствие трещин, забоин, рисок, царапин и коррозии. Трещины лонжерона не допускаются. При наличии рисок и царапин поврежденный участок осматривают с помощью лупы, а глубину дефекта определяют индикатором. Риски, забоины и царапины, не выходящие за пределы технических требований, выводят шабером и шкуркой с последующей полировкой участка пастой ГОИ вдоль оси лонжерона. Дефект устраняют лишь в том случае, если на участке на 50 мм в обе стороны от дефекта на той же поверхности лонжерона и на 100 мм в обе стороны на противоположной поверхности лонжерона нет следов устранения подобных дефектов, выполненных ранее. Глубина зачистки после выведения дефекта зависит от зоны на лонжероне и не должна превышать 0,2 мм.
При осмотре лопастей проверяют отсутствие коррозии на лонжероне и состояние герметизации между хвостовыми отсеками. Коррозионные поражения лонжерона в местах нарушения лакокрасочного покрытия контролируют с помощью лупы семикратного увеличения. Повреждения, наблюдаемые с помощью лупы, выглядят в виде темны пятен, имеющих неровные ломаные очертания с ответвлениями. В местах их обнаружения производят местную размывку лакокрасочного покрытия. Места с подозрением на коррозию дополнительно протирают чернильной резинкой. Если после этого размер и конфигурация черного пятна сохраняются, то это указывает на коррозию Обычное механическое повреждение при обработке резинкой имеет светлое дно. Коррозионные повреждения лонжерона без видимого повреждение лакокрасочного покрытия при осмотре через лупу выглядят в виде мелких вздутий краски, а в ряде случаев с выходом продуктов коррозии на окрашенную поверхность в виде мелких белых пятен. В местах обнаружения вздутий лакокрасочного покрытия выполняют местную размывку краски и тщательную проверку. Эксплуатация лопастей с коррозией на лонжероне не допускается.
При проверке состояния герметизации между отсеками необходимо обращать внимание на растрескивание и выкрашивание герметика, восстановление которого возможно в эксплуатационных условиях.
Качество клеевых соединений проверяют приборами ИАД-1 или ИАД-2, а в их отсутствие - простукиванием пластмассовым молоточком. Нарушение склейки обшивки хвостовых отсеков с лонжероном проверяют вдоль всей лопасти на ширине 33 мм. Допустимые дефекты приклейки хвостовых отсеков не должны превышать 18 см2 с каждого края отсека на обеих поверхностях. Одновременные нарушения приклейки обшивки по краям и в средней части отсека не допускаются. Нарушения приклейки обшивки хвостового отсека с сотовым заполнителем с каждого края отсека не должны превышать 100 см2 со стороны каждой нервюры с отставанием обшивки от полок нервюры на длине не более 50 мм, а в средней части отсека - площадью не более 350 см2. Если нарушение приклейки обшивки хвостового отсека с сотовым заполнителем превышает по площади 280 см2 на каждой стороне отсека или нарушения приклейки обшивки, выходящие на торцы отсека по площади более 80 см2 одновременно более чем на трех отсеках лопасти, то состояние клеевого соединения с помощью прибора или простукиванием проверяют после каждого летного дня.
Простукиванием молоточком проверяют также вспучивание и отставание нагревательной накладки противообледенительного устройства лопасти. Допускается отставание накладки от лонжерона лопасти общей площадью 100 см2. При этом одиночные нарушения склейки могут быть не более 180 см2 .
При техническом обслуживании втулки несущего винта особое внимание уделяется наличию и своевременности заправки масел и смазки в шарниры втулки и в компенсационный бачок. Уровень масла в шарнирах проверяют по масломерам. Для этого выворачивают заливные пробки шарниров и определяют уровень масла, который должен быть: в горизонтальном шарнире 30...40 мм (при наличии компенсатора давления 30...35 мм), в вертикальном 25...35 мм (с компенсатором давления 30...35 мм) и в осевом шарнире 15...20 мм (с компенсатором давления до внутреннего торца отверстия).
Дозаправку шарниров маслом производят через резьбовые отверстия с помощью воронки с фильтрующей сеткой, размер ячейки которой 63 мкм. Не следует заливать масло в шарниры до уровня, превышающего рекомендованный, так как переполнение маслом является одной из причин появления течи. В случае замены масла в горизонтальных и осевых шарнирах требуется подогреть шарниры аэродромным подогревателем до теплого их состояния, подставить емкости под сливные отверстия и вывернуть сливные и заливные пробки. Слив масла ведут до полного прекращения течи масла из сливных отверстий, после чего сливные пробки заворачивают. Заливают масло через воронку с сеткой согласно предусмотренному уровню. Из осевых шарниров сливают по 200...300 см3 в чистую стеклянную емкость для контроля на отсутствие воды в масле. После окончания работы сливные и заливные пробки следует надежно затянуть и законтрить.При замене масла в вертикальных шарнирах следует вывернуть пробки заливных отверстий в крышках пальцев и с помощью шприца с наконечником удалить старое масло из полости стакана вертикального шарнира. Заправить через воронку с сеткой свежее масло, завернуть пробки и дополнительно зашприцевать через масленку в днище стакана до его появления без пузырьков воздуха из перепускного клапана в упоре цапфы. После этого требуется проконтролировать уровень масла в шарнире.
Дозаправка компенсационного бачка маслом АМГ-10 возможна при демонтаже токосъемника. При этом заливку ведут через заправочную горловину бачка с помощью воронки с фильтрующей сеткой до уровня риски на бачке.
Набивка смазки ЦИАТИМ-201 в шарнирные соединения гидродемпферов, центробежных ограничителей свеса и рычагов поворота лопастей осуществляется через масленки посредством рычажно-плунжерного шприца
Техническое обслуживание рулевого винта так же, как и несущего, предусматривает сохранение защитных покрытий втулки и лопастей, их целостность и надежность крепления, сохранение шарнирных моментов в сочленениях втулки, своевременное выявление дефектов и их устранение. Лед, снег, иней с поверхности лопастей удаляются теплым воздухом от наземного подогревателя с температурой не выше 60° С с последующей протиркой поверхности насухо.
На рулевом винте контролируют: отсутствие механических повреждений, надежность контровки разъемных соединений, работу шарниров винта, состояние лопастей. При обнаружении трещин втулку рулевого винта следует заменить. Забоины, риски и царапины глубиной до 0,2 мм зачищаются шкуркой, заполировываются и покрываются бесцветным лаком. При выбивании смазки из-под пробок шарниров винта пробки подтягивают или на них заменяют уплотнительные прокладки. Поверхностные забоины, риски и коррозионный налет без образования раковин на проушинах лопасти выводятся наждачной шкуркой с последующей полировкой пастой ГОИ и покрытием грунтом. На лакокрасочном покрытии материала обшивки лопастей допускаются потертости и царапины без повреждения стеклоткани с последующей зачисткой, грунтовкой и покраской.
Контроль качества приклейки обшивки к сотовому заполнителю, лонжерону, стрингеру и нервюре лопасти, а также противообледенительного устройства лопасти к лонжерону производится простукиванием молоточком и на ощупь, не снимая лопасти с втулки. Участок шириной 30 мм от хвостового стрингера проверке простукиванием не подлежит. Допускаются к эксплуатации лопасти рулевого винта при нарушении склейки обшивки хвостового отсека с лонжероном, не выходящие на край отсека, общей площадью не более 16 см2 при одиночном нарушении склейки не более 4 см2. Нарушение склейки обшивки с сотовым заполнением не должно превышать по общей площади 30 см2 с каждой стороны отсека при одиночном нарушении склейки не более 5 см2. В том и другом случаях расстояние между двумя соседними нарушениями должно быть не менее 50 мм.
Вмятины на хвостовой части лопасти допускаются глубиной до 0,5 мм при наличии их не более трех и до 0,8 мм не более одной. Стрела прогиба хвостового стрингера может быть не более 3 мм.
На законцовках допускаются плавные вмятины глубиной до 0,8 мм и царапины до 0,4 мм при длине не более 25 мм. При контроле противообледенительного устройства лопасти не допускаются непроклеи между нагревательной накладкой и лонжероном, а также вспучивание резины.
Техническое обслуживание втулки винта предусматривает периодический замер зазора валиков и вилок рычагов поворота лопастей винта. При этом проверяются зазор валика рычага в плоскости тяги и в плоскости вращения винта, а также осевой зазор вилки тяги относительно валика рычага. В первом случае лопасти винта устанавливают на максимальный угол (правая педаль вперед до упора). На бачок визуального контроля масла в осевом шарнире закреплено специальное приспособление (рис.6.9.),
Рис. 6.9. Установка приспособления для замера люфта валиков и вилок рычагов поворота лопастей рулевого винта:
фиксированное винтом 6 на пробке бачка. Ножка 5 индикатора приспособления с натягом 0,6 мм подведена к сферической поверхности (точка А) валика поворота лопасти и затянута винтами 1, 2, 4. Угол между плоскостью замера и ножкой индикатора должен быть не более 10°. Поворотом шкалы стрелку индикатора устанавливают на "0". Прикладывая к корпусу осевого шарнира усилие по часовой и против часовой стрелки, фиксируют крайние положения стрелки индикатора. По сумме показаний индикатора определяют зазор валика, который не должен превышать 0,45 мм. Во втором случае аналогичным образом ножку индикатора приспособления с натягом 0,6 мм подводят к щеке (точка Б) валика поворота лопасти, после чего стрелку индикатора также устанавливают на 0. Покачивая валик в плоскости вращения винта к индикатору и от него, фиксируют крайние положения стрелки, суммарная величина показаний которой не должна превышать 0,45 мм. После этого проверяют зазор валиков рычагов в плоскости тяги и в плоскости вращения винта двух других лопастей. В обоих случаях при обнаружении зазора, равного 0,43 мм, решается целесообразность дальнейшей эксплуатации втулки рулевого винта.
Проверку осевого зазора вилки тяги относительно валика рычага поворота лопасти ведут тем же приспособлением. Для проверки следует, перемещая индикатор в скобе 7 и кронштейне 3, установить ножку 5 индикатора на плоскость поверхности (точка В) вилки с натягом 0,6 мм. После затяжки винтов 1, 2, 4 поставить стрелку индикатора на "0" и, покачивая вилку в плоскости вращения винта к индикатору и от него с максимальным усилием, зафиксировать крайние положения стрелки индикатора. Зазор вилки определяют путем вычитания из суммарных показаний стрелки индикатора зазора валика рычага в плоскости вращения винта. Полученная величина является зазором вилки и не должна превышать 0,2 мм. Аналогично проверяют осевой зазор вилок тяг двух других осевых шарниров. Вопрос о целесообразности дальнейшей эксплуатации втулки решается при наличии зазора 0,18 мм.
Двухрядный шариковый подшипник, обеспечивающий независимость возвратно-поступательного движения штока от вращательного движения поводка втулки винта, является высоконагруженным конструктивным элементом. Поэтому при выполнении обслуживания втулки рулевого винта замеряют осевой зазор этого подшипника. Для выполнения работы следует расконтрить и отвернуть крышку ползуна и вынуть шплинт гайки штока редуктора. В резьбовую расточку ползуна завернуть крышку 5 (рис.6.9.) приспособления с моментом затяжки 4 кгс·м. На шестигранник крышки установить приспособление 2 и закрепить его винтами 4, а в расточку приспособления поставить индикатор и, создав натяг 0,4...0,5 мм, закрепить его винтом 3. После установки индикатора переместить его ножку 1 в сторону, противоположную индикатору, и стрелку индикатора поставить в положение 0. Переместить педали ножного управления вправо, а затем влево и зафиксировать при этом показания индикатора, сумма которых и образует величину зазора, который не должен превышать 0,08 мм.
Рис. 6.10. Установка приспособления для замера осевого люфта подшипника штока рулевого винта:
При зазоре 0,06 мм требуются дополнительное внимание и решение вопроса о дальнейшей эксплуатации винта. После проверки следует демонтировать приспособление, установить шплинт гайки штока и затянуть крышку ползуна с моментом (8 + 2) кгс·м, законтрить ее и зашприцевать в полость подшипника смазку ЦИАТИМ-201.
При проверке момента затяжки гаек крепления втулки рулевого винта к фланцу хвостового редуктора пользуются тарировочным ключом. Затяжку гаек ведут перекрестным чередованием с моментом 6...10 кгс·м.
Для контроля уровня масла каждую из лопастей устанавливают вертикально вниз и по контрольным стаканчикам проверяют уровень масла в осевом шарнире, который должен быть не ниже контрольной риски, нанесенной на стакане, и не выше 15 мм от его верхнего края. В случае необходимости дозаправляют или заменяют масло в осевых шарнирах. При дозаправке лопасть устанавливают в заднее горизонтальное положение, и левую педаль перемещают вперед с целью выдвижения штока с ползуном. На корпусе осевого шарнира и контрольном стаканчике выворачивают пробки 1 (рис.6.11.) и 4 и в отверстие корпуса устанавливают приспособление, из баллона 2 которого производят дозаправку шарнира маслом. После этого лопасть поворачивают на 15...20° вверх, приспособление переставляют в отверстие стаканчика и масло доливают до его верхнего уровня. При замене масла в осевом шарнире лопасть устанавливают на 10...15° выше горизонтального положения в направлении к фюзеляжу. На корпусе осевого шарнира подвешивают емкость и выворачивают пробки 1 и 4, обеспечивающие слив масла из шарнира. Для заправки шарнира лопасть устанавливают в горизонтальное положение. При этом валик рычага поворота лопасти должен находиться в верхнем положении.
Рис. 6.11. Заправка масла в осевой шарнир внутри рулевого винта:
Установить заправленный чистым маслом баллон 2 приспособления в резьбовое отверстие корпуса шарнира, предварительно сняв с него колпачок 3 вентиляционной трубки. Отвернуть пробку бачка с целью суфлирования полости шарнира и заправить шарнир маслом путем полного слива последнего из баллона приспособления. Для ускорения заправки шарнира масло сжимают стенки полиэтиленового баллона приспособления с одновременным закрытием его вентиляционной трубки. После полной заправки шарнира маслом по контрольным стаканчикам бачка проверяют уровень масла. Аналогичным путем заменяют масло в других осевых шарнирах. Карданный шарнир, подшипники штока, поводка и валиков осевых шарниров, а также шлицы ползуна смазывают смазкой ЦИАТИМ-201 путем зашприцовки ее рычажно-плунжерным шприцом через пресс-масленки узлов втулки.
При оперативном обслуживании согласно видам подготовки по регламенту необходимо:
-осмотреть втулки несущего и рулевого винтов, их шарниры на отсутствие трещин, коррозии, нарушения целостности контровки, герметичности шарниров;
-проверить уровень масла в компенсационном бачке гидродемпферов вертикальных шарниров втулки НВ, внешнее состояние шлангов к гидродемпферам;
-проконтролировать качество масла в осевых шарнирах втулки НВ по контрольным стаканчикам;
-проверить центробежные ограничители свеса лопастей НВ на отсутствие наклепа и выработки на упорах собачки и скобы;
-убедиться в целости контровки и надежности крепления рычагов поворота лопасти на корпусах осевых шарниров втулки НВ;
-проверить герметичность уплотнений общего горизонтального шарнира (кардана), осевых шарниров, узлов рычагов поворота лопастей и двухрядного шарикового подшипника штока, а также целостность контровки всех деталей крепления втулки рулевого винта;
-проконтролировать уровень и качество масла в осевых шарнирах втулки рулевого винта по их контрольным стаканчикам;
-проверить работу шарниров втулки рулевого винта;
-осмотреть состояние лонжеронов, хвостовых отсеков, комлевых наконечников, концевых обтекателей лопастей несущего и рулевого винтов на предмет отсутствия механических повреждений, трещин, вспучивания, отставания, износа обшивки, оковок, резиновых накладок;
-визуально проконтролировать наличие давления воздуха в лонжеронах лопастей по сигнализаторам давления.
При периодическом обслуживании согласно периодичности, указанной в регламенте, выполняются следующие работы:
снятие и контроль магнитных пробок в осевых шарнирах втулки несущего винта;
проверка моментов затяжки гайки крепления втулки НВ на валу НВ главного редуктора, а также болтов крепления рычагов поворота лопастей и гаек болтов крепления гидродемпферов к цапфам осевых шарниров;
снятие лопастей НВ с последующей установкой и проверка качества приклейки обшивки прибором ИАД-2 или методом простукивания;
проверка момента затяжки гаек болтов крепления втулки рулевого винта к ведомому валу хвостового редуктора, лопастей к корпусам осевых шарниров;
замер осевого люфта двухрядного шарикового подшипника штока механизма изменения шага рулевого винта, люфта рычагов и вилок тяг поворота лопастей;
визуальный осмотр лопастей рулевого винта, проверка на ощупь и простукиванием состояния приклейки обшивки хвостовых отсеков, резиновых накладок и оковок как при снятых, так и неснятых лопастях.
Снятие, осмотр магнитных пробок и проверка состояния масла в ОШ втулки НВ осуществляется в следующем порядке.
Установить лопасть НВ, с ОШ которой будет сливаться масло, вдоль хвостовой балки. Слить 200...300 см масла в стеклянную емкость через отверстие магнитной пробки. После слива масла в отверстие под магнитную пробку установить технологическую заглушку из ЗИПа втулки.
При осмотре магнитной пробки нужно убедиться, что отсутствуют чешуйчатые и иглообразные металлические частицы размером более 0,5 мм. В противном случае втулку НВ снять с эксплуатации и вызвать представителя завода - поставщика. Если на магнитной пробке обнаружена металлическая пыль, то заменить масло в шарнире на свежее, прокрутить несущий винт в течение 30 мин на частоте вращения, соответствующей крейсерскому режиму. При повторном обнаружении металлической пыли необходимо снять втулку с эксплуатации и вызвать представителя завода-поставщика. При эксплуатации вертолета на оперативных точках разрешается перелет продолжительностью до 2 ч на базовый аэродром.
Проверку состояния масла в осевых шарнирах втулки рулевого винта производят в следующем порядке. Предварительно лопасти рулевого винта поочередно устанавливают вертикально вверх и через 5 мин осматривают масло в контрольном стаканчике - масло должно быть прозрачным (видна противоположная стенка стаканчика).
При помутнении масла и наличии видимых металлических частиц сливают масло из шарнира в чистую емкость, разжижают двумя частями по объему чистого бензина, профильтровывают, высушивают остаток на фильтровальной бумаге и с помощью магнита убеждаются в отсутствии стальной стружки.
В случае обнаружения стальной стружки рулевой винт снимают с эксплуатации. Разрешается эксплуатация винта при наличии в масле частиц кадмия, бронзы.
Предупреждение.
Допустимо помутнение масла при замене масла МС-20 на ВНИИ НП-25.При проверке качества масла при температуре наружного воздуха ниже +5 °С подогреть втулку РВ теплым воздухом (30-40 °С) от подогревателя
6.4 КОНТРОЛЬНЫЕ ВОПРОСЫ И ЗАДАНИЯ.
1. Для чего предназначены горизонтальный, вертикальный и осевой шарниры втулки несущего винта?
2. Из каких основных узлов состоит втулка несущего винта?
3. Как обеспечивается центрирование втулки несущего винта и передача нагрузок от втулки к валу главного редуктора?
4. Почему углы свеса лопастей в полете и на стоянке различны?
5. Из каких основных узлов состоит лопасть несущего винта?
6. С какой целью к лонжерону лопасти несущего винта крепятся противовесы, балансиры?
7. Почему между хвостовыми отсеками лопасти несущего винта установлены уплотнительные вкладыши?
8. Назначение, состав и работа сигнализатора давления воздуха?
9. Как проконтролировать давление воздуха в лонжероне лопасти несущего винта, от чего будет зависеть эта величина, что необходимо предпринять, если давление не будет соответствовать требуемой величине?
10. Для чего предназначен кардан втулки рулевого винта?
11. Из каких основных узлов состоит втулка рулевого винта?
12. Как контролируется количество масла, находящегося в осевом шарнире втулки рулевого винта?
13. Какие детали втулки рулевого винта обеспечивают изменение шага рулевого винта?
14. Из каких основных узлов состоит лопасть несущего винта?
7 СИСТЕМА УПРАВЛЕНИЯ ВЕРТОЛЕТОМ
В систему управления вертолетом входят: продольно-поперечное управление; путевое управление; объединенное управление; управление перенастройкой частоты вращения несущего винта; раздельное управление двигателями; управление остановом двигателей; управление тормозом несущего винта.
7.1. ОБЩИЕ СВЕДЕНИЯ
Управление вертолетом, т.е. изменение его балансировочного положения относительно трех пространственных осей, производится путем изменения величины и направления силы тяги несущего винта, а также силы тяги рулевого винта.
Управление силами тяги несущего и рулевого винтов осуществляется с помощью системы управления вертолетом, которая включает отдельные самостоятельные цепи продольного, поперечного, путевого управления и вертикального перемещения.
Продольное и поперечное управление достигается отклонением ручки циклического шага, которое приводит к наклону тарелки автомата перекоса, изменению циклического шага и завалу оси конуса несущего винта в сторону отклонения ручки. В результате этого отклоняется вектор силы тяги несущего винта, а также возникает момент, под действием которого вертолет поворачивает вокруг продольной или поперечной оси, изменяя угол крена или тангажа.
Путевое управление осуществляется отклонением педалей. При этом изменяется шаг, а следовательно, и сила тяги рулевого винта. Это в свою очередь вызывает изменение момента относительно вертикальной оси вертолета и изменение азимутального положения вертолета.
Для вертикального перемещения вертолета необходимо изменить вертикальную составляющую, что достигается изменением общего шага несущего винта. Изменение тяги несущего винта по величине производится при помощи ручки объединенного управления „шаг-газ" путем одновременного изменения общего шага несущего винта и режима работы двигателей. Наряду с объединенным управлением двигателя с помощью ручки „шаг-газ" на вертолете имеются рычаги раздельного управления двигателями.Рычаги позволяют производить раздельное опробование двигателей без изменения общего шага несущего винта.
Для снятия нагрузок с органов управления во всех системах установлены гидроусилители. В продольном, поперечном управлениях и в управлении общим шагом несущего винта установлены . гидроусилители типа КАУ-30Б, а в путевом управлении -гидроусилитель типа РА-60Б, которые одновременно являются рулевыми приводами в автопилоте АП-34Б.
Для создания необходимого градиента усилий на ручке и педалях управления, а также для снятия с них усилий при установившемся режиме полета вертолета в системах продольного, поперечного и путевого управлений установлены пружинные механизмы загрузки с электромагнитными тормозами ЭМТ-2М.
7.2 АВТОМАТ ПЕРЕКОСА
Автомат перекоса предназначен для изменения величины и направления тяги несущего винта.
Автомат перекоса (рис. 7.1) состоит из направляющей ползуна, ползуна,кронштейна, внутреннего и наружного колец кардана, тарелки, тяг поворота лопастей, качалок продольного и поперечного управлений, рычага общего шага и поводка тарелки.
Направляющая ползуна крепится к верхнему корпусу редуктора. Снаружи по двум хромированным ее поверхностям перемещается ползун. Внутри него заделаны две бронзовые втулки для скольжения по направляющей. На наружной поверхности ползуна имеется фланец, к которому на шпильках крепится кронштейн.
В верхней части ползуна расточены два диаметрально расположенных отверстия, в которых установлены радиальные шарикоподшипники и пальцы, при помощи которых с ползуном шарнирно соединяется внутреннее кольцо кардана. Для защиты трущихся поверхностей от грязи и удержания смазки в канавках ползуна установлены резиновые манжеты.
Внутреннее кольцо кардана имеет четыре диаметрально противоположных отверстия для установки пальцев. К нему с помощью второй пары пальцев и радиальных подшипников шарнирно крепится наружное кольцо кардана.
Наружное кольцо кардана - переменного сечения. На ним под углом 90° Друг к другу закреплены два консольных пальца, к которым крепятся через сферические подшипники тяги продольного и поперечного управлений.
Пальцы расположены таким образом, что точки присоединения тяг продольного и поперечного управлений к наружному кольцу кардана оказываются смещенными с продольной и поперечной осей вертолета на 2о против направления вращения несущего винта. Вследствие чего расположения пальцев достигался опережение продольного и поперечного управлений, необходимого для соответствия наклона оси конуса вращения несущего винта с отклонением ручки продольно-поперечного управления.
На цилиндрической поверхности наружного кольца кардана на двухрядном шариковом подшипнике установлена тарелка. Наружное кольцо подшипника прижато фланцем к внутреннему буртику обоймы, запрессованной в тарелку; уплотнение полости подшипника осуществляется двумя резиновыми манжетами.
Тарелка автомата перекоса отштампована из алюминиевого сплава, имеет пять лап, расположенных под углом 72° друг к другу. На концах лап имеются цилиндрические расточки, в которые запрессованы стаканы для монтажа на игольчатом и двухрядном шариковом подшипниках шарнирных валиков. Валики соединяются пальцами с тягами поворота лопастей через два шариковых подшипника.
Тарелка приводится во вращение поводком, представляющим собой кинематическое звено, состоящее из кронштейна, серьги и рычага, шарнирно связанных между собой. Наличие на поводке пяти шарниров обеспечивает вращение тарелки при любых ее наклонах и поступательном перемещении вместе с ползуном по направляющей.
Кронштейн поводка, состоящий из двух половин, смонтирован в нижней части корпуса втулки несущего винта и зафиксирован двумя стяжными болтами и штифтом. К кронштейну с помощью оси и двух шариковых подшипников закреплена серьга. Аналогично выполнено и соединение серьги с рычагом.
Рычаг поводка состоит из корпуса, вилки и валика. Вилка на игольчатом и шариковом подшипниках монтируется в цилиндрической расточке корпуса рычага, а посредством пальца и игольчатого подшипника шарнирно связана с валиком рычага. Валик рычага смонтирован на двух радиально-упорных шариковых подшипниках в корпусе, который закреплен к одной из лап тарелки.
Тяга поворота лопасти состоит из стержня и двух вилок. В расточке нижней вилки на двухрядном шариковом подшипнике смонтирован осевой шарнир тяги. Верхняя вилка навернута на резьбовой носок стержня тяги и имеет разрез, позволяющий регулировать длину тяги и надежно фиксировать верхнюю вилку относительно стержня стяжным болтом. Кронштейн изготовлен из алюминиевого сплава и закреплен шпильками на фланце ползуна. Он имеет приливы с расточками, в которые запрессованы и зафиксированы стальные втулки для монтажа узлов качалок продольного и поперечного управлений. В средней части кронштейна выполнены две диаметрально противоположные расточки для шарнирного подсоединения рычага общего шага.
Качалки продольного и поперечного управлений обеспечивают изменения положения (наклон) тарелки автомата перекоса. Качалка продольного управления состоит из стального валика, к которому с внутренней стороны с помощью торцовых шлиц и винта закреплен рычаг, а с наружной стороны на шлицах установлена и зафиксирована вилка. Валик смонтирован на двух игольчатых подшипниках. Рычаг качалки посредством шарикового подшипника и пальца соединяется с тягой автомата перекоса, а вилка - с тягой от гидроусилителя. На торце втулки качалки винтами закреплена пластина с нониусом, а на шлицах валика - диск со шкалой.
Рис. 7.1 Автомат перекоса.
1— качалка поперечного управления; 2— тяга; 3 — внутреннее кольцо кардана; 4,30— валик; 5— тарелка автомата перекоса; 6 — тяга поворота лопасти; 7 — подшипник; 8 — фланец; 9— кронштейн поводка; 10— серьга; 11 — рычаг; 12 — направляющая ползуна;13— наружноекольцо кардана;14 — ползун; 15 — кронштейн; 16— рычаг общего шага; 17 — кронштейн; 18 — бронзовая втулка; 19 — пластина с нониусом; 20 — диск со шкалой; 21 — качалка продольного управления; 23 — крышка подшипникового узла; 22,24,25,26,28— палец; 27— серьга; 29 — основание кронштейна; 31 — рычаг
Качалка поперечного управления выполнена за одно во втулке кронштейна на двух конических роликовых подшипниках. целое с
вилкой и рычагом и смонтирована на стальной оси, закрепленной Шкала качалки поперечного управления соединена с диском, закрепленным на кронштейне; деления нониуса нанесены на ступицу качалки. Шкалы и нониусы качалок позволяют контролировать наклон тарелки автомата перекоса в продольном и поперечном направлениях с точностью до 6 и дают возможность производить регулировку управления.
Рычаг общего шага, в проушинах которого установлены шариковые подшипники, соединяется с кронштейном ползуна посредством пальцев. В середине щек рычага общего шага имеются гнезда с установленными в них коническими роликовыми подшипниками, являющимися опорами цапф серьги. Другим концом серьга с помощью пропущенного через ее нижнюю расточку пальца соединяется с основанием кронштейна, имеющим аналогичные гнезда с коническими роликовыми подшипниками. Основание болтами закреплено на картере главного редуктора.
7.3. ПРОВОДКА УПРАВЛЕНИЯ
Проводка управления вертолетом и двигателями - смешанной конструкции (рис. 7.2). Жесткая проводка проложена от рычагов управления вертолетом до автомата перекоса и насоса НР-ЗВМ. Тросовая проводка применена в управлении тормозом несущего винта, остановом двигателей и в управлении рулевым винтом на участке от гидроусилителя РА-60Б до хвостового редуктора.
Колонки продольно-поперечного и педали путевого управления кинематически связаны между собой тягами и качалками, проложенными под полом кабины экипажа. Рычаги „шаг-газ" связаны между собой замыкающим валом, от которого проложена раздельная проводка к автомату перекоса и насосу-регулятору. Рычаги раздельного управления включены в проводку управления двигателей при помощи дифференциального узла.
От рычагов управления вертолетом и двигателями проложены тяги под полом кабины экипажа. Они соединяются с нижними угловыми качалками, установленными на общем кронштейне в нижней части шпангоута № 5Н со стороны центральной части фюзеляжа.
От нижних угловых качалок тяги проложены по стенке шпангоута № 5Н и соединяются с верхними угловыми качалками, установленными на общем кронштейне. Между нижними и верхними угловыми качалками тяги состоят из двух звеньев, шарнирно соединенных с промежуточными качалками с целью создания необходимой жесткости проводки управления на вертикальном участке.
От верхних угловых качалок тяги управления двигателями соединяются с рычагами блока валов, а тяги продольного, поперечного, путевого управлений и управления общим шагом проложены с нижней стороны потолочной панели и соединяются с нижними рычагами агрегата продольного, поперечного, путевого управлений и управления общим шагом.
Рис. 7.2. Кинематическая схема управления вертолетом:
1 — рычаги останова двигателей; 2, 16 — тросы; 3, 4, 17, 18, 19, 20 — тяги; 5— рычаг общего шага автомата перекоса; 6, 7, 8, 15—гидроусилители; 9 — направляющие ролики; 10 — звездочка механизма изменения шага рулевого винта; 11— втулочно-роликовая цепь; 12 — кронштейн; 13 — тросовая проводка управления рулевым винтом; 14 — агрегат управления; 21, 22, 23 — пружинные механизмы загрузки; 24 — электромагнитные тормоза ЭМТ-2М; 25— рычаги раздельного управления двигателями; 26 — ручка управления тормозом несущеговинта; 27 — ручка ШАГ—ГАЗ; 28 — ручка продольно-поперечного управления; 29 — педали
Агрегат управления установлен с верхней стороны панели у шпангоута № 10 центральной части фюзеляжа. Тяги, расположенные между верхними угловыми качалками и рычагами агрегата управления, состоят из трех звеньев, шарнирно соединенных между собой. Средние звенья тяг закреплены в роликовых направляющих, установленных на шпангоутах № 4 и 6 центральной части фюзеляжа. Верхние рычаги агрегата управления соединяются вертикальными тягами с качалками соответствующих гидроусилителей. Соединение агрегата управления с гидроусилителем путевого управления производится через механизм подвижного упора управления СПУУ-52.
Гидроусилители продольного и поперечного управлений тягами и качалками кинематически соединены с автоматом перекоса. Гидроусилитель путевого управления соединен с рычагом сектора, от которого проложена тросовая проводка к механизму изменения шага рулевого винта. Гидроусилитель общего шага звеном соединен с рычагом общего шага автомата перекоса.
В проводку продольного, поперечного и путевого управлений установлены загрузочные механизмы с электромагнитными тормозами ЭМТ-2М.. Загрузочные механизмы установлены на шпангоуте № 5Н со стороны центральной части фюзеляжа и параллельно подключены к каждой проводке в районе средних передаточных качалок. Цилиндры загрузочных механизмов соединены с промежуточными качалками, а штоки -с рычагами электромагнитных тормозов ЭМТ-2М.
Поперечные тяги, соединяющие ручки и педали управления, а также тяги продольного и поперечного управлений после гидроусилителей, выполнены из хромансилевых труб, остальные - из дюралюминиевых. На концах труб вклепаны стальные стаканы, в которые ввернуты ушковые или вильчатые наконечники для регулировки управления. В стаканах просверлены радиальные отверстия, которые должны быть всегда перекрыты резьбовой частью наконечника. Соединение тяг с качалками и между собой выполнено на сферических шарикоподшипниках, имеющих пресс-масленки для смазки. Крепление качалок в кронштейнах осуществлено на шариковых подшипниках.
Роликовые направляющие на шпангоутах № 4 и 6 состоят из кронштейна, в котором на валиках установлено 12 текстолитовых роликов (по 3 ролика для каждой тяги). Для регулировки зазора между тягой и роликами предусмотрена эксцентриковая ось, которая в отрегулированном положении стопорится винтом.
Рис. 7.3. Агрегат продольного, поперечного, путевого управлений и управления общим шагом:
1,3,5,7— валы; 2,4,6,8,11,12,13,14— рычаги;
Агрегат управления (рис. 7.3) состоит из кронштейна и четырех валов. Валы установлены по соосной схеме на двух шариковых подшипниковых опорах каждый, что обеспечивает независимое вращение их относительно друг друга. Каждый вал изготовлен из стальной трубы, по концам которой имеются шлицевые пояса для крепления рычагов и цапфы для монтажа в опорах. Полости опор набиты смазкой и закрыты крышками с сальниками для исключения попадания пыли в грязи к подшипникам. Кронштейн своим фланцем крепится к потолочной панели. Часть кронштейна со стороны нижних рычагов закрыта кожухом, так как последние выведены в грузовую кабину через люк на потолочной панели.
7.4. ПРОДОЛЬНО-ПОПЕРЕЧНОЕ УПРАВЛЕНИЕ
Продольно-поперечное управление (рис. 7.4) включает две колонки управления, проводку продольного и поперечного управлений.
Рис. 7.4. Схема продольно-поперечного управления:
1, 4—колонки продольно-поперечного управления; 2—тяга продольного управления; 3—тяга поперечного управления; 5— пружинные загрузочные механизмы; 6 — роликовые направляющие тяг; 7 — агрегат продольного, поперечного, путевого управлений и управления общим шагом; 8, 9 — гидроусилители продольного и поперечного управлений; 10 — кронштейн крепления гидроусилителей
Каждая колонка (рис. 7.5) состоит из ручки, корпуса, кронштейна, стакана, шарнирной тяги, качалок, установленных на оси.
Ручка управления изготовлена из изогнутой стальной трубы, к нижнему концу которой закреплен рычаг, а на верхнем конце установлена рукоятка из эбонита. На рукоятке смонтированы кнопки включения радио и СПУ, выключения автопилота, включения ЭМТ-2М. Электропроводы от кнопок проложены внутри трубы ручки и подсоединены к штепсельному разъему. На рукоятке левой ручки установлен рычаг торможения колес, для удержания которого в заторможенном положении предусмотрен фиксатор. В средней части рычага выполнена расточка для монтажа двух шариковых подшипников закрытого типа, обеспечивающих шарнирную навеску на корпусе.
Рис. 7.5. Колонка продольно-поперечного управления:
1— рычаг; 2— ручка управления вертолетом; 3— рычаг торможения колес; 4,5,6,7— кнопки;8— рукоятка; 9— корпус; 10— регулируемый винтовой упор; 11— кронштейн; 12— стакан; 13— шарнирная тяга; 14— ось; 15,16— качалки; 17— проушины
Болт крепления ручки является осью, относительно которой ручка управления может отклоняться в продольном направлении. В отверстие нижнего конца рычага запрессован шариковый подшипник для подсоединения к наконечнику шарнирной тяги продольного управления,
Корпус жестко закреплен к стакану, в его нижней части имеются две проушины для подсоединения тяг. К одной проушине крепится тяга, соединяющая левую ручку с правой, к другой - тяга проводки поперечного управления.Стакан установлен в расточке кронштейна на двух шариковых подшипниках. Шарнирная тяга изготовлена из стальной трубы, в задний ее конец ввернут резьбовой наконечник для регулировки длины тяги. В проушину наконечника запрессован шариковый подшипник для соединения тяги с качалкой продольного управления. В передний конец трубы на двухрядном шариковом подшипнике установлен вильчатый наконечник. Шарнирная тяга проходит внутри стакана, и ее ось совпадает с осью его вращения. Наличие шарниров в конструкции тяги исключает скручивание тяги при поперечном отклонении ручки управления. Кронштейн имеет фланец для крепления к балке пола кабины, расточку для монтажа стакана и расточку под ось качалок. Ось качалок установлена в кронштейне на двух шариковых подшипниках. В продольном направлении отклонение ручки управления ограничивается регулируемыми винтовыми упорами, один из которых расположен на корпусе, другой - на кронштейне. Отклонение ручки в поперечном направлении ограничивается торцам" выреза на фланце стакана и упором, установленным на кронштейне.
Тяги, соединяющие колонки управления, состоят из двух звеньев и связаны между собой через качалку. В целях исключения повреждения лопастей о хвостовую балку при посадке вертолета с большим углом кабрирования в проводку продольного управления установлен гидравлический упор, загружающий на земле ручку управления дополнительным усилием при отклонении ее за пределы, соответствующие положению наклона тарелки автомата перекоса назад на угол 2°± 12'.Гидравлический упор установлен на кронштейне, укрепленном на стенке шпангоута № 5Н, ниже верхней угловой качалки продольного управления, Которая имеет прилив с роликом. При включенном гидроупоре ролик упирается в упор и препятствует дальнейшему отклонению ручки назад. Включение гидроупора осуществляется автоматически концевыми выключателями, установленными на главных опорах шасси, при обжатии штоков камер низкого давления.
Для устранения низкочастотных колебаний проводки продольного управления на верхней угловой качалке и на качалке колонки установлены балансировочные грузы.
7.5. ПУТЕВОЕ УПРАВЛЕНИЕ
Путевое управление (рис. 7.6) состоит из двух педалей и проводки управления.
Проводка управления - смешанной конструкции; она включает в себя систему тяг и качалок, участок тросовой проводки с втулочно-роликовой цепью, систему подвижного упора управления СПУУ-52, гидроусилитель РА-60Б, механизм загрузки с электромагнитным тормозом ЭМТ-2М, агрегат управления, сектор и механизм изменения шага рулевого винта. Для повышения надежности управления тросовая проводка выполнена двойной. Изменение шага рулевого винта осуществляется отклонением педалей.
Рис. 7.6 Схема путевого управления:
1 — педали;. 2, 4, 8,10,12 — тяги; 3,5,9— качалки; 6 — пружинный механизм загрузки; 7 — электромагнитный тормоз ЭМТ-2М; 11 — агрегат управления; 13 — механизм подвижного упора управления СПУУ-52; 14 — гидроусилитель PA-60Б; 15 — сектор; 16,20 — направляющие ролики; 17, 19 — колодки; 18 — тросовая проводка; 21 — втулочно-роликовая цепь.
Рис. 7.7. Педали путевого управления:
1 — гашетка; 2 — подножка; 3 — угловой рычаг; 4 — основание; 5 — винтовой упор; 6 — кронштейн; 7 — выравнивающая тяга; 8 — регулировочный винт с маховиком.
При отклонении правой подножки педалей вперед шток механизма изменения шага рулевого винта выходит, обеспечивая тем самым увеличение шага лопастей рулевого винта и разворот вертолета вправо; при отклонении левой подножки педалей вперед происходит обратный процесс.
Педали (рис. 7.7) выполнены в виде отдельного агрегата, смонтированного на полу кабины экипажа. В комплект педалей входят основание, вал, кронштейн, два угловых рычага, две подножки, выравнивающие тяги, двуплечая качалка и регулировочный болт с маховиком.
Основание педалей закреплено к полу кабины экипажа, в вертикальную расточку основания на двух шариковых подшипниках установлен вал. В средней части вала укреплен кронштейн, на котором с помощью болтов и бронзовых втулок шарнирно крепятся угловые рычаги. На шлицевом хвостовике вала закреплена двуплечая качалка, соединенная тягами с педалями правого пилота и с проводкой управления рулевым винтом. На наружных плечах угловых рычагов посредством двух шариковых подшипников шарнирно установлены подножки. В расточках внутренних плеч рычагов размещены вкладыши с резьбовыми отверстиями под регулировочный болт с маховиком, позволяющий изменять расстояние между подножками в пределах 75 мм. На подножках смонтированы гашетки и концевые выключатели для переключения канала направления автопилота на режим согласования. Выравнивающие тяги обеспечивают параллельность хода подножек педалей.
Компоновка жесткой проводки от педалей до агрегата управления аналогична проводке продольного и поперечного управления. Кинематическая связь жесткой проводки с тросовой осуществляется с помощью сектора, который имеет две канавки для установки и фиксации концов тросов. В средней части на секторе выполнена проушина, к которой подсоединяется звено, связывающее сектор с двуплечей качалкой. Другой конец качалки соединен со штоком гидроусилителя РА-60Б. Противоположные концы тросов через серьги соединены с втулочно-роликовой цепью, которая перекинута через звездочку механизма изменения шага рулевого винта.
Тросовая проводка - двойная, проложена в текстолитовых направляющих колодках и трех парах направляющих роликов. В районе шпангоутов № 12...14 хвостовой балки с целью повышения живучести тросы каждой ветви перекинуты на двух ларах направляющих роликов.
Система подвижного упора управления СПУУ-52 обеспечивает автоматическое ограничение максимального угла установки лопастей рулевого винта в зависимости от плотности воздуха для предохранения рулевого винта и трансмиссии от перегрузок. В комплект СПУУ-52 входят: механизм подвижного упора, блок БУ-32, измерительный комплекс ИКД-27Д и приемник П-1. Механизм (рис. 7.8) подвижного упора включает в себя электромеханизм МП-100М, узел качалки с пружинным упором и микровыключателем, тягу с ограничительной муфтой, датчик обратной связи ДОС-6 с тендером и пружиной. Кронштейн механизма закреплен на передней стенке контейнера расходного топливного бака. На кронштейне шарнирно смонтирована качалка с пружинным упором, откидыванию последнего препятствует эксцентриковый винт, посредством которого регулируется зазор между регулировочным винтом и штоком микровыключателя при не прижатом упоре. Тяга механизма представляет собой трубу, в верхней части которой смонтирована муфта с гайкой, пружиной и втулкой. Электромеханизм соединен с проушиной кронштейна и плечом узла качалки и при выдвижении штока позволяет совершить угловое перемещение качалки для ограничения диапазона хода тяги.
Рис. 7.8. Механизм подвижного упора СПУУ-52:
1 -качалка; 2 - микровыключатель; 3 - регулировочный вит; 4 - втулка; 5, 12,15 - пружины; 6 - гайка; 7 - эксцентриковый винт; 8 - датчик обратной свели; 9 - кронштейн; 10 - тяга;
11 -электромеханизм МП-100М; 13 — тандер; 14 — упор.
При ро=760 мм рт. ст. и tо=+10оС шток электромеханизма полностью убран и пружинный упор не ограничивает угол установки лопастей рулевого винта - он составляет 23о +30'-15'. При полностью выдвинутом штоке качалка поворачивается и ее пружинный упор ограничивает перемещение тяги, а следовательно, и максимальный шаг винта до 20о±25'. Таким образом, повышение давления и понижение температуры ограничивает шаг РВ в пределах 80 % максимального его значения. Электромеханизм МП-100М срабатывает от сигнала системы СПУУ-52, управление которой производится с помощью АЗС СПУУ-52, выключателя и кнопки-табло „Откл.". Контроль за работой осуществляется по изменению положения подвижного индекса на блоке управления БУ-32. Крайнее левое положение подвижного индекса свидетельствует о том, что упор полностью убран и обеспечивается максимальный установочный угол; крайнее правое положение индекса сигнализирует об ограничении установочного угла лопастей рулевого винта.
7.6. ПРУЖИННЫЙ МЕХАНИЗМ ЗАГРУЗКИ И ЭЛЕКТРОМАГНИТНЫЙ ТОРМОЗ ЭМТ-2М
Все гидроусилители включены в проводку управлений по необратимой схеме, поэтому усилия с органов управления на командные рычаги не передаются. Для создания положительного градиента усилия на ручке управления и педалях в системах продольного, поперечного и путевого управлений установлены пружинные механизмы загрузки.
Механизм загрузки состоит из цилиндра, стакана, двух направляющих втулок, пружины, штока, резьбовых наконечников с подшипниками. Внутри стального цилиндра между двумя бронзовыми втулками расположена пружина, которая имеет предварительную затяжку, в результате чего снимается ощущение трения в системе управления и улучшается центрируемость ручки.
При перемещении ручки или педалей управления пружина в механизме сжимается и усилия передаются через тяги и качалки на ручку продольно-поперечного управления или педали. Чем больше диапазон отклонения органов управления, тем большее усилие воспринимается на ручке или педалях. При необходимости возможно снятие усилия с ручки управления и педалей нажатием кнопки, расположенной на ручке продольно-поперечного управления.При нажатии кнопки происходит растормаживание одновременно всех трех электромагнитных тормозов ЭМТ-2М, поводки которых связаны со штоками механизмов загрузки, и усилия с ручки управления и педалей снимаются мгновенно.
Рис. 7.9. Установка пружинных механизмов загрузки с электромагнитными тормозами:
1—пружинный механизм загрузки поперечного управления; 2—пружинный механизм загрузки путевого управления; 3 — пружинный механизм загрузки продольного управления; 4 — электромагнитные тормоза ЭМТ-2М; 5 — ушковый наконечник; 6 — стакан; 7 — направляющая втулка; 8 — цилиндр; 9 — шток; 10 — пружина
Электромагнитный тормоз ЭМТ-2М состоит из редуктора, электромагнитной муфты и центробежного тормоза. В корпусе электромагнитной муфты расположены катушка, нажимной диск со ступицей, три тормозных диска и пружина. Редуктор состоит из зубчатого сектора, двойного зубчатого колеса и блока зубчатых колес. Большое зубчатое колесо блока находится в зацеплении и приводит во вращение зубчатое колесо вала центробежного тормоза. Передаточное отношение редуктора от выводного вала к валу центробежного тормоза составляет 1:77,735.
Центробежный тормоз состоит из вала, стакана с подвижными грузами и фрикционного кольца. Стакан неподвижно закреплен на валу и имеет четыре радиальных колодца для установки подвижных грузов. Фрикционное кольцо запрессовано в корпус и закрыто крышкой. Тормозной диск шлицами связан с валом двойного зубчатого колеса и при обесточенной электромагнитной муфте прижат пружиной к тормозному диску закрепленному на корпусе редуктора. При движении ручки управления или педалей пружина в загрузочном механизме сжимается и усилие передаете на ручку или педали управления, а также на поводок, закрепленный на шлицах выводного вала электромагнитного тормоза.Для снятия усилий с ручки или педалей необходимо нажать на кнопку ручки, при этом включается электромагнитная муфта, и нажимной диск, притягиваясь к корпусу муфты, освобождает двойное зубчатое колесо. Сила сжатой пружины механизма загрузки отклоняет поводок на выводном валу тормоза. При этом механизм загрузки устанавливается в нейтральное положение и снимается усилие с ручки управления. При повороте поводка тормоза через зубчатые пары колес редуктора приводится во вращение стакан с подвижными грузами центробежного тормоза, которые, прижимаясь к неподвижному кольцу, замедляют вращение выводного вала, ликвидируя инерционность привода.
7.7. ОБЪЕДИНЕННОЕ УПРАВЛЕНИЕ
Объединенное управление (рис. 7.10) состоит из системы управления общим шагом несущего винта и системы управления двигателями. Общими в этом управлении являются ручки „шаг-газ" и соединенный с ними замыкающий вал, от которого идут проводки управления указанных систем.
В проводку управления общим шагом несущего винта входят тяги, угловые и промежуточные качалки, агрегат управления, гидроусилитель РАЗОВ и автомат перекоса.
В проводку управления двигателями входят дифференциальный узел, тяги, угловые и промежуточные качалки, блок валов. От блока валов тяги подсоединены к рычагам управления топливными насосами-регуляторами НР-ЗВМ.
Наряду с объединенным управлением „шаг-газ" предусмотрено раздельное управление двигателями, позволяющее изменять режим работы каждого двигателя без изменения общего шага несущего винта. Раздельное управление осуществляется рычагами, установленными на кронштейне левой ручки „шаг-газ". От рычагов раздельного управления двигателями движение передается через тяги на дифференциальный узел и далее через вышеуказанную проводку к рычагам топливных насосов.
Рис. 7.10. Схема объединенного управления:
1 — ручки „шаг—газ"; 2 — рычаги раздельного управления двигателями (РУД); 3,6, 7,10 — тяги управления двигателями; 4 — замыкающий вал; 5, 8, 11 — тяги управления общим шагом; 9 — дифференциальный узел; 12 — блок валов; 13 — агрегат управления; 14 — гидроусилитель КАУ-30Б; 15 — рычаг общего шага автомата перекоса.
Система управления „шаг-газ" является резервной системой регулирования частоты вращения несущего винта, так как система автоматического поддержания частоты его вращения предусмотрена на двигателях. Переход с системы автоматического поддержания частоты на систему управления „шаг-газ" и обратно осуществляется поворотом рукоятки коррекции. При правой коррекции работает система автоматического поддержания частоты вращения. При повороте рукоятки коррекции влево отключается систем автоматического регулирования частоты вращения и вступает в работу система управления „шаг-газ".
Левая ручка „шаг-газ" (рис. 7.11). состоит из корпуса, рукоятки коррекции, стопорного устройства, корпус кнопок, дискового фрикциона, ос кронштейна, кнопок и основания. Корпус ручки со срезанной по диаметру нижней частью закреплен к основанию шпильками. Основание двух шариковых подшипниках смонтировано на оси, которая установлена на кронштейне и зафиксирована болтом. На оси смонтирован фрикцион ручки, включающий в себя маховик, нажимную втулку, упорный диск, тарелку фрикциона, восемь пружин, подвижные фрикционные диски, укрепленные через внутренний барабан к основанию ручки и неподвижные фрикционные диски, укрепленные через наружный барабан к оси. Внутренняя полость оси является гидравлическим цилиндром управления фрикционом, в котором установлены плунжер и поршень.
Рис. 7.11. Левая ручка „шаг-газ":
1 — кронштейн; 2 — сектор; 3 — рычаги раздельного управления двигателями; 4 — кнопка фиксатора; 5 — корпус кнопок; 6 — рукоятка коррекции; 7 — стопорное устройство; 8 — корпус ручки; 9 — поршень; 10 - штуцер; 11 — основание ручки; 12 — ось; 13 — тарелка; 14 — упорный диск; 15 — нажимная втулка; 16 — маховик; 17 - диски фрикциона; 18- плунжер; 19 - кнопка тактического сброса груза; 20 - кнопка управления фарами; 21 - кнопка аварийного сброс груза; 22 — кнопка выключения фрикциона ручки „шаг—газ".
С торца оси имеется штуцер подачи жидкости от основной гидросистемы вертолета. Фрикцион надежно удерживает ручку „шаг-газ" в любом положении, что обеспечивает возможность бесступенчатого изменения общего шага несущего винта. Фрикцион затянут маховиком так, что без нажатия на кнопку выключения фрикциона ручку „шаг-газ" можно перемещать только с усилием 196...245 Н (20...25 кгс). При нажатии кнопки срабатывает электромагнитный кран ГА-192Т гидросистемы, и жидкость поступает в цилиндр фрикциона под поршень. Под давлением жидкости поршень совместно с плунжером перемещается, отжимает тарелку, и диски фрикциона освобождаются. При отпускании кнопки тарелка под действием усилий сжатых пружин вновь прижмет подвижные диски фрикциона к неподвижным. Диапазон отклонений ручки „шаг-газ" - 56°, крайние положения ручки „шаг-газ" ограничиваются винтовыми упорами.
Рукоятка коррекции изготовлена из трубы переменного сечения, В верхней части ее напрессован слой резины с ромбовидной насечкой. Своим хвостовиком рукоятка установлена на двух шариковых подшипниках в корпусе ручки. На конце хвостовика рукоятки установлен поводок с шарнирным ушком, к которому подсоединяется звено проводки управления двигателями. Полный угол поворота рукоятки коррекции равен 90о и ограничивается двумя винтами, установленными на корпусе ручки. Поворотная рукоятка имеет стопорное устройство, состоящее из набора дюралюминиевых дисков, пружины и муфты.
Корпус кнопок - сварной конструкции. Нижняя его часть хомутом укреп; лена к корпусу ручки, а верхняя осью через шариковый подшипник шарнирно соединена с рукояткой коррекции. В верхней части корпуса кнопок расположены четыре гнезда под кнопки: выключения фрикциона ручки „шаг-газ", аварийного сброса груза, управления фарами, тактического сброса груза.
Два рычага раздельного управления двигателями установлены соосно. Один рычаг жестко закреплен на валике, а второй - на втулке, которая центрируется на этом же валике посредством двух шариковых подшипников. Валик опирается на два шариковых подшипника, смонтированных в расточках проушин кронштейна. Каждый рычаг состоит из основания, трубы, головки и фиксирующего устройства. Рычаги в среднем положении фиксируются во впадине сектора. В фиксирующее устройство входят кнопка, качалка, стальной толкатель, ползун с зубом и возвратная пружина. Перемещение рычага вверх от среднего положения обеспечивает перевод двигателя на режим большей мощности. Для подсоединения тяг от дифференциального узла проводки управления мощностью двигателей на валике и втулке смонтированы рычаги с фрикционами. Последние состоят из подвижных и неподвижных дисков, которые сжаты тарельчатыми пружинами, поэтому для перемещения рычагов необходимо прикладывать усилие 39...58 Н (4...6 кгс).
Правая ручка „шаг-газ" в отличие от левой не имеет дискового фрикциона ручки, стопорного устройства рукоятки коррекций и рычагов раздельного управления двигателями.
Замыкающий вал соединяет обе ручки „шаг-газ", с которыми связан четырьмя тягами: две из них предназначены для управления общим шагом, а две другие - для управления двигателями. Он состоит из наружного и внутреннего валов, установленных по соосной схеме. Каждый вал выполнен из трубы, по концам которой приклепаны стальные цапфы, и валы могут поворачиваться независимо друг от друга. Внутренний вал предназначен для передачи движения от ручки „шаг-газ" в проводку управления двигателями, а наружный вал - в проводку управления общим шагом. Внутренний вал цапфами устанавливается на двух шариковых подшипниках в кронштейнах, закрепленных к каркасу пола кабины. По концам вала на болтах установлены рычаги, к которым подсоединяются тяги от ручек „шаг-газ"; в средней части вала закреплен и выведен через усиленный вырез наружного вала рычаг с проушинами для двух тяг, идущих к дифференциальному узлу. Наружный вал шарнирно установлен на внутреннем валу посредством двух пар шариковых подшипников; полости подшипников набиты смазкой и закрыты крышками с сальниками. На концах вала закреплены рычаги для тяг от ручек „шаг-газ", в средней части -рычаг для соединения с проводкой управления общим шагом.
Дифференциальный узел является кинематическим звеном проводки управления двигателями и обеспечивает независимость управления от ручки „шаг-газ" и рычагов раздельного управления двигателями. Он состоит из внутреннего и наружного валов, установленных соосно. Внутренний вал цапфами опирается на два шариковых подшипника, смонтированных в кронштейнах навески узла. Наружный вал посредством двух шарикоподшипников центрируется на внутреннем вале. Каждый вал на концах имеет закрепленные рычаги. К одним из них подсоединяются тяги от рычагов раздельного управления двигателями, к другим с помощью двух шарикоподшипников устанавливаются качалки. К нижним концам качалок подсоединяются тяги, идущие от замыкающего вала, к верхним - тяги проводки управления двигателями.
При отклонении ручки „шаг-газ" или повороте рукоятки коррекции качалки поворачиваются на своих осях и передают движение в провод управления двигателями. При отключении рычагов управления двигателями движение через рычаги передается непосредственно на валы, который поворачиваясь, отклоняют качалки. При этом нижние плечи качалок не изменяет своего положения, а верхние переда движение в проводку управление двигателями.
Блок валов установлен на потолочной панели и состоит из двух вал смонтированных на шариковых подшипниках в кронштейнах. Внутренний кронштейн для опор валов является общим. Валы имеют возможность одновременного, так и разделы углового перемещения. На конце валов укреплены рычаги, соединенные тягами с рычагами топливных насосов двигателей, и рычаги, к которым подсоединены тяги, связанные с проводом управления.
Для возможности воздействия полете на работу системы автоматам кого поддержания частоты вращения несущего винта предусмотрено управления перенастройкой частоты вращения двигателей. Управление включается электромеханизм МП-100М, распределительный вал и две тяги управления рычагами перенастройки на насос НР-ЗВМ. Электромеханизм МП-100М размещен на потолочной панели перед распределительным валом и штоком крепления к кронштейну, установленному шпангоуте № 2А. Корпус механизма соединен с рычагом распределительного вала, который расположен перед блоком валов. Распределительный вал размещен в опорах на двух шарикоподшипниках. Опорами являются кронштейн блока роликов управления правого двигателя и левый кронштейн блока валов. Распределительный вал своими рычагами соединен с регулируемыми тягами, а последним с рычагами на насосах НР-ЗВМ. Управление электромеханизмами МП - 100М осуществляется переключателями „Обороты. Больше - Меньше", смонтированными на ручках „шаг-газ". Величина и знак изменения частоты вращения несущего винта зависят от величины и направления хода штока электромеханизма, а контроль за перенастройкой частоты вращения двигателей производится по указателю оборотов несущего винта.
7.8. УПРАВЛЕНИЕ ОСТАНОВОМ ДВИГАТЕЛЕЙ И ТОРМОЗОМ НЕСУЩЕГО ВИНТА
Управление остановом двигателей (рис.7.12)осуществляется двумя ручками, которые тросовой проводкой связаны с кранами останова топливных насосов-регуляторов НР-ЗВМ.Ручки крепятся в кронштейне на потолке кабины экипажа; на рукоятках ручек установлены фиксаторы с пружинами, обеспечивающие стопорение ручек в положении „Закрыто" -для этого на кронштейне имеются упоры к рычагам рукояток, а через серьгу закреплены пружины, предназначенные для фиксации ручек в положении „Открыто".К концам ручек приклепаны ролики, на которых закреплены тросы. От роликов тросовая проводка идет к роликам, смонтированным в кронштейнах, установленных на потолочной панели в двигательном отсеке. К ведущим роликам кронштейнов прикреплены поводки, соединенные с тягами кранов останова насосов двигателей. Для регулировки натяжения тросов в проводке установлены тендеры. При останове двигателя необходимо перевести соответствующую ручку вниз до упора.
Рис. 7.12. Схема управления остановом двигателей
1— рукоятка; 2,5— кронштейн; 3,7— ролик; 4— трос; 6— тяга
Рис. 7.13. Схема управления тормозом несущего винта
1 — ручка; 2— ролик; 3— тросовая проводка; 4— текстолитовые направляющие 5— разгрузочная пружина; 6 — кнопка; 7— стержень; 8— ползун; 9— защелка; 10— пружина; 11— кронштейн; 12— концевой выключатель; 13— зубчатый сектор; 14— основание ручки
Управление тормозом несущего винта (рис.7.13) осуществляется ручкой, которая связана с рычагом тормоза тросовой проводкой, проложенной через ролики и текстолитовые направляющие. Для предохранения рычага тормоза от перегрузки при резком торможении в тросовую проводку включена разгрузочная пружина. В тросовой проводке установлен тандер для ее регулирования. Ручка установлена в кабине экипажа на кронштейне вместе с зубчатым сектором, который обеспечивает стопорение ручки в различных положениях. Ручка состоит из трубы, эбонитовой рукоятки, основания и стопорного устройства. В расточке основания ручки имеются шариковые подшипники, которыми она устанавливается на оси. К нижнему рычагу основания крепится трос управления. Ручка стопорится защелкой, которая под действием пружины заходит во впадины зубчатого сектора. Расстопоривание ручки осуществляется нажатием на кнопку, которая через стержень и ползун выводит защелку из впадины зубчатого сектора.
Управление тормозом сблокировано с системой запуска двигателей, вследствие чего их запуск возможен только при полностью расторможенной трансмиссии, т.е. когда ручка управления тормозом находится в крайнем нижнем положении.
7.9. ТЕХНИЧЕСКОЕ ОБСЛУЖИВАНИЕ СИСТЕМЫ УПРАВЛЕНИЯ ВЕРТОЛЕТОМ
В процессе эксплуатации вертолета обслуживание элементов управления в основном заключается в визуальном контроле их фактического состояния (тяг, качалок, тросовой проводки), отсутствия на них механических повреждений, надежности крепления, смазки шарнирных соединений, правильности отклонения командных рычагов, регулировки зазоров. Все осматриваемые элементы управления должны быть чистыми, не иметь следов коррозии, трещин, острых кромок и прочих дефектов. Гайки должны быть полностью затянуты и зашплинтованы. На тягах не должно быть глубоких вмятин и потертостей, ослабления трубчатых заклепок люфтов в резьбовых соединениях, прогибов и коррозии. Допускаются овальность и вмятины на трубах до 0,5 мм, потертости и выработка от роликов глубиной до 0,2 мм, прогибы до 0,5 мм. Прогиб тяг не должен превышать 0,5 мм при длине тяги 700 мм и 1,2 мм при большей ее длине, продольные царапины длиной более 150 мм и глубиной более 0,2 мм не допускаются. Если дефекты превышают установленные размеры, тяги заменяются. Легким покачиванием тяги вдоль оси убеждаются в отсутствии люфтов в шарнирных соединениях наконечников тяг, которые устраняются заменой этих наконечников. При замене наконечников не следует допускать выхода резьбовой части наконечника за контрольное отверстие, при ослаблении заклепок крепления наконечников тяг поврежденную тягу заменяют. При ослаблении контргаек регулируемых наконечников следует затянуть их и восстановить контровку и метки. Перемычки металлизации должны обеспечивать свободный ход тяги на всем диапазоне и не задевать за другие детали. При прижатой тяге к двум нижним роликам направляющих зазор между верхним роликом и тягой должен быть в пределах 0,1…0,4 мм; зазор уменьшается поворотом эксцентрикового болта ролика.Зазоры между подвижными элементами управления и неподвижными элементами конструкции вертолета должны быть не менее 3 мм, а между тягами, качалками и подвижными элементами конструкции вертолета -не менее 5 мм. Тщательно осматриваются забустерные тяги и качалки, а также болты установки качалок на отсутствие трещин, царапин, коррозии.
Шарнирные соединения элементов проводки управления смазывают смазкой ЦИАТИМ-201.
При осмотре механизма загрузки и ЭМТ-2М необходимо убедиться в отсутствии ослабления гаек штоков, трещин на вильчатом наконечнике штока, ушке цилиндра и качалке, которые не допускаются. Зазоры между подвижными элементами механизма и деталями должны быть не менее 3 мм. Механические повреждения корпуса тормоза ЭМТ-2М, а также трещины на поводке, срез шлиц и ослабление его крепления не допускаются.
При осмотре тросовой проводки особое внимание обращают на места прохода тросов через ролики и текстолитовые направляющие и отсутствие повреждения тросов. На тросах не допускаются обрыв отдельных нитей или прядей, нарушения заделки в наконечнике, резкие перегибы и изломы, уменьшение диаметра троса за счет вытяжки и коррозии. Не допускаются касания тросов в местах прохождения их по роликам и на участках, где имеются минимально допустимые зазоры между тросами и деталями конструкции. Зазоры между тросами и неподвижными деталями конструкции должны быть не менее 3 мм, а между подвижными деталями - 5 мм. Трещины и изломы реборд роликов и текстолитовых направляющих не допускаются, направляющие устанавливаются строго по направлению тросов. Тендеры тросов управления должны быть надежно законтрены; тросы с заершенностью, вспучиванием отдельных нитей или прядей заменяют. Коррозию с тросовой проводки удаляют ветошью, смоченной в керосине. Если этим способом коррозия не устраняется, то трос необходимо заменить. Проверяется надежность соединения тросовой проводки с втулочно-роликовой цепью механизма управления рулевым винтом.
Проверка цепей управления вертолетом производится при подсоединенной к вертолету наземной гидроустановки. Усилие при перемещении ручки управления циклическим шагом по мере ее отклонения от нейтрального положения должно возрастать. Ручка управления при отпущенной кнопке управления триммером должна фиксироваться во всех промежуточных положениях. Педали и ручка „шаг-газ" при перемещении должны отклоняться плавно, без заеданий во всем диапазоне рабочего хода. Рукоятка коррекции ручки „шаг-газ" должна вращаться плавно, без заеданий, с некоторым самоторможением, необходимым для ее удержания при вибрациях вертолета в полете. Поочередно установив рычаги раздельного управления двигателей в крайнее нижнее, а затем в крайнее верхнее положение, следует убедиться в отсутствии заеданий, а также в их фиксации в среднем положении. ычаги управления кранами останова должны перемещаться без заеданий и фиксироваться в крайних положениях. При заедании фиксатора проверяют состояние оси и пружины рычага фиксатора. Натяжение тросов управления остановом двигателей должно быть (196±29) Н [(20±3) кгс].
В случае эксплуатации вертолета без замены подвижных элементов управления производится периодическая проверка отклонения тарелки автомата перекоса в продольном и поперечном направлении по шкалам и нониусам, а также отсутствия люфтов в соединениях. Для этого подключают наземную гидроустановку и включают основную гидросистему. Плавно перемещая ручку управления и устанавливая ее в крайние положения до упоров, проверяют наклон тарелки автомата перекоса, который должен соответствовать техническим требованиям. Кроме того, проверяется нейтральное положение при фиксации ручки и агрегата управления в нейтральном положении. В этом случае ручка „шаг-газ" находится в среднем положении. Люфты при покачивании тяг управления не допускаются. Все шарнирные соединения при выполнении периодических видов обслуживания смазывают согласно карте смазки.
Моменты затяжки элементов крепления управления, Н-м (кгс-м)
Гайки шпилек крепления направляющей ползуна
автомата перекоса 49...58 (5...6)
Гайки шпилек крепления кронштейна ползуна
автомата перекоса 12...16 (1,3...1,65)
Гайки шпилек крепления кронштейна рычага общего
шага автомата перекоса 49...58 (5...6)
Гайки шпилек крепления верхнего фланца тарелки
автомата перекоса 22...2б (2,3...2,7)
Гайки стяжных болтов верхних вилок тяг поворота лопастей несущего
винта 44...49 (4,5...5)
Гайки стяжных болтов крепления кронштейна поводка автомата
Перекоса 58...64 (6...7)
Гайки болтов крепления кронштейна датчика
УП 21-15 12...16 (1,3...1,65)
Гайки стяжных болтов крепления ограничителя смешения хомута поводка
автомата перекоса 19...24 (2...2,5)
Гайки болтов крепления качалок продольного
и поперечного управления 10...19 (1...2)
Винты крепления кронштейнов, установки направляющих колодок тросов путевого управления 4,9…..5,8 (0,5...0,6)
Смазывание узлов системы управления производится путем ее зашприцовки в подшипники через пресс-масленки, а в случае отсутствия последних выполняется предварительная протирка и ручная смазка поверхности подшипников и защитных шайб.
При подготовке вертолета к летней эксплуатации смазывают:
-смазкой ЦИАТИМ-201 - подшипники колонок ручного управления, качалок колонок ручного управления, вала системы „шаг-газ", поводка и качалки ручек „шаг-газ", качалок системы „шаг-газ", тяг управления перенастройкой частоты вращения двигателей, механизмов МП-100М педалей путевого управления, качалок путевого управления, сектора путевого управления, системы управления остановом двигателей, рычага управления тормозом несущего винта;
- смазкой СТ (НК-50) - тросы системы путевого управления; втулочно-роликовую цепь системы путевого управления-тросы системы управления остановом двигателей; тросы системы управления тормозом несущего винта.
При подготовке вертолета к зимней эксплуатации смазывают:
-смазкой ЦИАТИМ-201 - подшипники тяг проводки ручного управления, качалок проводки ручного управления, наконечников штоков гидроусилителей и механизмов загрузки, подшипники тяг проводки управления общим шагом и газом двигателей, качалок проводки путевого управления, тяг проводки путевого управления, тяг управления остановом двигателей, механизма системы СПУУ-52;
-смазкой СТ (НК-50) - ролики тросовой проводки путевого управления; ролики управления остановом двигателей; ролики управления тормозом несущего винта.
7.10. КОНТРОЛНЫЕ ВОПРОСЫ И ЗАДАНИЯ
1. Перечислите основные составные части автомата перекоса. Каково их назначение?
2. Как обеспечивается независимость продольного и поперечного управления вертолета?
3. Какие типы проводки используются в системе управления вертолета?
4. Используя рисунок7.10, укажите командные рычаги, которые управляют мощностью двигателей, общим шагом несущего винта? Как осуществляется регулировка усилий перемещения этих рычагов?
5. Как осуществляется загрузка ручки продольно-поперечного управления вертолетом? Что необходимо сделать летчику для снятия нагрузки при перемещении ручки?
6. Каково назначение замыкающего вала, дифференциального узла?
7. Как осуществляется управление остановом двигателей, тормозом несущего винта?
8 ГИДРАВЛИЧЕСКАЯ СИСТЕМА
Гидравлическая система (ГС) предназначена для питания рабочей жидкостью четырех гидроусилителей, гидроцилиндра управления фрикционом ручки „шаг-газ", цилиндра гидроупора в цепи продольного управления посредством передачи энергии движущейся под давлением жидкости.
8.1. ОБЩИЕ СВЕДЕНИЯ
В гидросистеме для повышения уровня безопасности полетов имеются основная (ОГС) и дублирующая (ДГС) гидросистемы.
Основные технические данные ГС:
Рабочая жидкость. масло АМГ-10
Объем масла АМГ-10 в системе, л. 23
В том числе, л:
в гидробаках ОГС и ДГС 2x10
трубопроводах 2
Рабочее давление в ОГС и ДГС, МПа (кгс/см2). 4,5+-0,3...6,5 +0,8-0,2 (45±3...65+8-2)
Минимальное давление в ОГС, при котором переключается питание гидроусилителей на ДГС, МПа I (кгс/см2). 3±0,5 (30±5)
Давление в ОГС, при котором переключается питание гидроусилителей с ДГС на ОГС, МПа (кгс/см2), не менее. 3,5±0,5 (35+5)
Давление срабатывания сигнализатора давления МСТ-25вДГС,МПа
(кгс/см2). 2,5±0,16 (25±1,6)
Давление срабатывания сигнализатора давления
МСТ-35А в ОГС, МПа (кгс/смг). 3,5±0,16 (36±1,6)
Начальное давление зарядки гидроаккумуляторов, МПа
(кгс/см2) 3+0,2 (30+2)
Температура окружающего воздуха, при которой ГС работает нормально, °С -50...+60
Допустимая температура рабочей жидкости, "С +70
Рис. 9.1. Принципиальная схема гидравлической системы:
1 — гидробак; 2 — шестеренный насос НШ-39М; 3 — обратные клапаны ОК-10А; 4 — фильтр тонкой очистки 8Д2.996.017-2: 5 — автомат разгрузки насоса ГА-77В; 6 — магистраль слива жидкости от ГА-77В в бак; 7 — указатель манометра ДИМ-100К; 8 — датчик манометра ДИМ-100К; 9 — гидроаккумуляторы; 10— магистраль подачи жидкости к управляющему золотнику ГА-77В; 11 — электромагнитный кран ГА-74М/5; 12— сигнализатор давления МСТ-35; 13, 14, 18 — электромагнитные краны ГА-192Т; 15,— дозатор ГА-172-00-2; 16—ручка ШАГ—ГАЗ с цилиндром растопоривания фрикциона; 17 — фильтр тонкой очистки ФГ-11БН; 19—дроссель: 20 — гидроупор; 21 — комбинированные гидроусилители КАУ-30Б; 22 — комбинированный гидроусилитель РА-60Б; 23, 24, 25, 26, 27—коллекторы; 28 — бортовой клапан нагнетания основной системы; 29 — бортовые клапаны всасывания; 30 — бортовой клапан нагнетания дублирующей системы; 31 — автоматический клапан ГА-59/1 включения дублирующей системы; 32 — масломерное стекло; 33 — магистраль слива жидкости из автомата разгрузки насоса и клапана ГА-59/1; 34 — трубопроводы дренажа полостей гидробака; 35 — заливная горловина; 36 — сигнализатор давления МСТ-25
Перечень и число агрегатов, входящих в основную и дублирующую гидросистемы (рис. 8.1), приведены в табл. 8.1.
Таблица8.1
Агрегат | Число агрегатов | ||
ОГС | ДГС | ||
Гидробак | 1 | 1 | |
Насос шестеренный НШ-39М | 1 | 1 | |
Обратный клапан ОК-10 | 2 | 2 | |
Фильтр тонкой очистки |
| ||
8Д2.996.017-2 | 1 | 1 | |
Фильтр тонкой очистки ФГ-11БН | 1 | 1 | |
Автомат разгрузки насоса ГА-77В | 1 1 | ||
Гидроаккумулятор | 2 | 1 | |
Электромагнитный крен ГА-74М/5 | 1 | 1 | |
Г ГА-192 | 4 | _ | |
" ГА-192Т | 1 | _ | |
Дозатор ГА-172-00-2 | 1 | _ | |
Дроссель | 1 | _ | |
Автоматический клапан включения ГА-59/1 | _ | 1 | |
Бортовой клапан всасывания 1890А-3-Г | 1 | 1 | |
Бортовой клапан нагнетания 1925А-1-Т | 1 | 1 | |
Перекрывной кран 630600 | 1 | 1 | |
Коллекторы нагнетания | 2 | 1 | |
Коллекторы слива | 1 | 1 | |
Дистанционный электрический манометр ДИМ-100 | 1 | 1 | |
Сигнализатор давления МСТ-35А | 1 | _ | |
МСТ-25А | — | 1 | |
Цилиндр гидроупора | 1 | _ | |
Гидроцилиндр управления фрикционом датчики „шаг-газ" | 1 | _ | |
ОГС и ДГС, состоят из контура питания и контура потребления.
Контур потребления ОГС включает три гидроусилителя КАУ-305, один -РА-60Б, цилиндр управления гидроупором, гидроцилиндр управления фрикционом левой ручки „шаг-газ".
В ГС входят также трубопроводы и гибкие шланги, а также элементы управления ГС (2АЗСГК-10, „Гидросист. основн.", „Гидросист. дублир." - на правой панели АЗС, два переключателя ЛПГ-15К „Гидросист. основн.", „Гидросист. дублир." и кнопка „Откл. дублир" - на средней панели электропульта).
Контроль параметров работы гидросистемы приведен в табл. 8.2.
Таблица 8.2
Контроль работы гидросистемы | Тип датчика | Контролируемая аппаратура | Примечание |
Давление рабочей жидкости в ОГС | ИД-100 | Указатель УИ-1-100 | Датчики располагаются на гидропанели, указатели — на средней панели электропульта |
Давление рабочей жидкости в ДГС | ИД-100 | Указатель УИ-1-100 | То же |
Основной | МСТ-35А | Сигнальное табло зеленого цвета „Основная включена" | Датчики сигнализаторов расположены на гидропанели, табло - на средней панели электропульта |
Дублирующей | МСТ-25А | Сигнальное табло красного цвета „Дублир. включена" | Тоже |
8.2 РАБОТА ГИДРОСИСТЕМЫ.
При работающей трансмиссии рабочая жидкость из бака ОГС засасывается насосом НШ-39М, который подает под давлением жидкость через обратный клапан к фильтру, в котором масло АМГ-10 очищается с тонкостью фильтрации 12...16 мкм, а затем поступает к автомату разгрузки насоса ГА-77В. Из агрегата ГА-77В жидкость поступает в гидравлические полости гадроаккумуляторов, сжимая азот при давлении в ОГС свыше (30±2) кгс/см2 (гидроаккумуляторы сглаживают пульсации давления жидкости в ГС, что повышает надежность работы агрегатов). От гидроаккумуляторов жидкость подводится к командному золотнику ГА-77В и к датчику манометра ДИМ-100. Одновременно жидкость приходит к электромагнитному крану ГА-74М/5 и электромагнитному крану ГА-192, включающему при нажатии кнопок „Фрикцион" на ручках „шаг-газ" подачу жидкости через дозатор к гидроцилиндру управления фрикционом ручки, в результате растормаживания пилот может перемещать ручки „шаг-газ". Дозатор пропускает 400 см3 жидкости к потребителю и прекращает гидропитание. при утечке жидкости из этой магистрали.
При включении переключателя „Гидросист. основн." открывается электромагнитный кран ГА-74М/5, который подключает контур питания к контуру потребителей. Жидкость поступает к фильтру тонкой очистки ФГ-11БН, где очищается с тонкостью фильтрации 12...15 мкм, и далее к коллектору нагнетания ОГС, из которого жидкость поступает к четырем гидроусилителям, снимающим шарнирные нагрузки с командных органов при управлении вертолетом. Одновременно жидкость подается к трем электромагнитным кранам, которые срабатывают при включении соответствующих каналов автопилота на центральном пульте, для перевода гидроусилителей в комбинированный режим управления (автоматическая стабилизация режима полета по командам от автопилота).
После фильтра ФГ-11БН жидкость при открытом электромагнитном кране ГА-192 (включают его микровыключатели АМ-800К, расположенные на штоках камер низкого давления при полном их обжатии) через дроссель проходит к цилиндру гидроупора, в результате чего шток гидроупора выходит из цилиндра и ограничивает перемещение цепи продольного управления и, как следствие, - отклонение тарелки автомата перекоса назад в пределах 2о+-12'. Дроссель предотвращает резкое перемещение штока гидроупора.
После крана ГА-74М/5 жидкость подводится к сигнализатору давления МСТ-35А (МСТ-35А при достижении давления в ОГС (35±1,6) кгс/см2 срабатывает, и загорается зеленое табло „Основная включена") и к автоматическому клапану включения ГА-59/1 ДГС. В случае уменьшения расхода жидкости потребителями и достижения давления в ОГС 6,5 МПа (65 кгс/см2) автомат разгрузки насоса ГА-77В переключается автоматически на сообщение магистрали нагнетания от насоса НШ-39М с магистралью слива в бак. Расход жидкости в этом случае в системе при работе потребителей восполняют гидроаккумуляторы. При понижении давления в системе до (4,5±0,3) МПа [(45+3) кгс/см2] автомат разгрузки подключит магистраль нагнетания от насоса на подпитку контура потребления. Жидкость из гидроусилителей при их работе сливается в коллектор слива ОГС, соединенный магистралью с гидробаком.
Электромагнитные краны ГА-192 соединяют при выключенном положении магистрали питания своих потребителей с магистралью слива в бак ОГС, по которой сливается жидкость из автомата разгрузки насоса ГА-77В и электромагнитного крана ГА-74М/5.
В полете переключатель („Гидросист. дублир.") включен и находится под предохранительной скобой. При работающей ОГС, давление в которой более (3,5±0,5) МПа [(35±5) кгс/см2], дублирующая ГС находится в состоянии „горячего" резервирования: насос НШ-39М ДГС подает жидкость через обратный клапан, фильтр, автомат разгрузки насоса ГА-77В, электромагнитный кран ГА-74М/5 и открытый (под давлением жидкости в ОГС) автоматический клапан включения ГА-59/1 по магистрали слива в бак ДГС.
При падении давления жидкости в ОГС до(3,5±1,6)МПа [(35±1,б) кгс/см2] гаснет сигнальное табло „Основная включена", а при давлении (3±0,5) МПа [(30+5) кгс/см2] автоматический клапан включения ГА-59/1 закрывает слив жидкости от насоса ДГС в бак. Давление жидкости в ДГС возрастает, происходит подача жидкости в гидроаккумулятор, а через электромагнитный кран ГА-74М/5, фильтр ФГ-11БН - к коллектору нагнетания ДГС, от которого жидкость АМГ-10 поступает к четырем гидроусилителям. Гидроусилители работают в этом случае как силовые следящие гидроприводы. Слив жидкости из гидроусилителей происходит в коллектор слива, из которого жидкость отводится в бак ДГС. При достижении давления в ДГС (2,5±0,16) МПа [(25±1,6) кгс/см2] срабатывает сигнализатор Давления МСТ-25А, который включает красное сигнальное табло „Дублир. включена" с одновременным замыканием электроцепи электромагнитного реле, срабатывающего на закрытие электромагнитного крана ГА-74М/5 ОГС (хотя переключатель „Гидросист. основн." включен). Тем самым происходит отключение контура основных потребителей от контура питания ОГС во избежание утечки жидкости из гидросистемы через негерметичный контур потребления ОГС. Речевой информатор выдает звуковую информацию в телефоны.
При возрастании давления в ДГС до 6,5 МПа (65 кгс/см2) автомат разгрузки сообщает магистраль нагнетания после насоса с магистралью слива в бак ДГС, а питание потребителей обеспечивает гидроаккумулятор. При понижении давления до (4,5±0,3) МПа [(45±3) кгс/см2] автомат разгрузки ГА-77В вновь подключает насос на подачу жидкости в контур потребления.
При подключении наземной гидроустановки к бортовым клапанам всасывания, нагнетания ОГС, ДГС и открытых перекрывных кранах 630600 рабочая жидкость из гидробаков ГС подается насосами гидроустановки через бортовые клапаны нагнетания, обратные клапаны к фильтрам, автоматам разгрузки и далее в магистрали ОГС, ДГС. Обратные клапаны на выходе из насосов предотвращают при этом движение жидкости к неработающим насосам.
Бортовые клапаны всасывания используются также для слива жидкости из баков и заправки жидкости в баки закрытым способом от наземной гидроустановки.
Предупреждение. В начальный период работы гидросистемы при запуске двигателей (или включении наземной гидроустановки при проверке ГС) при включенных обоих электромагнитных кранах ГА-74М/5 давление в ДГС может нарастать быстрее, чем в ОГС. Если в последней давление значительно меньше (3+0,5) МПа [(30±5) кгс/см2], а в ДГС достигло уже (2,5±0,16) МПа [(25±1,6) кгс/см2], то сигнализатор МСТ-25А ДГС выключит электромагнитный кран ГА-74М/5 ОГС. При этом клапан ГА-59/1 обеспечивает питание гидроусилителей от ДГС. В этой ситуации следует переключиться на ОГС, нажав кнопку „Откл. дублир." и удерживая ее 1...1,5 с, пока не загорится зеленое табло „Основная включена" и погаснет красное табло „Дублир. включена".
Когда же давление в ОГС нарастает быстрее, чем в ДГС (что зависит от состояния агрегатов, их регулировки), и достигнет (3,5±0,5) МПа [(35±5) кгс/см2], клапан ГА-59/1 переключает насос ДГС на слив в бак ДГС, а работающей остается только ОГС.)
8.3. АГРЕГАТЫ ГИДРОСИСТЕМЫ
Панель гидроагрегатов - специальный кронштейн, склепанный из листового дюралюминия и уголковых профилей, на котором установлена основная часть агрегатов ОГС и ДГС, кроме гидронасосов, гидроусилителей, цилиндров фрикциона ручки „шаг-газ", гидроупора, бортовых клапанов всасывания и нагнетания, перекрывных кранов 630600.
Гидропанель с агрегатами в собранном виде устанавливается в редукторном отсеке рядом с гидронасосами и гидроусилителями.
Гидробак (рис. 8.2) сваривается из сплава АМцМ и имеет обечайку, два днища и внутреннюю перегородку, разделяющую на отсеки ОГС и ДГС и имеющую в верхней части отверстие для предотвращения переполнения одного из баков.
Рис. 8.2. Гидробак:
1— днище; 2 — обечайка; 3,10— штуцеры слива жидкости из автоматов разгрузки насосов; 4,9— дренажные штуцеры; 5— штуцер слива жидкости из гидроагрегатов; 6— заливная горловина; 7— крышка; 8— перегородка; 11— штуцеры слива жидкости из гидроусилителей; 12,13— штуцеры подсоединения всасывающих трубопроводов
Насос НШ-39М (рис. 8.3) обеспечивает подачу жидкости из гидробака к потребителям.
Рис. 8.3. Насос шестеренный НШ-39М:
1 — крышка; 2 — корпус; 3 — дистанционное кольцо; 4, 7 — неподвижные и подвижные бронзовые диски; S — наружная обойма игольчатого подшипника; 6,14.— ведущее и ведомое зубчатое колесо; 8, 12 — резиновые уплотнительные кольца; 9 — маслоуплотнительная втулка; 10 — армированная резиновая манжета; 11 — шлицевой пояс; 13 - стопорное кольцо; А — полость повышенного давления; Б — полость всасывания жидкости; В — полость управляющего давления подвижными дисками; Г — внутренний канал в корпусе, соединяющий полости А и В; Д — внутренний канал, отводящий утечки масла в полость Б; К — канал в корпусе, дренирующий полость между манжетами и атмосферой.
Основные технические данные НШ-39М
Тип насоса шестеренный высокого давления
Давление жидкости на выходе, кгс/см2 (МПа):
Рабочее 75 (7,5)
Максимальное 90 (9)
Номинальная частота вращения, мин-1:
насоса ОГС 2426
насоса ДГС 2437
Подача насоса при номинальной частоте
вращения и давлении 6,5 МПа (65 кгс/см2), л/мин 30
Полость между манжетами дренируется каналом и внешним трубопроводом с атмосферой в редукторном отсеке. Степень прижатия подвижных дисков (со стороны привода) и к зубчатым колесам регулируется давлением жидкости, поступающей через щелевой канал из полости нагнетания насоса. Насосы ОГС и ДГС крепятся болтовым соединением соответственно на крышках приводов агрегатов левого и правого бортов на главном редукторе ВР-14.
Гидроаккумулятор (рис. 8.4) предназначен для уменьшения пульсаций давления жидкости в ГС и восполнения расхода жидкости при работе насоса на холостом режиме. Составными частями являются сферический корпус с двумя резьбовыми горловинами, крышка с зарядным клапаном и гайкой, крышка со штуцером подвода (отвода) жидкости, гайкой и уплотнительным кольцом, резиновая диафрагма. Для равномерного обжатия на диафрагме имеется буртик утолщения, а также в корпусе ряд перфорированных отверстий.
Рис. 8.4. Гидроаккумулятор
1— зарядный клапан; 2— гайка; 3— крышка; 4— горловина; 5— верхняя обечайка; 6— резиновая диафрагма; 7— нижняя обечайка; 8— стакан; 9— гайка; 10— уплотнительное кольцо; 11— крышка; 12— угольник; 13— поясок
Фильтры обеспечивают очистку жидкости, от механических примесей для улучшения условий смазки и предотвращения заклинивания золотниковых пар.
Фильтр тонкой очистки8Д2.966.017-2 (рис. 8.5) состоит из стакана, головки со штуцерами входа, выхода, малым отсечным, перепуско-отсечным клапанами, фильтроэлемента, деталей уплотнения и крепления. В собранном фильтре жидкость проходит со штуцера входа через кольцевое отверстие между седлом и перепуско-отсечным клапаном в полость между стаканом и фильтром, а также через никелевую сетку саржевого плетения, открытый малый отсечной клапан к штуцеру выхода. При загрязнении фильтра под действием перепада давлений перепускно-отсечной клапан отжимается и жидкость со вода движется напрямую к выходному штуцеру. В случае демонтажа фильтроэлемента перепускно-отсечной клапан предотвращает утечку жидкости из системы со стороны входа, а малый отсечной - со стороны выхода.
Рис. 8.5. Фильтр 8Д2.966.017-2:
1 — стакан; 2 — фильтроэлемент; 3 — головка; 4 — резиновое уплотнительное кольцо; 5, 8 — пружины; 6 — перепускно-отсечной клапан; 7 — направляющая; 9 — седло; 10 — малый отсечной клапан
Основные технические данные фильтра 8Д2.966.017-2
Рабочее давление, МПа (кгс/см2) 21+1-0,7 (210+10-7)
Давление срабатывания перепускного клапана,
МПа (кгс/см2) 7+2-1(0,7+0,2-0,1)
Максимальная пропускная способность, л/мин 40
Тонкость фильтрации, мкм 12...16 (25 мкм - до1%)
Температура окружающей среды, оС 60...+100
Фильтр тонкой очистки ФГ-11БН (рис. 8.6) состоит из стакана, головки со штуцерами входа и выхода, фильтроэлемента, резиновых колец уплотнения.
Фильтроэлемент выполнен из никелевой проволоки саржевого плетения, гофрированной каркасной сетки, цилиндрического стального корпуса. Тонкость фильтрации 12...15 мкм.
Рис. 8.6. Фильтр тонкой очистки ФГ-11БН:
1,3 — резиновые уплотнительные кольца; 2 — каркас; 4 — штуцер входа; 5 — головка; 6 — стакан; 7 — фильтроэлемент; 8 — втулка.
Автомат разгрузки насоса ГА-77В (рис. 8.7) предназначен для автоматического поддержания рабочего давления в системе в пределах 4,5±0,3...6,5) МПа (45±3...65кгс/см2), так как насос НШ-39М - постоянной подачи. Обратный клапан шарикового типа пропускает жидкость только в систему и предотвращает разрядку ГС при работе насоса на режиме холостого хода. Узел командного золотника (гильза, золотник, редукционная пружина, плунжер, дроссель, детали крепления) является чувствительным и командным элементом, устанавливающим рабочее давление.
Рис. 8.7. Принципиальная схема работы разгрузки насоса ГА-77В:
I - насос переключен на рабочий режим; II - насос включен на холостой режим работы; III - сработал предохранительный клапан; 1 - корпус; 2 - обратный клапан; 3, 5, 6,13,14 - пружины; 4 - шариковый клапан; 7 -плунжер предохранительного клапана; 8 - исполнит золотник; 9-плунжер командного золотника; 10- промежуточный золотник; 11 - командный золотник;
12- крышка; 15 - антивибрационный замок.
Узел исполнительного золотника (гильза, золотник, пружина) непосредственно соединяет или разобщает магистраль нагнетания после насоса со сливом. Узел промежуточного золотника (гильза, золотник, антивибрационный замок) является связующим звеном между командным и исполнительным золотниками.
Предохранительный клапан, открываясь при давлении 7,8+0,1МПа (78+10 кгс/см2), предотвращает чрезмерное повышение давления в ГС при заедании командного, исполнительного или промежуточного золотника в положении на подачу жидкости в систему.
Работа автомата разгрузки насоса ГА-77В.
При создании насосом давления рабочей жидкости, она через штуцер входа, канал Б, обратный клапан 2 агрегата и канал В поступает в систему. Одновременно по каналу А в корпусе агрегата, кольцевой проточке в гильзе поршня 8 и средней кольцевой расточке промежуточного золотника 10 жидкость поступает к центральной проточке командного золотника 11. Положение командного золотника зависит, с одной стороны, от усилий редукционной пружины 6, с другой — от усилий на золотник со стороны давления гидрожидкости в системе, подводимой к плунжеру 9 командного золотника через канал Д.
Поскольку в данный момент давление жидкости ниже (6,5 ) МПа [(65
) кгс/см2], пружина 6 удерживает золотник в крайнем правом положении. В этом случае центральная проточка командного золотника 11 сообщает жидкость из канала А с правой рабочей полостью промежуточного золотника 10. Последний через свою среднюю расточку обеспечивает подвод жидкости из канала А в левую полость поршня 8. Соответственно противоположные полости золотника 10 и поршня 8 сообщатся со сливной магистралью через каналы Е и Г. Поршень 8, установленный в крайнем правом положении, предотвращает перепуск жидкости из канала А в канал Г на слив и обеспечивает рабочий диапазон давления в системе.
При достижении давления жидкости в системе (6,5 ) МПа [(65
) кгс/см2] плунжер 9, преодолевая усилие пружины 6, перемещает золотник 11 влево. Тогда жидкость через центральную кольцевую канавку золотника 11 поступает под левый торец золотника 10 и перемещает его вправо. Золотник 10 своей средней кольцевой расточкой сообщает канал А с правой полостью поршня 8, который, перемещаясь влево, соединяет своей кольцевой проточкой подводящий канал А с каналом Г слива жидкости в бак. Насос переключается на режим холостого хода. Вследствие образовавшейся разности давления в подводящем А и отводящем Г каналах обратный клапан 2 прижимается к своему седлу и перекрывает перепуск жидкости из системы.
По мере понижения давления жидкости в системе пружина 6 начинает перемещать золотник 11 вправо. Когда давление достигает нижнего предела (4,5±0,3) МПа [(45±3 кгс/см2)], золотник 11 занимает правое крайнее положение и подает жидкость под правый торец золотника 10, который, перемещаясь влево до упора, через свою среднюю кольцевую, расточку подает жидкость под левый торец поршня 8. Поршень под давлением жидкости и пружины 13 перемещается в противоположное положение и разобщает подводящий канал А от сливного канала Г. Насос начинает подавать жидкость в систему.
В случае отказа подвижных элементов автомата разгрузки насоса давление в системе повышается до (7,8+1) МПа [(78+10) кгс/см2], после чего срабатывает шариковый клапан 4, и жидкость из правой полости плунжера 7 сливается в бак. Вследствие возникновения перепада давления, действующего на плунжер 7, он перемещается в сторону пружины 3, преодолевая ее усилия, и открывает канал Г для слива жидкости в бак. При падении давления в системе и закрытии шарикового клапана 4 давление жидкости в обеих полостях плунжера выравнивается. Под действием пружины 3 он перемещается в противоположное положение и перекрывает канал Г. Перепуск жидкости на слив в бак прекращается.
Электромагнитный кран ГА-74М/5 (рис. 8.8) является перекрывным краном гидравлического действия с электромагнитным управлением и позволяет подключить контур питания к контуру потребления соответствующей ГС, а также проверить работоспособность ГС.
Рис. 8.8. Электромагнитный клапан ГА-74М/5:
а — кран включен (контур потребления подключен к контуру питания); б — кран выключен (контур потребления отключен от контура питания); 1 — корпус; 2 — штуцер слива жидкости; 3 — плунжер; 4, 8 — резиновые уплотнительные кольца; 5 — исполнительный золотник; 6,9 — гильзы; 7 — пробка; 10 — командный золотник; 11 - замок; 12,19 - ограничители; 13,15 - катушки; 14 - шайба; 16, 21 — корпус; 17- микровыключатель; 18 — штепсельный разъем; 20 - якорь; 22 — тяга узла электромагнита; 23 — штуцер подвода жидкости от насоса; 24 —штуцер отвода жидкости к потребителям.
Основные технические данные ГA-74M/5
Минимальное давление, МПа (кгс/см2) 5 (0,5)
Напряжение, подводимое к электромагниту, В 27±10 %
Потребляемая сила тока, не более, А 10
Командный золотник соединяется с тягой с якорем электромагнита и размещается за счет последнего при подаче напряжения на одну из катушек. Исполнительный золотник передвигается в крайнее положение („Открыто" или „Закрыто") под действием давления жидкости, подаваемой командным золотником. В исполнительном золотнике имеется осевое и радиальное калиброванное отверстия.
Электромагнитный кран ГА-192 (рис. 8.9) - перекрывной, электромеханического действия, обеспечивающий подключение соответствующих потребителей к магистрали подачи жидкости или слива в бак.
Рис. 8.9. Электромагнитный кран ГА-192:
а — электромагнитный кран включен (потребитель соединен с насосом); б — электромагнитный кран выключен (потребитель соединен с магистралью слива) ;
1 — пружина; 2 — крышка; 3 — корпус; 4,9- уплотнительные кольца; 5 — корпус электромагнита; 6 — упор сердечника электромагнита; 7 — гильза; 8- — золотник, 10 — тарелка
Основные технические данные ГА-192
Напряжение, подводимое к электромагниту, В 27+-10 %
Потребляемая сила тока, не более, А 1,2
Время срабатывания, с 0,1
Масса, кг 0,9
При обесточенном электромагните золотник под действием пружины сообщает потребитель с магистралью слива. В этом случае магистраль подачи от насоса отсечена. При подаче напряжения золотник сдвигается сердечником электромагнита под действием наведенной электромагнитной силы, преодолевая усилие пружины, и магистраль подачи жидкости от насоса соединяется с потребителем, а магистраль слива отсечена.
Автоматический клапан включения ГА-59/1 предназначен для автоматического включения ДГС на питание гидроусилителей при падении давления в ОГС менее (3±0,5) МПа [(30±5) кгс/см2] и отключения ДГС при достижении давления в ОГС свыше (3,5+0,5) МПа ((35±5) кгс/см2).
Основные составные части ГА-59/1 (рис. 8.10): корпус со штуцерами (подвода от насоса ДГС, слива в бак ДГС), золотник с гильзой, редукционной пружиной, переходник со штуцером подвода жидкости от ОГС, сетчатым фильтром, дросселем, детали уплотнения и крепления. Дроссель дополнительно гасит пульсации давления жидкости, подводимой от ОГС.
Рис. 8.10. Автоматический клапан включения ГА-59
а — ДГС обеспечивает питание гидроусилителей; б — ДГС находится в состоянии „горячего" резервирования (давление в ДГС равно нулю); 1 - гайка; 2 - пружина; 3, 7, 13, 15 - резиновые уплотнительные кольца; 4 — штуцер подвода жидкости от насоса ДГС; 5 — гильза; 6 — золотник; 8 — закладная шайба; 9 'направляющая; 10 — корпус; 11 — стакан; 12 — тарелка; 14 — штуцер слива в бак ДГС; 16 — переходник; 17—дроссель; I8 — сетчатый фильтр; 19 — штуцер подвода жидкости от ОГС.
При давлении в ОГС менее (3±0,5) МПа [(30 ±5) кгс/см2] золотник пор действием пружины сдвигается в направлении переходника и отсекает магистраль подачи от насоса ДГС от магистрали слива в бак ДГС - питание гидроусилителей обеспечивается от ДГС. Если давление жидкости в ОГС более (3,5±0,5) МПа [(35+5) кгс/см2], золотник сдвигается под действием этого давления, сжимая пружину, и сообщает магистраль от насоса ДГС со сливом в бак ДГС. Питание потребителей осуществляется от ОГС.
Дозатор ГА-172-00-2 (рис. 8.11) отключает магистраль питания гидроцилиндра управления фрикционом ручки „шаг-газ" при ее повреждении во избежание утечки жидкости из ГС.
Жидкость от насоса ОГС поступает на вход, через кольцевые полости между корпусом, гильзой, золотником проходит в полость между золотником и поршнем, что вызывает перемещение золотника в направлении штуцера выхода и сжатие пружины, а жидкость проходит к штуцеру выхода. Одновременно жидкость через калиброванное отверстие в диафрагме поступает в полость между поршнем и пробкой, и поршень, являющийся чувствительной мембраной, передвигается к золотнику до тех пор, пока давление по обе стороны поршня не станет одинаковым по величине. При этом поршень не дойдет до крайнего положения и не перекроет радиальные отверстия в гильзе.
Рис. 8.11. Дозатор ГА-172-00-2:
а — прямой ход дозатора (жидкость поступает к потребителю); б — конец прямого хода; в — обратный ход; 1 — корпус; 2 — упор; 3 — гильза; 4, 8 — пружины; 5 — золотник; 6 — уплотнительное кольцо; 7 — обратный клапан; 9 — поршень; 10 — заглушка; 11 — седло; 12 — диафрагма; 13 — пробка; 14 — переходник штуцера входа.
В случае появления негерметичности в магистрали после дозатора наступает падение давления в полости между поршнем и золотником, и поршень перемещается, вызывая закрытие радиальных отверстий в гильзе и предотвращение тем самым утечки жидкости из системы.
При сообщении штуцера входа со сливом через электромагнитный кран ГА-192 золотник под действием своей пружины передвигается, толкая поршень в направлении штуцера входа. Жидкость из полости между поршнем и заглушкой вытесняется через калиброванное отверстие в диафрагме, чем и обеспечивается плавность перемещения поршня и золотника. В конце хода золотника открывается под действием давления жидкости обратный клапан, и жидкость сливается от потребителя, затем обратный клапан закрывается.
Перекрывные краны 630600 закрывают магистрали от баков ОГС и ДГС и бортовым клапанам всасывания при работе ГС в полете, предотвращая утечку жидкости из баков при негерметичности указанных магистралей.Основными элементами крана являются корпус, тарельчатый клапан, рукоятка, ось, рычажная пружина детали уплотнения. Краны устанавливаются в редукторном отсеке слева у шпангоута № 12 на специальных кронштейнах.
Обратный клапан ОК-10К (рис.8.12) обеспечивает пропускание рабочей жидкости в заданном направлении и закрывает магистраль при обратном движении жидкости. В состав клапана входят корпус 1, поршень 2, пружина 3, штуцер с уплотнительным кольцом 4.
Рис.8.12 Обратный клапан ОК-10А
Бортовые клапаны всасывания и нагнетания ОГС и ДГС используются для подключения к ГС вертолета наземной гидроустановки для проверки работоспособности ГС без запуска двигателей, клапаны всасывания -дополнительно для слива жидкости из баков, а также заправки закрытым способом от наземной гидроустановки.
Рис.8.13. Клапан бортовой панели:
1— штуцер; 2,6— резиновые уплотнительные кольца; 3— пружина;
4— клапан; 5— корпус; 7— заглушка; 8—цепочка
Клапаны нагнетания и слива (рис.8.13) аналогичны по конструкции, отличаясь тем, что диаметральные размеры клапанов всасывания больше, чем клапанов нагнетания. Составными частями клапана являются корпус, штуцер трубопровода гидросистемы, плунжерный клапан с пружиной, заглушка с цепочкой, детали уплотнения.
Цилиндр управления фрикционом ручки „шаг-газ" выполнен в виде расточки в стальной оси левой ручки „шаг-газ", в которой установлен поршень с уплотнительными кольцами. При подаче жидкости в полость цилиндра со стороны штуцера входа поршень смещается в противоположную сторону, воздействует на промежуточный плунжер, передвигая нажимную тарелку, фрикционный пакет расстопоривается, и ручку можно перемещать. В случае выключения крана ГА-192 жидкость сливается из цилиндра, а пружины прижимают тарелку к фрикционному пакету, который затормаживается, и ручка „шаг-газ" фиксируется.
Гидравлический упор обеспечивает загрузку на земле ручки циклического шага дополнительным усилием в (120±30) Н [(12±3) кгс] при отклонении ее назад за пределы, соответствующие углу наклона тарелки автомата перекоса назад 2о±12' во избежание касания лопастями НВ хвостовой балки при снижении частоты вращения НВ при посадке. Составные части: корпус со штуцером подвода, поршень со штоком и винтовым упором, букса, детали уплотнения. Цилиндр гидроупора крепится двумя болтами к специальному кронштейну на шпангоуте № 5Н под верхней угловой качалкой продольного управления, на которой устанавливается упорный ролик.
Коллекторы, состоящие из стальной трубы и штуцеров, имеют осевой штуцер для подсоединения трубопровода или шланга и заглушку, а также радиальные штуцера для подсоединения гибких шлангов от штуцеров на головках гидроусилителей.
Трубопроводы гидросистемы магистралей нагнетания выполнены из бесшовных труб из стали Х19Н9Т, а на остальных участках - из труб алюминиевого сплава АМГ2М. Трубопроводы имеют ниппельные соединения и крепятся к гидропанели, другим элементам конструкции типовыми колодками с резиновыми прокладками. На трубопроводы наносится маркировка, определяющая назначение трубопровода.
Трубопроводы ОГС имеют маркировку: магистрали нагнетания - черный широкий и голубой узкий пояски; всасывания - черный широкий; дренажа - черные широкий и узкий пояски. Трубопроводы ДГС имеют пояски: магистрали нагнетания - черный широкий, узкие желтый и голубой; всасывания - черный широкий и узкий желтый; дренаж - черный широкий, узкие желтый и голубой.
Дата добавления: 2021-06-02; просмотров: 6031; Мы поможем в написании вашей работы! |
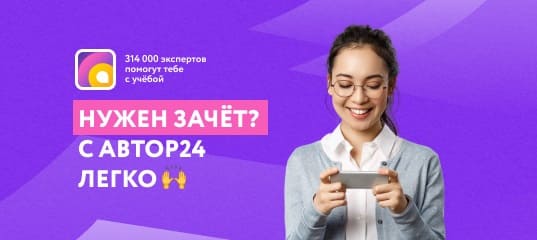
Мы поможем в написании ваших работ!