Существующие методы среднего ремонта колесных пар вагонов
В ремонтной практике различают следующие основные методы ремонта вагонов: стационарный и поточный.
При стационарном методе вагоны от начала до конца ремонта находятся на одних и тех же позициях. На каждой из позиций производится полный комплекс работ по ремонту вагонов. Все ремонтные позиции оснащаются самостоятельным комплексом технологической оснастки. Большое число выполняемых технологических операций и ограниченная производственная площадь, отводимая под ремонтную позицию, не позволяют в широких мас
Изм. |
Лист |
№ докум. |
Подпись |
Дата |
Лист |
КП.ТВиРВ.МВ-41.2017.15 |
При этом методе ремонта особое значение имеет график работы, так как значительная плотность работ (одновременно на вагоне работает максимально возможное количество рабочих) при ограниченном времени на их выполнение требует строжайшего соблюдения технологической дисциплины. Работы по ремонту осуществляют специализированные и комплексные бригады рабочих, которые последовательно переходят с вагона на вагон. Это также требует затрат дополнительного времени на ремонт.
Поточный метод характеризуется разделением комплекса операций, закрепленных за отдельными рабочими, позициями, размещенными последовательно в соответствии с технологическим процессом.
|
|
Ремонтируемый объект постепенно перемещается с одной позиции на другую. Значительное сокращение количества технологических операций, выполняемых на каждой позиции, создает возможность внедрения высокопроизводительной специализированной стационарной технологической оснастки и существенного повышения производительности труда. В зависимости от типа вагоносборочного участка вагоны могут перемещаться в процессе ремонта в одном направлении или П-образно (при вагоносборочном цехе тупикового типа). На каждой позиции могут находиться один или несколько вагонов в зависимости от принятой технологии ремонта. Совокупность рабочих мест, расположенных в последовательности выполнения операции технологического процесса и предназначенных для производства закрепленных за ними операций, образуют поточную линию. Поточный метод нашел широкое применение не только при ремонте вагонов, но и при ремонте узлов и деталей, например, поточно-конвейерная линия ремонта тележек, колесных пар, букс, автосцепок, тормозных приборов и так далее.
|
|
Изм.
Лист
№ докум.
Подпись
Дата
Лист
3 РАЗРАБОТКА ТЕХНОЛОГИЧЕСКОГО ПРОЦЕССА Изготовления устроуства для контроля прочности на сдвиг и распрессовки колесных пар. Разработка технологической оснастки КП.ТВиРВ.МВ-41.2017.15
Выбор оборудования для реализации проектируемого технологического процесса. Разработка технологической оснастки
Устройство для контроля прочности на сдвиг и распрессовки колец подшипников колесных пар
Рисунок 3.1 – Устройство для контроля прочности на сдвиг и распрессовки колец подшипников колесных пар
Тензометрический измерительный элемент 1 с тензорезисторами 2 смонтирован концентрично относительно корпуса 3 рабочего гидроцилиндра и прижимается к упорному фланцу 4 последнего нажимной плитой 5 с тяговым диском 6 и болтами 7 скрепления измерительного блока. Поршень-шток 8 снабжен кольцевыми уплотнениями 9 в своей донной части 10 и резьбовой частью 11 для соосного скрепления с шейкой оси 12 с напрессованными на ней кольцами 13 и 14 переднего и заднего подшипников, на которых закрепляют поочередно клеммовый разрезной зажим 15 с элементами продольного скрепления (тягами) 16. Защитный кожух 17 предназначен для предохранения измерительного моста тензометрического элемента 1. Штуцер 18 служит для подключения к сдвигающей полости рабочего гидроцилиндра гибкого трубопровода высокого давления от масляного насоса (на чертеже условно не показан).
|
|
Изм. |
Лист |
№ докум. |
Подпись |
Дата |
Лист |
КП.ТВиРВ.МВ-41.2017.15 |
масла через штуцер 18 в полость сдвига над донной частью 10 поршень - штока осуществляют нагружение контролируемого кольца 13 нормированным аксиальным сдвигающим усилием относительно шейки оси, передаваемым на кольцо 13 через месдозу. Увеличивают аксиальную сдвигающую нагрузку до нормативного значения Рс1, установленного требованиями ТНПА, фиксируя ее по показаниям приборов тензометрического контроля (на
чертеже условно не показаны), и проверяют наличие смещения по шкале индикатора часового типа. При отсутствии смещения (стрелка индикатора не отклоняется от начального положения) контролируемое соединение признается годным к эксплуатации и не подлежит браковке. В противном случае производят механическую распрессовку забракованного кольца 13. Для этого снимают индикатор часового типа (на чертеже условно не показан) с поршень-штока 8 рабочего гидроцилиндра и, увеличивая подачу масла под давлением через штуцер 18, перемещают кольцо 13 на свободное место поршень-штока перед упорным фланцем 4 корпуса гидроцилиндра. Проверку прочности напрессовки кольца 14 заднего подшипника выполняют аналогично, переместив на буртик его разъемный (разрезной) клеммовый зажим 15. В этом случае величина контрольного аксиального сдвигающего усилия определяется по формуле:
|
|
где - допустимое по требованиям ТНПА значение величины аксиальной сдвигающей нагрузки для кольца 14 заднего подшипника.
При наличии признаков сдвига (по индикатору часового типа) выполняют механическую распрессовку колец 13, 14 или поочередно, или совместно при увеличении давления масла в рабочем гидроцилиндре.
Эффективность предложенного устройства заключается в использовании более эффективного контроля прочности на сдвиг колец роликовых подшипников буксовых узлов колесных пар вагонов по сравнению с известными устройствами, применяемыми для технической диагностики напрессовок (проверка на проворачивание кольца на шейке оси, ультразвуковой и виброакустический контроль), в обеспечении возможности распрессовок по
Изм. |
Лист |
№ докум. |
Подпись |
Дата |
Лист |
КП.ТВиРВ.МВ-41.2017.15 |
Для изготовления устройства для контроля прочности на сдвиг и распрессовки колец подшипников колесных пар используется токарно-винторезный станов модели 1К62 и радиально - сверлильный станок модели 2А554. Технические характеристики танков представлены в таблице 3.1 и 3.2 соответственно.
Таблица 3.1 – Технические характеристики токарно-винторезного станка 1К62
Наименование параметра | 1К62 | ||||||||
Основные параметры станка | |||||||||
Класс точности по ГОСТ 8-82 | Н | ||||||||
Наибольший диаметр заготовки над станиной, мм | 400 | ||||||||
Наибольший диаметр заготовки над суппортом, мм | 220 | ||||||||
Наибольшая длина заготовки (РМЦ), мм | 750, 1000, 1500 | ||||||||
Наибольшая масса заготовки в патроне, кг | 500 | ||||||||
Наибольшая масса заготовки в центрах, кг | 1500 | ||||||||
Шпиндель | |||||||||
Диаметр сквозного отверстия в шпинделе, мм | 47 | ||||||||
Наибольший диаметр прутка, мм | 45 | ||||||||
Число ступеней частот прямого вращения шпинделя | 24 | ||||||||
Частота прямого вращения шпинделя, об/мин | 12,5..2000 | ||||||||
Число ступеней частот обратного вращения шпинделя | 12 | ||||||||
Частота обратного вращения шпинделя, об/мин | 19..2420 | ||||||||
Размер внутреннего конуса в шпинделе, М | Морзе 6 | ||||||||
Конец шпинделя по ГОСТ 12593-72 | 6К | ||||||||
Подачи | |||||||||
Наибольшая длина хода каретки, мм | 640, 930, 1330 | ||||||||
Наибольший поперечный ход суппорта, мм | 250 | ||||||||
Наибольший ход верхнего суппорта, мм | 140 | ||||||||
Число ступеней продольных подач | 49 | ||||||||
Пределы рабочих подач продольных, мм/об | 0,07..4,16 | ||||||||
Число ступеней поперечных подач | 49 | ||||||||
Пределы рабочих подач поперечных, мм/об | 0,035..2,08 | ||||||||
Скорость быстрых перемещений суппорта, продольных, м/мин | 3,4 | ||||||||
Скорость быстрых перемещений суппорта, поперечных, м/мин | 1,7 | ||||||||
Количество нарезаемых резьб метрических | 44 | ||||||||
Пределы шагов нарезаемых резьб метрических, мм | 1..192 | ||||||||
Количество нарезаемых резьб дюймовых | 38 | ||||||||
Пределы шагов нарезаемых резьб дюймовых | 24..2 | ||||||||
Количество нарезаемых резьб модульных | 20 | ||||||||
Пределы шагов нарезаемых резьб модульных | 0,5..48 | ||||||||
Количество нарезаемых резьб питчевых | 37 | ||||||||
Пределы шагов нарезаемых резьб питчевых | 96..1 | ||||||||
Окончание таблицы 3.1 | |||||||||
| |||||||||
Количество электродвигателей на станке | 4 | ||||||||
Мощность электродвигателя главного привода, кВт | 10 | ||||||||
Тип электродвигателя главного привода | АО2-52-4Ф | ||||||||
Мощность электродвигателя быстрых перемещений, кВт | 0,8 | ||||||||
Тип электродвигателя быстрых перемещений | АОЛ2-12-4Ф | ||||||||
Мощность электродвигателя гидростанции, кВт | 1,1 | ||||||||
Тип электродвигателя гидростанции | АОЛ2-22-6Ф | ||||||||
Мощность электродвигателя насоса охлаждения, кВт | 0,125 | ||||||||
Насос охлаждения (помпа) | ПА-22 | ||||||||
Габариты и масса станка | |||||||||
Габариты станка (длина ширина высота) (РМЦ = 1000), мм | 2812 х 1166 х 1324 | ||||||||
Масса станка (РМЦ = 1000), кг | 2140 |
Таблица 3.2 – Технические характеристики радиально-сверлильного станка 2А554
Основные параметры | 2A554 | |
Наибольший диаметр сверления,мм: | ||
в стали | 50 | |
в чугуне | 63 | |
нарезаемой резьбы: | ||
в стали | М52х5 | |
в чугуне | М54х4 | |
Расстояние от оси шпинделя до направляющих колоны,мм: | ||
наибольшее | 1600 | |
наименьшее | 375 | |
Перемещение шпинделя,мм: | ||
наибольшее | 400 | |
на один оборот лимба | 120 | |
на одно деления лимба | 1 | |
Наибольшее перемещение сверлильной головки по колонне,мм | 1225 | |
Наибольший угол поворота рукава вокруг оси колонны,град | 360 | |
Скорость вертикального перемещения рукава,м/с | 0,023 | |
Пределы частоты вращения шпинделя, об/мин | 18...2000 | |
Наибольший крутящий момент на шпинделе,Нм | 7100 | |
Габаритные размеры станка,мм: | ||
длина | 2850 | |
ширина | 1030 | |
высота | 3430 | |
Масса станка,кг | 4700 |
Изм.
Лист
№ докум.
Подпись
Дата
Лист
3.2 Разработка технологического процесса. Нормирование операций КП.ТВиРВ.МВ-41.2017.15
Для изготовления детали 1 используем токарно-винторезный станок 1К62 и радиально-сверлильный станок 2А554.
На первом этапе изготовления детали 1 необходимо:
1) Установить заготовку ⌀130 мм. в патрон токарно-винторезного станка;
2) Подрезным резцом обработать поверхность 1;
На каждую операцию устанавливается определяется основное мемеханическое время. Основное механическое время – это время, непосредственно затраченное на процесс резания, подсчитывается для каждого перехода. Для точения и сверления основное механическое время будет определяться по формуле:
где L – расчетная длина обработки;
i – число проходов;
n – частота вращения шпинделя, об/мин;
S – подача на оборот шпинделя.
3) Проходным резцом обработать поверхность 2 до ⌀87 мм;
4) Подрезным резцом обработать поверхность 3;
5) Расточным резцом проточить канавки 4 глубиной 9 мм;
6) Переустановить заготовку обратной стороной.
На рисунке 3.1 представлено расположение заготовки в патроне токарно-винторезного станка и условное обозначение поверхностей для первого этапа изготовления детали 1.
Изм. |
Лист |
№ докум. |
Подпись |
Дата |
Лист |
КП.ТВиРВ.МВ-41.2017.15 |
На втором этапе изготовления детали 1 необходимо:
7) Подрезным резцом обработать поверхность 5;
8) Проходным резцом обработать поверхность 6;
9) Расточным резцом обработать поверхность 7;
10) Проходным резцом обработать поверхность 8;
11) Резьбовым резцом нарезать на поверхности 7 резьбу шагом 4 мм;
12) Извлечь заготовку из патрона токарно-винторезного станка и установить в станину радиально-сверлильного станка.
На рисунке 3.2 представлено расположение заготовки в патроне токарно-винторезного станка и условное обозначение поверхностей для второго этапа изготовления детали 1.
Изм. |
Лист |
№ докум. |
Подпись |
Дата |
Лист |
КП.ТВиРВ.МВ-41.2017.15 |

Рисунок 3.2 – Расположение заготовки в патроне токарно-винторезного станка и условное обозначение поверхностей для второго этапа изготовления детали 1
На третьем этапе изготовления детали 1 необходимо:
13) При помощи керна и молотка нанести метку для отверстия 9, просверлить отверстие 9 ⌀50 мм;
14) Переустановить заготовку 1 обратной стороной.
На рисунке 3.3 представлено расположение заготовки в станине радиально-сверлильного станка и условное обозначение поверхностей для третьего этапа изготовления детали 1.
Рисунок 3.3 – Расположение заготовки в станине радиально-сверлильного станка и условное обозначение поверхностей для третьего этапа изготовления детали 1
На четвертом этапе изготовления детали 1 необходимо:
15) При помощи керна и молотка нанести метку для отверстия 10, просверлить отверстие 10 ⌀6 мм, глубиной 4 мм;
16) Извлечь заготовку 1 из станины радиально-сверлильного станка и произвести зачистку шлифовальной шкуркой по металлу.
На рисунке 3.3 представлено расположение заготовки в станине радиально-сверлильного станка и условное обозначение поверхностей для четвертого этапа изготовления детали 1.
Рисунок 3.4 – Расположение заготовки в станине радиально-сверлильного станка и условное обозначение поверхностей для четвертого этапа изготовления детали 1
Аналогично произведем расчет деталей 2–7, приведенные на листе №1 графической части.
Дата добавления: 2021-06-02; просмотров: 110; Мы поможем в написании вашей работы! |
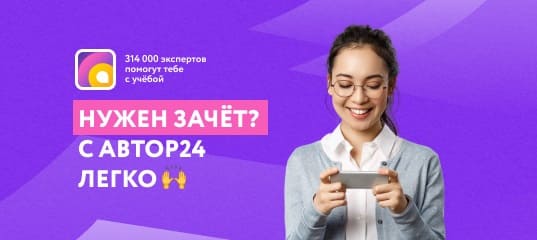
Мы поможем в написании ваших работ!