Правила техники безопасности требуют:
до начала работы
- подробно ознакомиться с содержанием работы и порядком ее проведения на лабораторном оборудовании: проверить закрепление всех элементов лаботорной установки и возможность их безопасного функционирования;
в процессе работы
- при обнаружении каких-либо неисправностей срочно сообщить об этом преподавателю:
после окончаний работы
- лабораторная установка должна быть приведена в первоначальное состояние.
Запрещается
- приступать к выполнению работы бeз разрешения преподавателя;
- разбирать опытные образцы приборов и лабораторных установок.
2 Лабораторная работа № 1 « Рабочие процессы и анализ конструкции сухих фрикционных сцеплений»
Цель работы: научиться экспериментально определять влияние износа фрикционных накладок на коэффициент запаса сцепления.
Основные положения
Сцепление автомобиля - это механизм трансмиссии, передающий крутящий момент двигателя и позволяющий кратковременно отсоединять двигатель от трансмиссии и вновь плавно их соединять.
По характеру передачи крутящего момента сцепления разделяются на фрикционные и электромагнитные. Работа фрикционного сцепления основана на использовании сил трения, действующих в зоне контакта ведущих и ведомых частей. Электромагнитные сцепления передают момент за счёт сил магнитного притяжения частиц ферромагнитного наполнителя, расположенного между ведомыми и ведущими частями сцепления.
|
|
На современных автомобилях преимущественное распространение получили фрикционные сцепления, классификация которых приведена в литературе [1].
В настоящее время применяют два типа фрикционных сцеплений:
— с периферийным расположением пружин;
— с диафрагменной пружиной.
Схема сцепления с периферийными пружинами, которую называют также рычажной, показана на рис. 2.1. В состав сцепления входят:
— ведущая часть: маховик 6, кожух сцепления 14, нажимной (ведущий) диск 11 и устройство 7 для передачи момента с маховика на нажимной диск;
— ведомая часть: ведомый диск 5, гаситель 3 крутильных колебаний (демпфер), ступица 26 и вал 27, который в большинстве конструкций является первичным валом коробки передач;
— нажимное устройство: цилиндрические витые пружины 24, расположенные периферийно на одной или нескольких окружностях;
— механизм выключения: отжимные рычаги 12, вилки 13, подшипники в соединениях рычагов с нажимным диском и вилками, детали крепления вилок к кожуху;
— привод сцепления: педаль 19, гидравлические цилиндры 20 и 23, вилка 22, муфта 16 выключения с нажимным подшипником 15 (при механическом приводе педаль и вилка соединяются тягой 21).
|
|
Рис 2.1. Схема рычажного сцепления
а) сцепление включено, б) сцепление выключено
С целью обеспечения соосного расположения коленчатого вала 1 и первичного вала 27 блок двигателя 8, картеры сцепления 10 и коробки передач 17 фиксируются при сборке по базовым поверхностям А и Б. Базовыми поверхностями А служат штифты 9 на блоке двигателя и отверстия во фланце картера сцепления. Базовыми поверхностями Б являются центральное отверстие в картере сцепления и наружная поверхность фланца крышки 18 подшипника первичного вала.
Кожух сцепления в сборке крепится к маховику специальными болтами с цилиндрической поверхностью, не допускающими смещения кожуха и, следовательно, нарушения балансировки при вращении с высокой скоростью.
Сцепление во включенном состоянии является уравновешенным механизмом, который не передаёт на коленчатый вал осевого усилия нажимных пружин. При выключении сцепления на коленчатый вал действует осевое усилие нажимных пружин.
Диафрагменное сцепление (рис. 2.2) отличается от рычажного нажимным устройством и механизмом выключения. Нажимное устройство создаётся центральной диафрагменной (тарельчатой) пружиной 6. Она имеет в свободном состоянии форму усечённого конуса, состоящего из сплошного кольца с радиально расположенными лепестками, которые выполняют функции рычагов механизма выключения. В механизме выключения отсутствуют вилки рычагов, подшипники и детали крепления вилок.
|
|
Рис. 2.2. Схемы диафрагменного сцепления
а) сцеление включено, б) сцепление выключено
Диафрагменная пружина с помощью двух проволочных опорных колец 7 и заклёпок 8 крепится к кожуху 3. При креплении кожуха к маховику 1 наружная кромка пружины опирается на кольцевой выступ нажимного диска 4, пружина распрямляется и принимает форму диска. Силы упругости, вызванные деформацией пружины, прижимают нажимной диск к ведомому 2.
При включении сцепления выжимной подшипник через упорный фланец давит на лепестки. Пружина выгибается в обратную сторону и через фиксаторы 5 отводит нажимной диск от ведомого.
В работе сцепления различают следующие режимы: 1) сцепление включено; 2) сцепление выключено; 3) включение сцепления.
Сцепление включено
Автомобильные сцепления относятся к постоянно включенным (замкнутым), у которых основным рабочим процессом является передача крутящего момента от двигателя к трансмиссии. Момент с маховика и нажимного диска за счёт сил трения передаётся на фрикционные накладки ведомого диска и далее через гаситель крутильных колебаний на ступицу и вал. Силы трения создаются усилием нажимных пружин, установленных с натягом (сжатием) между кожухом и нажимным диском.
|
|
Момент трения Мс сцепления:
, (2.1)
где Т = m × RS — результирующая тангенциальная сила трения, Н;
RS — суммарное усилие нажимных пружин на поверхности трения, Н;
m — коэффициент трения;
Rср — средний радиус поверхности трения, м;
i — число поверхностей трения.
Момент трения в процессе эксплуатации снижается из-за износа фрикционных накладок, уменьшения коэффициента трения и изменения упругих свойств пружин. С целью обеспечения надёжной передачи момента двигателя сцепления проектируются так, чтобы момент трения превышал максимальный момент Мсmax двигателя:
, (2.2)
где b — коэффициент запаса сцепления.
Момент трения может изменяться примерно на 8—10 % вследствие осадки пружин и на 15 % — вследствие износа накладок (в сцеплениях с цилиндрическими пружинами). Момент трения может уменьшаться и при неполном включении сцепления, когда отсутствует зазор d (рис. 2.1) между отжимными рычагами и выжимным подшипником и нажимное усилие пружин не полностью передаётся на поверхности трения.
При включенном сцеплении в трансмиссии могут возникать динамические нагрузки из-за циклического изменения момента двигателя даже при работе на установившихся режимах, изменения сил сопротивления движению автомобиля и при интенсивном торможении. Значительные центробежные силы могут действовать при неудовлетворительной балансировке элементов сцепления.
Сцепление выключено
Выключение сцепления — разъединение поверхностей трения, передающих момент, производится при переключении передач, торможении автомобиля и запуске двигателя. При выключении сцепления усилие водителя передаётся от педали 19 (рис. 2.1) через детали привода на вилку 22 и далее на муфту 16, которая скользит по переднему концу крышки 18 подшипника. Выбирается зазор между отжимными рычагами и выжимным подшипником, рычаги поворачиваются в вилках 13 и отводят нажимной диск, сжимая нажимные пружины. Между маховиком, нажимным диском и фрикционными накладками образуются зазоры.
Водителю при движении автомобиля приходится часто пользоваться сцеплением. Поэтому и усилие на педали, и ход педали при выключении сцепления должны быть небольшими, чтобы водитель не утомлялся.
После выключения сцепления ведомый диск, первичный и промежуточный валы коробки передач продолжают вращаться. В коробке передач для безударного переключения шестерен устанавливаются синхронизаторы, которые за счёт пробуксовывания увеличивают или снижают скорость вращения ведомых частей сцепления и промежуточного вала с целью выравнивания угловых скоростей соединяемых деталей. Работа буксования и, следовательно, износ фрикционных элементов синхронизатора будут тем больше, чем больше момент инерции ведомых частей сцепления. Момент инерции ведомых частей увеличивается, если сцепление нечисто выключено — отсутствует зазор между маховиком, нажимным диском и ведомым диском. Для уменьшения износа накладок ведомого диска сцепление должно выключаться быстро и чисто.
Включение сцепления
Включение сцепления происходит при снятии усилия водителя с педали. Нажимной диск под действием нажимных пружин перемещается к маховику и прижимает к нему ведомый диск. Муфта включения, рычаги и педаль возвращаются в исходное положение возвратными пружинами. При включении сцепления момент трения изменяется от Мс=0 до Мс=max. Процесс включения при трогании с места можно разделить на два этапа.
Первый этап — с момента соприкосновения поверхностей трения (Мс = 0) до начала движения автомобиля, когда момент Мс становится равным моменту М y сопротивления движению автомобиля. На этом этапе вращающийся маховик и нажимной диск скользят по неподвижному ведомому диску.
Второй этап — с начала движения автомобиля до выравнивания угловых скоростей ведущих и ведомых частей w е = w с. При буксовании сцепления во время включения выделяется большое количество тепла, которое может вызвать чрезмерный нагрев дисков, пружин и накладок.
Включение может быть плавным и резким. Кроме того, оно может быть неполным, в том случае, когда сцепление работает продолжительное время с пробуксовыванием, например, при маневрировании автомобиля.
При плавном включении сцепления ускорения автомобиля во время трогания с места не превышает 3—4 м/с2, нет отрицательных воздействий на пассажиров и груз, динамические нагрузки в трансмиссии незначительные.
При резком включении сцепление к маховику двигателя, вращающемуся с высокой скоростью, подводится большой момент сопротивления неподвижного автомобиля. Скорость вращения маховика быстро снижается и к крутящему моменту двигателя добавляется инерционный момент массы маховика. Момент трения сцепления при резком включении также увеличивается за счёт добавления к нажимному усилию пружин силы инерции нажимного диска, скорость которого быстро снижается во время прижатия к ведомому диску. Через трансмиссию может кратковременно передаваться момент, превышающий в 2—3 раза максимальный момент двигателя. Резкое включение сцепления является ненормальным, но в некоторых случаях необходимым.
Анализ конструкций сцеплений
Анализ и оценка конструкций сцеплений в целом и их отдельных элементов должны производиться на основании предъявляемых к ним требований.
Конструкции сцеплений должны обеспечивать ряд специфических требований:
— во включенном состоянии передавать крутящий момент двигателя без пробуксовывания, предохранять детали трансмиссии от перегрузок, не вызывать осевых усилий на коленчатый вал двигателя, надёжно отводить тепло, выделяющееся во время буксования при включении от поверхностей трения;
— чистое, лёгкое и удобное выключение, малый момент инерции ведомых частей;
— плавное включение;
— небольшие затраты на производство и в эксплуатации при высокой надёжности и долговечности.
Нажимные пружины
Стабильность момента трения и, следовательно, надёжная передача момента двигателя в значительной степени зависят от типа нажимных пружин. На рис. 2.3 для сравнительной оценки приведены упругие характеристики диафрагменной (линия 1) и цилиндрических пружин (линии 2 и 3) различной жесткости. Все пружины создают одинаковое усилие Рвкл при включённом сцеплении и сжатии соответственно на величины f1, f2 и f3.
Износ фрикционных накладок на величину D f смоделирован на рисунке уменьшением сжатия пружин на ту же величину. Нажимное усилие диафрагменной пружины при износе накладок практически не изменяется. У цилиндрических пружин нажимное усилие при одинаковом износе накладок уменьшается тем больше, чем больше жёсткость пружины.
При выключении сцепления увеличивается сжатие пружин. У диафрагменной пружины при выключении сцепления (участок А — А2) усилие пружины уменьшается и, следовательно, снижается усилие водителя. В сцеплении с цилиндрическими пружинами усилие водителя при выключении возрастает тем больше, чем больше жёсткость пружин. Однако пружины малой жёсткости имеют большую длину, что приводит к увеличению размера сцепления в осевом направлении.
Ещё недавно применение диафрагменных пружин сдерживалось сложностями их изготовления: узкие температурные допуски на закалку и отпуск, затруднена вырубка узких прорезей между лепестками, жёсткие требования на толщину заготовки. Однако в настоящее время эти вопросы решены и диафрагменные сцепления получают все более широкое применение.
Рис. 2.3. Упругие характеристики пружин
Нажимные диски
Обычно изготовляются из серого чугуна, обладающего хорошими фрикционными и противозадирными свойствами при работе с фрикционными накладками. Диски должны быть достаточно жесткими для обеспечения равномерного давления на ведомый диск и уменьшения коробления при нагреве.
Для передачи крутящего момента с маховика на нажимной (ведущий) диск применяют специальные устройства (рис. 2.4):
а) пружинные пластины между диском и кожухом;
б) выступы на диске и окна в кожухе;
в) шипы на диске и пазы в маховике.
Эти устройства одновременно фиксируют нажимные диски в окружном и радиальном направлении при включении сцепления.
В устройствах б) и в) при включении сцепления возникает трение между сопряжёнными деталями, уменьшающее нажимное усилие на поверхностях трения, происходит износ опорных поверхностей.
Устройства должны быть равномерно расположены на окружности диска, чтобы сохранялась балансировка и не происходил перекос дисков при включении сцепления.
Ведомые диски
Конструкция ведомых дисков должна обеспечивать плавное включение сцепления и гашение крутильных колебаний. Фрикционные накладки должны иметь высокий малоизменяющийся коэффициент трения, особенно при нагреве.
Рис. 2.4. Устройства для передачи крутящего момента
1 – Нажимной диск; 2 – пластина; 3- кожух; 4 – ведомый диск; 5 - маховик
Плавность включения обеспечивается применением упругих в осевом направлении ведомых дисков. Упругость достигается размещением между фрикционными накладками элементов типа пластинчатых пружин, которые могут быть выполнены непосредственно в диске или в виде специальных деталей, приклёпанных к диску. В первом случае на периферийной части диска делают ^-образные прорези. Образующиеся секторы через один отгибают в разные стороны и к ним приклёпывают фрикционные накладки. Такая конструкция затрудняет получение секторов одинаковой жесткости. Во втором варианте к диску приклёпываются тонкие стальные волнистые секторы, к которым также приклёпывают накладки. В обоих вариантах в свободном состоянии между фрикционными накладками имеется зазор, равный изгибу пружинных элементов.
Упругий ведомый диск позволяет увеличить ход педали, при котором происходит включение сцепления, и тем самым обеспечивать плавное нарастание момента трения. В двухдисковых сцеплениях упругие диски не применяют из-за существенного увеличения хода педали при включении сцепления.
Фрикционные накладки изготовляются из асбофрикционного материала, состоящего из асбеста, металлических и минеральных наполнителей и связующего вещества. Накладки должны обладать необходимой прочностью на разрыв и иметь хорошую стабильность коэффициента трения.
В трансмиссии при передаче крутящего момента действуют крутильные колебания, вызываемые, в основном, циклическим изменением крутящего момента двигателя даже при работе в установившемся режиме. Для снижения крутильных колебаний в ведомом диске устанавливают гаситель крутильных колебаний.
Гаситель представляет собой упругую муфту, соединяющую ведомый диск со ступицей сцепления. Наибольшее распространение получили гасители с цилиндрическими тангенциально-расположенными пружинами и фрикционными элементами. Крутящий момент передаётся от ведомого диска через пружины на фланец ступицы. Колебания момента заставляют пружины попеременно сжиматься и разжиматься, и диск совершает перемещения относительно фланца ступицы. При этом на фрикционном элементе гасителя, расположенном между диском и фланцем ступицы, возникает момент трения.
Упругий элемент (пружины) гасителя изменяет собственные частоты трансмиссии и предназначен для вывода резонансных режимов из зоны эксплуатационных скоростей. В реальных конструкциях трансмиссий осуществлять это полностью не удаётся, и гасители только снижают минимальные величины инерционных моментов при возникновении резонансных режимов.
Фрикционный элемент гасителя служит для уменьшения амплитуды крутильных колебаний (размаха крутящего момента). Размахи крутящего момента могут достигать величины, превосходящей максимальный момент двигателя более чем в 1,3 раза. Для эффективного действия гасителя на фрикционный элемент должно действовать постоянное нажимное усилие, создаваемое специальными пружинами.
Угловое перемещение ведомого диска относительно фланца ступицы ограничивается специальными упорами или полным сжатием пружин гасителя. Момент, при котором происходит максимальная деформация пружин гасителя, называется моментом замыкания.
Рычаги выключения сцепления
Рычаги, шарнирно соединённые с нажимным диском и кожухом, служат для принудительного отвода диска при выключении сцепления. Диск во время выключения движется поступательно вдоль оси сцепления. Наружный конец рычага должен поворачиваться относительно опоры на кожухе, функцию которого выполняет вилка. Для компенсации кинематического несоответствия движения диска и конца рычага опора последнего на кожухе должна иметь возможность перемещаться в радиальном направлении. Чаще всего это достигается шарнирным креплением вилки к кожуху, которое позволяет вилке качаться относительно кожуха. Рычаги соединяются с диском и вилкой с помощью игольчатых подшипников. Вилка опирается на кожух гайкой с шаровой поверхностью. Гайка прижимается к кожуху конусной витой или пластинчатой пружиной. Число рычагов принимается кратным числу нажимных пружин, чтобы исключить перекос диска при выключении сцепления.
Тепловой режим
При буксовании сцепления на поверхностях трения выделяется тепло, повышается температура фрикционных накладок, снижается коэффициент трения и уменьшается момент трения. При чрезмерном нагреве возможно коробление ведомого и нажимного дисков, появление трещин на нажимном диске и снижение упругости нажимных пружин.
Для быстрого отвода тепла нажимные диски изготовляются массивными. Кожух сцепления делается ажурным для интенсивной циркуляции воздуха, в картере имеются вентиляционные лаки. Между нажимным диском и пружинами устанавливаются теплоизолирующие шайбы. В двухдисковых сцеплениях внутренний нажимной (промежуточный) диск с обеих сторон закрыт ведомыми дисками и плохо охлаждается. Для охлаждения диска в нём иногда делают радиальные воздушные каналы.
Привод сцепления
Приводы сцепления бывают механические и гидравлические. Механический привод имеет более низкий КПД, больший свободный ход педали из-за зазоров в шарнирных соединениях и расположения элементов привода на перемещающихся друг относительно друга кабине и двигателе, требуется специальное уплотнение пола кабины. Чем дальше расположено место водителя от сцепления, тем сложнее его привод.
Гидравлический привод имеет более высокий КПД, обладает большей жесткостью, хорошо приспособлен для дистанционного управления, проще при опрокидывающейся кабине.
Если усилие водителя при выключении сцепления превышает 200—250 Н, в привод устанавливают усилитель, который должен обладать следящим действием.
В конструкцию привода, как правило, включается устройство для регулирования зазора между отжимными рычагами и выжимным подшипником. Регулировка позволяет поддерживать зазор в процессе эксплуатации в заданных пределах и тем самым обеспечивать полное включение и чистое выключение сцепления.
Одно- и двухдисковые сцепления
При передаче больших крутящих моментов целесообразно применять двухдисковые сцепления, которые обеспечивают требуемый момент трения при меньших диаметрах ведомых дисков. Увеличение диаметра ведомого диска в однодисковом сцеплении для получения большого момента ограничивается размерами маховика и максимально допустимой окружной скоростью нажимного диска.
Однодисковые сцепления по сравнению с двухдисковыми имеют следующие преимущества:
— простота конструкции и обслуживания, меньше масса и размер в осевом направлении, дешевле в производстве;
— более стабильный момент трения, так как лучше отвод тепла от поверхностей трения;
— меньше момент инерции ведомой части;
— чистое выключение достигается без дополнительных устройств, меньше ход педали при выключении.
Рычажные и диафрагменные сцепления
На современных автомобилях применяют два типа сцеплений: рычажные с периферийным расположением пружин и диафрагменные. Первые в основном применяют на грузовых автомобилях, вторые — на легковых. По прогнозам специалистов диафрагменные сцепления в ближайшие годы получат более широкое применение и на грузовых автомобилях.
Диафрагменные сцепления по сравнению с рычажными имеют следующие преимущества:
— более стабильный момент трения;
— отсутствует сложный с большим количеством пар трения рычажный механизм выключения;
— легче в управлении благодаря отрицательной жесткости диафрагменной пружины на участке выключения сцепления;
— выше плавность включения благодаря гибкости лепестков пружины, выполняющие функции рычагов;
— хорошо балансируется и сохраняет балансировку в процессе эксплуатации;
— число деталей в 2 раза меньше;
— себестоимость изготовления примерно на 30 % ниже;
— габаритные размеры в осевом направлении меньше примерно в два раза.
Сцепление является одним из наиболее ответственных агрегатов трансмиссии, поэтому их качественную проверку проводят при дорожных и стендовых испытаниях. Исследованию подвергается как все сцепление, так и его отдельные детали: измеряют момент трения сцепления, балансировку сцепления, термостойкость фрикционных накладок, а также определяют характеристики демпфера, механизма выключения сцепления, нажимных пружин и фрикционных материалов. При определении долговечности сцепления устанавливают износостойкость фрикционных накладок и долговечности нажимных пружин, деталей механизма выключения, демпфера крутильных колебаний, ведомого диска и картера сцепления.
Порядок выполнения работы
1. Используя лабораторную установку (рис. 2.5):
— определить момент сцепления Мс;
— рассчитать коэффициент запаса сцепления b;
— построить характеристику нажимного устройства Мс = Y (f).
2. Используя плакаты, схемы, макеты, каталоги, учебные экспонаты, литературу, провести сравнительный анализ предложенных преподавателем конструкций сцеплений, выделить их основные особенности. При проведении анализа выяснить каким образом в данных конструкциях реализованы предъявляемые к ним требования.
Описание лабораторной установки и проведения работы
Оценочными параметрами сцепления являются:
— коэффициент запаса сцепления;
— усилие нажимных пружин;
— степень износа накладок.
Рис. 2.5. Схема лабораторной установки
Лабораторная установка позволяет определить момент запаса сцепления, снять характеристику нажимного устройства.
Установка включает в себя раму 1, на которой жестко закреплён маховик 2, а на нём соответственно установлено сцепление 3, вилка выключателя 4 и первичный вал 5 коробки передач.
Поворачивая первичный вал 5 с помощью динамометрического ключа 6, определяют момент начала его вращения. Величина этого момента соответствует моменту сцепления Мс. Зная максимальный момент двигателя Мсмах = 58 Н × м, определяют величину коэффициента запаса сцепления b.
Для снятия характеристики нажимного устройства поворачивают гайку управления вилкой сцепления на половину оборота, имитируя тем самым начало процесса выключения сцепления, и замеряют соответствующий новому положению Мс. И так далее через каждые пол-оборота гайки до полного выключения сцепления (Мс = 0). По полученным значениям строят характеристику Мс = Y (f).
Содержание отчёта
В отчёте должна быть отражена цель работы, представлены результаты измерений в виде таблицы, приведены полученные значения Мс, расчётное значение b и характеристика Мс = Y (f) в виде графика.
Также должны быть представлены результаты сравнительного анализа изучаемых конструкций (оценка выполнения требований, положительные и отрицательные характеристики конструктивных элементов, оценочные параметры).
Сделать выводы по результатам анализа.
Контрольные вопросы
1. Назначение сцепления и его основных деталей.
2. Требования, предъявляемые к конструкциям сцеплений.
3. Основные рабочие процессы сцеплений.
4. Обеспечение теплового режима сцепления.
5. Преимущества однодисковых сцеплений над двухдисковыми.
6. Особенности диафрагменных сцеплений.
7. Основные регулировки сцеплений.
3 Лабораторная работа №2 « ИССЛЕДОВАНИЕ РАБОЧИХ ПРОЦЕССОВ ГИДРОПРИВОДА СЦЕПЛЕНИЯ С ПНЕВМАТИЧЕСКИМ УСИЛИТЕЛЕМ»
Цель работы: научиться определять статистические характеристики следящего механизма и привода.
Общие положения
На современных грузовых автомобилях и автобусах с двигателями большой мощности широко применяется привод сцепления с пневматическим усилителем — сервопривод. Такой привод уменьшает утомляемость водителя и, следовательно, повышает безопасность движения.
Гидравлический привод имеет высокий КПД и более простую конструкцию в сравнении с механическим при опрокидывающейся кабине и большом удалении места водителя от сцепления. Как правило, грузовые автомобили и автобусы снабжаются компрессорами для питания тормозной системы, поэтому на них целесообразно применять пневматические усилители.
Усилители должны обладать следящим действием, иметь линейную статическую характеристику, стабильную в различных условиях эксплуатации, с малой петлёй гистерезиса, быть надёжным в эксплуатации. Привод должен сохранять работоспособность при неработающем усилителе.
Гидравлический привод с пневматическим усилителем состоит из следующих основных элементов (рис. 3.1): главного цилиндра 2 с педалью 3, рабочего гидравлического цилиндра 18, пневматического цилиндра 23 усилителя, следящего механизма 7, гидравлических и пневматических трубопроводов.
Рис. 3.1. Схема привода сцепления с пневматическим усилителем
Рабочие процессы усилителя
Сцепление включено.
На педали усилия водителя нет (Рп = 0), в гидроприводе давление отсутствует. В следящем механизме диафрагма 11, подвижное седло 12 и поршень 13 отжаты пружиной 10 в крайнее правое положение. Выпускной клапан 9 открыт, а соединённый с ним стержнем впускной клапан 6 закрыт пружиной 8. Полости А и Б соединены с атмосферой через подвижное седло и полость В. В цилиндре усилителя поршень 22 и соединённый с ним штоком 20 поршень 19 гидроцилиндра отведены пружиной 21 в крайнее левое положение. Усилия на штоке 17 нет. Муфта 15 отведена от нажимных рычагов 14 возвратной пружиной.
Выключение сцепления.
На педаль действует усилие Рп, которое создаёт в гидросистеме привода давление жидкости:
, (3.1)
где iп — передаточное число педали;
F1 — площадь поршня главного цилиндра.
Давление жидкости на поршень 19 вызывает на штоке 17 силу:
, (3.2)
где F2 — площадь поршня 19.
Одновременно жидкость давит на поршень 13, смещая его и диафрагму с подвижным седлом влево. Закрывается выпускной клапан 9, отсоединяя полости А и Б от атмосферы. Открывается впускной клапан, и в полости А и Б поступает сжатый воздух из ресивера 4. Давление воздуха PВ на поршень 22 создает на штоке 20 усилие QУ, которое передается на поршень 19 и далее на шток 17.
, (3.3)
где F 3 — площадь поршня 22;
Q п — сила возвратной пружины 21.
При исправном усилителе на штоке 17 действует суммарная сила:
. (3.4)
Если усилитель неисправен, то на шток действует только сила Q р, и водителю для выключения сцепления необходимо прикладывать к педали большее усилие.
Для обеспечения требуемого режима выключения сцепления сила на штоке усилителя должна быть пропорциональна усилию водителя на педали. Это обеспечивается следящим механизмом.
Рабочие процессы следящего механизма
Следящий механизм в приводе сцепления является регулятором давления воздуха прямого действия диафрагменного типа. Его назначение: регулировать давление воздуха в цилиндре 23 и, следовательно, силу Qy усилителя, в зависимости от усилия водителя на педали. Следящий механизм должен иметь линейную характеристику.
При выключении сцепления на диафрагму 11 следящего механизма действуют силы: справа сила Nr давление жидкости на поршень 13, слева сила N п пружины 10 и сила N в давления воздуха, сила трения между поршнем и цилиндром не учитывается.
Поршень начнет движение влево, когда сила Nr сравняется с силой N п пружины (впускной клапан закрыт и Pв = 0):
Nг = Pг × F4 = Nп, (3.5)
где F 4 — площадь поршня 13.
Давление Pr и, следовательно, сила Nr характеризуют начальную нечувствительность следящего механизма.
При изменении давления жидкости от Р’г до Рг, которое соответствует усилию водителя Рп, поршень 13 двигается влево, открывая впускной клапан 6. В полостях А и Б растет давление от Рв = 0 до Рв. Сила давления воздуха прогибает диафрагму вправо, вместе с ней сдвигается впускной клапан под действием пружины 8. Когда диафрагма прогнется настолько, что клапан закроется, силы, действующие на диафрагму слева и справа, будут равны.
Уравнение равновесия диаграммы в данном случае имеет следующий вид:
Рг × F 4 = N г + Pl × F 5 , (3.6)
где F 5 — активная площадь диафрагмы 11.
При равновесном положении диафрагмы оба клапана (впускной и выпускной) закрыты. Найдем значение Рв, используя выражение для силы, действующей на шток 17, и выражение для суммарной силы при исправном усилителе:
. (3.7)
Используя полученное выражение, можно построить статическую характеристику следящего механизма, приведенную на рис. 3.2. Пружина 10, неуравновешенная площадь клапана 6 и трение в механизме обуславливают начальную нечувствительность следящего механизма (участок 0 — Рг) и петлю гистерезиса. В полученном выражении для Р l неуравновешенная площадь клапана и трение не учтены.
Рис. 3.2. Статическая характеристика следящего механизма
Полученное выражение показывает, что давление воздуха в цилиндре усилителя пропорционально усилию водителя на педали. Зависимость имеет линейный характер.
С учетом полученного выражения для Рв выражение для суммарной силы будет иметь следующий вид:
. (3.8)
Данная зависимость позволяет построить статическую характеристику привода с усилителем, приведенную на рис. 3.3.
Рис. 3.3. Статическая характеристика привода с усилителем
Линия 1 характеризует работу привода без усилителя (участок ОА обусловлен начальной нечувствительностью следящего механизма), линия 2 — при действии усилителя в следящем режиме, линия 3 — при максимальном усилии на штоке 20 усилителя (Рв = Рв).
Анализ полученной зависимости для суммарной силы показывает:
— усилитель вступает в работу, когда выражение в скобках становится больше нуля; выражение (Nг × F3/F5 + Qг) характеризует начальную нечувствительность усилителя;
— максимальное усилие, создаваемое усилителем, зависит от давления в ресивере (от давления после редукционного клапана).
Представленные зависимости могут быть использованы при курсовом проектировании для расчета усилителя привода сцепления.
Описание лабораторной установки
Лабораторная установка, представленная на рис. 3.4, состоит из следующих элементов: усилителя 2, соединенного с одной стороны с главным цилиндром 6, а с другой — с ресивером 4. Нагрузка на педаль 5 создается винтовым устройством 7. Давление в гидросистеме привода, создаваемое в главном цилиндре 6, измеряется манометром 8. Давление воздуха, поступающего в усилитель 2 из ресивера 4 через редукционный клапан, измеряется манометром 3. Давление воздуха в цилиндре усилителя (после следящего механизма) измеряется манометром 9. Усилие на штоке усилителя измеряется индикатором 10 динамометрической скобы 1.
Рис. 3.4. Схема лабораторной установки
Порядок выполнения работы
Используя плакаты, схемы и саму лабораторную установку изучить рабочие процессы гидроприводы сцепления с пневматическим усилителем.
Рассчитать статические характеристики следящего механизма и привода. Снять экспериментальные характеристики следящего механизма и привода.
Провести анализ расчетных и экспериментальных характеристик.
Содержание отчета
В отчете необходимо отразить схему привода сцепления с пневматическим усилителем, построить расчетные и экспериментальные характеристики следящего механизма и привода. Провести их анализ и сделать выводы.
Контрольные вопросы
1. Требования к усилителям привода.
2. Работа усилителя при включенном и выключенном сцеплении.
3. Рабочие процессы следящего механизма.
4. Статические характеристики привода сцепления с усилителем.
5. Как работает лабораторная установка?
4 Лабораторная работа №3 « РАБОЧИЕ ПРОЦЕССЫ И АНАЛИЗ КОНСТРУКЦИЙ КОРОБОК ПЕРЕМЕНЫ ПЕРЕДАЧ»
Цель работы: научиться экспериментально определять передаточное число включенной передачи и КПД включенной передачи.
Основные положения
Коробка передач является агрегатом трансмиссии, преобразующим крутящий момент и частоту вращения по величине и направлению. В механической трансмиссии это преобразование осуществляется, как правило, с помощью зубчатых колес и является ступенчатым.
Ступенчатые коробки передач получили наибольшее распространение на современных автомобилях. Полная их классификация приведена в литературе [1].
На автомобилях с механической трансмиссией применяют коробки с числом передач от 3 до 16. Число элементов управления включается на одной передаче на единицу меньше числа степеней свободы коробки передач. Наиболее распространены коробки с двумя степенями свободы, в которых для получения определенной передачи включается одна зубчатая муфта или передвижное зубчатое колесо. На автопоездах устанавливают коробки передач с тремя, иногда четырьмя степенями свободы. Такие коробки имеют, как правило, восемь передач и более. Поэтому их называют многоступенчатыми.
Коробки передач с двумя степенями свободы имеют обычно не более шести передач. В механической трансмиссии их выполняют или по трехвальной соосной схеме, или двухвальной несоосной. Соосность определяется по взаимному расположению ведущего и ведомого валов коробки передач.
Двух ва льные коробки передач
Применяют для переднеприводных и заднеприводных автомобилей. Конструктивно они совмещены в одном блоке с двигателем, сцеплением, главной передачей и дифференциалом.
При поперечном расположении коробки передач применяется цилиндрическая главная передача. Шестерня главной передачи, выполненная за одно целое с ведомым валом коробки передач, расположена консольно.
Привод поперечно расположенной коробки передач имеет некоторые особенности в связи с тем, что необходимо совместить обычный способ переключения, когда выбор передачи происходит в результате поперечного перемещения рычага, а включение зубчатого зацепления - в результате продольного перемещения. При продольном расположении двигателя применяется коническая или гипоидная главная передача. Управление коробкой передач непосредственное. При заднем расположении двигателя и коробки продольно, управление коробкой - дистанционное.
В двухвальной коробке передач (рис. 2.1 а) крутящий момент передастся двумя зубчатыми колесами. Передаточное число зубчатой лары не должно превышать некоторого предела, близкого 4, так как дальнейшее увеличение передаточного числа приводит к увеличению размеров коробки и повышению уровня шума.
а) б)
Рис. 4.1. Схемы двухвальной (а) и трехвальной (б) коробок передач:
а - ЗАЗ-968; б - ГАЗ-53А
Передаточное число высшей передачи в таких коробках, как правило, не делают равным единице, число зубьев сопрягаемых зубчатых колес отличается на 1…2, что позволяет обеспечить хорошую прирабатываемость. В некоторых конструкциях высшая передача - повышающая.
Основные достоинства двухвальных коробок передач: простота конструкции, малая масса, высокий КПД на промежуточных передачах.
Трёхвальные коробки передач
При числе ступеней обычно не более шести управление такой коробкой передач осуществляется при помощи одного рычага. Отличительной особенностью трехвальной коробки передач является наличие прямой передачи, на которой автомобиль движется большую часть пробега. Она образуется в результате непосредственного соединения соосных ведущего (первично) и ведомого (вторичного) валов. При движении на прямой передаче зубчатые колеса и подшипники коробки разгружены, вследствие чего снижается износ, потери мощности и шум. На других передачах переднего хода в трехвальной коробке силовой поток проходит через два зубчатых зацепления, что позволяет получить достаточно большое передаточное число (с 7...9), что часто требуется для первой передачи.
В современных конструкциях коробок передач большинство зубчатых колес находится впостоянном зацеплении. Для включения передач используют зубчатые муфты и синхронизаторы. Зубчатые колеса первой передачи и заднего хода часто не имеют постоянного зацепления. В этих случаях одно из зубчатых колес пары выполняют передвижным и используют его для включения передачи.
Схемы трехвальных соосных коробок передач с двумя степенями свободы, распространенные в настоящее время, имеют принципиальные различия только в схеме включения первой передачи и передачи заднего хода. Можно выделить следующие варианты схем: все зубчатые колеса находятся в постоянном зацеплении (например, коробки передач автомобиля КамАЗ); не имеют постоянного зацепления только зубчатые колеса заднего хода (например, коробки передач автомобиля ГАЗ-24); не имеют постоянного зацепления зубчатые колеса первой передачи и заднего хода (например, коробка передач автомобиля ГАЗ-53). Отличительной особенностью последних схем является отсутствие отдельного зубчатого колеса на ведомом валу (рис. 2.1 б). Для включения заднего хода используется то же передвижное зубчатое колесо, которое образует первую передачу.
Схемы с постоянным зацеплением всех зубчатых колес применяют для коробок передач с относительно большой продолжительностью работы на первой передаче и заднем ходу. Преимуществами таких схем являются отсутствие изнашивания торцов зубчатых венцов и сокращение хода вилок переключения передач; недостатком -необходимость свободной установки на ведомом валу отдельного зубчатого колеса большого размера для передачи заднего хода. Установка такого колеса увеличивает не только общее число зубчатых колес, но и суммарный момент инерции согласованно вращающихся деталей коробки, в результате чего повышается нагрузка на синхронизаторы.
Наряду с коробками передач, имеющими в качестве высшей передачи прямую, получили распространение коробки передач с высшей ускоряющей передачей. Их появление было вызвано стремлением уменьшить частоту вращения вала двигателя при движении автомобиля без груза. Ускоряющую передачу используют для расширения диапазона коробки передач без увеличения передаточного числа первой передачи или сохранения диапазона при уменьшении этого числа.
Схемы коробок передач с двумя степенями свободы не накладывают каких-либо ограничений на закономерности построения ряда передаточных чисел. При выборе числа передач и передаточных чисел руководствуются основным требованием, предъявляемым к коробке передач: обеспечить заданные тягово-скоростные качества и высокую топливную экономичность автомобиля.
Многовальные коробки передач
Такие коробки передач применяются при большом числе передач они представляют собой четырех-...шестиступенчатую трехвальную коробку передач со встроенным или совмещенным редуктором. Редуктор может быть повышающим или понижающим. Повышающий редуктор (мультипликатор или делитель) устанавливают перед коробкой передач, его назначение уменьшить разрыв между передаточными числами соседних передач (уплотнить ряд), незначительно увеличивая диапазон передач. В большинстве случаев делитель увеличивает диапазон на 20...25%,он обычно имеет две передачи - прямую и повышающую, что позволяет увеличить число передач в два раза. Понижающий редуктор (демультипликатор) размещают за коробкой передач. Устанавливать его перед коробкой передач нецелесообразно, поскольку при этом зубчатые колеса коробки и валы передач придется рассчитывать на повышенный крутящий момент, что приводит к увеличению их массы и размеров. Демультипликатор выполняют двух- или трехступенчатым, что позволяет увеличить число передач соответственно в 2 или 3 раза. Его обычно выполняют с большим передаточным числом, благодаря чему расширяется диапазон. Примером многовальной коробки передач может служить десятиступенчатая коробка передач автомобиля КамАЗ-5320.
Способы включения передач
Включение передач при помощи зубчатых колес (кареток) в настоящее время применяется главным образом для первой передачи и передачи заднего хода, включение которых производится в условиях, когда автомобиль неподвижен. Такое ограниченное применение зубчатых колес для включения передач объясняется двумя причинами:
- инерционная ударная нагрузка от сил инерции ведомых деталей при включении приходится на один или два зуба включаемых колес, что приводит к быстрому износу торцов зубьев, сколу зубьев и их
поломке;
- для включения передачи требуется переместить каретку на всю
длину зуба, что приводит к увеличению длины коробки передач и ее
массы.
Запиловка торцов зубьев включаемых зубчатых колес хотя и облегчает процесс включения, но в те же время уменьшает рабочую длину зуба. Обычно такие зубчатые колеса выполняют прямозубыми, но встречается и косозубое исполнение ("Москвич-40").
Применение в коробках передач зубчатых колес постоянного зацепления привело к необходимости использования для включения передач кулачковых или зубчатых муфт. В этом случае ударные нагрузки при включении распределяются между всеми зубьями или кулачками, что, в целом, не снижает шума при включении и не облегчает процесса включения. В настоящее время ограниченно используются только зубчатые муфты легкого включения, у которых зубья укорочены через один.
Полностью исключают ударную нагрузку и шум при включении передач синхронизаторы. В современных коробках передач применяют синхронизаторы, выравнивающие угловые скорости соединяемых элементов перед включением передач. Коробки передач могут быть полностью синхронизированы, но в большинстве случаев наряду с синхронизаторами на высших передачах применяются также кулачковые или зубчатые муфты, а часто - подвижные зубчатые колеса (каретки), дня включения низших передач.
В настоящее время используют только инерционные синхронизаторы, которые блокируют включающую зубчатую муфту до тех пор, пока кинетическая энергия деталей, вращающихся вместе с ведомым диском сцепления (при выключенном сцеплении и нейтральном положении коробки передач), не будет поглощена работой трения в синхронизаторе. Синхронизаторы могут быть одностороннего (для включения одной передачи) и двустороннего (для включения двух передач) действия. Инерционный синхронизатор включает следующие элементы:
- выравнивающий - функционный элемент, поглощающий энергию касательных сил инерции вращающихся масс;
- блокирующий - устройство, препятствующее перемещению включающей зубчатой муфты до полного выравнивания угловых скоростей;
- включающий - зубчатая муфта, включающая передачу.
Наибольшее распространение получили конусные синхронизаторы, в котрых выравнивающим, элементом является конусная муфта. Иногда применяются в качестве выравнивающего элемента многодисковые муфты. Рабочий процесс инерционного синхронизатора описан в литературе [1].
К коробкам передач предъявляются следующие требования: обеспечение оптимальных тягово-скоростных и топливно-экономических свойств автомобиля при заданной внешней скоростной характеристике двигателя;
- бесшумность при работе и переключении передач;
- легкость управления;
- высокий КПД;
- общие требования (надежность, долговечность, ремонтопригодность и т.д.).
В соответствии с предъявляемыми требованиями для оценки и анализа конструкций коробок передач используется ряд оценочных параметров:
1. Диапазон передаточных чисел (диапазон коробки передач). Под ним понимают отношение передаточного числа низшей и высшей передач:
(4.1)
В легковых автомобилях иавтобусах малой вместимости на их базе D= 3...4., в грузовых автомобилях в зависимости от грузоподъемности и назначения и в автобусах средней и большой вместимости D = 5...8. Для автомобилей тягачей и автомобилей высокой проходимости D= 9…13.
2. Число передач и плотность ряда передаточных чисел.
Плотность ряда характеризуется отношением передаточных чисел соседних передач. Чем больше число передач, тем выше плотность ряда, тем в большей степени выполняется требование обеспечения высоких тяговых и экономичных свойств автомобиля. В современных конструкциях коробок передач показатель плотности ряда передач стремятся выполнять в пределах 1,1…1,5. Помимо сказанного, большая плотность ряда позволяет синхронизаторам работать в более благоприятных условиях, поскольку при этом угловые скорости выравниваемых элементов отличаются незначительно.
3. Уровень шума, создаваемого при работе.
Этот параметр зависит от качества, точности изготовления и типа зубчатых пар, жесткости валов и картера коробки. Меньший уровень шума обеспечивают косозубые и шевронные колеса (одновременно им присуща большая прочность).
Недостаточная жесткость валов приводит к нарушению зацепления, что сопровождается повышением уровня шума. Жесткость картера обеспечивается путем создания рациональной формы и оребрения. Показателем оценки уровня шума коробки передач может служить ее КПД, так как шум всегда сопровождается потерей энергии.
4. Легкость управления
Оценочными показателями являются как усилие прилагаемое к рычагу управления, так и сложность манипуляций, которая определяется степенью сложности самой конструкции коробки передач и ее привода.
5. Металлоемкость конструкции, трудоемкость изготовления и стоимо-сть.
Металлоемкость оценивают удельной массой коробки передач - отношением ее массы к мощности двигателя. В целом она характеризуется значениями от 0,3 до 2,0 кг/кВт.
6. Ресурс
Срок службы современных коробок передач составляет от 125 до 250 тыс. км пробега.
Порядок выполнения работы
Используя плакаты, схемы, макеты и учебные экспонаты, провести сравнительный анализ предложенных преподавателем конструкций коробок передач, выделить основные их особенности. При проведении анализа выяснить, каким образом в данных конструкциях реализованы предъявляемые к ним требования.
Используя лабораторную установку (рис. 4.2.), определить передаточные числа исследуемой коробки передач, посчитать плотность ряда и диапазон передаточных чисел.
Описание лабораторной установки
Лабораторная установка представляет собой коробку передач автомобиля КамАЗ-5320 1, установленную на подставке и, на ведущем и ведомом валах которой закреплены круговые шкалы 3. Угол поворота ведущего вала замеряется путем вращения его на един оборот, одновременно при этом замеряется угол поворота ведомого вала. Отношение этих углов и дает передаточное число включенной передачи.
Для определения передаточного числа включенной передачи к фланцу выходного вала коробки передач прикрепляется барабан, к которому с помощью троса подвешивается груз заданного веса. Порядок выполнения задания следующий: для каждой из включаемых передач, поворачивая с помощью динамометрического ключа ведущий вал коробки передач, приводят во вращение барабан, на который начинает наматываться трос с грузом. Зная массу груза и радиус барабана (плечо), определяют момент на выходном валу коробки передач. Момент на ведущем валу коробки передач определяется с помощью динамометрического ключа. Соотношение этих моментов с учетом передаточного числа включенной передачи (формула 2.1) и позволяет определить КПД коробки передач на данной передаче.
Рис. 4.2. Схема лабораторной установки
Отчет по данной лабораторной работе должен содержать анализ предложенных преподавателем конструкций коробок передач, их конструктивные схемы, результаты измерений передаточных чисел и КПД исследуемой коробки передач, а также результаты расчетов диапазона и плотности ряда передаточных чисел анализируемых коробок передач. Вместе с тем могут быть предложены и другие задания по определению основных характеристик анализируемых коробок передач.
Контрольные вопросы
1. Назначение коробок передач и их классификация.
2. Требования, предъявляемые к конструкциям коробок передач,
как они реализованы в тех или иных конструкциях.
3. Особенности конструкций двухвальных и трехвальных коробок передач.
4. Многовальные коробки передач.
5. Оценочные показатели конструкций коробок передач, основные характеристики.
6. Способы включения передач, конструкции синхронизаторов.
5 Лабораторная работа №4 « Рабочие процессы и анализ конструкций карданных передач »
Цель работы: научиться определять характеристики и параметры карданной передачи с двумя асинхронными шарнирами.
Общие положения
Карданные передачи применяются в трансмиссиях автомобилей для силовой связи механизмов, валы которых не соосны или расположены под углом, причем взаимное положение их может меняться в процессе движения. Карданные передачи применяют также для привода вспомогательных механизмов и в ряде случаев для связи рулевого колеса с рулевым механизмом.
Карданные передачи могут быть открытыми или закрытыми и классифицируются по типу карданных шарниров [1]. К ним предъявляются следующие требования:
— передача крутящего момента без создания дополнительных нагрузок в трансмиссии (изгибающих, скручивающих, вибрационных, осевых);
— возможность передачи крутящего момента с обеспечением равенства угловых скоростей ведущего и ведомого валов независимо от угла между соединяемыми валами;
— бесшумность;
— высокий КПД;
— общие требования.
Рабочие процессы карданных передач
При передаче вращательного движения под углом при помощи шарниров возникают трудности в обеспечении равномерного вращения вала, расположенного после шарнира.
Равномерность вращения (равенство угловых скоростей ведущего и ведомого валов) в синхронных карданных шарнирах обеспечивается при выполнении определенных условий. Из рис. 5.1. а следует, что VА=w1×r1 =w2×r2, а значит, условие w1=w2 выполнимо, если r1=r2. При повороте вала 1, например, на 1800, r1 и r2 уменьшатся, но их равенство должно сохраниться. При этом точка контакта А валов 1 и 2 должна перемещаться по биссекторной плоскости ОО (j1=j2) при вращении валов.
Это условие не выполняется в жестком шарнире неравных угловых скоростей (рис. 2.10б), так как шипы А1 и В1 крестовины 3 перемещаются в плоскости О1О1, перпендикулярной оси вала 1, а шипы А2 и В2 — в плоскости О2О2, перпендикулярной оси вала 2.
Рис. 5.1. Кинематика шарниров: а) синхронного; б) асинхронного
Если вал 1 повернется на угол a, вал 2 повернется на угол b, причем
tg a = tg b × cos g. (5.1)
Продифференцировав, получим
(5.2)
и после преобразований
. (5.3)
Отсюда следует, что w 1 ¹ w 2, причем коэффициент неравномерности
. (5.4)
при g < 100 невелик.
Для того чтобы обеспечить равномерное вращение валов карданной передачи с такими шарнирами используют два шарнира неравных угловых скоростей. При этом необходимо обеспечить выполнение условия сборки (рис. 5.2.):
1) g1=g2;
2) ведущие вилки первого и второго шарниров должны быть повернуты друг относительно друга на угол равный 900.
Рис. 5.2. Схема карданной передачи с двумя асинхронными
карданными шарнирами
Для асинхронного карданного шарнира неравенство угловых скоростей приводит к неравенству моментов на ведущем и ведомом валах, поскольку М2w2=М1w1. Это приводит к появлению дополнительного момента, который вызывает дополнительную закрутку карданного вала:
, (5.5)
где С — крутильная жесткость ведомого вала.
Следует учитывать, что М2 изменяется периодически, т. е. карданный вал (трансмиссия) нагружается переменным крутящим моментом, вызывающим крутильные колебания.
Карданный вал и действующие на него нагрузки
Валы изготавливают из стального прутка или стальных труб. При работе на них действуют изгибающие, скручивающие и осевые нагрузки.
Изгибающие нагрузки появляются за счет центробежной силы, вызываемой неуравновешенностью карданного вала. В эксплуатации неуравновешенность может появиться не только из-за механических повреждений вала, но также из-за износа шлицевого соединения или подшипников карданных шарниров. Неуравновешенность приводит к вибрациям карданной передачи и возникновению шума. Поэтому валы подвергают тщательной балансировке. Точность балансировки составляет 15—25 гсм для автомобилей грузоподъемностью менее 5 т. и 50—75 гсм для автомобилей грузоподъемностью 5 т. и выше. Допустимая величина биения вала при 6000 об/мин не должна превышать 2 мм. Но даже хорошо уравновешенный вал из-за прогиба, вызванного собственным весом, при некоторых оборотах, называемых критическими, теряет устойчивость, т.е. его прогиб возрастает настолько, что возможна поломка вала. Критические обороты вала рассчитываются по эмпирической формуле:
, (5.6)
где a н и a вн — соответственно наружный и внутренний диаметры вала;
L — длина вала.
Скручивающие нагрузки связаны с передачей крутящего момента от КПП к главной передаче. Вместе с тем, являясь элементом многомассовой упругой системы трансмиссии, карданный вал участвует в крутильных колебаниях и воспринимает дополнительные скручивающие нагрузки. Крутильные колебания могут возбуждаться неравномерностью сопротивления движению и неравномерностью крутящего момента карданной передачи. Крутильные колебания, как известно, гасятся демпфером сцепления. Применение упругих резиновых карданных сочленений (ВАЗ) также способствует поглощению энергии крутильных колебаний, и, кроме того, в значительной степени снижает скручивающие нагрузки при резком включения сцепления и торможении с неотключенным двигателем.
Осевые нагрузки возникают в шлицевом соединении при перемещениях, связанных с изменением расстояния между карданными шарнирами (при колебаниях кузова на рессорах). Перемещения в шлицевом соединении происходят в условиях граничного трения. Коэффициент трения при этом равен 0,2, а при появлении задиров в шлицевом соединении происходит защемление, и карданный вал, по существу, передает тяговое усилие. При этом двигатель получает продольное смещение (ГАЗ-52 до 10 мм). Граничное трение в шлицах приводит к быстрому их износу и к нарушению в связи с этим балансировки карданной передачи. Большая величина осевых сил (ГАЗ-52 до 2000 кг) создает дополнительные нагрузки на карданную передачу, а также на подшипники КПП и главной передачи. Осевые силы являются главной причиной того, что долговечность карданных передач в 2—3 раза меньше долговечности основных агрегатов автомобиля. Осевые силы могут снижены:
— согласованием кинематики подвески и карданной передачи, (чтобы перемещения в шлицевом соединении были минимальными);
— уменьшением удельного давления в шлицах за счет увеличения диаметра шлицевой части вала, длины шлицов и их количества;
— покрытием шлицов полимерным материалом;
— применением специальных конструкций шлицевых соединений.
Анализ конструкций шарниров равных угловых скоростей
Синхронные карданные шарниры применяют в приводе ведущих и одновременно управляемых колес, угол между осями валов в зависимости от конструкции шарнира может достигать 450.
Среди наиболее используемых шарниров данного вида можно выделить следующие:
1. Четырехшариковый карданный шарнир с делительными канавками (типа “Вейс”).
Состоит из двух кулачков с выфрезерованными на них канавками, четырех шариков, расположенных в канавках, и одного центрального, центрирующего шарика (УАЗ-469, ГАЗ-66, ЗИЛ-131). Кинематическая схема шарнира изображена на рис. 5.3. Четыре шарика всегда располагаются на пересечении канавок, т. е. в биссекторной плоскости.
Рис. 5.3. Кинематическая схема шарнира с делительными канавками
Наиболее точно шарики устанавливаются при пересечении канавок под углом в 900, но при этом большее скольжение приводило бы к сильному износу канавок и шариков. При пересечении канавок под малым углом возможно заклинивание шариков. Обычно канавки выполняются так, чтобы центр средней окружности канавок находится на расстоянии а=(0,4—0,45)×R от центра шарнира.
Особенности:
— допускает максимальный угол между валами до 30—320;
— наиболее простой и дешевый из всех синхронных карданных шарниров;
— передача усилия от одного кулака к другому осуществляется двумя шариками при движении вперед и двумя другими при движении задним ходом, отсюда высокие удельные давления. Теоретически точечный контакт;
— при работе возникают большие распорные нагрузки, которые необходимо воспринимать специальными шайбами или подшипниками;
— целесообразно применять при нагрузке на ось не свыше 2,5—3 т, т. к. при больших нагрузках габариты его возрастают значительно;
— КПД достаточно высокий, поскольку в основном преобладает трение качения;
— долговечность в эксплуатации не превышает 25—30 тыс. км.
2. Шариковый карданный шарнир с делительным рычажком (типа “Рцепп”).
Состоит из сферического кулака, связанного с одним валом, и сферической чашки, связанной с другим валом. На кулаке и чашке выфрезеровано по 6 канавок, в которых размещено 6 шариков, связанных общей обоймой. При помощи делительного рычажка, управляемого обоймой, шарики устанавливаются в биссекторной плоскости. Точность установки зависит от подбора плеч делительного рычажка, причем точность обеспечивается только в некотором диапазоне углов между валами (рис. 5.4).
Рис. 5.4. Кинематическая схема шарикового
карданного шарнира с делительным рычажком
Особенности:
— допускает угол между валами до 35—380;
— усилие передается шестью шариками, причем контакт шариков с канавками линейный;
— обеспечивает передачу большого крутящего момента при малых габаритных размерах;
— распорные нагрузки отсутствуют;
— имеет высокий КПД, обладает большой надежностью и долговечностью;
— технологически сложен и наиболее дорогой из всех.
За рубежом аналогичные шарниры некоторыми фирмами выполняются без делительного рычажка. Установка шариков в биссекторной плоскости происходит за счет выполнения канавок в сферической чашке и в сферическом кулаке не из общего центра, а из смещенных в обе стороны центров (типа “Бирфильд”). Такие шарниры устанавливаются в карданной передаче передних управляемых и ведущих колес некоторых отечественных автомобилей (ВАЗ-2108) на наружном конце карданного вала.
3. Сдвоенный карданный шарнир с делительным рычажком.
Состоит из двух карданных шарниров неравных угловых скоростей, объединенных одной вилкой. Равенство угловых скоростей должно обеспечиваться делительным рычажком. Однако такое равенство возможно только при равенстве углов g1=g2, что в данной конструкции не соблюдается точно, т. к. при наклоне вала плечо, связанное с левым валом, остается постоянным, а плечо, связанное с другим валом, увеличивается на Da (рис. 5.5). Поэтому в сдвоенном шарнире с делительным рычажком синхронное вращение соединяемых валов может быть обеспечено только с некоторым приближением.
Рис. 5.5. Кинематическая схема сдвоенного карданного шарнира
с делительным рычажком
Особенности:
— значительный износ игольчатых подшипников и крестовин, поскольку благодаря преимущественно прямолинейному движению автомобиля иглы подшипников не перекатываются, вследствие чего поверхности деталей, с которыми они соприкасаются, подвержены бринеллированию, а сами иголки иногда сплющиваются;
— большие габариты.
4. Кулачковый карданный шарнир.
Состоит из пяти простых по конфигурации деталей: двух вилок 1 и 4, двух кулачков 2 и 3 и диска 5 (рис. 5.6), поэтому иногда его называют дисковым. Такие шарниры устанавливаются на ряде отечественных автомобилей (КамАЗ-4310, Урал-4320, КАЗ-4540, КраЗ-260 и др.).
Рис. 5.6. Кинематическая схема кулачкового шарнира
Особенности:
— допускает угол между валами до 450;
— при малых габаритах обеспечивает передачу большого крутящего момента;
— КПД ниже, чем у других из-за трения скольжения между элементами шарнира;
— в эксплуатации наблюдается значительный нагрев, иногда задиры из-за неудовлетворительного подвода смазки к поверхностям трения.
Описание лабораторной установки
Лабораторная установка (рис. 5.7) состоит из стенда, имеющего основание 1 и две вертикальные параллельные друг другу стойки 2. Между стойками, опираясь на них, размещается карданный вал 3 с двумя шарнирами 4 неравных угловых скоростей. Длина вала может изменяться за счет шлицевого соединения. Это достигается посредством изменения положения по высоте одного из концов вала за счет его перемещения по стойке. Угол наклона вала контролируется по градусной шкале 5, размещенной на стойке. Углы поворота ведущей вилки первого шарнира и ведомой вилки второго контролируется по круговым шкалам 6, расположенным на торцевых поверхностях стоек.
Рис. 5.7. Схема лабораторной установки
Порядок выполнения работы
Используя плакаты, схемы, образцы и саму лабораторную установку, изучить рабочие процессы карданной передачи, проанализировать предложенные преподавателем конструкции.
Провести экспериментальную проверку условия сборки карданной передачи. Для этого:
— установить ведущие вилки первого и второго шарниров под углом 900;
— изменяя угол наклона вала g от 00 до 400 через 100, провести замеры углов поворота ведущей вилки первого a и ведомой вилки второго b шарниров. Значения a задаются при этом от 00 до 3600 через 300. Составить таблицу полученных результатов;
— определить степень неравномерности вращения по формуле:
. (5.7)
— установить ведущие вилки первого и второго шарниров в одной плоскости;
— изменяя угол наклона вала от 00 до 400 через 100, повторить те же замеры, что и в первом случае. Составить таблицу полученных результатов;
— определить степень неравномерности вращения по той же формуле;
— построить зависимость степени неравномерности от угла g.
Сделать выводы.
Содержание отчета
В отчете следует отразить анализ предложенных преподавателем конструкций карданных передач, схему лабораторной установки, построить экспериментальные зависимости n=f(g). Сделать выводы.
Контрольные вопросы
1. Пояснить назначение карданной передачи и требований, предъявляемых к ней.
2. Условие обеспечения синхронности вращения в шарнире равных угловых скоростей.
3. Обеспечение синхронности вращения в карданной передаче с шарнирами неравных угловых скоростей.
4. Особенности конструкций асинхронных карданных шарниров.
5. Какие нагрузки действуют в карданной передаче?
6. Какие обороты карданного вала называются критическими?
7. К чему приводит неравномерность вращения в карданной передаче?
6 Лабораторная работа № 5 « РАБОЧИЕ ПРОЦЕССЫ И АНАЛИЗ КОНСТРУКЦИЙ ГЛАВНЫХ ПЕРЕДАЧ»
Цель работы: Экспериментальное определение влияния предварительного натяга подшипников на величину осевого перемещения ведущей шестерни главной передачи.
Основные положения
Главная передача - механизм трансмиссии автомобиля, преобразующий крутящий момент и расположенный перед ведущими колесами автомобиля. Выбирается из условий получения заданной максимальной скорости автомобиля на высшей передаче в коробке передач и оптимальной топливной экономичности.
Главные передачи по числу, виду и расположению зубчатых колес подразделяют на одинарные, двойные, конические, гипоидные, центральные двойные, разнесенные двойные, цилиндрические, червячные, двухступенчатые. Полная ах классификация приведена в литературе [1].
Одинарные главные передачи
Компактны имеют минимальные размеры и массу, невысокую стоимость, простоту в производстве и эксплуатации. Их применение ограничено величиной передаточного числа и несущей способностью зубчатого зацепления: при передаче большого крутящего момента необходимо увеличивать модуль зуба, а, следовательно, и размеры зубчатых колес, что приводит к уменьшению дорожного просвета.
Одинарные конические главные передачи применяют на легковых автомобилях и грузовых автомобилях малой грузоподъемности (рис. 6.1 а). Более широкое распространение получила гипоидная главная передача (рис. 6.2 б), обладающая рядом преимуществ перед конической: повышенной несущей способностью по контактным напряжениям, большей плавностью работы и бесшумностью. Иногда применение такой передачи обусловлено наличием гипоидного смещения Е как фактора, расширяющего компоновочные возможности. Гипоидные передачи устанавливают на автомобили семейства ВАЗ, "Москвич", "Волга", ГАЗ-53 и др.
Абсолютное большинство зубчатых колес конических и гипоидных передач, устанавливаемых на автомобилях (около 95%), имеют круговую линию зубьев. Иногда используются эвольвентная или циклоидальная линии зубьев. Для устранения концентрации напряжений на поверхности зубьев, вызываемых деформированием сопрягаемых деталей, радиус кривизны выпуклой стороны зуба делают меньшим, чем радиус кривизны вогнутой стороны. В этом случае линейный контакт зубьев происходит не по всей длине зуба, а лишь на некотором участке по обе стороны от контактной точки, и действительная длина контактной линии увеличивается с ростом нагрузки.
Направление винтовой линии зуба конических зубчатых колес выбирают из определенного условия с тем, чтобы при эксплуатации осевое усилие шестерни было направлено от вершины конуса и отжимало шестерню от колеса, не давая ему защемляться. При вращении конической шестерни по часовой стрелке (движение автомобиля вперед) это условие выполняется в случае левого направления винтовой линии зуба. При движении автомобиля назад направление осевого усилия изменится, но величина его будет меньше.
В гипоидных передачах направление винтовой линии зуба зубчатых колес определяется направлением смешения оси шестерни. При смещении оси вниз направление винтовой линии зубьев шестерни должно быть левое, чтобы осевое усилие шестерни было направлено от вершины конуса. При смещении оси вверх направление винтовой линии зуба по тем же соображениям, должно быть правое. Смещение Е в гипоидных передачах легковых автомобилей не должно повышать 0,2 Dw - внешний делительный диаметр шестерни, а в грузовых автомобилях
0,125 Dw.
Одинарную цилиндрическую передачу используют на легковых автомобилях при поперечном расположении двигателя. Некоторые зарубежные фирмы применяют одинарную червячную главную передачу. В этом случае можно получить главную передачу с передаточным числом более 7,0. Однако более низкий по сравнению с конической и гипоидной передачами КПД червячной передачи, меньшая нагрузочная способность при тех же размерах и несколько большая сто-имость производства ограничивают область применения таких передач.
Двойные главные передачи
Центральная двойная главная передача обладает большей нагрузочной способностью по сравнению с одинарной при тех же размерах колес и позволяет получить большие передаточные числа без уменьшения дорожного просвета под картером главной передачи.
Центральные главные передачи выполняют по следующим схемам: а) первая ступень коническая (гипоидная), вторая - цилиндрическая (рис. 6.1 г); б) первая ступень коническая (гипоидная, червячная), вторая ступень - планетарная (рис.6.1 д); в) первая ступень планетарная, вторая - коническая (гипоидная) (рис. 6.1 е).
В отечественном автомобилестроении наибольшее распространение получили передачи по схеме, представленной на рис. 6.1 г. Эти передачи могут быть плоскими: все валы расположены в горизонтальной плоскости (ЗИЛ-130) (рис. 6.1 ж); "пистолетного" типа: расположены в двух неперпендикулярных плоскостях (КрАЗ-257Б) (рис. 6.1 з); Г-образными: валы расположены в двух взаимно перпендикулярных плоскостях - горизонтальной и вертикальной (Урал-375, ЗИЛ-131, КамАЗ-5320). Последний тип главной передачи позволяет получить наиболее компактный промежуточный проходной мост тележки трехосного автомобиля.
Рис 6.1. Схемы главных передач
одинарных (а, б, в); двойных (г, д. е, ж, з, и)
При "плоской" главной передаче сокращается расстояние между фланцами крепления карданного вала, что при небольшой базе автомобиля может привести к большим углам наклона этого вала. В случае Г-образной главной передачи пара конических зубчатых колес размещена над балкой моста, вследствие чего необходимо увеличение высоты пола кузова и соответственно погрузочной высоты платформы.
С точки зрения нагруженности опор промежуточного вала преимущество имеет плоская схема, где радиальные усилия, действующие на промежуточный вал со стороны конического колеса и цилиндрической шестерни, направлены в противоположные стороны и лежат в одной плоскости. Это обусловливает уменьшение результирующей этих усилий.
Условия смазывания опор вала, шестерни и промежуточного вала хуже в схемах "пистолетного" типа и Г-образной. В этих конструкциях обычно предусматривают либо принудительную подачу масла с помощью насоса, либо устанавливают специальные ловушки, масляные каналы со стеком масла к опорным подшипникам указанных валов.
Главная передача, выполненная по схеме, изображенной на рис. 6.1 г. может передавать больший крутящий момент. Обычно передаточное число конической пары составляет 1,5~2,7. Главная передача, выполненная по схеме (рис. 6.1 д), обеспечивает лучшие условия компоновки по сравнению со схемами г) и ж). К недостаткам этого типа передач относятся повышенная трудоемкость их изготовления, а также несколько большие потери на перемещение масла в центральном редукторе. Главная передача, выполненная по схеме, изображенной на рис. 6.1 ж, обладает существенными преимуществами в отношении требуемой жесткости конструкции и простоты осуществления привода заднего моста тележки. Недостатком ее является несколько меньшая компактность конструкции.
Разнесенная двойная главная передача состоит из центрального редуктора с одинарной конической или гипоидной передачей и межколесным дифференциалом, за которым расположены два колесных редуктора.
Разнесенные главные передачи сложнее по конструкции, чем центральные, имеют большее число зубчатых колес и подшипников. Несмотря на это, они получили широкое распространение на автомобилях средней и большой грузоподъемности, из-за ряда преимуществ, например, возможности уменьшения размеров межколёсного дифференциала и диаметра полуосей вследствие малой степени редакции момента, подводимого к дифференциалу, получения компактной центральной части ведущего моста и достаточно большого дорожного просвета под центральной частью балки ведущего моста, осуществления изменения передаточного числа без изменения конструкции центрального редуктора и центральной части балки ведущего моста.
В практике конструирования привода ведущих колес редукторы разнесенной двойной главной передачи разделяют на бортовые, расположенные перед ведущими колесами или непосредственно за межколесным дифференциалом, и колесные, расположенные в ступице ведущего колеса или его тормозного барабана. Применяют следующие виды редукторов: с цилиндрической передачей внешнего зацепления; с конической передачей внешнего зацепления; с цилиндрической передачей внутреннего зацепления; с цилиндрической планетарной передачей; с заторможенными центральным или солнечным колесами; с конической планетарной передачей.
Наибольшее распространение получили передачи с многосателлитными планетарными и непланетарными цилиндрическими передачами (МАЗ-5ООА, БелАЗ-540А) вследствие своей повышенной нагрузочной способности и компактности конструкции. Их применение, однако, ограничено допустимой нагрузкой на ось не менее 60 кН. К конструкциям главных передач предъявляются следующие требования:
- минимальные размеры по высоте для обеспечения максимального дорожного просвета;
- возможно более низкий уровень шума;
- общие требования.
Получение возможно более высокого дорожного просвета реализуется подбором соответствующей конструкции главной передачи, например, использованием гипоидной одинарной главной передачи c верхним смешением.
Низкий уровень шума главной передачи является одной из ее основных эксплуатационных характеристик, определяющих как конструктивное и технологическое совершенство, так и состояние при эксплуатации. Технологически уровень шума снижается за счет точности изготовления зубьев,высокой чистоты их поверхности, а также условий смазки. Точность зацепления зависит как от регулировочных, так и от конструктивных параметров - жесткости установки зубчатых колес и способа их установки.
Жесткость установки зубчатых колес во многом зависит от жесткости самого картера главной передачи. Его жесткость обеспечивается конфигурацией и целесообразным оребрением. Зубчатые зацепления главной передачи устанавливаются с учетом соответствующих ограничений на смещение (рис. 6.2).
Рис. 6.2. Схема допустимых смещений в главной передаче
Обеспечение допустимых смещений элементов главной передачи достигается рядом специальных конструктивных мероприятий:
- подбором соответствующих подшипников валов;
- использованием дополнительной опоры вала ведущей шестерни;
- созданием предварительного натяга подшипников вала веду
щей шестерни;
- использованием упоров для конического колеса главной передачи;
- регулированием зацепления с помощью прокладок.
Уровень шума, а также обеспечение качественного уплотнения соединяемых элементов (выходных валов, крышек и т. д.), обеспечивается правильной организацией смазки элементов главной передачи.
Выход из строя главной передачи связан в первую очередь с износом зубьев - более 70%, усталостным выкрашиванием - более 20% и поломками - менее5%.
Ресурс главныхпередач до капитального ремонта лежит в пределах 125…250 тыс. км пробега для легковых автомобилей и 200…500 тыс. км пробега для грузовых автомобилей.
Порядок выполнения работы
Используя плакаты, схемы, макеты и учебные экспонаты, провести сравнительный анализ предложенных преподавателем конструкций главных передач, выделить основные их особенности. При проведении анализа выяснить, каким образом в данных конструкциях реализованы предъявляемые к ним требования.
Используя лабораторную установку (рис. 6.3), определить коэффициент полезного действия главной передачи и передаточное число.
Описание лабораторной установки
Лабораторная установка представляет собой главную передачу автомобиля, смонтированную на учебном столе, включающую часть кожуха заднего моста и барабан (тормозной), надетый на полуось.
Рис. 6.3.Схема лабораторной установки
На барабан намотан трос, к которому подвешен груз заданного веса. Суть выполнения задания по лабораторной работе в следующем: поворачивая с помощью динамометрического ключа хвостовик ведущего вала главной передачи, приводят во вращение тормозной барабан, на который начинает наматываться трос с грузом. Зная массу груза и радиус барабана (плечо), можно достаточно легко определить момент на выходе главной передачи. Момент на входе определяется с помощью динамометрического ключа. Соотношение этих моментов с учетом передаточного числа главной передачи (формула 2.1) и определяет КПД передачи:
(6.1)
Порядок определения передаточного числа главной передачи аналогичен описанному в лабораторной работе. Угол поворота ведущего вала главной передачи замеряется путем вращения его на один оборот при одновременном замере угла поворота полуоси. При этом следует учитывать, что вторая полуось не вращается (защемлена). Отношение этих углов и позволяет определить передаточное число главной передачи.
Отчет по данной лабораторной работе должен содержать анализ предложенных преподавателем конструкций главных передач с указанием их отличий, преимуществ и недостатков, результаты измерений передаточных чисел, прямого и обратного КПД. Вместе с тем могут быть предложены и другие задания по теме данной лабораторной работы.
Контрольные вопросы
1. Назначение главных передач и их классификация.
2. Требования к конструкциям главных передач; как они реализуются в тех или иных конструкциях.
3. Особенности конструкций одинарных и двойных главных передач.
4. Разнесенные главные передачи.
5. Основные характеристики главных передач.
6. Преднатяг подшипников, основные регулировки главной передачи.
7 Лабораторная работа №6 « РАБОЧИЕ ПРОЦЕССЫ И АНАЛИЗ КОНСТРУКЦИЙ ДИФФЕРЕНЦИАЛОВ ПОЛУОСИ»
Цель работы:Определение деформаций и напряжений в полуоси автомобиля с использованием методов электротензометрии.
Основные положения
Дифференциал - механизм трансмиссии автомобиля, распределяющий подводимый к нему крутящий момент между выходными валами и позволяющий им вращаться с неодинаковыми скоростями. Их устанавливают в узлах деления мощности, когда требуется, чтобы на участке трансмиссии за этим узлом отсутствовала циркуляция мощности, в частности, между ведущими колесами (межколесный дифференциал) и между мостами (межосевые дифференциалы).
В зависимости от характера распределения крутящего момента дифференциалы делят на симметричные, несимметричные и блокируемые (с принудительной блокировкой или самоблокирующиеся).
По конструкции передач различают дифференциалы шестеренчатые, кулачковые, червячные и с механизмом свободного хода. Межосевые дифференциалы могут быть симметричными и несимметричными, межколесный дифференциал всегда симметричный. Полная классификация дифференциалов приведена в литературе [I].
К дифференциалам предъявляются следующие требования:
- распределение крутящих моментов между колесами и мостами
в пропорции, обеспечивающей наилучшие эксплуатационные свойств-
ва (максимальную тягловую силу, хорошие устойчивость и управляемость):
- общие требования.
Анализ конструкций дифференциалов
1. Симметричный конический дифференциал.
Наиболее распространенный тип (их часто называют простыми). Коэффициент блокировки для такого дифференциала можно считать равным единице. Число зубьев шестерен и полуосевых шестерен может быть четным или нечетным, но для обеспечения сборки должно подчиняться условию:
(7.1)
где Z ш - число зубьев полуосевой шестерни;
- число сателлитов;
К - целое число.
Основные преимущества такого дифференциала:
- обеспечение устойчивости при движении по скользкой дороге
и торможении двигателем благодаря равенству тангенциальных реакций на ведущих колесах;
- простота конструкции, малые размерь; и масса, надежность,
высокий КПД.
Отрицательным качеством является ограничение проходимости.
2. Симметричный цилиндрический дифференциал.
Примером такого дифференциала является дифференциал автомобиля "Татра".
Он имеет небольшие размеры в случае установки перед главной передачей. Имеет большее число зубчатых колес, чем конический, более сложен в изготовлении. Применяется в основном в качестве межосевого дифференциала.
3. Самоблокирующиеся дифференциалы.
Конструкций такого типа известно достаточно много, но на автомобилях применяются лишь шестеренчатые конические дифференциалы. Они включают в себя те же детали, что и простой конический, единственное отличие в профиле зубьев. Профиль зубьев сателлитов и полуосевых шестерен специальный, что приводит к изменению передаточного числа. Передаточное число имеет максимальное значение при контакте ножки зуба сателлита с головкой зуба полуосевой шестерни и минимальное значение - при контакте головки зуба сателлита с ножкой зуба полуосевой шестерни. Число зубьев сателлита обязательно должно быть нечетным. Коэффициент блокировки такого дифференциала переменный от 2,0 до 2,5. Недостаточная величина коэффициента блокировки, не обеспечивающая значительного, повышения проходимости, является одной из причин ограничивающих применение таких дифференциалов. Вместе с тем при вращении сателлита в такой конструкции создается пульсация момента в трансмиссии, что ограничивает допустимую величину К 6.
4. Дифференциалы свободного хода.
Эти механизмы не всегда относят к дифференциалам, поскольку они не подчиняются закономерностям, установленным кинематическим уравнением дифференциала.
Известна конструкция роликового дифференциала свободного хода. Коэффициент блокировки для него равен бесконечности, что позволяет передавать тяговое усилие на одно колесо, когда второе вывешено или когда полуось сломана. Дифференциал работает практически постоянно, поэтому крутящий момент передается в большинстве случаев через одно колесо, что может сказаться на управляемости. Его большим недостатком является также недостаточная долговечность.
Дальнейшим развитием конструкций этого типа явились кулачковые дифференциалы свободного хода (МАЗ-537). Однако кулачковый дифференциал свободного хода технологически очень сложен, что отражается на его стоимости.
5. Дифференциалы повышенного трения.
Конструктивно могут выполняться различными: шестеренчатыми с фрикционными элементами, червячными, кулачковыми (сухарными), гидравлическими. По рабочему процессу их можно разбить на три группы:
1) с постоянным моментом трения;
2) с моментом трения, пропорциональным передаваемому моменту:
3) с моментом трения, пропорциональным квадрату разности угловых скоростей выходных валов.
Из наиболее известных конструкций дифференциалов такого типа следует назвать следующие:
- шестеренчатый дифференциал с моментом трения, пропорциональным передаваемому моменту. Используется на автомобилях высокого класса, имеет постоянный коэффициент блокировки, обычно 4:
- червячный дифференциал. Применяется крайне редко, поскольку является наиболее дорогостоящим и сложным;
- кулачковый дифференциал (сухарный). В выполненных конструкциях коэффициент блокировки равен 4-5. Его основным недостатком является возможность заклинивания при сильном износе сухарей:
- гидравлические дифференциалы ("силиконовые"). Опыт эксплуатации таких дифференциалов пока отсутствует. Однако некоторые выводы об их достоинствах и недостатках дают экспериментальные исследования. В качестве основных недостатков отмечены следующие: давление, создаваемое насосом, должно
быть высоким, что трудно осуществимо, а гидравлическое сопротивление зависит от температуры масла.
В целом можно сделать вывод о том, что практически в 90% всех автомобилей используются простые конические дифференциалы.
6. Межосевые дифференциалы.
Симметричные межосевые дифференциалы, устанавливаемые между равнонагруженными мостами автомобилей повышенной и высокой проходимости, выполняют обычно коническими с возможностью блокировки с места водителя. Их устанавливают или в раздаточной коробке (ВАЗ-2121), или на промежуточном мосту трехосного автомобиля (КамАЗ-5320) в приводе главной передачи. Несимметричные межосевые дифференциалы, устанавливаемые в раздаточных коробках и распределяющие крутящие моменты соответственно массам, приходящимся на ведущие мосты, выполняют главным образом цилиндрическими планетарными (КамАЗ-4310). При принудительной блокировке дифференциала все его элементы вращаются как одно целое и коэффициент блокировки равен бесконечности. Момент включения определяется водителем, что не всегда оптимально: если не выключена блокировка при движении по хорошей дороге, наблюдается ускоренное изнашивание шин; на дороге с неоднородным коэффициентом сцепления возможна потеря устойчивости.
Крутящий момент от межколесного дифференциала к каждому из ведущих колес может передаваться с помощью:
1) вала и шарниров, размещенных в приводе ведущих управляемых колес;
2) привода ведущих колес;
3) вала, соединяющего непосредственно ведущее колесо с дифференциалом.
В зависимости от схемы подшипникового узла вал ведущего колеса (полуоси) может быть или нагружен изгибающим моментом от сил взаимодействия колес с дорогой, или разгружен от таких моментов. На рис. 7.1 приведены схемы подшипниковых узлов ведущего колеса. Первая схема (рис. 7.1 а) используется в грузовых автомобилях. Благодаря тому, что подшипники несколько разнесены, изгибающие моменты от сил взаимодействия колес с дорогой воспринимаются картером, не нагружая полуось. Вторая схема (рис. 7.1 б) отличается от первой тем, что вместо двух подшипников имеется только один. В этом случае изгибающие моменты от сил взаимодействия колеса с дорогой воспринимаются совместно полуосью и картером ведущего моста. Эта схема применяется редко.
Рис. 7.1. Схемы подшипниковых узлов с полуосями:
а – разгруженной; б – разгруженной на три четверти; в – полуразгруженной.
В третьей схеме (рис. 7.1 в) полуось у внешнего конца имеет шейку, на которую установлен подшипник, расположенный во внутренней расточке картера ведущего моста. На внешнем конце полуоси крепится ступица колеса. Она отсутствует в том случае, когда полуось выполняют с фланцем, к которому крепят тормозной барабан и диск колеса. Изгибающие моменты от сил взаимодействия колеса с дорогой воспринимаются полуосью. Моменты от вертикальной Rz и продольной Rх сил незначительны, так как плечо а выполняют возможно меньшим, момент от поперечной силы Rу может достичь большой величины. По такой схеме, являющейся наиболее простой, выполняют подшипниковый узел колеса в легковых автомобилях.
Деформация полуоси при передаче крутящего момента (при кручении) характеризуется взаимным поворотом смежных сечений. Угол поворота одного сечения относительно другого называется углом закручивания
, (7.2)
где М k - максимальный крутящий момент, передаваемый полуосью;
l - расстояние от средины длины шлицев полуоси до внутреннего торца ее фланца;
G - модуль упругости при кручении G=0,85 ГПа или 0,85.×106кгс/см2;
- полярный момент инерции
;
d -диаметр полуоси.
Величину касательных напряжений в полуоси определяют по формуле:
, (7.3)
где Wр – полярный момент сопротивления при кручении .
В практике исследований деформаций и напряжений деталей автомобиля широкое применение нашли методы электротензометрии, основанные на использовании изменения электросопротивления проволочных тензорезисторов при их деформации.
Описание лабораторной установки
Основным элементом установки является исследуемая полуось с наклеенными на нее гензорезисторами (рис. 7.2.), которые соединены в мостовую электрическую схему (рис. 7.3.). При таком соединении электросопротивлений R1, R2, R3 и R4 в мостовую схему с соблюдением условия и подаче тока в одну
Рис. 7.2.Полуось с наклеенными тензорезисторами
Рис. 7.3. Схема соединения тензорезистров R1, R2, R3 и R4
R -тензорезисторы; Г- измерительный прибор
издиагоналей моста, например /1-3/, ток в другой (измерительной) диагонали /2-4/ отсутствует. При деформации полуоси тензорезисторы изменяют свое сопротивление электрическому току пропорционально деформации полуоси. Изменение сопротивления хотя бы одного из тензорезисторов прекращает приведенное выше равенство в неравенство), и в измерительной диагонали появляется ток, сила которого пропорциональна деформации полуоси. В связи с тем, что ток, возникающий в диагонали /2-4/, весьма мал, его усиливают. Усиленный выходной сигнал регистрируют с помощью осциллографа или самописца.
Блок-схема соединения тензометрического моста, усилителя и осциллографа представлена на рис. 7.4, а общая схема лабораторной установки для определения деформаций полуоси - на рис. 7.5).
Рис. 7.4. Блок-схема соединения приборов:
1 - тензомост; 2 - усилитель; 3 - осциллограф
Рис. 7.5. Схема установки для определения деформаций полуоси:
1 - домкрат, 2 - динамометр; 3 - индикатор;
4 - рычаг; 5 - стойка; 6 - полуось; 7 – указатель
При приложении усилия, передаваемого от домкрата 1 через динамометр 3 к фланцу полуоси 6, полуось, защемленная шлицевым концом, закручивается на угол, пропорциональный приложенной нагрузке. О величине угла можно ориентировочно судить по отклонению стрелки указателя 7. Отклонение стрелки пропорционально отклонению луча на экране осциллографа, фиксирующего изменение выходного тока в тензометрическом мосте.
Порядок выполнения работы
1. Включить осциллограф и тензоусилитель.
2. С помощью домкрата приложить к рычагу 4 нагрузку, соответствующую 5 (пяти) делениям индикатора (одно деление индикатора соответствует 50 Н).
3. Данные об отклонении луча гальванометра занести в табл. 7.1.
4. Повторить опыты, последовательно нагружая рычаг усилиями, соответствующими 10, 15, 20, 25 и 30 делениям индикатора. Повторить опыт три раза.
5. Вычислить средние значения отклонения луча гальванометра и занести в табл. 7.1.
6. По результатам измерений построить на миллимитровой бумаге тарировочный график h = f(M) рис. 7.6.
Рис. 7.6. Тарировочный график
7. Вычислить масштаб записи m h по выражению:
(7.4)
где а - угол наклона прямой к оси абсцисс;
К - масштабный коэффициент индикатора (К = 50 Н/дел);
1р - плечо приложения силы Р (lp = 0,5м).
8. С помощью домкрата нагружать полуось ступенчато, контролируя нагружение по перемещению луча гальванометра. Задать 5-6
значений нагрузки в пределах перемещения луча гальванометра от 0
до 35...40 мм. Повторить опыт три раза.
9. Данные об отклонении луча гальванометра занести в табл. 7.2.
Таблица 7.1
Число делений индикатора, n | Усиление прилож.
к рычагу Р, Н
![]() | Крутящий момент, действ. на полуось,
![]() | Отклонение луча гальванометра, h мм | ||||
h1 | h2 | h3 | h4 | h5 | |||
10.Пользуясь найденным масштабом записи mh, вычистить величину прикладываемого момента в каждом из опытов. Результаты занести в табл. 7.2.
11. По выражениям (7.2) и (7.3) вычислить угол закручивания полуоси и возникающие в ней напряжения. Результаты занести в табл. 7.2.
Построить графики изменения угла закручивания полуоси
и возникающих вней напряжений от величины приложенного момента (рис. 7.7).
Таблица 7.2
Отклонение луча гальванометра, h мм | Крутящий момент, прилож. к полуоси, М
![]() | Угол закручив. q | Напряжение t, МПа | ||
h1 | h2 | h3
![]() | |||
Рис.7.7. Зависимости изменения угла закручивания
полуоси и напряжения от величины приложенного момента
В отчете по данной работе должен быть приведен анализ предложенных преподавателем конструкций дифференциалов и полуосей, а также результаты измерений и расчетов по определению напряжений и деформаций в полуоси автомобиля.
Контрольные вопросы
1. Назначение дифференциалов и их классификация.
2. Особенности конструкций дифференциалов, их преимущества и недостатки.
3. Полуоси, их конструктивные особенности.
4. Состав и порядок работы лабораторной установки.
5. Влияние дифференциала на эксплуатационные свойства автомобиля.
8 Лабораторная работа №7 « РАБОЧИЕ ПРОЦЕССЫ И АНАЛИЗ КОНСТРУКЦИЙ ПОДВЕСОК»
Цель работы:изучить конструкции подвесок и научиться экспериментальному определению отдельных характеристик подвесок.
Основные положения
Под подвеской понимают совокупность устройств, обеспечивающих связьнесущей системы с мостами или колесами автомобиля. По назначению детали подвески делят на направляющее устройство, упругий элемент и гасящее устройство.
Направляющее устройство подвески передает несущей системе автомобиля силы взаимодействия колес и дороги и определяет характер перемещения колес относительно несущей системы автомобиля.
Упругий элемент (рессора, пружина, торсион) снижает динамические нагрузки действующие на автомобиль при его движении по неровностям дороги.
Гасящее устройство и трение в подвеске обеспечивают затухание колебаний кузова и колес автомобиля.
В зависимости от кинематической схемы все встречающиеся на практике подвески делятся на зависимые и независимые. При зависимой подвеске оба колеса данного моста установлены на одной жесткой оси так, что перемещение одного колеса, вызванное неровностями дороги, передается другому колесу. При независимой подвеске каждое колесо данного моста перемещается самостоятельно, независимо от другого.
Кинематические схемы подвесок
От схемы подвески зависит компоновка автомобиля, параметры плавности хода, устойчивости и управляемости, массы автомобиля и т.д.
На рис. 8.1 представлены характерные схемы подвесок. Зависимая (рис. 8.1 а) и однорычажная независимая (рис. 8.1 б) отличаются тем, что вертикальное перемещение колеса сопровождается изменением угла l,что вызывает гироскопический эффект, возбуждающий колебания колеса относительно шкворня.
В двухрычажной подвеске с рычагами равной длины - параллелограммной (рис. 8.1 в) угловое перемещение отсутствует, но значительно поперечное перемещение колеса, что ведет к быстрому изнашиванию шин и уменьшению боковой устойчивости.
В двухрычажной подвеске с рычагами разной длины (рис. 8.1 г) при l = 5...6 и гироскопический момент гасится моментом сил трения в системе, а поперечное перемещение
компенсируется упругостью шин.
Рычажно-телескопическая подвеска передних колес автомобилей - качающаяся свеча (рис. 8.1 д) обеспечивает незначительные изменения колеи, развала и схождения колес, при этом замедляется изнашивание шин, улучшается устойчивость автомобиля. Подвеска имеет один поперечный рычаг снизу, ее основной элемент - амортизационная стойка, имеющая верхнее шарнирное крепление под крылом, что обеспечивает большое плечо между опорами стойки. В верхней опоре имеется подшипник, необходимый для исключения закручивания пружины, что могло бы вызвать стабилизирующий момент и дополнительные изгибающие нагрузки. Малые размеры и масса, большое расстояние по высоте между опорами, большой ход относятся к преимуществам этой подвески. Конструктивные трудности обусловлены нагружением крыла в точке крепления верхней опоры. Такую подвеску, например, имеют передние колеса ВАЗ-2108.
Рис. 8.1. Кинематические схемы подвесок автомобилей
а - зависимой; б - однорычажной независимой; в - двухрычажной независимой с рычагами равной длины; г - с рычагами равной длины; д - независимой рычажно-телескопической; е - независимой с двухрычажной с торсионом; ж - независимой с продольным качанием
Находят применение независимые двухрычажные подвески с торсионом (рис. 8.1 е), которые по своим характеристикам близки к подвеске с рычагами разной длины. Для двухрычажной параллелограммной подвески с продольным качанием (рис. 8.1 ж) характерно продольное перемещение колес при отсутствии поперечного перемещения и наклона.
В целом к преимуществам независимых подвесок можно отнести следующие:
- возможность большого прогиба;
- уменьшение гироскопического момента;
- улучшение устойчивости и управляемости;
- уменьшение массы подвески;
- хорошая приспособляемость к неровностям дороги.
Для грузовых автомобилей наибольшее применение получили зависимые подвески (рис. 8.1 а), а для легковых - двухрычажные трапециевидные (рис. 8.1 г) и рычажно-телескопические (рис. 8.1 д), на трехосных автомобилях используют балансирный подвески, имеющие рад конструктивных исполнений [1].
При рассмотрении рабочих процессов подвески автомобиля, его представляют а виде системы, состоящей из трех взаимосвязанных частей: подрессоренной, неподрессоренной и элементов их соединения.
Подрессоренную часть автомобиля составляют кузов с кабиной, рама, двигатель, коробка передач и другие агрегаты, вес которых передается на рессоры. Те элементы, вес которых не передается на рессоры, называют неподрессоренной частью автомобиля. Это передний и задний мосты с колесами и шинами.
Основные требования к подвескам автомобилей;
- обеспечение плавности хода;
- обеспечение движения по неровным дорогам без ударов в ограничитель;
- кинематическое согласование перемещений управляемых колее, исключающее их колебания относительно шкворней;
- обеспечение затуханий колебаний кузова и колее;
- постоянство колеи, углов наклона колес и шкворней;
- надежная передача от колес к кузову продольных и поперечных сил;
- снижение массы неподрессоренных частей;
- общие требования.
Характеристики подвесок автомобилей
1. Упругом характеристика подвески.
Для удовлетворения требованиям плавности хода подвеска должна обеспечивать определенный закон изменения вертикальной реакции на колесо Rz, в зависимости от прогиба f (рис. 8.2). Эта характеристика может быть линейной или нелинейной, что определяется главным образом упругой характеристикой упругого элемента (рессоры, пружины и т.д.).
Рис. 8.2. Упругая характеристика подвески
2.Жесткость подвески С.
Отношение называю жесткостью подвески в данной точке характеристики. Жесткость представляет собой нагрузку, которую надо положить к подвеске, чтобы ее упругая деформация равнялась единице. Для сохранения оптимальной частоты собственных колебаний кузова при переменной нагрузке необходимо, чтобы жесткость подвески изменялась пропорционально приходящейся на нее нагрузке.
3. Статический прогиб подвески
Под ним понимают величину прогиба подвески под действием нагрузки от подрессоренной части на неподвижном автомобиле.
4. Частота собственник колебаний подвески .
В некотором диапазоне изменения нагрузки, близком статической f характеристики подвески должны обеспечивать оптимальную частоту колебаний: для легковых автомобилей 0,8... 1.2 Гц, а для грузовых 1,2... 1,9 Гц, что соответствует уровню колебаний человека при ходьбе. Частота собственных колебаний подрессоренной массы зависит от статического прогиба подвески:
. (8.1)
5. Коэффициент динамичности Кд.
При движении по неровным дорогам, с увеличением амплитуды колебаний подвески относительно статического положения, для предотвращения ударов в ограничитель, жесткость подвески должна увеличиваться. При этом Отношение динамической нагрузки к статической и определяет коэффициент динамичности
. (8.2)
6. Динамическая энергоёмкость подвески Эд .
Определяется площадью под кривой упругой характеристики, которая эквивалентна работе, необходимой для полной деформации упругого элемента. Для увеличения динамической энергоемкости упругая характеристика подвески должна быть прогрессивной, т.е. обеспечивать прогрессивное возрастание реакции Кzд при меньшем прогибе. Такой же коэффициент динамичности может быть получен при линейной характеристике, но при этом динамический прогиб fд чрезмерно увеличивается, что трудно обеспечить конструктивно.
7. Характеристика свободных колебаний подвески.
Возникают такие колебания после проезда дорожных неровностей и являются затухающими, так как всегда сопровождаются рассеиванием механической энергии и переходом ее в тепловую. Для ускорения затухания собственных колебаний подрессорной части автомобиля путем превращения энергии колебательного процесса в тепло, рассеиваемое в окружающем пространстве, служат амортизаторы.
Характеристика свободных затухающих колебаний рессорной подвески автомобиля показана на рис. 8.3.
Рис. 8.3. Характеристика свободных колебаний подвески:
I - ход сжатия; II - ход отдачи; Z1, Z 2, Z 3, и Z 4 – амплитуды
Порядок выполнения работы
Используя плакаты, схемы, макеты и учебные экспонаты, провести сравнительный анализ предложенных преподавателем конструкций подвесок, выделить основные их особенности. При проведении анализа выяснить, каким образом в данных конструкциях реализованы предъявляемые к ним требования.
Используя испытуемый автомобиль, определить частоту собственных колебаний кузова легкового автомобиля и построить график зависимости частоты собственных колебаний кузова от статического прогиба рессоры.
Описание лабораторной установки
В работе используется легковой автомобиль, устройство обеспечивающее вынужденные собственные колебания кузова, домкрат, секундомер, линейка.
Для получения названных характеристик подвески необходимо:
- поднять кузов автомобиля домкратом до свободного состояния рессор;
- при помощи линейки измерить расстояние от балки заднего
моста до лонжерона рамы;
- отпустить домкрат и изменить при помощи линейки статический прогиб рессоры;
- домкратом поднять кузов автомобиля и поставить на упорное
устройство;
- вывести упорное устройство из зацепления и с помощью секундомера определить частоту собственных колебаний кузова;
- провести вышеуказанные измерения для трех случаев;
1) порожний автомобиль; 2) с 50% загрузкой; 3) полностью загруженный.
Измерения провести троекратно.
Отчет по данной лабораторной работе должен содержать анализ предложенных преподавателем конструкций подвесок, их конструктивные схемы, результаты измерений и расчетов согласно заданию.
Контрольные вопросы
1. Назначение подвесок и их классификация.
2. Требования, предъявляемые к конструкциям подвесок, как они
реализуются в тех или иных конструкциях.
3. Особенности конструкций зависимых и независимых подвесок.
4. Основные характеристики подвесок, способы их получения.
Частота собственных колебаний кузова автомобиля и ее влияние на работоспособность человека.
9 Лабораторная работа №8 « ОПРЕДЕЛЕНИЕ ОЦЕНОЧНЫХ ПАРАМЕТРОВ РУЛЕВОГО МЕХАНИЗМА АВТОМОБИЛЯ»
Цель работы: закрепить знания студентов по конструкции рулевых механизмов и принципу их работы;
- ознакомиться с конструкцией стенда и методами определения оценочных параметров рулевого механизма;
- определить экспериментальные оценочные параметры рулевого механизма;
- определить техническое состояние рулевого механизма, сравнив
полученные результаты с данными, приведенными в технической и
справочной литературе.
Основные положения
В соответствии с ГОСТ 18657-73 (Автомобили. Основные агрегаты и механизмы. Термины и определения) рулевым механизмом называется часть рулевого управления автомобиля, осуществляющая передачу усилий от водителя к рулевому приводу.
К рулевым механизмам предъявляются следующие требования:
- высокий коэффициент полезного действия в прямом направлении (при передаче усилия от рулевого колеса) для облегчения управления автомобилем и несколько пониженный коэффициент полезного действия в обратном направлении для снижения ударов, передаваемых на рулевое колесо от управляемых колес при наезде на неровности дороги;
- хорошая обратимость, чтобы не препятствовать стабилизации управляемых колес;
- минимальный люфт в нейтральном положении управляемых колес (беззазорное зацепление) при обязательной возможности регулировки зазора в процессе эксплуатации, если он может возникнуть; минимальное число мест регулировки;
- обеспечение заданного характера изменения передаточного числа;
- травмобезопасность;
- общие требования: надежность, низкая стоимость, технологичность, малые габариты, малая масса и др.
Классификация и конструкция рулевых механизмов приведены в литературе [1].
Оценочными параметрами рулевого механизма являются:
- кинематическое передаточное число:
- силовое передаточное число;
- коэффициент полезного действия в прямом направлении (прямой КПД);
- коэффициент полезного действия в обратном направлении (обратный КПД);
- жесткость;
- зазор в передаче.
Кинематическое передаточное число рулевого механизма представляет собой отношение угла поворота, рулевого колеса к углу поворота вала сошки, т.е.
. (9.1)
Силовое передаточное число механизма определяется отношением моментов на валу сошки к моменту на рулевом колесе, т.е.
. (9.2)
Коэффициент полезного действия рулевого механизма в прямом направлении определяется отношением работы на валу сошки к работе на рулевом валу, т.е.
. (9.3)
Коэффициент полезного действия в прямом направлении определяется тогда, когда возмущающий сигнал передается от рулевого колеса. КПД в прямом направлении определяется легкостью управления и существенно зависит от конструкции рулевых механизмов. Наиболее высокий КПД в прямом направлении имеют шестеренчатые рулевые механизмы ( ). У остальных современных рулевых механизмов прямой КПД составляет 0,8-0,85.
Коэффициент полезного действия рулевого механизма в обратном направлении определяется отношением работы на рулевом валу к работе на валу сошки, т.е.
. (9.4)
Коэффициент полезного действия в обратном направлении определяется тогда, когда возмущающий сигнал передается от управляемых колес. Высокий КПД в обратном направлении способствует стабилизации управляемых колес, т.е. возвращению колес в нейтральное положение, однако при этом ухудшается поглощение толчков передаваемых на рулевое колесо при наезде управляемых колес на неровности.
Наиболее высокий КПД в обратном направлении имеют шестеренчатые рулевые механизмы ( ), наиболее низкий - червячные (
). При КПД в обратном направление, равном 0,5 и ниже, рулевые механизмы становятся необратимыми и стабилизация управляемых колес отсутствует.
Жесткость рулевого механизма определяется отношением момента, прикладываемого к рулевому валу, к его углу поворота при неподвижном вале сошки т.е.
. (9.5)
Зазор в передаче определяется величиной люфта рулевого вала при неподвижном вале сошки. В зависимости от типа и технического состояния рулевого механизма зазоры в передаче могут быть постоянными или переменными при различном угле поворота вала сошки. Изменение зазора в зацеплении обеспечивается за счет разной величины радиуса дуги образующей червяка (в червячном рулевом механизме) и радиуса траектории ролика или за счет конструктивных размеров сопрягаемых поверхностей.
Дата добавления: 2020-12-12; просмотров: 134; Мы поможем в написании вашей работы! |
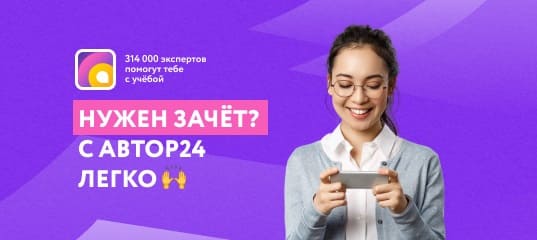
Мы поможем в написании ваших работ!