Контактный способ получения серной кислоты
Технология производства серной кислоты
На сегодняшний день серную кислоту получают двумя основными способами: контактным и нитрозным. На данный момент производство по контактному способу постепенно вытесняет производство нитрозным способом, который также называется башенным способом.
Получение кислоты в сернокислотном производстве является определенным комплексом различных химических процессов, суть которых состоит в изменении степени окисления исходного серосодержащего сырья и промежуточных продуктов производства серной кислоты.
Сернокислотное производство по любой схеме можно представить в виде определенных этапов. Начальным этапом производства будет процесс получения печного газа с оксидом серы (IV). Затем осуществляется каталитическое окисление оксида серы (IV) до оксида серы (VI) и его переработка в серную кислоту (абсорбцию) [1].
В условиях реального сернокислотного производства на практике к вышеперечисленным химическим процессам и реакциям добавляются стадии сырьевой подготовки, очистки печного газа и др. процессы. Общая схема сернокислотного производства включает в себя основные стадии производства:
Серосодержащее сырье - стадия подготовки сырья - сжигание или обжиг сырья - процесс очистки печного газа - стадия контактирования - этап абсорбции контактированного газа - выработка серной кислоты
Исходя из вида серосодержащего сырья используется конкретная технологическая схема сернокислотного производства. Также на выбор технологической схемы производства влияют особенности каталитического окисления оксида серы (IV), наличие или отсутствие этапа абсорбции оксида серы (VI) [2].
|
|
Вне зависимости от той или иной схемы и способа производства, начальным этапом будет получение сернистого газа при сжигании серосодержащего сырья. Затем осуществляют очистку печного газа, особенно при использовании контактного способа получения. Вслед за очисткой газа происходит его окисление до серного ангидрида. Серный ангидрид с водой образует серную кислоту. Так как окисление SО2 в SО3 происходит очень медленно, для интенсификации этой реакции используют катализаторы.
В контактном способе процесс окисления SО2 в SО3 происходит на поверхности зерен твердого катализатора. Процесс окисления простой, обратный, гетерогенно-каталитический, экзотермический, протекает с уменьшением объема. На данный момент около 80 % всей серной кислоты производится именно контактным способом [3].
В нитрозном способе производства серной кислоты в качестве катализатора используют оксиды азота. Окисление сернистого ангидрида протекает преимущественно в жидкой фазе и происходит в башнях с насадкой. По этой причине нитрозный способ по аппаратурному признаку также называют башенным. Производство серной кислоты башенным способом заключается в том, что произведенный при сжигании серосодержащего сырья сернистый газ, который содержит в среднем 9 % SО2 и 9-10 % О2, проходит очистку от пыли и подается в систему башен с насадками. В этой системе башен протекают различные абсорбционные и десорбционные химические процессы, и превращения. Данным нитрозным или башенным способом производят серную кислоту, которая загрязнена примесями и разбавлена 70–75 %. Произведенная кислота в большинстве случаев идет на создание минеральных удобрений [2].
|
|
В производстве серной кислоты начальным сырьем может быть элементарная природная сера, а также разнообразные серосодержащее сырье, из которых впоследствии может быть получена сера или собственно сам оксид серы для дальнейшей технологической переработки [3].
В производстве по любой схеме и способу, самыми важными стадиям будут первые две, то есть подготовка исходного сырья и его сжигание или же обжиг с целью производства технологического газа с оксидом серы. Реализация первых двух главных стадий и степень их сложности зависит от исходного сырья
|
|
Далее приведен пример сернокислотного производства из элементарной серы по короткой схеме.
Рис. 1 – Производство серной кислоты из элементарной серы по короткой схеме:
1 – плавильная камера для серы; 2 – фильтр жидкой серы; 3 – печь для сжигания серы; 4 – котел-утилизатор; 5 – контактный аппарат; 6 – система абсорбции оксида-серы (VI); 7 – холодильники серной кислоты.
Первой стадией будет подготовка сырья, то есть расплавка серы. Плавка исходной природной серы происходит с помощью водяного пара, который вырабатывается во время протекания основной реакции сжигания серы и воздуха. Температура плавления серы относительна низка и по этой причине ее без труда можно очистить от твердых частиц и механических примесей. В итоге получается жидкая элементарная сера с приемлемой степенью чистоты [4].
Процесс сжигания элементарной серы представляет собой гомогенную экзотермическую реакцию и осуществляется в газовой фазе в потоке воздух, который был предварительно высушен.
Для проведения процесса горения жидкой элементарной серы эксплуатируют форсуночные и циклонные печи. В форсуночных печных агрегатах расплавленная элементарная сера распыляется в камере топки сжатым воздухом при помощи форсунок. Однако использование форсунок зачастую не гарантирует достаточного смешивания серы с воздухом и нужной для технологического процесса интенсивности горения. Печные агрегаты циклонного типа функционируют по принципу центробежных пылеуловителей или циклонов. В печах этого типа происходит в значительной степени лучшее смешивание компонентов и повышается скорость горения серы, нежели в печных агрегатах форсуночного типа [4].
|
|
Рис. 2 – Технологическая схема печного отделения сернокислотного производства, работающего по "короткой" схеме на сере:
1, 2 – сборники жидкой серы; 3 – калориферы; 4 – циклонная печь; 5 – энерготехнологический котел РКС; 6, 7 – горелки; 8 – барабан котла; 9 – коллектор насыщенного пара; 10, 11 – погружные насосы; 12 – нагнетатель.
Обжиговый технологический газ, который получается при сжигании жидкой элементарной серы, достаточно чист и не содержит каталитических ядов, поэтому отпадает потребность в стадии очистки. Также газ обладает гораздо более высокой концентрацией оксида серы (IV) [5].
Третьей стадией производства является обратимый экзотермический химический процесс контактного окисления диоксида серы. Последним этапом производства серной кислоты является абсорбция триоксида серы концентрированной серной кислотой или абсорбция олеумом.
Контактный способ получения серной кислоты
В производстве серной кислоты контактным методом можновыделить три стадии [7]:
1) стадия получения и очистки диоксида серы (сернистого газа);
2) стадия окисления двуокиси серы до триокиси серы (серного ангидрида) в присутствии катализатора;
3) стадия хемосорбции триокиси серы с образованием серной кислоты.
Ниже рассмотрим контактный способ получения серной кислоты из серного колчедана, главным компонентом которого является пирит (FeS2), который содержит 53,3 % серы и 46,7 % железа.
Кроме FeS2 в природный колчедан входит ряд примесей (сульфиды других металлов, в том числе мышьяка и селена, а также другие минералы). В связи с этим содержание серы в колчедане может колебаться от 30 до 52 %. Обжиг серного колчедана описывается суммарной реакцией:
4FeS2 + 11O2 = 2Fe2O3 + 8SO2 + Q. (1)
В результате обжига колчедана образуется обжиговый (печной) технологический газ (в него переходит 98…99,5 % всей серы), содержащий SO2, O2, N2 и небольшое количество SO3.
Во время обжига колчедана одновременно с окислением пирита происходит также окисление сульфидов других металлов, содержащихся в нем: мышьяк и селен образуют газообразные оксиды (As2O3 и SeO2), попадающие в состав газа; в состав этого газа также входит и влага колчедана [7].
Процесс обжига является сложным, необратимым, некаталитическим, экзотермическим, гетерогенным, скорость которого отображается уравнением: r = KFΔC. Из анализа уравнения вытекают пути интенсификации процесса обжига. Для увеличения движущей силы процесса (ΔC) применяется избыток воздуха (1,2…1,8 от теоретической потребности) и обогащение колчедана методом флотации. Применение для обжига обогащенного кислородом воздуха не нашло практического использования, поскольку требует больших затрат. Для увеличения поверхности контакта (F) сульфида железа с кислородом воздуха и облегчения диффузии важнейшее значение имеет измельчение колчедана. Увеличение скорости процесса за счет роста наблюдаемой константы скорости (K) достигается повышением температуры. Оптимальное значение температуры и около 800 °С, дальнейшее ее повышение ограничивается спеканием частиц колчедана, что приводит к уменьшению поверхности контакта. При высокой температуре процесс обжига протекает в диффузионной области и для его интенсификации необходимо перемешивание, характер которого определяется типом печи, которая применяется в производстве [7].
Окисления двуокиси серы до серного ангидрида протекает на поверхности зерен катализатора по реакции:
2SO2 + O2 « 2SO3 + Q (2)
Процесс окисления – простой, обратный, гетерогенно- каталитический, экзотермический, протекает с уменьшением объема. Наибольший выход серного ангидрида наблюдается из газовой смеси примерно следующего оптимального состава: 7 % SO2, 11 % O2, 82 % N2.
Так как реакция окисления двуокиси серы обратная и образование SO3 сопровождается выделением теплоты, выход серного ангидрида (или степень превращения двуокиси серы) с повышением температуры уменьшается. Практически при 400 °С и ниже реакция окисления SO2 в SO3 необратима; при 1000 °С серный ангидрид почти полностью диссоциируется на двуокись серы и кислород. Итак, с точки зрения полноты превращения SO2 в SO3, необходимо работать при возможно более низкой температуре. Однако температурный режим контактного окисления SO2 в SO3 определяется свойствами катализатора, используемого в промышленности.
Поглощение (абсорбция) SO3 раствором серной кислоты является последней стадией производства серной кислоты. В процессе абсорбции SO3 раствором серной кислоты протекает экзотермическая химическая реакция:
SO3 + H2O = H2SO4 + Q. (3)
Наибольшую абсорбционную способность по отношению к SO3 имеет 98,3 % кислота.
С целью получения сернистого газа используют печи трех типов:
1) механических полочных, в которых колчедан перемешивается в слое;
2) пылевидного обжига с распылением колчедана в потоке воздуха;
3) с кипящим слоем колчедана.
На рисунке 5 представлена технологическая схема производства серной кислоты из колчедана контактным методом с использованием процесса двойного контактирования – двойной абсорбции (ДКДА) [8].
Рис.5 – Технологическая схема производства серной кислоты из колчедана контактным методом с использованием процесса ДКДА:
I – получение и очистка сернистого газа; II – окисление сернистого газа до серного ангидрида в присутствии катализатора; III – абсорбция серного ангидрида с образованием серной кислоты;
1,10 – нагнетатели; 2 – печь кипящего слоя; 3 – котел-утилизатор; 4 – циклон; 5 – сухой электрофильтр; 6, 7 – первая и вторая промывные башни; 8 – мокрый электрофильтр; 9 – сушильная башня; 11– контактный аппарат; 12, 13 – моногидратные абсорберы; 14 – сборники кислоты; 15 – насосы; 16 – холодильники кислоты
Наиболее совершенными реакторами для обжига колчедана являются печи кипящего слоя (КС). Интенсивность их работы примерно вдвое выше по сравнению с печами пылевидного обжига и в 10 раз выше, чем при использовании механических полочных печей.
“Кипящий” (или взвешенный, псевдоожиженный) слой образуется при пропускании воздуха снизу вверх через слой измельченного серного колчедана с такой скоростью, при которой частицы колчедана перемещаются (решаются) в потоке воздуха, но не покидают пределов кипящего слоя (не выдуваются потоком газа и не проваливаются сквозь решетку, на которую загружают колчедан). Такое состояние реагирующей системы обеспечивает интенсивное взаимодействие веществ, участвующих в реакции. При этом температура по всему объему кипящего слоя быстро выравнивается [8].
Печь кипящего слоя 2 представляет собой вертикальную полую камеру цилиндрической формы из листовой стали, футерованную изнутри огнеупорной кирпичом.
Внизу камеры размещена решетка, на которую шнековым питателем подается колчедан. Снизу через решетку и слой колчедана нагнетателем 1 подается воздух.
Обжиговый газ выходит из верхней части печи. Печь кипящего слоя по гидродинамическому режиму движения газовой фазы близка к режиму вытеснения, по твердой фазе – к режиму смешивания. По тепловому режиму печь кипящего слоя представляет собой изотермический реактор с отводом избыточной теплоты за счет введения в печь секции котла-утилизатора (на схеме он показан отдельно) [9].
В связи с большой интенсивностью работы печи кипящего слоя наблюдается значительный вынос пыли с газами (до 300 г/м3), что ухудшает технико-экономические показатели процесса за счет загрязнения аппаратуры и катализатора. Газы очищают от пыли механическим и электрическим способами (грубая очистка в котле-утилизаторе 3, циклоне 4 и электрофильтре 5). Для окончательной очистки газов от пыли и вредных примесей (соединений мышьяка, селена и паров воды) применяют мокрую очистку (промывку растворами серной кислоты в промывных башнях 6 и 7) и “мокрую” електроочистку в электрофильтре 8. Очищенный и высушенный с помощью концентрированной серной кислоты в сушильной башне 9 обжиговый технологический газ через нагнетатель 10 поступает в контактный аппарат 11.
Для обеспечения оптимального температурного режима окисления SO2 до SO3 наиболее часто используются полочные контактные аппараты с внутренним теплообменом. По гидродинамическому режиму они представляют собой каскад реакторов вытеснения с промежуточным охлаждением, по тепловому – каскад адиабатических реакторов.
Поскольку действующие контактные сернокислотные установки имеют большую единичную мощность, количество SO2, что выбрасывается с выхлопными газами, очень велика даже при использовании пятислойного контактного аппарата, где достигается степень превращения SO2 98 %. Поэтому для снижения концентрации SO2 в выхлопных газах используют процесс двойного контактирования – двойной абсорбции (ДКДА) [8].
Уменьшение концентрации SO2 при использовании процесса ДКДА достигается за счет вывода продукта реакции (SO3) из зоны реакции. Таким образом, двойное контактирование состоит из двух этапов окисления SO2 на катализаторе. На первом этапе процесса степень превращения составляет около 90 %. Перед вторым этапом контактирования из газовой смеси выделяют серный ангидрид, в результате чего равновесие реакции смещается в сторону образования SO3, то есть повышается равновесная степень превращения, что соответственно приводит к увеличению фактической степени превращения. При использовании процесса ДКДА фактическая степень преобразования составляет 99,5/99,7 % [8].
Внутри контактного аппарата находятся четыре решетки со слоем контактной массы на каждой. Под решетками установлены трубчатые теплообменники с горизонтальными направляющими перегородками.
Газы, которые поступают в контактный аппарат, последовательно проходят межтрубное пространство теплообменников, расположенных под третьим и первым слоем контактной массы, где нагреваются до 450 °С за счет теплоты газов, прошедших через контактную массу. С этой температурой газы поступают в первый, затем во второй и третий слои контактной массы. Здесь происходит экзотермическая реакция окисления SO2 до SO3, температура газов повышается, но, пройдя очередной слой катализатора, газы входят в трубное пространство соответствующего теплообменника, где отдают часть теплоты газам, поступающим на контактирование. Таким образом, с помощью теплообменников между слоями контактной массы можно достичь максимального приближения к оптимальному температурному режиму, регулируя температуру по высоте контактного аппарата [9].
После прохождения газом третьего слоя контактной массы его подают в промежуточный моногидратный абсорбер 12, где циркулирующей через сборник 14, насос 15 и холодильник 16 серной кислотой поглощается часть SO3, а затем, через теплообменники, расположенные под четвертым и вторым слоями контактной массы, в четвертый слой контактной массы. Пройдя четвертый слой контактной
массы и остыв в межтрубном пространстве расположенного под ним теплообменника до температуры 40…50 °С, газ подается в моногидратный абсорбер 13 и далее, после очистки от остатка SO2 и SO3, через выхлопную трубу выбрасывается в атмосферу.
Контактный метод имеет свои преимущества [8]:
- выработка продукта в виде чистой концентрированной серной кислоты, оптимальной и подходящей для всех потребителей;
- снижение выбросов вредных веществ производства в атмосферу с отходящими газами.
Дата добавления: 2020-12-22; просмотров: 1044; Мы поможем в написании вашей работы! |
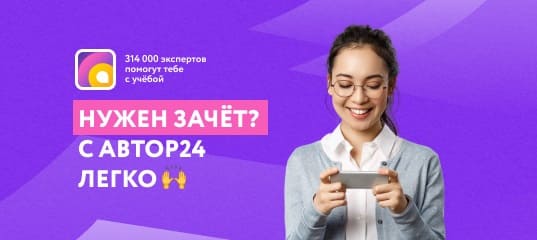
Мы поможем в написании ваших работ!