Тепловой расчет теплообменника
Технологический раздел
Технологическая схема и ее описание
Изм. |
Лист |
№ докум. |
Подпись |
Дата |
Лист |
1 |
КР 01.00 ПЗ |
Разраб. |
Коритич Н.В. |
Пров. |
Конс. |
Н.контр. |
Утв. |
Технологический раздел |
Лит. |
Листов |
2 |
71206618000 БГТУ, 2018 |
Технологическая схема промышленного производства дихлорэтана показана на рис. 1.1.В трубчатый реактор 1 подают этилен, хлорид водорода и воздух; при 483-533 К происходит реакция в присутствии катализатора хлорида меди, нанесенного на оксид алюминия или алюмосиликат. Применяется небольшой избыток этилена. В закалочной колонне 2 отделяют НСl, из которого получают кислоту. Инертные газы уходят из верхней части сборника 8, верхний слой из которого поступает в колонну 2; хлорсодержащий продукт нейтрализуют и промывают в колонне 4, а затем разделяют на легкую фракцию и дихлорэтан в колоннах 5 и 6 (секция ректификации). Кубовые остатки отводят. В колонне 5 происходит также осушка влажного дихлорэтана азеотропной перегонкой.
Рисунок 1.1. – Принципиальная схема получения 1,2 дихлорэтана оксихлорированием этилена [1]
1 - реактор; 2 - закалочная колонна; 3 - холодильник; 4 – нейтрализатор; 5, 6 – ректификационные колонны; 7 – насос; 8 – сборник; 9 - кипятильник.
Потоки: I –этилен; II –хлорид водорода; III – воздух; IV – продукт на абсорбцию; V – сточные воды; VI – вода; VII – NaOH; VIII – легкая фракция;IX – 1,2-ДХЭ; X – кубовые остатки.
|
|
У |
1.2 Сводная таблица материального баланса процесса по потокам
Материальный баланс процесса окислительного хлорирования 1,2-дихлорэтана приведен в таблице 1.1:
Таблица 1.1 – Материальный баланс стадии окислительного хлорирования 1,2 – дихлорэтана.
Входит | кмоль/ч | кг/ч | Выходит | кмоль/ч | кг/ч |
Технический этилен (поток 1): | Продукты реакции (поток 4) | ||||
СН4 | 4,52 | 72,32 | Сl2 | 1,541 | 100,1 |
С2Н4 | 369,07 | 10333,96 | N2 | 1079,29 | 30192,12 |
С2Н6 | 2,99 | 89,7 | О2 | 57,05 | 1825,6 |
С3Н6 | 0,019 | 0,8 | СО | 13 | 364 |
Итого… | 376,6 | 10496,8 | СО2 | 27,32 | 1202,08 |
Технический хлороводород (поток 2): | HCl | 7,61 | 277,8 | ||
Сl2 | 1,541 | 100,1 | H2О | 387,94 | 6982,92 |
H2 | 3,31 | 6,6 | СН4 | 4,52 | 72,32 |
N2 | 5,21 | 145,9 | С2Н4 | 7,75 | 217 |
HCl | 691,56 | 25241,9 | С2Н6 | 4,68 | 140,4 |
С2Н6 | 1,69 | 50,7 | С3Н6 | 0,019 | 0,8 |
С2Cl4 | 0,7 | 116,2 | С2Cl4 | 0,81 | 134,46 |
С2H4Cl2 | 0,63 | 62,4 | С2H4Cl2 | 340,27 | 33686,73 |
Итого… | 704,5 | 25723,8 | CCl3 CНО | 0,87 | 128,3 |
Воздух (поток 3) | CНСl=CCl2 | 0,54 | 71,01 | ||
N2 | 1073,08 | 30046,33 | |||
О2 | 285,25 | 9128 | |||
Итого… | 1358,33 | 39174,33 | |||
Всего… | 2439,43 | 75394,93 | Всего… | 1933,21 | 75394,93 |
|
|
Изм. |
Лист |
№ докум. |
Подпись |
Дата |
Лист |
1 |
КР 02.00 ПЗ |
Разраб. |
Коритич Н.В. |
Пров. |
Кон с. |
Н.контр. |
Утв. |
Механические расчеты отдельных узлов и деталей основного аппарата |
Лит. |
Листов |
9 |
71206618000 БГТУ, 2018 |
Принимаем к расчету реактор с внутренним диаметром обечайки
Dу = 3200мм (ГОСТ 9617 – 76) и толщиной футеровки 100 мм.
Диаметр реактора (в футеровке):
Dф = 3200 – 2 · 100 = 3000мм
Площадь сечения реактора:
S1 = 0,785·Dф2 = 0,785·32 = 7,1м2.
Технологический режим:
Температура процесса 220 °С;
Давление в реакторе 0,4 МПа.
Характеристика катализатора:
Средний диаметр частиц катализатора 144 мкм;
Плотность катализатора (кг/м3):
Частиц ρ = 1750; насыпная ρ н = 1050.
Для заданной производительнсти используется три реактора.
Расчет толщины обечайки
Выбор марки стали проводим на основе допустимой скорости коррозии, которая должна быть меньше или равной 0,1 мм/год для заданной среды и условий, имеющихся в аппарате.
Для корпуса, где средой является дихлорэтан, а температура корпуса составляет 220 0С, выбираем сталь 08Х18Н10Т [1]. Для этой стали при заданной температуре допускаемое напряжение составляет: [σ]=137МПа [4], скорость коррозии равняется 0,1 мм/год [2].
|
|
Толщину стенки корпуса аппарата под внутренним давлением определяем по формуле:
(2.1)
где D - наружный или внутренний диаметр обечайки, м;
Р – внутреннее избыточное давление, МПа;
- допускаемое напряжение на растяжение для материала обечайки, МПа;
- коэффициент, учитывающий ослабление обечайки из-за сварного шва, (для стали
=1, т.к. берем обечайку, изготовленную из бесшовной трубы);
ск – запас на коррозию, мм;
сокр – прибавка округления толщины детали до номинального размера, мм.
У |
Принимаем толщину обечайки 11 мм.
Допускаемое внутреннее избыточное давление рассчитываем по формуле:
,
Проверяем условие :
- условие соблюдается.
Вывод: В результате произведённых расчётов и полученных результатов принимаем толщину стенки цилиндрической обечайки 11 мм.
Расчет толщины днища
Исполнительная толщина стенки эллиптического отбортованного днища определяется по формуле 1.17 [5, с 20]:
|
|
(2.2)
где φ = 1 - для днищ, изготовленных из цельной заготовки;
D - внутренний диаметр, D = 3,2 м;
м. (2.3)
Проверяем применимость формулы для нахождения Sэ:
(Sэ - С)/D < 0,125
(0,007 – 0,002)/3,2 = 0,00156 < 0,125
Исполнительная толщина днища должна быть не меньше исполнительной толщины обечайки. Принимаем толщину днища s = 11 мм.
Допускаемое внутреннее избыточное давление:
МПа. (2.4)
Проверяем условие :
- условие соблюдается.
Вывод: В результате произведённых расчётов и полученных результатов принимаем толщину эллиптического днища 11 мм.
Расчет штуцеров, фланцев
Присоединение трубопроводов к аппарату осуществляется с помощью штуцеров.
В один реактор из трех согласно технологической схеме входят следующие потоки:
1) Технический этилен (поток I) в количестве 376,6:3 = 125,53 кмоль/ч = 0,0349 кмоль/с;
2) Технический хлороводород (поток II) в количестве 704,5 : 3 = 234,83 кмоль/ч =
= 0,0652 кмоль/с;
3) воздух (поток III) в количестве 1358,33: 3 = 452,77 кмоль/ч = 0,126 кмоль/с.
Из реактора выводится продукты реакции в количестве 1933,21 : 3 = 644,40 кмоль/ч = 0,179 кмоль/с.
Рассчитаем объемный расход газов в условияхв реакторе по формуле
(2.5)
где 22,4 – объем 1 кмоля газа в стандартных условиях, м3;
Т0, Р0 – соответственно стандартные температура и давление (Т0 = 273 К, Р0 = 0,101325 МПа);
Т, Р – соответственно температура (в К) и давление (в Па) в реакторе.
N – мольный расход газа, кмоль/ч
Этилен вводится в реактор при температуре 125 оС, тогда
м3/с
Диаметр штуцеров рассчитываем по формуле:
, (2.6)
где V – объемный расход смеси, м3/с;
ω – скорость среды в штуцере, м/с;
Тогда диаметр штуцера ввода этилена равен:
Принимаем стандартный штуцер внутренним диаметром 150 мм [5].
Технический хлороводород вводится в реактор при температуре 160 оС, тогда
м3/с
Тогда диаметр штуцера ввода технического хлороводорода равен:
Принимаем стандартный штуцер внутренним диаметром 200 мм [5].
Воздух вводится в реактор при температуре 150 оС, тогда
м3/с
Тогда диаметр штуцера ввода воздуха равен:
Принимаем стандартный штуцер внутренним диаметром 300 мм [5].
Продукты реакции выводятся из реактора при температуре 220оС, тогда
м3/с
Тогда диаметр штуцера для вывода продуктов реакции равен:
Принимаем стандартный штуцер внутренним диаметром 350 мм [5].
В химических аппаратах для разъемного соединения составных корпусов и отдельных частей применяются фланцевые соединения преимущественно круглой формы. Фланцевые соединения должны быть прочными, жесткими, герметичными и доступными для сборки, разборки и осмотра. Фланцевые соединения стандартизованы для труб и трубной арматуры и отдельно для аппаратов. Конструкции стандартных стальных фланцев для труб и арматуры показаны на
рисунке 1.1:
Рисунок 2.1– Типы фланцев
а – стальной приварной к корпусу; б – приварной встык с плоской поверхностью; в – приварной встык с выступом и впадиной; г – приварной встык с шипом и пазом (1:2,5 – рекомендуемый угол конусности)
Выбираем фланцы приварные встык с выступом и впадиной.
Основные размеры подобранных фланцев к штуцерам в таблице 2.1. (табл. 13.3, стр. 217 [4]).
Таблица 2.1 – Основные размеры подобранных фланцев к патрубкам (мм)
Патрубок | Dу | Dф | Dб | Н | h | d | Z |
1 | 150 | 260 | 225 | 46 | 15 | 18 | 8 |
2 | 200 | 315 | 280 | 53 | 17 | 18 | 8 |
3 | 300 | 435 | 395 | 54 | 18 | 23 | 12 |
4 | 350 | 485 | 445 | 54 | 18 | 23 | 12 |
Выбираем конструкцию и материал прокладки по рекомендациям по выбору прокладок, ОСТ 26-373-78.
Выбираем прокладку плоскую, которая рассчитана на Ру> 2,5 МПа, и температуры от –200 до 300.
Материал прокладок − паронит ПОН ГОСТ 481-80.
Прокладка устанавливается между уплотненными поверхностями и позволяет обеспечивать герметичность при относительно небольшом усилии затяжки болтов.
Прокладка должна отвечать следующим основным требованиям: при сжатии с возможно малым давлением заполнять все микронеровности уплотнительных поверхностей сохранять герметичность соединения при упругих перемещениях элементов фланцевого соединения (для этого материал прокладки должен обладать упругими свойствами); сохранять герметичность соединения при его длительной эксплуатации в условиях воздействия коррозионных сред при высоких и низких температурах; материал прокладки не должен быть дефицитным.
Расчет укрепления отверстий
Определение расчетных размеров:
Определение расчетного диаметра днища для цилиндрической обечайки:
м
Диаметр отверстия штуцера мм по табл. 10.2, стр. 179, [4].
Расчетная толщина обечайки (по п. 1.2):
Расчетная толщина штуцера
, (2.7)
где d – проходной диаметр штуцера, м,
p – внутреннее избыточное давление, МПа,
- допускаемое напряжение на растяжение для материала штуцера, МН/м2
( ),
- коэффициент, учитывающий ослабление штуцера из-за сварного шва, (для стали
=1, т.к. берем штуцер, изготовленную из бесшовной трубы ,
с – запас на коррозию, мм.
м,
Принимаем толщину штуцера равной 10 мм (табл. 10.2, стр. 175 [4]).
Ширина зоны укрепления в эллиптическом днище
, (2.8)
где - реальная толщина днища, м.
м
Диаметр отверстия, не требующего укрепления
, (2.9)
м.
SR = 0,0107 м– расчетная толщина цилиндрической обечайки аппарата (из п.1.2)
<
- укрепление необходимо.
Определение возможности укрепления отверстия избыточным металлом:
Расчетная площадь вырезанного сечения
, (2.10)
м2
Расчетная площадь укрепляющего сечения укрепляемой стенки
, (2.11)
где b1R – расчетная ширина зоны укрепления
, (2.12)
- расстояние от наружной стенки штуцера до ближайшего несущего конструкционного элемента на укрепляемом элементе
, (2.13)
- исполнительная толщина штуцера, м. При этом необходимо, чтобы соблюдалось условие 0,7S≤s1≤ 1,45S.
Примем утолщенный штуцер:
Dу = 350 мм, d = 412, s = 25 мм, H = 370 мм (табл. 10.4, стр. 179, [4]);
м,
м,
Следовательно,
,
Расчетная площадь укрепляющего сечения внешней части штуцера
, (2.14)
- расчетная длина внешней части штуцера, участвующего в укреплении
, (2.15)
мм принимаем конструктивно (по чертежу)
м
м2
Укрепление избыточным металлом произойдет, если выполнится условие:
,
>
- условие выполнилось.
Расчет опор аппарата
Химические аппараты устанавливают на фундаменты или специальные несущие конструкции с помощью опор.
Рис. 2.2 – Общий вид опоры
Для расчета опоры аппарата необходимо знать массу аппарата.
Масса аппарата находится по формуле:
(2.16)
где ткр – масса крышки аппарата, кг,
тоб – масса средней части аппарата, кг,
ткат – масса катализатора, кг,
mтр – масса труб змеевика, кг,
mфут – масса футеровки, кг,
Массу крышки аппарата находим по формуле:
(2.17)
где D - диаметр крышки, м,
s – толщина крышки, м,
Н – высота крышки, м
ρст – плотность стали, для стали плотность равна 7850 кг/м3 (табл. II, стр. 510, [8]), тогда
кг.
Масса обечайки аппаратаравна:
(2.18)
где D - диаметр обечайки, м,
s – толщина обечайки, м,
Н – высота обечайки, м,
ρст – плотность стали, кг/м3, для стали плотность равна 7850 кг/м3 (табл. II, стр. 510, [8], тогда
кг.
Масса катализатора
(2.19)
где V – объем катализатора, м3. Объем катализатора равен 88,7 м3.
ρна с– насыпная плотность катализатора, кг/м3. Для катализатора насыпная плотность равна 1,050 кг/м3, тогда
кг.
Масса труб змеевика равна:
(2.20)
где n – количество труб, шт, равно 327;
d – диамет труб, м, равен 0,122 м;
s – толщина труб, м, равна 0,002 м:
Нтр – высота труб, м, равна 14,4 м.
ρст – плотность стали, кг/м3, для стали плотность равна 7850 кг/м3 (табл. II, стр. 510, [8], тогда
Массу распределительной решетки принимаем равной 250 кг.
Масса футеровки аппаратаравна:
(2.21)
где Dфут - диаметр футеровки, м,
s – толщина футеровки, м,
Н – высота обечайки, м,
ρст – плотность торкретбетона, кг/м3, для бетона плотность равна 2300 кг/м3 (табл. II, стр. 510, [8], тогда
кг.
Следовательно, масса всего аппарата в рабочем состоянии будет равна:
кг.
В рабочем состоянии нагрузка на опору составит:
При гидроиспытаниях аппарат наполняется водой. Масса воды при гидроиспытаниях:
mв = 1000· 0,785 · D2 · H = 1000·0,785·3,22·14,4 = 115752 кг
Тогда максимальная нагрузка на опору равна:
(2.22)
Следовательно, по табл. 14.11, стр. 288 [5] выбираем опору цилиндрическую с Qmax = 2,5 МН.
Минимальная нагрузка на опору равна (рассчитывается для аппарата без внутреннего оборудования):
(2.23)
где g – ускорение свободного падения.
Таблица 2.2 – Основные размеры опор (тип 3, Q = 2,5 МН)
D | D1 | D2 | D3 | s1 | s2 | s3 | d | dБ | число болтов Z |
3200 | 3050 | 3420 | 3560 | 10 | 25 | 20 | 42 | М36 | 16 |
Так как высота колонны Н > 10 м, произведем расчет на ветровую нагрузку. Принимаем толщину цилиндрической стенки опоры s1= 11 мм.
В качестве материала опоры принимаем сталь ВСт 3 ГОСТ 380-88:
σв = 4604 МПа; σт = 250 МПа; Е = 2,10·105 МПа; [σ ]= 154 МПа [4].
Диаметр опоры равен наружному диаметру аппарата :
D = 3,20 + 2· 0,011 = 3,222 м.
Размеры опорного кольца:
Внутренний диаметр кольца
D1 = 3,05 м
Наружный диаметр кольца
D3 = 3,56 м.
Опорная площадь кольца
F = 0,785(D32 – D12) = 0,785(3,562 – 3,052) = 2,646 м2
Момент сопротивления изгибу опорной площади кольца:
м4
Напряжение сжатия в стенке опоры с учетом отверстия для лаза d = 0,5 м
МН/м2
Напряжение на изгиб в стенке опоры:
(2.24)
где М – изгибающий момент от ветровой нагрузки, Н·м.
Для аппаратов, имеющих по высоте постоянный диаметр и толщину стенки корпуса, расчетными сечениями являются только поперечные сечения корпуса в месте присоединения к нему обечайки опоры и сечения опоры. Изгибающий момент М определяем по формуле:
(2.25)
где Рi – ветровая нагрузка на i-м участке аппарата, Н;
hi – высота i-го участка, м.
Условно разбиваем по высоте аппарат на 3 участка по 3,6 метров, вес участка принимается сосредоточенным в середине участка; ветровая нагрузка, равномерно распределенная по высоте аппарата, заменяется сосредоточенными силами, приложенными в середине участка:
Ветровую нагрузку на i-й участок определяем по формуле:
(2.26)
где βi - коэффициент увеличения скоростного напора,
qi – нормативное значение статической составляющей ветровой нагрузки, МПа.
D – наружный диаметр аппарата, м;
hi – высота i-го участка, м.
Нормативное значение статической составляющей ветровой нагрузки
(2.27)
где qо – скоростной напор ветра для высоты над поверхностью земли до 10 м в зависимости от района установки аппарата. Город Минск расположен в I районе,
следовательно, q0 = 27 · 10-5 МПа (стр. 105, [7]),
θi – коэффициент, учитывающий возрастание скоростного напора с увеличением х i над поверхностью земли, θi = (хi/10)0.16 = (3/10)0,16 = 0,82;
с – аэродинамический коэффициент, зависящий от формы аппарата, для цилиндрического корпуса с = 0,7. Тогда
ξ – коэффициент динамичности, определяем по графику (рис. 76, стр. 105 [6]) в зависимости от параметра ε = (Т – период собственных колебаний аппарата, с);
ηi – приведенное ускорение центра масс i-го участка, м/с2.
При расчете периода собственных колебаний аппарат рассматриваем как упруго защемленный стержень. Период собственных колебаний аппарата с постоянным сечением определяем по формуле:
(2.28)
где Н – высота аппарата, м;
Q – вес аппарата, МН;
Е – модуль продольной упругости, для ВСт 3 ГОСТ 380-88 Е = 2,10·105 МПа [3];
g – ускорение свободного падения, м/с2;
I – экваториальный момент инерции площади поперечного сечения стенки корпуса аппарата, м4;
φ0 – угол поворота опорного сечения фундамента под действием единичного момента (МН ·м)-1.
Для цилиндрических аппаратов
, (2.29)
где D1 и D2 – соответственно наружный и внутренний диаметр корпуса аппарата, м.
м4
Угол поворота опорного сечения фундамента
, (2.30)
где Сφ – коэффициент упругого неравномерного сжатия грунта, для грунтов средней плотности принимаем Сφ = 100 МН/м3 [6]),
Iφ = 0,065 D34 где D3 – наружный диаметр фундаментального кольца аппарата
Iφ = 0,065 · 3,564 = 10,44 м4.
Тогда угол поворота опорного сечения фундамента равен:
.
Период собственных колебаний аппарата для максимальной силы тяжести аппарата равен:
с.
Для минимальной силы тяжести аппарата
с.
При максимальном весе аппарата:
ε =
При минимальном весе аппарата:
ε =
По рис. 76, стр. 105 [7] определяем коэффициент динамичности. При максимальном весе аппарата ξ = 1,7, при минимальном ξ = 1,5.Тогда коэффициент пульсации скоростного напора ветра
для участка 1 - m1 = 0,34
для участка 2 - m2 = 0,35
для участка 3 - m3 = 0,35
Коэффициент увеличения скоростного напора
β = 1 + ξ·m
при максимальной массе аппарата
β1 = 1 + 1,7·0,34 = 1,578
β2 = 1 + 1,7·0,35 = 1,595
β3 = 1 + 1,7·0,35 = 1,595
при минимальной массе аппарата
β1 = 1 + 1,5·0,34 = 1,51
β2 = 1 + 1,5·0,35 = 1,525
β3 = 1 + 1,5·0,35 = 1,525
Сила от ветровой нагрузки, действующей на каждый участок аппарата при максимальной силе тяжести аппарата
Р1 = 0,6·1,578·1,545·10-4 ·3,222·3,6 = 0,0017 МН;
Р2 = 0,6·1,595·1,545·10-4 ·3,222·7,2 = 0,0034 МН;
Р3 = 0,6·1,595·1,545·10-4 ·3,222·10,8 = 0,0051 МН;
при минимальной силе тяжести аппарата
Р1 = 0,6·1,51·1,545·10-4 ·3,222·3,6 = 0,0016 МН;
Р2 = 0,6·1,525·1,545·10-4 ·3,222·7,2 = 0,0033 МН;
Р3 = 0,6·1,525·1,545·10-4 ·3,222·10,8 = 0,0049 МН.
Изгибающий момент от ветровой нагрузки на аппарат относительно основания при максимальной силе тяжести аппарата:
Мв1 = 0,0017·3,6 = 0,006 МН
Мв2 = 0,0034·7,2 = 0,024 МН
Мв3 = 0,0051·10,8 = 0,055 МН
∑Мв = 0,085 МН
при минимальной силе тяжести аппарата:
Мв1 = 0,0016·3,6 = 0,006 МН
Мв2 = 0,0033·7,2 = 0,024 МН
Мв3 = 0,0049·10,8 = 0,053 МН
∑Мв = 0,083 МН
Напряжение на изгиб в стенке опоры:
МН/м2
Отношение
по этой величине находим коэффициенты (стр. 115 [7]):
kи = 0,17; kc = 0,14
Коэффициент Кс определяется по формуле:
где σт – предел текучести материала опоры, σт = 250 МПа,
Коэффициент Ки определяется по формуле:
Допускаемое напряжение на сжатие в обечайке опоры:
МПа
Допускаемое напряжение на изгиб в обечайке опоры:
МПа
Устойчивость цилиндрической опоры
≤ 1
Устойчивость обеспечена.
Изм. |
Лист |
№ докум. |
Подпись |
Дата |
Лист |
1 |
КР 03.00 ПЗ |
Разраб. |
Коритич Н.В. |
Пров. |
Конс. |
Н.контр. |
Утв. |
Расчет и подбор теплообменника |
Лит. |
Листов |
6 |
71206618000 БГТУ, 2018 |
Тепловой расчет теплообменника
В холодильнике 3 производится охлаждение продуктовой смеси от 220°С до 180°С водой с начальной температурой 25°С и конечной температурой 35°С.
Cредняя разность температур при противотоке
220 180
35 25
=185
(3.1)
Средняя температура воды
Физико-химические показатели воды при температуре tcp= 30°С:
(по табл. IV, стр. 512, [8]);
(табл. IX, стр. 516, [8]);
(табл. ХXXIX, стр. 537, [8]);
(табл. XXХIX, стр. 537 [8]).
Средняя температура газов
Определяем количество теплоты, отводимое в теплообменнике:
(3.2)
где Gг– количество продуктовой смеси, поступающей в холодильник
(равна 0,179 кмоль/с из п. 2.3);
с – молярная теплоемкость продуктовой смеси, Дж/(моль·К),
(равна 44, 3135 Дж/(моль·К));
t1и t2 – конечная и начальная температуры продуктовой газовой смеси, оС.
Определим расход воды
(3.3)
где с – теплоёмкость воды, Дж/(кг×К).
Дата добавления: 2020-11-27; просмотров: 277; Мы поможем в написании вашей работы! |
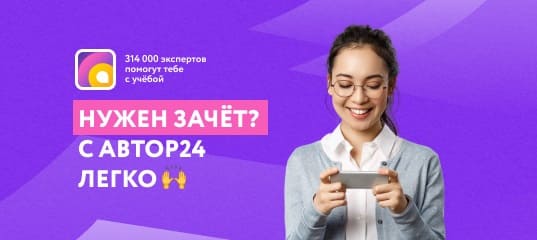
Мы поможем в написании ваших работ!