Технические требования на ремонт муфт.
Муфты всех типов.
Взможные дефекты:
1. Трещины на теле полумуфт.
2. Разработка посадочного места полумуфты
3. Износ шпоночного паза
Рекомендуемый способ устранения дефектов:
- Замена полумуфт.
- Замена полумуфт. Восстановление посадочного места стальных полумуфт путем его рассверловки, запрессовки втулки с последующей расточкой под размер.
- Строжка нового шпоночного паза на расстоянии ¼ окружности от старого паза.
Муфта втулочно-пальцевая.
Возможные дефекты:
- Износ эластичных колец пальцев
- Разработка отверстий под пальцы и эластичные элементы пальцев
- Несоосность посадочных отверстий полумуфт и отверстий под пальцы.
Рекомендуемый способ устранения:
- Замена колец. Поворот колец на 1800.
- Расточка отверстий под пальцы при спаренных полумуфтах.
- Расточка отверстий под пальцы при спаренных полумуфтах. Допускаются заглушка и заварка старых отверстий стальных полумуфт и сверление отверстий в новых местах.
Муфта зубчатая.
Возможные дефекты:
- Износ зубьев втулки и коронки.
- Образование шлама в районе зубчатого зацепления.
Рекомендуемый способ устранения:
- При износе до 20% толщины – запиловка зубьев. При большем износе – замена втулок и коронок муфт.
- Замена части или всей смазки.
Муфта дробевая.
Возможные дефекты:
- Непроектная скорость разворота ведомого ротора.
- Износ дроби.
- Износ поверхностей полумуфт.
- Небаланс полумуфты из-за разной массы дроби в ее секциях
|
|
Рекомендуемый способ устранения:
- Подбор размера дроби для обеспечения необходимой скорости разворота.
- Замена дроби при изменении скорости разворота на 25%. Ремонт полумуфт.
- Наплавка ребер полумуфты с последующей проточкой.
- Загрузка необходимого и равного по массе количества дроби.
Ремонт полумуфт
Муфты во вращающихся механизмах применяют для соединения валов электродвигателя с основным механизмом и передачи вращающего момента с одного вала на другой.
В механизмах котельных цехов чаще всего используют муфты с эластичным диском и пальцевые муфты. В современных мощных котельных установках применяют также дробевые муфты.
Муфты с эластичным диском и пальцевые муфты называют упругими, так как они допускают некоторый сдвиг валов и смягчают передачу вращения. Однако при неточной сборке и центровке валов рассчитывать на упругие муфты нельзя, поскольку они при этом подвергаются ускоренному износу и выходят из строя.
Муфты с эластичным диском (рис.1) наиболее надежны в работе, просты в изготовлении и ремонте, обладают значительной компенсирующей способностью при расцентровке валов. Полумуфты 1выполняют в виде звездочек с тремя углами, в которых расположены пальцы 3. Углы одной полумуфты сдвинуты по окружности относительно углов другой на 60°. Таким образом, для соединения полумуфт требуется шесть пальцев. Эластичные кольца 4 изготовляют из отработанных транспортерных лент или прорезиненных ремней, а для передачи небольших вращающих моментов — из листовой резины.
|
|
Рис. 1. Муфта с эластичным диском:
7 — полумуфта; 2, 6 — шайбы; 3 — палец; 4 — эластичное кольцо; 5 — шайба эластичного кольца; 7 — гайка; 8 — шплинт
Пальцевые муфты (рис.2) обеспечивают компенсацию небольших радиального и углового смещений валов за счет упругости кожаных или резиновых шайб, которые надеваются на пальцы. Вращение от одной полумуфты на другую передается пальцами. Эти муфты допускают осевые перемещения роторов и их взаимные смещения на некоторый угол по окружности, что сглаживает резкие изменения вращающего момента.
Дробевая муфта (рис.3) состоит из двух неодинаковых полумуфт. Полумуфта 1 электродвигателя выполнена в виде ступицы с двумя дисками, между которыми в диаметрально противоположных местах приварены ребра 3. Полумуфта 4, надеваемая на вал основного механизма, имеет вид стакана и надвигается на полумуфту электродвигателя. Полумуфты не соединены между собой; между их деталями должны быть зазоры в радиальном направлении 0,5—1 мм, а в осевом 2 — 3 мм. В полости полумуфты электродвигателя, образованные ребрами 3, через пробку 2 второй полумуфты засыпают дробь, нарубленную из углеродистой проволоки диаметром 5 — 6 мм.
|
|
Рис.2 1. Пальцевая муфта:
1 — полумуфты; 2 — палец; 3 — эластичная шайба; 4 — шайба; 5 — гайка
Рис.3. Дробевая муфта:
1,4 — полумуфты приводимого механизма электродвигателя; 2 — пробка для засыпки дроби; 3 — ребра
Длина кусочков 6—10 мм. в зависимости от размера муфты засыпают 4 — 6 кг дроби (равное количество во все полости).
При включении электродвигатель начинает вращаться на холостом ходу. По мере увеличения частоты вращения дробь центробежной силой отбрасывается к периферии и прижимается к внутренней поверхности стакана полумуфты приводимого механизма, обеспечивая плавную передачу вращающего момента. Количество дроби подбирается такое, чтобы время разгона приводимого ротора составляло 10-15 с.
|
|
Дробевые муфты устанавливают для привода крупных молотковых мельниц, а также центробежных и осевых дымососов.
Проверку состояния и ремонт полумуфт электродвигателей выполняет персонал котельного цеха, а снятие и установку — персонал электрического цеха.
Ремонт питателей пыли
Лопастной питатель пыли заключен в три части корпуса: верхнюю 4, среднюю 5 и нижнюю 6 (рис. 1). Верхнюю часть присоединяют к фланцу пылевого бункера 2, а нижнюю — к фланцу пылепровода. Части корпуса соединены между собой также фланцами.
Рис. 1. Лопастной питатель пыли:
1 — люки; 2 — пылевой бункер; 3 — отсекающая заслонка; 4, 5, 6 — верхняя, средняя и нижняя части корпуса; 7— главный вал; 8, 9, 12 — подающее, червячное и мерительное колеса; 10 — червяк; 11 — сальниковое уплотнение вала; 13 — крышка коробки; 14 – ворошитель.
При капитальном ремонте питателя его отделяют от пылевого бункера и пылепровода и разбирают все сборочные единицы. Для снятия, установки и перевозки питателя используют тележку с подъемным столом.
В процессе эксплуатации изнашиваются многие детали лопастного питателя. В результате истирающего действия угольной пыли изнашиваются створки отсекающих заслонок и буртики на корпусе (заслонки начинают пропускать пыль), ворошитель, подающее и мерительное колеса. Естественный износ вала, подшипников и червячного редуктора ускоряется в случае неправильной сборки питателя, применения смазки плохого качества или попадания угольной пыли.
Ремонт полумуфт, редуктора, вала, подшипников, червячной и зубчатой передач производят в том же порядке, который был описан ранее.
Лопастные колеса (подающее и мерительное) заменяют, если разработаны посадочные места или радиальные и осевые зазоры в камерах превышают 0,5 мм на одну сторону. Изношенные колеса восстанавливают наплавкой.
Чтобы повысить качество ремонта, производят контрольную сборку основных деталей на переносном стенде, при которой убеждаются в том, что зазоры в мерительных и подающих камерах лопастных колес не превышают следующих размеров: радиальный зазор — 0,75 мм, осевой — 0,5 мм.
Собранный питатель до установки на место обкатывают 1 —1,5 ч на полных оборотах, проверяя правильность сборки, температуру подшипников, отсутствие задеваний и вибрации. Вторую обкатку на холостых оборотах производят после установки питателя на место. При холостых обкатках, а также при комплексном опробовании котла в течение 24 ч тщательно проверяют работу всех сборочных единиц питателя.
От воздействия угольной пыли в шнековом питателе (рис.2) сильно изнашивается вал шнека под сальниками и подшипниками. Входной и выходной патрубки обычно повреждаются от ударов при устранении зависания пыли.
Рис. 2. Шнековый питатель пыли:
/, 5 —входной и выходной патрубки; 2 — выдвижной шибер с приводом; 3 — съемная часть корпуса с сальником; 4 — подшипник; 6— вал со спиральной лопастью (шнек); 7, 8 — части корпуса; 9 — электродвигатель; 10 — ограждение; 11 — клиноременная передача.
При разборке питателя снимают шкивы ременной передачи, затем торцевые крышки корпуса, подшипники и концевые патрубки, разбирают сальники и вынимают шнек. В случае необходимости разбирают шибер и его привод, разъединяют детали корпуса. Все детали очищают от пыли и осматривают. Кроме того, выявляют наличие истираний кромок спирали шнека и увеличения внутреннего диаметра корпуса, поломок и погнутостей спирали и отрыва ее от вала, искривления вала. Спираль заменяют обычно при износе ее на 2 мм на одну сторону, а корпус — при износе полости более 4 мм по диаметру.
Погнутые участки вала исправляют в холодном состоянии домкратами и кувалдой или в горячем состоянии после нагрева горелками. Правку вала заканчивают, если стрела прогиба в любом месте не превышает 0,25 мм.
При местном износе лопастей спирали их вырезают, при общем износе удаляют всю спираль. Заготовки для лопастей вырезают из листовой стали толщиной 5 — 6 мм по шаблону, затем их нагревают до 600 — 700 °С и придают им необходимую форму. Приварив лопасти к валу, протачивают спираль на токарном станке. Правку лопастей спирали на валу производят ударами молотка, как в холодном состоянии, так и с нагревом.
Собирают питатель в обратном порядке. При этом при сборке подшипников обеспечивают торцевой зазор в упорном подшипнике 0,15 — 0,2 мм, а в опорном — не менее 5 мм. Упорный подшипник закрепляют только после выверки шнека в корпусе. Зазор между спиралью шнека и корпусом на сторону должен быть не более 2 мм.
Собранный питатель обкатывают без пыли 1,5 — 2 ч, проверяя отсутствие заеданий, стуков, нагрева подшипников до температуры более 60 °С и повышенной вибрации.
Ремонт зубчатых передач
При ремонте зубчатых колес выполняют несложные операции: снимают заусенцы с зубьев, проверяют степень их износа, исправляют шпоночные канавки, устанавливают втулку в отверстие для вала, если оно разработано настолько, что не обеспечивает необходимой посадки.
Рис. 3.6. Проверка точности прилегания зубьев по отпечаткам краски:
а —- нормально; б — увеличено межосевое расстояние; в — уменьшено межосевое расстояние; г — оси валов перекошены
Износ зубьев цилиндрических зубчатых колес проверяют штангензубомером. Предельный допустимый износ зубьев по толщине указан в инструкциях на ремонт агрегата.
В случае значительного износа рабочей поверхности зубьев и односторонней нагрузки зубчатые колеса переворачивают, чтобы в зацеплении находился неизношенный профиль зуба. Колеса с предельным износом заменяют.
Зубчатые колеса снимают с вала стяжными скобами. Ответственной операцией, определяющей длительность работы зубчатых колес, является сборка элементов передачи. Зубчатые колеса устанавливают на валы в соответствии с посадками, указанными в чертеже.
При сборке валов с надетыми колесами проверяют параллельность осей валов (радиальные и боковые зазоры в зацеплении) и прилегание рабочих поверхностей зубьев.
Правильное положение колес контролируют по отпечаткам краски на одном колесе (обычно большом), полученным при вращении другого колеса (обычно малого), зубья которого с рабочей стороны покрыты тонким слоем краски. При вращении малого колеса на несколько оборотов одновременно притормаживают большое колесо, чтобы получить лучший отпечаток краски. По размеру и расположению отпечатка на ведомом колесе (рис. 3.6) судят о качестве сборки зубчатой пары. Высота отпечатка должна быть не менее 60 % высоты зуба. По высоте зуба пятно должно располагаться в средней части и не доходить до верхней кромки или дна впадины. При правильном расположении пятен, но недостаточном их размере, пары обкатывают, применяя абразивные пасты.
Ремонт червячных передач
Червяк представляет собой вал с зубьями в виде винтовой линии. По числу винтовых линий червяки бывают однозаходными, двухзаходными, трехзаходными и т.д. Передаточное число червячной пары равно отношению числа заходов червяка к числу зубьев червячного 66 колеса. При полном обороте однозаходного червяка колесо повернется на один зуб, двухзаходного — на два зуба и т.д.
Вследствие непрерывного скольжения зубьев червяка по поверхности зубьев колеса червячная передача работает на истирание, требует лучшей смазки и быстрее изнашивается, чем зубчатая. При ремонте червячную пару очищают от смазки, осматривают и исправляют мелкие дефекты, зачищают заусенцы на зубьях червяка и колеса, проверяют износ зубьев. Зубья червячного колеса изнашиваются быстрее зубьев червяка, поэтому в нереверсивных передачах часто переворачивают колесо на валу, заставляя зубья работать неизношенным профилем. При значительном износе червячную пару заменяют. Если заменяют только червяк или червячное колесо, новую
пару прирабатывают.
Червячные передачи требуют точной сборки, при которой контролируют радиальные и боковые зазоры, отклонения межосевого расстояния, перекос осей и смещение червяка относительно среднего сечения колеса. Радиальные и боковые зазоры в зацеплении проверяют так же, как и в зубчатой передаче. По радиальному зазору определяют высоту расположения червяка над червячным колесом, т.е. межосевое расстояние, нарушение которого вызывает повышенный износ червяка и зубьев червячного колеса. Смещение оси червяка относительно среднего сечения колеса устанавливают отвесом или линейками. Вертикальная ось червяка должна совпадать со средним сечением колеса, что определяется равенством расстояний.
Контакт зубьев собранной червячной пары проверяют по отпечаткам краски, определяя характер и размер пятен касания. На рабочую поверхность витка червяка наносят тонкий слой краски, а затем поворачивают червяк, притормаживая колесо, если оно еще не сцеплено с валом механизма. Размер отпечатка должен составлять 50 —60 % высоты и 35 —75 % длины зуба (в зависимости от точности изготовления пары). Если размер пятна недостаточен, червячную пару обкатывают. Смещение отпечатка от среднего положения указывает на неправильную сборку.
Вал червяка вместе с насаженными на него подшипниками качения должен иметь свободу для осевых перемещений. В зависимости от конструкции редуктора свобода для осевых перемещений предусматривается в одном подшипнике или в обоих. Осевые перемещения Указаны на чертеже. При установке червяка в подшипниках скольжения свобода для осевых перемещений обеспечивается зазором между буртами вала.
Дата добавления: 2020-11-15; просмотров: 1279; Мы поможем в написании вашей работы! |
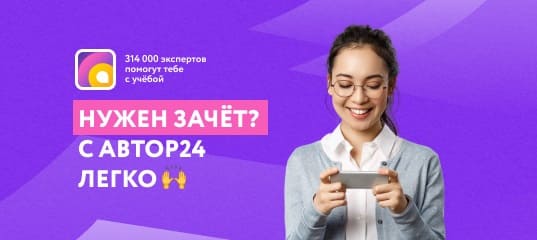
Мы поможем в написании ваших работ!