Аппаратурное оформление процессов гранулирования
Выбор аппаратуры для проведения процессов гранулировання определяется механизмом гранулообразования. Конструктивно грапуляторы различаются местом и способом подвода реагентов, формой и подвижностью корпуса (стационарный, вращающийся, вибрирующий), способом перемешивания материала (механическое пневматическое, вибрационное). Грануляторы могут coстоять из одного или нескольких аппаратов, в зависимости от последовательности различных стадий гранула образования. В аппаратах для гранулирования могут проходить и другие процессы (аммонизация, сушка, охлаждение и т. п.), что накладывает специфические особенности на конструкции различных узлов.
Конструкция гранулятора должна быть такой, чтобы в нем можно было перерабатывать как можно больше материалов в соответствии с требуемым механизмом и наименьшими затратами, т. е. требуемое качество продукта должно обеспечиваться при максимальных удельных производительностях. При этом особое внимание следует уделять стабильной работе аппарата. Длительная работа при постоянном режиме и сокращение времени на чистку, и ремонт позволяют упростить эксплуатацию не только самого гранулятора, но и вспомогательного оборудования. Надежность работы гранулятора во многом зависит от размеров и простоты конструкции а также от числа вспомогательного оборудования. Чем проще узел гранулирования, тем меньше отказов в
его работе, больше возможностей для автоматизации процесса и, следовательно, для повышения производительности труда. Компактность оборудования - это высокий выход продукта и низкие капитальные затраты. Таким образом, высокий выход продукта, снижение капитальных и эксплуатационных затрат, увеличение надежности работы оборудования (стабилизация режима и предотвращение простоев) — все это пути интенсификации работы грануляторов.
|
|
Аппараты для гранулирования методом окатывания
Грануляторы, в которых происходит окатывание материала, по типу движения поверхности делятся на ротационные, ленточные и вибрационные. Ротационные аппараты бывают барабанные, тарельчатые (дисковые), центробежные, лопастные. Барабанный гранулятор (рисунок 4.6) представляет собой горизонтальный или наклоненный под углом 1—3° в сторону выгрузки цилиндр с закрепленными на нем бандажами и венцовой шестерней, через которую передается крутящий момент от электродвигателя.
1-обечайка; 2-течка для разгрузки порошка; 3 - распределитель связующего; 4- бандаж; 5-венцовая шестерня; 6 - патрубок для отсоса паров; 7-выгрузочная камера; 8-окно для подсветки; 9-смотровое окно; 10— патрубок для выгрузки гранул; 11— опорный ролик; 12-бетонные основание; 13-редуктор; 14-элекромотор.
|
|
Рисунок 4.6 - Барабанный гранулятор.
С торцов барабан снабжен загрузочной и разгрузочной камерами, герметизирующими рабочий объем гранулятора. Через загрузочную течку вводится исходная шихта или сухой порошок. В последнем случае для подачи связующего в головной части барабана над слоем материала установлены распределители жидкости.
К распределителям жидкости предъявляют следующие требования: простота конструкции, равномерность распределении, возможность регулирования дисперсности распыла, возможность очистки во время эксплуатации. В туковой промышленности широко применяются распределитель типа «пила», представляющий собой трубу с зубчатым желобом (рисунок 4.7). Желоб снабжают, крышкой, предотвращающей попадание в него материала. Недостатком таких распределителей являетеся необходимость строго горизонтальной их установки и невозможность регулирования размера капель.
Рисунок 4.7 - Распределитель жидкости типа «пила».
Для диспергирования жидкости применяют пневматические форсунки внутреннего н внешнего смешения, работу которых регулируют изменением давления распыливающсго агента. Это давление, однако, ограничено, так как происходит размывание слоя материала струей. Поскольку для гранулирования окатыванием не требуется особенно тонкого и однородного распыливания жидкости, часто используют механические форсунки.
|
|
Для устранения налипания продукта на внутренние стенки отделения в пространство между секторными перегородками в барабане помещены металлические шары, которые удерживаются от падении упорами. При определенном положении барабана шары освобождаются от упоров и ударяются о стенки, способствуя очистке их от налипшего материала.
Для осуществления метода окатывания применяют, помимо барабанных, тарельчатые (чашевые, дисковые) грануляторы. Основной частью такого аппарата является диск, вращающийся вокруг оси, угол наклона которой к вертикали регулируется. Диск снабжен бортом. что обеспечивает требуемое заполнение аппарата (рисунок 4.8). Для подачи связующего над тарелкой устанавливают форсунки: для очистки от налипающего материала — скребки.
1 — вращающаяся тарелка; 2 —герметизирующий кожух; 3 — форсунка для подачи жидкости; 4 — патрубок для отсоса паров; 5 — смотровое окно; 6 —патрубок для подачи порошка; 7—вал; 8- механизм для изменения угла наклона тарелки; 9 -- рама.
|
|
Рисунок 4.8 - Схема тарельчатого гранулятора
Аппарат для герметизации заключен в кожух, имеющий патрубки для отвода продукта и паров и подвода порошка. Для визуального наблюдения за процессом служит смотровое окно. По сути дела, дисковый гранулятор —это барабан большого (1—5 м) диаметра и малой (0,02—0,80 м) длины, ось которого наклонена под большим (45—75°) углом к вертикали. Рабочая поверхность такого аппарата, в отличие от рабочей поверхности барабана, не боковая поверхность цилиндра, а торцовая, т. е. дно тарелки.
По форме днища грануляторы делятся на плоские, конические, сферические, эллиптические. Применение неплоских днищ позволяет избежать мертвого пространства в месте стыка с бортом и увеличить путь окатывания, т. е. производительность аппарата.
Место ввода сухих н жидких компонентов определяется требованиями к гранулометрическому составу продукта. Для получения крупных комков орошение ведут в верхней части поднимающегося слоя, а порошок загружают в нижнюю часть тарелки. Для получения более мелких гранул поднимают место ввода порошка и опускают место ввода жидкости, причем поток жидкости делят на две части. Большую часть дают в слой для образования зародышей, а меньшую на участок пересыпания крупных комков, способствуя накатке гранул.
Производительность тарельчатого гранулятора, используемого в химической промышленности, достигает 50 т/ч или, считая на поверхность тарелки, 0,5—3.0 т/(м2-ч) при удельных энергозатратах 1—5 кВт-ч/т.
Сравнивая работу барабанных и тарельчатых грануляторов, следует отдать предпочтение тарельчатым, поскольку они обладают лучшим классифицирующим действием, требуют меньше рецикла, удобны в эксплуатации, так как допускают визуальное наблюдение, возможность регулирования параметров, сравнительно легко поддаются наладке при переходе на другой продукт, имеют меньшую массу и габариты. Однако тарельчатый гранулятор не эффективен при проведении процесса, сопровождаемого химическими реакциями (например, аммонизацни), и менее удобен для удаления пыли и испарений.
Гранулирование методом окатывания можно производить в лопастном грануляторе. Конструктивной особенностью таких аппаратов является наличие одного или двух вращающихся валов с лопастями, расположенными по винтовой линии (рисунок 4.9). Валы заключены в неподвижный корпус в виде корыта или образованный пересечением двух параллельных цилиндров. В корпус подводится сухой материал, жидкость, а при необходимости и другие компоненты (пар, аммиак и др.).
1-корпус- 2-вращающийся вал; 3-лопасти; 4-загрузочная воронка; 5- распределитель жидкости; 6-выгружной патрубок.
Рисунок 4.9 - Схема лопастного гранулятора
Принцип гранулирования основан на интенсивном перемешивании и разности скоростей материала и лопастей. В двухвальном аппарате валы вращаются в противоположные стороны так, что лопатки опускаются по периферии и поднимаются, касаясь друг друга и очишаясь при этом в центре. Сухие компоненты подают в верхнюю часть аппарата между валами. В нижней части по центру аппарата под слоем материала располагают распределители реагентов. Для создания требуемой высоты слоя перед выгрузной течкой устанавливают переливные пороги. Иногда эти пороги препятствуют выгрузке крупных комков, что приводит к заклиниванию валов. Во избежание этого явления высоту слоя поддерживают, создавая подпор неравномерным расположением лопаток, расстояние между которыми сокращается от места загрузки к месту выгрузки. Стенки гранулятора очищаются концами лопаток; зазор между ними и стенкой должен составлять не более 5% от диаметра корпуса.
В лопастном грануляторе обеспечивается хорошее смешение материала и однородность получаемого продукта, вязкость которого может быть значительно большие чем в барабанных или тарельчатых грануляторах. Другим преимуществом лопастного гранулятора является возможность отклонения от рабочего режима в большей степени, чем в других аппаратах, что обусловлено самоочисткой движущихся элементов. К недостаткам лопастных грануляторов следует отнести сложность подачи компонентов под слой и трудность визуальных наблюдений.
Окружная скорость вращения лопаток гранулятора обычно не превышает 1,0-1,5 м/с. При увеличении скорости концов лопаток до 15-30 м/с резко изменяется механизм гранулообразования преобладает ударный эффект и процесс агломерации интенсифицируется: возрастает скорость роста гранул, фракционный состав становится более однородным, меньше расходуется связующего. Такие граиуляторы, названные скоростными, имеют высокие производительности, пригодны для очень вязких
материалов. Однако износ гранулирующих элсментов и энергозатраты на гранулирование несколько выше, чем в обычных грануляторах.
Кроме ротационных в промышленности применяют хотя и в меньшем масштабе, ленточные грануляторы. Аппарат в виде наклонного ленточного транспортера, движущегося вверх навстречу скатывающимся под действием собственного веса частицам работает по принципу барабана, однако менее металлоемок. Известны качающиеся вперед-назад транспортеры Транспортеры с вогнутой поверхностью и регулируемым углом наклона занимают меньшую площадь. При движении ленты гранулы по мере укрупнения скатываются вниз и, достигнув заданного размера, покидают окомкователь. Скатыванию вбок препятствуют неподвижные борта. Транспортеры часто применяют как приставку к дисковому гранулятору. Недостатком ленточного гранулятора является трудность его герметизации и необходимость частой наладки, так как лента растягивается.
Для виброгранулировання применяют аппараты с вибрирующими корпусом или отдельными деталями, помещенными в слой материала. Широкое применение получили аппараты с цилиндрической горизонтальной рабочей камерой, совершающей круговые или эллиптические колебания в вертикальной плоскости. Эти аппараты выполняют однокорпусными или двухкорпусными. Привод однокорпусных грануляторов осуществляют дебалансными вибраторами, двухкорпусных — эксцентриковыми.
Рисунок 4.10 - Конструктивные схемы виброгрануляторов с цилиндрической камерой.
Однокорпусные аппараты с одной камерой выполняют с центрально расположенным вибратором (рисунок 4.10,а), с несколькими вибраторами (рисунок 4.10,б) и с вынесенным вибратором (рисунок 4.10,в). В грануляторе с двумя камерами вибратор устанавливают в центре тяжести подрессоренной части аппарата (рисунок 4.10,г).
Выносной вибратор обычно крепят в точке, сдвинутой по окружности относительно вертикальной оси на 45°. Такое расположение вибратора вызывает вижение камеры по траектории в виде эллипса. Дополнительные поворотные колебания камеры интенсифицируют циркуляционное движение слоя и способствуют его окатыванию.
Анализируя конструкции грануляторов, в которых реализуется принцип окатывания частиц, следует отметить, что каждый аппарат имеет свои преимущества и недостатки. Выбор той или иной конструкции зависит от степени изученности процесса, технических возможностей изготовления и монтажа аппарата, подготовленности производства к эксплуатации гранулятора.
Для производства минеральных удобрений методом окатывания наиболее широко применяют барабанные грануляторы, поскольку они являются высоко производительными аппаратами, обеспечивают сравнительно высокий выход целевой фракции, возможность проведения химической реакции одновременно с гранулированием и возможность проведения процесса без загрязнения помещения. Однако следует совершенствовать и конструкции аппаратов других типов, особенно виброгрануляторов и скоростных грануляторов, позволяющих, интенсифицировать процесс гранулирования и улучшать качество продукта.
Дата добавления: 2020-04-08; просмотров: 50042; Мы поможем в написании вашей работы! |
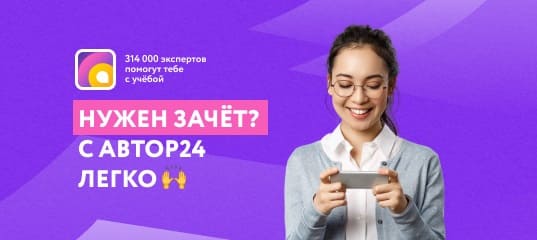
Мы поможем в написании ваших работ!