Проведение процесса электрофоретического осаждения
Электрофоретическое осаждение представляет собой направленное движение заряженных частиц дисперсной фазы суспензии в электрическом поле. На рисунке 2.6 представлена схема движения заряженных частиц суспензии.
Рисунок 2.6 – Схема движения заряженных частиц суспензии при проведении процесса электрофоретического осаждения
Нормальное течение процесса электрофоретического осаждения возможно при наличии устойчивой суспензии. Изначально в качестве растворителя суспензии использовался ацетон + этанол. Однако эксперимент оказался неудачным еще на стадии подготовки суспензии. Затем в качестве растворителя успешно был подобран изопропиловый спирт.
В случае проведения эксперимента в стеклянном стакане в растворитель опускались два электрода. Устанавливалось определенное расстояние между ними, после чего выставлялось одно напряжение. Эксперимент проводился в несколько циклов по несколько минут. После каждого цикла образец вынимали и высушивали, после чего снова опускали в растворитель и устанавливали расстояние между электродами. При этом суспензия не обновлялась, а оставалась в стакане на протяжении всего процесса.
После замены стеклянного стакана на более удобный, распечатанный на 3D-принтере, процедура проведения процесса немного изменилась. Объем нового стакана значительно меньше объема стеклянного. Поэтому теперь после каждого цикла заливалась новая партия одной и той же суспензии, а старая выливалась. Таким образом, суспензия не истощалась и постоянно сохраняла свою консистенцию. Кроме того, пропала необходимость в постоянном выставлении одного и того же расстояния между электродами, так как конструкцией стакана было предусмотрено постоянное расстояние в 10 мм.
|
|
Во время проведения экспериментов напряжение варьировалось от 50 до 150 В. Время осаждения от 5 до 50 минут в течение одного цикла. Количество циклов осаждения менялось от 1 до 5. Масса навески суспензии изменялась по нисходящей с 75 до 30 мг.
ГЛАВА 3. ЭКСПЕРИМЕНТАЛЬНАЯ ЧАСТЬ
Несмотря на то, что наиболее актуальным соединением является Al-Ni, так как горит практически без газового выделения, для проведения экспериментов был выбран состав Al-CuOx-CNT. У данного соединения не возникает проблем с инициацией воспламенения, чего нельзя сказать про соединение Al-Ni.
Сначала исследовался состав Al-CuOx без углеродных нанотрубок. Но в таком виде скорость распространения реакции горения термитного материала была слишком высока. Кроме того, зачастую материал прогорает не полностью. Именно поэтому в состав суспензии были добавлены углеродные нанотрубки. На рисунке 3.1 представлены РЭМ-изображения термитных соединений Al-CuOx и Al-CuOx-CNT соответственно.
|
|
а б
Рисунок 3.1 – РЭМ-изображения термитных соединений: а) Al-CuOx; б) Al-CuOx-CNT
Как видно из рисунка 3.1 углеродные нанотрубки выступают как связующий компонент между осаждаемыми материалами. Тем самым снижают скорость распространения реакции горения. Данное утверждение было проверено экспериментально.
3.1 Экспериментальное исследование процесса осаждения с составом Al - CuOx
Было проведено несколько экспериментов с составом Al-CuOx + изопропиловый спирт. По результатам выявлена зависимость веса осадка от напряжения и построен график, который представлен на рисунке 3.2.
Рисунок 3.2 – Зависимость веса осаждаемого материала Al-CuOx от напряжения
Эксперименты проводились при напряжении от 10 до 160 В с шагом 10 В. На графике точками обозначены выборочные результаты измерения при 10, 30, 70, 100 и 160 В. Каждое измерение проводилось одним циклом по пять минут. По графику можно сделать вывод, что зависимость веса от напряжения практически линейная.
Кроме того, была проведена раскадровка горения термитного материала Al-CuOx, которая представлена на рисунке 3.3.
|
|
Рисунок 3.3 – Раскадровка видеосъемки горения термитного материала Al-CuOx
Скорость распространения фронта реакции составляла 4,2 м/с и определялась высокоскоростной видеокамерой. Нужно отметить, что скорость достаточно высока по сравнению с составом Al-CuOx-CNT, который будет рассмотрен далее.
3.2 Экспериментальное исследование процесса осаждения с составом Al - CuOx - CNT
Изначально в качестве растворителя для суспензии был взят ацетон + этанол. Однако суспензия получилась неравномерной, и осаждения не произошло.
Затем растворитель был заменен на изопропиловый спирт. Была рассчитана навеска в стехиометрическом соотношении Al:CuOx – 1:2. Взяли 25 мг алюминия и 50 мг оксида меди. Туда же был добавлен 1 мг углеродных нанотрубок. Было проведено два цикла осаждения по четыре минуты каждый при напряжении 70 В. Готовый образец под номером 69 был отправлен на РЭМ. Результаты РЭМ-исследования приведены на рисунке 3.4.
а б
в г
Рисунок 3.4 – РЭМ-изображения образца под номером 69 Al-CuOx-CNT в разных масштабах
|
|
Как видно из результатов исследования, слишком мало нанотрубок осело на образец. В результате образец не загорелся. В связи с этим было решено взять меньшее количество навески, но сохранить стехиометрическое соотношение и количество нанотрубок.
В новом эксперименте было взято 15 мг алюминия и 30 мг оксида меди. Масса углеродных нанотрубок осталась прежней (1 мг). Было увеличено подаваемое напряжение до 100 В. Осаждение проходило одним циклом в течение десяти минут. РЭМ-изображения образца под номером 112 представлены на рисунке 3.5.
а б
в г
Рисунок 3.5 – РЭМ-изображения образца под номером 112 Al-CuOx-CNT в разных масштабах
С тем же составом суспензии был проведен эксперимент с образцом под номером 117. Однако напряжение было увеличено до 150 В, а количество циклов до шести. Каждый цикл длился по пять минут. РЭМ-изображения образца под номером 117 представлены на рисунке 3.6.
а б
в г
Рисунок 3.6 – РЭМ-изображения образца под номером 117 Al-CuOx-CNT в разных масштабах
Оба образца равномерно хорошо покрылись углеродными нанотрубками по сравнению с образцом под номером 69. Однако и в этот раз ни один из образцов не загорелся. Возникло предположение, что проблема кроется в стехиометрическом соотношении компонентов суспензии. Чтобы выяснить соотношение осажденного материала на образцах, пришлось обратиться к результатам элементного анализа термитного материала, которые представлены на рисунке 3.7.
а
б
Рисунок 3.7 – Элементный анализ термитного материала Al-CuOx-CNT двух образцов: а) образец 112; б) образец 117
Как видно из элементного анализа больше всего в процентном соотношении осело алюминия. Количество алюминия от общего осадка составляет около 30%.
Как уже упоминалось выше, проблема могла крыться в стехиометрическом соотношении. Исходя из данного умозаключения, решено было уменьшить навеску и сделать соотношение Al:CuOx = 1:1, оставив при этом массу алюминия в составе 15 мг и уменьшив массу оксида меди также до 15 мг. Масса углеродных нанотрубок остается неизменной (1 мг).
Был проведен эксперимент с новым стехиометрическим соотношением, но напряжение осталось неизменным. Был проведен процесс с образцом под номером 128 также, как и с образцом под номером 112, одним циклом в течение 10 минут. РЭМ-изображения образца под номером 128 представлены на рисунке 3.8.
а б
в г
Рисунок 3.8 – РЭМ-изображения образца под номером 128 Al-CuOx-CNT в разных масштабах
На изображениях видно, что материал ложится равномерно и казалось бы, должен воспламениться. Но и в этот раз эксперимент завершился неудачно. В чем же проблема? Рассмотрим элементный анализ, который представлен на рисунке 3.9.
Рисунок 3.9 – Элементный анализ термитного материала Al-CuOx-CNT образца под номером 128
Из элементного анализа видно, что алюминий составляет около 45% от общей массы осадка. Проведя сравнительный анализ всех образцов, было выдвинуто предположение, что стехиометрический состав должен быть в соотношении Al:CuOx=2,5:3,5 с сохранением общей массы навески. Таким образом, для следующего эксперимента была подготовлена суспензия с массой алюминия, равной 12,5 мг и массой оксида меди, равной 17,5 мг.
Кроме того, было выдвинуто предположение, что толщина осадка слишком тонкая. Именно поэтому образец два раза был взвешен на высокоточных измерительных весах. Первый раз без осадка перед проведением эксперимента, второй – после проведения. Разница двух измерений показала массу осадка, которая равняется 3,2 мг.
Чтобы увеличить толщину осадка, было решено провести более длительный процесс. Именно поэтому эксперимент с образцом под номером 135 проводился в течение 20 минут при том же напряжении в 150 В. А эксперимент с образцом под номером 136 – 50 минут одним циклом. На рисунке 3.10 представлены РЭМ-изображения образца под номером 135.
а б
Рисунок 3.10 – РЭМ-изображения образца под номером 135 Al-CuOx-CNT в разных масштабах
Для сравнения на рисунке 3.11 представлены РЭМ-изображения образца под номером 136.
а б
Рисунок 3.11 – РЭМ-изображения образца под номером 136 Al-CuOx-CNT в разных масштабах
На обоих образцах материал распределился достаточно равномерно. Но из-за разницы в длительности процесса толщина осадка равномерно поменялась. В первом случае эксперимент длился 20 минут, во втором – 50 минут, то есть в 2,5 раза длиннее. Масса осадка на образце под номером 135 равняется 2,4 мг, на образце под номером 136 – 5,6 мг. Почти так же в 2,5 раза больше. Соответственно и толщина осадка в 2,5 раза больше, так как площадь осаждения одинакова. Исходя из вышеперечисленных данных, можно сделать вывод, что толщина осадка линейно увеличивается с увеличением длительности процесса.
Так каков должен быть вес осадка, чтобы эксперимент дал положительный результат? Оказалось, что 2,4 мг слишком мало, так как образец 135 не загорелся. Но зато вспыхнул образец под номером 136, который имеет осадок весом 5,6 мг. Казалось, эксперимент наконец-то удался. Но осадок прогорел не полностью, а лишь наполовину. Тогда было решено провести контрольный эксперимент.
Уже было ясно, что состав суспензии и стехиометрия подходящие. Задача была лишь в том, чтобы осадок получился тяжелее 5,6 мг. Для этого было решено не увеличивать время проведения процесса. Оставить те же 50 минут, но разбить их на 5 циклов по 10 минут каждый. И, в отличие от предыдущих экспериментов, после каждого цикла выливалась суспензия и наливалась в стакан новая с тем же составом. Это должно было решить проблему, так как за 50 минут суспензия истощается практически полностью. И спустя какое-то время материал уже не осаждается. Электрод просто погружен в растворитель, но процесс не идет. Поэтому для осаждения более толстого слоя было решено перед каждым новым циклом заливать в стакан новую суспензию. И это решение оказалось верным. На рисунке 3.12 представлены РЭМ-изображения образца под номером 141.
а б
Рисунок 3.12 – РЭМ-изображения образца под номером 141 Al-CuOx-CNT в разных масштабах
Образец под номером 141 имеет осадок массой 11,1 мг. Это в два раза выше, чем предыдущий, 136 образец. И уже в этот раз образец вспыхнул и полностью прогорел. Эксперимент можно считать удачным. Нанотермитный материал был получен методом электрофоретического осаждения. И его можно использовать в качестве инициатора вторичной реакции.
В таблице 3.1 представлена сравнительная характеристика всех образцов.
Таблица 3.1 – Сравнительная характеристика образцов
Номер образца | Al, мг | CuOx,мг | U, В | Время, с | Кол-во циклов |
69 | 25 | 50 | 70 | 4 | 2 |
112 | 15 | 30 | 100 | 10 | 1 |
117 | 15 | 30 | 150 | 5 | 6 |
128 | 15 | 15 | 150 | 10 | 1 |
135 | 12,5 | 17,5 | 150 | 20 | 1 |
136 | 12,5 | 17,5 | 150 | 50 | 1 |
141 | 12,5 | 17,5 | 150 | 10 | 5 |
Как видно из таблицы, лучшими характеристиками для инициации реакции являются соотношение Al:CuOx = 2,5:3,5 при общей навеске в 30 г, напряжение 150 В, время проведения процесса 5 циклов по 10 минут каждый с заменой суспензии после каждого раза. Именно при таких характеристиках воспламенился термитный материал Al-CuOx-CNT, коим является образец под номером 141.
Была проведена видеосъемка горения данного образца, после чего сделана раскадровка. Также была определена скорость горения термитного материала. Раскадровка представлена на рисунке 3.13.
а б в
г д
Рисунок 3.13 – Раскадровка видеосъемки горения термитного материала Al-CuOx-CNT со скоростью распространения фронта реакции: а) 0 мс; б) 0,08 мс; в) 0,16 мс; г) 0,23 мс; д) 0,31 мс
Скорость распространения фронта реакции составляет 0,31 м/с. Это в 13,5 раз ниже, чем скорость распространения фронта реакции при горении термитного материала без углеродных нанотрубок, о которых упоминалось выше.
Выводы
Таким образом, экспериментальным путем было доказано предположение о том, что при добавлении углеродных нанотрубок скорость распространения фронта реакции снижается (4,2 м/с без нанотрубок и 0,31 м/с при их добавлении).
Был выбран оптимальный состав суспензии для проведения эксперимента и подобрана стехиометрия навески. В итоге экспериментальным путем получен термитный материал Al-CuOx-CNT с массой, равной 11,1 мг. Осаждение длилось в течение пяти циклов по 10 минут каждый. Данный образец можно использовать в качестве инициатора вторичных реакций.
Заключение
В настоящее время активно исследуются термитные материалы для различных применений в микро и наноэлектронике, так как привлекают интерес со стороны исследователей по всему миру.
В последнее время термитные материалы все чаще формируют методом электрофоретического осаждения. Данный метод не требует дорогих установок и является простым в исполнении. Успех процесса зависит от заранее выбранных компонентов в правильном стехиометрическом отношении.
В нашем случае соотношение получилось Al:CuO = 2,5:3,5 (12,5 мг алюминия и 17,5 мг оксида меди) при добавлении 1 мг углеродных нанотрубок. Проведя серию экспериментов при достаточно высоком напряжении, равном 150 В, были выявлены оптимальные условия осаждения. Пять циклов по 10 минут каждый с постоянным обновлением суспензии. Именно в таком режиме осаждается достаточно толстый слой, который хорошо воспламеняется. При таких параметрах получается готовый нанотермитный материал, который можно использовать в микроэлектронике в качестве инициатора вторичных реакций.
Также экспериментальным путем было доказано, что при добавлении углеродных нанотрубок (CNT) в состав Al-CuOx скорость распространения фронта реакции снижается. В нашем случае очень существенно, в 13,5 раз.
Список литературы
1. Laxmidhar Besra, Meilin Liu // A review on fundamentals and applications of electrophoretic deposition (EPD) // Progress in Materials Science. – 2007. – P. 3-16.
2. Hamaker HC // Formation of deposition by electrophoresis // Trans Farad Soc. - 1940. – Vol. 36 – P. 79–83.
3. Heavens N. // Electrophoretic deposition as a processing route for ceramics. In: Binner GP, editor // Advanced ceramic processing and technology, vol. 1. Park Ridge (NJ), USA: Noyes Publications. – 1990. - P. 83.
4. Zhitomirsky I. // Cathodic electrophoretic deposition of ceramic and organoceramic materials – fundamental aspects // Adv Colloid Interface Sci. – 2002. - Vol. 97 – P. 279–317.
5. Sato N, Kawachi M, Noto K, Yoshimoto N, Yoshizawa M. // Effect of particle size reduction on crack formation in electrophoretically deposited YBCO films //Physica C. – 2001. – P. 357–360.
6. Sarkar P, Nicholson PS. // Electrophoretic deposition (EPD): mechanisms, kinetics and application to ceramics // J Am Ceram Soc. – 1996. – P. 79.
7. Chen F, Liu M. // Preparation of yttria-stabilised zirconia (YSZ) films on La0.85Sr0.15MnO3 (LSM) and LSM – YSZ substrate using an electrophoretic deposition (EPD) process // J Eur Ceram Soc. – 2001. – Vol. 21 – P. 127.
8. Negishi H, Yanagishita H, Yokokawa H. // Electrophoretic deposition of solid oxide fuel cell material powders. In: Proceedings of the electrochemical society on electrophoretic deposition: fundamentals and applications // Pennington, USA – 2002. – Vol. 21 - P. 214.
9. Ferrari B, Moreno R. // The conductivity of aqueous Al2O3 slips for electrophoretic deposition // Mater Lett – 1996. – Vol. 28 – P. 353.
10. Ferrari B, Moreno R. // Electrophoretic deposition of aqueous alumina slip // J Eur Ceram Soc. – 1997. – P. 17.
11. Basu RN, Randall CA, Mayo MJ. // Fabrication of dense zirconia electrolyte films for tubular solid oxide fuel cells by electrophoretic deposition // J Am Ceram Soc. – 2001. – P. 33–40.
12. Wang Y-C, Leu I-Chi, Hon M-H. // Kinetics of electrophoretic deposition for nanocrystalline zinc oxide coatings // J Am Ceram Soc. – 2004. – P. 87.
13. Zhitomirsky I, Gal-or L. // Electrophoretic deposition of hydroxyapatite // J Mater Sci Mater Med. – 1997. – P. 8.
14. Vandeperre L, Van Der Biest O, Clegg WJ. // Silicon carbide laminates with carbon interlayers by electrophoretic deposition // Key Eng Mater (Pt. 1, Ceramic and Metal Matrix Composites) – 1997. – P. 127–131.
15. Sarkar P, De D, Rho H. // Synthesis and microstructural manipulation of ceramics by electrophoretic deposition // J Mater Sci. – 2004. – P. 39.
16. Daixiong Zhang, Xueming Li // Fabrication and Kinetics Study of Nano-Al/NiO Thermite Film by Electrophoretic Deposition // The journal of physical chemistry – 2015. – P. 4688-4689.
17. Kaili Zhang, Carole Rossi, Marine Petrantoni, Nicolas Mauran // A Nano Initiator Realized by Integrating Al/CuO - Based Nanoenergetic Materials withan Au/Pt/Cr Microheater // Journal of microelectromechanical systems – 2008. – P. 832-833.
Дата добавления: 2020-01-07; просмотров: 127; Мы поможем в написании вашей работы! |
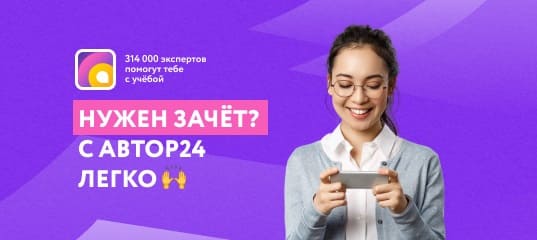
Мы поможем в написании ваших работ!