Способы изготовления углерод-углеродных композиционных материалов
Решение задачи упрочнения матрицы в целях приближения ее прочности при повышенных температурах к высокому температурному сопротивлению углеродных волокон привело к появлению углеродной (или графитовой) матрицы и композиционных материалов на ее основе.
Новый класс высокотемпературных материалов, получил название углерод-углеродных композиционных материалов. Пространственное армирование резко повышает сопротивление этих материалов к действию нестационарных температурных напряжений.
Суть процесса изготовления композиционных материалов класса углерод-углерод состоит в создании армирующего каркаса, введении в каркас матрицы с последующим уплотнением, карбонизацией и графитизацией.
Армирующие каркасы. Одной из главных задач при создании многонаправленных каркасов является укладка армирующих волокон выбранного типа и объема в направлениях, предусмотренных расчетом.
Реальный объем волокон в каркасе всегда значительно ниже расчетного. Обусловлено это тем, что нити не имеют правильной формы поперечного сечения, принятой при расчете, и элементарные волокна немонолитны.
Методы изготовления каркасов различны, среди них – ткачество сухих нитей, прошивка тканей, сбор жестких пучков (из нитей), намотка нитью, а также комбинация этих методов. Наибольшее распространение получил метод ткачества сухих нитей. Он приемлем для изготовления как самых простых так и наиболее сложных многонаправленных каркасов. При этом используют нити малого диаметра с плотной их укладкой (рисунок 6.18), что обеспечивает получение малых пустот и высокой плотности каркаса.
|
|
![]() | ![]() |
Рисунок 6.18 – Типичная схема укладки волокон малого диаметра в ортогонально-армированном материале | 1 – радиальные нити; 2 – осевые; 3 – окружные Рисунок 6.19 – Расположение нитей в трехнаправленном цилиндрическом переплетении |
Метод ткачества сухих нитей применим и для создания каркасов цилиндрической формы. Тканые каркасы этого типа показаны на рисунке 6.19. Обеспечение постоянной плотности армирования цилиндрических каркасов с увеличением расхождения радиальных нитей при приближении к наружному диаметру достигается за счет увеличения диаметра осевых пучков нитей (рисунок 6.20) или за счет введения в основную систему армирования радиальных элементов разной длины (рисунке 6.19). Изготовляют такие каркасы на ткацких станках. Возможно создание и других, более сложных структур.
Многонаправленные каркасы могут быть созданы и из одних предварительно ужесточенных волокон (прутков), Прутки получают методом пультрузии из однонаправленно уложенных высокопрочных углеродных волокон и фенольных связующих.
|
|
Недостатком таких каркасов является отсутствие целостности до введения связующего, преимуществом – высокая степень заполнения арматурой.
![]() | Рисунок 6.20 – Схема трехнаправленной цилиндрической структуры, набранной из подэлементов: осевых (x), радиальных (z), окружных (у) | Дальнейшее развитие этого метода привело к созданию отдельных под элементов, из которых получают каркас. Примером может служить создание цилиндрического каркаса (рисунок 6.20). Радиальное армирование представляет собой предварительно изготовленные подэлементы — материалы из графитовых нитей и фенольных связующих. Эти радиальные подэлементы образуют решетку с пазами в окружном и осевом направлениях, которая укладывается на цилиндрическую оправку. В образовавшиеся пазы заматывается предварительно пропитанная лента из однонаправленных графитовых волокон. При этом окружные слои чередуются с осевыми. После намотки каркас подвергается отверждению, затем осуществляется процесс создания углеродной матрицы. |
Матрицы (композиционные материалы). Создание углеродной матрицы является одним из сложных и наиболее важных этапов в технологическом процессе производства материалов, класса углерод-углерод. Поэтому большое внимание на этом этапе уделяется не только технологическим операциям (пропитке, отверждению, карбонизации и графитизации), но и выбору исходного материала матрицы.
|
|
Определяющими показателями при выборе исходного материала матрицы, как правило, являются вязкость, выход кокса, микроструктура кокса и кристаллическая структура. В качестве исходного материала матрицы наибольшее распространение получили термореактивные фенольные и фурфуроловые смолы, а также пеки из каменноугольной смолы или нефти. Структуры кокса стекловидные и не графитизируются вплоть до 3000 °С.
Рассмотренные типы исходных материалов используют для формирования углеродной матрицы в армирующем каркасе методом жидкофазного насыщения. Сущность его сводится к следующему. Армирующий каркас пропитывают в вакууме реактивной смолой или расплавом каменноугольного или нефтяного пека.
В некоторых случаях в целях заполнения всех пор в каркасе в процессе пропитки создается давление. Далее происходит отверждение и термообработка до завершения процесса отверждения.
Детали, пропитанные пеком, не отверждаются, а подвергаются карбонизации в атмосфере азота. Карбонизацию насыщенных смолой или пеком армирующих каркасов проводят при 650…1100°С с заданной и контролируемой скоростью нагрева. Следующим этапом в формировании углеродной матрицы является графитизация проводимая обычно в индукционной печи при 2600…2750 оС. Скорость нагрева для каждого цикла, определяется размерами и формой армирующего каркаса (заготовки). Все этапы неоднократно повторяются до получения материала необходимой плотности при наличии минимальной пористости.
|
|
Одним из необходимых условий, исключающих пористость, является полная пропитка каркаса, которая' особенно затруднена при пропитке его смолами высокой вязкости. С увеличением плотности материала пористость снижается. Остаточная пористость составляет 8…10% при плотности 1,6…1,65 г/см3. Высокая плотность материала (порядка 1,7 г/см3) достигается многократным повторением всех этапов цикла: пропитки, отверждения, карбонизации и графиизации.
Повышение плотности материала может достигаться также за счет увеличения выхода кокса с исходного материала матрицы. Одним из существенных факторов, способствующих этому, является создание изостатического давления при карбонизации пека.
Создание углеродной матрицы может осуществляться также химическим осаждением на армирующий каркас из газовой фазы (метана или природного газа) с последующей графитизацией полуфабриката. Процесс включает в себя диффузию газа, содержащего активный углерод, через армирующий каркас таким образом, чтобы осаждением получить однородную матрицу. На свойства матрицы влияет множество факторов: армирующий каркас, теплопроводный кожух, несущий углерод, транспортный газ, температура, давление и скорость продувки, равномерность и эффективность процесса.
Используют три вида химического осаждения – изотермический, термического градиента и перепада давления. В изотермическом процессе субстрат нагревают излучением через углеродный кожух индукционной печи. Углеродный и транспортный газы вводят во внутреннюю полость формуемого тела и для насыщения «продувают» через нагретый армирующий каркас. Обычно процесс проводят при пониженном давлении. В ходе его образуется равномерный осадок на волокнах каркаса, и за время одного цикла сам каркас покрывается поверхностной коркой. В целях достижения высокой плотности композиционного материала поверхностную корку между циклами следует удалять механически.
Вопросы для самоконтроля
- Методы получения армирующих элементов для композиционных материалов: стеклянного, углеродного, базальтового, органического волокона.
- Способы изготовления углерод-углеродных композиционных материалов.
- Способы изготовления армирующих каркасов.
- Создание углеродной матрицы.
Дата добавления: 2020-01-07; просмотров: 260; Мы поможем в написании вашей работы! |
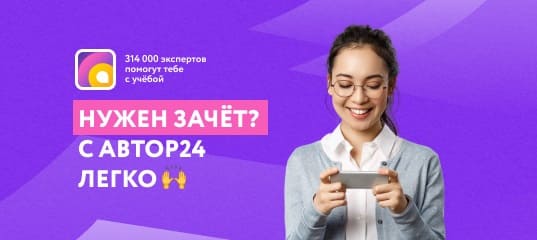
Мы поможем в написании ваших работ!