Изготовление деталей из резиновых материалов
Основным видом сырья для резиновых технических деталей являются синтетические каучуки. Сырьем для получения синтетических каучуков являются нефть, нефтепродукты, природный газ, древесина. Резину получают вулканизацией каучука. В качестве вулканизирующего вещества обычно применяют серу. Количество серы определяет эластичность резины. Мягкие резины содержат 1-3% серы, твердые (эбониты) до 30%. Для улучшения физико-механических и эксплуатационных свойств резиновых технических изделий в состав резиновых смесей вводят различные компоненты: наполнители, мягчители, противостарители, вулканизаторы, красители и др.
Наполнители уменьшают расход каучука, улучшают эксплуатационные свойства деталей. В качестве наполнителей используют сажу, тальк, мел, ткани, стальную проволоку и др. Мягчители (парафин, канифоль, стеариновая кислота и др.) вводят для обеспечения мягкости и морозоустойчивости. Противостарители (вазелины, ароматические амины) вводят для замедления процесса старения. Вулканизаторы (оксид цинка и пр.) используют для ускорения процесса вулканизации.
Технологический процесс изготовления резиновых технических деталей (ремней, шлангов, сальников, манжет, муфт, амортизаторов, транспортерных лент, уплотнений и пр.) состоит из приготовления резиновой смеси, формования и вулканизации.
Приготовление резиновой смеси заключается в смешении входящих в нее компонентов в червячных или валковых смесителях.
|
|
Формование резиновых изделий осуществляется методами выдавливания, прессования, литья под давлением и др.
Выдавливание используют для получения профилированных резиновых изделий (труб, прутков) и осуществляют машинами червячного типа.
Прессованием изготавливают манжеты, уплотнительные кольца, клиновые ремни и пр. Применяют горячее и холодное прессование. При горячем прессовании резиновую смесь закладывают в горячую прессформу и прессуют на гидравлических прессах с обогреваемыми плитами при температуре 140-150°С. при этом одновременно происходит формообразование и вулканизация детали.
Холодным прессованием получают детали из эбонитовых смесей. После прессования, полученные этим способом, заготовки отправляют на вулканизацию. Вулканизация является завершающей операцией при изготовлении резиновых деталей. Вулканизацию проводят в специальных камерах-вулканизаторах при температуре 120-150 °С в атмосфере водяного пара при небольших давлениях. В процессе вулканизации происходит химическая реакция серы и каучука, в результате которой увеличивается прочность изделия.
Вопросы для самоконтроля
- Изготовление деталей из резиновых материалов. Сырьё для получения резиновых технических деталей.
- Формование резиновых изделий.
Производство композиционных материалов
|
|
Все технологические способы получения полуфабрикатов и изделий из металлических композиционных материалов можно условно разделить на четыре основные группы: парогазофазные, жидкофазные, твердожидкофазные и твердофазные.
Основой для производства полуфабрикатов и изделий из композиционных материалов всеми способами служат однослойные ленты с одним рядом армирующих волокон или тканей, пропитанных или покрытых материалом матрицы с одной или с обеих сторон.
Парогазофазные способы характеризуются низкой производительностью процесса, поэтому применять их для компактирования композиционного материала нецелесообразно.
Жидкофазные способы используют на всех стадиях производства композиционных материалов – от полуфабрикатов до изделий. К ним относятся: протяжка волокон, жгутов и тканей через расплав материала матрицы для пластифицирования волокна, пропитка полученных пакетов материалом матрицы, плазменное, и другие виды газотермического напыления металлов для получения полуфабрикатов, подвергаемых последующей обработке давлением.
|
|
Применяют два способа пропитки:
- самопроизвольную пропитку$
- пропитку под давлением.
Самопроизвольную пропитку осуществляют путем заливки расплавленного материала в форму с уложенным в ней каркасом из армирующих волокон. Пропитку под давлением используют при недостаточной смачиваемости в системе матрица-волокно или для ускорения процесса пропитки для компонентов с удовлетворительной и хорошей смачиваемостью.
Твердожидкофазные способы используют для получения полуфабрикатов и изделий из композиционных материалов методами горячего прессования, волочения и прокатки. Прессование осуществляется в интервале кристаллизации сплава материала матрицы.
Твердофазные способы используют для компактирования изделий из полуфабрикатов ковкой, прокаткой, импульсным прессованием, диффузионной сваркой.
Получение армирующих волокон
Армирующими элементами в композиционных материалах, как было сказано в гл. 3, являются волокна, жгуты, ленты, ткани, листы. Жгуты, ленты, ткани изготовляют из волокон (рисунок 4.16).
![]() | а – стеклонити; б – углеродные нити; в – базальтовые нити; г – органические нити Рисунок 4.16 – Волокна армирующих элементов |
Получение стеклянных волокон. Технология производства стеклянного волокна включает операции подготовки шихты, варки стекломассы и получения волокна. Подготовка компонентов шихты включает сушку, помол, классификацию любых природных минералов, а также стеклобоя.
|
|
Для получения стекловолокна в основном применяют щелочесодержащие составы стекол. Основными сырьевыми материалами, как и в производстве обычного стекла, являются кварцевый песок, известняк, доломит, мел, а в качестве щелочесодержащих компонентов – кальцинированная сода, поташ и др.
Стекловарение ведут в печах с электро- или газовым нагревом. Стеклонити для композиционных материалов получают двухстадийным способом. На первой стадии стеклянное сырье расплавляют и распыляют аналогично металлическим порошкам.
При охлаждении образуются микросферы.
На второй стадии их вновь расплавляют и через фильеры, расположенные на дне тигля, вытягивают отвердевшие стеклонити, наматываемые на вращающийся барабан.
Существует также одностадийный способ производства стеклянных волокон, когда фильеры устанавливают непосредственно в печь, в которой получают стекломассу. Отказ от стадии изготовления микросфер удешевляет производство, но ухудшает качество волокон. Из рубленых стекловолокон изготовляют вату и маты для фильтров и теплоизоляции.
Получение углеродных волокон. Углеродные волокна обычно получают термической обработкой химических или природных органических волокон, при которой в материале волокна остаются главным образом атомы углерода.
Температурная обработка состоит из нескольких этапов.
Первый из них представляет собой окисление исходного (полиакрилонитрильного, вискозного) волокна на воздухе при температуре 250°С в течение 24 ч.
После окисления следует стадия карбонизации – нагрева волокна в среде азота или аргона при температурах 800…1500°С.
В результате атомы кислорода, водорода, азота и других элементов «выжигаются», а углеродная цепочка полимерной молекулы остается.
Процесс термической обработки заканчивается графитизацией при температуре 1600…3000°С, которая также проходит в инертной среде. В результате количество углерода в волокне доводится до 99%.
Для повышения термоокислительной устойчивости углеродных волокон на их поверхности создают защитные слои или барьерные покрытия из карбидов кремния или тугоплавких металлов, нитрида бора, фосфатных стекол и др. Армирующие углеродные волокна подвергают поверхностной обработке – окислению или металлизации – с целью повышения адгезии к полимерам или металлам соответственно.
Углеродные волокна выпускают в разнообразном виде:
- резаные;
- короткие и непрерывные нити;
- тканые и нетканые материалы.
Наиболее распространенный вид продукции – жгуты, пряжа, ровинги, нетканые холсты.
Производство базальтового волокна. Сырьем для производства базальтового волокна является базальтовая крошка с размерами фракций 3…10 мм.
![]() | Принципиальная схема получения базальтового волокна представлена на рисунке 4.17. Исходное сырье 1 в виде отмытой базальтовой крошки, пропущенной через магнитные сепараторы, загружают в плавильную печь 2. Расплавленная при температуре 1450…1500°С масса подается на фильерную пластину 3, откуда под действием сил гравитации расплавленный базальт в виде отдельных струек 4 стекает на раздувочное устройство 5. После раздува базальтовое волокно 6 попадает в камеру волокноосаждения 7 и ложится на приемный конвейер 8 в виде ковра 9. |
Производство органоволокон. Различные виды органических химических армирующих волокон, нитей и волокнистых материалов на их основе: технические нити – полиэфирные, поливинилспиртовые и др.; параарамидные высокопрочные и высокомодульные волокна и нити, метаарамидные термостойкие волокна для некоторых видов термостойких материалов получают методами экструзии на предприятиях химической промышленности.
Можно указать еще на несколько способов получения армирующих нитевидных элементов для композитов. Это растягивание нитей, намораживание струи расплава на вращающийся барабан, кристаллизация из расплавов и растворов, охлаждение на нити-подложки.
Дата добавления: 2020-01-07; просмотров: 258; Мы поможем в написании вашей работы! |
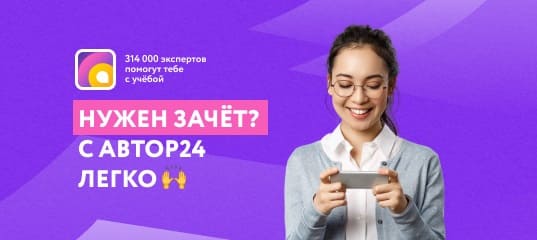
Мы поможем в написании ваших работ!