Технология изготовления деталей из пластмасс
Технология изготовления деталей из пластмасс имеет ряд специфических особенностей, связанных с природой материала. В ряде случаев в технологическом процессе получения изделий одновременно проходят процессы фopмoo6paзовaния и процессы получения пластмассы как конструкционного материала. Выбор метода переработки зависит от природы материала, от желаемых показателей физико-механических, диэлектрических, оптических и других свойств изделия. Пластмассы могут находиться в вязко-текучем, высокоэластичном и в твердом состояниях, поэтому целесообразно рассмотреть методы переработки пластмасс в изделия, классифицируя их по физическому состоянию материала на стадии формообразования изделия и физической характеристики процесса.
Методы переработки пластмасс в вязко-текучем состоянии требуют, как правило, при формообразовании изделий одновременного действия тепла и давления. К этим методам относятся прессование, литье под давлением, экструзия, каландрирование и т. д.
Прямое (компрессионное) горячее прессование. Такое прессование заключается в непосредственном приложении внешнего давления к прессматериалу, находящемуся в нагретой замкнутой прессформе (рисунок 5.33). Прессматериал под влиянием температуры и давления переходит в вязкотекучее состояние и заполняет полость прессформы. После отверждения и снятия давления готовое изделие извлекают из прессформы.
|
|
Отверждение является результатом реакции полимеризации. Для изготовления деталей из термопластичных пластмасс требуются не только давление и предварительный нагрев, но и последующее охлаждение в прессформе до отверждения. прямое прессование применяют для изготовления деталей простой конфигурации из термореактивных пластмасс.
Прессматериал применяют в виде порошка, гранул или таблеток. Дозировку проводят по массе, объему или поштучно. Применение предварительно отформованных холодным прессованием таблеток упрощает и ускоряет дозировку, позволяет проводить предварительный подогрев, ускоряет удаление летучих веществ. Предварительный подогрев осуществляют токами высокой частоты.
![]() | 1 - матрица; 2 - выталкиватель; 3 - готовая деталь; 4 - изоляция; 5 - нагревательный элемент; 6 - обойма; 7 - пуансон. Рисунок 5.33 Прессформа для компрессионного прессования |
Инструментом при компрессионном прессовании является прессформа (рисунок 5.33), состоящая из матрицы 1, заключенной в обойму 6 пуансона 7, нагревательного элемента 5 с изоляцией 4. После выдержки готовую деталь 3 извлекают из прессформы с помощью выталкивателя 2. Прессформы могут быть одногнездовыми (для изготовления одной детали) или многогнездовыми.
|
|
Перед загрузкой прессматериала прессформы тщательно очищают, смазывают и, если необходимо, устанавливают металлическую арматуру. Давление увеличивают постепенно, доводя до требуемой величины в зависимости от марки прессматериала.
Литьевое прессование. При литьевом прессовании перевод прессматериала в вязко-текучее состояние осуществляется в отдельной камере, вне формующей полости матрицы (рисунок 5.34). При этом пуансон применяют не для формования детали, а для выдавливания прессматериала из загрузочной камеры 2 прессформы 3 в рабочую полость 5 через литник 4. При литьевом прессовании давление в рабочей полости значительно выше, чем при прямом, и составляет 150…200 МПа.
![]() | 1 - пуансон; 2 - загрузочная камера; 3 - прессформа; 4 - литник; 5 - рабочая полость; 6 - выталкиватель Рисунок 5.34 Схема литьевого прессования |
Литьевое прессование имеет ряд преимуществ перед прямым прессованием:
- не происходит смещения и деформации металлической арматуры;
- равномерно прогретый прессматериал, обладающий хорошей текучестью, позволяет получать детали с глубокими отверстиями и различной толщиной стенок;
- уменьшаются напряжения и деформации сокращается цикл изготовления деталей.
Литьевое прессование применяют для изготовления деталей сложной конфигурации с глубокими отверстиями и полостями из высокопластичных термореактивных пластмасс.
|
|
Прессование листов и плит из слоистых пластмасс (гетинакса, текстолита, стекловолокнита и т.д.).
Листы бумаги или слои ткани, пропитанные смолами и высушенные, укладывают на металлические пластины в виде пакета. Несколько пакетов, изолированных друг от друга металлическими полированными листами со специальной смазкой, устанавливают на плиты пресса.
Для подогрева прессуемого материала пар подают в паровые рубашки рабочих плит пресса. После поджатия пакетов вспомогательными плунжерами пресса постепенно повышают давление до необходимой величины. Смола под действием температуры и давления плавится и склеивает в сплошной лист или плиту отдельные слои ткани. Одновременно в результате химических реакций происходит отверждение смолы.
После выдержки под давлением пакеты охлаждаются водой до 30…40°С, поступающей по трубам к рабочим плитам пресса. Пресс разгружают, пакеты отделяют от прокладочных пластин. Обрезку кромок осуществляют на дисковых пилах или ножницах.
|
|
Литье под давлением. Применяют для получения изделий из термопластичных пластмасс на специальных литьевых машинах –термопластоавтоматах.
На рисунке 5.35 приведены принципиальные схемы литья под давлением. Гранулированное сырье из бункера 7 подается плунжером 6 в цилиндр 5, где происходит пластификация материала с помощью электронагревателя 4. Прессующий поршень 8 подает порцию сырья в зону нагрева и порцию пластифицированного материала через сопло 3 и литниковые каналы в рабочую полость пресс-формы для формирования детали 2.
![]() |
Предварительная пластификация материала в отдельном нагревательном цилиндре и его перемешивание с помощью шнека 9 повышают однородность материала, заливаемого в прессформу, и улучшают качество изделий. Конечное давление на пластифицированную массу материала зависит от вязкости массы и составляет 50…250 МПа.
Методом литья под давлением можно получать изделия сложной формы, с разной толщиной стенок, с ребрами жесткости, с резьбами и т. д.
Литье под давлением является высокопроизводительным технологическим процессом, позволяющим применять комплексную механизацию и автоматизацию.
Экструзию или непрерывное выдавливание, применяют для получения труб, лент, различных профилей из термопластичных и термореактивных пластмасс, для нанесения защитных оболочек на провода и т. д.
Экструзионное формование проводят на специальных машинах – зкструдерах (червячных прессах). Пресспорошок, поступающий из бункера в рабочий цилиндр, продвигается шнеком через несколько зон обогрева и его доводят до пластифицированного состояния, а затем выдавливают через отверстие заданной формы в мундштуке и охлаждают в специальных устройствах.
Вопросы для самоконтроля
Дата добавления: 2020-01-07; просмотров: 95; Мы поможем в написании вашей работы! |
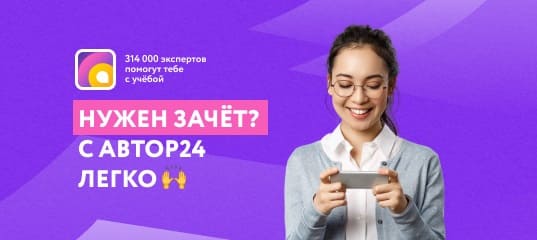
Мы поможем в написании ваших работ!