Способы получения резинотехнических изделий
Технологический процесс изготовления сырых резиновых смесей включает следующие операции: подготовка ингредиентов, приготовление их смеси и получение полуфабрикатов путем каландрирования, в результате чего сырая резина приобретает форму листов или лент определенной толщины. Из резиновых смесей различными способами изготавливают изделия, заключительной операцией для которых является вулканизация. Изделия из сырых резин изготавливают прессованием, литьем под давлением и на специальных (дерновых) станках.
Прессование проводят на гидравлических прессах при давлении 5 – 10 МПа. Прессование может быть холодным, после чего отпрессованные детали подвергают вулканизации, или горячим, при котором процессы формования и вулканизации протекают одновременно. Прессованием изготавливают уплотнительные кольца, клиновые ремни, муфты и др. детали.
Литьем под давлением изготавливают детали из разогретой резиновой смеси под давлением 30 - 150 МПа. При необходимости для упрочнения резиновых изделий их армируют проволокой, нитями и сетками.
На специальных станках изготавливают сложные изделия, которые представляют собой композиционные материалы на основе резины. К таким изделиям относятся покрышки колес транспортных машин, рукава, бронированные шланги. Они получаются путем последовательной намотки на полый металлический стержень слоев резины, а также изолирующих и армирующих материалов в виде тканей и проволок. Вулканизация может быть горячей и холодной. В первом случае процесс осуществляется в котлах или прессах, машинах и аппаратах непрерывного действия при 130 - 150°С под давлением в среде горячего воздуха, водяного пара, горячей воды или расплава соли. Во втором случае детали изготавливают из сырой резины, в которой отсутствует сера и она вводится в обрабатываемую деталь специальными способами.
|
|
Марочный ассортимент резин очень разнообразен. По назначению резины подразделяются на резиныобщего назначения, предназначенные для производства шин, приводных ремней, лент и т.п. и специального назначения (масло -, бензо -, тепло -, морозостойкие, фрикционные, диэлектрические и др.).
Прорезиненные ткани
Предназначенная для изготовления и ремонта шин ткань, как и резина, определяет эксплуатационные качества и стоимость шин. Масса ткани составляет 30-35 % массы всей покрышки, а стоимость ее составляет примерно 25 % стоимости всех других материалов.
При изготовлении и ремонте покрышек и бескамерных шин применяют в основном прорезиненные кордовыеткани, состоящие из прочных нитей основы и слабых, редко расположенных нитей утка, а также различные ткани полотняного переплетения, например,чефер, представляющий собой техническую (грубую) ткань из одних и тех же нитей с одинаковым строением основы и утка. Из корда изготавливают каркас покрышки, являющийся ее основой, а чефер используют при изготовлении крыльев и усилительных ленточек бортов покрышки.Прорезиненный корд, как и листовая резина, поступает закатанным в рулоны на деревянных или картонных роликах с полиэтиленовой пленкой. Толщина резинового слоя должна быть 0,2 - 0,3 мм
|
|
Ткань с уткомсостоит из крученых нитей 1 основы и тонких, редко расположенных поперечных уточных нитей 2 (рис. 6.1, а). У безуточного корда (рис. 6.1, б) поперечных нитей нет.
|
|
Рис. 4.1. Ткань корда: а - с утком; б - безуточная; 1 - нити основы; 2 - уточные нити
Такое строение ткани корда позволяет после пропитки составом покрыть резиной каждую отдельную нить, изолировав их одну от другой резиновой прослойкой, что предохраняет нити от быстрого перетирания, снижает трение и теплообразование, придает каркасу покрышки прочность и эластичность.
Лучшим является корд, который более прочен при одном и том же калибре нитей, имеет меньшее удлинение, более эластичен, теплостоек и влагостоек, создает меньшие потери на трение и обеспечивает хорошее обрезинивание.
|
|
Качество корда зависит от типа используемых волокон, которые подразделяются на искусственные (вискозное) и синтетические(капрон, найлон и др.).
Искусственные волокна получают в результате химических превращений природных высокомолекулярных соединений (клетчатки или целлюлозы), а синтетические - из синтетических высокомолекулярных соединений (капролактама, полиэфирной смолы и др.).
Вискозный кордпочти не изменяет прочность при температурах до 100°С. Недостатками вискозного корда являются пониженное сцепление с резиной, повышенная гигроскопичность и заметное (до 40 %) снижение прочности при увеличении влажности.
Полиамидный кордиз капрона и найлона превосходит вискозный по качеству. Капроновое волокно не гниет, отличается устойчивостью к истиранию и к действию многократных деформаций, теплостойкостью (плавится при 215°С), имеет низкую разнашиваемость.
Применение капронового и найлонового корда сокращает расход каучука при изготовлении автомобильных шин примерно на 15%, увеличивает срок их службы на 30-40 %, а также уменьшает потери на качение. Недостатком капронового корда является значительное упругое удлинение нити, что способствует разнашиваемости каркаса. Однако качество химических волокон непрерывно совершенствуется и создаются новые более совершенные их виды. В частности, перспективным является кордиз синтетического полиэфирного волокна, который, имея такую же высокую прочность, отличается высокой эластичностью, теплостойкостью, усталостной прочностью (в 1,5 - 2 раза выше, чем у вискозы).
|
|
Широкое применение находит металлокорд, который изготавливают из стальных тросиков толщиной 0,5 - 1,5 мм, свитых из проволоки диаметром 0,1 - 0,25 мм. Стальная металлическая проволока, применяемая для металлокорда, намного превосходит прочность нитей из искусственных волокон. Прочность металлокорда практически не снижается при повышенных температурах. Он обладает высокой теплопроводностью и незначительной разнашиваемостью. Шины с металлокордом на автомобильных дорогах с усовершенствованным покрытием служат примерно в 2 раза дольше обычных. Недостатками металлокорда являются невысокая усталостная прочность и повышенная стоимость.
Для изготовления бортовых колец покрышек применяют четырех -, шести -, восьми - и десятипрядную проволочные плетенки, а также одиночную проволоку. Диаметр проволоки, составляющей основу плетенки, равен 1,0 - 1,2 мм. Для предохранения от коррозии и лучшего сцепления с резиной проволоку покрывают латунью.
При ремонте автомобильных шин наряду с резинами и тканями применяют пластыри, манжеты, протекторную профилированную резину и резиновый клей.
Пластыри представляют собой крестообразные заплаты из прорезиненного корда и применяются для усиления поврежденных участков каркаса при ремонте сквозных повреждений покрышек.
Манжетами называют куски каркаса, вырезанные из покрышек, непригодных к ремонту, и соответствующим образом обработанные. Их также применяют для ремонта сквозных повреждений каркаса покрышек.
Протекторная профилированная резина предназначена для восстановления изношенного протектора покрышек. Она имеет трапецеидальное поперечное сечение, размеры которого зависят от размера и способа восстановления, и длину, несколько больше длины окружности покрышки.
Резиновый клей применяется при ремонте для промазки поврежденных мест покрышек и камер, а также для промазки ремонтных материалов. Приготавливают его путем растворения клеевой саженаполненной резиновой смеси в бензине.
Дата добавления: 2020-01-07; просмотров: 198; Мы поможем в написании вашей работы! |
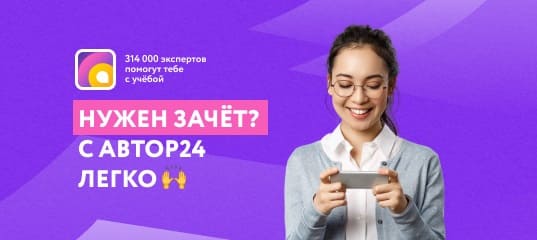
Мы поможем в написании ваших работ!