Формование прессованием и пропиткой в замкнутой форме
Методы прессования и пропитки наполнителя в замкнутой форме относятся к закрытым методам формования и позволяют с высокой точностью фиксировать толщину изделия, а также обеспечивают получение высококачественной поверхности.
При прессовании (рис. 4.13, а) на пуансон 2, укрепленный на неподвижной плите 1 пресса, укладывают необходимое число слоев наполнителя 3. Связующее 4 под давлением матрицы 5, укрепленной на подвижной плите 6 пресса, распределяется по всей полости формы, пропитывая наполнитель.
Метод пропитки наполнителя в замкнутой форме (рис. 4.13, б) состоит в том, что непропитанный сухой наполнитель 2 выкладывают послойно на пуансоне 1. После этого пуансон 1 и матрица 3 смыкаются, сжимая наполнитель до окончательных размеров изделия. Герметичность полости формы достигается установкой уплотняющего кольца 4. Благодаря разрежению, создаваемому в полости формы, полимерное связующее засасывается из бака 5 и пропитывает наполнитель. Метод используется при формовании различных оболочек, емкостей и других изделий, для которых требуется высокое качество.
Рис. 4.13. Схемы формования изделий:
а – прессование; б – пропитка
Формование намоткой
Формование изделий намоткой наиболее современный и перспективный метод формования изделий из АП, так как позволяет создавать ориентируемую структуру наполнителя в изделиях с учетом их формы и особенностей эксплуатации. Высокая прочность изделий, полученных намоткой, достигается благодаря ориентированной укладке наполнителя, и, как следствие этого, реализуются высокие прочностные свойства наполнителя в изделии.
|
|
Детали, изготовливаемые методом намотки, как правило, должны иметь форму тел вращения. В сочетании с другими приемами этим методом можно получать детали, не имеющие форму тел вращения, например, детали коробчатой формы, пластины и плиты, заготовки рабочих и статорных лопаток и даже панелей крыла.
Наибольшее применение метод намотки нашел в ракетной технике и авиации для формирования корпусов ракет и ракетных двигателей, а также элементов фюзеляжей самолетов и вертолетов.
Детали формуют с помощью технологической системы, состоящей из намоточного станка, технологической оправки для формования детали, приспособления для раскладки материала, материала из длинномерных армирующих волокон и полимерного связующего.
Давление формования создается в результате технологического натяжения наматываемого материала.
Оборудование для намотки можно разделить на две группы: машины периодического действия, которые предназначены в основном для формования оболочек самых различных форм, и машины непрерывного действия для производства труб.
|
|
Рис. 4.14. Типы намотанных станков:
а – с возвратно-поступательным движением раскладчика; б – с вращением раскладчика; в – с неподвижным раскладчиком и оправкой, вращающейся в двух плоскостях
Наиболее просты по устройству станки (рис. 4.14, а) с вращающейся оправкой 1 и возвратно-поступательно движущимся раскладчиком 2, с которого наполнитель подается на оправку.
В станках планетарного типа (рис. 4.14, б) раскладчик вращается в плоскости, составляющей небольшой угол с осью оправки. На таких установках оправки вращаются в основном с малыми скоростями. Наконец, станки третьей группы, применяемые для формования небольших изделий, имеют оправку, вращающуюся в двух плоскостях (рис. 4.14, в). В этом случае раскладчик неподвижен.
Формование деталей методом намотки обладает рядом преимуществ перед другими методами: высокий коэффициент использования прочности и жесткости армирующих волокон, возможность механизации и автоматизации процесса, хорошая воспроизводимость свойств деталей.
В зависимости от способа нанесения полимерного связующего на армирующий наполнитель различаются два способа намотки: мокрый (жидкофазный) и сухой (твердофазный).
|
|
Мокрыйметод позволяет совместить операцию приготовления АП с техпроцессом изготовления изделия. По этому способу непрерывный волокнистый наполнитель поступает в ванну с жидким связующим, пропитывается им, а потом укладывается на оправку по заданной программе. Достоинством метода является большая степень достигаемой анизотропии. Ограничение – скорость намотки определяется скоростью пропитки, а недостатком является неоднородность распределения наполнителя и связующего по толщине изделия (3 – 4 %).
Сухой метод предполагает намотку заранее пропитанного полимерным связующим армирующего наполнителя (препрега). Этот метод более прогрессивен и технологичен. Достоинства метода – более однородное распределение связующего и наполнителя по толщине (1 %), возможность применения больших скоростей намотки, использование связующих с высокой вязкостью. Недостатки – повреждение волокон на промежуточных операциях приготовления препрега и ограниченная длина лент препрега.
В зависимости от структуры наматываемого слоя армирующего наполнителя различают поперечную (кольцевую) и спиральную намотки.
|
|
Поперечная намотка характеризуется укладкой армирующего наполнителя вокруг оправки с шагом смещения вдоль оси на каждый оборот не свыше ширины наматываемой пряди. Кольцевая намотка является наиболее простым методом и не требует сложного оборудования. Пропитанные нити в виде одинарной пряди или множества прядей накладывают на оправку под углом 90° к оси вращения оправки. Кольцевая намотка применяется для усиления тонкостенных металлических труб или баллонов в тангенциальном направлении. Изделия имеют высокую прочность в тангенциальном (окружном) направлении и низкую в осевом направлении.
Способ спиральной намотки характеризуется шагом смещения траектории укладываемого наполнителя на каждый оборот оправки свыше ширины наматываемой пряди.
Как правило, шаг намотки многократно превышает ширину пряди. Необходимое соотношение прочности изделия в осевом и окружном направлениях обеспечивается назначением соответствующего угла намотки. Способ позволяет изготавливать изделия типа труб, цилиндров с овальными днищами, шаровых оболочек, конусов, торов.
Для намотки изделий из АП используются специальные или модернизированные токарные станки. В зависимости от технологического варианта намотки кинематическое исполнение станков подразделяется на два типа: токарное и планетарное.
Формование и отверждение, а иногда и механическая доработка изделий выполняются на оправках, которые должны удовлетворять конструкторско-технологическим требованиям: точность размеров изделий, прочность оправки, механическая извлекаемость изделия, возможность установки нагревателя в оправке.
Оправки многократного использования выпоняются из стали или сплавов алюминия. Для большинства изделий конструкция оправки разборная. Для фасонных изделий и оболочек крупных размеров экономически оправданным бывает изготовление оправок однократного использования из гипса, алебастра, солей, легкоплавких сплавов. Единственно возможным условием изготовления ряда изделий замкнутого контура является использование расплавляемой или растворяемой внутри него оправки. В некоторых случаях оправка не извлекается и образует совместно с намотанным материалом единое изделие.
Пултрузия
Пултрузия – технологический процесс формования длинномерных профильных деталей в результате непрерывного протягивания армирующего материала, пропитанного связующим, через формующую нагретую фильеру. Этот процесс аналогичен процессу экструзии, в котором заготовка продавливается через формующую фильеру под действием давления, создаваемого в экструдере. При пултрузии материал протягивается через фильеру под действием внешней силы, создаваемой тянущим устройством.
Рис. 4.15. Пултрузионный агрегат
На рис. 3.15 представлена схема метода пултрузии. Со шпулярника 1 волокно поступает в пропиточную ванну 2 и затем в формующую матрицу, где отжимается от избытка связующего, сжимается в поперечном направлении и приобретает конфигурацию изделия. В камере термообработки 4 происходит окончательное отверждение полимерной матрицы. Изделие охлаждается по заданному режиму в камере охлаждения 5 и затем поступает на резательное устройство 7. Движение изделия происходит с помощью тянущего (транспортирующего) блока 6.
В методе пултрузии важным конструктивным элементом является матрица (рис. 4.16), которая состоит из распределительной плиты 1, в расположенные по контуру изделия фильеры которой поступают пропитанные волокна 2 и происходит предварительный отжим связующего. Далее волокна через губку охлаждаемой плиты 3 попадают в горячую зону матрицы 5, в которой необходимая температура создается внешними нагревателями 8 и контролируется термопарой 6. Стальные колонны 9 обеспечивают жесткость конструкции формующей матрицы, а теплоизоляционный слой 7 разделяет холодную и горячую зоны. В конструкции матрицы имеется дорн 4, обтекаемый потоком ориентированных пропитанных волокон на холодном участке тракта формообразования.
Рис. 4.16. Формующая матрица пултрузионного агрегата
Многое в свойствах изделия зависит от правильности выбора матричной конструкции. По свойствам пултрузионные изделия превосходят детали, полученные контактным формованием, они более монолитные, более кислото- и щелочестойкие. Строгий контроль натяжения волокна позволяет увеличить прочность даже при наиболее опасном для пултрузионной технологии межслойном сдвиге. Она на 30 – 35 % превышает аналогичный показатель материалов с войлочной структурой наполнителя, полученных вакуумным формованием.
Армирующий материал (жгуты, нити или тканые ленты) последовательно проходит через ванну с жидким связующим, пропитывается, сжимается и поступает в матрицу предварительного формования, а затем в обогреваемую пресс-форму, где фиксируется требуемая конфигурация и отверждается полимерное связующее. В матрице предварительного формования плоская по форме лента пропитанного материала постепенно преобразуется по сечению к форме получаемого конструктивного элемента. Окончательное формирование сечения происходит в профилирующей матрице, где в результате нагрева происходит частичное отверждение. Для завершения отверждения элемент после формования дополнительно термообрабатывают в печи.
Материал протягивается по всему тракту формообразования с помощью тянущего устройства, например фрикционной роликовой передачи, гусеничного механизма и т.п. Полученный профиль, трубу или пруток разрезают на части определенной длины.
Особенностью метода является: высокая точность получаемых деталей; изготовление деталей любой длины; высокое значение коэффициента использования материала (до 95 %); точное регулирование заданного соотношения наполнитель - связующее; высокая производительность (до 1,5 м/мин).
Важным преимуществом пултрузионной технологии является возможность при изготовлении профилей открытого сечения формовать исходный полуфабрикат вне пултрузионной установки (на ткацком станке или шнуроплетельной машине). Это увеличивает производительность, сокращает габариты пултрудера, поскольку основную длину такой установки составляет узел формирования исходного материала.
В качестве исходного материала в пултрузионной технологии можно использовать препреги, но их применение очень ограничено.
Существует два способа пропитки армирующих материалов при пултрузии:
- пропитка сухих волокон в ванночке с последующим формованием профиля в матрице;
- предварительное формование профиля сухими волокнами с последующей пропиткой непосредственно в формующем фильтре.
Второй способ наиболее предпочтителен при пултрузии пустотелых деталей типа трубы.
В пултрузионных установках применяют три способа отверждения заготовок: в туннельных термокамерах; внешним нагревателем; в формующей фильере в электромагнитном поле СВЧ.
При отверждении внешним нагревом требуется прерывать движение заготовки для проведения процесса полимеризации. Наиболее эффективным является третий способ, при котором полное отверждение композита происходит при непрерывном движении материала в формующей фильере длиной около 500 мм (рис. 4.17).
|
|
Рис. 4.17. Схема пултрузионной установки с отверждением заготовки в электромагнитном поле СВЧ:
1 – исходный материал; 2 – магнетрон СВЧ; 3 – предварительная формующая фильера; 4 – тянущее устройство; 5 – отвержденная заготовка;
6 – термокамера с формующей фильерой
Производительность пултрузионного процесса определяется в основном временем отверждения композита и в зависимости от типа связующего и толщины детали скорость пултрузии составляет от 0,6 до 1,5 м/мин.
Тянущие устройства представляют собой простые механизмы трех типов: ременные или гусеничные со сменными траками под каждый типоразмер; непрерывные возвратно-поступательные; прерывистые возвратно-поступательные.
Наиболее эффективны для проведения непрерывного вытягивания заготовок механизмы первого типа.
Дата добавления: 2020-01-07; просмотров: 220; Мы поможем в написании вашей работы! |
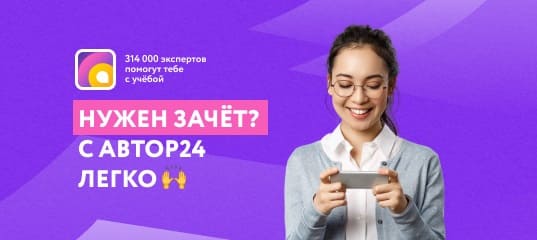
Мы поможем в написании ваших работ!