Методы получения изделий из пластических масс
Технология получения изделий из пластических масс представляет собой комплекс процессов, обеспечивающий получение изделий или полуфабрикатов с заданными свойствами на специальном оборудовании. Переработке пластмасс предшествует: проектирование рациональной конструкции изделия и формующего инструмента (формы, головки); выбор оптимального метода переработки; разработка рецептуры материала, наиболее пригодного для данного метода. Переработка включает приготовление материала и подготовку его к формованию (гранулирование, таблетирование), формование изделий и их последующую обработку с целью улучшения свойств готовых изделий.
Процессы переработки пластических масс чаще всего классифицируются по организационно-технологическим признакам, т.е. выделяются подготовительные, основные, завершающие и вспомогательные процессы.
К подготовительным процессам относятся: смешение, таблетирование, приготовление препрегов, предварительный нагрев и сушка, гранулирование.
Основными процессами переработки являются прессование, экструзия, литье под давлением, вакуумное и пневматическое формование.
Завершающими процессами являются механическая обработка и доделка отформованных изделий, сварка и склейка, окрашивание и металлизация и др.
Вспомогательные процессы связаны главным образом с переработкой пластмассовых отходов, образующихся при изготовлении изделий.
|
|
В процессе переработки термореактивные материалы (реактопласты) испытывают физико-химические превращения, а термопластичные материалы (термопласты) – в основном только физические, связанные с расплавлением материала и охлаждением изделий.
Требования к конструкции деталей из пластмасс. К пластмассовым деталям предъявляются особые требования конструктивного или технологического характера. Требования конструктивного характера включают мероприятия способствующие повышению эксплуатационных свойств деталей, а технологического характера - повышению производительности, экономии материалов и удешевлению стоимости.
Пластмассовая деталь по форме должна быть простой и конфигурация детали не должна препятствовать свободному течению расплава при заполнении формы. Это облегчает и удешевляет изготовление оснастки, улучшает качество детали, упрощает технологический процесс.
При изготовлении сложной детали иногда целесообразнее выполнить ее из отдельных элементов, с последующим соединением сваркой, склейкой, при помощи резьбы и другими способами.
Точность размеров деталей из пластмасс, изготовляемых литьем под давлением и прессованием, зависит от колебания расчетной усадки материала, конфигурации и габаритных размеров деталей, способа подготовки сырья, точности и конструкции пресс-формы, технологического режима. Точность деталей характеризуется квалитетом – совокупностью допусков, соответствующих одинаковой степени точности для всех номинальных размеров. Обычно детали из пластмасс изготавливают 12 – 15-го квалитетов точности.
|
|
Шероховатость поверхности деталей определяется состоянием оформляющих поверхностей пресс-формы. Обычно допускаемая шероховатость поверхности лежит в пределах 9 – 10-го классов.
При получении деталей методами прессования и литья под давлением предусматриваются технологические уклоны, которые способствуют беспрепятственному выталкиванию детали из пресс-формы. Технологические уклоны внутренних поверхностей должны быть больше уклона наружных поверхностей. Угол уклона для внутренних поверхностей составляет 30′ – 2°, для наружных – 15′ – 1°.
При конструировании деталей необходимо соблюдать условия равностенности, допускаемая разнотолщинность не должна превышать 2:1 для реактопластов при прямом прессовании, 2,5:1 – при литьевом прессовании; для термопластов допускается разнотолщинность от 1,5:1 до 4:1 для малоответственных деталей.
|
|
Максимальная толщина стенок деталей из реактопластов равна 8 – 14 мм, а из термопластов – 4 – 5 мм; минимальная толщина стенок для термопластов и реактопластов – 0,3 – 0,5 мм.
Переходы от большого сечения стенки к меньшему выполняют при помощи радиусов закруглений или уклонов, а в цилиндрических элементах при помощи конусности.
Для увеличения жесткости и прочности торцов деталей следует предусматривать на них буртики, оптимальная толщина которых не должна превышать удвоенной толщины стенки. Для этих же целей предусматриваются ребра жесткости, оптимальная толщина которых составляет 0,6 – 0,8 толщины сопрягаемой стенки.
Основы рационального выбора полимерных материалов для проектируемых изделий. Проблема применения полимерных материалов для изготовления изделия требует последовательного выполнения этапов выбора конкретной марки материала, проектирования изделия, проектирования и изготовления технологической оснастки и получения изделия по соответствующей технологии.
В связи с огромным марочным ассортиментом полимерных материалов выбор конкретного материала, наиболее полно удовлетворяющего при данных условиях эксплуатации физико-механическим, теплофизическим, электроизоляционным и другим свойствам изделий, представляет сложную задачу. Рациональный выбор полимерного материала является необходимым условием повышения надежности и сроков службы изделий, а следовательно, и эффективности использования этих материалов.
|
|
Успешное решение задачи по рациональному выбору материалов и конструированию изделий возможно лишь при учете различных характерных свойств материалов в зависимости от условий эксплуатации и методов переработки. Необходимо стремиться к наиболее полному использованию возможностей материала при его минимальной стоимости.
При выборе материала учитывают следующие основные критерии:
- стоимость материала и себестоимость его переработки в изделие;
- механические свойства (модуль упругости, ударную вязкость, разрушающее напряжение при растяжении, твердость, фрикционные и антифрикционные свойства и др.);
- теплофизические свойства (теплопроводность, коэффициент линейного расширения, температурный диапазон эксплуатации и др.);
- электрические свойства (диэлектрическая проницаемость, диэлектрические потери, электрическая прочность, дугостойкость, удельные объемные и поверхностные сопротивления и др.);
- комплекс специальных требований (токсичность, горючесть, воспламеняемость, влагостойкость, химстойкость и др.).
В зависимости от функционального назначения и условий эксплуатации изделий, приведенные критерии должны уточняться с учетом влияния на технологию их получения, их конструкционных свойств и других параметров.
Важнейшими критериями для выбора конкретного материала являются стоимость сырья и себестоимость изготовления изделия. Преимущества использования полимерных материалов становятся очевидными в сравнении со сложными и трудоемкими операциями по изготовлению и сборке металлических изделий. Изделия из полимерных материалов могут быть получены на простой оснастке с применением несложного оборудования и по короткому технологическому процессу, т.е. сокращаются производственный цикл и сроки освоения новых конструкций. Например, взамен трех видов обработки (литье, термообработка, механическая обработка) с большим количеством операций (до 30 – 50), для пластмассы требуется только один вид – формование детали методом пластической деформации. Кроме того, детали из полимерных материалов снижают материалоемкость в связи с малым весом и значительно более высоким КИМ (0,95 – 0,5).
Себестоимость изготовления изделий из полимерного материала зависит, в первую очередь, от объема заказа и технологичности материала, который тесным образом связан с конструктивными и эксплуатационными особенностями изделий, способом их переработки, видом оснастки и перерабатывающего оборудования.
В условиях опытного, единичного производства снижение себестоимости изготовления изделий достигается применением групповых блоков и формовкладышей к ним. При серийном производстве изменение затрат (без учета стоимости сырья) зависит от исходного вида сырья, способа его переработки, массы и сложности конфигурации изделия.
Важная роль при выборе полимерного материала отводится физико-механическим свойствам, зависящим от условий эксплуатации (температура, нагрузка, среда), способа приготовления материалов, методов и режимов переработки, конструкции формы и других параметров.
Прессование
Прессование реактопластов – это формование изделий под давлением из пресс-материалов, нагретых до вязкотекучего состояния непосредственно в полости формующего инструмента (пресс-форме) – между матрицей и пуансоном. В течение короткого времени пребывания в вязкотекучем состоянии к материалу прикладывается давление, действующее вплоть до окончательного отверждения расплава и оформления детали. В результате отверждения образуется сетчатая пространственная структура материала, он делается жестким, неплавким и нерастворимым и вследствие этого изделие может быть извлечено из матрицы при температуре прессования.
Прессование термопластичных материалов нерентабельно, так как извлечение отпрессованного изделия возможно лишь после охлаждения его вместе с формой до температуры стеклования, в результате чего снижается производительность процесса и увеличиваются энергетические затраты.
Пресс-материалы перерабатываются в изделия из сырья в порошкообразном, волокнистом или слоистом состоянии.
Прессование реактопластов осуществляется двумя основными способами: прямым (компрессионным) и литьевым (трансферным).
Прямое (компрессионное) прессование – наиболее распространенный способ. При этом способе предварительно нагретый или ненагретый, таблетированный или порошкообразный материал загружают в пресс-форму, которая замыкается, и пресс-материал подвергается давлению и нагреву. Давление передается непосредственно на прессуемый материал вплоть до полного замыкания пресс-формы. В зависимости от природы и свойств перерабатываемого материала обычно возникает необходимость выпуска из формы паров и газов, выделяющихся из прессуемого материала при его отверждении. Для этого в процессе прессования выполняют операцию подпрессовки, заключающуюся в переключении гидропресса после определенной выдержки на обратный ход, в подъеме пуансона на высоту, достаточную для выпуска газов (5–30 мм), и выдержке его в таком положении в течение 3 – 10 с. После этого пресс-форма снова замыкается. При прессовании крупных толстостенных деталей из материалов с повышенной влажностью подпрессовку проводят 2 – 3 раза.
Схема формования изделий представлена на рис. 3.1.
|
Рис. 3.1. Схема формования изделий из реактопластов прямым прессованием:
1 – верхний плунжер; 2 – матрица; 3 – перерабатываемый материал;
Изделие; 5 – пресс-форма
В полость матрицы 2 раскрытой пресс-формы (рис. 3.1, а) загружают предварительно таблетированный или порошкообразный материал 3. При замыкании пресс-формы под действием усилия пресса верхний плунжер 1 создает давление на прессуемый материал (рис.3.1, б). Под действием этого давления и теплоты от нагретой пресс-формы материал пластицируется (переходит в вязкотекучее состояние), заполняет формообразующую полость пресс-формы и отверждается. После определенной выдержки пресс-форма раскрывается и из нее извлекается готовая деталь.
Прямым прессованием получают детали средней сложности и небольших габаритных размеров из термореактивных материалов с порошкообразным и волокнистым наполнителем.
Недостатки компрессионного прессования – появление облоя (грата) по линии разъема пресс-формы, необходимость повышенных усилий прессования
Литье под давлением
Литье под давлением – один из основных методов переработки полимеров, широко применяющихся при производстве различных изделий из термопластичных и термореактивных материалов.
При формовании методом литья под давлением перерабатываемый материал нагревается до вязкотекучего состояния (пластицируется) в обогреваемом цилиндре, из которого впрыскивается под действием поршня или червяка в предварительно замкнутую литьевую форму, где материал затвердевает при изменении температуры, приобретая конфигурацию внутренней полости формы.
При литье термопластичных материалов расплав, заполнивший форму, охлаждается и затвердевает, затем форма открывается и готовое изделие удаляется из ее гнезда. При переработке термореактивных материалов впрыснутый в форму материал нагревается до температуры отверждения и выдерживается в течение времени, необходимого для полного отверждения изделия.
Переработка материалов литьем под давлением состоит из операций подготовки материала и формования. Подготовка материала в литьевой машине заключается в разогреве его до вязкотекучего состояния. Процессы пластикации в червячных и поршневых машинах существенно различаются: в поршневых машинах пластикация осуществляется только в результате прогрева, а в червячных машинах – как в результате прогрева (от нагревателей цилиндра), так и при выделении тепла трения в витке червяка сдвиговыми усилиями. В червячных конструкциях материал подвергается интенсивному перемешиванию, что позволяет выравнить температуру в объеме материала, подготовленного для впрыска.
Формование проводится в вязкотекучем состоянии, в которое материал переходит при повышенной температуре. При этом основное значение имеет выбор температуры переработки и времени пребывания при повышенной температуре до разложения или отверждения полимера. При увеличении температуры переработки выше определенного предела, характерного для каждого полимера, может произойти его термодеструкция (разложение) или преждевременное отверждение (для термореактивных полимеров). При пониженной температуре переработки материал обладает высокой вязкостью, что затрудняет формование готовых изделий.
При переработке термопластов цилиндр нагревают до 200 – 350°С, при переработке реактопластов – до 80 – 120°С. В литьевой форме термопласты в зависимости от их природы и требований, предъявляемых к изделию, охлаждаются до 20 – 40°С (полистирол, полиэтилен) или до 80 – 120°С (поликарбонат, полиформальдегид), а реактопласты нагреваются до 160 – 200°С. В форме материал выдерживается под давлением для уплотнения, что значительно снижает последующую усадку при охлаждении изделия вне формы.
Конструкции и принципы действия литьевых машин. Литьевая машина (рис. 3.2) состоит из устройства для дозирования материала, механизмов замыкания формы и инжекции, привода, пультов для управления машиной, а также для контроля и регулирования температуры.
Важнейшим узлом литьевой машины является инжекционный механизм, состоящий из устройства для объемного или весового дозирования, пластикации и инжекции материала; привода для возвратно-поступательного движения поршней, а также вращательного и поступательного движения червяков; устройства для перемещения инжекционного механизма.
Основными технологическими узлами литьевых машин являются механизмы инжекции и замыкания формы.
По принципу работы инжекционного механизма литьевые машины разделяют на поршневые, червячно-поршневые и червячные, а также на машины с предварительной пластикацией и без нее; по расположению механизмов инжекции и замыкания формы – на горизонтальные, вертикальные, угловые и комбинированные; по виду привода – на механические, гидравлические, пневматические, гидромеханические, пневмомеханические, пневмогидравлические; по количеству материальных цилиндров – на одно- и многоцилиндровые.
Основные параметры литьевой машины: максимальные объем и площадь одной отливки, усилие замыкания формы, ход подвижной плиты и максимальные размеры устанавливаемых форм, инжекционное давление, мощность электродвигателя привода и нагревателей материальных цилиндров.
Наибольшее распространение получили горизонтальные червячные литьевые машины с объемом одной отливки 30 – 125 см3.
Механизм замыкания формы поршневой литьевой машины (рис. 3.2, а) включает гидравлический цилиндр 1 и плунжер 2 для привода подвижной плиты 3 (при замыкании и размыкании литьевой формы 4), а также подвижную плиту 5.
б
Рис.3.2. Литьевые машины: а – поршневая; б – червячная
Инжекционный механизм состоит из инжекционного обогреваемого цилиндра 6, оснащенного обычно рассекателем 7, бункера 8 с весовым или объемным дозатором для перерабатываемого материала и инжекционного поршня 9, который перемещается под действием плунжера 11, расположенного в гидравлическом цилиндре 10. Перемещение инжекционного механизма для прижатия инжекционного сопла к литниковой втулке формы или отодвигания сопла осуществляется плунжером 12 гидравлического цилиндра 13. Червячная литьевая машина, в отличие от поршневой, оснащена червяком 14 и двигателем 15 для вращения червяка (рис. 3.2, б).
Процесс литья под давлением включает стадии: объемного и весового дозирования порошкообразного или гранулированного материала, загрузки материала в обогреваемый инжекционный цилиндр, пластикации материала, смыкания и запирания формы, подвода инжекционного механизма к форме, впрыска материала из сопла инжекционного цилиндра в полость закрытой формы, выдержки под давлением, возвращения червяка или поршня и инжекционного механизма в исходное положение, охлаждения изделия в форме, размыкания формы и удаления из нее изделий.
Формы для литья под давлением из пластмасс классифицируются по следующим признакам: по связи с машиной (стационарные и полустационарные); по направлению разъема формы относительно горизонтальной оси машины (с горизонтальным и комбинированным разъемами); по числу гнезд (одно- и многогнездные); по степени автоматизации (полуавтоматические и автоматические).
Для извлечения изделия из формы необходимо предусмотреть выталкиватели или плиту съема.
Процесс литья под давлением основан на заполнении формующей полости формы расплавом с его последующим уплотнением и охлаждением.
Процесс формования протекает очень быстро, расплав впрыскивается в форму с очень большой скоростью, он дополнительно разогревается, происходит ориентация макромолекул полимера из-за больших сдвиговых напряжений, возникающих в формующей полости при высокой скорости течения расплава между двумя охлаждаемыми пластинами. Быстрое двухстороннее охлаждение приводит к сильному изменению объема. Вследствие того, что полимер охлаждается снаружи, образующийся наружный слой полимера препятствует уменьшению объема и поэтому возможно появление утяжин. Для предотвращения этого необходимо перед охлаждением повышать давление в форме до 140 – 180 МПа. При литье плоских изделий, когда отсутствует разнотолщинность, могут применяться более низкие давления – 60 – 80 МПа.
Впрыск расплавав формующую полость формы происходит через литниковые каналы за короткое время (1 – 3 с).
После заполнения формы расплавом происходит его охлаждение, в результате чего увеличивается плотность и уменьшается объем, занимаемый полимером. Вследствие уменьшения объема через литники в форму продолжает поступать дополнительная порция расплава и давление в ней поддерживается постоянным. Наблюдается равновесие давления в цилиндре машины и в формующей полости, при этом происходит дополнительное медленное нагнетание (подпитка), что компенсирует уменьшение объема полимера в форме при его охлаждении и уменьшает усадку изделий.
Охлаждение изделияначинается сразу после впрыска расплава. Выдержка под давлением при охлаждении необходима для окончательного затвердевания расплава полимера и достижения определенной конструкционной жесткости изделий, исключающей их деформацию при извлечении из формы с помощью толкателей или плит съема. Температура полимера перед размыканием формы должна быть такой, чтобы при извлечении изделия не произошло его коробление или разрушение. При определении времени охлаждения необходимо учитывать конфигурацию изделий, их размеры, температуру расплава и формы, а также коэффициент температуропроводности расплава.
К формообразующим деталям относятся матрицы, пуансоны, формующие знаки, плиты и т.д.
Под термином матрица подразумевается углубленная формующая часть формы, под пуансоном – выступающая. Поверхность изделия распределяется между оформляющими деталями, места стыка оставляют на поверхности изделия следы. Поэтому важно, чтобы эти стыки совпадали с естественными переходами поверхностей.
Геометрическая форма плит выталкивания зависит от конструкции литьевой формы, гнездности и вида вталкивающей системы (стержневые, трубчатые выталкиватели или плиты съема), а также от расположения формующих гнезд.
Литниковые втулкиобразуют центральный литниковый канал, который является либо частью разветвленной литниковой системы, либо единственным ее элементом. Литниковые втулки располагают в центре плиты формы, если изделие симметрично, или со смещением, в зависимости от расположения формующей полости.
Для облегчения извлечения литника после охлаждения расплава канал литниковой втулки выполняют коническим. Конусность отверстия литниковой втулки α 3°. Отверстие литниковой втулки полируют до зеркального блеска.
Втулку изготавливают из коррозионно-стойких сталей или внутреннюю поверхность втулки дополнительно хромируют.
При заполнении расплавом оформляющего гнезда воздух и выделяющиеся из полимера газы скапливаются, сжимаются в наиболее удаленных местах, препятствуют заполнению формы и способствуют появлению дефектов в виде пустот, спаев, недоливов, прижогов. Кроме того, происходит растворение газов в отливках, приводящее к снижению прочности изделий.
Как правило, воздух и газы могут выходить через зазоры подвижных соединений, а также по плоскостям смыкания формы. Часто в формах предусматривают специальные вентиляционные каналы, которые располагают в наиболее удаленных от места впуска участках, полости.
Система охлаждения форм для литьятермопластов под давлением ответственна за равномерное и интенсивное охлаждение отливки по всему объему. Основное требование к системе охлаждения – обеспечение однородного температурного поля при максимальном отводе тепла из зоны отливки и минимальном – из зоны литниковых каналов.
Наиболее распространенным хладоагентом является вода, температурные ограничения для которой связаны с температурой ее кипения и снижением теплопередачи вследствие осаждения солей на стенках канала. При температуре формы более 80°С применяется минеральное масло (веретенное «Индустриальное-20»), а при пониженных температурах (+ 5°С) – раствор этиленгликоля в воде.
Формы для литья реактопластов под давлением имеют много общего с формами при литье термопластов. Однако имеется и ряд принципиальных отличий:
- не используются горячеканальные литниковые системы, так как при литье происходит отверждение материалов;
- вместо охлаждения применяется нагревание путем установки в плитах электронагревателей;
- конструктивно несколько отличаются, так как в каналах мундштука может произойти отверждение пресс-материала.
Поскольку термореактивные пресс-материалы в своем составе имеют наполнители, то повышается износ литниковых втулок и поверхностей формирующих элементов. Поэтому для их изготовления применяют стали с более высокой поверхностной твердостью, и они должны иметь хромовое покрытие толщиной приблизительно 20 мкм.
Экструзия
Значительная часть термопластичных полимеров перерабатывается в изделия методом экструзии с использованием экструзионных машин (червячных прессов) различных типов. При переработке гранулированных или порошкообразных термопластов экструдеры предназначаются для непрерывной пластикации и гомогенизации полимера, получения однородного расплава, перемешивания его и выдавливания через формующие головки в виде спрофилированного изделия. С помощью экструдеров наносят тонкослойные покрытия на бумагу, ткани, картон и изоляции на провода и кабели. Экструдеры применяются и для дегазации, окрашивания, обезвоживания, смешения, пластикации термопластов, реактопластов и эластомеров.
Непрерывность и высокая производительность процесса экструзии создают возможность максимальной автоматизации и поэтому червячные экструдеры – это один из наиболее распространенных и перспективных видов оборудования для переработки полимерных материалов.
Основные особенности экструзионной машины на примере одночервячного экструдера представлены на рис. 3.3.
Установка состоит из червяка, вращающегося внутри обогреваемого цилиндрического корпуса, на конце которого устанавливается головка с профилирующим инструментом. Между червяком и головкой располагается решетка с пакетом фильтрующих сеток. Материал поступает в загрузочное отверстие, где захватывается червяком и, продвигаясь по каналу червяка, разогревается теплом, выделяющимся вследствие вязкого трения и тепла, подводимого от расположенных на корпусе нагревателей. В процессе уплотнения из материала удаляется захваченный вместе с гранулами воздух и удельный объем композиции уменьшается. Для компенсации уменьшения удельного объема композиции канал червяка выполняют с уменьшающимся объемом витка (шнеки с переменным шагом или переменной глубиной нарезки).
Рис. 3.3. Одночервячный экструдер (а) и червяк (б):
1 – двигатель; 2 – канал для охлаждения зоны бункера; 3 – канал для выхода расплава в профилирующую головку; 4 – нагреватели цилиндра; 5 – цилиндр; 6 – червяк; 7 – загрузочная камера; 8 – бункер; 9 – упорный подшипник; 10 – редуктор;
зоны червяка: I – питание, II – плавление, III – дозирование; D – диаметр; L – длина; h 1 , h 3 – глубина винтового канала;е – ширина гребня витка; t – шаг нарезки
Одной из наиболее важных характеристик пресса является отношение длины червяка к диаметру, которое равно отношению длины червяка от края загрузочного отверстия на наружный диаметр червяка (L/D).
Соответственно характеру процессов, протекающих на каждом участке червяка, его можно разделить по длине на три основные зоны: питания - I, плавления - II, дозирования - III (рис. 3.3, б).
Зона питания – участок, в котором материал находится в твердом состоянии; в зоне плавления – плавление материала происходит почти полностью; в дозирующей зоне – материал находится в вязкотекучем состоянии.
Червячные экструдеры классифицируются по ряду признаков и разделяются следующим образом: одно - и многочервячные; одно- и многостадийные; одно- и многоцилиндровые; с простым или сложным профилем червяка.
По величине скорости вращения червяка различаются нормальные (до 150 об/мин) и скоростные (свыше 150 об/мин) экструдеры. На большинстве экструдеров червяки неподвижны в осевом направлении, однако на некоторых машинах, кроме вращательного движения, червяк осуществляет возвратно-поступательное (осциллирующее) движение.
В зависимости от конструктивного исполнения различаются экструдеры горизонтальные и вертикальные, стационарные и вращающиеся.
Одночервячные экструдеры применяют, главным образом, при получении труб, пленок, листов. Многочервячные экструдеры используют, прежде всего, в грануляционных установках.
![]() | Рис.3.4. Головка к экструдеру прямоточная плоскощелевая для листов и плит: 1 – мундштук; 2 – поток расплава; 3 – дорн; 4 – щель; 5 – регулировочные болты |
В соответствии с многообразием изделий имеются различные типы формующих головок: прутковые (гранулирующие), профильные, трубные, кабельные, плоскощелевые (листовые, ленточные), пленочные (кольцевые и плоскощелевые). По конструкционным признакам головки делятся на прямоточные и поперечные (угловые и др.).
Конструкции некоторых видов головок экструзионных машин приведены на рис. 3.4 – 3.6.
![]() | Рис. 3.5. Головка к экструдеру угловая кольцевая для получения рукавной пленки: 1 – рукавная пленка; 2 – регулировочный болт; 3,7 – детали корпуса головки; 4 – переходник; 5 – канал для экспедируемого материала; 6 – рассекатель; 8 – каналы для сжатого воздуха; 9 – фланец; 10 – дорн; 11 – кольцевой канал; 12 – мундштук |
Рис. 3.6. Головка для экструзии труб:
1 – дорн; 2 – мундштук; 3 – стакан; 4 – решетка дорна; 5 – торпеда;
Дата добавления: 2020-01-07; просмотров: 319; Мы поможем в написании вашей работы! |
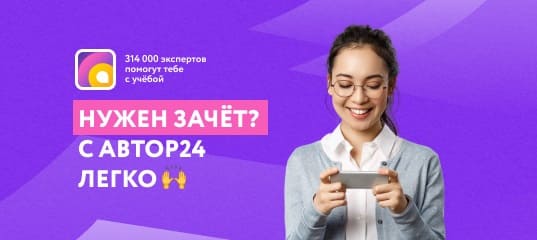
Мы поможем в написании ваших работ!