Марки и применение рессорно-пружинных сталей
Назначение | Примеры марок сталей | Применение | Особые свойства |
Стали общего назначения | Стали 65, 70, 75, У9А, У12А, марганцовистые стали 60Г, 65Г | Пружины механизмов и машин (небольшие сечения) | Пониженная релаксационная стойкость |
Кремнистые стали 55С2, 60С, 60С2 | Пружины и рессоры в автомобильной, автотракторной промышленности, железнодорожном транспорте | Склонность к обезуглероживанию | |
Комплекснолеги-рованные 50ХФА 60С2ХФА | Пружины и рессоры ответственного назначения (крупные сечения) | Теплостойкость до 300ºС | |
70С2ХА | Пружины часовых механизмов | Чувствительность к концентраторам напряжений | |
Стали специального назначения
| 30Х13, 40Х13 стали мартенситного класса | Пружины и упругие элементы | Коррозионная стойкость, жаропрочность (до 550ºС), магнитность |
12Х18Н10Т аустенитного класса | Пружины и упругие элементы | Коррозионная стойкость, жаропрочность (700ºС), немагнитность | |
Н18К9М5Т, Х12Н10Д2Т | Пружины и упругие элементы при высоких нагрузках | Высокая прочность, рабочие температуры от отрицательных до повышенных (до 500ºС) |
Стали специального назначения
Коррозионно-стойкие стали
Большинство коррозионно-стойких сталей содержат одновременно и хром и никель в количествах 13 – 27 % и 9 – 12 % соответственно, т.е. такие стали являются высоколегированными в зависимости от соотношения аустенито- и ферритообразующих элементов могут принадлежать к различным структурным классам: ферритному, мартенситному, аустенитному или смешанным классам (мартенситно-ферритному, аустенитно-ферритному, аустенитно-мартенситному) (ГОСТ 5632–72).
|
|
Хром, как основной элемент, обеспечивающий защиту стали от воздействия внешней среды, присутствует практически во всех коррозионно-стойких и жаростойких сталях. Хромистые стали, при содержании хрома более 12 %, имеют ферритную структуру.
Основным аустенитообразующим элементом в жаростойких сталях является никель, Вдвое слабее на образование аустенита влияет марганец. Существенно расширяют аустенитную область углерод и азот. Так, если в ферритный сплав с 28 % Cr ввести 0,6% С, то сплав приобретает полностью аустенитную структуру.
Комплексное влияние легирующих элементов на матричную структуру сложнолегированных хромоникелевых сталей может быть оценено по специальным структурным диаграммам, наиболее распространенной из которых является диаграмма Шеффлера (рис. 3.7). Диаграмма построена в координатах «эквивалент хрома ЭCr – эквивалент никеля ЭNi». Эквиваленты представляют собой сумму величин: произведение массовой доли элемента в стали (обозначенное символом элемента) на соответствующий коэффициент, учитывающий влияние элемента на положение ферритной или аустенитной области:
|
|
ЭCr = Cr + 2Si + 1,5Mo + 5V + 5,5Al + 1,75Nb + 1,5Ti + 0,75W
ЭNi = Ni + 0,5Mn + 30C + 30N + 0,3Cu
Матричная структура сталей, как известно, определяется той структурой, которую приобретает стали после нагрева на 900°С и охлаждения на воздухе. В сложнолегированных хромоникелевых сталей она зависит от соотношения величин Э Cr и Э Ni (рис. 3.8.):
1) при ЭCr > 16 % и ЭNi < 8 % (высокохромистый вариант) стали имеют ферритную структуру;
2) при увеличении ЭNi структура становится смешанной, феррито-аустенитной;
3) при ЭNi > 12 % стали находятся в аустенитной области: эта область при высоких значениях хромового эквивалента ограничена аустенито-ферритной областью, а при низких его значениях – аустенито-мартенситной областью;
4) при содержании Э Ni < 19 и Э Cr <13 существует большая область составов сталей, которые при охлаждении на воздухе имеют мартенситную структуру.
Каждый структурный класс коррозионно-стойких сталей характеризуется определенными не только коррозионными, но механическими и технологическими свойствами.
Стали мартенситного (20Х13, 30Х13, 40Х13, 95Х18) и мартенситно-ферритного классов (12Х13) представляют собой наиболее экономно-легированную группу коррозионно-стойких сталей и обладают хорошей коррозионной стойкостью в атмосферных условиях, в слабоагрессивных средах (растворах солей и кислот).
|
|
Стали данных классов являются наиболее прочными среди коррозионно-стойких сталей различных структурных классов (рис. 3.8). Это обусловлено их способностью к термическому упрочнению при закалке на мартенсит и отпуске. В зависимости от температуры отпуска получают различное сочетание прочности и коррозионной стойкости. После закалки и низкого отпуска (200 – 400ºС) стали имеют высокую коррозионная стойкость, так как весь хром находится в твердом растворе. При этом стали имеют высокую прочность (σв до 1600 МПа), но пониженную пластичность (δ = 3 %). В таком состоянии стали используют для изготовления инструмента.
Отпуск при 400 – 600°С приводит к выделению карбида хрома. При этом обеднение хромом твёрдого раствора и высокие внутренние напряжения вследствие образования высокодисперсных частиц способствуют ухудшению коррозионной стойкости. Подобный отпуск для сталей не применяют.
При более высокой температуре, когда карбиды хрома выделяются в виде более крупных равномерно распределенных частиц, стали обладают достаточно высокой коррозионной стойкостью. Такая термообработка обеспечивает благоприятное сочетание свойств – коррозионной стойкости, прочности, пластичности: σв до 960 МПа при δ = 14 – 20 %.
|
|
Мартенситно-ферритные стали являются менее прочными, чем мартенситные, из-за присутствия ферритной составляющей (не упрочняемой при термообработке).
Стали 30Х13, 40Х13 не применяются для сварных конструкций, их используют как материалы с повышенной твёрдостью для деталей, работающих на износ, а также для пружин, работающих в агрессивных средах. Для подшипников качения применяют высокоуглеродистую сталь 95Х18 (табл. 2.24).
Стали ферритного класса (08Х13, 08Х17Т, 12Х17, 15Х25Т, 15Х28 и др. – ГОСТ5632–72) как высокохромистые являются наиболее коррозионно-стойкими по сравнению со сталями других классов (см. рис. 3.8). Они обладают высоким сопротивлением коррозии в кипящих растворах кислот, горячих растворах щелочей; они стойки к питтинговой коррозии, к коррозии под напряжением. Легирование титаном не только повышает стойкость к межкристаллитной коррозии (МКК), но и снижает склонность к росту зерна при высокотемпературных нагревах.
Стали имеют наименьшую прочность среди коррозионно-стойких сталей (σв = 400 – 500 МПа, δ = 12 – 20 %, после отжига), так как из-за отсутствия фазовых превращений не упрочняются термической обработкой. К ним применяют только различные виды универсальных отжигов. К недостаткам сталей также относятся пониженная ударная вязкость и повышенный порог хладноломкости.
Стали удовлетворительно деформируются в горячем состоянии и неудовлетворительно – в холодном, ограниченно свариваются. Низкоуглеродистые стали свариваются аргоно - дуговой и контактной сваркой.
Стали аустенитного класса представляют собой наиболее широко распространённую группу коррозионно-стойких сталей.
По химическому составу аустенитные стали подразделят на хромоникелевые (12Х18Н10Т, 12Х18Н9, 08Х12Н12Б), хромомарганцевоникелевые (10Х14Г14Н4Т), хромомарганцевые стали (12Х13АГ14Д) (ГОСТ 5632–72).
Стали аустенитного класса являются стойкими в большинстве агрессивных сред: в промышленной атмосфере, в средах окислительного характера (например, с азотной кислотой), в некоторых органических кислотах средней концентрации. Исключение составляют солянокислые и сернокислые, растворы с ионами Сl- и SO42-, которые разрушают защитную пленку, в особенности при нагреве.
Высокая коррозионная стойкость сталей достигается в состоянии с однофазной аустенитной структуры, получаемой после закалки. Максимальная растворимость в легированном никелем аустените при 200С не превышает 0,04 %. При более высоких концентрациях углерода в стали технологические нагревы, связанные с проведением сварки или пайки, приводят к выделению карбидов хрома по границам зерен и развитию межкристаллитной коррозии. Для уменьшения склонности к МКК стали легируют титаном или ниобием, более сильными по сравнению с хромом карбидообразующими элементами, которые связывают выделяющийся углерод в карбиды типа МеС. Стали, легированные титаном или ниобием называют стабилизированными, и именно их используют в сварных конструкциях.
Хромоникелевые стали обладают невысокой прочностью (σв = 500 – 550 МПа), которая может быть повышена почти втрое холодной деформацией со степенью обжатия 20 %. Стали, в которых никель полностью или частично заменен марганцем, более прочны (σв = 600 – 800 МПа). Аустенитные стали более пластичны (δ = 40 – 60 %), вязки, а также хладостойки по сравнению со сталями на основе ОЦК - железа.
Аустенитные стали имеют хорошие технологические свойства: высокую технологическую пластичность, хорошую свариваемость.
Недостатками аустенитных сталей являются: склонность к местным видам коррозии – МКК, щелевой, питтинговой, а также к коррозионному растрескиванию; низкий предел текучести; низкая теплопроводность; плохая обрабатываемость резанием.
Применяются стали аустенитного класса в химической промышленности для изготовления емкостного, теплообменного оборудования, в том числе и сварного; для деталей и сварных конструкции в криогенной технике (до – 269ºС)
Аустенито -ферритные стали разработаны как материал, который является более прочным (в 1,5 – 2 раза) и более коррозионно-стойким, чем стали аустенитного класса в таких средах как щелочные и растворы серной кислоты. Стали содержат больше хрома и меньше никеля, чем стали аустенитного класса, что обеспечивает им двухфазную матричную структуру, в которой количество каждой фазы составляет 40 – 60 %. Основными марками являются 08Х22Н6Т (ЭП53) и 08Х21Н6М2Т (ЭП54) (ГОСТ 5632–72, ГОСТ 9941–81).
Аустенито-ферритные стали, так же, как и аустенитные, не упрочняются при термической обработке. Повышение прочности и достигается за счёт применении холодной пластической деформации.
Применяются стали для изготовления сварной химической аппаратуры (емкостей, испарителей, теплообменников, трубопроводов, арматуры), работающих в интервале от –70 до + 300°С. В судостроении и авиастроении их используют взамен стали 08Х18Н10Т.
Аустенито-мартенситные стали (марок 09Х15Н9Ю, 07Х16Н6Ю, 08Х17Н5М3) относятся к так называемым сталям переходного класса. Вследствие более низкого содержания углерода и никеля аустенит этих сталей, получаемый при закалке, не является стабильным. При последующей холодной деформации он превращается в мартенсит. В связи с этим стали отличаются хорошей технологической пластичностью и высокой прочностью, являющейся результатом фазового превращения А → М. Так, на ленте из стали09Х15Н9Ю временное сопротивление разрыву достигает 1600 МПа. Последующее старение при температурах 400 – 500ºС приводит к дополнительному упрочнению. Протеканию процесса старения в сталях переходного класса способствует легирование алюминием, медью, титаном, молибденом, вольфрамом, медью.
Жаростойкие стали
В качестве жаростойких в различных областях машиностроения используют хромистые и хромоникелевые стали таких же структурных классов, как и коррозионно - стойкие стали – ферритного, аустенитного и мартенситного.
Стали ферритного класса (08Х17Т, 12Х17, 15Х25Т, 15Х28 и т.д.) жаростойки в атмосфере сухого воздуха и сернистых газов. При этом они нежаростойки в восстановительных средах (водород, оксид углерода). Главным недостатком ферритных сталей является охрупчивание при длительном нагреве в интервале температур 450 – 750ºС.
Стали ферритного класса применяют для изготовления теплообменников и других изделий, не испытывающих значительных нагрузок.
Стали аустенитного класса (08Х18Н9Т, 12Х18Н9, 20Х23Н18, и др.) жаростойки во всех газовых средах, кроме серосодержащих. Они обладают не только высокой жаростойкостью, но и жаропрочностью и могут применяться для выхлопных систем, деталей печного оборудования и т.д.
Поскольку, стали аустенитного класса отличаются способностью к глубокой вытяжке и штамповке, то из них изготавливают такие полуфабрикаты как листы, ленты, трубы, полосы и прутки. Главным недостатком сталей аустенитного класса является их высокая стоимость из-за присутствия дефицитного никеля. Кроме того, они имеют высокий коэффициент линейного расширения, что делает необходимым увеличение зазоров между деталями при проектировании конструкций.
Рис. 2.44. Схема сравнительной прочности и коррозионной стойкости хромоникелевых сталей различных структурных классов
Сильхромы (15X6CЮ, 40Х9С2, 40Х10С2М, 30Х13Н7С2) - жаростойкие стали мартенситного класса, легированные кремнием (1 – 2 %) и хромом (6 – 13 %). Сильхромы предназначены в основном, для изготовления клапанов двигателей внутреннего сгорания (ДВС), рабочие температуры которых не превышают 800°С.Клапана ДВС работают в сложных условиях нагружения: вырезкие теплосмены. Для таких условий работы требуются материал с комплексом свойств, которые обеспечиваются как легированием. Так и термообработкой (рис. 2. 44). Хром и кремний обеспечивают жаростойкость сильхромов. Углерод и хром образуют карбид Cr7C3, способствующий увеличению износостойкости. Молибден вводят в сильхромы для повышения жаропрочности, уменьшения склонности к отпускной хрупкости.
Термообработка сильхромов включает либо отжиг при 850 – 870ºС либо закалку с высоким отпуском; оба вида термообработки обеспечивают необходимый уровень ударной вязкости.
Сильхромы не содержат дорогих легирующих элементов, поэтому широко используются для клапанов автомобильных, тракторных и дизельных двигателей с воздушным охлаждением, а также для крепежных деталей моторов.
Жаропрочные стали
Широкое использование сталей в высокотемпературной технике при различных сочетаниях рабочей температуры, продолжительности силового воздействия и действующих напряжений объясняется возможностью изменения структурного состояния сплавов за счет легирования. Жаропрочные стали являются многокомпонентными сплавами, химический состав которых отвечают требованиям сопротивления ползучести.
Рис. 2.45. Требуемые свойства сильхромов как материалов для клапанов
ДВС и пути их обеспечения
Процесс ползучести – это увеличение удлинения стали в условиях одновременного воздействия повышенной температуры и напряжений (рис. 3.10). Он состоит из трех стадий: начальной (неустановившейся ползучести, установившейся ползучести и разрушения). Жаропрочные стали должны обеспечить работу деталей на стадии установившейся ползучести; при этом удлинение не должно превышать 0,1 %. Для обеспечения работы в условиях одновременного воздействия на деталь температуры и напряжения стали должны содержать тугоплавкие металлы, которые замедляют диффузионные процессы, упрочняют твердые растворы сталей, а также образуют дисперсные промежуточные фазы (при отпуске или старении), которые также упрочняют стали по механизму дисперсионного упрочнения. Кроме того, в жаропрочных сталях соблюдается баланс феррито - и аустенитообразующих элементов с целью получения определенного структурного класса (рис. 2.46).
Рис. 2.46. Кривая ползучести
Для длительной работы при температурах до 580ºС и невысоких напряжениях применяют низколегированные стали перлитного класса, для более высоких температур и напряжений, в условиях более агрессивных сред – 12-%-ные хромистые комплексно-легированные стали мартенситного класса. Детали, работающие при температурах 700 - 850ºС и высоких нагрузках, изготавливают из самых жаропрочных сталей – сталей аустенитного класса с различным типом упрочнения (карбидным или интерметаллидным) (рис. 2.47).
Рис. 2.47. Легирующие элементы жаропрочных сталей различных структурных классов
В зависимости от назначения деталей и условий эксплуатации применяются стали различных систем, интервалов легирования и структурных классов.
Перлитные стали (12Х1МФ, 25Х2М1Ф и др.) предназначены для длительной эксплуатации при температуре 450 – 580°С в атмосфере перегретого пара и невысоких нагрузках и широко применяются в теплоэнергетике для изготовления трубопроводов, паропроводов, деталей паросиловых установок. Для перлитных сталей особенно важна стабильность исходной структуры и свойств, так как изготовленные из них детали теплоэнергетических установок эксплуатируются годами. Это требование стабильности структуры обеспечивается выбором системы легирования сплавов.
По химическому составу они относятся к низкоуглеродистым (0,08 – 0,15 % С) низколегированным сталям. Основными легирующими элементами являются Мо, Сr и V и их количество не превышает 2 – 3 %. Молибден упрочняет феррит, а хром и ванадий образуют дисперсные карбиды VC, Cr7C3, выделяющиеся после нормализации при температуре 1000 0С и последующего отпуска при 650 – 750°С в течение 2 – 3 ч.
Перлитные стали высокотехнологичны: они хорошо деформируются в горячем и в холодном состоянии, удовлетворительно обрабатываются резанием и свариваются.
Главными недостатками сталей перлитного класса являются низкая жаростойкость и коррозионная стойкость, так как они содержат не более 5 % хрома. Детали из сталей перлитного класса требуют специальных покрытий.
Стали мартенситного класса содержат 12 – 15 % хрома и являются одновременно коррозионно - стойкими, жаростойкими и жаропрочными. Эти стали с рабочей температурой 450 – 650ºС имеют две области применения: котлотурбостроение и двигателестроение (детали компрессоров газотурбинных двигателей).
Стали мартенситного класса являются низкоуглеродистыми, содержат от 0,08 до 0,15 % С, а также 12 – 15 % Сr, молибден, ванадий, ниобий. Стали котлотурбостроения не содержат никель (15Х11МФ); а стали для деталей ГТД, чтобы выдержать сложные механические нагрузки, в том числе ударные, легированы никелем (14Х12Н2В2МФБ), повышающим ударную вязкость.
Термическая обработка сталейсостоит в закалке на мартенсит и высоком отпуске при 650 – 690ºС, во время которого образуются дисперсные карбиды.
Стали мартенситногокласса обладают комплексом свойств, благоприятным для использования при повышенных температурах и в сложных условиях нагружения: жаропрочностью, жаростойкостью, высоким пределом выносливости, высокой ударной вязкостью и термостойкостью.
Условия эксплуатации:
1) в котлотурбостроении – при более высоких температурах, больших давлениях перегретого пара и более агрессивных газовых средах, чем для перлитных сталей;
2) в двигателестроении – для деталей газотурбинного двигателя (ГТД), работающих в сложных условиях нагружения: статические растягивающие и изгибающие нагрузки, циклические и динамические нагрузки, газовая коррозия, резкие теплосмены.
Аустенитные стали по рабочей температуре и уровню жаропрочных свойств превосходят стали перлитного и мартенситного классов (рис. 2.48, рис. 2.49).Это обеспечивается как большей компактностью гранецентрированной кристаллической решётки, что затрудняет развитие диффузионных процессов, так и большей растворимостью легирующих элементов в аустените. Повышение жаропрочности может составлять до 40 %.
Рис. 2.48. Рабочие температуры жаропрочных сталей различных структурных классов и типов упрочнения: П – перлитный; М - мартенситный с карбидным упрочнением; А - аустенитный «гомогенный»; А+К - аустенитный с карбидным упрочнением;
А+И - аустенитный к с интерметаллидным упрочнением
Аустенитные стали содержат 11 – 27 % хрома, 9 – 29 % никеля, до 0,4 % углерода и могут быть легированы элементами: Ti, Nb, Mo, Al, W. В зависимости от типа основной упрочняющей фазы стали подразделяются на 3 подгруппы:
1. Однофазные (гомогенные) стали типа 12Х18Н9Т, не упрочняемые термической обработкой;
2. Стали с карбидным упрочнением (45Х14Н14В2М, 37Х12Н8Г8МФБ);
3. Стали с интерметаллидным упрочнением (10Х11Н20Т3Р).
Однофазные аустенитные стали обычно называют «гомогенными». Они имеют твердорастворное упрочнение; титан добавляется для образования карбида и предотвращения межкристаллитной коррозии.
Аустенитные стали с карбидным упрочнением имеют повышенноесодержание углерода (до 0,5 %). Термическая обработка заключается в закалке на пересыщенный твёрдый раствор от температур 1150 – 1200°С и последующем старении при 650 – 800°С, во время которого из аустенита выделяется карбид (Сг,Ме)23С6; возможно также образование карбида VC (часто эту термообработку называют «отпуском»). Таким образом, в этих сталях, по сравнению с гомогенными, реализуется, кроме твердорастворного, ещё один механизм упрочнения – дисперсионное твердение за счёт частиц карбида. Поэтому детали из этих сталей (рабочие лопатки газовых турбин, диски, роторы, крепежные детали) работают при более высоких температурах и напряжениях. Рабочая температура аустенитных сталей с карбидным упрочнением достигает 750°С, что на 100°С превышает рабочую температуру гомогенных сталей.
Рис. 2.49. Предел 100-часовой длительной прочности жаропрочных сталей различных структурных классов и типов упрочнения
Аустенитные стали с интерметаллидным упрочнением содержат больше никеля, легированы титаном и алюминием; они являются самыми жаропрочными в группе аустенитных сталей. Титан и алюминий имеют переменную растворимость в хромоникелевом аустените, поэтому после закалки с температур 1080 – 1150ºС образуется пересыщенный твёрдый раствор, из которого при старении (750 – 850ºС) выделяется интерметаллическая фаза γ΄- Ni3 (Ti, Al). Стали, упрочнённые γ΄- фазой, более жаропрочны, чем стали с карбидным упрочнением по следующим причинам:
– количество γ΄- фазы, образующейся при старении, больше, чем количество карбида (8 – 10 % по сравнению с 1,3 – 3 %);
– частицы γ΄ - фазы когерентно связаны с матрицей, потому что у них близкие периоды кристаллических решёток; когерентная границаявляется дополнительным препятствием для перемещения дислокаций;
– частицы γ΄- фазы более дисперсны, чем частицы карбида.
К недостаткам сталей аустенитного класса следует отнести их высокую стоимость, меньшую термостойкость (из-за более высокого коэффициента линейного расширения и более низкой теплопроводности). Стали с карбидным упрочнением из-за высокого содержания углерода – плохо свариваются.
Чугуны
Чугуны – литейные сплавы системы железо - углерод с содержанием углерода более 2,14%, кристаллизация которых заканчивается при постоянной температуре по эвтектической реакции, что обеспечивает хорошие литейные свойства: жидкотекучесть (способность жидкого металла заполнять весь объем литейной формы), герметичность (свойство металла образовывать плотные отливки с минимальным количеством пор), а также малую усадку. Высокие литейные свойства при небольшой стоимости обуславливают широкое применение чугунов для изготовления фасонных отливок.
В чугунах метастабильной системы «железо - цементит» весь углерод находится в связанном состоянии – в виде химического соединения карбида Fe3C. Благодаря большому содержанию цементита эти чугуны имеют светлый излом, и поэтому называются белыми. Белые чугуны обладают повышенной хрупкостью, и как конструкционный материал не используются.
Конструкционные чугуны – это сплавы тройной системы Fe – C – Si, в которых углерод присутствует (полностью или частично) в виде равномерно распределённых в металлической матрице включений графита.
Конструкционные чугуны – это доэвтектические сплавы, которые содержат 2,2 – 3,7 % С и 1,0 – 2,9 % Si, а также постоянные примеси (марганец, серу и фосфор). Кремний – элемент-металлоид, который как и углерод выполняет функцию графитизатора: он способствует образованию графита в чугунах как при кристаллизации, так и при фазовых превращениях в твердом состоянии. Марганец, в отличие от кремния, затрудняет графитизацию, способствует «отбеливанию» и его содержание в чугунах не превышает 0,4 % - 0,8 %. Фосфор в чугунах является полезной примесью, так как он улучшает жидкотекучесть; его содержание на порядок выше, чем в сталях и может достигать 0,03 %. Сера в чугунах является вредной примесью и ее содержание не превышает 0,02 %.
Химический состав нелегированных чугунов. Содержание углерода находится в пределах доэвтектической концентрации, т.е. менее 4,3 % (табл. 2.25).
Присутствие графита позволяет считать чугуны естественным композиционным материалом, который состоит из неметаллической и металлической составляющих.
Влияние графита на свойства чугунов неоднозначно. Обладая низкой прочностью и твёрдостью, графит уменьшает временное сопротивление и особенно сильно снижает пластичность сплавов. Вместе с тем нарушение сплошности металлической основы из-за присутствия графитовых включений приводит к улучшению обрабатываемости резанием (за счет образования ломкой стружки) и делает чугун малочувствительным к концентраторам напряжений.
Таблица 2.25
Дата добавления: 2020-01-07; просмотров: 211; Мы поможем в написании вашей работы! |
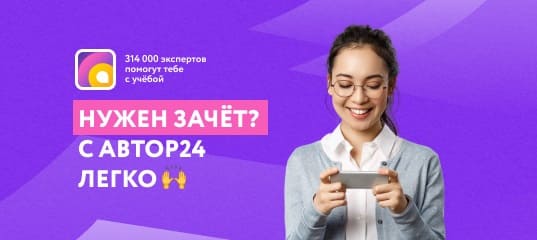
Мы поможем в написании ваших работ!