Техническое диагностирование и прогнозирование остаточного ресурса дизелей тепловозов методом спектрального анализа масла.
Общие положения
Состояние дизелей с помощью спектрального анализа картерного масла можно оценить по величине концентрации в нем продуктов износа. Об износе трущихся поверхностей деталей цилиндропоршневой группы можно судить по концентрации в картерном масле железа; вкладышей подшипникового коленчатого вала – свинца; втулки поршневого пальца – меди.
На рис.25 приведены зависимости износа деталей, изменения концентрации продуктов износа в масле и интенсивность отказов от времени работы Т или пробега Z при эксплуатации тепловозов.
Рис.25 |
Характер кривых А, Б, и Г справедлив для работы дизеля без смены масла.
При выполнении технического обслуживания и текущих ремонтов с заменой отбракованных деталей, подверженных случайным отказам, плотность их на графике (зависимость Г) представляет прямую линию, параллельную оси абсцисс:
где m/ - среднее время работы (пробег) деталей до случайного отказа.
В III периоде наблюдается совместное действие случайных отказов и отказов, вызванных износом деталей вследствие работы соединений со сверх допустимыми зазорами.
В основу спектрального анализа положен эмиссионный метод (испускание), сущность которого заключается в излучении света, который излучается анализируемым веществом.
Для того, чтобы продукты износа трущихся пар (металлы, содержащиеся в масле) излучали свет, их необходимо подогреть до температуры, обеспечивающей возбуждение атомов. Возвращаясь в обычное состояние при остывании, атомы анализируемого вещества отдают избыточную энергию в виде света, который излучается в пространство по закону электромагнитных колебаний с различными длинами волн l. Длина световой волны для конкретного элемента есть постоянная величина, обычно измеряемая в ангстремах (А) или в микрометрах (1А=10-4мкм).
|
|
Техническая оснастка и оборудование
Для проведения работы используется 12-ти канальные фотоэлектрические установки типа МФС-3, предназначенные для регистрации интенсивности спектральных линий (рис.26).
Рис. 26.Фотоэлектрическая установка МФС-3:
1 – электрон - регистрирующее устройство; 2 – камера сжигания порции масла; 3 – неподвижный электрод; 4 – подвижный электрод; 5 – ванночка с маслом; 6 – линза; 7 – полихроматор; 8 – фотокатод; 9 – конденсатор
При анализе масла нижним электродом является вращающийся угольный диск, часть которого постоянно погружена в ванночку с пробой масла. При вращении диска масло с находящимися в нем продуктами износа поступает в разряд, где происходит испарение масла и возбуждение атомов элементов, присутствующих в пробе масла.
|
|
Полихроматор (спектральный прибор) с вогнутой дифракционной решеткой разлагает излучение в спектр, который характеризует химический состав вещества пробы. Каждому элементу соответствует своя совокупность спектральных линий, интенсивность которых зависит от концентрации элемента в данной пробе. Двенадцать наиболее пригодных для проведения анализа спектральных линий различных элементов выделяются из спектра пробы с помощью выходных щелей, установленных в фональной поверхности полихроматора. Монохроматические излучения выделенных линий проектируются на фотокатоды фотоэлектронных умножителей (ФЭУ) и вызывают фототоки в их анодных цепях.
Электронно-регистрирующее устройство (ЭРУ) обеспечивает автоматическое включение конденсаторов в анодные цепи облучаемых ФЭУ, накопление на конденсаторах заряда в течении заданного времени и последовательное получение на шкалах выходных приборов отсчетов, пропорциональных напряжениям на конденсаторах. Кроме того, ЭРУ обеспечивает автоматическое включение и выключение источника возбуждения спектра в заданный момент времени, а также при предварительном обжиге электродов, накопление и опрос. Для определения концентрации элементов продуктов износа в пробах, соответствующих полученным отсчетам, необходимо предварительное построение градуированных графиков по стандартным образцам (эталонам). Графики строятся в логарифмических координатах. По оси абсцисс откладываются величины концентрации элементов, а по оси ординат – средние величины отсчетов с измерительных приборов установки.
|
|
Порядок выполнения работы
Перед началом анализа установка прогревается в течение двух часов, пробы масла перемешиваются на механической мешалке в течение получаса, после чего приступают к сожжению пробы.
Последовательность операций следующая:
1. Включить вытяжную вентиляцию.
2. Вставить верхний и нижний электроды в зажимы штатива. Установить промежуток между ними 1,5 мм с помощью шаблона.
3. Налить масло в ванночку по уровню края и поставить ее на аналитический столик штатива, предварительно опустив кронштейн в них до упора, нажав на него пальцем. Опустить кронштейн и подвести ванночку под нижний электрод винтом до касания масла. Подождав, пока нижний электрод сделает один полный оборот, закрыть камеру сжигания.
4. Включить установку нажатием кнопки одного из каналов анализируемых элементов (Fe, Pb, Cu, Al и др.). После нажатия кнопки в штативе загорается дуга и сигнальная лампа на пульте управления «Обжиг». По истечении заданных реле времени 20 с обжига, установка автоматически переключает режим работы «Обжиг» на «Накопление», загорается соответствующая сигнальная лампа и начинается накопление заряда на конденсаторах, регистрируемое цифровым вольтметром.
|
|
По окончании режима «Накопления», сопровождаемого прекращением дуги в штативе, необходимо снять показания с вольтметра, поочередно нажимая на кнопку опроса канала.
5. Записать показания вольтметра по всем контролируемым каналам в журнал лабораторных работ.
После этого ознакомиться с содержанием формы, получаемой из вычислительного центра, где приняты следующие обозначения:
Д – диагноз по каждому контролируемому узлу;
ДК – диагностический коэффициент по каждому контролируемому узлу;
П – прогноз остаточного ресурса в количестве ТО-3.
ДВС предусматривает диагноз по следующим узлам и неисправностям:
- вкладыши подшипников коленчатого вала – по зазору на масло;
- вкладыши подшипников коленчатого вала – по выкрашиванию;
- поршневые кольца – по излому и износу;
- поршни – по износу;
- подшипники турбокомпрессора – по износу;
- топливные форсунки – по плохому распылу;
- водяная система – по течи;
- втулки верхней головки шатуна – по износу;
- выпускной коллектор – по нагару;
- воздушный ресивер – по загрязнению;
- ТНВД – по повышенной производительности.
По каждому узлу ЭВМ определяет уровень его состояния:
0 – состояние хорошее;
1 – состояние удовлетворительное;
2 – состояние, требующее повышенного контроля;
3 – состояние неудовлетворительное.
Прогноз остаточного ресурса производится по нарастанию концентрации продуктов износа и общей загрязненности масла для следующих узлов:
- по железу – износ поршневых колец;
- по свинцу – износ подшипников коленчатого вала;
- по кремнию – состояние воздушного ресивера;
- по алюминию – износ корпуса нагнетателя второй ступени и рабочего колеса турбокомпрессора;
- по олову – износ поршней;
- по меди – износ втулок верхней головки шатуна и поршневых колец;
- по хрому – износ деталей, содержащих хром;
- по общей загрязненности – состояние поршней по нагару во внутренних полостях;
по вязкости – наличие топлива в масле.
Список литературы
1. Правила деповского ремонта тепловозов типа ТЭ3, ТЭ10 (ЦТ/2586), М: Транспорт, 1969, 312 с.. 14 шт
2. Правила технического обслуживания и текущего ремонта тепловозов типа ТЭ3 и ТЭ10 № ЦТ/4410, М: Транспорт, 1988. 14 шт
3. Правила технического обслуживания и текущего ремонта тепловозов ТЭМ2, ТЭМ2А, ТЭМ2У, ТЭМ2УМ: ЦТ/519, М., 1998, 183 с. 3 шт
4. И.А. Биргер Техническая диагностика.- М.: Машиностроение 1978, - 240 с.
5. Технические средства диагностирования: Справочник. Под общ. ред. В.В.Клюева.- М.: Машиностроение, 1989, 672 с.
6. В.И. Бервинов, Техническое диагностирование локомотивов. Учебное пособие. М.: УМК МПС России, 1999, 190 с.
7. Тепловозные дизели типа Д49. Под редакцией Е.А.Никитина. М.: Транспорт, 1982, 255 с.
8. Правила технического обслуживания и текущего ремонта тепловозов 2Т116, ЦТ 468. М.: Транспорт ,1997, 310 с.
9. Топливные системы тепловозных дизелей. М. Транспорт, 1983, 192 с.
Учебно-методическое издание
Какоткин Владимир Захарович
Скепский Вадим Петрович
Балабин Валентин Николаевич
Дата добавления: 2019-09-13; просмотров: 296; Мы поможем в написании вашей работы! |
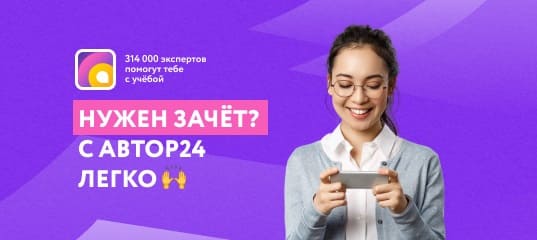
Мы поможем в написании ваших работ!