Ультразвуковая дефектоскопия детали
Цель - ознакомить студентов с аппаратурой научить практическим приемам по отысканию глубинных пороков, трещин в поршнях, шейках коленчатых валов дизелей Д100 и бандажах колесных пар.
Общие положения
Ультразвуковые дефектоскопы УД2-12 и УЗД-64 обеспечивают обнаружение несплошностей в различных металлах или пластмассах теневым или эхо – методом.
Метод отраженного излучения применяется для отыскания глубинных пороков металла, т. е. пороков, не выходящих на поверхность деталей. К внутренним порокам металлических деталей обычно относят: волосовины, трещины, усадочные раковины, пористость, шлаковые включения и непровары в сварочных швах.
Метод отраженного излучения основан на свойстве ультразвуковых колебаний с частотами выше 20000 Гц проникать в толщину любого твердого или жидкого тела и отражаться от границ раздела двух сред (воздух - металл, инородные включения - металл, жидкость - газ и т. д.).
Дефектоскопию методом отраженного излучения можно осуществить двумя способами: акустической тени и отраженного излучения.
При первом способе (рис.4, а) контролируемое изделие располагается между двумя индикаторами, один из которых посылает ультразвуковые колебания, а другой их принимает. Если у детали имеется дефект, то часть ультразвуковых колебаний отразится от него и не достигнет индикатора. Вследствие этого за дефектом образуется «акустическая тень».
|
|
Рис. 4. Схема ультразвуковой дефектоскопии
При втором способе (рис.4, б) оба индикатора располагаются на одной какой-либо стороне детали, а индикатор - приемник воспринимает лишь ультразвуковые колебания, отраженные от дефекта.
Способ акустической тени обладает сравнительно малой чувствительностью, поэтому большее распространение получил способ отраженного излучения с использованием импульсных ультразвуковых дефектоскопов.
Наиболее существенным достоинством дефектоскопии методом отраженного излучения является возможность выявления глубинных дефектов, как у отдельных деталей, так и у деталей, находящихся в сборочных единицах, независимо от материала, из которого они изготовлены. Например, можно выявить дефекты в осях колесных пар, шейках коленчатого вала, не снятого с дизеля, болтах крепления полюсов тягового электродвигателя, находящегося под тепловозом, и т. д.
Недостатком этого метода является необходимость изготовления «своего» индикатора для проверки каждого типа изделия, а иногда и отдельных его участков. Кроме того, метод отраженного излучения требует не только настройки дефектоскопа для проверки каждого типа изделия, но и знания особенностей работы аппаратуры и навыков по расшифровке дефектов.
|
|
Технологическая аппаратура
Для выполнения этой работы необходим ультразвуковой дефектоскоп УЗД-64, работающий по принципу отраженного излучения с набором индикаторов. Он состоит из генератора электрических импульсов и генератора развертки, под действием которого электрические импульсы перемещаются по экрану электроннолучевой трубки и блока усилителя.
В качестве генератора импульсов используется конденсатор, который периодически разряжается и через управляемый прибор (тиратрон) посылает импульсы тока в колебательный контур дефектоскопа. Генератором пилообразного напряжения для развертки служит электронная лампа 6Ж4. На лицевой панели дефектоскопа, кроме экрана электроннолучевой трубки, расположены рукоятки режимов работы и рукоятка глубиномера.
Рис. 5. Принципиальная схема ультразвукового дефектоскопа:
1 – электроннолучевая трубка; 2 – генератор развертки; 3 – усилитель; 4 – импульсный генератор; 5 – приемный индикатор; 6 – передающий индикатор; 7 – контролируемое изделие; 8 – дефект детали; I – служебный импульс; II – донный сигнал; III – эхо-сигнал
Импульсный генератор 4 через равные промежутки времени посылает короткие электрические импульсы на пьезоэлектрическую пластинку передающего индикатора 6, который преобразует эти импульсы в ультразвуковые и направляет в контролируемое изделие 7. Одновременно с этим вступает в работу генератор развертки 2. При отсутствии дефекта ультразвуковые колебания отражаются от противоположной поверхности изделия (дна) и воспринимаются такой же (или той же) пластиной приемного индикатора 5, где они вновь преобразуются в электрические импульсы, которые поступают в усилитель 3, а затем на вертикально-отклоняющие пластины электроннолучевой трубки 1. На ее экране при этом возникает так называемый донный сигнал.
|
|
При наличии в изделии дефекта часть ультразвуковых колебаний вначале отразится от него (эхо-сигнал), а остальная часть отразится от противоположной стороны изделия (донный сигнал). Усиленный эхо-сигнал попадает на вертикально-отклоняющие пластины электроннолучевой трубки раньше донного. Вследствие этого на экране левее донного появится эхо-сигнал от дефекта (см. рис.5). Прием эхо-сигналов происходит в промежутке между двумя очередными электрическими импульсами генератора.
Дефектоскоп позволяет определять местонахождение дефекта и оценивать его размеры. Аппарат работает на переменном токе и подключается к сети, как и магнитные дефектоскопы, трехжильным кабелем, третья жила которого служит для заземления металлических частей дефектоскопа.
|
|
Индикатор для выявления трещин и рыхлостей против второго ручья поршня 5 дизеля Д100 представляет собой плексигласовый корпус 8 (рис.6), в который под углом 45° вставлены плоские (8×3 мм, 5×14 мм) пьезоэлектрические пластинки 4 и 6 и две индукционные катушки 2. Пластины катушки соединены между собой и со штепсельными разъемами 1 при помощи константановой проволоки. Демпфером у каждой пластины служит эпоксидная смола 3 и 7 с резиной в качестве наполнителя. Собственная (резонансная) частота ультразвуковых колебаний индикатора 2,5 МГц.
Рис. 6. Индикатор к ультразвуковому дефектоскопу для отыскания трещин в ручьях поршня:
1 – штепсельный разъем; 2 – индукционные катушки; 3, 7 – демпфера
4, 6 – пьезоэлектрические пластинки; 5 – поршень; 8 - корпус; 9 – дефект детали; I – начальный импульс; II – сигнал настройки по бездефектному поршню; III – предельная высота сигналов дефектоскопа
Для контроля коленчатых валов дизелей Д100 используются пять различных индикаторов. Два из них с метками III предназначены для контроля шатунных шеек, два индикатора с метками К - для контроля коренных шеек валов, индикатор с меткой А - для отыскания поперечных трещин на галтели хвостовика вала под антивибратор.
Индикаторы с метками Ш и К с двумя одинаковыми плоскими пьезоэлектрическими пластинами из титанита бария (толщиной 3 и диаметром 18 мм) служат для выявления поперечных трещин, а индикаторы с одной пластиной - для выявления продольных трещин на шейках вала. Корпусы индикаторов с метками Ш и К различаются между собой только радиусами кривизны контактирующих поверхностей.
Рис. 7. Индикатор к ультразвуковому дефектоскопу для отыскания трещин у коренных шеек коленчатого вала дизеля:
1 – корпус; 2 – штепсельное гнездо; 3 – демпфер; 4 – пьезоэлектрическая пластина; 5 – индукционная катушка; Д – дефект на детали
Конструктивное оформление и схема индикатора с меткой К для обнаружения поперечных трещин показаны на рис.7. Как видно, одна из пластин индикатора служит для передачи, а другая - для приема ультразвуковых колебаний.
Шейки коленчатого вала контролируют поверхностными ультразвуковыми волнами, а проверка ручьев поршня ведется наклонными волнами.
Настройка и проварка работы дефектоскопа по эталонам ведется согласно прилагаемому к аппарату руководству.
Порядок контроля
Технологический процесс контроля деталей состоит из следующих операций:
- измерение сопротивления изоляции токопроводящих частей и проверка надежности заземления металлических частей дефектоскопа;
- включение и настройка дефектоскопа;
- подготовка контролируемых деталей;
- контроль деталей.
Измерение сопротивления изоляции и проверка надежности заземления металлических частей ультразвукового дефектоскопа производится так же, как и магнитного дефектоскопа.
Контроль поршня дизеля 2Д100
1. Включение и настройка дефектоскопа ведется в следующем порядке. Заранее подключённый к сети дефектоскоп поворотом верхнего левого тумблера включается в работу. При этом загорается сигнальная лампа. Спустя 20-30с на экране появится горизонтальная линия развертки. Поворотом рукоятки «ФОКУС» достигается контрастность изображения вертикальной части линии развёртки. Затем при помощи регулятора «СДВИГ» и «ПУСК» начальный импульс на линии развертки перемещается в левую часть экрана. Нижний тумблер ставят в положение П, тумблер развертки в положение «БЫСТРАЯ», а тумблер «ОГРАНИЧЕНИЕ» переводится в положение «ВКЛ».
Служебный импульс глубиномера поворотом рукоятки «ГЛУБИНА» выводится из видимой части экрана дефектоскопа. После этих операций дефектоскопу присоединяют индикатор, предназначенный для контроля поршня. При надобности вновь регулируют контрастность изображения на экране.
2. Подготовка поршня к контролю заключается в следующем. Поршень, особенно его первый и третий ручьи для колец, тщательно очищают от грязи. Чтобы избежать воздушной прослойки между индикатором и поршнем и тем самым создать лучшие условия для проникновения ультразвуковых колебаний в металл, поверхность проверяемых ручьев поршня обильно смазывают маслом. Лучше всего для этой цели подходит чистое, без механических примесей компрессорное масло.
3. Для контроля поршень укладывают боковой поверхностью на ролики, позволяющие свободно вращать его вокруг оси. Затем ножки индикатора вставляют в ручьи поршня (см. рис.6), плотно прижимают к поверхности поршня и медленно перемещают по поршню.
На исправном участке поршня ультразвуковые колебания будут проходить по металлу, а на экране дефектоскопа появятся один или два сигнала. При наличии дефекта (трещины, рыхлости, неметаллических включений и т. п.) указанные сигналы сильно уменьшаются по высоте, либо пропадут совсем. Передвигая индикатор и наблюдая за экраном дефектоскопа, замечают размеры и месторасположение дефекта.
Начало дефектного места определяется по снижению высоты сигналов с 25 до 5-8 мм, а конец - по их увеличению от 0 до 5-8 мм. Начало и конец дефекта отмечают мелом на поршне против середины индикатора.
В карте контроля деталей журнала лабораторных работ выверчивают эскиз дефектной части поршня, указывают местонахождение и длину дефекта, а также дают заключение о пригодности поршня к дальнейшей эксплуатации.
Трещины против второго ручья возникают обычно в галтелях банок с внутренней стороны поршня, постепенно углубляются и выходят на поверхность ручья.
Дата добавления: 2019-09-13; просмотров: 241; Мы поможем в написании вашей работы! |
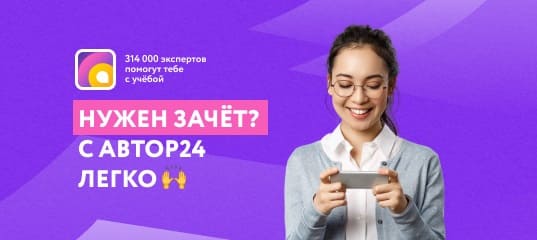
Мы поможем в написании ваших работ!