Технологическое оборудование и материалы
МОСКОВСКИЙ ГОСУДАРСТВЕННЫЙ
УНИВЕРСИТЕТ ПУТЕЙ СООБЩЕНИЯ (МИИТ)
ИНСТИТУТ ТРАНСПОРТНОЙ ТЕХНИКИ
И ОРГАНИЗАЦИИ ПРОИЗВОДСТВА (ИТТОП)
Кафедра «Локомотивы и локомотивное хозяйство»
В.З. Какоткин, В.П. Скепский, В.Н. Балабин
Утверждено
редакционно-издательским
советом университета
ТЕХНИЧЕСКАЯ ДИАГНОСТИКА
ТЕПЛОВОЗОВ
Методические указания к лабораторным
работам и практическим занятиям
Для студентов специальности “Локомотивы”
Москва – 2005
МОСКОВСКИЙ ГОСУДАРСТВЕННЫЙ
УНИВЕРСИТЕТ ПУТЕЙ СООБЩЕНИЯ (МИИТ)
ИНСТИТУТ ТРАНСПОРТНОЙ ТЕХНИКИ
И ОРГАНИЗАЦИИ ПРОИЗВОДСТВА (ИТТОП)
Кафедра «Локомотивы и локомотивное хозяйство»
В.З. Какоткин, В.П. Скепский, В.Н. Балабин
ТЕХНИЧЕСКАЯ ДИАГНОСТИКА
ТЕПЛОВОЗОВ
Методические указания к лабораторным
работам и практическим занятиям
Для студентов специальности “Локомотивы”
Москва – 2005
УДК 621.873: 681.121.8
К-20
Какоткин В.З., Скепский В.П., Балабин В.Н.
|
|
ТЕХНИЧЕСКАЯ ДИАГНОСТИКА ТЕПЛОВОЗОВ.
Методические указания к лабораторным работам и практическим занятиям для студентов специальности150700 «Локомотивы». М.: МИИТ, 2005, - 68с.
Приведены основные сведения по различным методам контроля и диагностики оборудования тепловозов.
Ó Московский государственный университет путей сообщения
(МИИТ), 2005
СОДЕРЖАНИЕ
Стр. | |
Введение……………………………………………………….….... | |
Лабораторная работа №1 «Магнитопорошковый метод контроля деталей и цветная дефектоскопия деталей»………….………..… | |
Лабораторная работа №2 «Ультразвуковая дефектоскопия детали»………………………………………………………………….... | |
Лабораторная работа №3 «Контроль состояния якоря электродвигателя тепловоза»…………………………………………….… | |
Лабораторная работа №4 «Измерение износа деталей топливной аппаратуры дизеля интегральным методом»………………………. | |
Лабораторная работа №5 «Диагностика процесса топливоподачи в цилиндры дизеля по осциллограмме»…………………………… | |
Лабораторная работа №6 «Определение и регулировка геометрического угла опережения подачи топлива ТНВД»……………. | |
Лабораторная работа №7 «Техническое диагностирование и прогнозирование остаточного ресурса дизелей тепловозов методом спектрального анализа масла»…………………………………..… | |
Список литературы…………………………………………..…….. |
|
|
ВВЕДЕНИЕ
Работающие в тяжелых условиях ответственные сборочные единицы и детали машин и механизмов подвержены трещинообразованию, т. е. зарождению и развитию в них усталостных трещин. Такие трещины, являясь сильными концентраторами напряжений, развиваясь, угрожают разрушением детали в процессе работы и созданием аварийных ситуаций. Поэтому для безопасности эксплуатации наиболее ответственные детали периодически контролируют. Цель контроля в условиях эксплуатации или ремонта - обнаружение усталостных трещин и выбраковка деталей, угрожающих поломкой. Такой контроль во многих случаях невозможно осуществлять "на глаз" из-за недостаточной достоверности визуального контроля. Для этой цели применяют различные виды неразрушающего контроля, который может быть реализован с помощью взаимодействия различных физических полей или веществ с проверяемой деталью.
Благодаря наилучшей технологичности и наибольшей простоте в промышленности и на транспорте наиболее широкое внедрение получили ультразвуковой, магнитный, капиллярный и вихретоковый виды контроля. Отличительной особенностью и достоинством ультразвукового неразрушающего контроля является способность ультразвуковых волн глубоко проникать в толщу металла и, отражаясь от несплошностей, обеспечивать таким образом контроль зон, закрытых для доступа извне.
|
|
На ремонтных предприятиях длительное время применялись ламповые ультразвуковые дефектоскопы УЗД-56 и УЗД-64, которые заменяют новыми, сконструированными на базе полупроводниковой схемотехники (УД-11ПУ, УД2-12, DI-4). Эти дефектоскопы имеют более широкие функциональные возможности, например индикацию зоны контроля, автоматическую сигнализацию наличия дефекта с оптической или звуковой индикацией, "отсечку" слабых сигналов с регулируемым уровнем срабатывания.
Лабораторная работа №1
Магнитопорошковый метод контроля и цветная дефектоскопия деталей
Цель - знакомство с применяемыми на ремонтных заводах и в локомотивных депо методами магнитной дефектоскопии и приобретение практических навыков работы с ними по проверке деталей тепловозов, а также обучение студентов отысканию скрытых и внешних дефектов у вкладышей коленчатого вала дизеля и у других деталей тепловоза путем обмеливания и осмотра.
|
|
Общие положения
Магнитопорошковый метод применяется для контроля деталей из черных металлов, которые могут быть намагничены. Этот метод позволяет обнаружить усталостные и закалочные трещины, волосовины, включения и другие пороки металла, выходящие на поверхность.
Сущность метода заключается в следующем. Деталь намагничивается. При наличии на поверхности детали трещины процесс намагничивания сопровождается (вследствие изменения магнитной проницаемости) концентрацией магнитных силовых линий до насыщения на заостренных кромках трещины и образованием в этих местах магнитных полюсов. Если на такую деталь нанести ферромагнитный порошок, то под действием сил магнитного поля частицы порошка будут скапливаться и удерживаться в том месте, где трещина выходит на поверхность. Частички порошка в этом случае будут как бы обрисовывать контур трещины, т. е. показывать ее форму, длину, месторасположение.
В качестве искателя дефекта используют ферромагнитные порошки (мягкую сталь, кузнечную окалину и крокус-окись железа), доведенные до пылевидного состояния (поперечный размер частиц 50-60 мкм). Лучшими магнитными свойствами обладает порошок из мягкой стали. Жидкой основой для смеси служат органические масла или их смеси с керосином. Обычно в 1 л жидкости рекомендуется добавлять 125-175 г порошка из окиси железа или 200 г порошка из мягкой стали.
Магнитопорошковый метод дефектоскопии очень эффективен при выявлении поверхностных дефектов. Испытания деталей этим методом быстры, надежны, дешевы и наглядны.
К недостаткам следует отнести трудности, возникающие при размагничивании громоздких деталей (коленчатых валов, блоков и т.д.) недоступность непосредственного контроля деталей в сборочных единицах без их разборки, а также невозможность контроля деталей из цветных металлов и сталей аустенитного класса.
Цветная дефектоскопия применяется для контроля состояния деталей из магнитных и немагнитных материалов (цветных металлов, пластмасс, твердых сплавов), имеющих пороки, выходящие на поверхность. Сущность метода основана на регистрации контраста цветного индикаторного следа на фоне поверхности контролируемой детали.
Деталь, подлежащую контролю, очищают и обезжиривают; затем погружают в индикаторную жидкость или ее наносят на поверхность детали. По истечении 5-10 мин, когда индикаторная жидкость глубоко проникает в трещины и поры, деталь промывают проточной холодной водой или 5-процентным раствором каустической соды. Затем деталь сушат (обычно подогретым воздухом), покрывают мелким сухим микропористым порошком силикагеля или водным раствором каолина или мела (на 1 л воды 600-700 г каолина или 300-400 г порошка мела). Нанесенный на поверхность детали каолин или мел должен высохнуть.
Поскольку размеры пор в силикагеле (каолине, мелу) меньше ширины трещины, то под действием капиллярных сил индикаторная жидкость заполняет микропоры силикагеля. В результате над трещиной появляется цветная линия в виде жилки, копирующая форму и размеры трещины. По ширине жилки судят о глубине трещины: чем шире жилка, тем глубже трещина.
В качестве индикаторной жидкости, может служить состав, приготовленный из 80% керосина, 15% трансформаторного масла, 5% скипидара и 10 г краски «Судан 3» на 1 л состава.
При люминесцентном методе контроля деталей, который не отличается от цветного, используют жидкости, в состав которых вводятся люминофоры – вещества, которые светятся собственным светом под воздействием ультрафиолетовых лучей. Состав индикаторной жидкости: трансформаторное масло - 5%, керосин - 50% с добавлением на 1 л 5 г технического антрацена.
При люминесцентном методе контроля используют переносной дефектоскоп КД-31Л, предназначенный для локального контроля деталей при ремонте тепловозов. Дефектоскоп представляет собой ультрафиолетовый облучатель, соединенный кабелем с пускорегулирующим аппаратом.
Цветной метод неразрушающего контроля применяется для выявления трещин, пор и других подобных дефектов в деталях, изготовленных из различных металлов, твердых сплавов и пластмасс.
Цветной метод нагляден, прост и недорог. С его помощью можно контролировать детали в сборочных единицах без их разборки.
Метод цветной дефектоскопии позволяет обнаружить на поверхности детали трещины глубиной до 0,01 и шириной до 0,001 мм при темперaтуре детали 15-20°С.
Технологическое оборудование и материалы
Для выполнения работы необходимы магнитные дефектоскопы типов ДГН и ДГС с контрольными эталонами и магнитной смесью и мегомметр типа M1101 напряжением в разомкнутой цепи 500 В.
Дефектоскопы переменного тока ДГС (рис.1) и настольные ДГН (рис.2) относятся к числу соленоидных приборов, отличающихся друг от друга конструктивным оформлением. круглых стержней или деталей другого поперечного сечения, которые могут уместиться в отверстии дефектоскопа.
Общим для дефектоскопов этих типов является то, что контроль деталей осуществляется при действующем (приложенном) магнитном поле, т. е. при включенном дефектоскопе. Исследуемая деталь может охватываться намагничивающей катушкой полностью (ДГН) или частично (ДГС).
Рис. 1. Общий вид дефектоскопа ДГС-М
1 – выключатель; 2 – сердечник; 3 – клеммовый щиток; 4 – корпус; 5 – трехжильный кабель; 6 – катушка намагничивающая; 7 – катушка дополнительная
Каждый из указанных дефектоскопов состоит: из корпуса; намагничивающей катушки, состоящей из двух или более изолированных друг от друга секций; стального сердечника, служащего магнитопроводом; выключателя. Каждый дефектоскоп присоединяется к сети трехжильным кабелем, который с одной стороны имеет штепсельную розетку, а с другой – трехштыревую вилку. Средний удлиненный штырь вилки и третья жила служат для заземления металлических частей дефектоскопа.
Рис. 2. Общий вид настольного дефектоскопа ДГН:
1 – намагничивающая катушка; 2 – корпус; 3 – трехжильный кабель; 4 – стойка; 5 – эталон; 6 – понижающий трансформатор; 7 – посуда с магнитной смесью
Дефектоскопом ДГС можно проверять детали диаметром до 240 мм; зона полезного действия этих приборов не более 250 мм при использовании магнитной смеси и не более 150 мм при использовании сухого порошка. Дефектоскоп ДГН служит для контроля деталей диаметром до 80 мм, а зона его действия 125-150 мм.
Описываемые дефектоскопы могут быть включены в сеть переменного тока напряжением 220 или 127В путем соответствующего переключения секций намагничивающих катушек.
Исправность дефектоскопа и качество искателя, т. е. магнитной смеси (или сухого порошка), проверяют контрольным эталоном, представляющим собой стальной валик (часть бандажа и т. д.) с естественными трещинами или хорошо зачеканенной искусственной вставкой.
Цветная дефектоскопия: Для выполнения данной работы необходимо иметь лупу 5-10 кратного увеличения, деревянный молоток, меловой раствор и бачок с индикаторной жидкостью.
Порядок выполнения работы
Технологический процесс контроля деталей магнитным дефектоскопом состоит из следующих операций:
- измерение сопротивления изоляции токопроводящих частей дефектоскопа и проверка надежности заземления его металлических частей;
- проверка качества выявления дефекта прибором по контроль ному эталону;
- подготовка деталей для контроля;
- дефектоскопия и размагничивание.
Эти операции проводятся в следующем порядке:
1. Состояние изоляции токопроводящих частей и надежность заземления металлических частей дефектоскопа проверяется измерением сопротивления изоляции мегомметром.
Сопротивление изоляции токопроводящих частей должно быть не менее 2 МОм, а заземленных частей - равно нулю.
При контроле надежности заземления провод от зажима «линия» мегомметра подсоединяют к среднему удлиненному штырю вилки трехжильного кабеля, а от зажима «земля» - к металлической части корпуса дефектоскопа.
2. Для проверки качества выявления дефекта дефектоскоп подключают к сети (при разомкнутом выключателе), затем вставляют в него контрольный эталон так, чтобы последний находился в зоне полезного действия дефектоскопа. Включают дефектоскоп и поливают эталон предварительно взболтанной магнитной смесью. По четкости проявления трещины судят об исправном действии дефектоскопа и качестве магнитной смеси (искателя).
3. Подготовка детали к магнитному контролю заключается в очистке ее до металлического блеска от смазки, пыли, краски, коррозии и т. д.
4. Для выявления поперечных трещин или трещин, расположенных с большим наклоном, дефектоскоп на контролируемой детали располагают таким образом, чтобы обеспечить продольное намагничивание детали и особенно мест, наиболее подверженных образованию трещин (галтелей, углов прямоугольных рамок, шпоночных гнезд, отверстий и т. п.).
Нужно иметь в виду, что напряженность магнитного поля дефектоскопов ДГН со стороны, противоположной сердечнику, на 30-40% выше, чей со стороны сердечника, через который замыкается часть магнитных силовых линий (рис.3).
Поэтому дефектоскоп располагают на контролируемой детали так, чтобы проверяемый участок находился со стороны катушки, а у дефектоскопа ДГС со стороны выключателя, а у дефектоскопа ДГН - со стороны текстолитовой крышки.
Рис. 3. Схема напряженности магнитного поля дефектоскопа ДГН
1 – намагничивающее устройство; 2 – деталь
Чтобы обеспечить свободное стекание магнитной смеси с неповрежденных мест детали, ее устанавливают с некоторым наклоном к горизонту. Проверяемый участок детали должен находиться в зоне полезного действия дефектоскопа.
В процессе контроля, т. е. во время поливки магнитной смесью и осмотра детали, дефектоскоп должен оставаться на детали и быть включенным. В случае скопления на каком-либо участке поверхности детали магнитного порошка в виде характерной темной жилки, указывающей на наличие трещины, это место следует обтереть и вновь проверить, но более внимательно. Дефектное место очерчивается мелом.
5. Намагниченные детали могут длительное время притягивать к себе стальные опилки и частицы, которые особенно опасны для трущихся деталей подшипниковых узлов. Поэтому детали, подвергнутые контролю для устранения остаточного магнетизма, размагничивают.
Одним из простейших способов размагничивания является размагничивание в постепенно убывающем переменном магнитном поле. Деталь помещают внутри включенного дефектоскопа, а затем постепенно удаляют ее (или дефектоскоп от детали) на расстояние не менее 1,0—1,5 м., после чего дефектоскоп выключают. Полностью размагниченная деталь не должна притягивать стальную пластинку или опилки.
В карте контроля журнала лабораторных работ необходимо привести эскизы дефектных деталей, подвергнутых магнитному контролю, с указанием мест и характера трещин, а также дать заключение о пригодности их к дальнейшей эксплуатации или необходимости восстановления.
Цветная дефектоскопия: Контроль состояния вкладышей сводится к выявлению внешних и скрытых дефектов.
Внешние дефекты - повреждения поверхности баббитовой заливки, наклеп, потемнение тыльной части, забоины и риски - определяются визуальным осмотром. В необходимых случаях применяют лупы. Замеченные повреждения у каждого вкладыша фиксируют в карте контроля вкладышей журнала лабораторных работ. Вкладыши, не удовлетворяющие требованиям правил (по наличию обнаруженных дефектов), бракуют.
К скрытым дефектам вкладышей, которые нельзя обнаружить визуальным осмотром, относятся трещины в теле и отслоение баббитовой заливки от тела вкладыша. Для отыскания скрытых дефектов вкладышей поступают следующим образом. Контролируемые вкладыши опускают на 16-20 мин. в ванну с индикаторной жидкостью, затем извлекают из ванны, насухо протирают и покрывают меловым раствором. После высыхания мелового раствора, вкладыши остукивают деревянным молотком по тыльной части. Дребезжащий (или глухой) звук укажет на отслоение от тела вкладыша баббитовой заливки, а потемнение в виде узких жилок, появляющихся на поверхности вкладыша, - на наличие трещин. После дефектоскопии меловой раствор с поверхности вкладышей удаляется.
Обнаруженные повреждения у каждого вкладыша отмечают в карте контроля вкладышей и сравнивают с допускаемыми дефектами, регламентированными правилами ремонта. После этого дается заключение о возможности дальнейшей эксплуатации каждого вкладыша.
Лабораторная работа №2
Дата добавления: 2019-09-13; просмотров: 157; Мы поможем в написании вашей работы! |
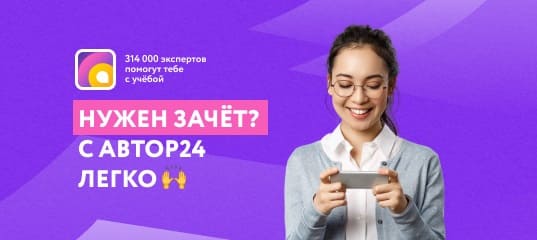
Мы поможем в написании ваших работ!