Содержание отчета по лабораторной работе
Отчет должен содержать:
– расчет эпюры шпал;
– выписанные шпалы с указанием номера дефекта;
– выписанные «кусты» шпал;
– вывод о допустимой скорости движения поездов.
Контрольные вопросы
1. Что такое старогодняя шпала?
2. Сколько в среднем весит деревянная шпала?
3. Сколько в среднем весит железобетонная шпала?
4. Что такое «куст» негодных шпал?
5. Какие бывают дефекты деревянных шпал?
6. Какие бывают дефекты железобетонных шпал?
7. Каковы условия пропуска поездов по участку пути с имеющимися кустами негодных шпал?
8. Причины возникновения дефектов деревянных шпал (по каждому дефекту отдельно)?
9. Для чего производится пропитка деревянных шпал?
10. По какой системе производится пропитка деревянных шпал?
11. Для чего производится армирование железобетонных шпал?
12. Для чего армирование производится с предварительным напряжением?
13. Что такое эпюра шпал? Какая эпюра шпал на прямых и кривых участках?
Лабораторная работа №4
Промежуточные рельсовые скрепления
В настоящее время на российских железных дорогах на железобетонных шпалах порядка 85% от общего количества скреплений составляют скрепления КБ-65. Данный тип скрепления используется с середины прошлого века и является морально устаревшими и не отвечающими современным потребностям.
Программа развития железнодорожного транспорта подразумевает строительство выделенных линий высокоскоростного движения, а также увеличения длины поезда и нагрузки на ось на действующих линиях. Сложные геологические условия иногда вынуждают укладывать железнодорожный путь в условиях кривых малого радиуса. Так же немаловажен тот факт, что Российская Федерация географически расположена в разных климатических поясах. Все эти факторы создают различные особенности во взаимодействии колеса и рельса, а значит, влияют на работу рельсовых скреплений.
|
|
ОАО «РЖД» проводит исследования работы рельсовых скреплений различных типов в разных условиях эксплуатации и, как показывают результаты, тестируемые скрепления имеют свои достоинства и недостатки.
Цель работы
Изучить особенности, достоинства и недостатки рельсовых скреплений различных типов. Научиться монтировать и демонтировать рельсовые скрепления.
Место проведения работы
Стенд «Рельсовые скрепления» в ангаре учебного полигона СамГУПС.
Необходимый инструмент
1. Ключ торцевой гаечный М36;
2. Ключ торцевой шурупный М24;
3. Ключ монтажный АРС;
4. Ключ для разборки анкерного рельсового скрепления;
5. Ключ для сборки анкерного рельсового скрепления;
6. Динамометрический ключ.
|
|
Рисунок 4.1. Инструмент, необходимый для проведения лабораторной работы №4
Теоретическая часть
1. Промежуточные скрепления, исполняя роль связующих элементов между рельсами и основанием, должны обеспечивать:
· стабильность ширины колеи;
Требование обеспечения стабильности ширины колеи важно и очевидно, оно прямо связано с обеспечением безопасности движения поездов из условия недопущения провала колес.
· прижатие рельсов к основанию, исключающее отрыв и угон рельсов;
Нарушение требования по обеспечению достаточности прижатия рельсов к основанию приводит к отрыву рельсов от шпал при укладке или разборке пути, а также при его подъемке при проведении выправочных работ. Обусловлено это гниением деревянных шпал, разрушением дюбелей, недостаточной прочностью и коррозией прикрепителей на железобетонных основаниях. Угон рельсов приводит к изменению их напряженно-деформированного состояния, что может вызвать выброс пути при повышении температуры и разрыв стыков при ее понижении. Угон пути приводит к смещению и перекосу шпал, выпадению подрельсовых прокладок. Ликвидация последствий угона рельсов сопряжена с выполнением сложных и трудоемких работ по регулировке зазоров и разрядке температурных напряжений в рельсовых плетях.
|
|
· оптимальные условия температурной работы рельсов;
Требование оптимизации температурной работы рельсов также связано с величиной усилий прижатия их к основанию. Исключить температурные деформации рельсов очень сложно, так как это вызывает усложнение конструкции пути, удорожание рельсовых скреплений. Недостаточное же прижатие рельсов к основанию вызывает чрезмерные деформации концевых участков рельсовых плетей, усложнение конструкции стыковых скреплений, быстрый износ промежуточных скреплений, нарушение равноупругости основания из-за перемещения шпал.
· проведение регулировки положения рельсов по высоте и ширине колеи, замену деталей скреплений без перерывов в движении поездов;
Проведение регулировки положения рельсов по высоте особенно важно на железобетонных подрельсовых основаниях и в зимнее время. В условиях высокой грузонапряженности в пути быстро накапливаются остаточные деформации, происходит нарушение проектного положения рельсов. Выправка пути с применением шпалоподбивочной техники сложна в организации, требует перерывов в движении поездов, поэтому использование регулировочных прокладок для выправки пути весьма целесообразно. В зимнее время на участках пучинообразования применение регулировочных прокладок является единственным способом исправления пути по уровню и в профиле.
|
|
· механизированную сборку и содержание узлов скреплений;
В современных условиях, когда сборка и разборка рельсошпальной решетки ведется на базах с применением поточных линий, требование о необходимости механизации работ по сборке и разборке узлов скреплений совершенно справедливо. Необходимость механизации работ по смене рельсов, замене изношенных элементов скреплений, регулировке натяжения прикрепителей при текущем содержании пути также не вызывает сомнений.
· рациональную пространственную упругость и вибростойкость узлов скреплений;
Обеспечение рациональной пространственной упругости рельсовых скреплений чрезвычайно необходимо для того, чтобы упруго перерабатывать динамические воздействия колес подвижного состава на рельсы, гасить высокочастотные вибрации, расстраивающие путь и особенно его болтовые соединения, а также для того, чтобы создавать равноупругость подрельсового основания.
· электроизоляцию рельсов от основания:
На участках с автоблокировкой скрепления для железобетонных шпал должны обеспечивать электрическую изоляцию рельсов от шпал с сопротивлением не ниже 1 Ом на километр пути.
· экономическую эффективность конструкции верхнего строения пути.
Требование к скреплениям о необходимости обеспечения экономической эффективности конструкций пути очевидно. Скрепления должны способствовать достижению высоких сроков службы всех элементов пути (в частности, они сильно влияют на сроки службы деревянных шпал) и оптимальных условий их эксплуатации.
2. Классификация рельсовых скреплений.
Промежуточные рельсовые скрепления по своей конструкции делятся на подкладочные и бесподкладочные (без металлических подкладок под рельсами). Подкладки обеспечивают большую площадь передачи давления от рельса на опору, подуклонку рельсов без затески деревянных шпал, объединяют все прикрепители при работе на сдвиг и имеют большое распространение на всех дорогах мира.
Промежуточные скрепления делятся еще на две группы в зависимости от того, обладают они или не обладают противоугонными свойствами. Первая группа - это непротивоугонные скрепления, у которых прикрепители не создают достаточного нажатия на подошву рельса и тем самым не обеспечивают необходимой продольной связи рельса с основанием. При применении этих скреплений необходима установка на подошву рельса дополнительных приспособлений, препятствующих продольной сдвижке рельса, — противоугонов. Ко второй группе скреплений относятся противоугонные конструкции, у которых с помощью упругих элементов создается необходимое нажатие на подошву рельса, исключающее его проскальзывание по опорам под проходящими поездами.
В свою очередь вторая группа делится на две подгруппы: болтовые и безболтовые скрепления. В первом случае натяжение прикрепителей, а, следовательно, их нажатие на подошву рельса, можно регулировать подтягиванием гаек клеммных болтов. В безболтовых скреплениях монтажное нажатие закладных упругих элементов должно оставаться неизменным в течение всего периода эксплуатации. Подкладочные скрепления подразделяются на раздельные, нераздельные и смешанные. В раздельном скреплении рельс к подкладке и подкладка к опоре прикрепляются разными прикрепителями. В нераздельном скреплении рельс через подкладку соединяется с опорой одними и теми же прикрепителями. В смешанном скреплении рельс через подкладку соединяется с опорой, а подкладка, кроме того, самостоятельно прикрепляется к опоре.
3. Скрепления для железобетонных шпал.
3.1. КБ-65 – клеммно-болтовое скрепление для рельсов Р-65.
Рисунок 4.2. Скрепление КБ-65. 1 – клеммный болт; 2 – клемма; 3 – изолирующая втулка; 4 – закладной болт; 5 – анкерная шайба; 6 – подрельсовая прокладка; 7 – прокладка под подкладкой; 8 – подкладка металлическая; 9 – плоская шайба; 10 – шайба двухвитковая
Рельсовое скрепление КБ-65 - наиболее распространенное на Российских железных дорогах скрепление. Данное скрепление подкладочное, раздельного типа. Прикрепление рельса к подкладке 8 осуществляется при помощи двух жестких клемм 2, прижимное усилие на которые создается путем затяжки гаек клеммных болтов 1.
Прикрепление подкладки 8 к шпале осуществляется при помощи пары закладных болтов 4, устанавливаемых в специальные анкерные шайбы 5, расположенные в отверстиях в шпале. Закрепление рельсовой подкладки в гнезде шпалы обеспечивает стабильность ширины колеи.
Нашпальная прокладка 7 и подрельсовая прокладка 6, изготовленные из упругих полимерных материалов, обеспечивают упругую передачу нагрузки от рельса к шпале, а также служат в качестве виброгасителей.
Упругие пружинные двухвитковые шайбы 10 устанавливаются на клеммные и закладные болты. Шайбы действуют как пружины и создают обратное усилие на гайку при сжатии, это предотвращает откручивание гайки под воздействием осевой нагрузки и вибрации.
![]() | ![]() |
![]() | ![]() |
![]() | ![]() |
![]() | ![]() |
![]() | ![]() |
Рисунок 4.3. Элементы скрепления КБ
Электрическую изоляцию скрепления КБ обеспечивают нашпальная прокладка 7 и изолирующая втулка 3. Рельс непосредственно контактирует с подкладкой металлической, изоляцию которой от шпалы обеспечивает нашпальная прокладка. Закладной болт контактирует с металлической анкерной шайбой, замоноличенной в шпалу, а от подкладки изолируется при помощи изолирующей втулки. На изолирующую втулку устанавливается плоская шайба 9, для предотвращения разрушения полимерного изолятора от воздействия усилия от двухвиковой шайбы.
Регулировка положения рельса по высоте осуществляется путем укладки регулировочных прокладок под рельс. Возможна регулировка на высоту до 14 мм.
Сборка узлов скреплений осуществляется на звеносборочных базах ПМС, при этом сборка скрепления осуществляется вручную, механизирована только затяжка гаек. В процессе эксплуатации требуется подтяжка и смазка гаек клеммных и закладных болтов два раза в год.
Затяжку гаек при подтягивании их в процессе эксплуатации проводят с крутящим моментом: для клеммных болтов – 200 Н-м, для закладных – 150 Нм.
Скрепление содержит 21 элемент в каждом узле, масса металлических частей одного узла скрепления равна 12,6 кг.
Существует модификация скрепления КБ-65 с применением клемм ОП-105 (рис 4.4). Данная клемма является упругой (рис 4.5).
![]() | ![]() |
Рисунок 4.4. Скрепление КБ-65: 1 – клемма упругая ОП-105. | Рисунок 4.5. Клемма упругая ОП-105. |
3.2. Бесподкладочное пружинное скрепление ЖБР-65 (рис 4.6)
Рисунок 4.6. Скрепление ЖБР-65
Скрепление ЖБР-65 бесподкладочное, упругое. Прикрепление рельса к шпале осуществляется при помощи двух упругих клемм, прижатие которых осуществляется путем затяжки гаек закладных болтов. Для увеличения площади касания с клеммой и предотвращения ее износа и разрушения между клеммой и гайкой устанавливается скоба прижимная.
Для упругой передачи нагрузки от рельса на шпалу, а также гашения вибрации укладывается подрельсовая упругая прокладка.
Для предотвращения поперечных перемещений рельса устанавливаются металлические скобы упорные, удерживаемые в неподвижном положении закладными болтами.
Электрическая изоляция данного скрепления обеспечивается при помощи подрельсовой прокладки, которая обеспечивает изоляцию рельса от шпалы. Упорная скоба, контактирующая с рельсом изолирована от шпалы прокладкой упругой. Закладной болт, контактирующий с клеммой и упорной скобой, устанавливается в пластиковый пустотообразователь, замоноличенный в шпалу.
Регулировка положения рельса по высоте осуществляется путем укладки регулировочных прокладок под рельс. Возможна регулировка на высоту до 15 мм.
Сборка узлов скреплений осуществляется на звеносборочных базах ПМС, при этом сборка скрепления осуществляется вручную, механизирована только затяжка гаек. В процессе эксплуатации требуется подтяжка и смазка гаек закладных болтов два раза в год.
Скрепление содержит 13 элементов в каждом узле, масса всех частей одного узла скрепления равна 7,24 кг.
Затяжку гаек при подтягивании их в процессе эксплуатации проводят с крутящим моментом 200 Н-м.
![]() | ![]() |
![]() | ![]() |
![]() | ![]() |
|
Рисунок 4.7. Элементы скрепления ЖБР-65
3.3. Скрепление шурупо-дюбельное ЖБР-65Ш (рис 4.8).
Скрепление ЖБР-65Ш бесподкладочное, упругое. Прикрепление рельса к шпале осуществляется при помощи двух упругих клемм, прижатие которых осуществляется путем завинчивания шурупов в полимерный дюбель, замоноличенный в шпалу. Для увеличения площади касания с клеммой и предотвращения ее износа и разрушения между клеммой и головкой шурупа устанавливается скоба прижимная.
Рисунок 4.8. Скрепление ЖБР-65Ш
Для упругой передачи нагрузки от рельса на шпалу, а также гашения вибрации укладывается подрельсовая упругая прокладка.
Для предотвращения поперечных перемещений рельса устанавливаются полимерные скобы упорные, удерживаемые в неподвижном положении шурупами.
Электрическая изоляция данного скрепления обеспечивается при помощи подрельсовой прокладки, которая обеспечивает изоляцию рельса от шпалы. Упорная полимерная скоба изолирует клемму, контактирующую с рельсом, от шпалы. Шуруп, контактирующий с клеммой, изолирован от шпалы полимерным дюбелем.
Регулировка положения рельса по высоте осуществляется путем укладки регулировочных прокладок под рельс. Возможна регулировка на высоту до 15 мм.
Сборка узлов скреплений осуществляется на звеносборочных базах ПМС, при этом сборка скрепления осуществляется вручную, механизировано только завинчивание шурупов. В процессе эксплуатации требуется подтяжка шурупов.
Скрепление содержит 9 элементов в каждом узле, масса всех частей одного узла скрепления равна 4,44 кг.
Затяжку шурупов при подтягивании их в процессе эксплуатации проводят с крутящим моментом 250 Н-м.
![]() | ![]() |
![]() | ![]() |
|
Рисунок 4.9. Элементы скрепления ЖБР-65Ш
Скрепление ЖБР-65Ш имеет несколько модификаций: ЖБР-65ПШ, ЖБР-65ПШМ, СМ-1.
ЖБР-65 ПШ (рис 4.10, 4.11) – шурупо-дюбельное скрепление с полимерной подкладкой. Данный тип скрепления применяется в кривых участках пути радиусом менее 650 м.
ЖБР-65ПШМ (4.12, 4.13) – шурупо-дюбельное скрепление с металлической подкладкой. Данный тип скрепления применяется в кривых участках пути радиусом менее 300 м.
СМ-1 (4.14, 4.15) – бесподкладочное шурупо-дюбельное скрепление с модифицированной упорной скобой.
![]() | ![]() |
Рисунок 4.10. Скрепление ЖБР-65ПШ | Рисунок 4.11. Подкладка полимерная |
![]() | ![]() |
Рисунок 4.12. Скрепление ЖБД-65ПШМ | Рисунок 4.13. Подкладка металлическая |
![]() | ![]() |
Рисунок 4.14. Скрепление СМ-1 | Рисунок 4.15. Скоба упорная |
3.4. Иностранные скрепления Vossloh W30 и SCHWIHAG SKL1.
В настоящее время на железнодорожной сети Российской Федерации активно укладываются шурупо-дюбельные скрепления зарубежных образцов: Vossloh W30 (рис 4.16) и SCHWIHAG SKL1 (рис 4.17). Конструкция данных скреплений схожа с конструкцией скрепления ЖБР-65Ш. Основное отличие – упругие клеммы других форм.
Рисунок 4.16. Скрепление Vossloh W30
Рисунок 4.17. Скрепление Schwihag SBS W SL-1-1900-R65
Скрепление Vossloh W30 – шурупо-дюбельное скрепление, разработанное Австрийской кампанией. Скрепление Schwihag – шурупо-дюбельное скрепление, разработанное Швейцарской кампанией.
Прикрепление рельса к шпале, работа по обеспечению стабильности рельсовой колеи и обеспечению электрической изоляции в данных скреплениях аналогичны скреплению ЖБР-Ш.
Данные скрепления полностью монтируются на шпалы, при их производстве и поставляются в собранном виде с установкой клемм в положение предварительного монтажа. При укладке шпал монтаж производится автоматически, путем перемещения клеммы в рабочее положение и затяжки шурупа.
Скрепления Vossloh W30 и Schwihag позволяют производить регулировку положения рельсов по высоте на величину 10 мм, и регулировку ширины колеи ±10 мм с шагом 2,5 мм, путем замены боковых упоров.
3.5. Анкерное рельсовое скрепление АРС-4 (рис 4.18).
Рисунок 4.18. Скрепление АРС-4
Скрепление АРС-4 бесподкладочное, упругое. Прикрепление рельса к шпале осуществляется при помощи двух упругих клемм, прижатие которых осуществляется путем изменения положения монорегулятора, закрепленного в анкере. Анкер жестко замоноличен в шпалу.
Для упругой передачи нагрузки от рельса на шпалу, а также гашения вибрации укладывается подрельсовая упругая прокладка.
Электрическая изоляция данного скрепления обеспечивается при помощи подрельсовой прокладки, которая обеспечивает изоляцию рельса от шпалы. Угловой изолятор обеспечивает изоляцию рельса от анкера и клеммы.
Регулировка положения рельса по высоте осуществляется путем укладки регулировочных прокладок под рельс. Возможна регулировка на высоту до 25 мм.
Сборка узлов скреплений осуществляется на звеносборочных базах ПМС вручную.
Скрепление содержит 9 элементов и анкер в каждом узле, масса всех частей одного узла скрепления равна 3,85 кг и масса анкера 4,7 кг.
3.7. Анкерное рельсовое скрепление Pandrol-350 (рис 4.19).
Рисунок 4.19. Скрепление Pandrol-350
Скрепление Pandrol-350 бесподкладочное, упругое, анкерное. Конструкция скрепления Пандрол-350 предусматривает закрепление рельса к подрельсовому основанию безболтовым способом с помощью анкера и двух пружинных прутковых клемм. Необходимое усилие прижатия достигается, когда клемма приводится в рабочее положение. Это исключает необходимость в приложении точного момента затяжки, как в скреплениях с резьбовыми и шурупными соединениями.
На П-образном изгибе в средней части клеммы зафиксирован прижимной изолятор, обеспечивающий электроизоляцию подошвы рельса и анкера. Боковые изоляторы устанавливаются на анкера, обеспечивают стабильность ширины рельсовой колеи и электроизоляцию подошвы рельса от выступов анкеров. В узле скрепления Пандрол-350 используется подрельсовая прокладка толщиной 10 мм. Прокладка изготавливается из термоэластопласта с выступами для препятствия ее смещению.
Сборка узлов скреплений осуществляется на шпальном заводе, монтаж и демонтаж скрепления полностью автоматизированный.
Ход работы
1. Группа делится на несколько бригад для выполнения работы. Каждая бригада получает для проведения работы шпалу со скреплением на стенде.
2. Группа при помощи инструмента демонтирует скрепление, фиксируя каждую технологическую операцию.
3. Все детали скрепления раскладываются на ровной поверхности и фотографируются.
4. Скрепление монтируется, устанавливается рельс, после чего фотографируется в собранном виде.
5. В собранном виде фотографируются все остальные скрепления.
6. Затяжка гаек болтовых скреплений осуществляется динамометрическим ключом с необходимым крутящим моментом.
7. При выполнении отчета каждая деталь скрепления подписывается и указывается ее функциональное предназначение.
8. В отчете необходимо провести сравнительный анализ скрепления с остальными типами скреплений по критериям назначения промежуточных рельсовых скреплений.
Дата добавления: 2019-09-13; просмотров: 2021; Мы поможем в написании вашей работы! |
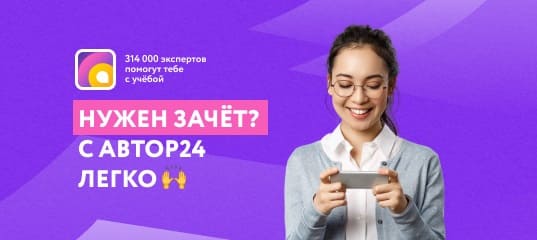
Мы поможем в написании ваших работ!