ТРЕБОВАНИЯ К УСТАНОВКЕ ДАТЧИКОВ ДВК
2.1. Датчики ДВК горючих газов и паров следует устанавливать в производственных помещениях, включая помещения БКУ и укрытия классов В-1 и В-1а.
Примечание. В помещениях БКУ и укрытиях класса В-1а объектов обустройства месторождений (кроме установок переработки газа) с периодическим пребыванием обслуживающего персонала, оборудованных вентиляционной установкой в исполнении, соответствующем категориям и группам образующихся взрывоопасных смесей, сблокированной с механизмом открывания входной двери, допускается датчики ДВК не устанавливать.
2.2. В заглубленных помещениях и приямках с технологическим оборудованием в пределах территории взрывопожароопасной установки, куда возможно проникновение взрывоопасных газов и паров извне, а также в заглубленных складских помещениях при хранении в них легковоспламеняющихся жидкостей (ЛВЖ) и горючих газов следует устанавливать по одному датчику ДВК на каждые 100 м2 площади, но не менее одного датчика на помещение.
2.3. В помещениях компрессорных и насосных станций датчики ДВК следует устанавливать у каждого перекачивающего агрегата в местах наиболее вероятных источников выделения взрывоопасных газов и паров, но не далее 3 м от источника (по горизонтали).
При групповом размещении агрегатов следует устанавливать не менее одного датчика ДВК на каждые 100 м2 площади.
2.4. При расположении технологического оборудования с источниками возможного выделения газов и паров в многоэтажных производственных помещениях с несплошными и решетчатыми междуэтажными перекрытиями каждый этаж следует рассматривать как самостоятельное помещение.
|
|
2.5. В нефтяной шахте датчики ДВК следует устанавливать в зоне исходящей струи воздуха действующих уклонов (находящихся в бурении и эксплуатации), насосных камер и полевых штреков.
Дополнительно следует осуществлять автоматический централизованный контроль за содержанием газа в атмосфере шахты.
2.6. Датчики ДВК в помещениях следует устанавливать в соответствии с плотностями газов и паров с учетом поправки на температуру воздуха:
над источником (при выделении легких газов с плотностью по воздуху менее 0,8);
на высоте источника или ниже него (при выделении газов с плотностью по воздуху от 0,8 до 1,5);
не более 0,5 м над полом (при выделении газов и паров с плотностью по воздуху более 1,5).
2.7. Датчики ДВК следует устанавливать во взрывоопасных зонах класса В-1г (в соответствии с ПУЭ, глава 7) следующих установок:
технологических установок промысловой подготовки нефти и газа, переработки газа и газохимических комплексов, содержащих горючие газы или ЛВЖ;
|
|
резервуаров для хранения сжиженных углеводородных газов (СУГ);
эстакад для налива ЛВЖ и СУГ и слива СУГ;
газонаполнительных станций СУГ;
насосно-компрессорных установок ЛВЖ, СУГ и горючих газов, находящихся на открытых площадках.
Допускается не устанавливать датчики ДВК на открытой площадке технологической установки (или ее части) в тех случаях, когда утечки технологической среды из возможных источников содержат более 5% молярной доли сероводорода и указанная площадка оснащена датчиками ПДК сероводорода в соответствии с требованиями раздела 1.
2.8. Допускается не устанавливать датчики ДВК во взрывоопасных зонах класса В-1г у помещений со взрывоопасными зонами классов В-1 и В-1а, а также устройств для выброса воздуха из системы вытяжной вентиляции помещений со взрывоопасными зонами любого класса, если указанные помещения оборудованы датчиками ДВК в соответствии с требованиями п.п. 2.1.-2.6.
2.9. На открытых площадках насосно-компрессорных установок, резервуарных парков СУГ, установок промысловой подготовки нефти и газа, переработки газа и газохимических комплексов датчики ДВК следует устанавливать по периметру зоны класса В-1г на расстоянии не более 20 м друг от друга, но не менее трех датчиков, в том числе при индивидуальном размещении технологических аппаратов, оборудования и резервуаров.
|
|
2.10. На эстакадах слива и налива СУГ следует устанавливать один датчик ДВК на два наливных стояка на расстоянии не более 20 м друг от друга вдоль эстакады. При двусторонней наливной эстакаде с полом, имеющим отверстия, - по одному датчику на четыре стояка.
2.11. На газонаполнительных станциях СУГ следует устанавливать по одному датчику ДВК у каждого газонаполнительного узла на расстоянии не более 5 м от узла наполнения со стороны подхода обслуживающего персонала.
2.12. Датчики ДВК следует устанавливать на открытых площадках технологических печей газоперерабатывающих заводов (ГПЗ), исходя из возможной загазованности их от расположенных вблизи взрывопожароопасных установок. Расстояние установки датчиков от печей - 15 м и не более 20 м друг от друга.
2.13. Датчики ДВК на открытых площадках следует устанавливать на высоте 0,5-1,0 м от поверхности земли (пола).
3.
Принцип действия клапанов Рабочая среда поступает в клапан по направлению стрелки на корпусе (под плунжер). Усилие, развиваемое МИМ или МЭП, через шток клапана 10 передаётся на плунжер 3, который, перемещаясь, открывает или закрывает проходное сечение между плунжером 3 и седлом 2 клапана, тем самым регулируется расход рабочей среды по определённому закону: - в клапане с линейной пропускной характеристикой обеспечивается приращение относительной пропускной способности пропорционально относительному ходу; - в клапане с равнопроцентной пропускной характеристикой обеспечивается приращение относительной пропускной способности по ходу пропорционально текущему значению относительной пропускной способности. В зависимости от вида действия клапана с МИМ они могут быть в исполнении НО (при отключении вспомогательной энергии клапан открывается) или НЗ (при отключении вспомогательной энергии клапан закрывается). При отключении вспомогательной энергии в клапанах с МЭП плунжер не меняет своего положения. Клапаны разгружены от входного давления. Рабочая среда, действуя на плунжер снизу, через отверстия в плунжере действует на него также сверху. Узел разгрузки плунжера от действия рабочей среды размещён в крышке клапанов.
|
|
Регулирующий клапан РК-1 (Dу = 150 ч 250 мм):
1 – корпус; 2 – золотник клапана нормально-открытой сборки; 3 – шток; 4 – сальник; 5 – регулировочная пружина; 6 – чаша гидропривода; 7 – мембрана; 8 – жесткий центр; 9 – золотник клапана нормально-закрытой сборки
Монтаж При монтаже клапана в агрегаты и системы необходимо руководствоваться общими техническими условиями на изготовление, приемку и монтаж агрегатов и систем, и указаниями технических условий, разработанных для каждого агрегата. При установке клапана на трубопровод необходимо, чтобы фланцы трубопровода не имели перекосов, а отверстия под крепежные детали совпадали с отверстиями во фланцах корпуса в пределах допусков по ГОСТ Р54432-2011. Для подвески, при монтаже или других работах следует использовать наружную поверхность корпуса. Установку клапана на трубопроводе следует производить так, чтобы направление движения среды совпадало с направлением стрелки на корпусе клапана. Рекомендуется устанавливать клапан на трубопровод, имеющий прямые участки до клапана длиной не менее 15DN и после клапана длиной не менее 20DN от магистральных патрубков клапана. Для удобства обслуживания должен быть обеспечен доступ к клапану. При монтаже запрещается: - применять ключи с удлиненными рукоятками; - устранять перекосы за счет натяжения (деформации) фланцев клапана. Перед монтажом клапан подвергают осмотру и испытаниям на герметичность мест соединений относительно внешней среды и на работоспособность. Испытание на герметичность мест соединений относительно внешней среды проводится подачей воздуха давлением PN в один из патрубков клапана при заглушенном втором. Затвор при испытании должен быть открыт. Пропуск воздуха через прокладочное соединение и в сальнике не допускается. Контроль – по технологии, принятой на объекте. Испытания на работоспособность проводятся с подключенным исполнительным механизмом. При подаче управляющего давления в МИМ в перестановочном диапазоне, указанном в таблице 1, или электрического сигнала в МЭП перемещение подвижных деталей должно производиться плавно без рывков и заеданий. Контроль визуальный.
ПАС-01
Прибор аварийной сигнализации и блокировки ПАС-01 является специализированным модульным программируемым микропроцессорным контроллером. ПАС-01 предназначен для контроля и обработки дискретных сигналов аварийных ситуаций, предупредительной и аварийной, световой и звуковой сигнализации, ведения архива событий и выдачи управляющих сигналов блокировки на исполнительные механизмы.
УСТРОЙСТВО И РАБОТА 4.1 ПАС-01 состоит из следующих модулей: - модуль питания МП-01; - модуль центрального процессора МЦП-1; - модуль индикации МДИ1-12R (МДИ1-6R для ПАС-01-06хх); - модуль расширения индикации МРИ1-12R (для ПАС-01-24хх); - модуль ввода дискретных сигналов искробезопасный МВДИ-4; - модуль реле МР (исполнения МР-1, МР-2, МР-3, МР-4); - модуль бесперебойного питания МБП-2011/24; - модуль внешней индикации МР-5. В зависимости от исполнения ПАС-01 комплектуется различным сочетанием модулей. 4.2 Конструктивно прибор выполнен в виде одного блока с использованием эле- ментов конструктива ЕВРОМЕХАНИКА 19’. Внешний вид ПАС-01 показан на рисунках 1.1 – 1.6. На лицевой панели расположены: - ЖКИ - 2 строки по 16 символов; - устройства световой индикации - 6, 12 или 24 светодиода повышенной яркости, закрытые съемным светофильтром; - 4 или 8 светодиодов состояния входов общепромышленного исполнения; - 4 или 8 светодиодов состояния выходных реле; - 3 служебные светодиодные индикаторы; - 7 кнопок для управления прибором. Под светофильтром установлен вкладыш - рассеиватель из карандашной кальки, на котором нанесено обозначение номера канала индикации. Модули устанавливаются в каркас с обратной стороны прибора в разъемы, закреп- ленные на кросс-плате, в произвольном порядке. На внешнем обрезе модулей установлены разъемные соединители для подключе- ния следующих цепей: - входных искробезопасных цепей МВДИ-4 (6 или12 входов); - входных цепей общепромышленного исполнения МР (МР-1, МР-4 – 4 входа, МР-2 - 2 входа); - выходных цепей МР (МР-1, МР-4 – 4 выхода, МР-2 – 6 выходов, МР-3 – 8 выходов); - цепей внешней звуковой сигнализации МР (МР-1, МР-2 - 1 выход); - программатора - разъем "ПРОГРАММАТОР" МЦП-1; ПАС-01 ЦКЛГ.421411.001 РЭ изм. "3" 21 - интерфейса - разъем "RS-485" МЦП-1; - сети питания - разъем "220 В, 50 Гц" МП-01. С обратной стороны каркаса имеется зажим защитного заземления.
Билет № 8
1. Полупроводнико́вый дио́д — полупроводниковый прибор, в широком смысле — электронный прибор, изготовленный из полупроводникового материала, имеющий два электрических вывода (электрода). В более узком смысле — полупроводниковый прибор, во внутренней структуре которого сформирован один p-n-переход.
В отличие от других типов диодов, например, вакуумных, принцип действия полупроводниковых диодов основывается на различных физических явлениях переноса зарядов в твердотельном полупроводнике и взаимодействии их с электромагнитным полем в полупроводнике.
Диоды широко используются для преобразования переменного тока в постоянный (точнее, в однонаправленный пульсирующий) . Диодный выпрямитель или диодный мост (То есть 4 диода для однофазной схемы, 6 для трёхфазной полумостовой схемы или 12 для трёхфазной полномостовой схемы, соединённых между собой по схеме) — основной компонент блоков питания практически всех электронных устройств. Диодный трёхфазный выпрямитель по схеме Ларионова А. Н. на трёх параллельных полумостах применяется в автомобильных генераторах, он преобразует переменный трёхфазный ток генератора в постоянный ток бортовой сети автомобиля. Применение генератора переменного тока в сочетании с диодным выпрямителем вместо генератора постоянного тока с щёточно-коллекторным узлом позволило значительно уменьшить размеры автомобильного генератора и повысить его надёжность. Двухполупериодный выпрямитель
Двухполупериодный выпрямитель — устройство или контур, проводящий ток в течение обеих половин цикла переменного тока. Двухполупериодный выпрямитель состоит из трансформатора с центральным отводом вторичной обмотки, двух диодов и сопротивления нагрузки.
Дата добавления: 2019-09-08; просмотров: 411; Мы поможем в написании вашей работы! |
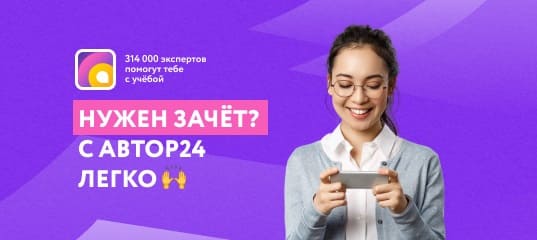
Мы поможем в написании ваших работ!