Проектирование материальных потоков и техпроцесса транспортирования
Этапы построения схемы материальных потоков:
1. За основу проектирования транспортной системы принимают схему материальных связей машиностроительного производства, на которой указывают грузопотоки между основным оборудованием, накопителями, производственными подразделениями.
2. Необходимо выявить потребность в основных и вспомогательных материалах, заготовках, полуфабрикатах и изделиях в тоннах на всю программу выпуска для каждого производственного участка, а также программу выпуска полуфабрикатов, готовых изделий в тоннах с каждого производственного участка.
3. Схема материальных потоков служит базой для разработки технологических процессов транспортных работ, а также выбора вида, числа и основных технических параметров средств транспортирования. При проектировании выполняют несколько вариантов схем материальных потоков и выбирают оптимальный.
Пример схемы материальных связей сборочного цеха приведен на рисунке ниже.
![]() |
Схема материальных связей сборочного цеха: 1 — склад готовых деталей; 2 — участок подправки и окраски корпусных деталей; 3 — участок сборки комплектов и узлов; 4 — участок сборки машин; 5 — участок испытания и отладки машин; 6 — участок окраски машин; 7 — краскоприготовительный участок; 8 — участок комплектования и упаковки; | Грузопотоки: Д — отдельных деталей; У — собранных узлов; К — собранных комплектов; М — собранных машин |
Требования, предъявляемые к оптимальной транспортно-технологической схеме:
|
|
· минимальное число действительно необходимых операций, минимальные расстояния транспортирования и число транспортных перемещений грузов;
· автоматизация каждой операции и всего процесса транспортирования;
· максимально возможное совмещение транспортных операций с операциями изготовления изделий;
· использование для автоматизации процессов прогрессивных высокопроизводительных средств, однотипность средств автоматизации процессов транспортирования ;
· малое число пересечений и разветвлений;
· требования охраны труда;
· экономическая эффективность и ремонтопригодность.
Блок-схема выбора оптимальной транспортной системы с учетом габаритных и массовых характеристик грузов, а также производственной программы и состава производственного оборудования приведена на рисунке ниже
Проектирование межоперационных транспортных систем. Промышленные роботы
В качестве транспортно-загрузочных устройств в автоматизированном производстве широкое распространение получили промышленные роботы и манипуляторы. Промышленный робот — это перепрограммируемый автоматический манипулятор промышленного применения.
|
|
Характерные признаки промышленного робота:
- автоматическое управление;
- способность к быстрому и относительно легкому перепрограммированию,
- способность к выполнению трудовых действий.
С помощью роботов можно объединять оборудование в производственные комплексы, обеспечивающие гибкую структуру производственных процессов в широком диапазоне серийности производства. Промышленные роботы зарекомендовали себя как гибкие автоматизированные средства реализации внутрицеховых и межоперационных материальных связей, обладающие целым рядом преимуществ по сравнению с другими устройствами:
- малые габаритные размеры подвижного органа,
- большой диапазон регулирования скорости перемещения,
- автоматические перемещения,
- автономность.
Роботизированный технологический комплекс (РТК) – автономно действующая совокупность средств производства, включающая набор основного и вспомогательного оборудования с наличием промышленного робота, выполняющего технологические, вспомогательные операции, а также обеспечивающую полностью автоматизированный цикл работы внутри комплекса и его связь с входными и выходными потоками остального производства.
|
|
Роботизированные технологические комплексы, используемые в машиностроительном производстве, можно классифицировать по трем основным признакам:
· Функциональный признак определяет характер функций, выполняемых промышленным роботом в составе комплекса. По функциональному назначению роботы делятся на:
- промышленные роботы, выполняющие операции технологического процесса (сборка, окраска, сварка и т. д.);
- многофункциональные роботы, выполняющие операции транспортирования в производственном процессе (загрузка и разгрузка станков, перемещение между оборудованием и т. д.) и одновременно технологические и транспортные операции.
· Структурный признак характеризует тип структуры комплекса (взаимодействие промышленного робота и основного оборудования внутри комплекса). По структурному признаку различают следующие РТК (рисунок 1):
- однопозиционные — модули «станок — робот», «сборочный стенд — робот» и т. д., включающие один робот в комплекте с единицей основного оборудования (а),
- однопозиционные групповые, включающие один робот, обслуживающий группу основного оборудования (б);
|
|
- многопозиционные, включающие группу роботов, выполняющих взаимосвязанные или взаимно дополняющие функции (в).
Рисунок 1
· Планировочный признак определяет пространственное расположение оборудования. Используются 5 типовых схем (рис. 2):
- Схема РТК. 1 включает комплексы, характеризуемые линейным расположением технологического и вспомогательного оборудования (а). Этот тип планировки комплексов создается на базе роботов, работающих в декартовой системе координат.
- Схема РТК.2 характеризуется линейно-параллельным расположением основного и вспомогательного оборудования (б). Создается на базе роботов портального типа с плечелоктевой конструкцией манипулятора.
- Схема РТК.3 включает комплексы, созданные на базе роботов, работающих в цилиндрической системе координат с горизонтальной осью вращения («качением» манипулятора) (в).
Рис. 2
- Схема РТК.4 создается на базе роботов, работающих в цилиндрической системе координат, и характеризуется круговым расположением основного и вспомогательного оборудования (г).
- Схема РТК.5 создается на базе роботов, работающих в сферической системе координат (д). Так как в данный тип схемы входят роботы, имеющие широкие функциональные возможности (до шести степеней подвижности), комплексы используются при групповом обслуживании разнотипного по схемам загрузки оборудования, а также при выполнении окрасочных и других работ.
В автоматизированном машиностроительном производстве широкое применение для транспортирования деталей и собираемых изделий нашли конвейерные системы, позволяющие обслуживать интенсивные материальные потоки. Так например, широкое использование для поточного и непоточного сборочного и механообрабатывающего производств нашли транспортные системы из роликовых конвейеров, применяемые как для перемещения полуфабрикатов, так и для их хранения. Так же в машиностроительном производстве возможно комбинированное применение непрерывного и периодического транспорта при условии расположения в местах их стыковки буферных накопителей. В качестве накопителей могут быть использованы собственно транспортные средства, специальные накопительные устройства или производственная тара.
Дата добавления: 2019-09-02; просмотров: 294; Мы поможем в написании вашей работы! |
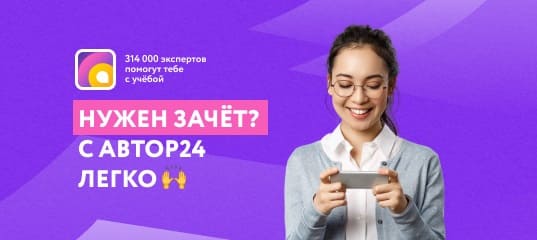
Мы поможем в написании ваших работ!