И температуры на выходе из кристаллизатора
Анализ процесса затвердевания заготовки в кристаллизаторе провел Хилс [5]. Расчет теплового поля заготовки ведет к полиному, константы которого рассчитывают с учетом поверхностных условий. Уравнения и результаты даны в безразмерных параметрах, что позволяет легко применять их для произволь-ных исходных данных и размеров заготовки. Расчетом установлены толщина застывшей корки в зависимости от расстояния от уровня металла, температура на поверхности заготовки и тепло, отведенное кристаллизатором.
Для определения толщины корки в кристаллизаторе , температуры по-верхности заготовки и количества отведенного тепла
А.В.Д. Хилс [5] уста-новил ряд упрощенных соотношений, которые в системе СИ имеют вид:
(3.1)
(3.2)
(3.3)
Безразмерное расстояние от уровня стали в кристаллизаторе
, (3.4)
где х -реальное расстояние, м; -время нахождения заготовки на глубине х в кристаллизаторе, с; v-скорость заливки, м*с-1;
-коэффициент теплоотдачи от поверхности заготовки к охлаждающей воде, Вт*м-2 *K-1:
(3.5)
|
|
где d -толщина зазора между заготовкой и стенкой кристаллизатора; - коэффициент теплопроводности жидкого вещества в зазоре;
-толщина медной стенки кристаллизатора;
- коэффициент теплопроводности меди;
-коэффи-циент теплоотдачи от внешней стороны медной стенки кристаллизатора к охла-ждающей воде (определяют по критериальным соотношениям).
Хилс использовал уравнение Nu = 0,023 (Re)0,8 (Pr)0,33 и параметры: Y- эф-фективная длина кристаллизатора, м (соответствует уровню стали в кристалли-заторе); -безразмерная длина кристаллизатора;
-безраз-мерная толщина застывшей стали;
-реальная толщина застывшей корки, м;
-безразмерная температура поверхности заготовки;
-реальная темпе-ратура поверхности заготовки, °С;
-температура солидуса; Н' = L 1 /( ctS )-безраз-мерное общее тепло затвердевания; L 1-реальная скрытая теплота затвердевания (включая теплоту перегрева)
(здесь t 1 -температура разливаемой стали);
-безразмерное тепло, отведенное от части заготовки длиной х, приходящееся на единицу окружности кристаллизатора;
-реальное тепло, отведенное из части заготовки длиной х, приходящееся на единицу окру-жности кристаллизатора за единицу времени.
Для расчета температуры застывшей корки в кристаллизаторе К. Фекете [6] разработал примерные упрощенные методы. Он исходит из рассуждений, что кристаллизатор в МНЛЗ является теплообменником, работающим противо-точно, так что можно считать, что разливаемая сталь охлаждается проточной водой. Им получено соотношение:
|
|
, (3.6)
где -разность температур между жидкой сталью и охлаждающей кристалли-затор водой;
-разность температур обоих веществ при входе в кристаллиза-тор;
-коэффициент теплоотдачи, Вт* м-2 *К-1;
-охлаждающая внутренняя поверхность кристаллизатора, м2;
-энтальпия стали;
- энтальпия воды, равная
;
-внутреннее сечение кристаллизатора, м; v-скорость вытягивания, м*с -1;
-плотность застывшей стали, кг*м -3; с-теплоемкость ста-ли, Дж * кг –1* К-1.
На основании известных результатов изучения отвода тепла, проведен-ного X. Крайнером и Б. Тарманном [7], а также И. Саважем и В.Х. Притчардом [2], К. Фекете составил уравнение для отвода тепла кристаллизатором:
. (3.7)
Для определения средней плотности теплового потока от кристаллиза-тора на данном расстоянии х от уровня стали в кристаллизаторе необходимо проинтегрировать предыдущее соотношение:
|
|
; (3.8)
, (3.9)
где - время, с.
При описании передачи тепла от твердого тела к обтекающей его жидко-сти или газу имеется в виду теплообмен. Количество тепла Q, Дж, переходящее с поверхности тела в окружающую среду, определяют по формуле Ньютона:
(3.10)
где - коэффициент теплоотдачи, Вт м-2 К-1; tп – температура поверхнос-ти тела, 0С; tср – температура окружающей среды, 0С; S – охлаждаемая площадь, м2;
- время, с.
Согласно уравнению Ньютона получим:
(3.11)
где , К - среднелогарифмическая разность температур в кристаллиза-торе между сталью и охлаждающей водой:
(3.12)
Здесь
(индекс 1 относится к стали, 2-к воде; р- для температуры входа; к- выхода).
Из теории расчета теплового обмена известно, что среднелогарифмичес-кую разность можно заменить среднеарифметической, если
|
|
По-видимому, эти условия при разливке стали на МНЛЗ будут всегда выполняться:
(3.13)
(3.14)
При этом упрощении коэффициент теплоотдачи из уравнения (3.11) будет выражен следующим образом:
(3.15)
Теперь подставим соотношение под уравнением (3.11) и (3.15) в уравнение (3.6) и одновременно заменим по предполагаемым температурным разностям и
выражения:
, (3.16)
(3.17)
В результате получим из уравнения (3.6):
(3.18)
В уравнение (3.17) следует еще подставить выражение, которое определя-ет количество общего тепла затвердевания в зависимости от времени. Если тол-щина корки
(3.19)
Общий объем застывшей корки на расстоянии х от уровня стали, то:
(3.20)
Количество освободившегося общего тепла ,
, которое должны отвести за время
через единицу поверхности
, выражают как плотность теп-лового потока:
(3.21)
Получим окончательный вид уравнения для расчета средней температуры застывшего слоя металла в кристаллизаторе, который будет иметь вид:
, (3.22)
где
Градиент температуры в застывшей корке стали определим графически с помощью двух точек в координатах:
, (3.23)
соответствующих границе зоны кристаллизации с температурой , и
(3.24)
Рассчитаем температуру поверхности заготовки в кристаллизаторе разме-ром а = 0,175 м; b = 0,175 м через 6,5 с после начала разливки и далее через каждые 5 с до выхода заготовки из кристаллизатора.
Для расчета принимаем: S=0,63 ;
=7055
; с= 545
;
; высота кристаллизатора h = 0,9 м.
Время движения заготовки в кристаллизаторе
=41,5 с.
За первые 6,5 с заготовка пройдет путь 0,021667*6,5 = 0,141 м, а соответствующая площадь кристаллизатора = 0,63*(6,5/41,5)=0,099
. По уравнению (3.21) определим:
По уравнению (3.9) рассчитаем :
Температуру определим последовательным приближением (итераци-ей). В калькулятор вводим оцениваемую величину и после вычисления с помо-щью уравнений (3.22) добавляем в
уточненное значение, чем достигаем же-лаемой точнoсти результатов. 1. Оценочная
=1460,
(расчетная)=1481,7. 2. Оценочная
=1481,7,
(расчетная)=1481,9.Таким образом,
=1482°С.
Аналогично при определении примерной температуры затвердевшего слоя заготовки на выходе из кристаллизатора (т.е через 41,5 с) получим:
После подстановки в уравнение (3.22) определим температуру с помо-щью итерации. 1.Оценочная =1400,
(расчетная)=1332,7; 2.Оценочная
=1332,7
(расчетная)=1328,7; 3.Оценочная
=1328,7
(расчетная)=1328,5.
=1329°С.
Граничные и промежуточные данные расчетов представлены в таблице 3.
Таким образом, средняя температура затвердевшего слоя стали в кристаллизаторе через 6,5 с после начала разливки составляет 1482°С, через 41,5 с (на выходе из кристаллизатора) она равна 1329°С.
Таблица 3. Результаты расчета температуры закристаллизовавшегося слоя и толщины корки по ходу движения слитка в кристаллизаторе.
Параметры | Время движения слитка в кристаллизаторе, с | |||||||
6,5 | 11,5 | 16,5 | 21,5 | 26,5 | 31,5 | 36,5 | 41,5 | |
Пройденный путь, м | 0,141 | 0,25 | 0,358 | 0,466 | 0,574 | 0,683 | 0,791 | 0,9 |
Площадь крист-ра, м2 | 0,099 | 0,174 | 0,25 | 0,326 | 0,402 | 0,478 | 0,554 | 0,63 |
Колич. освободивш. тепла, МВт/м2 | 1,503 | 1,117 | 0,924 | 0,803 | 0,718 | 0,654 | 0,604 | 0,563 |
Ср. плотн. теплового потока, МВт/м2 | 2,272 | 2,081 | 1,913 | 1,767 | 1,639 | 1,526 | 1,428 | 1,341 |
Средняя температура застывшего слоя, оС | 1482 | 1448 | 1418 | 1393 | 1373 | 1355 | 1341 | 1329 |
Толщ. закристаллиз. корочки, мм | 7,9 | 10,51 | 12,59 | 14,37 | 15,96 | 17,4 | 18,73 | 19,97 |
Координата у1, мм | 79,6 | 76,99 | 74,9 | 73,13 | 71,54 | 70,1 | 68,77 | 67,53 |
Координата у2, мм | 83,5 | 82,24 | 81,2 | 80,31 | 79,52 | 78,8 | 78,14 | 77,51 |
Температуру на поверхности слитка определим графически с помощью выражений (3.23) и (3.24) (Приложение 1, рис. 1) . Толщина корки по формуле (3.19) через 6,5с будет
мм, а через 41,5 с
мм.
Температура поверхности через 6,5 с составляет 1445°С, температура через 41,5с на выходе из кристаллизатора равна 1190°С.
3.2 Определение температуры поверхности по длине
заготовки и расхода воды на охлаждение в ЗВО
Для выбора режима охлаждения в зависимости от разливаемой стали (те-мпературы поверхности слитка в конце ЗВО) и скорости вытягивания слитка задается кривая температуры поверхности по длине слитка. Эта кривая выбира-ется из условия минимизации термических напряжений в непрерывнолитом слитке, что достигается равенством скоростей охлаждения слоев металла, рас-положенных у фронта кристаллизации и на поверхности:
.
Решение этого равенства позволило получить следующее уравнение:
, (3.25)
где qо = to/tr –относительная температура поверхности и заготовки на вы-ходе из кристаллизатора; to –температура поверхности слитка на выходе из кри-сталлизатора, оС; tr – температура кристаллизации стали, оС; qк = tк/tr– относите-льная температура поверхности заготовки в конце затвердевания; (tк – темпера-тура поверхности слитка в конце затвердевания, оС); а – толщина слитка;
dо–толщина оболочки слитка при выходе из кристаллизатора.
Как следует из уравнения, если заданы толщина оболочки, температура поверхности слитка на выходе из кристаллизатора и температура поверхности слитка в конце зоны затвердевания, то для каждого размера заготовки и скоро-сти вытягивания существует определенная закономерность изменения темпера-туры поверхности слитка по его длине, при которой коэффициент j имеет мак-симальное постоянное значение на всем участке охлаждения.
Так как коэффициент j постоянен, то для любого участка зоны вторич-ного охлаждения можно записать:
, (3.26)
где qn и d – относительная температура и толщина оболочки слитка в мо-мент времени t;
Если известно распределение температуры по длине слитка, то приведен-ное уравнение позволяет определить толщину оболочки слитка в любой момент времени t.
Время достижения соответствующей температуры поверхности определя-ется из выражения:
,
(3.27)
где r – плотность жидкой стали; qк – скрытая теплота плавления стали;
l – коэффициент теплопроводности стали.
Уравнения (3.26), (3.27) позволяют построить зависимости температуры поверхности слитка tn и толщины затвердевающей оболочки d от времени t или глубины жидкой лунки L для заданных скоростей разливки и температуры поверхности слитка в конце затвердевания tк .
На основании приведенных выше уравнений определим температуру по-верхности по длине слитка при разливке на МНЛЗ заданной марки стали. Принимаем температуру поверхности слитка в конце затвердевания металла tк=9000С; теплоемкость затвердевшей стали С=0,545 кДж/(кг*К); теплопровод-ность стали l=29 Вт/(м*К); скрытую теплоту затвердевания qк=270 кДж/кг; коэффициент кристаллизации k=30 мм/мин0,5; эффективную высоту кристал-лизатора Н=0,9 м. По значению толщины оболочки d и температуры поверхно-сти tп слитка на выходе из кристаллизатора и температуре поверхности слитка в конце зоны затвердевания определяем из условий (t–время от начала выхода из кристаллизатора; L–расстояние от среза кристаллизатора) найдем
Толщина оболочки слитка на выходе из кристаллизатора была определена выше и составляет 19,97 мм.
Температура поверхности слитка на выходе из кристаллизатора равна 1190 оС.
Относительная температура поверхности слитка на выходе из кристалли-затора:
в конце затвердевания слитка
Тогда
Используя уравнения (3.25), (3.26) и задаваясь температурой поверхности слитка, определим зависимости
Время, необходимое для достижения температуры поверхности 11500С при j=0,51 составит
Относительная температура поверхности:
Определим
После подстановки получим t=29,3 с или 0,49 мин.
Толщина оболочки слитка при tn=11500C
мм.
Расстояние точки с tn=11500C от нижнего среза кристаллизатора:
L=wt=1,3*0,49=0,63 м.
Распределение температуры поверхности и толщины корки слитка по длине непрерывнолитого слитка при j=0,51 приведено в таблице 4.
Данные, приведенные на рис.2 (Приложение 1), иллюстрируют распреде-ление температуры поверхности по длине слитка и изменение толщины закри-сталлизовавшейся оболочки.
Наличие распределения температур по длине слитка и толщине оболочки позволяет определить тепловые потоки на поверхности слитка, необходимые для отвода физической теплоты оболочки и теплоты кристаллизации qкр:
, (3.28)
, (3.29)
где tср1, tср2 – средняя температура оболочки в начале и конце участка охлаждения; d1, d2 – толщина оболочки в начале и в конце участка охлаждения; L1, L2 – расстояние от торца кристаллизатора на входе и выходе с участка охлаждения; w – скорость вытягивания слитка; С – теплоемкость затвердевшего металла.
Таблица 4. Изменение температуры поверхности заготовки и толщины корки по длине непрерывного слитка.
tп, 0С….. | 1190 | 1150 | 1100 | 1050 | 1000 | 950 | 900 |
Qo | 0,79 | 0,79 | 0,79 | 0,79 | 0,79 | 0,79 | 0,79 |
Qk | 0,6 | 0,6 | 0,6 | 0,6 | 0,6 | 0,6 | 0,6 |
![]() | 0,51 | 0,51 | 0,51 | 0,51 | 0,51 | 0,51 | 0,51 |
Qn | 0,79 | 0,76 | 0,73 | 0,7 | 0,66 | 0,63 | 0,6 |
To | 8,44 | 8,44 | 8,44 | 8,44 | 8,44 | 8,44 | 8,44 |
Tn | 8,44 | 7,39 | 6,37 | 5,57 | 4,92 | 4,39 | 3,95 |
t, мин… | 0 | 0,49 | 1,34 | 2,55 | 4,21 | 6,46 | 9,46 |
d, мм…. | 19,97 | 25,86 | 34,56 | 44,9 | 57,05 | 71,17 | 87,5 |
L, м…… | 0 | 0,63 | 1,75 | 3,31 | 5,47 | 8,39 | 12,3 |
Зная тепловой поток и температуру поверхности, можно определить
.
Для выполнения требований по плавному изменению интенсивности ох-лаждения слитка по его длине для стали различных марок и возможности регу-лирования длины участка водяного охлаждения в зависимости от скорости ли-тья и глубины жидкой лунки вся зона вторичного водяного охлаждения разби-вается на отдельные секции. Каждая секция обеспечивается самостоятельным подводом воды и установкой соответствующих форсунок.
При расчете основных параметров систем вторичного охлаждения радиальных и криволинейных машин необходимо скорректировать плотность орошения слитка по малому радиусу за счет стекания воды, уменьшив его на 20…30 % по сравнению с большим радиусом.
Как показывает практика эксплуатации слябовых машин, протяженность зоны форсуночного охлаждения по узким граням может быть сокращена на 20…30 %.
Определим расход воды на четырехроликовую секцию длиной l=1 м, расположенную на расстоянии L=2,0 м от мениска металла.
Как следует из уравнений (3.28), (3.29) необходимо определить среднюю температуру и толщину оболочки в начале и конце участка охлаждения. По приведенным числовым данным и данным рис.2 определим, что tп на входе в секцию составляет 1130 0С, а на выходе из секции tп =10900С, соответственно толщина образовавшейся корки слитка на входе и выходе из секции соответст-венно составили d1 =30 и d2 =38 мм.
Принимаем с целью упрощения расчета линейное изменение температу-ры по толщине корочки. Тогда
Суммарный тепловой поток q на поверхности слитка, обусловлен-ный отводом физической теплоты и теплоты кристаллизации, составит:
а средний коэффициент теплоотдачи соответственно:
Плотность орошения на данном участке составит:
Учитывая, что секция расположена практически вертикально, расход во-ды на грань по большому радиусу и грань по малому радиусу будет одинаков, а общий расход воды на секцию составит:
Дата добавления: 2019-09-02; просмотров: 175; Мы поможем в написании вашей работы! |
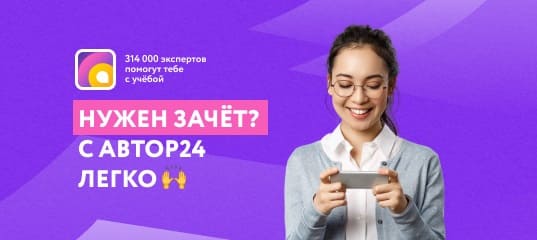
Мы поможем в написании ваших работ!