Пути повышения эффективности использования рабочего времени
Процесс управления рабочим временем на предприятиях должен осуществляться при помощи определенных рычагов и стимулов, которые должны включать не только меры, связанные с пресечением и наказанием работников, допускающих те или иные нарушения, но и меры профилактического характера предупреждающие возможные нарушения, меры, стимулирующие улучшение использования рабочего времени.
Экономические рычаги воздействуют на рабочее время посредством стимулирования работников, побуждения их к достижению высоких результатов в труде и представлены мерами поощрения и наказания, из которых, наибольшее значение имеют меры материального и морального поощрения за более рациональное использование рабочего времени. Если правовое регулирование осуществляется посредством правильного применения правовых норм, оказывающих воздействие на поведение людей, участвующих в процессе производства, то к учетно-контрольным рычагам относится применение средств механизированного учета и контроля за использованием рабочего времени, внедрение (там, где это возможно) автоматизированных пропускных устройств.
Стимулы, с помощью которых также удается управлять рабочим временем, можно разделить на материальные, моральные.
К материальным и моральным стимулам относятся: выплата премий по итогам работы; награждение ценными подарками, почетной грамотой, занесение на Доску почета и т.д.
|
|
Хотелось бы отметить, что со временем острота используемых стимулов притупляется и снижается действенность применяемых форм мотивирования, поэтому необходимо постоянно обновлять и искать новые формы. Широко применяя различные формы поощрения за добросовестный труд, необходимо в то же время решительно бороться с нарушениями трудовой дисциплины.
Важным элементом системы управления рабочим временем является выявление резервов, социально-экономическая оценка потерь и определение степени влияния на эффективность производства.
Для формирования системы управления рабочим временем нужны соответствующие экономические условия, общая заинтересованность в результатах труда, такой механизм экономического стимулирования, который предполагает использование, как поощрений, так и наказаний, включает материальное стимулирование и ответственность за рациональное использование рабочего времени. Важным условием повышения действенности системы стимулирования является соблюдение единства подхода к поощрению и наказанию. Единство не означает однообразие приемов, методов, форм стимулирования и санкций. Напротив, такое единство требует максимального учета особенностей труда и производства. Между тем, на практике можно встретить недопустимое разнообразие в характере и степени наказаний за один и тот же проступок.
|
|
Виды брака, причины и пути устранения при обработке детали
При обтачивании цилиндрических поверхностей возможны следующие виды брака:
1. Часть поверхности детали осталась необработанной;
2. Размеры обточенной поверхности неправильны;
3. Обточенная поверхность получилась конической;
4. Обточенная поверхность получилась овальной;
5. Шероховатость обработанной поверхности не соответствует указаниям в чертеже.
Часть поверхности детали остается необработанной из-за неправильных размеров заготовки, недостаточного припуска на обработку, плохой правки (кривизна) заготовки, неправильной установки и неточной выверки детали, неточного расположения центровых отверстий и смещения заднего центра. Такой брак обычно неисправим.
Чтобы предупредить брак такого вида, необходимо:
1. Осматривать заготовку и проверять сомнительные размеры ее;
2. Следить за достаточной величиной припуска на обработку;
3. Тщательно править заготовку перед её установкой на станок;
4. Проверять правильность установки заготовки;
|
|
5. Следить за правильным расположением центровых отверстий;
6. Проверять правильность установки заднего центра.
Неправильные размеры обточенной поверхности возможны при неточной установке резца на глубину резания или при неправильном измерении детали при снятии пробной стружки. Исправить этот брак можно повторным обтачиванием только в том случае, если размер диаметра детали получился больше требуемого. При получении диаметра детали меньше требуемого, брак неисправим.
Конусность обточенной поверхности получается обычно при результате смещения заднего центра относительно переднего. Для устранения причины этого вида брака необходимо правильно установить задний центр. Обычной причиной смещения заднего центра является попадание грязи или мелкой стружки в коническое отверстие пиноли. Очисткой центра и конического отверстия пиноли можно устранить и эту причину брака. Если и после очистки вершины конусов переднего и заднего центров не совпадают, надо соответственно переместить корпус задней бабки на ее плите.
Исправить этот вид брака повторным обтачиванием можно только в том случае, если меньший диаметр конуса равен или больше требуемого размера.
|
|
Овальность обточенной детали получается при биении шпинделя вследствие неравномерной выработки его подшипников или неравномерного износа его шеек. Предупредить брак по этой причине можно своевременной проверкой и ремонтом станка.
Указанный вид брака получается также при биении переднего центра вследствие попадания грязи или мелкой стружки в коническое отверстие шпинделя.
Очисткой переднего центра и конического отверстия шпинделя можно устранить брак по этой причине.
Недостаточная чистота поверхности при обтачивании может быть по ряду причин:
1. Большая подача резца,
2. Применение резца с неправильными углами,
3. Плохая заточка резца,
4. Малый радиус закругления вершины резца,
5. Большая вязкость материала детали,
6. Вибрации резца из-за большого вылета из резцовой головки,
7. Недостаточно прочное крепление резца,
8. Увеличение зазора между отдельными частями суппорта,
9. Вибрация детали из-за слабого крепления ее или вследствие износа подшипников и шеек шпинделя.
Перечисленные в п. 5 причины брака могут быть своевременно устранены. Исправить этот брак иногда удается снятием тонкой отделочной стружки.
Брак при подрезании торцовых поверхностей и уступов и меры его предупреждения. При подрезании торцовых поверхностей и уступов возможны следующие виды брака:
1. Часть торцовой поверхности или уступа осталась необработанной;
2.Торцовая поверхность или уступ неправильно расположены по длине детали;
3. Уступ расположен не перпендикулярно к оси детали;
4. Чистота торцовой поверхности или уступа недостаточна.
Часть торцовой поверхности или уступа остается необработанной вследствие неверных размеров заготовки, малого припуска на обработку, неправильной установки и неточной выверки детали в патроне, неправильной установки резца по длине детали или по высоте центров.
Такой брак обычно неисправим, но предупредить его можно:
1. Проверкой размеров заготовки;
2. Увеличением припуска на обработку;
3. Проверкой правильности установки детали и резца.
Неправильное расположение торцовой поверхности или уступа по длине получается при неверном или неточном нанесении риски на поверхности детали, при неточной установке резца или несвоевременном выключений самохода (при продольной подаче), а также при осевом смещении детали в патроне в результате недостаточно прочного ее закрепления. Если при этом граница уступа перейдена, то брак неисправим. Предупредить такой брак можно более тщательным нанесением рисок, проверкой установки резца и прочности закрепления детали в патроне, а также своевременным выключением самохода при работе с продольной подачей.
Неперпендикулярное расположение торцовой поверхности или уступа к оси детали при работе с поперечной подачей получается при неточности направляющих суппорта, вследствие отжима резца из-за его чрезмерно большого вылета или слишком малого сечения, непрочного закрепления резца в резцовой головке, а также из-за завышенных подачи и глубины резания. При работе с продольной подачей обычная причина брака -- неправильная установка резца. Устранив перечисленные причины, брак, указанный в п. 3, можно избежать. Часто, когда требуется изготовить большую партию деталей, измеряют не диаметр канавки, а ее глубину, пользуясь для этого шаблоном. Для этой же цели можно пользоваться штангенциркулем, у которого для таких измерений имеется специальный выдвигаемый стержень, или штангенглубиномером. Ширину канавки измеряют линейкой, штангенциркулем или шаблоном.
Брак при вытачивании канавок и отрезании и меры его предупреждения.
При вытачивании канавок и отрезании возможны следующие виды брака:
1. Неточное расположение канавки по длине детали;
2. Ширина канавки больше или меньше требуемой;
3. Глубина канавки больше или меньше требуемой;
4. Неправильная длина отрезанной детали;
5. Недостаточная чистота поверхности канавки или торца отрезанной детали.
Неточное расположение канавки по длине детали получается при неправильной разметке места под канавку или неверной установке резца и является результатом невнимательности токаря; брак является неисправимым. Предупредить брак можно точной разметкой и правильным нанесением рисок под канавки, проверкой нанесенных рисок и правильной установкой резца по длине детали.
Ширина канавки получается больше или меньше требуемой, если ширина резца выбрана неверно. Брак неисправим, когда ширина канавки получилась больше требуемой; при ширине канавки меньше требуемой исправление возможно дополнительным вытачиванием.
Глубина канавки больше требуемой получается при неправильной длине прохода резца. Брак неисправим.
Неправильная длина отрезанной детали получается при невнимательной работе. Брак неисправим, если длина отрезанной детали получилась меньше требуемой.
Недостаточная чистота поверхности канавки, а также торца отрезанной детали, получается, по причинам, указанным выше для такого же вида брака при подрезании торцов и уступов. Кроме того, причиной может быть неверная установка резца, касающегося боковым краем уже обработанной поверхности.
Брак при сверлении и меры его предупреждения.
Основной причиной брака при сверлении является увод сверла от требуемого направления, что чаще всего наблюдается при сверлении длинных отверстий.
Увод сверла происходит:
1. При сверлении заготовок, у которых торцовые поверхности не перпендикулярны к оси;
2. При работе длинными сверлами;
3. При работе неправильно заточенными сверлами, у которых одна режущая кромка длиннее другой;
4. При сверлении металла, который имеет раковины или содержит твердые включения.
В целях предупреждения увода сверла необходимо обращать внимание на то, чтобы торцовая поверхность детали была чисто и точно обработана и была перпендикулярна к оси отверстия.
Увод сверла при работе длинными сверлами можно уменьшить предварительным надсверливанием отверстия коротким сверлом того же диаметра.
Увод сверла из-за неправильной заточки легко предупредить предварительной проверкой заточки шаблоном.
Если на пути сверла в материале детали встречаются раковины или твердые включения, то предотвратить увод сверла почти невозможно. Его можно только уменьшить путем уменьшения подачи, что в то же время явится средством предупреждения возможной поломки сверла.
Брак при центровании и меры его предупреждения.
Изготовление центровых отверстий в деталях должно быть качественным, так как от этого зависит правильное базирование деталей при их обработке в центрах.
Для того, чтобы предупредить брак при центровании, необходимо: обеспечить глубину, диаметры.
Конус под углом 60° должен быть чисто обработан, не иметь дробления или огранки.
Для того, чтобы избежать увода сверла при центровании, торцовые поверхности детали перед центрованием должны быть чисто обработаны и перпендикулярны к оси детали.
Рекомендации: в пояснительной записке указать возможные виды брака, причины и пути устранения при обработке детали.
Дата добавления: 2019-07-15; просмотров: 6259; Мы поможем в написании вашей работы! |
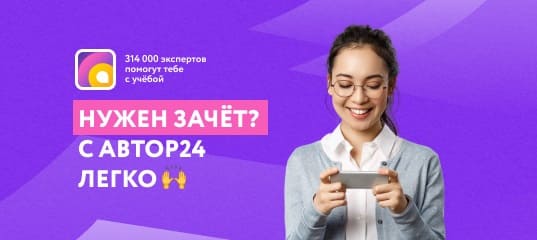
Мы поможем в написании ваших работ!