Разработка сборочного чертежа приспособления
1. Вычертить сборочный чертеж приспособления с необходимым количеством видов, разрезов, сечений. Формат и масштаб чертежа выбирает конструктор.
2. На сборочном чертеже проставить размеры: габаритные, присоединительные, установочные, посадочные и размеры, от точности которых зависит точность выдерживаемых технологических размеров детали.
3. Назначить технические требования и технические условия. К ним относятся: необходимость совместной обработки деталей приспособления в процессе сборки, точность взаимного расположения поверхностей и т.д.
Расчет приспособления на точность
Расчет проводится по методике [4].
Расчет приспособления на точность состоит в определении погрешности изготовления и сборки приспособления (E НП) и сравнении ее с допустимой погрешностью (ЕНПдоп). Приспособление обеспечивает заданную точность изготовления детали при соблюдении неравенства E НП < ЕНПдоп. При невыполнении условия необходимо уменьшить погрешность изготовлении приспособления за счет уменьшения допусков размеров деталей приспособления, изменения схемы базирования и т.д.
Последовательность расчета
1. Выявить размеры, на точность которых влияет приспособление.
2. Из этих размеров выбирается размер с минимальным допуском для расчета на точность.
3. Составляется схема для расчета допуска на изготовление приспособления.
4. Определяется допускаемая для проектируемой операции погрешность установки Едоп.
|
|
5. Определяется погрешность базирования Еб.
6. Определяется погрешность закрепления Ез.
7. Определяется допускаемая величина погрешности положения (приспособления) ЕПдоп.
8. Определяются составляющие допускаемой величины погрешности положения ЕПдоп.
9. Определяется допускаемая величина ЕНПдоп погрешности неточности изготовления и сборки приспособления.
10. Определяется величина ЕНП, реально существующая в приспособлении, и устанавливается с ЕНПдоп.
При определении точности приспособления необходимо учитывать метод обработки, тип приспособления, конструкцию инструмента. Например, обработка в кондукторе вызывает погрешность межцентровых расстояний обрабатываемых отверстий b и расстояния от установочной базы до оси обрабатываемого отверстия a. Точность диаметральных размеров d не зависит от точности приспособления и обеспечивается инструментом (рис. 1).
Рис. 1. Эскиз детали
Обработка во фрезерных приспособлениях вызывает неточность заданного размера из-за неточности положения установочных элементов приспособления относительно режущего инструмента ∆.
Рис. 2. Схема установки детали при фрезеровании
|
|
На размер в точность приспособления не влияет, т.к. этот размер обеспечивается инструментом. Размеры а и Δ зависят от настройки фрезы относительно приспособления (рис. 2).
Обработка в токарных приспособлениях влияет на взаимное положение обрабатываемой и установочной поверхностей и не влияет на погрешность формы и точность диаметральных размеров.
Пример расчета приспособления на точность
Для обработки отверстия диаметром 10Н8 (рис. 3) спроектирован кондуктор.
1. На операции выдерживаются три размера: Æ10Н8, 50+0,1, 15±0,1. Приспособление влияет только на точность размеров 50±0,1 и 15±0,1.
2. Допуски этих размеров одинаковы (0,2 мм), поэтому расчету подлежит размер 50+0,1 как наиболее точный.
3. Составляем схему для расчета допуска на изготовление приспособления (рис. 4).
Рис. 3. Операционный эскиз
4. Определяем допускаемую погрешность установки:
,
где δТ = 0,2 мм – допуск рассчитываемого размера;
– суммарная погрешность формы обрабатываемой поверхности, зависящая от геометрических погрешностей станка [1, табл. 35, с. 58].
для обработки в кондукторе, т.к. биение сверла гасится втулкой;
Δу – погрешность выполняемого размера, вызываемая упругими отжатиями элементов технологической системы под влиянием нестабильности сил резания.
|
|
,
где ky – коэффициент уточнения [1, том 2, с.181]; – ожидаемая погрешность припуска, находится по графу размерных цепей.
Рис. 4. Схема приспособления: 1 – палец ромбический; 2, 3 – опора; 4 – палец цилиндрический; 5 – втулка сменная; 6 – втулка постоянная
Принимаем ∆y=0, т.к. упругие обжатия происходят вдоль оси сверла и не влияют на полученный размер;
∆H – погрешность настройки станка и инструмента [1, табл. 36, с. 66].
∆H=0 для смены кондукторной втулки;
∆И – погрешность, вызываемая размерным износом режущего инструмента
[4, табл. 47, с. 76]. ∆И=0 принимаем из-за легкости смены инструмента;
∆T – погрешность, вызываемая тепловыми деформациями технологической системы. ∆T находится только для операции с жестким допуском на обработку (JТ5 - JТ7).
где К – коэффициент, учитывающий влияние тепловых деформаций технологической системы на суммарную погрешность: К=0,1–0,5 – для лезвийного инструмента, К=0,3–0,4 – для шлифования.
Принимаем ∆T=0, т.к. требования к точности невысоки.
.
5. Определяем погрешность базирования Еб [1, табл. 19, с. 31].
Принимаем Еб=0, т.к. совпадают установочная и измерительная базы. В данном случае не учтен зазор между отверстием заготовки и пальцем, он будет учтен в погрешности приспособления.
|
|
6. Определяем погрешность закрепления.
Ез выбирается по [1, табл. 22, с. 40]. Ез=0, т.к. направление усилия зажима Q перпендикулярно к рассчитываемому размеру.
7. Определяем допускаемую величину погрешности положения ЕПдоп:
,
где Е – погрешность установки. Вместо Е подставляем Едоп (пункт 4).
,
откуда .
.
8. Определяем составляющие допускаемой погрешности положения ЕПдоп,
кроме ЕНП
,
где Еизн – погрешность износа, возникающая в результате износа установочных элементов:
,
,
где – износ установочных элементов;
N – количество контактов заготовки с установочным элементом. N ≈ годовой программе выпуска;
– коэффициент, зависящий от вида применяемых установочных элементов:
– для опоры со сферической головкой,
– для призмы,
– для опорных пластин,
– для гладких установочных пальцев,
– для срезанных пальцев.
,
где – износ втулок [3, с. 564];
αвт – допуск на диаметр отверстия втулки, определяется из принятой посадки (F8 – для сверла, G7 – для развертки). При точности 6–7 квалитета и выше назначают Н8 – для сверла, G6 – для развертки;
К – коэффициент, зависящий от величины отклонения на размер от базы до оси обрабатываемого размера.
К= 1 – при отклонении до ±0,1; К= 2 – при отклонении от ± 0,1 до ±0,3.
=0 – при единичном производстве.
= 1 . 0,022=0,022 мм (рис. 4).
Еизн = 0,022 мм.
Еуст – погрешность установки на станке. Определяется исходя из зазора (рис. 5) между посадочным элементом станка (паз станка) и приспособления (шпонка), который рассчитывается как
Рис. 5. Схема возникновения погрешности установки
приспособления на станке
Еуст = 0 для сверлильных приспособлений, устанавливаемых на станок без шпонки.
Езаз – погрешность зазора, определяется исходя из посадки между установочным элементом и заготовкой. Рекомендуемые посадки при сверлении: H8/q5, H8/q6, Н8/Т7, H8/h9. Например, при установке приспособления на столе станка по посадке 12H8/f7 погрешность зазора составит:
.
Епер –погрешность перекоса или смещения инструмента, возникающая из-за неточности изготовления направляющих элементов приспособления (рис. 6).
При сверлении:
Рис. 6. Схема возникновения погрешности перекоса
9. Определяем допускаемую величину изготовления и сборки приспособления ЕНПдоп:
пункт 7 пункт 8
10. Определяем погрешность неточности изготовления и сборки
ЕНПрасч, реально получаемую при изготовлении приспособления:
,
где е i – эксцентриситет;
2е i – биение;
δ i – допуски размеров, составляющих размерную цепь, замыкающим звеном которой является рассчитываемый размер.
11. Проверяем выполнение условия E НПрасч E НПдоп.
Выявим размерную цепь. Для этого, начав от одной из поверхностей (оси), ограничивающей замыкающее звено, найдем составляющие звенья – размеры между базирующими поверхностями деталей или их осями, придем ко второй поверхности (оси), ограничивающей замыкающее звено.
Размерная цепь:
- ось отверстия втулки 5
- ось наружной поверхности втулки 5
- ось отверстия втулки 6
- ось наружной поверхности втулки 6
- ось отверстия корпуса под втулку 6
- ось отверстия корпуса под срезанный палец 1
- ось наружной поверхности (цилиндрической) срезанного пальца 1
- ось центрирующей (срезанной) поверхности пальца 1
- ось отверстия втулки 5.
e 1 –несоосность между осями отверстия и наружной поверхностью втулки 5 (зависит от точности изготовления втулки). е1 задается конструктором, принимаем е1 =0,01 мм.
е2 –несоосность между осями наружной поверхности втулки 5 и отверстия втулки 6 (если зазор – е2 =1/2 отSmax, если натяг – е2 = 0). Посадка H7/q6; H7/h6.
е3 –несоосность между осями отверстия и наружной поверхности втулки 6, аналогично е2.
е4 –несоосность между осями нижней поверхности втулки 6 и отверстием в корпусе, аналогично е2.
δ i – допуск на межцентровое расстояние между отверстием корпуса под втулку 6 и отверстием под палец 1. δi ≈ 1/2 δна размер в приспособлении (≈0,02 мм).
е5 –несоосность между осями отверстия корпуса под палец 1 и наружной поверхностью пальца 1, аналогично е2.
е6 –несоосность между осями наружной и центрирующей поверхностей пальца 1. е6 =0,01 мм.
.
Условие E НПрасч E НПдоп выполняется.
Дата добавления: 2019-07-17; просмотров: 175; Мы поможем в написании вашей работы! |
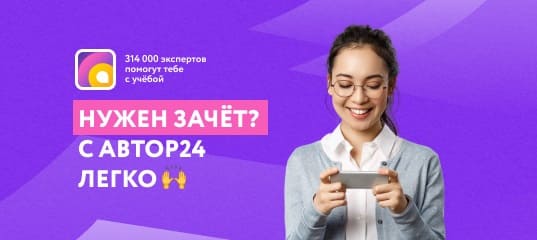
Мы поможем в написании ваших работ!