Комплексные показатели надежности.
Показателем, определяющим долговечность системы, объекта, машины, может служить коэффициент технического использования.
Коэффициент технического использования — отношение математического ожидания суммарного времени пребывания объекта в работоспособном состоянии за некоторый период эксплуатации к математическому ожиданию суммарного времени пребывания объекта в работоспособном состоянии и всех простоев для ремонта и технического обслуживания:
Коэффициент готовности — вероятность того, что объект окажется в работоспособном состоянии в произвольный момент времени, кроме планируемых периодов, в течение которых применение объекта по назначению не предусматривается.
Влияние надежности технологических систем на производительность
Производительность машин прямо-пропорциональна использованию их рабочего времени. А оно зависит от надежности машин, поддержание которой связано с простоями в текущем обслуживании и ремонте, что приводит к потерям рабочего времени. По мере увеличения наработки простои в ремонтах увеличиваются, а, следовательно, производительность уменьшается.
Простои зависят от частоты отказов, т.е. безотказности, и времени их устранения, т.е. ремонтопригодности.
Комплексными показателями, оценивающими эти свойства надежности, являются коэффициенты готовности (Кг) итехнического использования(Кти).
Коэффициент готовности(Кг) - это вероятность того, что объект окажется работоспособным в произвольный момент времени, кроме (планируемых) периодов, когда использование (объектов) по назначению не предусматривается.
|
|
Коэффициент технического использования — отношение математического ожидания суммарного времени пребывания объекта в работоспособном состоянии за некоторый период эксплуатации к математическому ожиданию суммарного времени пребывания объекта в работоспособном состоянии и всех простоев для ремонта и технического обслуживания:
Техническая диагностика тепловых, силовых и динамических повреждений деталей машин.
Основная задача технической диагностики - распознавание состояния системы в условиях ограниченной информации.
Информация поступает в виде показателей датчиков: вибраций, температур, давлений, путем визуальных осмотров и т.д.
Процедура диагностирования машины включает в себя три основных этапа:
1) первичное описание объекта -на основе экспериментальной информации, необходимой для принятия решения.
2) выделение признаков оценки состояния -
3) принятие решения (диагноз) - глубокое изучение свойств машины, целей и сути диагноза является основной предпосылкой эффективности диагностики.
|
|
При поиске признаков следует различать три аспекта технического состояния: структурный геометрией - конструктивных элементов (размерами и формой), взаимосвязями деталей (посадками, зазорами, углами и т.д.), состоянием материала (напряженностью, температурой, структурой), функциональный – (эксплуатационными показателями, статистическими и динамическими характеристиками протекания рабочего процесса и процессов регулирования) и вибрационный - вибрационные характеристики объекта.
На этапах проектирования, производства и эксплуатации требуется поставить диагноз неисправного элемента (детали) и установить причины неисправности. Для этого узел нужно представить в виде совокупности взаимосвязанных деталей. Получается трехступенчатая модель «изделие-узел-деталь» и соответственно три степени глубины диагноза.
Диагноз состояния узла можно установить различными методами диагностики. Так, состояние подшипника можно оценить по химическому составу масла, наличию в нем стружки, по температуре масла или температуре корпуса подшипника, по вибрации и т.д.
Виброзащита машин и механизмов
Динамические гасители колебаний.
|
|
Метод динамического гашения колебаний состоит в присоединении к объекту виброзащиты дополнительных устройств с целью изменения его вибрационного состояния. Работа динамических гасителей основана на формировании силовых воздействий, передаваемых на объект. Этим динамическое гашение отличается от другого способа уменьшения вибрации, характеризуемого наложением на объект дополнительных кинематических связей, например, закреплением отдельных его точек. Изменение вибрационного состояния объекта при присоединении динамического гасителя может осуществляться как путем перераспределения колебательной энергии от объекта к гасителю, так и в направлении увеличения рассеяния энергии колебаний. Первое реализуется изменением настройки системы объект–гаситель по отношению к частотам действующих вибрационных возмущений путем коррекции упругоинерционных свойств системы. В этом случае, присоединяемые к объекту устройства называют инерционными динамическими гасителями. Инерционные гасители применяют для подавления моногармонических или узкополосных случайных колебаний. При действии вибрационных нагрузок более широкого частотного диапазона предпочтительней оказывается второй способ, основанный на повышении диссипативных свойств системы путем присоединения к объекту дополнительных специально демпфируемых элементов. Динамические гасители диссипативного типа получили название поглотителей колебаний. Возможны и комбинированные способы динамического гашения, использующие одновременную коррекцию упругоинерционных и диссипативных свойств системы. В этом случае говорят о динамических гасителях с трением.
|
|
Динамическое гашение применимо для всех видов колебаний: продольных, изгибных, крутильных и т.д., при этом вид колебаний, осуществляемых присоединенным устройством, как правило, аналогичен виду подавляемых колебаний.
Дата добавления: 2019-07-15; просмотров: 495; Мы поможем в написании вашей работы! |
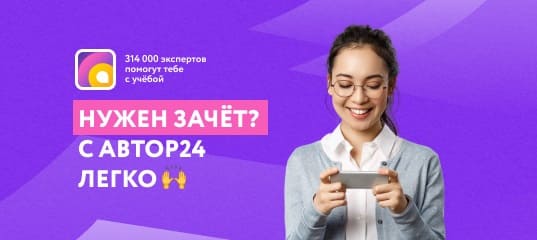
Мы поможем в написании ваших работ!