Что является главным в определении потребности создания новых машин?
При освоении производства новых моделей машин и оборудования решаются следующие задачи:
1) достижение объема выпуска в соответствии с проектной
мощностью предприятия;
2)обеспечение требуемого качества;
3)достижение рентабельности на всех стадиях производства.
При подготовке производства используют два подхода:
- с остановом производства;
- и без останова.
Наибольшее распространение получил второй подход. Он наиболее эффективен в том случае, когда новая модель машины относится к тому же конструктивному ряду, что и предшествующая.
Основой этого метода является постепенное последовательное освоение производства отдельных элементов машины, монтируемых по мере освоения на новую машину взамен старых элементов. Выпуск машин при этом не прекращается.
На продолжительность процесса освоения производства новой машины значительное влияние оказывает уровень отработки конструкторской документации данной машины (до 25...34% затрат на доработку чертежей в процессе освоения). Качественное изменение процесса проектирования достигается при использовании в качестве инструментария графических редакторов обеспечивающих 3D моделирование. В этом случае возможно проведение виртуальных контрольных сборок. В совокупности с численным моделированием, обеспечивающем проведение виртуальных исследований поведения машины при различных условиях нагружения (Пр. Fluid Sim), достигается проведение испытаний и исследования поведения машин без ее физической реализации.
|
|
Конструктивные и технологические особенности шпоночных соединений.
Общие сведения о шпоночном соединении.
Шпоночное соединение образуют вал, шпонка и ступица колеса (шкива, звездочки и др.). Шпонка – деталь, устанавливаемая в разъём двух соединяемых деталей и препятствующая их взаимному перемещению. Шпонка представляет собой стальной брус, устанавливаемый в пазы вала и ступицы. Она служит для передачи вращающего момента между валом и ступицей. Основные типы шпонок стандартизованы. Шпоночные пазы на валах получают фрезерованием дисковым или концевыми фрезами, в ступицах протягиванием.
Достоинства шпоночных соединений - простота конструкции и сравнительная легкость монтажа и демонтажа, вследствие чего их широко применяют во всех отраслях машиностроения.
Недостаток - шпоночные пазы ослабляют вал и ступицу насаживаемой на вал детали. Ослабление вала обусловлено не только уменьшением его сечения, но главное, значительной концентрацией напряжений изгиба и кручения, вызываемой шпоночным пазом. Шпоночное соединение трудоемко в изготовлении: при изготовлении паза концевой фрезой требуется ручная пригонка шпонки по пазу; при изготовлении паза дисковой фрезой крепление шпонки в пазу винтами (от возможных осевых смещений).
|
|
Различают два основных способа передачи крутящего момента – жесткий и фрикционный. При первом способе крутящий момент передается жесткими элементами, работающими на срез, изгиб или смятие; при втором – силами трения, возбуждаемыми на цилиндрических, конических или торцовых поверхностях вала.
Главные виды жестких соединений: шпоночные (рисунок 1) , шлицевые, призматические, профильные, штифтовые, фланцевые.
Рисунок 1 –Передача крутящего момента
К фрикционным относятся соединения: с натягом, конусные, с пружинными затяжными кольцами, клеммные.
Применяют также сочетание обоих способов. Нагружаемость жестких соединений увеличивают введением трения путем осевой или радиально-осевой затяжки.
Для страховки от провертывания, а также для фиксации деталей в определенном угловом положении в фрикционные соединения вводят жесткие элементы, например шпонки (рисунок 2).
Рисунок 2 – Передача крутящего момента
Дата добавления: 2019-07-15; просмотров: 231; Мы поможем в написании вашей работы! |
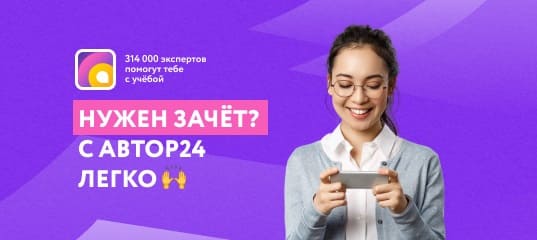
Мы поможем в написании ваших работ!