Гидропривод с замкнутой схемой циркуляции
в котором рабочая жидкость от гидродвигателя возвращается во всасывающую гидролинию насоса.
Гидропривод с замкнутой циркуляцией рабочей жидкости компактен, имеет небольшую массу и допускает большую частоту вращения ротора насоса без опасности возникновения кавитации, поскольку в такой системе во всасывающей линии давление всегда превышает атмосферное. К недостаткам следует отнести плохие условия для охлаждения рабочей жидкости, а также необходимость спускать из гидросистемы рабочую жидкость при замене или ремонте гидроаппаратуры;
1. Материалы несущих элементов металлических конструкций различных видов кранов. Выбор и обоснование марки материала.
1.1. Настоящие нормы следует соблюдать при проектировании стальных строительных конструкций зданий и сооружений различного назначения.
Нормы не распространяются на проектирование стальных конструкций мостов, транспортных тоннелей и труб под насыпями.
При проектировании стальных конструкций, находящихся в особых условиях эксплуатации (например, конструкций доменных печей, магистральных и технологических трубопроводов, резервуаров специального назначения, конструкций зданий, подвергающихся сейсмическим, интенсивным температурным воздействиям или воздействиям агрессивных сред, конструкций морских гидротехнических сооружений), конструкций уникальных зданий и сооружений, а также специальных видов конструкций (например, предварительно напряженных, пространственных, висячих) следует соблюдать дополнительные требования, отражающие особенности работы этих конструкций, предусмотренные соответствующими нормативными документами, утвержденными или согласованными Госстроем СССР.
|
|
1.2. При проектировании стальных конструкций следует соблюдать нормы СНиП по защите строительных конструкций от коррозии и противопожарные нормы проектирования зданий и сооружений. Увеличение толщины проката и стенок труб с целью защиты конструкций от коррозии и повышения предела огнестойкости конструкций не допускается.
Все конструкции должны быть доступны для наблюдения, очистки, окраски, а также не должны задерживать влагу и затруднять проветривание. Замкнутые профили должны быть герметизированы.
1.3*. При проектировании стельных конструкций следует:
выбирать оптимальные в технико-экономическом отношении схемы сооружений и сечения элементов;
применять экономичные профили проката и эффективные стали;
применять для зданий и сооружений, как правило, унифицированные типовые или стандартные конструкции;
применять прогрессивные конструкции (пространственные системы из стандартных элементов; конструкции, совмещающие несущие и ограждающие функции; предварительно напряженные, вантовые, тонколистовые и комбинированные конструкции из разных сталей);
|
|
предусматривать технологичность изготовления и монтажа конструкций;
применять конструкции, обеспечивающие наименьшую трудоемкость их изготовления, транспортирования и монтажа;
предусматривать, как правило, поточное изготовление конструкций и их конвейерный или крупноблочный монтаж;
предусматривать применение заводских соединений прогрессивных типов (автоматической и полуавтоматической сварки, соединений фланцевых, с фрезерованными торцами, на болтах, в том числе на высокопрочных и др.);
предусматривать, как правило, монтажные соединения на болтах, в том числе на высокопрочных; сварные монтажные соединения допускаются при соответствующем обосновании;
выполнять требования государственных стандартов на конструкции соответствующего вида.
1.4. При проектировании зданий и сооружений необходимо принимать конструктивные схемы, обеспечивающие прочность, устойчивость и пространственную неизменяемость зданий и сооружений в целом, а также их отдельных элементов при транспортировании, монтаже и эксплуатации.
|
|
1.5*. Стали и материалы соединений, ограничения по применению сталей С345Т и С375Т, а также дополнительные требования к поставляемой стали, предусмотренные государственными стандартами и стандартами СЭВ или техническими условиями, следует указывать в рабочих (КМ) и деталировочных (КМД) чертежах стальных конструкций и в документации на заказ материалов.
В зависимости от особенностей конструкций и их узлов необходимо при заказе стали указывать класс сплошности по ГОСТ 27772-88.
1.6*. Стальные конструкции и их расчет должны удовлетворять требованиям ГОСТ 27751-88 «Надежность строительных конструкций и оснований. Основные положения по расчету» и СТ СЭВ 3972-83 «Надежность строительных конструкций и оснований. Конструкции стальные. Основные положения по расчету».
1.7. Расчетные схемы и основные предпосылки расчета должны отражать действительные условия работы стальных конструкций.
Внесены
ЦНИИСК им. Кучеренко
Госстроя СССР
Утверждены
Постановлением Госстроя СССР
от 14 августа 1981 г. № 144
Срок введения
|
|
в действие
1 января 1982 г.
Стальные конструкции следует, как правило, рассчитывать как единые пространственные системы.
При разделении единых пространственных систем на отдельные плоские конструкции следует учитывать взаимодействие элементов между собой и с основанием.
Выбор расчетных схем, а также методов расчета стальных конструкций необходимо производить с учетом эффективного использования ЭВМ.
1.8. Расчет стальных конструкций следует, как правило, выполнять с учетом неупругих деформаций стали.
Для статически неопределимых конструкций, методика расчета которых с учетом неупругих деформаций стали не разработана, расчетные усилия (изгибающие и крутящие моменты, продольные и поперечные силы) следует определять в предположении упругих деформаций стали по недеформированной схеме.
При соответствующем технико-экономическом обосновании расчет допускается производить по деформированной схеме, учитывающей влияние перемещений конструкций под нагрузкой.
1.9. Элементы стальных конструкций должны иметь минимальные сечения, удовлетворяющие требованиям настоящих норм с учетом сортамента на прокат и трубы. В составных сечениях, устанавливаемых расчетом, недонапряжение не должно превышать 5 %.
1. Материалы вспомогательных элементов металлических конструкций различных видов кранов. Выбор и обоснование.
Усло в н ые о бо з на че ния
А - площадь поперечного сечения элемента конструкции;
Jx, Jy Wx, - моменты инерции сечения относительно главных осей;
Wy - моменты сопротивления сечения;
ix, iy - радиусы инерции;
h - высота сечения;
b - ширина сечения;
t - толщина элемента;
М,N - изгибающий момент и продольная сила;
Q - поперечная сила;
Ry - расчетное сопротивление стали растяжению, сжатию и изгибу по пределу
текучести;
Rs - расчетное сопротивление стали срезу ( Rs = 0.58 • R y );
a - нормальное напряжение;
т - касательное напряжение;
E - модуль упругости (для стали Е=2,06105 МПа);
- длина, пролет элемента (стержня, балки);
eФ - расчетная длина стержня (расчетный пролет балки);
Ус - коэффициент продольного изгиба; -
л коэффициент условий работы;
- гибкость стержня ( X = ee f /i);
- объемная масса (плотность) материала.
1. Балки. Выбор основных размеров. Расчет балок открытого и закрытого (коробчатого) сечения по методу предельных соотношений и методу допустимых напряжений.
Расчет балок на чистый изгиб по предельному состоянию. Поставив требование, чтобы наибольшие напряжения не превосходили допускаемых, мы обеспечиваем гарантию того, что эти напряжения не достигнут для балок из хрупких материалов временного сопротивления, а для балок из пластичных материалов — предела текучести. Иными словами, при таком расчете за предельное состояние балок из хрупкого материала принимается состояние по рис. 97, а, а для балок из пластичного материала — по рис. 97, б (при одинаковом Ст для растяжения и сжатия). Представленное на рис. 97, а состояние балки из хрупкого материала можно действительно считать предельным, так как при нем начинается разрушение балки. Что касается состояния, представленного на рис. 97, б, то рассматривать его как предельное можно лишь условно, в том смысле, что в этом состоянии в балке начинают развиваться пластические дефор.мации. Однако это обстоятельство не может ни повлечь за собой значительного увеличения прогибов, ни отразиться на грузоподъемности балки, так как в этом состоянии пластически деформируются лишь крайние волокна балки, все же остальные испытывают упругие деформации. При дальнейшем увеличении изгибающих моментов крайние волокна, правда, деформируются без существенного увеличения напряжений, зато в остальных напряжения могут увеличиваться по крайней мере до От- В результате начинают пластически деформироваться волокна, ближайшие к крайним, затем ближайшие к названным и т. д. Таким образом, пренебрегая возможностью незначительного роста напряжений после достижения величины От, можно представить последовательное изменение напряженного состояния эпюрами, изображенными на рис. 98 пунктиром. Иными словами, пластическая деформация, начавшись у поверхности балки, при дальнейшем росте изгибающих моментов постепенно распространяется вглубь. [c.174]
Расчет балок на изгиб с поперечной силой по предельному состоянию. Выше мы видели, что при чистом изгибе расчет по допускаемому напряжению не дает возможности использовать полностью способность балки сопротивляться действию внешних сил с гарантией, что не будет происходить быстрого возрастания прогибов. Эту возможность мы получили, выполнив расчет по предельному состоянию, которому соответствовала эпюра напряжений, представленная на рис. 99. При изгибе с поперечной силой такая эпюра напряжений оказывается недопустимой. Применяя, например, четвертую теорию прочности, мы установим, что в точках сечения балки, в которых имеет место пластическая деформация, должно соблюдаться условие пластичности [c.190]
Для каркасов котлоагрегатов имеем один и тот же коэффициент перегрузки (/г =1,1), одинаковый коэффициент однородности стали (. = 0,85-г-0,9) и общий для балок и колонн коэффициент условий работы т). Величина коэффициента может быть так подобрана, что оба метода расчета (по допускаемому напряжению и по предельному состоянию) будут давать одни и те же результаты. Расчет каркасов котлоагрегатов будем вести по допускаемым напряжениям, как это принято в Нормах расчета элементов паровых котлов на прочность . Для справок приведены расчетные формулы по предельному состоянию в приложении 6. В этих формулах величина / представляет собой расчетное сопротивление стали [c.14]
Расчет балок на поперечный изгиб по предельным состояниям. [c.248]
Рельсы подвесных дорог работают в сложных условиях местных и общих напряженных состояний. Их расчет на прочность рекомендуется выполнять по методу допускаемых напряжений. Если исходить из принятых значений коэффициентов перегрузки, однородности материала и условий работы, принимаемых в расчетах по предельному состоянию, то коэффициент запаса при определении допускаемых напряжений по отношению к нижнему значению предела текучести для сталей класса С38/23 можно принять равным 1,35, для сталей более высокого класса прочности 1,45 и для алюминия 1,6 для расчета на выносливость — 1,25. Значения допускаемых напряжений для расчета рельсов и рельсов-балок подвесных путей на прочность при действии основных нагрузок для разных марок стали приведены в табл. 3.1. [c.37]
При расчете многопролетных неразрезных балок предельные состояния устанавливаются для каждого пролета в отдельности. Построив эпюры моментов, соответствующие предельному состоянию каждого пролета, находят расчетные моменты. По этим моментам подбирается сечение в каждом пролете. [c.563]
При расчете изгибаемых элементов конструкций на прочность используются методы, рассмотренные в 3.7. При расчете строительных конструкций применяется метод расчета по первой группе предельных состояний в машиностроении — метод допускаемых напряжений. В подавляющем большинстве случаев решающее значение на прочность элементов конструкций оказывают нормальные напряжения, действующие в крайних волокнах балок и лишь в некоторых случаях касательные напряжения, а также главные напряжения в наклонных сечениях. Во всех случаях наибольшие напряжения, возникающие в балке, не должны превышать некоторой допустимой для данного материала величины. При расчете по первой группе предельных состояний эта величина принимается равной расчетному сопротивлению R, умноженному на коэффициент условий работы при расчете по методу допускаемых напряжений — допускаемому напряжению [а]. В первом случае условие прочности записывается в виде [c.150]
Расчетные нагрузки для мостов мостовых кранов при расчете по методу предельных состояний см. в табл. 1.5.8, 1.5.9 и 1.5.10, а при расчете по методу допускаемых напряжений — в табл. 1.5.16. При этом комбинации нагрузок 1Ь и ПЬ при движении моста служат для расчета пролетных и концевых балок, а при движении тележки — для расчета концевых балок, [c.430]
Расчет балок на изгиб с поперечной силой по несущей способности и по расчетному предельному состоянию [c.197]
При расчете статически неопределимых балок по несущей способности и по расчетным предельным состояниям строительными нормами и правилами допускается определять изгибающие моменты по упругой стадии работы. Однако для балок, обладающих малой деформа- а) тивностью при работе в упруго-пластической стадии, определение усилий по упругому методу расчета приводит к неоправданному перерасходу материала. Для таких балок, не-сущих статическую нагрузку, нормами предписывается изгибающие моменты определять с учетом выравнивания моментов на опорах и в пролете в процессе развития пластических деформаций. [c.297]
Расчет балок производят по двум предельным состояниям несущей способности и прогибам. Расчет прокатных балок, выполненных из прокатных или гнутых двутавров, швеллеров и других профилей, сводится к определению необходимого номера профиля по сортаменту и проверке его на прочность, жесткость и устойчивость. [c.62]
Уравнения равновесия составляются в предположении малости перемещении. В действительности образование пластического шарнира связано с бесконечно большим местным пзменепием кривизны. Таким образом, в расчете по предельным нагрузкам содержится логическое несоответствие. Однако, несмотря на это, расчет рам и балок по предельному состоянию оказывается в ряде случаев весьма тглодотворным, так как позволяет избежать сложрюго анализа внутренних закономерностей и быстро приводит I. цели. [c.46]
При упругом расчете балок за предельное состояние принимают такое, при котором в крайних волокнах наибЬлее напряженного сечения напряжения достигают предела упругости. Рассмотрим дальнейшую работу статически неопределимой балки при увеличении нагрузки. Будем считать, что материал балки следует идеальной диаграмме Прандтля и работает одинаково как на растяжение, так и на сжатие. Сущность расчета поясним на примере балки, заделанной по концам и нагруженной равномерно распределенной нагрузкой (рис. 11.49, о). При постепенном возрастании нагрузки сначала балка работает в упругой стадии, причем эпюра изгибающих моментов имеет вид параболы (рис. 11.49,6). При дальнейшем возрастании нагрузки настанет такой момент, когда [c.376]
Из этой эормулы следует, что эффект выигрыша в несущей способности при переходе от допускаемых напряжений к предельным состояниям для двутавровых балок значительно меньше, чем для балок сплошного сечения. Однако, как будет ясно из последующего (см. 12.9), и для двутавровых сечений переход к расчету по предельным состояниям весьма эффективен, если рассматривается статически неопределимая балка. [c.275]
Советский ученый А. А. Гвоздев распространил расчет балок исходя из модели жесткопластического материала на изгиб иластинок. В качестве предельного пластического состояния для любого сечения пластинки он принял возникновение цилиндрического пластического шарнира, в котором образуется двугранный угол любой величины при постоянном предельном значении изгибающего момента. Упругие деформации пластинки в соответствии с моделью жесткопластического материала считаются малыми по сравнению с пластическими. А сани пластические деформации принимаются малыми по сравнению с толщиной пластинки, что позволяет применять линейную теорию изгиба пластинок, [c.243]
Если определение предельных состояний грунтовых массивов можно отнести к обобщенной теории пластичности, то расчет конструкций на упругом основании можно считать разделом теории упругости. При этом основание рассматривалось или как упругое тело, или моделировалось при помощи гипотезы коэффициента постели Винклера — Фусса. При расчете плит и балок на такой упрощенной модели упругого основания использовался, как правило, тот же аппарат, что и для конструкций, опертых по точкам и линиям. С целью уточнения расчета в 30-х годах предлагался ряд уточнений теории Винклера — Фусса, связанных, например, с введением двух коэффициентов постели, однако в дальнейшем предпочтение было отдано расчету конструкций на подстилающем слое конечной толщины. [c.275]
Согласно СНиПу, расчет стальных балок, закрепленных от потери устойчивости, ведется по пластическому моменту сопротивления W J lЛ2W, и, таким образом, при расчете по первому предельному состоянию условие обеспечения несущей способности выражается формулой [c.242]
Несущая способность балок в общем случае изгиба при расчете их по мето,ду расчетных предельных состояний обычно определяется по тем же формулам, что и при чистом изгибе. Касательные напряжения при этом могут вычисляться по методу, изложенному выше. [c.200]
В связи с тем, что принимаемые при расчетах на выносливость по методу предельных состояний расчетные нагрузки и коэффициенты условий работы окончательно не установлены, проверочный расчет главных балок на выносливость и прочность производят по методу допускаемых напряжений. При этом в случае расчета на вертикальные и горизонтальные нагрузки суммарное нормальное напряжение Отах в угловой Т0ЧК6 сечения балки определяется в виде суммы нормальных напряжений от действия изгибающих моментов И inax- ФормуЛЫ ДЛЯ ОПреДеЛбНИЯ уСЛОВИЙ ВЫНОСЛИВОСТИ [c.236]
1. Работа металлических конструкций при переменных напряжениях. Вычисление концентраторов напряжений и ассиметрия цикла нагружения на сопротивление усталости.
5.1.1 Расчеты бетонных и железобетонных конструкций следует производить в соответствии с требованиями ГОСТ 27751 по предельным состояниям, включающим:
предельные состояния первой группы, приводящие к полной непригодности эксплуатации конструкций;
предельные состояния второй группы, затрудняющие нормальную эксплуатацию конструкций или уменьшающие долговечность зданий и сооружений по сравнению с предусматриваемым сроком службы.
Расчеты должны обеспечивать надежность зданий или сооружений в течение всего срока их службы, а также при производстве работ в соответствии с требованиями, предъявляемыми к ним.
Расчеты по предельным состояниям первой группы включают:
расчет по прочности;
расчет по устойчивости формы (для тонкостенных конструкций);
расчет по устойчивости положения (опрокидывание, скольжение, всплывание).
Расчеты по прочности бетонных и железобетонных конструкций следует производить из условия, по которому усилия, напряжения и деформации в конструкциях от различных воздействий с учетом начального напряженного состояния (преднапряжение, температурные и другие воздействия) не должны превышать соответствующих значений, установленных нормативными документами.
Расчеты по устойчивости формы конструкции, а также по устойчивости положения (с учетом совместной работы конструкции и основания, их деформационных свойств, сопротивления сдвигу по контакту с основанием и других особенностей) следует производить согласно указаниям нормативных документов на отдельные виды конструкций.
В необходимых случаях в зависимости от вида и назначения конструкции должны быть произведены расчеты по предельным состояниям, связанным с явлениями, при которых возникает необходимость прекращения эксплуатации здания и сооружения (чрезмерные деформации, сдвиги в соединениях и другие явления).
Расчеты по предельным состояниям второй группы включают:
расчет по образованию трещин;
расчет по раскрытию трещин;
расчет по деформациям.
Расчет бетонных и железобетонных конструкций по образованию трещин следует производить из условия, по которому усилия, напряжения или деформации в конструкциях от различных воздействий не должны превышать соответствующих их предельных значений, воспринимаемых конструкцией при образовании трещин.
Расчет железобетонных конструкций по раскрытию трещин производят из условия, по которому ширина раскрытия трещин в конструкции от различных воздействий не должна превышать предельно допустимых значений, устанавливаемых в зависимости от требований, предъявляемых к конструкции, условий ее эксплуатации, воздействия окружающей среды и характеристик материалов с учетом особенностей коррозионного поведения арматуры.
Расчет бетонных и железобетонных конструкций по деформациям следует производить из условия, по которому прогибы, углы поворота, перемещения и амплитуды колебания конструкций от различных воздействий не должны превышать соответствующих предельно допустимых значений.
Для конструкций, в которых не допускается образование трещин, должны быть обеспечены требования по отсутствию трещин. В этом случае расчет по раскрытию трещин не производят.
Для остальных конструкций, в которых допускается образование трещин, расчет по образованию трещин производят для определения необходимости расчета по раскрытию трещин и учета трещин при расчете по деформациям.
5.1.2 Расчет бетонных и железобетонных конструкций (линейных, плоскостных, пространственных, массивных) по предельным состояниям первой и второй групп производят по напряжениям, усилиям, деформациям и перемещениям, вычисленным от внешних воздействий в конструкциях и образуемых ими системах зданий и сооружений с учетом физической нелинейности (неупругих деформаций бетона и арматуры), возможного образования трещин и в необходимых случаях - анизотропии, накопления повреждений и геометрической нелинейности (влияние деформаций на изменение усилий в конструкциях).
Физическую нелинейность и анизотропию следует учитывать в определяющих соотношениях, связывающих между собой напряжения и деформации (или усилия и перемещения), а также в условиях прочности и трещиностойкости материала.
В статически неопределимых конструкциях следует учитывать перераспределение усилий в элементах системы вследствие образования трещин и развития неупругих деформаций в бетоне и арматуре вплоть до возникновения предельного состояния в элементе. При отсутствии методов расчета, учитывающих неупругие свойства железобетона, а также для предварительных расчетов с учетом неупругих свойств железобетона усилия и напряжения в статически неопределимых конструкциях и системах допускается определять в предположении упругой работы железобетонных элементов. При этом влияние физической нелинейности рекомендуется учитывать путем корректировки результатов линейного расчета на основе данных экспериментальных исследований, нелинейного моделирования, результатов расчета аналогичных объектов и экспертных оценок.
При расчете конструкций по прочности, деформациям, образованию и раскрытию трещин на основе метода конечных элементов должны быть проверены условия прочности и трещиностойкости для всех конечных элементов, составляющих конструкцию, а также условия возникновения чрезмерных перемещений конструкции. При оценке предельного состояния по прочности допускается полагать отдельные конечные элементы разрушенными, если это не влечет за собой прогрессирующего разрушения здания или сооружения, и по истечении действия рассматриваемой нагрузки эксплуатационная пригодность здания или сооружения сохраняется или может быть восстановлена.
Определение предельных усилий и деформаций в бетонных и железобетонных конструкциях следует производить на основе расчетных схем (моделей), наиболее близко отвечающих реальному физическому характеру работы конструкций и материалов в рассматриваемом предельном состоянии.
Несущую способность железобетонных конструкций, способных претерпевать достаточные пластические деформации (в частности, при использовании арматуры с физическим пределом текучести), допускается определять методом предельного равновесия.
5.1.3 При расчетах бетонных и железобетонных конструкций по предельным состояниям следует рассматривать различные расчетные ситуации в соответствии с ГОСТ 27751, в том числе стадии изготовления, транспортирования, возведения, эксплуатации, аварийные ситуации, а также пожар.
(Измененная редакция, Изм. N 2).
5.1.4 Расчеты бетонных и железобетонных конструкций следует производить на все виды нагрузок, отвечающих функциональному назначению зданий и сооружений, с учетом влияния окружающей среды (климатических воздействий и воды - для конструкций, окруженных водой), а в необходимых случаях - с учетом воздействия пожара, технологических температурных и влажностных воздействий и воздействий агрессивных химических сред.
5.1.5 Расчеты бетонных и железобетонных конструкций производят на действие изгибающих моментов, продольных сил, поперечных сил и крутящих моментов, а также на местное действие нагрузки.
5.1.6 При расчете элементов сборных конструкций на воздействие усилий, возникающих при их подъеме, транспортировании и монтаже, нагрузку от массы элементов следует принимать с коэффициентом динамичности, равным:
1,60 - при транспортировании,
1,40 - при подъеме и монтаже.
Допускается принимать более низкие, обоснованные в установленном порядке, значения коэффициентов динамичности, но не ниже 1,25.
5.1.7 При расчетах бетонных и железобетонных конструкций следует учитывать особенности свойств различных видов бетона и арматуры, влияния на них характера нагрузки и окружающей среды, способов армирования, совместность работы арматуры и бетона (при наличии и отсутствии сцепления арматуры с бетоном), технологию изготовления конструктивных типов железобетонных элементов зданий и сооружений.
5.1.8 Расчет предварительно напряженных конструкций следует производить с учетом начальных (предварительных) напряжений и деформаций в арматуре и бетоне, потерь предварительного напряжения и особенностей передачи предварительного напряжения на бетон.
5.1.9 В монолитных конструкциях должна быть обеспечена прочность конструкции с учетом рабочих швов бетонирования.
5.1.10 При расчете сборных конструкций должна быть обеспечена прочность узловых и стыковых сопряжений сборных элементов, осуществленныхСП 63.13330.2012 Бетонные и железобетонные конструкции. Основные положения. Актуализированная редакция СНиП 52-01-2003 (с Изменениями N 1, 2, 3) путем соединения стальных закладных деталей, выпусков арматуры и замоноличивания бетоном.
1. Стреловые краны. Типы стрел. Расчетные нагрузки и их комбинации. Особенности расчета (стрела с прямой осью и с изогнутой осью).
К кранам стрелового типа относят:
Стреловой самоходный кран — кран стрелового типа со стрелой, закреплённой на раме платформы или ходового устройства[3].
Башенный кран — кран стрелового типа поворотный, со стрелой, закреплённой в верхней части вертикально расположенной башни[3].
Деррик-кран — кран стрелового типа поворотный, имеющий вертикальную мачту и стрелу, закреплённую шарнирно на мачте, имеющей нижнюю и верхнюю опоры[3].
Портальный кран — кран стрелового типа поворотный, передвижной, на портале, предназначенном для пропуска автомобильного или железнодорожного транспорта[3].
Полупортальный кран — кран стрелового типа поворотный, передвижной, на полупортале[3].
Судовой кран — кран стрелового типа, поворотный, стационарный, установленный на борту судна и предназначенный для его загрузки и разгрузки[3].
Монтажная стрела — кран стрелового типа, неповоротный, стационарный, монтируемый непосредственно у места производства работ[3].
Стреловые самоходные краны
Стреловым краном грузят танк КВ
Стреловые краны подразделяют на несколько групп, самая распространённая из которых — группа самоходных (передвижных) кранов[4], в зависимости от условий эксплуатации оборудуемых различными ходовыми устройствами[2].
Для независимого перемещения по местности они оснащены специальным ходовым устройством. Стреловое оборудование этих кранов — сменное. Всё это позволяет быстро изменять параметры и использовать их при выполнении широкого круга задач[4].
Стреловые краны относятся к группе универсальных кранов, предназначенных для подачи строительных конструкций и материалов на строящиеся объекты, а также для механизации погрузочно-разгрузочных работ на складах. В процессе монтажных работ их используют для поддержания конструкций при их закреплении на месте монтажа[5].
Кроме того, они широко применяются:
На строительстве мостов: при погрузочно-разгрузочных, монтажных работах с различными конструкциями[6].
В энергетическом строительстве: в зависимости от мощности электростанции краны могут выполнять функции основного монтажного механизма (на объектах малой мощности), либо вспомогательного (на объектах средней и большой мощности) при монтаже основного энергетического оборудования. При монтаже вспомогательных объектов (химводоочистка, эстакады трубопроводов и пр.) самоходные краны становятся главным монтажным механизмом[7].
Достоинства и недостатки
Основное достоинство — способность быстро перебазироваться с одного объекта на другой, а затем сразу по прибытии на новое место начать работу. Благодаря этому краны успешно используются на рассредоточенных объектах с небольшим объёмом работ[5].
Главный недостаток — передвижение с грузом допускается со значительными ограничениями[5].
Классификация стреловых кранов
Самоходные стреловые краны
…на автомобильном шасси…
…На гусеничных тележках…
…на специальном шасси автомобильного типа
Стреловые самоходные краны классифицируют по следующим характеристикам: грузоподъёмности, конструкции ходовой части, типу привода, типу рабочего (стрелового) оборудования[2], а также по исполнению подвески стрелового оборудования[4].
Конструкция ходовой части
По конструкции ходовой части (шасси), стреловые краны подразделяются на следующие виды:
Автомобильный[2][6] — кран стрелового типа на шасси автомобиля[3].
Гусеничный[2][6] — кран на гусеничных тележках[3].
Железнодорожный[6] — кран стреловой, на платформе, передвигающийся по железнодорожному пути[3].
Кран на шасси автомобильного типа[6] — кран стрелового типа на ходовом устройстве типа автомобильного шасси[3].
Плавучий — кран на плавучих средствах[3].
Пневмоколёсный[2][6] — кран стрелового типа на пневмоколёсном шасси, управляемый из кабины, установленной на поворотной части крана[3].
Рельсовый[2] — кран на рельсовом ходовом устройстве[3]: краны типа «СКР».
Тракторный[8] — кран стреловой на шасси трактора[3].
Привод стреловых кранов
Типы стрел
Стреловое оборудование…
…Башенно-стреловое исполнение крана…
…стрела одноковшового экскаватора…
В стреловых самоходных кранах используют:
Механический привод. При использовании группового механического привода все механизмы крана получают движение от дизеля или другого двигателя внутреннего сгорания[2].
Электрический привод. В случае использования электрического многодвигательного привода, каждый механизм имеет индивидуальный электродвигатель[2].
Гидравлический привод. При использовании гидропривода каждый механизм оснащается индивидуальным гидродвигателем[2].
Смешанный привод[2].
По типу привода механизмов самоходные стреловые краны делятся на две группы:
Одномоторный привод: все рабочие механизмы приводятся в движение одним или несколькими двигателями, работающими на один вал. Одномоторный привод может быть механическим, либо комбинированным[4].
Многомоторный или индивидуальный привод, когда каждый механизм получает движение от отдельного двигателя[4].
Тип стрелового оборудования
В стреловых кранах применяются:
Стреловое оборудование — оборудование крана, состоящее из рабочей (наклонной) стрелы, поддерживающих её элементов и крюковой подвески[9]. Оборудование стрелового крана представляет собой наклонную стрелу, которая установлена на поворотной раме крана[2].
Башенно-стреловое оборудование (сокр. БСО, исполнение крана в этом случае БСИ) — сменное оборудование стрелового самоходного крана с механическим приводом, состоящее из вертикальной или наклонно установленной башни (мачты), стрелы с гуськом (или без него) и необходимых устройств[9]. Мачта оборудования монтируется на поворотной раме крана и конструктивно представляет собой пространственную ферму, в верхней части которой на шарнирах крепится стрела с изменяющимся углом наклона, называемая управляемым гуськом[2]. Кран с установленным оборудованием этого типа позволяет получить наибольшее свободное пространство под стрелой, называемое полезным подстреловым пространством[2].
Крановое оборудование одноковшового экскаватора — решётчатая стрела, установленная на одноковшовый экскаватор[6]. В этом случае экскаватор используется в качестве стрелового крана. Грузоподъёмность кранового оборудования для экскаваторов с ковшами ёмкостью 0,4 м³; 0,65 м³; 1 м³ и 1,65 м³ составляет: 6,3 т; 10 т; 16 т и 25 т[6].
Конструкция стрелового оборудования
По конструкции подразделяется на два основных типа:
Стрелы решётчатой конструкции[6]. Подвешиваются на гибкой подвеске при помощи системы канатов[4] — от стрелового полиспаста[8]. Стрелы, изменяемые по длине, оснащаются специальными вставками, устанавливаемыми в среднюю часть стрелы[6].
По конструкции, в свою очередь, решётчатые стрелы подразделяются на четыре подвида:
Прямые решётчатые стрелы. Применяются на кранах, которые предназначены для выполнения разнообразных работ. При этом возникают ситуации, когда при малых вылетах стрелы при наибольшей грузоподъёмности крана пространства под стрелой перестаёт хватать для подъёма крупногабаритных грузов[2].
Непрямолинейные стрелы. Стрела подвешивается на стреловом полиспасте в зоне перегиба стрелы. Применяются для увеличения пространства под стрелой. В таких случаях размеры поднимаемого груза могут быть очень большими, однако стрела при этом испытывает значительный изгибающий момент, а также при повороте крана — значительный крутящий момент[2].
Наращиваемые стрелы. Стрелу кранов, имеющих значительную грузоподъёмность, выполняют из нескольких секций-вставок, что позволяет применять стрелы большой длины[2].
Шарнирно-сочленённые стрелы. Представляют собой стреловое устройство, состоящее из основной стрелы и шарнирно закреплённого на ней гуська. Гусёк позволяет значительно увеличить вылет стрелы при существенном пространстве под стрелой крана, однако при этом снижается грузоподъёмность. Гусёк в этом случае является неуправляемым, так как угол наклона во время работы крана остаётся постоянным[2].
Подвески стрелы
Гибкая с системой канатов…
…жёсткая с гидроцилиндром…
Стрелы телескопической конструкции[6]. На кранах с гидравлическим приводом является основным оборудованием[4]. Представляет собой сплошностенчатую (коробчатую) телескопическую стрелу балочного типа[6], подвешиваемую на жёсткой подвеске. Стрела при этом удерживается гидроцилиндрами[8], с помощью которых меняется её угол наклона[4]. Стрелы этого типа изменяют свою длину с помощью телескопических элементов (от трёх и более). Эта операция по изменению длины стрелы, называемая телескопированием, может производиться в процессе работы с крюком, в том числе с грузом[6]. В качестве грузозахватного приспособления на телескопических стрелах устанавливается крюковая подвеска. При грузоподъёмности до 10 т (включительно), на кран устанавливается двухсекционная телескопическая стрела, а при грузоподъёмности более 10 т — трёх-, четырёхсекционные и т. д[4].
Изменяемость длины стрелы
Длина стрелы может оставаться постоянной или изменяемой, при использовании специальных выдвижных устройств[2]. По этому признаку стреловые устройства разделяют на:
Выдвижные устройства — стрелы, имеющие одну или несколько выдвижных секций для изменения длины[2].
Невыдвижные устройства — решётчатые стрелы, секции которых жёстко соединены одна с другой[2].
Подвеска стрелового оборудования
В зависимости от используемого стрелового оборудования, различают два типа подвесок:
Гибкая стреловая подвеска — с применением полиспаста и системы канатов[4].
Жёсткая подвеска — с использованием гидравлических цилиндров, при помощи которых обеспечивается удержание стрелы и смена угла её наклона. Используется в телескопических стрелах[4].
Параметры
Параметрами называются основные величины, характеризующие кран[3]. Основными параметрами стреловых кранов являются:
Грузоподъёмность — масса наибольшего рабочего груза, на подъём которого он рассчитан. В величину грузоподъёмности включается масса съёмных грузозахватных приспособлений и тары: у машин, которые оснащены грейфером или электромагнитом, масса этих грузозахватных органов. Этот параметр является общим для всех типов кранов[3]. Грузоподъёмность зависит от вылета стрелы с учётом устойчивости крана от опрокидывания и прочности его элементов[2].
Высотные
Вылет крюка от ребра опрокидывания — расстояние по горизонтали от ребра опрокидывания до центра зёва крюка[3].
Вылет стрелы — расстояние по горизонтали от оси вращения крана до вертикальной линии, которая проходит через точку подвеса груза. Выпускаются краны с постоянным вылетом стрелы и переменным вылетом. Краны с переменным вылетом способны обслуживать большие площади[2].
Высота подъёма крюка — расстояние от уровня стоянки крана до центра зёва крюка, находящегося в верхнем (высшем) рабочем положении[3].
Глубина опускания крюка — расстояние от уровня стоянки крана до центра зёва крюка, находящегося в нижнем (низшем) рабочем положении[3].
Скорости
Скорость изменения вылета крюка — горизонтальная составляющая скорости перемещения крюка при изменении его вылета[3].
Скорость подъёма груза[2].
Скорость поворота[2].
Рабочая скорость передвижения крана — скорость передвижения крана в рабочем положении с подвешенным грузом, обеспечиваемая его собственным приводом[3].
Транспортная скорость передвижения крана — скорость передвижения крана в транспортном положении, обеспечиваемая его собственным приводом[3].
Наклон и поворот
Для стреловых поворотных кранов должна быть обеспечена возможность подъёма наибольшего рабочего груза на расчётном уклоне при всех положениях поворотной части[3].
Расчётный угол наклона — угол, величина которого:
для стреловых кранов (кроме кранов на железнодорожном ходу) принимается не менее 3°[3].
для портальных — не менее 1°[3].
для железнодорожных кранов угол наклона определяется величиной превышения на кривых участка пути одного рельса над другим[3].
При работе на выносных опорах для стреловых кранов угол наклона может приниматься 1° 30″. Расчётный угол наклона с башенно-стреловым оборудованием определяется проектирующей организацией и указывается в паспорте крана (в СССР введено информационно-директивным письмом Госгортехнадзора СССР от 26 августа 1971 года)[3].
Угол поворота[2].
Портальные краны: типы порталов, расчетные нагрузки и их комбинации,
Показатели Расчет на сопротивление усталости Расчет на прочность и устойчивость
Первый случай нагружения Второй случай нагружения Третий случай нагружения
Комбинации нагрузок
I a I b1 I b2 I c I d II a II b1 II b2 II c II d III
Вес поворотной части Вес неповоротной части Вес груза с грузозахватом Коэффициент динамичности Угол отклонения канатов от вертикали Коэффициент толчков Касательные и центробежные силы инерции при пуске и торможении механизма вращения Силы инерции при пуске и торможении механизма изменения вылета Силы инерции при пуске и торможении механизма передвижения Ветровая нагрузка GП GH GЭ yI - - - - - - GП GH GЭ - aI - - 0,5FИ.В - - GП GH GЭ - aI - - 0,5FИ.В - - GП GH GЭ - bI - 0,5 FИ.К, 0,5 FИ.Ц - - - GП GH GЗ - 0,5aI kT =1,1 - - 0,5FИ.П - GП GH G yП aK - - - - - GП GH G - aII - - FИ.В - - GП GH G - aII - - FИ.В - - GП GH G - bII - FИ.К, FИ.Ц - - - GП GH GЗ - aII kT =1,2 - - FИ.П - GП GH GЗ - - - - - - РВШ
Примечания. 1. Комбинации нагрузок: Iа, IIа – работает только механизм подъема; I b1, I b2, II b1, II b2 – работает только механизм изменения вылета; I c, II c – работает только механизм вращения; I d, II d – работает только механизм передвижения. 2. aК=6° – угол косого подъема. 3. aI, a II – углы отклонения грузовых канатов в плоскости стреловой системы в сторону увеличения вылета; -aI, -aII – то же в сторону уменьшения вылета. 4. GЗ – вес грузозахвата. 5. GЭ=jЭG.
Рис. 1.14 График изменения веса груза по вылету
(1.1)
где G, G(R) – cоответственно допустимые веса грузов на наибольшем вылете Rmax и текущем вылете R; Rmin и Ro – соответственно наименьший вылет и вылет, соответствующий узловой точке грузовой характеристики.
Обычно t = Ro / Rmax ~ 1,25, тогда Ro = 0,625Rmax при t = 2; Ro = 0,5Rmax при t =2,5.
Коэффициенты динамичности YI и YII при работе механизма подъема вычисляют в зависимости от масс груза, жесткостей канатов и элементов крана и скорости подъема. В предварительных расчетах их принимают по данным, приведенным в табл. 1.2. Расчетные углы отклонения канатов от вертикали в плоскости качания стрелы (aI и aII) и в перпендикулярной ей плоскости (bI и bII) соответственно для случаев работы механизмов изменения вылета и вращения принимают по данным испытаний портальных кранов в соответствии с табл. 1.2. Для выбора двигателей используют иные значения углов отклонения канатов от вертикали (табл. 1.2).
Силы инерции определяют по формулам вида Fиi = mi ai, где mi – ускоряемая масса, ai – ускорение, вычисляемое в зависимости от времени неустановившегося движения. Ветровую нагрузку определяют по ГОСТ 1451 и учитывают при выборе двигателей (ветровая нагрузка рабочего состояния) и прочностных расчетах (ветровая нагрузка нерабочего состояния).
1. Башенные краны: типы башен, расчетные нагрузки и их комбинации, Особенности расчета.
Рамы, перекрывающие большие пролеты, могут быть двухшарнирные и бесшарнирные.
Бесшарнирные рамы более жестки, экономичнее по расходу металла и удобнее в монтаже; однако они требуют более массивные фундаменты с плотными основаниями для них и более чувствительны к температурным воздействиям и неравномерным осадкам опор.
Рамные конструкции по сравнению с балочными более экономичны по затрате металла и более жестки, благодаря чему высота ригеля рамы имеет меньшую высоту, чем высота балочных ферм.
Рамные конструкции применяются для пролетов до 150м. При дальнейшем увеличении пролетов они становятся неэкономичными.
В большепролетных покрытиях применяются как сплошные, так и сквозные рамы.
Сплошные рамы применяются редко при небольших пролетах (50-60м), их преимущества: меньшая трудоемкость, транспортабельность и возможность уменьшения высоты помещения.
Наиболее часто применяются рамы с шарнирным опиранием. Высоту ригеля рам рекомендуется принимать равной: при сквозных фермах 1/12 – 1/18 пролета, при сплошных ригелях 1/20 – 1/30 пролета.
Рамы рассчитывают методами строительной механики. В целях упрощения расчета легкие сквозные рамы можно приводить к эквивалентным им сплошным рамам.
Тяжелые сквозные рамы (типа тяжелых ферм) должны рассчитываться как решетчатые системы с учетом деформации всех стержней решетки.
При больших пролетах (более 50м) и невысоких жестких стойках необходимо производить расчет рам на температурные воздействия.
Ригели и стойки сплошных рам имеют сплошные двутавровые сечения; их несущая способность проверяется по формулам для внецентренно-сжатых стержней.
В целях упрощения расчета решетчатых рам их распор допускается определять как для сплошной рамы.
Рекомендуется следующий порядок расчета большепролетных рам:
приближенным расчетом устанавливают предварительные сечения поясов рамы;
определяют моменты инерции сечений ригеля и стоек по приближенным формулам;
рассчитывают раму методами строительной механики; расчетную схему рамы следует принимать по геометрическим осям;
определив опорные реакции, находят расчетные усилия во всех стержнях, по которым окончательно подбирают их сечения.
Типы сечений, конструкция узлов и соединения рамных ферм такие же, как и для тяжелых ферм балочных конструкций.
Уменьшение изгибающего момента в ригеле рамы можно получить путем передачи веса стены или покрытия пристроек, примыкающих к главному пролету, на внешний узел стойки рамы.
Другим искусственным приемом разгрузки ригеля является смещение в двушарнирной раме опорных шарниров с оси стойки внутрь.
В этом случае вертикальные опорные реакции создают дополнительные моменты, разгружающие ригель.
1. Листовые конструкции. Общие принципы расчета. Особенности расчета листовых конструкций (бункера, конвейеры и т.п.).
1.1 Область применения, классификация и особенности
листовых конструкций
Листовыми конструкциями называют пространственные конструкции, в
которых основную несущую и ограждающую функцию выполняют
металлические листы, образующие оболочки различной формы. Классификация
листовых конструкций может быть представлена в следующем виде:
Резервуары, предназначенные для хранения нефтепродуктов, масел,
воды, сжиженных газов, кислот, спиртов и других жидкостей.
В зависимости от положения в пространстве и геометрической формы
резервуары делят на вертикальные цилиндрические, горизонтальные
цилиндрические, сферические, каплевидные, торовые, траншейные.
По расположению относительно планировочного уровня строительной
площадки различают: надземные (на опорах), когда днище резервуара
расположено на опорах выше уровня основания (грунта); наземные, когда
днище резервуара опирается непосредственно на основание (грунт);
полузаглубленные, когда нижняя грань (днище) или образующая расположены
ниже планировочного уровня грунта; подземные резервуары, когда верхняя
грань или верхняя образующая резервуара расположена ниже планировочного
уровня площадки.
Вертикальные цилиндрические резервуары выполняют со стационарной
крышей, с понтоном и плавающей крышей. Резервуары со стационарной
крышей в зависимости от конструкции покрытия могут быть с конической
крышей с центральной стойкой или без стойки; со сферической крышей в виде
распорной конструкции; торосферической кровлей и кривизной в двух
направлениях.
Газгольдеры, предназначенные для хранения, смешивания и
выравнивания состава газов, для регулирования их расхода и давления. Их
включают в газовую сеть между источником получения газа и его
6
потребителями в качестве аккумуляторов, выравнивающих производство и
потребление газа.
В зависимости от применяемого давления газгольдеры могут быть
разделены на 2 класса: газгольдеры высокого давления (>70 кПа); газгольдеры
низкого давления ( 70 кПа). Газгольдеры высокого давления предназначены
для эксплуатации при рабочем давлении от 70 кПа до 3 МПа, а иногда и при
более высоком давлении. Рабочее давление в газгольдерах низкого давления
назначают, исходя из специфики технологических процессов, но в большинстве
случаев оно не превышает 4-5 кПа.
По своим технологическим особенностям и требованиям газгольдеры
разделяют на два типа: переменного объѐма (постоянного давления) и
постоянного объѐма (переменного давления). Газгольдеры переменного объѐма
предназначены для эксплуатации при низком избыточном давлении (не выше
0,005 МПа), а газгольдеры постоянного объѐма – для хранения газа при более
высоком избыточном давлении (нередко более 0,4 МПа).
Газгольдеры постоянного объѐма имеют цилиндрическую или
сферическую геометрическую форму.
Цилиндрические газгольдеры могут быть как вертикальные, так и
горизонтальные и иметь различную форму днищ: сферическую, эллиптическую
и торовую. Объѐмы их колеблются от 100 до 200 м³ при внутреннем давлении
от 0,4 до 1,8 МПа.
Объѐмы сферических газгольдеров составляют 600-1000 м³. Они более
экономичны по массе, расход металла на их изготовление на 40% меньше, чем
на цилиндрические.
Бункера и силосы, предназначенные для хранения и перегрузки
сыпучих материалов: руды, угля, кокса, флюсов, цемента, песка, гравия, щебня
и др. Группы бункеров обычно объединяются в бункерные эстакады. Силосы
отличаются от бункеров сравнительно большим отношением высоты к
размерам в плане.
7
Стальные бункера отличаются многообразием объѐмно-планировочных
и конструктивных решений. Среди основных конструктивных решений
наиболее широкое применение нашли бункера с плоскими стенками и гибкие
бункера.
Трубопроводы большого диаметра (D>0,5 м), используемые для
транспортирования нефтепродуктов, газа, воды, размельчѐнных или
разжиженных твѐрдых веществ.
Протяжѐнные трубопроводы большого диаметра называют
магистральными трубопроводами. Область их применения велика:
магистральные газопроводы; нефтепроводы; углепроводы; напорные
трубопроводы гидравлических электростанций и циркуляционные
трубопроводы ТЭС и АЭС; заводские газопроводы и воздуховоды
металлургических заводов, нефтехимических заводов; подводные
трубопроводы (дюкеры). Они являются исключительно металлоѐмкими и
дорогостоящими сооружениями.
По месту укладки и типу опирания трубопроводы могут быть
надземными, лежащими на отдельных опорах; подземными, уложенными в
грунт (в траншеях, канавах насыпях) или на опоры в тоннелях; подводными,
уложенными по дну водоѐмов и рек или в траншеях, прорытых на дне.
Магистральные нефтепроводы и нефтепродуктоводы в зависимости от
диаметра подразделяют на 4 класса: 1 класс – при диаметре более 1000 мм;
2 класс – 500 < D < 1000 мм; 3 класс – 300 < D < 500 мм; 4 класс – D 300 мм.
В зависимости от внутреннего давления трубопроводы делят на
напорные и безнапорные. Напорные трубопроводы могут быть высокого,
среднего и низкого давления (в пределах от 0,7 до 10 МПа).
Специальные листовые конструкции – сооружения
металлургической, химической, нефтяной и других отраслей промышленности:
кожухи доменных печей, воздухонагревателей, пылеуловителей; сосуды
химической и нефтезаводской аппаратуры, защитные оболочки реакторов АЭС,
дымовые и вентиляционные трубы, сплошностенчатые башни, градирни и т.п.
8
По характеру работы листовые конструкции разделяют на: наливные и
работающие под внутренним давлением или вакуумом; находящиеся под
действием высокой, нормальной и низкой температуры; работающие на
статическую, знакопеременную и ударную нагрузки; работающие в условиях
нейтральных или агрессивных сред.
В большинстве случаев листовые конструкции представляют собой
ѐмкостные сооружения в виде тонкостенных сплошных оболочек.
Условия работы листовых конструкций весьма разнообразны: они могут
быть надземными, наземными, полузаглубленными, подземными, подводными;
могут воспринимать статические и динамические нагрузки; работать под
низким, средним и высоким давлением, под вакуумом, под воздействием
низких, средних и высоких температур, нейтральных или агрессивных сред и
т. д.
Для листовых конструкций характерно двухосное напряжѐнное
состояние, а в местах сопряжения различных оболочек или на участках
защемления оболочек у колец жѐсткости, крыш и днищ дополнительно
возникают местные напряжения, быстро затухающие по мере удаления от этих
участков (явление краевого эффекта). Причина возникновения местных
напряжений краевого эффекта заключается в том, что под действием расчѐтных
нагрузок общие точки сопряжѐнных между собой разных оболочек или
оболочек и конструктивных элементов из условия совместности деформаций
имеют одинаковые перемещения, хотя каждая из них под действием этих
нагрузок стремится к разным деформациям, соответствующим их
геометрическим и статическим параметрам.
Основной особенностью листовых конструкций является необходимость
обеспечить не только равнопрочные, но и герметичные (плотные) сопряжения
листов. При этом протяжѐнность сварных соединений существенно больше,
чем в других типах сварных соединений. Так, например, в сварных листовых
конструкциях малой и средней толщины на 1 т стали приходится 30-50 м
9
сварных швов против 15-25 м в обычных строительных металлических
конструкциях.
При изготовлении листовых конструкций необходимы операции, не
встречающие при изготовлении обычных металлических конструкций:
фасонный раскрой листового проката; вальцовка цилиндрических, конических
оболочек и колец; вальцовка и штамповка оболочек двоякой кривизны;
отбортовка и строжка кромок выпуклых днищ и другие операции.
1. Пути снижения металлоемкости металлических конструкций.
Черные металлы и особенно стальной прокат в экономике нашей страны еще долгие годы будут основным конструкционным материалом. Однако возможности экстенсивного пути развития черной металлургии, т. е. удовлетворение возрастающих потребностей народного хозяйства в металлопрокате за счет увеличения производства стали, выпуска проката и стальных труб, во многом исчерпаны. Поэтому одним из основных направлений развития народного хозяйства (в первую очередь главных металлопотребляющих отраслей: машиностроения, металлообработки и строительства) является пересмотр оценок качества металлопроката и уровня его использования в конструкциях с технической и экономической точек зрения.
Недопустимо положение, когда металлопотребляющие отрасли регламентируют применение углеродистых и низколегированных сталей и уровень использования их прочностных свойств. Неэффективна практика минимизации типоразмеров проката. Предприятия и отрасли таким путем облегчают условия металлоснабжения, но повышают металло-, трудо- и энергоемкости производства конструкций и эксплуатационных расходов в течение всего срока их службы.
Потребители стального проката непрерывно повышают требования к его качеству, и металлурги в основном удовлетворяют их. Однако этот фактор полностью не используется в целях снижения металлоемкости конструкций. Коэффициенты безопасности, допускаемые напряжения и расчетные сопротивления проката сохраняются неизменными.
Предприятия отраслей машиностроения и строительства ориентированы, главным образом, на снижение трудовых затрат. В связи с этим конструктивные и технологические решения и приемы, которые при снижении металлоемкости конструкций позволяют повысить их работоспособность, надежность, долговечность и другие качества, но требуют повышенных трудовых затрат, не получили достаточного применения. Необходимое качество выпускаемых конструкций в большинстве отраслей обеспечивается увеличением толщин и сечений применяемого металлопроката. Допускаемый при этом перерасход металла считают более выгодным для изготовителя конструкций, чем применение с той же целью конструктивно-технологических мероприятий, так как они увеличивают затраты труда в производстве. Такой практике способствуют и практические методы определения экономической эффективности снижения норм расхода металла. В частности, недооценивается значение экономии затрат прошлого труда, который в общей стоимости современной продукции доминирует. He учитываются последствия, обусловливаемые перерасходом конструкционного металла в металлургической промышленности и сопряженных с ней отраслях народного хозяйства, на магистральном транспорте и при эксплуатации промышленной продукции и сооружений.
Для изменения сложившегося в машиностроении и строительстве отношения к снижению металлоемкости конструкций необходимо ускорить введение в действие единой для всех отраслей народного хозяйства методики определения экономической эффективности снижения металлоемкости конструкций. Эта методика должна способствовать формированию объективных взглядов и практических приемов определения основных экономических показателей, характеризующих народнохозяйственный доход, сопутствующий снижению металлоемкости конструкций. В соответствии с единой методикой должны быть приведены прейскуранты оптовых цен на прокат и металлоконструкции.
Первым шагом к созданию методики можно считать признание интегральным показателем удельной металлоемкости национального дохода. Правильное понимание и применение нового экономического показателя должно быть обусловлено комментариями к единой обязательной методике. Необходимо изложить и регламентировать единую систему определения вспомогательных и промежуточных характеристик и показателей, которые отражают эффективность мероприятий, проводимых на этапах производства проката, проектирования и производства конструкций, а также в период эксплуатации промышленной продукции и сооружений.
Задания по снижению удельной металлоемкости национального дохода выполнимы лишь при использовании в каждой отрасли комплекса научно-технических, инженерно-производственных и организационноэкономических мероприятий. Планируя их практическое применение, следует учитывать, что большинство известных мероприятий требует увеличения затрат производственных ресурсов и дополнительных капитальных вложений. Все мероприятия, осуществляемые с привлечением дополнительных капитальных вложений, приводят к цели по истечении полного цикла их освоения, который обычно достаточно длителен, особенно в условиях действующего производства. Методы снижения металлоемкости конструкций, требующие дополнительных затрат производственных ресурсов, уступают по экономичности и срокам реализации мероприятиям, которые могут быть проведены без таких затрат или при небольшом их уровне. Удельная металлоемкость национального дохода при малозатратных мероприятиях снижается пропорционально уменьшению металлоемкости и повышению национального дохода. Поэтому они должны быть использованы в первую очередь.
Указанным целям соответствует зародившийся и разработанный в нашей стране комплексный путь снижения металлоемкости конструкций, который создает предпосылки для уменьшения удельной металлоемкости национального дохода на всех этапах его создания. Он основан на новых подходах к определению механических свойств проката и его нормативных характеристик прочности и пластичности, а также допускаемых напряжении, расчетных сопротивлений и коэффициентов безопасности, при которых может быть использован прокат в силовых конструкциях промышленной продукции и сооружений.
В сферах производства и потребления проката проводятся мероприятия, отвечающие новому подходу к оценке его качества и определению уровня использования в конструкциях. Так, в металлургическом производстве реализуется комплекс мероприятий по повышению уровня прочности и надежности, проката на этапе контроля его свойств и аттестации при выпуске. Это достигается дифференциацией проката каждой марки стали по двум группам нормативной прочности, обеспечением каждой поставляемой партии металла установленными механическими свойствами с довеительной вероятностью не менее 0,95. Дифференциацию проката проводят на основании статистического материала по каждому размеру и виду проката, получаемого металлургическим предприятием по установившейся технологии на конкретном оборудовании. Результаты обработки статистических данных с использованием теории вероятности позволяют установить зависимость контролируемых свойств проката от технологии выплавки стали и режимов прокатки, регламентировать приемочные характеристики, по которым необходимо вести отбраковку металла, чтобы принятый прокат имел свойства установленного уровня, а их вероятность в каждой партии соответствовала условию Pм > 0,95.
Теория показывает, а практика подтверждает, что заданный уровень вероятности контролируемых свойств 1-й (Ciн1) и 2-й (Ciн2) групп дифференцированного проката обеспечивается повышением приемочных (браковочных) значений (чисел) соответственно на Ai1 и Ai2 против нормативных.
Таким образом, механические свойства дифференцированного проката определяются условиями его приемки: Ciп1 > Ciн1 + Ai1; Ciп2 > Ciн2 + Ai2. Действующие ГОСТы не обусловливают уровень вероятности механических свойств каждой поставляемой партии проката. Приемку ведут по условию: Ciп0 > Ciн0 при Ai0 = 0, следовательно, нормативная прочность проката завышена на Ai0. Дифференцированный прокат превосходит идентичный гостированный по марке стали, виду и толщине. При равенстве нормативных значений Ciн1 = Ciн0
При превышении нормативных характеристик дифференцированного проката Ciп2 > Ciн0
Снижение металлоемкости в машиностроении и строительстве при применении дифференцированного по прочности проката
Такой подход к определению механических свойств проката и разделению его на группы прочности позволяет прогнозировать ожидаемые результаты. Благодаря этому по изменению статистических характеристик можно заблаговременно обнаружить негативные отклонения в технологии выплавки стали и режимах прокатки и своевременно предотвратить их влияние на качество продукции.
Вероятностно-статистический метод аттестации проката по двум группам прочности обеспечивает значительные преимущества по основной прочностной характеристике — пределу текучести отн. В этом нетрудно убедиться, анализируя кривые распределения проката по уровню предела текучести.
Рассмотрим листовую низкоуглеродистую и арматурную низколегированную стали (рис. 1 и 2). Кривые распределения и другие статистические характеристики этих сталей являются результатам испытания нескольких сот партий проката одинаковых марок стали, вида и толщины. Первая характеризует листовой прокат стали ВСтЗсп толщиной 10 мм, вторая — арматурную сталь 35ГС диаметром 20 мм. Разброс значений от для каждой рассматриваемой стали значителен, и, следовательно, дифференциация проката каждого вида может быть весьма эффективной. Нормативные значения предела текучести дифференцированного углеродистого листового проката определены в соответствии с ТУ 14-1-3023—80 для 1-й группы прочности отн1 = 245 МПа и для 2-й группы отн2 = 275 МПа. Средние квадратические отклонения предела текучести для всей совокупности плавок S = 25 МПа, для партии проката S0 = 10 МПа.
Арматурная сталь 35ГС характеризуется значениями S = 27,65 МПа и S0 = 6,57 МПа, для ее групп приняты отн1 = 392 МПа и отн2 = 422 МПа.
Статистические данные, приведенные выше, позволяют определить приемочные числа для каждой группы листовой и арматурной стали по формуле
(n — число образцов, по которым определяют свойства каждой партии проката; для дифференцированного проката n = 2, для гостированного n =1; d = S02/S2-S02; h1 = oт-отн1; h2 = от-отн2 здесь от — среднее значение предела текучести, соответствующее кривой распределения).
Расчеты дают следующие значения: для листовой стали Дт1 = 16,5 МПа, Aт2 =19,4 МПа, Стп1 = отп = 245 + 16,5 = 261,5 МПа; Cтп2 = отн2 = 294,4 МПа; для арматурной стали Ат1 = 11,5 МПа, Ат2 = 12,4 МПа, Стп1 = отп1 = 403,5 МПа; Стп2 = отн2 = 434,4 Мпа.
Приемочные числа являются абсциссами ординат, которые определяют массу кондиционного проката и разделяют его на две группы прочности (см. рис. 1 и 2). Очевидно, 1-я группа листовой стали комплектуется партиями проката с приемочными значениями прочности, находящимися в интервале 261,5...294,4 МПа. Нормативная фактическая прочность проката этой группы выше обусловленной ТУ 14-1-3023-80 отн1 = 245 МПа и регламентированной ГОСТ 380-71 отн0 = 235 МПа (см. рис. 1,6). Усредненная нормативная прочность согласно расчетам по 1-й группе проката отн1с = 265 МПа, по 2-й — отн2с = 300 МПа.
Фактические значения предела текучести проката oтiф превышают приемочные отпi — на величину Aф - A1(2). Поэтому характеристики вероятности, отнi, вычисляемые с помощью формулы
возрастают по мере приближения к границе высокого уровня значений от (см. рис. 1, в и 2, в). Усредненные значения вероятностей отн1(2) для листовой стали ВСтЗсп 1-й и 2-й групп соответственно равны Рмфс1 = 0,9992 и Рмфс2 = 0,9997.
Характеристики дифференцированного листового проката и арматурной стали, а также идентичного гостированного проката даны в табл. 1. Дифференцированные по двум группам прочности листовая и арматурные стали превосходят аналогичные стандартные не только по прочности, но и по надежности. Высокая достоверность прочностных характеристик дифференцированного проката каждой группы прочности, обусловленная введением в ТУ и ГОСТы на металлопрокат обязательного нового требования о гарантировании механических свойств с минимальной граничной вероятностью для каждой партии проката Pм > 0,95, позволяет использовать новые подходы к определению допускаемых напряжений и расчетных сопротивлений дифференцированного проката.
Одним из возможных новых подходов является установление расчетных сопротивлений и допускаемых напряжений для дифференцированного проката в зависимости от усредненных значений прочности и вероятности механических свойств каждой группы металлопроката. Такой подход позволяет без снижения существующих общих коэффициентов безопасности работы конструкций повысить по сравнению с уровнем 1985 г. допускаемые напряжения для проката углеродистой стали 1-й группы на 13 % и 2-й группы на 28 % (см. табл. 1). Расчетные сопротивления могут быть выше установленных действующими СНиП П-23-81 и СНиП 2.03.01-84 для листового проката стали ВСтЗсп толщиной 10 мм 1-й и 2-й групп прочности на 16 и 30 %, а для арматурной стали 35ГС диаметром 20 мм на 6,3 и 15 %.
Применение дифференцированного металлопроката с повышенными допускаемыми напряжениями и расчетными сопротивлениями позволяет снизить удельную металлоемкость машиностроительных конструкций в среднем на 9 %, стальных конструкций промышленных и гражданских объектов на 10 %, железобетонных в среднем на 9 %.
Переход к выпуску дифференцированного проката обусловливает повышение его эквивалента прочности в среднем на 10 %. Этот эффект достигается при существующем уровне сквозных приведенных затрат от добычи сырья до отгрузки готового проката. Применение такого проката позволяет потребителям снизить потребление конструкционной стали, вспомогательных материалов, всех видов производственной энергии и трудовых ресурсов. Ускоряется производство и снижается потребность в капитальных вложениях на наращивание производственных мощностей. Благодаря дифференциации проката народное хозяйство получает менее металлоемкие виды промышленной продукции и сооружения, которые по эксплуатационной экономичности превосходят эквивалентные конструкции из стандартного проката.
Итак, дифференциации проката по разным уровням прочности сопутствует положительный народнохозяйственный экономический эффект, образующийся в сферах производства металла, изготовления и монтажа конструкций, использования услуг сопряженных отраслей народного хозяйства, а также металлосодержащей промышленной продукции и сооружений в общественном производстве. Экономическая эффективность дифференциации определяется раздельно по каждой сфере с учетом их особенностей. Она выражается экономией приведенных затрат при производстве эквивалентных по назначению и потребительским свойствам видов продукции (работ) с учетом преимуществ дифференциации проката и без их учета.
Полная народнохозяйственная экономическая эффективность дифференциации проката равна, очевидно, суммарному эффекту по всем сферам, в которых проявляется действие дифференциации. Этот показатель определяет экономию затрат живого и прошлого труда: от добычи сырья для производства металла до окончания нормативного срока службы конструкции.
Таким образом, суммарная экономия приведенных затрат по всем сферам обращения дифференцированного проката (в явном и неявном виде) характеризует полную народнохозяйственную экономическую эффективность, обусловленную дифференциацией. Этот показатель может быть исчислен на единицу массы вытесняемого базового проката или вводимого нового. Таким удельным показателем удобно пользоваться при изучении экономики крупных производств, а также применительно к конкретному виду продукции.
Некоторое представление об общей эффективности дифференциации проката и долевом значении отдельных сфер дают приведенные в качестве примера данные табл. 2. Анализ показывает, что удельный национальный доход, сопутствующий дифференциации, в 2,5 раза превышает народнохозяйственную стоимость сэкономленного проката.
Выводы
1. Отраслям промышленности и строительства рекомендуется оценить техническую и экономическую сущность дифференциации проката и принять меры по распространению вероятностно-статистического метода аттестации на марки стали, еще не охваченные этой методикой. Следует переработать существующие правила проектирования и расчета конструкций, обеспечив широкое применение дифференцированного проката вместо аналогичного стандартного, при полном использовании всех его технических преимуществ, ускорить переработку существующей рабочей документации на изготовление конструкций пониженной металлоемкости из дифференцированного проката.
2. Госстандарту России целесообразно включить в ГОСТ 1.2-85 дополнительные требования, ориентирующие разработчиков на создание ГОСТов и ТУ на производство конструкционного проката, который по качеству превосходил бы лучшие зарубежные аналоги, и обязывающие в ГОСТах и ТУ на металлопрокат нормировать вероятность основных механических свойств.
3. Распространить государственную приемку на руководящие отраслевые материалы, определяющие расход и уровень использования конструкционной стали, и проектную документацию, используемую при производстве металлосодержащих конструкций.
Металлоконструкции для бизнеса
Металлоконструкции от производителя. Гарантия. Качество.
Узнать больше
techline-online.ru
Яндекс.Директ
Другие новости по теме:
Духовые шкафы с функцией СВЧ
Ультразвуковой неразрушающий метод измерения напряжений в сварных конструкциях
О повышении несущей способности и долговечности сварных конструкций
Сварные конструкции
Металлургия дуговой сварки конструкционных сталей и сварочные материалы
Оценка качества контактной точечной сварки с помощью нейронных сетей
Математическое моделирование сварочных процессов для создания систем прогнозирования качества соединений и оптимального управления
Автоматизированная система для экспериментальных исследований сварочных процессов на основе ВК М-6000
Машина для контактной стыковой сварки
Машина для контактной стыковой сварки рельсов
Технологии изготовления металлоконструкций ПТМ.
Технологии изготовления металлоконструкций
изготовление металлоконструкцийМеталл сегодня наиболее активно используется в строительстве и машиностроении. При этом совокупное количество металла, идущего на строительные нужды (возведение различных сооружений, создание энергетических и прочих коммуникаций), существенно превышает число металлических деталей, используемых в машиностроении. И это неудивительно, так как изготовление металлоконструкций позволяет создавать важнейший элемент разнообразных строительных объектов — каркасную основу.
Виды металлоконструкций
Без специальных металлоконструкций невозможно было бы строить многие инженерно-технические сооружения, являющиеся атрибутами современной цивилизации. Готовые металлоконструкции по способу эксплуатации подразделяются на три основных вида:
1. Стационарные.Монтируются и закрепляются на объекте на долгий срок.
2. Сборно-разборные.После демонтажа могут быть установлены на новом объекте.
3. Трансформируемые.Могут изменяться не только по форме, но и по размеру.
Назначение металлоконструкций
Производство строительных металлоконструкций ориентировано на особенности объекта, для которого выполняется тот или иной заказ. Так, каркас быстровозводимых сооружений, как правило, состоит из легких металлоконструкций. Строительные конструкции из усиленного металлопроката применяются для создания каркасной основы практически всех типов зданий. Для изготовления лестничных пролётов, дорожных знаков, ограждений и прочих малогабаритных объектов используют изделия, которые относятся к малым металлоконструкциям.
Различные цистерны и резервуары из металла предназначены для хранения технической или питьевой воды, горюче-смазочных материалов и прочих жидкостей, в том числе химически опасных. Кроме того, существуют дорожные металлоконструкции и изделия из металла для телекоммуникационных сооружений.
Изготовление металлоконструкций по чертежам заказчика подразумевает создание изделий фактически любых форм и размеров, какие возможны в условиях современного производственного цикла.
изготолвение металлоконструкций изготолвение металлоконструкций изготолвение металлоконструкций
Технологии производства металлоконструкций
Изготовление металлоконструкций на заказ осуществляется в несколько этапов, среди которых наиболее важное значение имеет сборка. На этой стадии производство металлоконструкций может включать сварку, склейку или сборку (болтами, заклёпками) отдельных фрагментов:
1. Сварка происходит путём нагрева двух деталей по стыковочной линии вплоть до частичного расплавления металла (по сварочной кромке). При электродуговой сварке особое значение имеет электрод, который, расплавляясь, обеспечивает стыковочный шов. Помимо этого, существует сварка газовой горелкой, в том числе с использованием инертных газов, а также точечная сварка (посредством прижимания двух металлических листов друг к другу и пропускания в месте точечного сдавливания электрического разряда).
2. Склейка относится к довольно надёжным способам соединения фрагментов металла. Современные клеящие составы не просто обеспечивают эффект склеивания — они способны соединять участки/плоскости/стыки на молекулярном уровне.
3. Сборка заклёпками и/или болтами представляет собой механический тип крепления. Склёпывание применяется в тех случаях, когда предполагается, что изделие будет испытывать существенные вибрационные нагрузки. Дело в том, что под воздействием вибрации фиксация, реализованная с помощью болтов и гаек, может ослабнуть, в то время как заклёпки обеспечивают более надежное крепление.
Вне зависимости от того, какую продукцию выпускает цех по производству металлоконструкций, готовые изделия (элементы будущих строительных сооружений) на всех стадиях производственного процесса должны проходить строгий контроль. Серьёзные производственные предприятия, занимающиеся изготовлением металлоконструкций, как правило, располагают несколькими цехами, специализирующимися на выполнении определённых манипуляций. В зависимости от специфики деятельности, материально-техническую базу такого предприятия могут формировать:
фрезеровочный цех (раскрой металлопроката по заданным размерам);
токарный цех (изготовление специальных крепёжных и дополнительных элементов/деталей);
прессовально-формовочный цех (изменение плоскостных параметров металлических заготовок согласно спецификации/чертежам, поданным заказчиком, в том числе методом кузнечного сгиба и прессовального выбивания отверстий);
сборочный цех (сборка отдельных элементов в изделия/секции посредством различных видов сварки, склейки, склёпывания и крепления на болты);
покрасочный цех, как правило, располагающий оборудованием для пескоструйной обработки (подготовка изделий к покраске, грунтовка антикоррозионными составами и на
1. Несущие конструкции манипуляторов.
Механическая система современного робота - его манипулятор - отличается большим многообразием конструктивных исполнений. В целом построение конкретного манипулятора определяется значительным числом факторов: грузоподъемностью, скоростью и величиной перемещений, типом привода, требованиями и условиями эксплуатации и другими, но прежде всего - принятой конфигурацией манипуляционной системы, т.е. его базовой системой координат, что наглядно проиллюстрировано в гл. 3 при рассмотрении промышленных роботов. Наряду с этим конструктивный облик манипулятора зависит также от особенностей компоновочных решений и конструкций основных составных частей (или узлов) манипулятора
5.1. Основные составные части манипулятора
При рассмотрении в гл. 4 структурных схем МС, дающих самое общее представление о конструктивном построении манипулятора, использовалось понятие "звена", как детали или жесткого элемента, не изменяющего своих размеров и формы в процессе движения и взаимодействия с другими звеньями и характеризующегося только массой, длиной и условиями перемещения. Такого представления было вполне достаточно для решения основных задач механики МС. Однако в реальном воплощении звено манипулятора как важнейший элемент конструкции имеет достаточно сложное построение, содержит, помимо жестких несущих элементов, ряд других компонентов реальной конструкции: части приводов, составляющие элементов кинематических пар; остановочные, тормозные и демпфирующие устройства и т.п. Такие звенья реальной конструкции будем называть узлами манипулятора
В общем виде в состав манипулятора входят: а) несущие элементы, обеспечивающие конструктивные жесткость и прочность и служащие базой для размещения на них других составляющих узла; б) совокупность деталей, образующих кинематические пары (цапфы, оси, подшипники, направляющие и т.п.); в) устройства, обеспечивающие движения по степеням подвижности и включающие элементы приводов манипулятора (двигатели, трансмиссии, линии подвода энергоносителя и т.п.); г) элементы, ограничивающие и регулирующие величины и скорости перемещений (упоры, амортизаторы, тормозные устройства и т.п.); д) устройства (датчики) обратной связи; е) прочие устройства - предохранительные, защитные, смазочные и т. п.
В промышленном роботостроении узлы манипуляторов часто оформляются в виде отдельных агрегатно-сборочных единиц, имеющих унифицированные присоединительные места для состыковки с другими узлами манипулятора. Такие автономные универсальные агрегатные блоки, позволяющие путем соответствующего их сочетания и компоновки собирать широкий диапазон различных конструкций ПР в соответствии с требованиями техпроцессов, принято называть модулями, в манипуляторы, составленные из них, - манипуляторами модульного исполнения. В зависимости от функционального назначения, а также от вида реализуемого движения выделим следующие основные разновидности узлов.
"Рука" - один из наиболее сложных узлов, сходный по своим функциям и структуре с рукой человека Завершением этого узла является рабочий орган, непосредственно взаимодействующий с объектом манипулятора "Рука" обеспечивает рабочему органу как переносные, так и ориентирующие степени подвижности. По структуре "руки" бывают и многозвенные. Первые имеют одну (поступательную) или две (поступательную и вращательную) степени подвижности, вторые - несколько. Преимущественно многозвенные "руки" выполняются в виде двухзвенных с двумя переносными вращательными (сгибы) степенями подвижности.
Каретка - узел, перемещающийся прямолинейно в вертикальном или горизонтальном направлениях по жестким направляющим смежного с ним узла - основания, колонны, другой каретки.
Колонна, или платформа, - узлы, обеспечивающие вращательное движение относительно вертикальной оси присоединенных к ним других узлов манипулятора
Блок углового перемещения, или качания (каретка вращательного движения), - узел, обеспечивающий вращательное, как правило, неполноповоротное движение относительно какой-либо оси (обычно горизонтальной) присоединенного к нему другого узла манипулятора (например, "руки" относительно колонны или каретки).
Основание - опорная конструкция, на которой размещаются узлы и системы манипулятора, может быть неподвижным или перемещаемым. В последнем случае основание оснащается устройством передвижения, реализующим одну или две (очень редко три) координатные степени подвижности манипулятора
Б1.Б.34 Грузоподъемные машины и оборудование
1. Классификация грузоподъемных машин.
62 Классификация грузоподъемных машин
Грузоподъемные машины предназначены для подъема или перемещения груза в горизонтальном и вертикальном направлении. В строительстве при помощи этих машин достаточно часто осуществляют различный монтаж и демонтаж. ГПМ по констр. признаку : подъемники (группа машин период. действия для подъема грузов и людей по направляющей); подъемные механизмы группа машин период. действия для подъема и опускания грузов (домкраты и лебедки).
Домкраты – толкатели, поднимающие или опускающие груз на небольшое расстояние бывают винтовые, зубчато-реечные, гидравл. и пневматические. использ. как самостоятельно так и в составе более сложных ГПМ.
Лебедки – совокупность приводного барабана и тягового органа. использ. для перемещения грузов как самостоятельные ГПМ.
Таль – подвешенная неподвижная лебедка.
Тельфер - подвешенная лебедка с приводом передвижения.
Кран – машина циклического действия для подъема и опускания груза, подвеш. с помощью крюка или др. грузозахватного устройства.
Краны делят в завис. от области обслуживания и конструкции:
Пролетные
Стреловые
Пролетные краны.
Горизонтальное перемещение таких кранов осущ. с помощью поступательного перемещения самого крана и крановой тележки.
Кран мостового типа – кран у которого грузозахватный орган подвешен к тележке, тали или стреловому крану, перемещ. по мосту.
Кран мостовой - кран у которого несущие элементы конструкции опираются на крановый путь.
Козловой кран - кран у которого несущие элементы конструкции опираются на крановый путь при помощи двух опорных стоек. Такие краны применяют для обслуживания больших открытых площадок.
Кабельный кран – кран у которого грузозахватный орган подвешен к тележке, перемещ. по несущим канатам, закрепленным на двух опорах. Такие краны применяют при пролетах от 100 м до 1 км.
Кран мосто-кабельный - кран у которого несущими элементами явл. канаты, закрепл. на концах моста, установленного на опорных стойках.
Стреловой (консольный) – поворотный кран у которого стрела закреплена на поворотной платформе. Гориз. перемещение груза обеспечивается либо вращат. движением стрелы, либо пост. движением тележки по стреле либо всего крана.
По конструктивным особенностям ходовой части и зоне обслуживания: мобильные краны (автомобильные, гусеничные); краны, действ. на малые расстояния (портальные, башенные, велосипедные, настенные
Портальный кран прим. Для погрузочных/разгрузочных работ в портах и на открытых площадках. Поворотная часть устанавл. на порталах и полупорталах.
Настенный кран имеет две опоры, уст. на стене.
Башенный кран – поворотный кран со стрелой, закрепл. в верхней части вертикально расположенной башни.
Велосипедный – кран, перемещ. по наземным рельсовым путям и удерживаемый верхней направляющей.
Классификация кранов.
По степени подвижности: подвижные (самоходные или прицепные), полустационарные – обслуж ограниченные пространства, стационарные.
По направлению перемещения груза: с прямолинейным движением крана, с поворотной стрелой и радиальным перемещением груза, комбинированные – поступ. движение тележки или крана с вращением стрелы.
По грузоподъемности: Легкие (до 10 т), Средние (10-40 т), Тяжелые (>40 т).
По типу привода: Ручной, Электр., Гидравлический, Пневматический.
По типу грузозахватного приспособления: Крюковые, Грейферные, Магнитные, Со спец. приспособлением.
По типу ходового устройства: Кран рельсовый, На гусеничном ходу, На колесном ходу, На пневмоколесном ходу.
Основные параметры ГПМ.
Основные параметры грузоподъемных машин.
Грузоподъемные машины характеризуются своей грузоподъемностью, скоростями движения отдельных механизмов и режимом работы.
Грузоподъемностью машины [1] называют массу номинального (максимального) рабочего груза, на подъем которого рассчитана данная машина. В величину грузоподъемности включается вес грузозахватного приспособления, а также вес всех вспомогательных устройств, подвешиваемых к грузозахватному приспособления. Значения грузоподъемности нормированы ГОСТ 1575-87 «Краны грузоподъемные. Ряды основных параметров», устанавливающим ряд номинальных грузоподъемностей для всех типов машин (до 900 тонн).
Скорость подъема груза, зависящая от грузоподъемности крана, обычно не превышает 25÷30 м/мин.
Скоростью передвижения моста крана достигает 100÷120 м/мин.
Скорость передвижения тележек мостовых кранов обычно составляет 35÷50 м/мин.
Скорости движения механизмов кранов, используемых в массовых перегрузочных работах, могут достигать 90÷120 м/мин для подъема и спуска груза, 240÷360 м/мин для передвижения тележек, движущихся по рельсовому пути.
Частота вращения стрелы достигает 3 об/мин в зависимости от скорости конца стрелы, не превышающей 5÷6 м/с.
Для грузоподъемных машин характерна работа с поворотно-кратковременными включениями, при которых рабочее приспособление и груз совершают возвратно-поступательные движения, а механизмы каждый раз реверсируются. Так работа механизма подъема состоит из процессов подъема и опускания груза, процессов подъема и опускания порожнего грузозахватного приспособления. Работа механизмов поворота и передвижения состоит из движений в одну и другую сторону, как с грузом, так и без него. Так же имеются периоды пауз, в течение которых двигатель не включен и механизм не работает. Время пауз используется для загрузки и разгрузки грузозахватного устройства и для подготовки проведения следующего процесса работы механизма.
Виды и режимы нагружения грузоподъемных машин, их механизмов.
Строй-Техника.ру
Строительные машины и оборудование, справочник
Пользовательский поиск
Характеристики грузоподъемных машин
Категория:
Подъемно-транспортные машины
Характеристики грузоподъемных машин
Далее: Расчетные нагрузки грузоподъемных машин
Грузоподъемные машины характеризуются грузоподъемностью, скоростями движения отдельных механизмов и режимом работы. Грузоподъемностью машины называют вес номинального (максимального) рабочего груза, на подъем которого рассчитана машина. В величину грузоподъемности включаются веса сменных грузозахватных приспособлений, вспомогательных устройств, подвешиваемых к грузозахватному органу, а для грузоподъемных машин, работающих с грейфером, электромагнитом, кюбелем, бадьей, — также и их вес. Величина грузоподъемности современных грузоподъемных машин имеет весьма широкие пределы, имеются устройства для подъема и установки на станки деталей весом 50—100 кГ, а также грузоподъемные машины, перемещающие грузы весом 400—800 т, используемые для монтажа тяжелого оборудования (например, монтажные краны на ГЭС).
Величина грузоподъемности должна соответствовать ГОСТ 1575—61 «Ряд грузоподъемностей.
Скорости движения различных механизмов выбираются в зависимости от требований технологического процесса, в котором участвует данная грузоподъемная машина, от характера работы, от типа машины и ее потребной производительности. Соответствующими стандартами установлены нормальные ряды скоростей для различных кранов.
Скорость вращения кранов достигает 3 об/мин, в зависимости от окружной скорости конца стрелы, не превышающей 5—6 м/сек. При необходимости точной установки груза (например, в монтажных кранах) применяют двухскоростные приводы с резко пониженной посадочной скоростью. Выбор скорости движения производится также с учетом величины пути перемещения. При малых путях перемещения назначение высоких скоростей нецелесообразно, так как механизм может не успеть достичь значения установившейся скорости и будет работать только в пусковом и тормозном режимах.
Пролеты кранов также выбирают по стандартам: так, для мостовых кранов они принимаются по ГОСТ 534—69 «Краны мостовые. Пролеты».
Грузоподъемные машины характеризуются работой в повторно-кратковременном режиме, при котором рабочий орган и груз совершают периодические поступательно-возвратные движения, а механизмы последовательно реверсируются. Так, работа механизма подъема состоит из процессов подъема и опускания груза, подъема и опускания порожнего грузозахватного приспособления. Работа механизмов поворота и передвижения состоит из движений в одну и другую сторону как с грузом, так и без груза.
Кроме периодов работы механизма, имеются периоды пауз, в течение которых двигатель не включен и механизм не работает. Это время используется для загрузки и разгрузки грузозахватного устройства и для подготовки проведения следующего процесса работы механизма. Кроме того, каждый процесс движения, в свою очередь, можно разделить на период неустановившегося движения, в течение которого происходит разгон (период пуска) или замедление (период торможения) поступательно движущихся и вращающихся масс груза и механизма, а также период движения с постоянной скоростью (период установившегося движения).
Для определения требуемого количества цеховых подъемных устройств подсчитывают среднюю производительность за год, исходя из средних нагрузок, средних длин перемещения, средних скоростей движения.
Заданную производительность крана (в т/ч) можно достигнуть путем различного сочетания числа циклов в час и грузоподъемности (в т). С увеличением числа циклов за счет увеличения скорости можно взять кран меньшей грузоподъемности, а следовательно, меньшего веса и стоимости. Однако надо иметь в виду, что увеличение скорости приводит к возрастанию мощности двигателей.
Согласно правилам Госгортехнадзора, установлены следующие работы грузоподъемных машин, определяемые совокупностью условии их эксплуатации:
— Режим Л — механизмы с машинным приводом легкого режима работы, характеризуемые большими перерывами в работе, редкой работой с номинальным грузом, малыми скоростями, малым числом включений в час (до 60), малой относительной продолжительностью включения. К этой группе относятся механизмы подъема и передвижения ремонтных кранов и кранов, работающих в машинных залах, механизмы передвижения строительных и портальных кранов, перегрузочных мостов и башен кабельных кранов, лебедки противоугонных захватов и другие редко работающие механизмы
— Режим С -— механизмы с машинным приводом среднего режима работы, характеризуемые работой с грузами различной величины, средними скоростями, средним числом включений в час (до 120), средним значением относительной продолжительности включения К этой группе относятся механизмы подъема и передвижения кранов механических и сборочных цехов заводов со среднесерийным производством и кранов ремонтно-механических цехов, механизмы поворота строительных кранов, электротали, механизмы монтажных кранов на строительстве.
— Режим Т — механизмы с машинным приводом тяжелого режима работы, характеризуемые постоянной работой с грузами, близкими по весу к номинальным, высокими скоростями, большим числом включений в час (до 240), высоким значением относительной продолжительности включения. К этой группе относятся все механизмы технологических кранов цехов и складов на заводах с крупносерийным производством, кранов литейных цехов и механизмы подъема строительных кранов.
— Режим ВТ — механизмы с машинным приводом весьма тяжелого режима работы, характеризуемые постоянной работой с грузами номинального веса, высокими скоростями, высоким значением относительной продолжительности включения, большим числом включений в час (свыше 240). К этой группе относятся механизмы технологических кранов металлургического производства, механизмы подъема и передвижения тележек, рудных и угольных перегружателей, механизмы грейферных, магнитных и складских кранов металлургических заводов. Работа этих кранов определяет устойчивость нормального ритма технологического процесса.
Различные механизмы грузоподъемных кранов могут работать в различном режиме работы. Режим работы для всей грузоподъемной машины устанавливается по режиму работы механизма главного подъема груза. По этому же режиму рассчитывается и металлоконструкция крана.
Расчет на прочность узлов и деталей механизмов грузоподъемных машин производится подействительному режиму их работы В зависимости от режима работы механизма проводится расчет его двигателя и тормоза, определяются нагрузки, учитываемые при расчете элементов механизма, и нагрузки, вызываемые работой этого механизма, действующие на металлоконструкции, запасы прочности, а также сроки ужоы отдельных элементов и узлов механизма.
Режим работы грузоподъемной машины определяет основные нормативные данные (запасы прочности, запасы торможения, сроки службы и т. п.), принимаемые при расчете основных деталей и узлов этой машины
Простейшие подъемные механизмы
Простые подъемные механизмы и принцип их работы.
Приспособления, служащие для преобразования силы, называют простыми
механизмами.
Классические расчеты действия простых механизмов принадлежат
выдающемуся античному механику Архимеду из Сиракуз. Еще древним
было известно правило, применимое не только к рычагу, но и ко всем
механизмам: во сколько раз механизм дает выигрыш в силе, во столько же
раз получается проигрыш в расстоянии. Этот закон получил название
"золотого правила" механики.
В большинстве случаев простые механизмы применяют для того, чтобы
получить выигрыш в силе, то есть увеличить силу, действующую на тело, в
несколько раз.
К простым подъемным механизмам относят рычаг, блок, лебедку, таль.
1. Рычаг - простейшее механическое устройство, представляющее собой
твёрдое тело (перекладину), вращающееся вокруг точки опоры.
Кратчайшее расстояние между точкой опоры и прямой, вдоль которой
действует на рычаг сила, называется плечом силы.
Чтобы найти плечо силы, надо из точки опоры опустить перпендикуляр на
линию действия силы. Длина этого перпендикуляра и будет плечом данной
силы.
F1, F2 - силы, действующие на рычаг.
L1 L2 - плечи сил, действующих на рычаг.
Рычаг находится в равновесии тогда, когда силы, действующие на него,
обратно пропорциональны плечам этих сил.
Это правило можно записать в виде формулы.
F1 / F2 = L1 / L2
2. Блок - простой механизм для подъема груза, позволяющий изменять
прикладываемую силу по направлению (неподвижный блок), или по
величине (подвижный блок).
Представляет собой колесо с жёлобом по окружности, вращающееся вокруг
своей оси.
3. Лебедка - механизм, тяговое усилие которого передается посредством
каната, цепи или иного гибкого элемента от приводного барабана.
Лебедка предназначена для производства подъемно-транспортных операций
при строительных, монтажных и других работах, также для комплектации
строительной подъемной техники, буровых установок, мачтовых
подъемников, бетономешалок различного типа. Существуют разные виды
лебедок: ручные, монтажные, механические, электрические, грузовые и
другие виды.
Лебедка ручная барабанная (Brano, Чехия)
Электролебедка ТЛ-12А
Электролебедки предназначены для проведения сложных подъемнотранспортных операций при строительных, монтажных и других работах, а
также для комплектации строительных подъемных устройств с питанием от
сети 220 В (380 В под заказ).
Лебедка не предназначена для подъема людей.
4. Таль - подвесное грузоподъемное устройство с ручным или механическим
приводом, состоящее подвижного и неподвижного блоков и основанного в их
шкивах троса (лопаря).
По числу шкивов в обоих блоках различают двух-, трех-, четырех-, шестивосьми-, десяти- и двенадцати шкивные тали. Каждый шкив в
подтягивающемся блоке дает выигрыш в силе в два раза.
Тали используются:
- как самостоятельные грузоподъемные устройства в цехах промышленных
предприятий, на судах и т.п., а также
- как механизмы подъема в однобалочных мостовых подъемных кранах,
настенных консольных передвижных и стационарных кранах и
монорельсовых грузовых тележках.
Таль ручная шестеренчатая модель TB.
Таль ручная рычажная модель HLB.
Таль электрическая модель КХ - это модификация подвесной лебедки
модели РА, оснащенной тележкой передвижения (кареткой), что увеличивает
область применения подвесной лебедки, поскольку груз можно не только
поднимать и опускать, но и перемещать в горизонтальном направлении.
Грузоподъемные машины стрелового типа.
Кран грузоподъемный - грузоподъемная машина, оснащенная стационарно установленными грузоподъемными механизмами. Классификация грузоподъемных кранов в виде схемы приведена на рис. 1.1
В соответствии с федеральным законом от 21.07.97 № 116-ФЗ «О промышленной безопасности опасных производственных объектов» предприятия, цехи, площадки, на которых используются стационарно установленные грузоподъемные механизмы, относятся к категории опасных
Кран короткобазовый
Рис. 1.1. Классификация грузоподъемных кранов
производственных объектов.
Рис. 1.2. Грузоподъемные краны
Кран мостового типа - это кран, у которого грузозахватный орган подвешен к грузовой тележке, перемещающейся по мосту. К этому типу относятся мостовые (рис. 1.2) и козловые краны.
Кран кабельного типа - это кран, у которого грузозахватный орган подвешен к грузовой тележке, перемещающейся по несущим канатам. К этому типу относят кабельные краны.
Кран стрелового типа - это кран, у которого грузозахватный орган подвешен к стреле или к грузовой тележке, перемещающейся по стреле.
Кран портальный - это кран поворотный на портале, предназначенном для пропуска железнодорожного или автомобильного транспорта.
Кран башенный - это кран поворотный, со стрелой, закрепленной в верхней части вертикально расположенной башни.
Кран стреловой - это кран поворотный, у которого стрела закреплена на поворотной платформе, размещенной непосредственно на ходовом устройстве (автомобильный, пневмоколесный, гусеничный и т. п.).
Кран железнодорожный - это кран, смонтированный на платформе, передвигающейся по железнодорожному пути. Железнодорожные краны похожи по устройству на стреловые.
Кран консольный — это кран стрелового типа, грузозахватный орган которого подвешен к жестко закрепленной консоли (стреле) или тележке, перемещающейся по консоли. На машиностроительных и ремонтных предприятиях широко применяются консольные поворотные краны на колонне.
Основные параметры кранов
1. Грузоподъемность т - наибольшая масса груза, на подъем и перемещение которого кран рассчитан в заданном режиме работы (рис. 1.3). В соответствии с международными стандартами в приложении 2 Правил указаны следующие виды грузоподъемности: грузоподъемность полезная mп = масса груза; грузоподъемность нетто mн = mп + масса съемных грузозахватных приспособлений; грузоподъемность полезная mп = масса груза; грузоподъемность миди mM = тп + масса несъемных грузозахватных приспособлений; грузоподъемность брутто тб = тм + масса подъемного средства (канаты, цепи)
Грузоподъемные машины мостового типа.
Все про устройство мостового крана: от грузовой тележки до электрооборудования
В 80-е годы в СССР ежегодно производилось 6-7 тысяч подъемных кранов мостового типа. В 2000-е годы их выпуск в России сократился до 1000-1500 единиц техники.
Несложное устройство мостового крана позволяет широко использовать грузоподъемные машины (ГПМ) этого типа на разномасштабных предприятиях — от маленьких автомастерских до больших металлургических комбинатов или ТЭЦ.
Содержание:
1 Классификация
2 Два способа опирания на крановый путь
3 Конструкция мостового крана
4 Тип привода мостового ГПМ
5 Из чего состоит мостовой кран?
5.1 Тормозная система
5.2 Подъемные механизмы
5.3 Редуктор мостового крана, его назначение и устройство
5.4 Подкрановые пути мостовых кранов
5.5 Электрообрудование
5.6 Устройство крановой тележки мостового крана
6 Схема управления мостовым краном
7 Монтаж мостового крана
8 Фото разных моделей
9 Подробное видео о мостовом кране
Классификация
img_002
Используются мостовые краны для того, чтобы поднимать и перемещать тяжелые грузы больших размеров во всех сферах промышленной деятельности человека.
Технические характеристики мостовых кранов разрешают применять эту категорию ГПМ как для внутренней погрузки-разгрузки, так и для наружных работ в любых климатических условиях.
Недостаток мостовых ГПМ — в их стационарности, а плюс — в том, что они могут использовать строительную высоту здания.
Мостовые ГПМ делятся на 2 большие группы: общего назначения и специальные.
Мостовые ОПИ (общепромышленного исполнения) оборудованы грузовым крюком.
Специальные — оснащаются захватами, имеющими узкоспециализированное назначение: грейфер, магнит, захваты для контейнеров. Подъемники спец. назначения производят с поворотной тележкой или стрелой.
В отдельную группу выделяют металлургические ГПМ, предназначенные только для данной отрасли промышленности. Оснащаются такие ГПМ спец. захватами: литейными, ковочными, для раздевания слитков и др.
Два способа опирания на крановый путь
img_011
У двутавровой пролетной балки есть верхний и нижний горизонтальные пояса. На верхний размещают опорные, а под нижний крепятся подвесные:
Опорные — устанавливаются колесами на рельсы сверху. Грузоподъемность опорных ГПМ — максимальна (до 500т), но постройка подкрановой эстакады или опор требует финансовых затрат.
Подвесные — подцепляются к нижним полкам кранового пути. Этот вид опирания прост в монтаже и имеет невысокую стоимость. Небольшая грузоподъемность (до 8т) окупается малой высотой конструкции, из-за чего размер рабочей зоны больше, чем у опорных кранов.
Подвесные краны можно установить на часть цеха. Есть возможность стыковать краны (стыковой замок) и перемещать тележки с одного крана на другой.
Конструкции устройства бывают разными. Они могут двигаться поступательно или совершать обороты вокруг вертикальной оси (хордовые, радиальные и поворотные) ГПМ.
Конструкция мостового крана
По количеству главных балок конструкция ГПМ бывает:
img_006
однобалочная. Используется на небольших производствах, может быть подвесным или опорным. Г/п <= 10 т.
Двухбалочная. Конструкция выполняется только в опорном варианте, т.к. их грузоподъемность > 8 т.
Использование — в больших производственных цехах, в автомобильной, металлургической промышленности. Длина пролета — до 60м. Грузовая тележка может иметь вспомогательный грузоподъемный механизм помимо основного.
Тип привода мостового ГПМ
img_008
Привод механизмов у мостовых ГПМ может быть ручным или электрическим.
Ручной привод. У этого мостового крана механизмом передвижения служат червячные тали.
Используют ручные ГПМ для подъема относительно небольших грузов, при производстве вспомогательных или ремонтных работ.
Электропривод. Электрические тельферы служат в качестве устройств подъема и перемещения грузов. Мост ГПМ движется тоже с помощью электродвигателей, они передают вращение ходовым колесам либо через редукторы, либо через редуктор и трансмиссию.
1. Классификация грузозахватных приспособлений; Требования правил Ростехнадзора к грузозахватным устройствам.
Съемные грузозахватные приспособления относятся к разряду наиболее ответственных устройств, на которые распространяются требования правил безопасности и нормативных документов Ростехнадзора.
Изготовление и ремонт съемных грузозахватных приспособлений производится специализированными предприятиями в соответствии с нормативными документами, техническими условиями и технологическими картами.
Грузозахватные приспособления после изготовления и ремонта испытываются нагрузкой на 25% выше их паспортной грузоподъемности. Все грузозахватные приспособления, находящиеся в эксплуатации, должны иметь паспорт и клеймо или прочно прикрепленную металлическую бирку, с указанием: номера, грузоподъемности и даты испытания (месяц, год).
Съемные грузозахватные приспособления должны содержаться в исправном состоянии и обеспечивать безопасные условия работы путем организации необходимого осмотра, ремонта, надзора и обслуживания, согласно требованиям правил безопасности.
Осмотр съемных грузозахватных приспособлений должен проводиться в соответствии с требованиями Инструкции по эксплуатации стропов, определяющей порядок и методы осмотра, браковочные признаки, а так же методы устранения обнаруженных дефектов.
Для осмотра стропов, находящихся в эксплуатации, начальник структурного подразделения из числа ИТР подразделения должен назначить приказом ответственного по надзору за безопасной эксплуатацией подъемных сооружений, съемных грузозахватных приспособлений и стропов.
Лицо, ответственное за контроль состояния стропов, должно быть обучено и аттестовано в установленном порядке.
Согласно требованиям правил безопасности, стропальщики должны производить осмотр съемных грузозахватных приспособлений перед их применением, а ИТР и лица, ответственные за безопасное производство работ грузоподъемными машинами, должны производить их осмотр с записью в журнале учета и осмотра, в следующие сроки:
- стропы и мягкие полотенца - каждые 10 дней:
- траверсы, захваты и тара - каждый месяц;
- редко используемые грузозахватные приспособления - перед выдачей их в работу.
При осмотре съемных грузозахватных приспособлений необходимо обращать внимание на состояние канатов, крюков, замыкающих устройств, карабинов и места их крепления, на сварные соединения, на состояние рабочих поверхностей, при этом, для оценки безопасности их использования, необходимо применять установленные правилами определенные критерии браковки.
При эксплуатации стропов запрещается:
- эксплуатация стропов, гибкие элементы, звенья и захватные органы которых достигли браковочного признака хотя бы по одному показателю;
- подъем и перемещение грузов с отклонением гибкого элемента стропа от плоскости захватного органа стропа, создающим боковой изгиб захватного органа;
- зацеп груза за рог крюка стропа;
- завязывать гибкие элементы стропа узлами;
- эксплуатация стропов, не имеющих маркировочные бирки;
- эксплуатация одно и многоветвевых стропов, не имеющих паспорта;
- эксплуатация стропов, с крюками у которых изготовителем предусмотрены предохранительные замки, без предохранительных замков.
Признаками браковки стропов из стальных круглопрядных и плоских канатов являются:
- наличие на любой ветви стропа шести и более обрывов наружных проволок каната на участке длиной равной шести шагам свивки каната;
- наличие на любой ветви стропа трех и более обрывов наружных проволок каната на одной пряди каната или в петле стропа;
- разрыв одной пряди каната любой ветви стропа;
- уменьшение диаметра проволок каната на 30% и более на любой ветви стропа, из-за поверхностного износа и коррозии проволок каната;
- необратимые деформации каната любой ветви стропа, такие как волнистость, местное уменьшение диаметра или толщины каната, выдавливание металлического сердечника на поверхность каната, выдавливание проволок каната на его поверхность, раздавливание и перекручивание каната, местный залом и перегиб каната,
- изменение цвета проволок, вследствие воздействия повышенной температуры окружающей среды или электрического тока.
Признаками браковки стропов ленточных и синтетических круглых, а также волокнистых канатов являются:
- поперечные или продольные разрезы, разрывы ленты и каната;
- местные расслоения по ширине ленты на суммарной длине 500мм и более;
- местные расслоения по краям ленты на длине 200мм и более;
- разрыв трех и более строчек шва;
- поверхностные обрывы нитей ленты общей длиной 10% и более от ширины ленты;
- обрыв 6 и более каболок или проволок волокнистого каната;
- поверхностный износ каната, ленты или чехла на 10% и более от первоначальных размеров;
- наличие узла связки на ветви стропа;
- выпучивание нитей ленты или прядей волокнистого каната на их поверхность;
- не отмываемые загрязнения (нефтепродуктами, смолами, красками и т.п.) на длине 50% и более от общей длины ленты, волокнистого каната.
Стропы грузовые ремонту не подлежат.
1. Крюки используемые в ГПМ. Типы. Материалы. Требования
Крюк крана. Типы, назначение
18.02.2013 | Автор: Дмитрий Николаевич
Не так давно я писал о грузозахватных приспособлениях. При написании той статьи появилось достаточно много вопросов, которые стоит уточнить. Сегодня постараюсь описать такую незаменимую в перемещении грузов вещь, как крюк подъемного крана.
Крюк крана
Ни один кран, будь то башенный кран или автоманипулятор самогруз, невозможно представить без крюка. Крюк — один из основных грузозахватных приспособлений для грузоподъемных машин.
Как и ранее, начнем с базовых элементов и перейдем к более сложным.
Материал крюка
А, собственно, из чего делают крюк крановой? Если говорить в общем, то из металла. Различают литые, кованные и пластинчатые крюки. Отличия заключаются в весе, цене и надежности. Литые крюки стараются не использовать по причине возможных скрытых дефектов и полостей. Хотя для небольших работ и они подойдут, так как цена крюка в данном случае будет низка из-за дешевизны материала и относительной простоты изготовления.
Назначение крюка
Вообще крюк используют для быстрого соединения и рассоединения грузового крана с грузом. Простейшим способом использования можно назвать соединение крюка напрямую к основному тросу крана и грузу. Какие проблемы могут возникнуть при этом?
Крюк крана подгруженыйВо-первых, вес крюка может быть недостаточен. Простые краны, а вернее их механизм выпуска троса, рассчитаны на «самотёк». Т.е. бобина с тросом может разматываться только под воздействием груза. Данную проблему можно решить, выбрав более массивный крюк либо подвесив небольшой дополнительный груз на канат. Параметр «самотёка» троса нужно смотреть в спецификации к крану.
Во-вторых, существуют грузы, которые необходимо перемещать в определенном положении. Например, лестничный пролет при строительстве высотного дома. Такие грузы требуют многоточечного захвата. В этом случае уже необходимо использование строп. На концах этих строп крепятся чалочные крюки. Т.е. одновременно на одном кране используются несколько крюков. Для распределения нагрузки зачастую используют двурогий крюк.
В-третьих, стальной канат крана вещь, плохо поддающаяся рукам человека. Изменить угол стыка крюка и груза зачастую крайне сложно. И тут мы переходим к следующему пункту:
Типы крепления крюка
У базового крюка сверху располагается ухо. В него продевается канат. Если же у вас цепь, то нужно использовать вилочное соединение крюка.
Для удобства зачастую необходимо использовать вертлюг. это верхняя часть крюка которая свободно крутиться вокруг своей оси значительно упрощая работу стропальщика.
Есть еще крайние варианты. Например «S»-образный крюк. Он имеет идентичные верхнюю и нижнюю части.
Типы крюков
Теперь более детально рассмотрим нижнюю часть подъемного крюка. Как я уже рассказывал, кроме стандартного однорогового крюка существуют двурогие, которые используются для более стабильной транспортировки грузов.
Типы крюков
Крюк с широким зевом редко используется, но бывает незаменим, когда проушины груза имеют нестандартные габариты. Обычно крюки с широким зевом или с большим загибом крюка не имеют замка или серьги. И тут мы переходим к следующему пункту.
Замок крюка
Вещь крайне необходимая не только с точки зрения сохранности груза, но с точки зрения ГОСТов и безопасности труда. Крюк без какого-нибудь предохранителя самопроизвольного отсоединения груза используется только в случае крюка с большим зевом и только если груз не перемещается над людьми. Во всех остальных случаях замок необходим.
Отдельно стоит заметить, что крюковые приспособления используются не только для кранов. Существуют приварные крюки, которые привариваются к ковшу экскаватора. Последний в этом случае может поднимать и перемещать грузы как манипулятор.
1. Грейфер. Типы грейферов.
Грейферы: описание, назначение и разновидности
Грейфер - приспособление, предназначенное для извлечения и погрузки навалочных (сыпучих, пылевидных, кусковых) и штучных грузов. Говоря о грейферах, выделяют два основных типа, принципиально отличных по назначению. К первому типу относят грейферные ковши, основная цель которых - копание грунта. Ко второму - грейферные захваты, предназначенные для осуществления погрузочно-разгрузочных работ.
Грейферами оснащаются грузоподъемные механизмы и копательная техника, такая как, подъемные краны и экскаваторы, на крюк или стрелу которых навешивается грейферный механизм, расширяя область их применимости. Конструктивная особенность грейферного ковша, состоящего из пары смыкающихся челюстей, позволяет работать "в глубину" без расширения границ копаемой области. Это нашло широкое применение в рытье (чистке) колодцев и бурении скважин.
Грейферные механизмы применяются также при подводной добыче строительных материалов и полезных ископаемых. Водные суда, оборудованные краном с грейферным ковшом, используются для добычи песка, гравия, руды со дна рек, озер, морей и океанов.
Иное назначение имеет погрузочный грейфер, конкретная конструкция которого зависит от типа перемещаемого груза. Для погрузки сыпучих материалов захватывающие элементы грейфера исполняются в виде лопастей, имеющих (в сомкнутом виде) ковшеобразную форму. Челюсти для захвата леса, труб и других продолговатых предметов цилиндрической формы, имеют клещевидную форму. Щупальцеобразный захват идеально подходит для взятия плотных крупнокусковых грузов (металлолома, крупного бытового мусора и др.).
Управление грейферным устройством заключается в выполнении двух действий: перемещение самого устройства и манипуляция его челюстями. В зависимости от кинематики управления выделяют два вида грейферов: канатные и приводные (моторные).
классификация грейферов по типу привода
Канатные грейферы
Канатный грейфер приводится в движение одним или несколькими приводными барабанами с намотанными на них управляющими тросами. Лебедки, в состав которых входят эти барабаны, размещаются на подъемном механизме, на крюк которого подвешивается грейфер. По числу управляющих канатов различают одноканатные и многоканатные грейферы. Последние, в свою очередь, подразделяются на двух-, трех- и четырехканатные.
Качество копания канатного грейфера, напрямую зависит от его массы и скорости смыкания челюстей, которая, в свою очередь, зависит от скорости вращения приводного барабана. Слишком быстрое вращение приводит к неэффективному захвату по причине того, что челюсти ковша не успевают углубиться в копаемый материал. Это проблема всех облегченных канатных грейферов – слишком малый вес не обеспечивает достаточной прижимной силы, что особенно критично при разработке плотного грунта.
Одноканатный грейфер
схема одноканатного грейфера
Управление данным типом грейферов осуществляется при помощи единственного каната, ответственного как за подъем, так и за замыкание челюстей. Главное преимущество заключается в том, что использовать его могут подъемные устройства, обладающие всего одной лебедкой. Одноканатный грейфер не требует сложной установки – его достаточно подвесить на крюк за прикрепленную к нему скобу и - он готов к работе. Указанные достоинства объясняют его популярность: он прост в эксплуатации и незаменим при проведении работ, требующих частой смены копательных насадок.
Общий принцип работы классического одноканатного грейфера заключается в следующем. Каждая челюсть ковша шарнирно соединена с нижней и верхней траверсами (опорными основаниями). Сближение траверс друг с другом приводит к смыканию челюстей, а удаление - к размыканию. Нижняя траверса грейфера является подвижной, следовательно, для сближения ее с верхней, предусмотрен специальный запорный механизм, состоящий из подвижной головки, напрямую или через полиспаст соединенную с подъемной лебедкой, и зацепного элемента (например, крюка), крепящегося к нижнему основанию. Поднимание головки, сцепленной с нижней траверсой посредством образуемого замка, приводит к сведению верхней и нижней опорных частей грейферного ковша и, как следствие, замыканию челюстей. Раскрытие челюстей осуществляется под действием собственного веса, при условии открытого запорного устройства.
Полный цикл работы одноканатного грейфера состоит из следующих этапов:
Опускание. Лебедка подъемного механизма работает на спуск. Грейфер с полностью раскрытыми челюстями опускается на рабочую поверхность до упора. Зачастую ковш не просто опускают, а практически "бросают", что приводит к более глубокому внедрению челюстей в материал. Такая техника позволяет эффективнее загребать плотные породы.
Захват. Замочный механизм защелкивается, и лебедка начинает работать на подъем, что приводит к постепенному смыканию челюстей и захвату материала.
Подъем. Когда челюсти полностью смыкаются, барабан подъемной лебедки продолжает наматывать трос, что приводит к отрыву грейферного ковша от поверхности и его дальнейшему подъему на необходимую высоту.
Выгрузка. Перемещенный на место выгрузки ковш опускается на поверхность, что приводит к открыванию замка. Дальнейший подъем ковша приводит к его распахиванию - груз высыпается, и полностью раскрытый ковш готов к следующей загрузке.
процесс работы одноканатного грефера
Основной недостаток, присущий одноканатному грейферу, - раскрытие замка происходит после полного опускания ковша в момент его контакта с поверхностью. Это снижает эффективность выполняемой работы. Избежать этого помогает специальный разгрузочный тросик, который принудительно снимает блокировку замка независимо от того, на какой высоте находится ковш. Данное техническое решение значительно ускоряет процедуру разгрузки, однако приводит к очень громкому удару головки о верхнюю траверсу в момент раскрытия захвата.
Для предотвращения раскачивания грейферного захвата используют стабилизирующие тросы.
Двухканатный грейфер
схема двухканатного грейфера
Для манипуляции данными видами грейферов используют два независимых барабанных привода. Первый отвечает за вертикальное перемещение ковша, второй - за работу челюстей. Использование двухканатной системы снижает износ тросов, что повышает надежность эксплуатации всей конструкции.
Цикл работы двухканатного грейфера несколько отличается от одноканатного:
Опускание. В момент снижения поддерживающий трос движется на спуск, а трос, управляющий смыканием челюстей, ослаблен. Челюсти находятся в полностью открытом состоянии.
Захват. После соприкосновения челюстей с рабочей поверхностью поддерживающий трос останавливается, а челюстно-управляющий - начинает движение вверх, обеспечивая сбор материала смыканием челюстей.
Подъем. В момент полного схлопывания челюстей управляющий трос не останавливается - происходит подъем ковша. Для снижения нагрузки на манипулирующий челюстями трос подключается второй, поддерживающий. Таким образом, нагрузка между ними распределяется поровну. Основные проблемы заключается в их синхронизации: барабанные приводы не всегда имеют одинаковую скорость вращения, а уловить момент включения поддерживающего барабана вручную, является искусством. С этой целью применяются разного рода синхронизационные устройства, автоматизирующие процесс подъема.
Выгрузка. Открытие висящего на определенной высоте ковша производится ослаблением челюстно-манипуляторного троса, барабан которого раскручивается до полного раскрывания челюстных зажимов. После выгрузки грейферный захват готов к новому циклу работы.
процесс работы двухканатного грефера
Трехканатные и четырехканатные грейферы
С принципиальной точки зрения, функционирование трех- и четырехканатных захватов не отличается от двухканатных. Разница лишь в количестве дополнительных тросов. В трехканатном - один канат поддерживает, а два - управляют челюстями, причем синхронно. В четырехканатном - одна пара канатов - поддерживающая, вторая - управляющая. Использование конструкций с дополнительными тросами позволяет повысить грузоподъемность и мощность грейферных захватов.
Приведенные схемы грейферов носят упрощенных характер. Для усиления эффективности эксплуатационных характеристик грейфера их базовая конструкция дополняется полезными механизмами. Так, интеграция полиспаста - системы из подвижных и неподвижных блоков с огибающим их тросом - дает выигрыш в силовых и скоростных характеристиках применяемого захвата.
Приводные грейферы
Управление челюстями данного вида механизмов реализуется посредством отдельного привода, который передает силовое усилие с электрического или дизельного мотора на исполнительные элементы. С целью подчеркнуть существование отдельного двигателя, ответственного за управление приводом, приводные грейферы часто называют моторными.
Двигатель, усилие с которого передается на челюсти посредством привода, может являться частью конструкции грейфера или размещаться за ее пределами, на подъемно-погрузочном механизме. В последнем случает, в зависимости от привода, к управляющему механизму грейфера должны дополнительно подводиться шланги или кабели.
По типу привода выделяются следующие типы грейферных захватов:
электромеханические
гидравлические
пневматические
электромагнитные
В электромеханическом приводном грейфере рабочее усилие, вырабатываемое электрическим двигателем, передается на челюстные захваты при помощи зубчатого, редукторного, ременного, винтового или другого передаточного механизма. Простые, но надежные, захваты оснащаются электрической талью - электромотором с полиспастом, подвижный блок которого в сочетании с шарнирной системой челюстей координирует работу последних.
схема гидравлического секторного привода
Гидравлические грейферы оснащаются гидроцилиндрами и системой подводящих шлангов. Насосное оборудование, служащее для нагнетания жидкости в цилиндры, не является частью конструкции гидравлического типа. Это следует четко понимать. Если насос установлен непосредственно в грейфере с системой цилиндров, то привод такого механизма будет называться электрогидравлическим.
Устройство пневматического грейфера, по сути, не отличаются от гидравлического, за исключением того, что вместо жидкости используется сжатый воздух, нагнетаемый воздушным насосом (компрессором).
схема электромагнитного захвата
В основе функционирования электромагнитного грейфера лежит явление возникновения магнитного поля под действием электрического тока. Напряжение, приложенное к катушкам возбуждения, заставляет подвижный магнитопровод сблизиться с корпусом и сомкнуть челюсти. Образуемый от двух катушек магнитный поток порождает единое магнитное поле, отвечающее за притяжение ферромагнитных материалов к электромагниту. Кроме того, возникающий магнитный эффект усиливает "хватательные" характеристики захвата - мелкая металлическая стружка и другие мелкокусковые предметы, являющиеся ферромагнетиками, не высыпаются из ковша при его перемещении, что повышает объем удерживаемого груза. Опорожнение ковша производится прекращением подачи напряжения на катушки магнитопроводов. Челюсти под действием собственного веса размыкаются - и груз вываливается.
Классификации грейферов по типу челюстей
схема многочелюстного грейферного захвата
Как было упомянуто выше, захватывающие элементы грейфера называются челюстями. Их количество варьируется от двух до восьми. Форма челюстей во многом определяет, с какими грузами способен работать захват. Ковшеобразные грейферы нередко используются для проведения копательных работ и добыче ископаемых. С целью улучшения черпающих характеристик режущие кромки ковша дополняются заостренными зубьями. Клещеобразные захваты удобны для погрузки круглого леса, трубных изделий и других цилиндрических объектов продолговатой формы. Вильчатые грейферы находят свое применение как оборудование сельскохозяйственного предназначения. Они незаменимы для высокопроизводительной погрузки сена, соломы, силоса и прочих волокнистых материалов, как в рулонном, так и рассыпном виде.
лесозахватный клещевой грейфер
Сыпучие, мелкокусковые и склонные к высыпанию (вытеканию) грузы перегружаются при помощи закрытого или полузакрытого грейферного ковша. Остальные типы грузов обрабатываются открытыми грейферами, лопасти которых при смыкании не образуют сплошной поверхности.
Отдельно стоит заострить внимание на траектории движения челюстного захвата. У копательных устройств челюсти смыкаются по "роющей " траектории, позволяя тем самым глубже внедряться в разрабатываемый грунт. Лопасти, двигающиеся по подгребающей траектории, наоборот, не должны врезаться в материал. Их основная задача - сгребать сыпучие и мелкокусковые грузы, послойно лежащие на поверхности. Отсюда и назначение у них совсем иное - погрузочное.
При проведении работ в ограниченном пространстве, например, при рытье колодца или скважины, важен такой параметр как максимальный размах челюстей грейфера. Чем меньше общая ширина размаха, тем лучше. В идеале: ширина размаха должна совпадать с шириной копания. На сегодняшний день, существуют грейферные модели с неизменяемой шириной размаха, обеспечиваемой благодаря кинематической схеме движения челюстей по фиксированным направляющим.
При копании и погрузке неоднородных по твердости пород предусмотрены грейферы с независимым смыканием челюстей. Классический вариант, когда конструкция привода предполагает одновременное равномерное закрывание всех челюстей, терпит в данном случае неудачу. Если одна из челюстей во время смыкания встречает на своем пути сопротивление и останавливается, то это блокирует работу остальных. Независимое (поочередное) челюстное схождение решает возникающую проблему. Это реализуется путем интеграции пружинных механизмов в тягу каждой челюсти, приводящих к перераспределению усилий на элементы грейфера с целью более плотного обхватывания груза.
Встречаются грейферные захваты, имеющие индивидуальный привод каждой челюсти. Отдельное исполнительное устройство на каждую "клешню" позволяет в существенной мере повысить ее мощность. Более того, это решает проблему неравномерного смыкания, описанную выше.
общий и индивидуальный привод
Вращение грейфера вокруг своей оси осуществляется за счет роторной установки. Оснащение подъемно-погрузочного механизма ротатором позволяет захватывать грузы из любого положения, что особенно актуально при подъеме контейнеров и емкостей, имеющих строго определенные места захвата.
классификация грейферов по типу челюстей
Основные характеристики грейферов:
Емкость (куб. м)
Грузоподъемность (кг)
Габаритные размеры (в открытом и закрытом состоянии) (мм)
Порожняя масса (кг)
Тип привода
Количество челюстей
Тип груза
Плотность груза (для копающих)
Мощность двигателя (для электроприводных)
Число канатов (для канатных)
Диаметр каната (для канатных)
4000
1. Общие требования к тормозам и остановам по правилам Ростехнадзора
Приводы и тормоза
72. Привод должен обеспечивать скорость тягового (несуще-тягового) каната как номинальную, так и пониженную (ревизионную).
73. Пуск привода ГПКД должен осуществляться с пульта управления.
74. Возможность останова привода ГПКД должна осуществляться как с пульта управления, так и от кнопок "СТОП", установленных на каждой станции и от аварийных выключателей "Аварийный стоп". Если для дороги предусмотрено несколько приводных участков, их приводы в режиме дистанционного управления должны быть синхронизированы.
75. Коэффициент запаса сцепления тягового каната с приводным шкивом должен быть не менее 1,1.
76. Приводы должны обеспечивать возможность работы канатной дороги с ревизионной скоростью не более 1 м/с.
77. Приводы должны иметь рабочие тормоза.
78. Приводы с канатоведущим шкивом, канатных ГПКД, на которых возможно самопроизвольное движение тягового или тягонесущего каната, должны иметь дополнительные предохранительные тормоза на валу или на ободе шкива.
79. Тормозной момент каждого тормоза должен быть не менее 1,25 величины статического момента при наиболее тяжелых условиях загрузки дороги.
80. При отключении электроэнергии на ГПКД должны автоматически срабатывать рабочий и предохранительный тормоза.
81. Приводы, предназначенные для работы в тормозном режиме, должны иметь устройства для контроля скорости и обеспечивать автоматическую остановку ГПКД при превышении расчетной скорости на 20 процентов.
82. На ГПКД с маятниковым движением подвижного состава конечные положения вагонетки должны контролироваться автоматически.
83. Привод ГПКД с маятниковым движением подвижного состава должен быть оснащен системой регулирования и контроля скорости с учетом ее снижения при подходе к станции или, когда это необходимо, при переходе через линейные опоры.
84. ГПКД с маятниковым движением подвижного состава должна автоматически останавливаться при возникновении неисправности в системе контроля скорости.
85. Зажимы должны иметь запас надежности не менее 1,5 с учетом возможного уменьшения диаметра каната.
86. Для ГПКД с отцепляющимся подвижным составом должны быть предусмотрены меры по предупреждению покидания станции и выхода на линию вагонеток, закрепленных на канате с отступлением от проектных характеристик.
87. Зоны прохождения ГПКД над железными и автомобильными дорогами, зданиями и сооружениями, пешеходными зонами должны быть оборудованы предохранительными устройствами в виде сетей или мостов, а также щитами с предупреждающими надписями.
Предохранительные устройства должны обеспечивать удержание падающей груженой вагонетки и исключать просыпание транспортируемого груза размером более 20 миллиметров.
88. Ширина предохранительных сетей должна обеспечивать перекрытие предохраняемого пространства на 2 метра в каждую сторону от оси несущего каната (для пролетов свыше 250 метров - от габарита качающейся вагонетки при расчетной ветровой нагрузке). Высота бортов сетей должна быть не менее 1,2 метра.
Длина предохранительных сетей должна приниматься исходя из необходимости перекрытия всего предохраняемого пространства с учетом траектории падения вагонетки или груза.
Ширина предохранительных мостов должна обеспечивать перекрытие пространства на 1,25 м в каждую сторону от оси несущего каната. Высота бортов мостов должна быть не менее 1,8 метра.
89. Провесы канатов предохранительных сетей с учетом статической нагрузки и нагрузки от упавшей вагонетки должны быть в пределах, допускаемых габаритами приближения строений для перекрываемых сетями сооружений.
90. Электрическое оборудование ГПКД должно иметь главный выключатель и дифференциальный автоматический выключатель цепи, способный полностью отключить электропитание.
91. Канатная система должна иметь встроенную цепь аварийного отключения. Кнопки управления цепью аварийного отключения должны быть легко идентифицируемыми. Цепь аварийного отключения должна обеспечивать экстренную остановку ГПКД и предотвращать повторный запуск ГПКД без участия оператора. Повторный запуск ГПКД после устранения причин аварийного отключения должен быть произведен оператором ГПКД вручную. Данная цепь аварийного отключения также должна автоматически активироваться при перебое в электропитании.
92. Сигнал о причине остановки ГПКД должен отображаться на пульте оператора. Сигнал не должен выключаться до тех пор, пока не будет восстановлена полная работоспособность ГПКД.
93. ГПКД должна быть оснащена защитой всех электрических линий, выходящих со станции от превышения проектных параметров.
94. ГПКД должна оснащаться отказоустойчивым программируемым управлением, имеющим функцию показа, хранения записей и документирования всех произошедших происшествий и неисправностей.
95. ГПКД, на которой возможно самопроизвольное движение тягового (несуще-тягового каната), должна иметь встроенную систему слежения за превышением скорости, которая активирует срабатывание предохранительного тормоза привода и размыкает цепь аварийного отключения, как только скорость ГПКД превысит максимально допустимое значение.
96. Включение дифференциальных тормозных систем, а также тормозных систем, активируемых при сбое питания и при аварийной остановке, не должно вызывать избыточное отрицательное ускорение ГПКД.
97. Скорость подвижного состава на входе станции реверсивных канатных дорог должна отслеживаться с помощью устройства, которое активирует цикл отключения питания, если скорость на входе превышает максимально допустимую. Также разрешается использование буферной системы останова подвижного состава.
98. ГПКД с маятниковым движением подвижного состава должны иметь встроенную систему аварийной остановки, которая активируется в случае неисправности рабочего тормоза и должна вызывать срабатывание предохранительного тормоза
1. Канаты стальные. Классификация. Общие требования. Материалы для изготовления канатов.
Канаты стальные. Технические условия на канаты. Настоящий стандарт распространяется на стальные канаты общего назначения. Обязательные требования к качеству канатов, обеспечивающие безопасность для жизни и здоровья населения, изложены в пп. 2.1.10, 2.1.12 (в части допускаемого разбега временного сопротивления разрыву проволок, взятых из каната), 2.1.13, 2.1.14, 3.2, 4.1, 4.10, 4.11, 4.12, 4.13, 4.14. 1. КЛАССИФИКАЦИЯ 1.1. Канаты подразделяются по признакам 1.1.1. По конструкции: одинарной свивки - состоящие из проволок, свитых по спирали в один или несколько концентрических слоев, двойной свивки - состоящие из прядей, свитых в один или несколько концентрических слоев, тройной свивки - состоящие из канатов двойной свивки (стренг), свитых в концентрический слой. 1.1.2. По форме поперечного сечения: круглые, плоские. 1.1.3. По форме поперечного сечения прядей: круглопрядные, фасоннопрядные. 1.1.4. По типу свивки прядей и канатов одинарной свивки: с точечным касанием проволок между слоями - ТК, с линейным касанием проволок между слоями - ЛК, с линейным касанием проволок между слоями при одинаковом диаметре проволок по слоям пряди - ЛК-О, с линейным касанием проволок между слоями при разных диаметрах проволок в наружном слое пряди - ЛК-Р, с линейным касанием проволок между слоями и проволоками заполнения - ЛК-З, с линейным касанием проволок между слоями и имеющих в пряди слои с проволоками разных диаметров и слои с проволоками одинакового диаметра - ЛК-РО, с комбинированным точечно-линейным касанием проволок - ТЛК. 1.1.5. По материалу сердечника: с органическим сердечником из натуральных или синтетических материалов - ОС, с металлическим сердечником - МС. 1.1.6. По способу свивки: нераскручивающиеся - Н, раскручивающиеся. 1.1.7. По степени уравновешенности: рихтованные - Р, нерихтованные. 1.1.8. По направлению свивки каната: правой, левой - Л. Направление свивки каната определяется: для канатов одинарной свивки - направлением свивки проволок наружного слоя, для канатов двойной свивки - направлением свивки прядей наружного слоя, для канатов тройной свивки - направлением свивки стренг в канат. 1.1.9. По сочетанию направлений свивки каната и его элементов в канатах двойной и тройной свивки: крестовой свивки (направление свивки каната и направление свивки стренг и прядей противоположны), односторонней свивки (направление свивки пряди и направление свивки проволоки в пряди одинаковы) - О. 1.1.10. По степени крутимости: крутящиеся (с одинаковым направлением свивки проволок в канатах одинарной свивки, прядей или стренг), малокрутящиеся (многослойные многопрядные и одинарной свивки с противоположным направлением свивки элементов по слоям) - МК. 1.1.11. По механическим свойствам марок ВК, В, 1. 1.1.12. По виду покрытия поверхности проволок в канате: из проволоки без покрытия, из оцинкованной проволоки: в зависимости от поверхностной плотности цинка - С, Ж, ОЖ, покрытие каната или прядей полимерными материалами - П. 1.1.13. По назначению: грузолюдские (марок ВK, В) - ГЛ, грузовые - Г. 1.1.14. По точности изготовления: повышенной - Т, нормальной. Рекомендации по применению канатов приведены в приложении 1. 1.2. Конструкция, основные характеристики и диаметры канатов указываются в соответствующих стандартах на сортамент. 1.3. Диаметр каната, назначение, марка, вид покрытия, направление свивки, сочетание направлений свивки, способ свивки, степень уравновешенности, степень крутимости, точность изготовления, маркировочная группа, обозначение соответствующего стандарта на сортамент указываются потребителем и входят в условное обозначение каната. 2. ТЕХНИЧЕСКИЕ ТРЕБОВАНИЯ 2.1. Характеристики 2.1.1. Стальные канаты и металлические сердечники должны изготовляться из проволоки по ГОСТ 7372. Канаты изготовляются по технологическому регламенту, утвержденному в установленном порядке. 2.1.2. В качестве органических сердечников должны применяться: пеньковые - по ГОСТ 5269, сизалевые - по нормативно-технической документации, синтетические и искусственные материалы - по нормативно-технической документации (полиэтилен, полипропилен, капрон, лавсан, вискоза), пряжа хлопчатобумажная, хлопчатобумажный корд - по нормативно-технической документации. Допускается по согласованию изготовителя с потребителем применение сердечника из других материалов. При отсутствии требований потребителя выбор материала сердечника производится изготовителем. 2.1.3. Сердечники из пенькового и сизалевого волокна, хлопчатобумажной пряжи и корда должны быть пропитаны смазкой по ГОСТ 15037 или смазкой по нормативно-технической документации. По требованию потребителя сердечник не пропитывается. 2.1.4. Канаты из проволоки без покрытия и оцинкованной должны быть смазаны канатными смазками по нормативно-технической документации. По согласованию изготовителя с потребителем допускается нанесение на канат других видов смазки. По требованию потребителя канаты покрываются смазкой Торсиол-55 по ГОСТ 20458. Рекомендации по применению смазки Торсиол-55 приведены в рекомендуемом приложении 1. По требованию потребителя канаты изготовляются несмазанными полностью или с несмазанной наружной поверхностью. 2.1.5. В канате не должно быть западающих, перекрещивающихся и оборванных проволок, западающих прядей. 2.1.6. Диаметры проволок в канатах должны соответствовать требованиям стандартов на сортамент. Допускается уточнение диаметров проволок в пределах до ±0,1 мм. При этом равные диаметры проволок одного слоя изменяются на одинаковую величину. При уточнении диаметра проволоки диаметры канатов не должны выходить за пределы, установленные настоящим стандартом. 2.1.7. Проволоки должны быть соединены стыковой электросваркой или высокотемпературной пайкой. Допускается концы оборванных проволок диаметром 0,55 мм и менее заделывать посредством прошивки через сечение прядей или соединять узлом. При этом допускается местное утолщение и нарушение свивки в месте соединения концов проволоки. В канатах марки 1 на одном метре каната допускается не более двух соединений проволок в разных поперечных сечениях, в канатах марок ВК и В не более одного соединения на расстоянии 10 м. 2.1.8. Канат должен иметь по всей длине равномерный шаг свивки элементов каната. Шаг свивки наружного слоя проволок в прядях должен составлять не более 9 диаметров пряди в канатах линейного касания проволок и 11 диаметров пряди в канатах точечного касания проволок, в трехгранных прядях и однопрядных металлических сердечниках. Шаг свивки проволок в канатах одинарной свивки, а также в канатах и прядях конструкции 1 + 6 должен быть не более 11 диаметров пряди. Шаг свивки канатов должен составлять не более: 6,5 диаметров в трех-, шестипрядных канатах, стренгах канатов тройной свивки и металлических сердечниках; 7 диаметров в канатах с количеством прядей более шести, в канатах тройной свивки и в канатах точечного касания, пряди которых изготовляются в три операции (1 + 6 + 12 + 18); 7,5 диаметров в канатах фасоннопрядных; 16 диаметров в стренгах и прядях плоского каната. По согласованию изготовителя с потребителем допускается шаги свивки наружного слоя проволок в прядях увеличить до 11 диаметров пряди, а каната - до 7 диаметров каната, при этом оптимальное соотношение шагов свивки в указанных пределах определяется в соответствии с методикой, приведенной в рекомендуемом приложении 2. 2.1.9. Концы канатов у места отреза должны быть прочно обвязаны мягкой проволокой. Для канатов диаметром до 14,5 мм включительно конец каната может быть заварен вместо обвязки. Торцы канатов диаметром более 57,0 мм с металлическим сердечником должны быть заварены. 2.1.10. Диаметр каната, ширина и толщина плоского каната должны соответствовать нормам, указанным в соответствующих стандартах на сортамент стальных канатов. Предельное отклонение по ширине и толщине плоских канатов должно быть не более: +5 %, -8 % - для повышенной точности, ±8 % - для нормальной точности. Предельное отклонение по диаметру каната должно соответствовать указанным в табл. 1 и 2. Канаты с органическим сердечником могут иметь зазоры между прядями, при этом диаметр каната не должен превышать предельных отклонений, приведенных в табл. 1. Допускается зазор между прядями в канатах с металлическим сердечником и выступающий ворс or органического сердечника в канатах с органическим сердечником. 2.1.11. Длина каната устанавливается потребителем. Допускаемое отклонение по длине должно быть не более для канатов длиной: ≤ 400 м – +5 %, ≥ 400 м – +20 м на каждые 1000 м или их части.
1. Расчет стальных канатов с учетом требований Ростехнадзора.
9.6. Стальные канаты и цепи
9.6.1. Стальные канаты, устанавливаемые на ПС при замене ранее установленных, должны соответствовать по марке и разрывному усилию указанным в Паспорте ПС, иметь сертификат (свидетельство) или копию сертификата предприятия — изготовителя канатов об их испытании в соответствии с ГОСТ 3241 или ГОСТ 18899.
Стальные канаты, не снабженные сертификатом (свидетельством) об их испытании, к использованию не допускаются.
Допускается применение канатов, изготовленных по международным стандартам, если они по своему назначению соответствуют технологии использования ПС, имеют диаметр, равный диаметру заменяемого каната, и разрывное усилие – не ниже указанного в Паспорте ПС для заменяемого каната.
Заменять стальные канаты крестовой свивки на канаты односторонней свивки запрещается.
9.6.2. Крепление стального каната на ПС, устанавливаемого взамен ранее установленного, должно соответствовать ранее принятой конструкции его крепления.
9.6.3. Соответствие коэффициента использования (коэффициента запаса прочности) стальных канатов, выбираемых для замены, следует выполнять в соответствии с требованиями ИСО 4308 расчетом по формуле:
где Fо
- разрывное усилие каната в целом (Н), принимаемое по сертификату (свидетельству об их испытании);
Zp -
- минимальный коэффициент использования каната (коэффициент запаса прочности), определяемый по табл. 9.3 в зависимости от группы классификации механизма по ИСО 4301;
S -
наибольшее натяжение ветви каната (Н), указанное в паспорте ПС.
9.6.4. Браковку стальных канатов в эксплуатации следует выполнять согласно Приложению 5 настоящих ФНП.
9.6.5. Стальные цепи, устанавливаемые на ПС при замене ранее установленных, должны соответствовать по марке и разрывному усилию, указанным в Паспорте ПС, иметь сертификат (свидетельство) или копию сертификата предприятия — изготовителя цепи об их испытании.
Допускается применение цепей, изготовленных по международным стандартам, если они по своему назначению соответствуют технологии использования ПС, имеют диаметр и шаг цепи, равные диаметру и шагу заменяемой цепи, а разрывное усилие – не ниже указанного в Паспорте ПС для заменяемого цепи.
Стальные цепи, не снабженные сертификатом (свидетельством об их испытании), к использованию не допускаются.
Таблица 9.3.
Минимальные значения коэффициентов использования канатов Zр
Группа классификации механизма по ИСО 4301/1
Подвижные канаты
Неподвижные канаты
9.6.6. Сращивание цепей допускается электросваркой новых вставленных звеньев или при помощи специальных соединительных звеньев. После сращивания цепь должна быть испытана нагрузкой, в 1,25 раза превышающей ее расчетное тяговое усилие, в течение 10 мин.
9.6.7. Браковку стальных цепей в эксплуатации следует выполнять согласно Приложению 6 настоящих ФНП.
1. Полиспасты. Основные определения. Типы.
Устройство полиспаста и условия его работы Основная область применения полиспастов – стреловые механизмы кранов. Всё многообразие полиспастов может быть сведено к двум требованиям: либо увеличить силу (силовые полиспасты), либо поднять скорость (скоростные полиспасты). В подъёмных кранах чаще используются первые, а подъёмниках – вторые. Таким образом, схемы скоростных и силовых полиспастов взаимно обратные. В состав полиспаста входят следующие составляющие: Блоки с неподвижными осями Блоки с подвижными осями. Обводные блоки. Обводочные барабаны. Все вышеперечисленные элементы располагаются преимущественно в вертикальной компоновке, причём место размещения барабана зависит от наличия обводных блоков: сверху, если такие блоки отсутствуют, и снизу – если присутствуют. Количество блоков с неподвижными осями всегда на один меньше, чем с подвижными. При этом общее количество блоков определяет (для силовых полиспастов) кратность увеличения суммарного усилия на механизме. Количество обводных блоков определяется размерами узла: с увеличением числа таких блоков усилие также увеличивается. Силовые полиспасты, назначение и устройство которых характеризуется несколькими параметрами, важнейшим из которых является нагрузка, развиваемая в подъёмном механизме. Она увеличивается с увеличением расчётной грузоподъёмности крана, кратности устройства (количества ветвей каната, на которых подвешен груз) и КПД блока. КПД учитывает потери на трение в осевых опорах, а также потери, определяемые жёсткостью каната или цепи. Полиспастов может быть несколько, тогда суммарная нагрузка на блок пропорционально уменьшается. Одинарные полиспасты конструктивно проще, но и наименее эффективны. В них один конец неподвижно закрепляется на неподвижном элементе, а второй – на барабане. При этом угол отклонения весьма ограничен из-за опасности схода каната с блока. Наличие обводного блока существенно улучшает условия работы механизма: нагрузка становится симметричной, что снижает износ каната, и увеличивает допустимую скорость вращения блоков. Устойчивость действия полиспаста зависит также от расстояния между обводным и основными блоками. С увеличением этого параметра надёжность полиспаста как функционального узла возрастает, хотя одновременно увеличивается (из-за наличия соединительной оси) и его сложность. Другими схемами полиспастов, применяемых на практике, являются: Сдвоенные трёхкратные, когда в схеме присутствует три рабочих блока и два обводных; Сдвоенные трёхкратные, снабжённые уравнительной траверсой. Вариант используется в грузоподъёмной технике, которая эксплуатируется в тяжёлых и особо тяжёлых условиях.
Расчет механизмов подъема
Расчет механизма подъема
1.1 Определение массы подвижных частей механизма подъема
Работа механизма подъема подъемника связана с перемещением массы кабины, противовеса, тяговых канатов и подвесного кабеля.
Работа по преодолению сил тяжести подвижных частей может быть существенно снижена, если добиться равновесия сил тяжести, действующих на канатоведущий орган лебедки со стороны кабины и противовеса.
Так как полезный груз в кабине не остается величиной постоянной, полное уравновешивание кабины с грузом практически исключается. Если силу тяжести конструкции кабины можно полностью уравновесить с помощью противовеса, то груз в кабине – только частично.
Влияние неуравновешенности канатов становится весьма ощутимым при значительной высоте подъема кабины.
Основную роль в системе уравновешивания играет противовес. При небольшой высоте подъема масса противовеса выбирается из условия уравновешивания кабины и среднестатистического значения массы полезного груза. Это обеспечивает существенное снижение окружной нагрузки КВШ и необходимой мощности привода лебедки.
При высоте подъема кабины более 45 м приходится учитывать влияние силы тяжести неуравновешенной части тяговых канатов и применять для их уравновешивания дополнительные гибкие уравновешивающие элементы в виде цепей или уравновешивающих канатов.
Определение массы противовеса требует предварительного определения массы кабины по исходным данным или по приближенным соотношениям, устанавливающим зависимость между площадью пола и массой кабины [10. стр.59].
Масса кабин отечественного производства приближенно определяться по следующим зависимостям:
пассажирский и грузопассажирский
Qк =(500 – 550) , кг, (1.1)
где А, В –ширина и глубина кабины, соответственно, м.
Qк = 550х1,9х2= 1900 кг.
Масса противовеса определяется по формуле
Qп = Qк + φQ, (1.2)
где φ – коэффициент уравновешивания номинального груза кабины; Q – масса груза, кг.
Qп = 1900 +0,5х1000 = 2400 кг.
Масса подвесного кабеля
Qпк = qпк * (H/2 + 5), кг. (1.3)
Выбор типа подвесного кабеля и определение массы 1 метра его длины производится в зависимости от числа проводящих жил и вида изоляции.
qпк = 0,392 кг/м,
Qпк = 0,392 х (110/2 +5) = 23,5 кг,
1. Основные требования к блокам и барабанам ГПМ по правилам Ростехнадзора.
2.2.3. Требования к барабанам и блокам
Понедельник, 8 апреля 2013 г. / Просмотров: 3934
Метки: барабаны, блоки, опоры, тормоза
2.2.3. Требования к барабанам и блокам
2.2.3.1. В случае применения на подъемнике дополнительного грузоподъемного оборудования (крюковых подвесок, крюка, блоков, барабанов) это оборудование должно соответствовать требованиям Правил устройства и безопасной эксплуатации грузоподъемных кранов.
Минимальный диаметр блока или барабана, огибаемого стальным канатом, применяемым в конструкции подъемника, определяют по формуле
D ³ hd,
где D - диаметр блока или барабана, измеряемый по средней линии каната, мм;
d - диаметр каната, мм;
h - коэффициент выбора диаметра блока, значение которого принимается равным 16.
Канатоемкость барабана должна быть такой, чтобы при низшем (высшем) возможном положении люльки на барабане оставались навитыми не менее 1,5 витков каната, не считая витков, находящихся под зажимным устройством.
Барабаны, предназначенные для многослойной навивки каната, должны иметь реборды с обеих сторон.
Реборды барабана должны возвышаться над верхним слоем навитого каната не менее чем на два его диаметра.
2.2.4. Требования к ходовым колесам
2.2.4.1. Ходовые колеса прицепных и самоходных (на собственном шасси) подъемников, предназначенные для транспортирования по автомобильным дорогам, должны иметь стандартные пневмошины.
Для подъемников, перевозка которых осуществляется автомобилем или другим транспортным средством и передвигаемых по рабочей площадке вручную, допускается применение других ходовых колес в соответствии с нормативными документами.
2.2.5. Требования к опорам
2.2.5.1. Усилие поднятия (выдвижения) вручную опор подъемника или их частей должно быть не более 200 H. При большем усилии опоры должны иметь гидравлический или другой привод. Установка подъемника должна производиться на площадке с учетом категории грунта.
При установке подъемника на все опоры колеса должны быть освобождены от нагрузки, если мосты и колеса участвуют в удерживающем моменте.
2.2.5.2. Подъемники, не имеющие опор, должны быть оборудованы устройством, исключающим действие упругих подвесок.
Необходимость оборудования подъемников стабилизатором упругих подвесок, позволяющих равномерно передавать нагрузку на все рессоры одной ходовой оси для обеспечения их равномерной просадки на поворотах во время движения, должна определяться разработчиком.
2.2.6. Требования к тормозам
2.2.6.1. Механизмы подъема подъемников должны быть снабжены тормозами нормально замкнутого типа, автоматически размыкающимися при включении, или другими устройствами, исключающими самопроизвольное опускание (перемещение) люльки.
Применение ленточных тормозов разрешено только на механизмах поворота платформы. Тормоза должны быть защищены от попадания масла и влаги.
Привод опорно-поворотного устройства подъемника должен быть самотормозящимся или оборудован тормозом. При этом коэффициент запаса торможения должен быть не менее 1,5.
У подъемного механизма подъемника с канатным приводом должно быть предусмотрено устройство, исключающее возможность самопроизвольного опускания люльки.
2.2.6.2. Автомобильные, прицепные, передвижные подъемники и подъемники на спецшасси должны быть оборудованы стояночным тормозом и отвечать требованиям Правил дорожного движения Российской Федерации.
Для подъемников, установленных на железнодорожном подвижном составе, тормоза на механизме передвижения должны отвечать требованиям Правил МПС Российской Федерации.
Расчет основных параметров барабанов.
Механические расчеты вращающихся барабанов включают определение толщины стенки барабана, обеспечивающей прочность и жесткость конструкции, а также опорных и упорных роликов.
Толщину стенки барабана предварительно определяют по нормалям или, в зависимости от диаметра барабана D, по эмпирической формуле
d = (0,007¸0,01)D, (44)
где D – диаметр барабана; D = 2200 мм,
d = 0,007·2200 = 15,4 мм.
Масса находящегося в сушилке материала, кг:
Gм = V∙β∙ρм = 45,6∙0,12∙900 = 4924,8 кг. (45)
Масса футеровки (теплоизоляции)
, (46)
где Dф – внутренний диаметр футеровки, (Dф = Dв – 2Sф= 2200 – 2×12 = 2176 м); плотность, толщина, длина футеровки.
кг = 1153 т.
Длина куска футеровки для барабана определяется из расчета:
Lф = (D + h) π,
где D – диаметр барабана, мм, h – толщина футеровки, мм.
Lф = (2,2 + 0,123) 3,14 = 5,463 м.
Поперечная сила, действующая на барабан в месте крепления венцовой шестерни (рис. 5)
, (47)
где mш – масса венцовой шестерни; mкр – масса элементов крепления венцовой шестерни; g = 9,81 м/с2.
Н.
Общая масса
, (48)
где mк – масса корпуса барабана.
т = 1158660 кг.
Линейная нагрузка
. (49)
Н
Реакции опор от действия q и Qв
(50)
Максимальный изгибающий момент
. (51)
где L – расстояние между бандажами, м (для барабана длиной 12000 мм L принимаем равной 7,2 м).
,
Н×м.
Барабану передается также крутящий момент от привода, необходимый главным образом для поднятия центра тяжести материала на определенную высоту. Крутящий момент можно определить из уравнения
, (52)
где N – мощность привода, N = 62·103 Вт; n – частота вращения барабана, n = 1,02 с-1.
Мкр = [62·103/(2·3,14·1,02)] = 9679 Нм.
Напряжение в барабане
, (53)
где [s] = 5¸10 МПа – допускаемое напряжение для аппаратов из сталей марок Ст2, Ст3, Ст10, Ст15 без футеровки; [s] = 20 МПа – для аппаратов с футеровкой.
Расчетный (приведенный) момент Мр определяют по формуле
, (54)
Н×м.
Момент сопротивления кольцевого сечения барабана
W = 0,785D2d = 0,785·2,22·15,4 = 58,5 м3. (55)
Проверка условия прочности барабана:
sи = 14269/58,5 = 243,9 < 20·106
Условие прочности выполняется.
; (56)
; (57)
Н м
; (58)
, (59)
Н м.
Расчет барабана на жесткость. Суммарный максимальный прогиб от действующих нагрузок
, (60)
где q1 – линейная нагрузка от массы обрабатываемого материала; q2 – линейная нагрузка от масс (футеровки, насадки и барабана); Е – модуль упругости материала корпуса Е = 1,76 1011 Па; момент инерции единичного кольцевого сечения барабана.
;
;
м4.
Относительный прогиб
, (61)
где допускаемый относительный прогиб (барабан с футеровкой); – допускаемый относительный прогиб (барабан без футеровки).
.
Условие жесткости выполняется.
Расчет свободно надетого бандажа. Реакция опорного ролика (рис. 6, а)
, (62)
где Ron = max (RA, RB) – реакция опоры; – половина угла между роликами.
Схемы механизма передвижения крана, тележки.
Кинематическая схема мостового крана с описанием
Кинематическая схема мостового крана позволяет понять принципы работы всех крановых узлов и механизмов. В целом принцип работы всего подъемно-транспортного оборудования одинаков: основой является одна или две металлических балки, на которых размещена грузовая лебедка, приводимая в движение электрическим двигателем.
Вид кранового оборудования зависит от типа конструкции и специфики поднимаемых грузов. Однако стоит отметить, что основные узлы грузоподъемных механизмов аналогичны.
Общая кинематическая схема мостового крана
схема мостового крана
Рис. 1. Кинематическая схема механизма передвижения мостового крана
На рисунке 1 представлена типовая кинематическая схема кранового механизма, включающая:
1. Электродвигатель (чаще всего используются асинхронные трехфазные двигатели).
2. Тормоз – обеспечивает остановку и фиксацию перемещаемого груза в любом положении.
3. Редуктор – понижает количество оборотов двигателя.
4. Барабан – служит для равномерного натяжения крановых тросов.
5. Полиспаст – одинарый или обойма из нескольких блоков, обеспечивающих эффективное распределение энергии от привода и выигрыш в скорости и силе.
6. Крюк – устройство для захвата груза.
Кинематическая схема механизма передвижения мостового крана
схема механизма передвижения мостового крана
Рис. 2. Схема трансмиссии крана с индивидуальным приводом
Механизм движения крана может быть центральным или индивидуальным. В свою очередь центральное перемещение подразделяется на два вида: с быстроходным и тихоходным трансмиссионным валом.
схема механизма передвижения с тихоходной трансмиссией
Рис. 3. Кинематическая схема передвижения мостового крана с тихоходной трансмиссией
Привод крана с тихоходной трансмиссией устанавливается в середине моста и включает: двигатель 3, муфты-тормоза 2 и редуктор 1. Выходной вал редуктора связывается с валом трансмиссии 4, изготовлен из сборных секций, которые соединяются муфтами 5, установленными в подшипниках. Также муфты соединяют трансмиссионный вал с приводом ходовых колес 7, используя зубчатую передачу 6. Вал 4 вращается с той же скоростью, что и колеса, передавая максимальный крутящий момент.
Кинематическая схема механизма подъема мостового крана
В крановых конструкциях мостового типа грузоподъемный механизм размещается на грузовой тележке. Количество устройств для подъема зависит от максимального веса груза, который способна поднять машина.
Схема подъема подъемно-транспортного оборудования зависит от ряда факторов: типа захватного устройства, высоты и массы поднимаемого груза, длины пролета. При использовании крюка, грейфера или электромагнита используется один подъемный механизм.
Определение сопротивления передвижению ходового колеса крана.
Определение сопротивлений передвижению крана
Согласно рекомендациям [1, параграфа 1.2], ориентировочная масса консольного крана m=т. По табл. 1,29 найдем рекомендуемый диаметр ходовых колес Dк =250 мм.
Коэффициент трения качения ходовых колес по рельсам с плоской головкой µ=0,0005 [1,табл. 1.28]. Коэффициент трения в подшипниках качения ходовых колес f=0,02 (подшипники конические).
Диаметр цапфы вала ходового колеса для подшипников качения dk =(0,2…0,25)• Dк . Соответственно dk=0,2·250=50 мм. Принимаем dk=50 мм. Примем также kp - коэффициент, учитывающий дополнительные сопротивления от трения реборд ходовых колёс и торцов ступиц колеса для подшипников качения kp=2,0…2,5.
Принимаем kp = 2,5.
Общее сопротивление передвижению крана:
(1)
где, - сопротивление трения, (см. 2.40) Н;
Fукл - сопротивление от уклона пути,(см. 2.41) Н;
Fв - сопротивление от ветровой нагрузки, (см.1.17) Н.
1. Схемы механизмов поворота кранов.
Механизм поворота предназначен для обеспечения вращения подвижной металлоконструкции крана. Поворот крана осуществляется при помощи расположенного на подвижной металлоконструкции привода (электро- или гидродвигатели, редуктора) следующим образом:, двигатель 1 передает движение редуктору 2, который уменьшая частоту его вращения nдв и увеличивая вращающий момент, приводит во вращение шестерню 3 (расположенную на выходном валу редуктора). Шестерня 3 находится в зацеплении с зубчатым колесом 4, которое закреплено неподвижно на неподвижной части металлоконструкции крана, вследствие чего шестерня 3 имеет возможность вращаться вокруг колеса 4, обеспечивая тем самым поворот подвижной части.
Рис. 7.7. Схема механизма поворота крана
Частота вращения крана определяется по зависимости
,
где – частота вращения двигателя, мин-1;
– передаточное отношение механизма,
,
– передаточное отношение редуктора;
– передаточное отношение открытой зубчатой передачи, ,
z4, z3 – числа зубьев колеса и шестерни.
Момент сопротивления вращению крана от сил трения, кН×м
,
где f – коэффициент трения, f =0,01….0,015;
Dср – средний диаметр опорно-поворотного круга., м.
Момент сопротивления вращения крана от ветровых нагрузок, кН×м
,
где – cила давления ветра на стрелу, кН;
– сила давления ветра на груз , кН;
– сила давления ветра на металлоконструкцию поворотной платформы, кН;
lк – плечо приложения силы , м.
Момент сопротивления вращения крана от весовых составляющих при крене (среднеквадратичный), Н×м
,
где q – угол крена судна, грд.
Расчетная мощность двигателя механизма поворотра, кВт
,
где – частота вращения крана, мин-1;
hмех – к.п.д. механизма поворота, вычисляется ,
hп – к.п.д. подшипников hп=0,98;
hред – к.п.д. редуктора, можно принять hр =0,91…0,94;
hозп – к.п.д. открытой зубчатой передачи hп=0,94
Дата добавления: 2019-07-15; просмотров: 550; Мы поможем в написании вашей работы! |
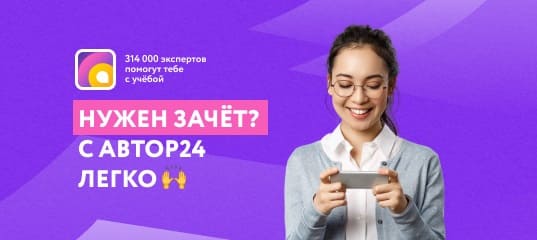
Мы поможем в написании ваших работ!