Литьевые формы и материалы для их изготовления
Форма для литья пластмасс под давлением (формующая оснастка) – основной элемент оборудования, определяющий конструкцию и качество готового полимерного изделия
.
Часто формы для литья пластмасс под давлением называют литьевыми формами, литформами или прессформами. И хотя, с точки зрения классификации форм, данные названия являются не совсем корректными, в данной статье они будут использоваться из-за своей широкой распространенности.
Как правило, литьевая форма в сборе состоит из набора плит, формообразующих (матриц и пуансонов), холодноканальной или горячеканальной литниковой системы, системы выталкивания отформованных изделий, системы охлаждения формы, системы выпаров и набора направляющих элементов. Схематично литьевая форма представлена на рис.1. Технология изготовления форм подобна технологии штампов или печатных плат. В условиях современного промышленного производства часто необходимо интенсифицировать процесс литья пластмасс. В этом случае изготавливают и используют формы для одновременного производства нескольких изделий. Такие прессформы называют многогнездными (многоместными). Число гнезд обычно бывает кратно двум в энной степени, например 2, 4, 8, 16, 32, 64, 128. Реже проектируют литьевые формы с другим количеством гнезд, обычно 6, 10, 12, 20, 24, 48, 96. Формы с наибольшим количеством мест (более ста) изготавливают для комплексов, производящих ПЭТ преформы. Обычно, прессформа проектируется для последующего производства какого-либо одного изделия из пластика. Кроме этого, существуют так называемые «модульные» формы, конструкция которых предполагает сменные компоненты, позволяющие изменять конструкцию изделий или же полностью заменить изделие на другое. Таким образом, одна и та же прессформа позволяет производить разные виды продукции в разное время. К недостаткам такой технологии можно отнести трудоемкость операций по периодическому изменению конструкции форм, необходимость более тщательного и частого обслуживания таких форм, небольшой ресурс универсальных форм.
|
|
Другой путь изготовления различных изделий посредством одной литформы – устройство формообразующих на различные продукты в одной многогнездной форме. Используя подобную форму, имеется возможность производства изделий разной конструкции, но из одного материала, за один цикл литья. В данном случае основная задача проектировщика – правильно сбалансировать литниковую систему для равномерного заполнения всех гнезд такой формы и получения качественной продукции.
Если изделия имеют большую площадь и относительно простую конструкцию, то иногда для интенсификации литья под давлением конструируют так называемые «этажные» формы. Эти формы имеют две параллельные плоскости разъема и при многоместной конструкции могут работать на относительно небольших термопластавтоматах. Недостатки таких форм – дорогостоящий горячий канал, увеличенный пакет плит (высота прессформы), что иногда вызывает необходимость применения нестандартных узлов смыкания ТПА.
|
|
Экструзия полимеров. Классификация методов экструзии.
Экструзия. Экструзия является одним из самых дешёвых методов производства широко распространённых изделий из пластмасс, таких как плёнки, волокна, трубы, листы, стержни, шланги и ремни, причём профиль этих изделий задаётся формой выходного отверстия головки экструдера. Расплавленный пластик при определённых условиях выдавливают через выходное отверстие головки экструдера, что
и придаёт желаемый профиль экструдату. Схема простейшей экструзионной машины показана на рис. 3.10.
В этой машине порошок или гранулы компаундированного полимерного материала загружают из бункера в цилиндр с электрическим обогревом для размягчения полимера. Спиралевидный вращающийся шнек обеспечивает движение горячей пластической массы по цилиндру. Поскольку при движении полимерной массы между вращающимся
|
|
шнеком и цилиндром возникает трение, это приводит к выделению теплоты и, следовательно, к повышению температуры перерабатываемого полимера. В процессе движения от бункера к выходному отверстию головки экструдера пластическая масса переходит три чётко разделённые зоны: зону загрузки (а), зону сжатия (б) и зону гомогенизации (в) (см. рис. 3.10). Каждая из этих зон вносит свой вклад в процесс экструзии. Зона загрузки, например, принимает полимерную массу из бункера и на-
правляет её в зону сжатия, эта операция проходит без нагревания. В зоне сжатия нагревательные элементы обеспечивают плавление порошкообразной загрузки, а вращающийся шнек сдавливает её. Затем пастообразный расплавленный пластический материал поступает в зону гомогенизации, где и приобретает постоянную скорость течения, обусловленную винтовой нарезкой шнека
Под действием давления, создаваемого в этой части экструдера, расплав полимера подаётся к выходному отверстию в головке экструдера и выходит из него с желаемым профилем. Из-за высокой вязкости некоторых полимеров иногда требуется наличие ещё одной зоны, называемой рабочей, где полимер подвергается воздействию высоких
|
|
сдвиговых нагрузок для повышения эффективности смешения. Экструдированный материал требуемого профиля выходит из экструдера в сильно нагретом состоянии (его температура составляет от 125 до 350 °С), и для сохранения формы требуется его быстрое охлаждение. Экструдат поступает на конвейерную ленту, проходящую через ванну с холодной водой, и затвердевает. Для охлаждения экструдата также
применяют обдувку холодным воздухом и орошение холодной водой. Сформованный продукт в дальнейшем или разрезается или сматывается в катушки. Процесс экструзии используют также для покрытия проволок и кабелей поливинилхлоридом или каучуком, а стержнеобразных металлических прутьев – подходящими термопластичными материалами.
Дата добавления: 2019-07-15; просмотров: 424; Мы поможем в написании вашей работы! |
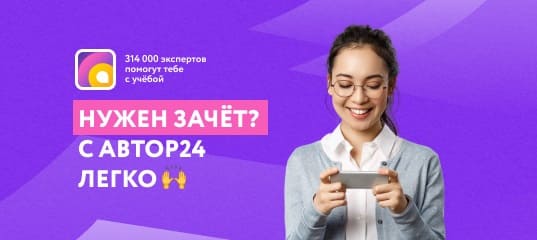
Мы поможем в написании ваших работ!