СВОЙСТВА ПОРОШКОВ И МЕТОДЫ ИХ КОНТРОЛЯ
Металлические порошки характеризуются химическими, физическими и технологическими свойствами. Основные характеристики порошков указывают в ГОСТах или технических условиях (ТУ).
Химические свойства
Химический состав порошка зависит от метода его производства, а также от степени чистоты исходных материалов. Химический анализ проводят по методикам, большинство которых аналогично применяемым при анализе состава литых металлов и сплавов. Содержщи^^скювногр металла ил11^мма_основных к^)мгю^Iе^^т^в_сплава в. поррщка_х составляет, как правило, не ниже 98-99%.
В металлических порошках содержится значительное количество газов (О^, Н^, К| и др.), как адсорбированных на поверхности, так и попавших внутрь частиц в процессе изготовления или при последующей обработке. Большие количества газов увеличивают хрупкость порошков и затрудняют как прессование, так и спекание. Поэтому целесообразна обработка порошков, особенно высокодисперсных, в вакууме, что обеспечивает эффективное газоотделение.
Важными химическими особенностями порошков являются их токсичность и пирофорность (способность порошка к самовозгоранию при соприкосновении с воздухом). Практически все порошкообразные металлы оказывают вредное воздействие на организм человека, находящегося в контакте с ними, хотя в компактном состоянии большинство металлов безвредны. Пирофорность может привести к воспламенению порошка и даже взрыву. Особенно это относится к очень мелким порошкам 7л, А1, М§, Ре, Со и некоторых других металлов. В связи с этим при работе с металлическими порошками обязательно соблюдение специальных мер безопасности и личной гигиены.
|
|
Физические свойства
Форма частиц
В зависимости от метода получения форма частиц порошка может быть сферической (распыление), губчатой (восстановление), осколочной (измельчение в шаровых мельницах), тарельчатой (измельчение в вихревой мельнице), дендритной (электролиз), каплевидной (распыление). Первичная форма частиц может несколько видоизменяться при последующей обработке порошка (размоле, отжиге, грануляции и др.). Для определения формы частиц используют оптические или электронные микроскопы. Форма частиц существенно влияет на технологические свойства порошка, а также плотность, прочность и однородность свойств заготовок из него.
Размер частиц и гранулометрический состав
Металлические порошки представляют собой совокупность частиц размером от долей микрометра до миллиметра. Практически никогда не встречаются металлические порошки с частицами одного размера. Самый широкий диапазон по размерам частиц у порошков, получаемых восстановлением и электролизом. Количественное содержание массы частиц в определенных фракциях по отношению к общему количеству порошка называют гранулометрическим составом порошка. Его выражают обычно либо в виде таблиц, либо графически в виде кривой зернистости. В зависимости от крупности частиц для определения гранулометрического состава порошка используют ситовый, микроскопический и другие виды анализа.
|
|
Удельная поверхность
Удельная поверхность порошка представляет собой сумму наружных поверхностей всех частиц, имеющихся в единице его объема или массы. Для металлических порошков характерна поверхность от 0,01 до 1 м2/г, хотя в отдельных случаях у очень мелких порошков она может достигать и значительно большей величины (например, 4 м2/г для высокодисперсного порошка вольфрама, 20 м2/г для порошка карбонильного никеля и др.). Удельная поверхность влияет на поведение порошков при формовании и спекании. Она зависит от размера и формы частиц. Для измерения удельной поверхности порошка применяют метод адсорбции или используют данные по газопроницаемости. Сущность адсорбционного метода состоит в определении количества вещества, покрывающего поверхность частиц порошка плотным мономолекулярным слоем. Наиболее широко применяют адсорбцию паров азота или криптона при низких температурах (-196°С) и метанола СНз^ОН при комнатной температуре. Более быстрым, но менее точным является определение удельной поверхности порошка по скорости фильтрации газа или жидкости через слой порошка, а также через пористый брикет. Методы основаны на существовании зависимости между удельной поверхностью.
|
|
и пористостью порошка (брикета) и скоростью потока, давлением ивязкостью газа (жидкости), протекающего через слой порошка (брикета).Необходимо помнить, что реальная (действительная) поверхность частиц из-за их шероховатости всегда больше рассчитанной, исходя из габаритных размеров частиц.
Плотность
При анализе определяют истинную плотность частицы порошка, носящая названиепикнометрической §|С, г/см?, которая всегда несколько отличается от теоретическое(рентгенографической) плотности вещества порошка. Это объясняется наличием вчастицах порошка примесей, закрытой пористости, дефектностью кристаллической решетки и другими причинами.
Микротвердость частицы порошка характеризует ее способность к деформированию, что важно для оценки возможного поведения порошка при формовании. Она в значительной степени зависит от содержания в частицах порошка различных примесей и искаженности кристаллической решетки.
|
|
При определении микротвердости измеряют диагональ отпечатка от вдавливания алмазной пирамидки с углом при вершине 136° под действием нагрузок 0,5 - 200 г в шлифованную поверхность частицы. Исследуемый порошок смешивают с бакелитом или
оргцементом . Смесь прессуют в небольшие брикеты, которые затем нагревают для полимеризации наполнителя. Затем брикеты с одного из торцов шлифуют и полируют. Для измерения микротвердости используют приборы ПМТ-3 и ПМТ-5.
Технологические свойства
Насыпная плотность и плотность утряски Насыпная плотность §нас, г/смЗ, есть объемная характеристика порошка, и представляет собой массу единицы его объема при свободной насыпке. Ее величина зависит от плотности упаковки частиц порошка при свободном заполнении ими какого-либо объема.
Она тем больше, чем крупнее и более правильной формы частицы порошка и чем больше их пикнометрическая плотность. Наличие выступов и неровностей на поверхности частиц, а также увеличение поверхности в связи с уменьшением размера частиц повышает межчастичное трение, что затрудняет их перемещение относительно друг друга и приводит к снижению насыпной плотности. Величину, обратную насыпной плотности, называют насыпным объемом Унас, смз/г, который представляет собой объем, занимаемый единицей массы порошка при его свободной насыпке. Насыпная плотность порошка влияет на объемное дозирование и сам
процесс формования, а также на величину усадки при спекании (чем меньше насыпная плотность, тем больше усадка).
При воздействии на свободно насыпанный порошок механических виброколебаний происходит уменьшение объема на 20-50%. Отношение массы порошка к величине этого нового, уменьшенного объема называют плотностью утряски. Максимальная плотность утряски достигается на порошках со сферической формой частиц при минимальной шероховатости их поверхности.
Текучесть
Текучесть порошка характеризует его способность с определенной скоростью вытекать из отверстий, что очень важно для рациональной организации процесса прессования:
хорошая текучесть нужна для быстрого и равномерного наполнения прессформы при объемном дозировании порошка.
Текучесть выражают числом секунд, за которое 50 г порошка вытекает через
калиброванное отверстие диаметром 2,5 мм конусной воронки.
Текучесть порошка обычно уменьшается, а время истечения возрастает при увеличении удельной поверхности и шероховатости частиц, а также усложнении их формы, так как при этом затрудняется относительное перемещение частиц. Окисление в большинстве
случаев повышает текучесть порошка в связи с уменьшением коэффициента трения и сглаживания рельефа поверхности частиц. Значительно понижает текучесть влажность порошка.
Уплотняемость, прессуемостъ и формуемость
Уплотняемость порошка показывает его способность изменять начальную плотность
укладки частиц в процессе прессования. Эта характеристика оценивается по плотности
прессовок, изготовленных при давлениях прессования 200, 400, 500, 600, 700 и 800 МПа в цилиндрической прессформе.
Данные по уплотняемости порошка представляют в виде таблицы или графика зависимости плотности прессовок от усилия прессования. Прессуемость порошка оценивают его способностьюобразовывать прессовку под воздействием определенного давления. Эта характеристика дает качественную оценку свойств порошка, комплексно связанную с уплотняемостью и формуемостью.
Формуемость порошка оценивает его способность сохранять приданную ему форму при прессовании в заданном интервале пористости. Эта характеристика порошка определяется при прессовании навески массой не менее 200 г. в прессформе с последующим определением границ (минимального и максимального значения) интервала пористости (плотности) при котором прессовки после извлечения из прессформы не осыпаются и не имеют расслоения. Формуемость порошка зависит от формы, размера и. состояния поверхности частиц.
Хорошая прессуемость облегчает и удешевляет процесс формования порошка, а хорошо формующиеся порошки дают прочные неосыпающиеся формовки. Как правило, порошки с хорошей формуемостью обладают не очень хорошей прессуемостью, и наоборот. Чем выше насыпная плотность порошка, тем хуже формуемость и лучше прессуемость.
3) Технологическое оборудование, предназначенное для получения металлических порошков.
Типовой технологический процесс изготовления деталей методом порошковой металлургии состоит из следующих основных операций: смешивание, формование, спекание и калибрование.
-Приготовление смеси
Смешивание — это приготовление с помощью смесителей однородной механической смеси из металлических порошков различного химического и гранулометрического состава или смеси металлических порошков с неметаллическими. Смешивание является подготовительной операцией. Некоторые производители металлических порошков для прессования поставляют готовые смеси.
-Формование порошка
Формование изделий осуществляем путем холодного прессования под большим давлением (30-1000 МПа) в металлических формах
-Спекание
Спекание изделий из однородных металлических порошков производится при температуре ниже температуры плавления металла.
-Калибрование
Калибрование изделий необходимо для достижения нужной точности размеров, улучшается качество поверхности и повышается прочность
-Дополнительные операции
Иногда применяются дополнительные операции: пропитка смазками, механическая доработка, термическая, химическая обработка и др
4) Технологическая оснастка, используемая для получения изделий методом спекания.
Спекание – процесс развития межчастичного сцепления и формирование свойств материала, полученного нагревом сформированного или свободно насыпанного порошка или волокна без расплавления основного компонента.
Спекание – одна из основных технологических операций порошковой металлургии, в процессе которой происходит превращение брикета, спрессованного из порошков, в прочное спеченное тело со свойствами, приближающимися к свойствам компактного материала
Для спекания порошковых сплавов применяют электропечи с металлическим сопротивлением, с угольными сопротивлениями в виде труб и высокочастотные. Спекание производится в защитной атмосфере. Для спекания медных сплавов, железа и фрикционных материалов применяют защитные атмосферы, получаемые при частичном сжигании газа. При спекании вольфрама, молибдена, твердых сплавов, магнитных и электротехнических материалов применяют водород. Температура спекания составляет примерно 2/3 температуры плавления металла, например для меди 800 – 850° С, для железа 1050 – 1150° С. Длительность спекания примерно 2 – 3 ч. Различаются два основных типа спекания – спекание однокомпонентной системы, спекание многокомпонентной системы с образованием или без образования жидкой фазы. При спекании происходят следующие пиления: повышение температуры увеличивает подвижность атомов, происходит изменение контактной поверхности частиц, которая большей частью увеличивается; происходит снятие напряжений в местах контакта и рекристаллизация, сопровождающаяся ростом зерна через контактные поверхности; восстанавливаются окислы и удаляются адсорбированные газы и жидкости, и результате контакт становится металлическим.
В случае многокомпонентных систем, кроме перечисленных явлений, происходит образование твердых растворов, диффузия и образование химических соединений. При спекании порошков с большой разницей температур плавления, например порошков карбида вольфрама с порошком кобальта, образуется жидкая фаза, которая капиллярными силами стягивает нерасплавившиеся частицы. В результате получаются плотные детали. Иногда, например при производстве медновольфрамовых электродов, сначала прессуют и спекают порошковый вольфрамовый каркас, потом пропитывают его расплавленной медью. Спекание обычно сопровождается усадкой, которая тем больше, чем выше температура спекания и чем ниже давление прессования. Усадка изменяет размеры деталей; поэтому детали, требующие высокой точности, например подшипники н зубчатые колеса, после спекания калибруют путем протягивания через сквозные прессформы. У сплавов, образующих жидкую фазу, усадка и процессе спекания составляет 5 – 25 %, а у сплавов, не образующих жидкой фазы, 0,5 – 2,5 %.
Горячее прессование, совмещающее прессование и спекание, благодаря ряду преимуществ начинает распространяется всё шире. При горячем прессовании требуется более низкое давление, которое составляет всего 5 – 10 % давления обычного прессования. Порошок лучше заполняет форму, и горячее прессование позволяет получать детали более сложной формы и более точных размеров, не требующих калибрования. Нагрев порошка производится электрическим током.
Дата добавления: 2019-07-15; просмотров: 976; Мы поможем в написании вашей работы! |
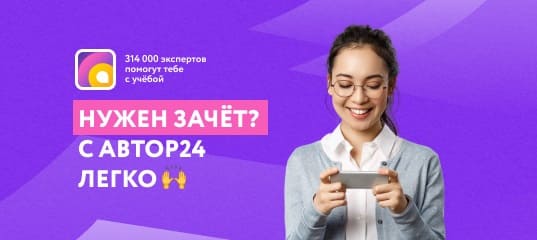
Мы поможем в написании ваших работ!