Устройство и принцип работы механизированных сит: качающихся, вращающихся, вибрационных. Техника безопасности при просеивании.
Механизированные сита в зависимости от метода приведения их в движение разделяют на 3 типа:
1. качающиеся или сита-трясучки;
2. барабанные;
3. вибрационные: электровибрационные, инерционные, гирациоиные.
Качающееся сито (рис. 2.16) состоит из собственно сита, расположенного горизонтально или чаще под углом 4-5° на роликах.
Приводится в возвратно-поступательное движение с помощью шатунно-кривошипного или шатунно-эксцентрикового механизма. Сито совершает от 50 до 400 качаний в минуту при амплитуде колебаний от 5 до 200 мм.
Рис. 2.16. Качающееся сито.
Под ситом устанавливается приемник для сбора просеянного материала.
Барабанные сита, применяемые в галеновом производстве, называются буратами (рис. 2.17).
Рис. 2.17. Бурат.
Применяются сравнительно редко. Они представляют собой цилиндр или шестиугольную призму, расположенную под углом 2-9° к горизонтальнойповерхности. С одной стороны бурата расположена загрузочная воронка, а с другой — коническая зубчатая передача посредством которой бурат приводится в движение от двигателя.
Поверхность цилиндра имеет много отверстий, через которые осуществляется просеивание. Чаще всего отверстия штампуются различного диаметра по участкам поверхности. У загрузочной воронки более мелкие, а далее более крупные. В таком случае происходит просеивание и одновременное деление измельченного продукта на ряд фракций. Естественно, что в этом случае сборники отделяют один от другого перегородками.
|
|
Вибрационные сита чаще всего применяются для просеивания тонких порошков. Они представляют собой разновидность качающихся сит. Амплитуда качания или обратно-поступательного движения не превышает 3 мм, частота колебаний — более 400 в минуту.
Вибрационные сита делятся на инерционные, электровибрационные, гирационные и др.
Вибрационные сита настоящее время успешно вытесняют грохоты или сита других типов.
На рис. 2.18 изображено инерционное сито.
Рис. 2.18. Инерционное сито.
1 - короб, 2 - сито, 3 - пружины, 4 - вал, 5 - шкив, 6 - дебаланс.
На валу 4 находятся два шкива 5, к которым приварены дебалансы. При вращении вала возникают центробежные силы инерции, под действием которых ситу 2 сообщаются колебательные движения.
На рис. 2.19 изображено электро-вибрационное сито.
Рис. 2.19. Электровибрационное сито.
1 - электромагнит, 2 - якорь, 3 - сито, 4 - электрические контакты,
5 - пружины.
При пропускании постоянного тока электромагнит 1 притягивает якорь и с ним сито. При этом разрывается электрический контакт 4. Пружины 5 возвращают сито в исходной положение. Цепь замыкается и сито с якорем снова движется влево. Таким образом создаются колебательные движения электровибрационного сита.
|
|
На рис. 2.20 изображена схема гирационного сита.
Рис. 2.20. Гирационное сито.
1 - вал с двумя эксцентриками и двумя дебалансами, 2 - короб, 3 - сито, 4 - пружины.
Работает оно следующим образом. При вращении коленчатого вала ситу 3 сообщаются частые вращательные движения. Кроме этого два дебаланса придают валу и ситу обратно-поступательные движения, Таким образом сито движется по кругу и одновременно совершает обратно-поступательные движения. Таким сложным движением обеспечивается эффективное просеивание.
На рис. 2.21 изображено вращательно-вибрационное сито модели ВС-2.
Рис. 2.21. Вращательно-вибрационное сито модели ВС-2.
1 - сито, 2 - конус приемника, 3 - дебалансы, 4 - ременная передача, 5 - бункер.
При вращении вала с двумя дебалансами 3, приваренными под различными углами к валу, возникают частые вращательно-колебательные движения сита 1в вертикальной и горизонтальной плоскости. Просеиваемый порошок высыпается из бункера на сито, просеивается и собирается в приемник. В настоящее время вибрационные сита практически вытеснили сита других типов.
Это объясняется следующими крупными достоинствами вибросит:
|
|
1. при высокой частоте колебаний его отверстия почти не забиваются материалом, т.е. устраняется недостаток, свойственный ситам других типов;
2. Более высокая производительность;
3. Пригодность для грубого и тонкого просеивания;
4. Компактность и легкость регулирования и смены сит;
5. Меньший расход энергии, чем у других сит.
Правила просеивания:
1. Просеивать материал сухим;
2. Соблюдать меры предосторожности при просеивании ядовитых веществ: заключать сито в непроницаемый кожух, открывать приемник после оседания пыли, работать в респираторах, обеспечить надежную вентиляцию, ионизацию воздуха;
При просеивании материала возникают трибоэлектрические явления, заключающиеся в электризации частиц за счет трения двух материалов — сита и просеиваемого. Это приводит к тому, что частички просеиваемого материала приобретают одинаковый заряд и отталкиваются друг от друга, образуя пыль, плавающую в воздушной среде. Для борьбы с трибоэлектрическими явлениями надо тщательно заземлять машины для ситовой классификации.
27. Смешивание в промышленном производстве лекарственных средств. Производство порошкообразных смесей. Факторы, влияющие на однородность смесей в процессе получения, транспортировки и хранения порошков.
|
|
Смешивание отдельных компонентов. Смешивание порошков производят в смесителях. Наиболее простым и легким способом смешивания является такой, при котором ингредиенты входят приблизительно в рациональных количествах, с частицами одинаковых размеров, близкими по плотности. Все компоненты засыпают в смеситель и производят перемешивание до получения однородной смеси. Если при указанных равных условиях удельная масса смешиваемых порошков различна, то тогда продолжительность перемешивания увеличивают.
Если в смесь входит компонент в небольшом количестве, то для повышения равномерности распределения необходимо дополнительное измельчение его частиц. При этом чем меньшее количество его в смеси, тем мельче должны быть частицы этого ингредиента. При значительной разнице в размерах частиц отдельных компонентов целесообразно уменьшить их крупные частицы до размеров наименьших с целью получения более равномерной смеси.
Если к большому количеству веществ надо добавить незначительное количество ядовитого или сильнодействующего ингредиента, то сначала необходимо последнее вещество тщательно смешать с одним из ингредиентов или индифферентным порошкообразным веществом. Первым в смеситель загружают вещество, которое имеется в наибольшем количестве, а затем к нему прибавляют приготовленную смесь с ядовитым или сильнодействующим веществом, после чего производят тщательное перемешивание.
В некоторых случаях вещества, входящие в состав смеси в небольших количествах, рациональнее растворить в небольшом количестве растворителя. Полученным раствором увлажняют смесь с остальным материалом.
Эфирные масла в небольших количествах добавляют к порошкам почти так же, как ядовитые и сильнодействующие вещества, т.е. их смешивают с небольшим количеством порошка или приготавливают спиртовой раствор.
Смешивание порошкообразных продуктов производится в специальных смесителях. Смесители классифицируют: по характеру процесса смешивания (конвективного или диффузионного), конструктивному признаку (барабанные смесители с вращающимся корпусом и вращающимися лопастями), способу воздействия на смесь (гравитационные, центробежные), характеру протекающего в них процесса смешивания (периодический или непрерывный) и другим признакам.
Качественной характеристикой процесса смешивания является однородность состава любой из проб, взятой из разных зон смесителя.
На процесс смешивания влияют следующие факторы: поверхностные силы (электростатические, молекулярные, ван-дер-ваальсовы), форма и величина частиц и их плотность. Время смешивания простых и сложных прописей в сухом состоянии составляет от 3 до 12 мин, а при увлажненном состоянии – от 5 до 20 мин. При смешивании необходимо также учитывать характер порошкообразного материала (ядовитость, токсичность, окрашенность, летучесть и т.д.). Основной принцип смешивания: к большему количеству добавляют меньшее, чтобы избежать потери малых количеств веществ. Процессы измельчения, просеивания и смешивания являются основными операциями при производстве порошков и лекарственных сборов.
Смесители твердых, жидких и пастообразных материалов. Виды, устройства и принципы работы смесителей: барабанных, шнековых, циркуляционных, центробежного действия, гравитационных, смесителей с псевдоожиженным слоем.
Смесительное оборудование для перемешивания твёрдых сыпучих веществ и тестообразных сред в зависимости от конструктивых особенностей делится на:
· смесители, имеющие вращающиеся лопасти;
· смесители шнековые;
· смесители барабанные;
· смесители, оснащённые лопастями с поступательными движениями.
Смесители, оснащённые лопастями с поступательным движением, используются в работе с большими объёмами твёрдых материалов, к примеру, для перелопачивания солода. В химической области промышленности они практически не применяются.
Твердые сыпучие материалы смешиваются в аппаратах периодического и непрерывного действия. Аппараты периодического действия конструктивно представляют собой барабаны, которые загружаются и выгружаются периодически. Наиболее простыми мешалками являются цилиндрические барабаны, горизонтально или вертикально закрепленные на валу. Шестигранные барабаны обеспечивают более интенсивное смешивание и измельчение. Для перемешивания небольших объемов используются аппараты под названием «пьяная бочка».
Смесители периодического действия для твердых сыпучих материалов:
Саморазгружающийся смеситель является более совершенным. Загрузку и выгрузку сыпучего материала осуществляет шнек.
Существует также много конструкций смесителей непрерывного действия. К данной группе относится смеситель с вращающимся лопастным барабаном. При каждом обороте барабана тангенциальные ребра обеспечивают большее перемещение материала вправо. В аппаратах со спиральными лентами, вращающимися внутри цилиндрического или корытообразного корпуса, смесь перемешается в сторону выгрузки. Встречное перемещение материала обеспечивается лентами с правым и левым направлением винтовых линий.
На крупных производствах часто используется установка для непрерывного двухступенчатого смешения сыпучих материалов. В таких мешалках компоненты смеси поступают через дозаторы в общий шнек, после чего вторично перемешиваются в смесителе непрерывного действия.
Дата добавления: 2019-07-15; просмотров: 2536; Мы поможем в написании вашей работы! |
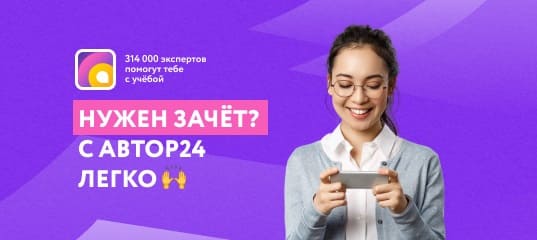
Мы поможем в написании ваших работ!