Способы повышения производительности и точности машин для земляных работ.
Коэффициент, учитывающий разрыхление грунта, равный L+K0, где K0 — первоначальное увеличение объема грунта в сотых долях;— коэффициент использования сменного времени, величина которого зависит от потерь на передвижения экскаватора, условий подачи транспортных средств и др.; при загрузке автомобилей-самосвалов в боковом забое— 0,73—0,74, а в лобовом — 0,68. На производительность экскаватора влияет продолжительность цикла, т. е. суммарное время, затрачиваемое на наполнение ковша, его подъем, поворот под разгрузку, разгрузку ковша его, обратный поворот и опускание. Сокращение продолжительности цикла в значительной степени зависит от квалификации машинистов и уменья применять наиболее прогрессивные способы работ.
Экономии времени машинисты достигают за счет уменьшения угла поворота экскаватора, путем уменьшения ширины забоя, а также совмещения таких операций, как подъем ковша и поворот кабины, разгрузки грунта в процессе движения ковша, Для сокращения продолжительности разгрузки влажного глинистого грунта, прилипающего к стенкам ковша, целесообразно производить резание влажного грунта тонкой стружкой, избегать плотного набивания ковша. Рекомендуется на стенках ковша устанавливать вибраторы.
Технические и технологические методы
Основные способы разработки грунта и применяемые механизмы
Грунты можно разрабатывать механическим, гидромеханическим и взрывным способами. Основным способом является механический.
|
|
Механический способ разработки заключается в отделении грунта от массива резанием с помощью землеройных машин (экскаваторов) или землеройно-транспортных машин (бульдозеров, скреперов, грейдеров).
Гидромеханический способ основан на размывании грунта водяной струей гидромонитора или всасывании разжиженного грунта земснарядом.
Взрывным способом в основном разрабатывают грунты, находящиеся за городом. Для этого в земляном массиве бурят скважины, в которые закладываются взрывчатые вещества (ВВ).
Основные процессы механической разработки грунта - рыхление, разработка, транспортирование, отсыпка, разравнивание, уплотнение, планирование откосов и площадей.
Повышение точности работы
Как известно, при формировании земляного полотна с заданным проектным уклоном и отметками и возведении насыпей требуются многократные проходы грейдера или бульдозера для достижения желаемого результата. Постоянные недоработки, переделки и контроль качества влекут за собой задержки в выполнении работ и дополнительный расход горюче-смазочных материалов.
Одной из важных проблем является перерасход строительных материалов. Зачастую выходит, что асфальтобетона расходуется больше, чем планировалось по проекту. Одной из причин этого является неправильно подготовленное земляное основание дороги (неровности или несоответствие проекту). Рассмотрим простой пример, позволяющий оценить реальные затраты.
|
|
Полотно дороги состоит из трех основных слоев, верхний из которых – асфальтобетон – должен иметь толщину 120 мм. Сейчас точность формирования подготовительных слоев при использовании в работе стандартных автогрейдеров и бульдозеров составляет около +50 мм. И даже такая невысокая точность достигается большим количеством проходов техники с постоянным контролем после каждого прохода.
В результате различных неровностей и несоответствия проекту подстилающих слоев эквивалентная толщина асфальтобетона может достигать до 170 мм. Нетрудно подсчитать, что на 1 км дороги шириной 9 м придется дополнительно уложить примерно 450 м3 этого материала.
Автоматизация машин для земляных работ .
Система BladePro в кабине автогрейдера
В последнее время для формирования проектной поверхности, как дорог, так и других линейно-площадных объектов стали широко применять системы автоматического управления строительной техникой (САУ). Такие системы могут обеспечить точность формирования проектной поверхности до ±5 – 10 мм, а это уже не более 90 м3 возможного перерасхода материала. Как мы видим, повышение точности работ приводит к существенной экономии (примерно $10 тыс. на каждый километр дороги шириной 9 м при средней стоимости асфальтобетона около $30 за 1 м3). Таким образом, установив на свою технику систему автоматического управления, уже через 15 – 20 км дороги вы полностью окупите не только ее, но и свой грейдер или бульдозер, только за счет реальной экономии материала.
|
|
Системы автоматического управления грейдером или бульдозером используют разнообразные датчики для определения положения отвала относительно проектной поверхности. В случае отклонения система подает команду машинисту или сама автоматически изменяет положение отвала, управляя гидравликой машины.
Можно определить три основных типа применяемых систем управления.
Компьютер системы TrimbleSiteVision
Простые индикаторные системы на основе лазерных приемников. Самый простой вариант системы подразумевает использование в качестве проектной плоскость, создаваемую лазерным нивелиром. Приемник лазерного излучения, установленный на машине, фиксирует положение этой плоскости и индикаторными стрелками показывает оператору направление смещения отвала или ковша. Лазерная плоскость в зависимости от модели нивелира может задаваться как горизонтально, так и под определенным проектом уклоном.
|
|
Автоматические системы контроля высоты и поперечного уклона отвала. В такой системе совместно используются датчик поперечного наклона отвала, ультразвуковой или лазерный датчик, измеряющий высоту отвала и система автоматического управления гидравликой машины.
Одной из самых популярных систем автоматического управления является TrimbleBladePro. Она может оснащаться различными датчиками положения отвала, которые подключаются к панели управления, установленной в кабине машины. Панель управления сравнивает введенные проектные данные с информацией о текущем положении отвала, которое автоматически корректируется в соответствии с полученными результатами.
Панель управления системы BladePro
В базовой комплектации системы BladePro на отвал машины устанавливается датчик поперечного наклона, который позволяет быстро и точно формировать поверхность с заданным поперечным уклоном.
Для того, чтобы в автоматическом режиме не только формировать поперечный уклон, но и выдерживать определенную глубину резанья, на грейдер устанавливается один или два ультразвуковых датчика. Они крепятся на краю отвала и непрерывно измеряют расстояние до какой-либо опорной поверхности, например, бордюрного камня или слоя земляного полотна, созданного при предыдущем проходе машины. Также ультразвуковой датчик может измерять расстояние до натянутой струны. При этом режиме работы вы можете формировать практически любые поверхности: виражи, отгоны, вогнутые и выпуклые кривые.
Вместо ультразвукового датчика на машину может устанавливаться лазерный приемник. В этом случае в качестве опорной плоскости будет выступать уже не бордюрный камень или струна, а плоскость, создаваемая лазерным нивелиром. В зависимости от модели нивелира может задаваться как горизонтальная плоскость, так и плоскость с определенным продольным и поперечным уклоном. Такая конфигурация системы обеспечивает быстрое и точное формирование поверхности, а кроме того, предоставляет дополнительные удобства в работе, например, не требуется создавать опорную поверхность или натягивать струну.
Приемник лазерного излучения
3D автоматические системы. 3D-системы объединяют в себе какую-либо из вышеописанных систем с датчиком планового положения самой машины. Они позволяют формировать не просто плоскость с заданным уклоном, а любую поверхность (вогнутые и выпуклые кривые, отгоны, виражи и т.д.) без предварительной разбивки, натягивания струны или любой другой разметки. Обычно такая система состоит из датчиков, определяющих наклон отвала и текущее положение машины в пространстве. Плановое положение машины определяется с помощью следящей системы – электронного тахеометра Trimble ATS или GPS-приемников. Все полученные данные передаются в бортовой компьютер, установленный в кабине машины, где они сравниваются с проектными данными. Компьютер вычисляет расхождения и в случае необходимости передает команду гидравлической системе на изменение положения отвала. Машинисту остается только правильно вести машину, можно сказать «по приборам», и иногда посматривать на дорогу. К такому типу систем относиться TrimbleBladePro 3D и Trimble GPS SiteVision.
Автоматические системы, описанные в этом разделе, помогают увеличить точность и качество работ, сократить время и материалы, ускорить окупаемость техники и тем самым увеличить конкурентоспособность предприятия. Все эти типы систем уже давно используются в мире при проведении земляных работ. В последнее время и в нашей стране строительные фирмы стали использовать различные системы управления машинами, что позволит им в ближайшем будущем выйти на мировой уровень качества при строительстве автомобильных дорог.
Дата добавления: 2019-03-09; просмотров: 274; Мы поможем в написании вашей работы! |
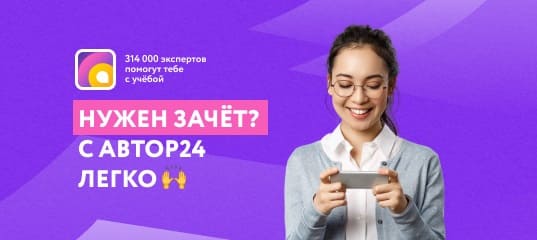
Мы поможем в написании ваших работ!