Фенолформальдегидные смолы (ФФС).
Компонентами смол являются фенол C6H5OH и формальдегид CH2O, реакция поликонденсации которых происходит при нагреве. Формальдегид иногда частично или полностью заменяют фурфуролом. Известны два типа ФФС резольные и новолачные, несколько отличающиеся по свойствам. При смешивании водного раствора формальдегида (формалина) с большим количеством фенола, добавлением кислоты (катализатор) и нагревании образуется новолачная смола. Смола термопластична, так как ее молекулы имеют линейное строение (рис. 6.10, 6.11).
ОН ОН ОН ОН
CH2 CH2
n + (n-1) CH2=O + (n-1)H2O
ОН ОН ОН
…. CH2 CH2 CH2 ….
Рис. 6.10. Схема образования новолачной фенолформальдегидной смолы.
Если же смешать большие количества формалина с фенолом в присутствии щелочи (катализатор) и нагреть, то получится резольная смола:
ОН ОН ОН
…. CH2 CH2 CH2 ….
CH2
….
… CH2 CH2 CH2….
|
|
ОН ОН ОН
Рис. 6.11. Схема строения резольной фенолформальдегидной смолы.
Исходным сырьем для ФФС является каменный уголь, что и объясняет дешевизну и постоялый рост производства, особенно в виде теплоизоляционных пенопластов для строительной промышленности.
В новолачные смолы часто добавляют смазывающие вещества (олеиновая кислота) и красители. Феноло-формальдегидная новолачная смола в твердом состоянии имеет цвет от светло- до темно-коричневого, удельный вес ее около 1,2г/см3. Такая смола способна многократно плавиться и вновь затвердевать, хорошо растворяется в спирте и многих растворителях. Переход смолы из нерасплавленного состояния при 150 – 2000С в неплавкое и нерастворимое состояние в отсутствии отвердителя происходит очень медленно. Температура плавления, вязкость и скорость отверждения новолачных смол изменяется с течением времени очень медленно. Новолачные смолы хорошо хранятся. Хранение резольных смол допускается лишь в течение короткого времени (2 – 3 дня после изготовления), так как при хранении сравнительно быстро возрастает вязкость эмульсионных и жидких смол, а также температура каплепадения и скорость отверждения твердых смол.
|
|
В электронике ФФС широко применяются для изготовления слоистых пластиков, покрытий и красок (лак на основе ФФС называется бакелитовым), деталей электроизоляционной аппаратуры, сепараторов, аккумуляторов. Диапазон рабочих температур ФФС составляет –60 – +200оС. Композиции на основе ФФС и рубленного углеродного волокна (углепрессволокнит) обладают повышенной термостойкостью и могут быть кратковременно нагреты до 530оС. В радиоэлектронике применяются гетинакс и текстолит, которые являются слоистыми пластиками на основе ФФС с бумажным и тканевым наполнителями. К недостаткам ФФС следует отнести их хрупкость, высокую вязкость олигомеров и высокую температуру отверждения.
Эпоксидные смолы.
Эпоксидные смолы являются продуктом поликонденсации многоатомных соединений, включающих эпоксигруппу кольца (рис. 6.12.).
O CH3
CH CH CH2 O O CH2 CH CH2 O
CH3 OH
Эпоксидная группа
Рис. 6.12. Структурная формула фрагмента молекулы эпоксидной смолы.
|
|
Благодаря высокой реакционной способности этих колец отверждение эпоксидных олигомеров можно осуществить с помощью многих соединений и таким образом варьировать температурно-временные режимы обработки и свойства пластмассы. Для холодного отверждения эпоксидных олигомеров применяют алифатические полиамины в количестве 5 – 15% от массы олигомера. Смесь сохраняет вязкостные характеристики в течение 1 - 3 часов, длительность отверждения, наоборот, высокая и составляет 24 часа. При этом степень полимеризации достигает 60 – 70% и продолжает увеличиваться еще в течение 10 – 30 суток. Реакция отверждения смол с алифатическими полиаминами экзотермична. В большом объеме реакционной смеси может произойти само разогрев до температуры выше 230оС, что приводит к деструкции полимера и растрескиванию изделия. Предпочтительнее использовать горячее отверждение, которое осуществляют ароматическими полиаминами. При изготовлении изделий важно избегать как недоотверждения, которое проявляется в повышенных диэлектрических потерях и недостаточной жесткости, так и переотверждения, сопровождающегося потерей эластичности.
Достоинства эпоксидных смол состоят в отсутствии побочных продуктов и очень малой усадке при отверждении (0,2 – 0,5%), высокой смачивающей способности и адгезии к различным материалам. Механическая прочность, химическая стойкость, совместимость с другими видами смол и олигомеров (ФФС, кремнийорганическими полимерами), большой выбор отвердителей и других добавок определяют незаменимость эпоксидных смол для многих отраслей техники. Высокие диэлектрические и влагозащитные свойства эпоксидных смол определили их использование в качестве герметизирующих материалов. Немаловажно, что эпоксидные олигомеры могут быть очищены от примесей, что сводит к минимуму вредное влияние на поверхность полупроводниковых приборов. Эпоксидные смолы (отвержденные) оптически прозрачны и широко применяются в оптоэлектронных приборах (фотоприемниках, светодиодах, оптические пары). На основе эпоксидных смол изготавливаются составы для изготовления ровных и нескользких полов. Свойства эпоксидных смол изменяют в широких пределах, используя различные добавки, которые делятся на следующие группы:
|
|
1. Пластификаторы – органические соединения олигомеры, действующие как внутренняя смазка и улучшающие эластичность и предотвращающие кристаллизацию, отделяя, цепи полимера друг от друга.
2. Наполнители, которые в небольших количествах вводят для улучшения прочности и диэлектрических свойств, повышения стабильности размеров, теплостойкости.
3. Катализаторы, добавляемые для ускорения отверждения.
4. Пигменты, придающие смолам необходимый цвет.
Поликарбонатые полимеры.
Поликарбонаты - группа термопластических пластиков, сложные полиэфиры угольной кислоты и двухатомных спиртов общей формулы (-O-R-O-CO-)n. Наибольшее промышленное значение имеют ароматические поликарбонаты, в первую очередь, поликарбонат на основе бисфенола А, благодаря доступности бисфенола А, синтезируемого конденсацией фенола и
ацетона.
Поликарбонат о случайно открыт изобретателем новокаина Альфредом Айнхорном в самом конце XIX века. В 1953 году работник немецкой компании Bayer Герман Шнелл доказал, что поликарбонаты – это соединения, которые не имеют аналогов среди других термопластов, поскольку обладают замечательными механическими и химическими свойствами. В том же году поликарбонат был запатентован под названием «макролон».
CН3
O
C O С О
CН3 n
Рис. 6.13. Структурная формула поликарбоната - эфира бисфенола А.
Промышленное же производство поликарбоната началось только в 1960 году, когда компания General Electric получила технически пригодные полимеризованные карбонаты.
Свойства. Поликарбонаты на основе бисфенола А - аморфный бесцветный полимер. Обладает хорошими оптическими свойствами. Светопропускание пластин толщиной 3 мм составляет 88%. Температура начала деструкции равна 310-3200C. Растворяется в хлороформе, пиридине, цикло-гексаноне, не растворяется в углеводородах, спиртах, ацетоне, простых эфирах.
Физико-механические свойства поликарбонатов зависят от величины молекулярной массы. Поликарбонаты, молекулярная масса которых менее 20 тысяч углеродных единиц - хрупкие полимеры с низкими прочностными свойствами, поликарбонаты, молекулярная масса которых более 25 тысяч углеродных единиц обладают высокой механической прочностью и эластичностью. Для поликарбонатов характерны высокое разрушающее напряжение при изгибе и прочность при действии ударных нагрузок (образцы поликарбонатов без надреза не разрушаются), высокая стабильность размеров. При действии растягивающего напряжения 220 кг/см2 в течение года не обнаружено пластич. деформации образцов поликарбонатов. По диэлектрическим свойствам поликарбонаты относят к среднечастотным диэлектрикам; диэлектрическая проницаемость практически не зависит от частоты тока. Ниже приведены некоторые свойства поликарбонатов на основе бисфенола А: плотность 1,2 см3; температура стеклования 150о С; температура размягчения 220-230о С; теплопроводность 0,2 Вт/(м.к); коэффициент теплового линейного расширения (5-6) · 10 -5 о С-1; равновесное влагосодержание (20о C, 50%-ная относительная влажность воздуха) 0,2 масс.%.
Поликарбонаты характеризуются невысокой горючестью. Кислородный индекс гомополикарбоната составляет 24-26%. Полимер биологически инертен. Изделия из него можно эксплуатировать в интервале температур от минус 100 до 1350C.
При переработке поликарбонатов применяют большинство методов переработки и формовки термопластичных полимеров: литьё под давлением (производство изделий), выдувное литьё (разного рода сосуды), экструзию (производство профилей и плёнок), формовку волокон из расплава. При производстве поликарбонатных плёнок также применяется формовка из растворов - этот метод позволяет получать тонкие плёнки из поликарбонатов высокой молекулярной массы.
Поликарбонаты являются крупнотоннажными продуктами органического синтеза, мировые производственные мощности в 2006 г. составляли более 3 млн. тонн в год.
Применение поликарбонатов. Благодаря высокой прочности и ударной вязкости (250 - 500 кдж/м2) поликарбонаты применяются в качестве конструкционных материалов в различных отраслях промышленности, используются при изготовлении защитных шлемов для экстремальных дисциплин вело- и мотоспорта. При этом для улучшения механических свойств, применяются и наполненные стекловолокном поликарбонатные композиции.
Благодаря сочетанию высоких механических и оптических качеств монолитный поликарбонат также применяется в качестве материала при изготовлении линз, компакт-дисков и светотехнических изделий.
В строительстве, а особенно в тепличном хозяйстве во всё больших масштабах используется сотовый поликарбонат. Сотовый поликарбонат (структурный поликарбонат, канальный поликарбонат, ячеистый поликарбонат) - это листовой пластик, облегченный, в отличие от монолитного, за счет наличия особых пустот («сот»). Такие листы состоят из двух или более тонких параллельных пластин и тонких перемычек между ними (так называемых ребер жесткости). Воздух, которым наполнены пустоты ячеек, обеспечивает высокие теплоизоляционные свойства материала, а ребра жесткости — большую конструктивную надежность при относительно небольшом весе.
Сотовый поликарбонат производят методом экструзии из поликарбонатного сырья. Показатель светопропускания для прозрачных листов сотового поликарбоната колеблется от 83 до 90%. Помимо прозрачных панелей, производятся белые и цветные панели с разной степенью светопропускания в широком диапазоне от 20 до 70 %.Технические условия ТУ 2256-001-54141872-2006. Поликарбонатные панели характеризуются высокими противоударными качествами в широком диапазоне температур от –40 до +120°C. Технические условия ТУ 2256-001-54141872-2006.
В процессе развития производства поликарбонатных листов были выработаны определенные стандарты на толщину листов: 4, 6, 8, 10 и 16 мм. Чем толще лист, тем меньше тепла он проводит. Соответственно рассчитываются затраты на энергию (обогрев, охлаждение) для данного объекта на 10 лет вперед (стандартный гарантийный срок на сотовый поликарбонат). Европейские производители уже выпускаются панели толщиной 50 - 60 мм. Условно можно выделить следующие основные области применения сотовых поликарбонатных листов в зависимости от их толщины:
· 4мм — парники и навесы, рекламные конструкции (выставочные стенды и витрины);
· 6мм — материал широкого применения (козырьки, теплицы, витражи);
· 8мм — материал широкого применения (перегородки, козырьки, теплицы, крыши);
· 10мм — для сплошного стекления вертикальных и частично горизонтальных поверхностей (зенитные фонари, шумозащитные барьеры для автомагистралей);
· 16мм — крыши над большими пролетами (здания, сооружения), для больших нагрузок.
· 20мм — остекление стадионов, спортивных сооружений, бассейнов, пешеходных переходов, покрытие автостоянок, мансардные окна и остекление балконов
· 25мм — зенитные фонари, остекление и перекрытие торговых, офисных и производственных зданий, оранжереи, зимние сады, офисные перегородки, остекление и покрытие железнодорожных вокзалов и аэропортов
· 32мм — элементы кровли с особыми требованиями, для больших нагрузок.
Каучук, природный каучук.
Природные каучуконосы. Слово «каучук» происходит от двух слов языка индейцев племени тупи-гуарани: «кау» - дерево, «учу» - течь, плакать. «Каучу» дословно «слёзы дерева» - сок гевеи, первого и самого главного каучуконоса. Европейцы прибавили к этому слову ещё одну букву. Каучуконосы лучше всего произрастают не далее 10° от экватора на север и юг. Поэтому эта полоса шириной 1300километров по обе стороны от экватора известна как «каучуковый пояс». Каучуконосы распространены, главным образом, в Южной Америке, Африке и на Малайском архипелаге. Из 20 видов каучуконосных деревьев, произрастающих в Бразилии, лучшим деревом, дающим каучук, является бразильская гевея (Hevea brasiliensis). Это высокое стройное дерево может достигать 45метров в высоту при 2,5-2,8м в обхвате. Родиной гевеи является бассейн Амазонки. По разным оценкам с гевеи бразильской собирают от 90 до 96 % мирового производства натурального каучука. Одно дерево гевеи способно давать в год до 2 – 3кг каучука. Производительность одного гектара составляет до 300 – 400кг в год.
Природный каучук встречается также в очень многих других растениях, не составляющих одного определённого ботанического семейства. Среди травянистых растений России есть всем знакомые одуванчик, полынь и молочай, которые тоже содержат млечный сок.
Каучук в гевеи содержится в млечном соке, распределённом в млечных каналах, которые образуют в стволе концентрические кольца. Млечный сок (латекс), выделяющийся из надрезов и представляющий собой коллоидный раствор каучука. Латекс состоит из мельчайших частичек жидкости, твёрдых частиц и других примесей. Только около 33% латекса составляет каучук, 66% вода и около 1% другие вещества. Латекс подвергают коагуляции действием электролита (раствор кислоты) или нагреванием. В результате коагуляции выделяется каучук. Основной компонент каучука - углеводород полиизопрен (91-96%).
Сырой каучук из других растительных источников обычно засорён примесями смол, которые должны быть удалены. Такие сырые каучуки содержат гуттаперчу - продукт некоторых тропических деревьев семейства Сапоговых.
Во время своего второго путешествия в 1493 году испанский адмирал Христофор Колумб увидел на острове Гаити (а тогда - Эспаньола) туземцев, игравших большим плотным мячом, который, ударяясь о землю, довольно высоко подскакивал в воздух. Индейцы скатывали мячи из загустевшего млечного сока, вытекавшего из порезов на коре дерева гевеи. Из млечного сока также изготовляли непромокаемые калоши. Первые попытки сделать каучуковую обувь в Европе вызывали только смех. Галоши или сапоги хорошо служили в дождь, но стоило выглянуть и припечь солнцу, как они растягивались, начинали прилипать. В мороз же такая обувь становилась хрупкой как стекло. В 1770 году британский химик Джозеф Пристли обнаружил, что каучук может стирать то, что написано графитовым карандашом. Тогда такие куски каучука называли гуммиластиком («смолой эластичной»). В 1791 году английский фабрикант Самуэль Пил запатентовал способ сделать одежду водонепроницаемой с помощью обработки её раствором каучука в скипидаре. Во Франции к 1820г. научились изготовлять подтяжки и подвязки из каучуковых нитей, сплетённых с тканью.
В Англии британский химик и изобретатель Чарльз Макинтош предложил класть тонкий слой каучука между двумя слоями ткани и из этого материала шить водонепроницаемые плащи. В 1823 году в Глазго он начал мануфактурное производство водонепроницаемой одежды. Непромокаемый плащ из прорезиненной ткани до сих пор носит его имя. В США вещи из каучука стали популярными в 1830-х годах, резиновые бутылки и обувь, сделанные южноамериканскими индейцами, импортировались в больших количествах. В 1834 году немецкий химик Фридрих Людерсдорф и американский химик Натаниель Хейвард обнаружили, что добавление серы к каучуку уменьшает или даже вовсе устраняет липкость изделий из каучука. Американский изобретатель Чарльз Гудьир в 1839г. обнаружил, что нагревание каучука с серой устраняет его неблагоприятные свойства. Он положил на печь кусок покрытой каучуком ткани, на которую был нанесён слой серы. Через некоторое время он обнаружил кожеподобный материал - резину. Этот процесс был назван вулканизацией. К 1919 году было предложено уже более 40 000 различных изделий из резины.
Природный каучук. Природный каучук – высокомолекулярный непредельный углеводород состава (С5 H8) n, где n = 1000 – 3000. Масса моля молекул полимера колеблется в пределах 150000-500000 г/моль. Полимер состоит из повторяющихся звеньев 1,4-цис-изопрена и имеет стереорегулярное строение (рис. 6.14).
Рис. 6.14. Фрагмент макромолекулы природного каучука - 1,4-цис-полиизопрена.
Методом рентгеноструктурного анализа установлено, что метиленовые СН2-группы расположены по одну сторону от двойной связи. Макромолекула каучука имеет спиральное строение с периодом идентичности 0.913 нм. Строение макромолекулы каучука обеспечивает его высокую эластичность – наиболее важное техническое свойство. Каучук обратимо растягивается до 900 % первоначальной длины.
Другой природный полимер - гуттаперча или балата - сок некоторых каучуконосных растений, произрастающих в Индии и на Малайском полуострове. В отличие от каучука молекула гуттаперчи короче и имеет транс-1,4-строение с периодом идентичности 0,504 нм (рис. 6.15).
Рис. 6.15. Фрагмент макромолекулы природного полимера - гуттаперчи - 1,4-транс-полиизопрен.
Синтетические каучуки.
Ограниченность ресурсов производства природного каучука, возрастающая потребность промышленности в каучуках и резинах с разнообразным комплексом свойств определили необходимость разработки методов производства синтетических каучуков. Заметный вклад в создание синтетических каучуков внесли российские, а затем и советские учёные И.Л. Кондаков, А.Е. Фаворский, С.В. Лебедев, которому впервые удалось получить синтетический каучук из бутадиена. На основе предложенного метода создано промышленное производство синтетических каучуков.
Синтетические каучуки классифицируют по химической природе мономеров. Наиболее распространёнными являются следующие каучуки: бутадиеновый, дивиниловый, изопреновый, хлоропреновый, бутадиен-стирольный.
Бутадиеновый каучук (СКБ) бывает двух видов: стереорегулярный и нестереорегулярный. Стереорегулярный бутадиеновый каучук применяют главным образом в производстве шин, которые превосходят шины из натурального каучука по износостойкости. Нестереорегулярный бутадиеновый каучук используется в производстве кислотостойкой и щелочностойкой резины, эбонита.
Сополимерные каучуки - продукты совместной полимеризации (сополимеризации) бутадиена с другими непредельными соединениями, например, со стиролом (СКС) или с акрилонитрилом (СКН). В макромолекулах каучуков звенья бутадиена чередуются со звеньями соответственно стирола и акрилонитрила. Бутадиен-стирольный каучук отличается повышенной износостойкостью и применяется в производстве автомобильных шин, конвейерных лент, резиновой обуви. Бутадиен-нитрильные каучуки проявляют свойства стойкости к бензину, природным и синтетическим маслам, используются при производстве изделий контактирующих с нефтепродуктами: сальники прокладки, уплотнители.
Винилпиридиновые каучуки являются продуктами сополимеризации диеновых углеводородов с винилпиридином, главным образом бутадиена с 2-метил-5-винилпиридином. Изготовленные из каучуков резины характеризуются масло-, бензо- и морозостойкостью, хорошо слипаются с различными материалами. Применяются, в основном, в виде латекса для пропитки шинного корда.
В России разработано и внедрено в производство получение синтетического полиизопренового каучука (СКИ), близкого по свойствам к натуральному каучуку. Резины из СКИ отличаются высокой механической прочностью и эластичностью. СКИ служит заменителем натурального каучука в производстве шин, конвейерных лент, резин, обуви, медицинских и спортивных изделий.
Кремнийорганические каучуки применяются в производстве оболочек проводов и кабелей, трубок для переливания крови, протезов (например, искусственных клапанов сердца) и др. Жидкие кремнийорганические каучуки являются герметиками.
Полиуретановый каучук используется как основа износостойкости резины.
Фторсодержащие каучуки имеют как особенность повышенную термостойкость и поэтому используются главным образом в производстве различных уплотнителей, эксплуатируемых при температурах выше 200°C.
Хлоропреновые каучуки - полимеры хлоропрена (2-хлор-1,3-бутадиена) - по свойствам сходны с натуральным каучуком, в резинах применяются для повышения атмосферо-, бензо- и маслостойкости.
Существует и неорганический синтетический каучук - полифосфонитрилхлорид.
Резины.
Резина – высокоэластичное, прочное соединение, но менее пластичное, чем каучук, получаемое при повышенной температуре в процессе вулканизации каучука с серой и различными добавками: ускорителями процесса вулканизации, мягчителями, противостарителями, активными и пассивными наполнителями, красителями. Добавляемые ингредиенты улучшают технологические свойства обрабатываемой смеси, повышают качество получаемых резиновых изделий.
Вулканизация каучука с серой, другими компонентами протекает при повышенной температуре. Атомы серы вступают в химическое взаимодействие с линейными молекулами каучука по месту двойных связей и «сшивают» их друг с другом. В результате образуется гигантская пространственная молекула, имеющая три измерения. Поскольку резина является многокомпонентной системой, в состав которой входит несколько веществ не участвующих в процессе вулканизации, то образующуюся пространственную структуру резины следует рассматривать как редко сетчатую. На макро-уровне резина является однородным материалом с набором характерных свойств. На микро-уровне в резине имеется матрица из вулканизированного каучука, в которой находятся внедрения неорганических веществ и органических молекул. Для обеспечения необходимых свойств резины количественные соотношения компонентов должны находиться в оптимальных соотношениях. Если к каучуку добавить больше серы, чем нужно для образования резины, то при вулканизации линейные молекулы окажутся «сшитыми» в очень многих местах и материал утратит эластичность, станет твёрдым – получится эбонит. Превышение оптимальных концентраций неорганических микро-внедрений приведёт к потере механической прочности резины и её разрушению при эксплуатации.
Для получения высококачественной резины, которую можно переработать в различные изделия, в реакционную смесь вводят несколько компонентов, каждый из которых выполняет свои функции.
Ускорители вулканизации – улучшают свойства вулканизаторов, сокращают время вулканизации и расход основного сырья, препятствует перевулканизации. В качестве ускорителей используются неорганические соединения (оксид магния MgO, оксид свинца PbO и другие) и органические: дитиокарбаматы (производные дитиокарбаминовой кислоты), тиурамы (производные диметиламина), ксантогенаты (соли ксантогеновой кислоты) и другие. Введения ускорителей в определённых случаях позволяет проводить вулканизацию вообще без нагревания (холодная вулканизация). Добавки ускорителей позволяют уменьшить количество вводимой серы.
Активаторы ускорителей вулканизации облегчают реакции взаимодействия всех компонентов резиновой смеси. В основном в качестве активаторов применяют оксид цинка.
Антиокислители (стабилизаторы, противостарители) вводят в резиновую смесь для предупреждения «старения» каучука (фенолы, воск, фенил-β-нафтиламин). С течением времени кислород присоединяется к оставшимся в молекулах резины двойным связям и усиливает тем самым образование сетчатых молекул, при этом резина теряет свои характерные качества и становится твердой и ломкой.
Наполнители повышают физико-механические свойства резин и увеличивают объём исходного сырья. Введение наполнителей сокращает расход каучука и снижает стоимость резины. В соответствии с функциями выделяют две группы наполнителей:
1. активные наполнители, которые улучшают качество каучука: прочность, износостойкость, сопротивление истиранию. К ним относятся активная газовая сажа, окись цинка, каолин (разновидность глины). Поверхностно активную газовую сажу получают сжиганием газа при недостатке кислорода.
2. инертные наполнители, которые увеличивают вес продукта, например, сажа, CaCO3, BaSO4, гипс CaO*2H2O, тальк 3MgO*4SiO2*2H2O, оксид кремния SiO2.
Правильный выбор наполнителей, их количественных соотношений с каучуком во многом определяет качество резины.
Пластификаторы (мягчители) – вещества, которые улучшают технологические свойства резины, облегчают её обработку (понижают вязкость системы), обеспечивают возможность увеличения содержания наполнителей. Введение пластификаторов повышают динамическую выносливость резины, сопротивление «стиранию». В качестве пластификаторов используются продукты переработки нефти (мазут, гудрон, парафины), вещества растительного происхождения (канифоль), жирные кислоты (стеариновая, олеиновая) и другие.
Технология производства резины осуществляется по следующим основным этапам:
1. Приготовление резиновой смеси, состоящей из каучука, вулканизирующих веществ, ускорителей вулканизации, активаторов, наполнителей, стабилизаторов и других наполнителей.
2. Изготовление полуфабрикатов, которое может проводиться одновременно с приготовлением резиновой смеси и включает следующие операции: а) развеска каучуков и ингредиентов; б) пластикация каучука; в) прорезинивание тканей, каландрирование, шприцевание; г) раскрой прорезиненных тканей и резиновых листов, сборка изделий из полуфабрикатов.
3. Вулканизация, после которой из сырых резиновых смесей получают готовые резиновые изделия. Вулканизацию проводят или после формования из резиновой смеси соответствующих изделий (труб, рукавов, листов и других), или одновременно с процессом формования изделий. Вулканизация протекает при нагревании.
Образование в процессе вулканизации пространственного полимера приводит к изменению свойств материала. Резина имеет более высокую прочность, чем исходный каучук. Каучук, хотя и медленно, растворяется в бензине, резина лишь набухает в нём. Свойства резины определяются также типом исходного сырья. Например, резина из натурального каучука характеризуется хорошей эластичностью, маслостойкостью, износостойкостью, в то же время мало устойчива к агрессивным средам; резина из каучука СКД имеет даже более высокую износостойкость, чем натуральный каучук. Бутадиен-стирольный каучук СКС способствует повышению износостойкости. Изопреновый каучук СКИ определяет эластичность и прочность резины на растяжение, а хлоропреновый – стойкость её к действию кислорода.
Резиновые материалы имеют существенное значение для обувной промышленности. В зависимости от структуры обувную резину делят на непористую (монолитную) и пористую.
Непористую резину изготовляют на основе бутадиенового каучука. Отличается высокой устойчивостью к истиранию. Резина не пропускает воду и практически в ней не набухает, является воздухо- и паронепроницаемой. Уступает коже по морозостойкости и теплопроводности, что снижает теплозащитные свойства обуви. Непористая резина бывает подошвенная, кожеподобная, и транспарентная.
Кожеподобная резина изготовляется на основе каучука с высоким содержанием стирола (до 85%), что придаёт резинам твёрдость. Толщина резины может быть уменьшена до 2,5 – 4,0 мм при сохранении хороших защитных функций. Эксплуатационные свойства кожеподобной резины сходны с натуральной кожей. Она обладает высокой твёрдостью и пластичностью. Кожеподобная резина хорошо окрашивается при отделке обуви, имеет высокую износостойкость, благодаря хорошему сопротивлению, истиранию и устойчивости к многократным изгибам. Недостатком этой резины являются высокая теплопроводность и отсутствие необходимой воздухонепроницаемости. Кожеподобную резину выпускают трёх разновидностей: непористой структуры с плотностью 1,28г/см3, пористой структуры, имеющую плотность 0,8-0,95г/см3, и пористой структуры с волокнистым наполнителем, плотность которых не выше 1,15г/см3.
Транспарентная резина представляет собой полупрозрачный материал с высоким содержанием натурального каучука. Отличается высоким сопротивлением к истиранию и твёрдостью, по износостойкости превосходит все виды резин. Разновидностью транспорентной резины является стиронип, содержащий большее количество каучука. Сопротивление многократному изгибу у стиронипа в три с лишним раза выше, чем у обычных непористых резин. Стиронип применяется при изготовлении обуви клеевого метода крепления.
Резина пористой структуры имеет замкнутые поры, объём которых в зависимости от вида резины колеблется от 20 до 80 % её общего объёма. Эти резины имеют ряд преимуществ по сравнению с непористыми резинами: повышенные мягкость, гибкость, высокие амортизационные свойства, упругость.
Дата добавления: 2019-02-22; просмотров: 1219; Мы поможем в написании вашей работы! |
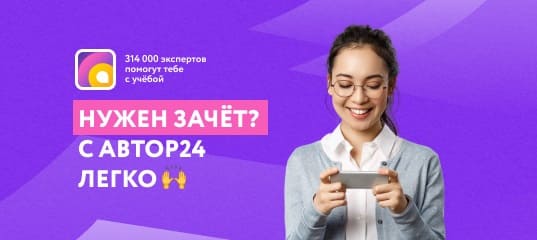
Мы поможем в написании ваших работ!