Области применения алюминиевых сплавов.
Сплавы АД и АД-1. Элементы конструкций и деталей, не несущие нагрузки и требующие применения материала с высокими пластическими свойствами, хорошей свариваемостью, высоким сопротивлением коррозии и высокой тепло- и электропроводностью. Из этих сплавов изготавливаются трубопроводы разного назначения, витражи, перегородки в комнатах, электропровода, двери, оконные рамы, корпусы часов, ювелирные поделки, палубные надстройки морских и речных судов, обои, обертки, баки и т. д.
Алюминиевые сплавы применяются также в виде заклепок для средненагружаемых конструкций из алюминиевых сплавов с повышенной коррозионной стойкостью и для конструкций из магниевых сплавов.
Сплав АМц. Сварные детали, трубопроводы, емкости для жидкостей и другие малонагружаемые детали и изделия; изделия, изготовляемые глубокой вытяжкой, гибкой и т. д., а также проволока для заклепок.
Заклепки для средненагружаемых конструкций из алюминиевых сплавов с повышенной коррозионной стойкостью и для конструкций из магниевых сплавов.
Сплав АМг2. Сварные и клепаные детали, трубопроводы разного назначения, емкости для жидкостей и другие средне- и малонагружаемые детали и изделия. Также изготовляются витражи, перегородки в комнатах, электропровода, двери, оконные рамы, корпусы часов, палубные надстройки морских и речных судов, обои, обертки, баки и т. д. Проволока применяется в качестве присадочного материала и для изготовления заклепок.
|
|
Сплав АМгЗ. Сварные малонагружаемые детали и конструкции, с высокой коррозионной стойкостью, трубопроводы, емкости для жидкостей и другие средне-нагружаемые детали и изделия.
Сплавы АМг5, АМг5В и АМг6. Сварные и клепаные средненагружаемые детали и конструкции, требующие высокой коррозионной стойкости; трубопроводы, емкости для жидкостей и другие детали и изделия.
Сплав АМг5П. Заклепки, применяемые для клепки средненагружаемых конструкций из алюминиевых сплавов с повышенной коррозионной стойкостью и конструкций из магниевых сплавов. Заклепки ставятся в конструкцию в отожженном состоянии.
Сплавы Д1 и Д1П. Различные детали и элементы конструкций средней прочности. Производство полуфабрикатов из сплава Д1 заметно сокращается. Заклепки ставятся в конструкцию свежезакаленными (не позднее 2 ч. после закалки).
Сплав Д6. Различные несущие детали конструкций, за исключением штамповок. Сплав аналогичен сплаву Д16, применение его сильно сокращается.
Сплавы Д16 и Д16П. В конструкциях средней и повышенной прочности, требующих повышенной долговечности при переменных нагрузках; в строительных конструкциях, не требующих высокой коррозионной стойкости, для изготовления ферм, а также для различных высоконагружаемых деталей и элементов-конструкций, за исключением штамповок и поковок. В сильно нагружаемых деталях сплав Д16 заменяется сплавом В95. Заклепки ставятся в конструкцию и в свежезакаленном состоянии (не позднее 20—30 мин после закалки).
|
|
Ставится в конструкциях, работающих при температуре до 250° С.
Сплав Д18П. Один из основных заклепочных материалов для клепки нагружаемых конструкций из алюминиевых сплавов, работающих при температуре не выше 100° С.
В конструкцию заклепки ставятся после закалки и естественного старения в течение не менее 4 суток.
Сплав АВ. Детали и элементы средненагружаемых конструкций, изготовление которых требует высокой пластичности в холодном и горячем состоянии.
Сплавы АД31 и АД3З. Применяются для клееных и клепаных конструкций сложной формы, а также для конструкций, где требуется повышенный предел текучести, и для прессованных изделий сложной формы (полые профили).
Сплав В65. Заклепки для клепки нагружаемых конструкций из алюминиевых сплавов, работающих при температуре не выше 100°С. Заклепки в конструкции можно ставить в любое время после закалки и старения. Эта особенность составляет преимущество сплава В65 перед сплавами Д1 и Д16, которые он заменяет.
|
|
Сплав АК2. Поршни двигателей внутреннего сгорания, работающие при повышенных температурах.
Сплавы АК4 и АК4-1. Лопатки компрессоров, крыльчатки, диски и кольца турбореактивных и турбовинтовых двигателей, поршни двигателей и другие кованые детали, работающие при повышенных температурах.
Сплавы АК6 и АК6-1. Штампованные и кованые детали сложной формы и средней прочности (крыльчатки большие и малые, подмоторные рамы, фитинги, качалки, крепежные детали).
Сплав АК8. Высоконагружаемые штампованные и кованые детали, подмоторные рамы, стыковые узлы, пояса лонжеронов. Трудности, связанные с горячей обработкой давлением, ограничивают применение этого сплава.
Сплав В93. Поковки и штамповки.
Сплав В94. Заклепки для сильнонагружаемых конструкций, работающих при температуре до 125° С.
Сплавы В95 и В95-1. Нагружаемые конструкции, работающие длительное время при температурах не выше 100 – 120°С. Обшивка, стрингеры, шпангоуты, лонжероны самолетов, силовой каркас клепаных строительных сооружений. Из сплава В95-1 изготовляются штампованные лопасти.
Сплавы В96 и В96ц. Прессованные и кованые изделия.
Сплав ВД17. Лопатки осевых компрессоров, крыльчатки, диски и кольца турбореактивных и турбовинтовых двигателей, поршни двигателей и другие кованые детали, работающие при повышенных температурах.
|
|
Сплав Д19. В конструкциях, работающих до 250°C; применяется сплав в искусственно состаренном состоянии.
Сплав Д19П. Заклепки для нагружаемых конструкций, работающих при температуре от 125 до 250° С.
Сплав Д20. Поковки и штамповки сложной формы, катаные листы, прессованные полуфабрикаты; нагружаемые детали и сварные изделия, работающие при 200—300° С. Лопатки, диски осевых компрессоров, сварные емкости и другие детали, работающие при повышенных температурах.
Сплав Д21. Поковки и штамповки.
Сплав Д23. Листы, плиты, поковки, штамповки, прессованные изделия, проволока. Заклепки ставятся в конструкцию в закаленном состоянии с последующим искусственным старением. Заклепки для сильнонагружаемых конструкций, работающих длительное время при температурах до 180°C. Применяется для сильно нагружаемых деталей, кратковременно и длительно работающих при температурах 160—180° С.
Область применения алюминия:
Благодаря уникальным свойствам алюминия: долговечности, легкости, эстетичности и, главное, безопасности, мир давно отдал ему предпочтение. Этот материал используется для отделки не только фасадов зданий, но и внутренних помещений: из алюминия делаются офисные перегородки, внутренние двери, витражи и пр.
Титан.
Титан относится к числу наиболее распространённых в природе элементов, его содержание в земной коре составляет 0,6 весовых %. Встречается главным образом в виде двуокиси TiO2 или её соединений - титанатов. Известно свыше 60 минералов, в состав которых входит титан. Температура плавления титана составляет 1668±3°C. По своей тугоплавкости титан среди основных конструкционных металлов находится на первом месте.
Промышленным способом титан производят в виде титановой губки, которая маркируется по твердости специально выплавленных из нее образцов. Полученный в результате последовательного дробления губки, прессования, спекания и переплавки брикетов технический титан маркируется в зависимости от содержания примесей.
Титановая губка имеет марки: ТГ-100, ТГ-110, ТГ-120, ТГ-130, ТГ-150,
Марки технического титана: ВТ1-0, ВТ1-00, ВТ1-1, ВТ1-2.
Титан относится к легким металлам, его плотность при 0°C составляет 4,517Мг/м3, а при 100°C – 4,506Мг/м3. Титан обладает высокой прочностью. Его отличает способность сопротивляться разрушению, а также необратимому изменению формы (пластические деформации). Титан является твердым металлом. Он в 12 раз тверже алюминия, в 4 раза железа и меди. Кислород, азот, а также пластическая деформация повышают сопротивление ползучести. Специально обработанный титан имеет высокий предел текучести. Чем выше предел текучести материала, тем лучше детали из этого металла сопротивляются эксплуатационным нагрузкам. Предел текучести у титана почти в 18 раз выше, чем у алюминия. Удельная прочность сплавов титана может быть повышена в 1,5 – 2 раза. Его высокие механические свойства хорошо сохраняются при температурах вплоть до нескольких сот градусов.
Титан обладает высокими прочностными характеристиками и удельной прочностью в условиях глубокого холода.
Технический титан хорошо обрабатывается давлением при 20-25 °С и повышенных температурах. Из него изготовляют все виды прессованного и катаного полуфабриката (листы, трубы, проволоку, поковки и др.). Ковку проводят при температуре 1000-750 °С, горячую прокатку - на 100 °С ниже температуры ковки. Горячей прокаткой получают листы толщиной более 6 мм, листы меньшей толщины изготовляют холодной прокаткой или с нагревом до 650-700 °С. Титин прокатывают в фольгу толщиной до 0,01мм. Температура прессования титана составляет 950-1000 °С. Титан хорошо сваривается аргоновой, дуговой и всеми видами контактной сварки. Сварной шов обладает хорошим сочетанием прочности и пластичности. Прочность шва составляет 90 % прочности основного металла.
Титан проявляет исключительную стойкость в условиях кавитации, т.е. при усиленной «бомбардировке» металла в жидкой среде пузырьками воздуха, которые образуются при быстром движении или вращении металлической детали в жидкой среде. Эти пузырьки воздуха, лопаясь на поверхности металла, вызывают очень сильные микро удары жидкости о поверхность движущегося тела. Они быстро разрушают многие материалы, и металлы в том числе. Испытания в морской воде быстровращающихся дисков из титана и других металлов показали, что при вращении в течение двух месяцев титановый диск практически не потерял в массе. Внешние края его, где скорость вращения, а, следовательно, и кавитация максимальны, не изменились. Диски из других материалов не выдержали испытания: у всех внешние края оказались поврежденными, а многие из них вовсе разрушились.
Титан и сплавы на его основе проявляют эффект «памяти» формы. Сплавы титана с никелем, и особенно с никелем и водородом «запоминают» форму изделия, которую из них сделали при определенной температуре. Если такое изделие потом деформировать, например, свернуть в пружину, изогнуть, то оно останется в таком положении на долгое время. После нагревания до той температуры, при которой это изделие было сделано, оно принимает первоначальную форму. Это свойство титана широко используется в космической технике - разворачивание космических антенн. Медики вводят подобные пружины в виде проволоки в сосуды для последующего их увеличения в объёме и расширения сосудов.
Титан обладает сравнительно низкой теплопроводностью 22,07Вт/(мК), что приблизительно в 3 раза ниже теплопроводности железа, в 7 раз для магния, в 17–20 раз для алюминия и меди. Соответственно и коэффициент линейного термического расширения у титана ниже, чем у других конструкционных материалов: при 200С он в 1,5 раза ниже, чем у железа, в 2 - у меди и почти в 3 - у алюминия. Таким образом, титан – плохой проводник электричества и тепла. Но при низких температурах титан проявляет сверхпроводящие свойства. Титан является парамагнитным металлом. Он не намагничивается, как железо, в магнитном поле, но и не выталкивается из него, как медь. Его магнитная восприимчивость очень слаба, это свойство можно использовать при строительстве, например, немагнитных кораблей, приборов, аппаратов. Немагнитность титана, представляет интерес для радиоэлектроники и электротехники.
Титан обладает высокой стойкостью к воздействию окислительных и коррозионных сред благодаря образованию на поверхности прочной оксидной пленки. Низкий модуль упругости, ползучесть, невысокая жаропрочность титана не позволяют применять его в качестве конструкционного материала для изготовления ответственных деталей. С повышением температуры происходит резкое снижение прочности титана, что обусловлено низкой температурой его рекристаллизации. Прочность титана можно повысить пластическим деформированием.
В чистом виде титан достаточно пластичен, имеет высокую удельную прочность, стоек к коррозии. Механические свойства титана определяются степенью его чистоты. Примеси кислорода, азота и углерода, образующие различные соединения с титаном, оказывают существенное влияние на его свойства. К числу наиболее вредных примесей относится водород, обуславливающий охрупчивание титана.
Титан плохо обрабатывается резанием, налипает на инструмент, что приводит к его быстрому износу. Для обработки титана требуется инструмент из быстрорежущей стали и твердых сплавов, малые скорости резания при большой подаче и глубине резания, интенсивное охлаждение. Недостатком титана является также низкая антифрикционность.
Технический титан применяют в химической промышленности, судостроении, ядерной энергетике. Для улучшения эксплуатационных характеристик титан легируют различными элементами.
Титановые сплавы. Достоинством титановых сплавов по сравнению с титаном являются более высокие прочность и жаропрочность при достаточно хорошей пластичности, высокой коррозионной стойкости и малой плотности.
Одним из важных преимуществ титановых сплавов перед алюминиевыми и магниевыми сплавами является жаропрочность, которая в условиях практического применения с избытком компенсирует разницу в плотности (магний 1,8, алюминий 2,7, титан 4,5). Превосходство титановых сплавов над алюминиевыми и магниевыми сплавами особенно резко проявляется при температурах выше 300°C, поскольку при повышении температуры прочность алюминиевых и магниевых сплавов сильно уменьшается, а прочность титановых сплавов остается высокой.
Титановые сплавы по удельной прочности (прочности, отнесенной к плотности) превосходят большинство нержавеющих и теплостойких сталей при температурах до 400 – 500 °C. Если учесть к тому же, что в большинстве случаев в реальных конструкциях не удается полностью использовать прочность сталей из-за необходимости сохранения жесткости или определенной аэродинамической формы изделия (например, профиль лопатки компрессора), то окажется, что при замене стальных деталей титановыми деталями можно получить значительную экономию в массе.
Недостатками титана являются его активное взаимодействие с атмосферными газами, склонность к водородной хрупкости. Азот, углерод, кислород и водород, упрочняя титан, снижают его пластичность, сопротивление коррозии, свариваемость.
Титан имеет две аллотропические модификации. Низкотемпературная модификация α-Ti со структурой типа гексагональной плотневшей упаковки при 882,5°C переходит в высокотемпературную модификацию β-Ti с объемно центрированной кубической структурой.
Легирующие элементы подразделяют в зависимости от их влияния на температуру полиморфного превращения титана (882,5°С) на две основные группы. Элементы α - стабилизаторы, расширяющие область существования α - фазы и повышающие температуру превращения – Al, Ga, Ge, La, С, О, N и элементы β - стабилизаторы, суживающие α - область и снижающие температуру полиморфного превращения, - V, Nb, Та, Zr, W, Mo, Cr, Mn, Fe, Co, Si, Ag.
Нейтральные элементы (Sn, Zr, Hf) мало влияют на температуру полиморфного превращения. Наибольшее практическое значение имеют олово и цирконий. Олово упрочняет титановые сплавы без заметного снижения пластичности, повышает жаропрочность; цирконий увеличивает предел ползучести и длительную прочность.
По технологии изготовления титановые сплавы подразделяются на деформируемые, литейные и порошковые.
По механическим свойствам сплавы классифицируют на сплавы нормальной прочности, высокопрочные, жаропрочные, повышенной пластичности.
По способности упрочняться с помощью термической обработки сплавы делятся на упрочняемые и неупрочняемые термической обработкой.
По структуре в отожженном состоянии сплавы классифицируются
на α-, псевдо-α, α + β, псевдо- β и β -сплавы.
Сплавы с α -структурой. К этой группе сплавов относят и технический титан. Это сплавы нормальной прочности при 20-25 °С, обладающие высоким сопротивлением разрушению при повышенных (350-500 °С) и криогенных температурах. Сплавы имеют высокую термическую стабильность свойств и обладают отличной свариваемостью в аргоновой дуге, а также всеми видами контактной и электронно-лучевой сварки. При этом прочность сварного шва составляет 90 % прочности основного сплава. Обрабатываемость резанием удовлетворительная. α-сплавы не упрочняются термической обработкой и применяются в отожженном состоянии. Сплавы с цирконием наиболее технологичны, но это самые дорогие из α-сплавов. В горячем состоянии сплавы куют, прокатывают и штампуют. Из сплава ПТ7М изготовляют горяче- и холоднокатаные трубы. Сплавы поставляют в виде прутков сортового проката, поковок, труб, проволоки. Они предназначены для изготовления деталей, работающих в широком диапазоне температур: от криогенных до 500 °С.
Псевдо- α-сплавы имеют преимущественно α—структуру. Легирование сплавов β -стабиливаторами (Мп, V, Nb, Mo) приводит к образованию 1-5 % β -фазы которая придаёт сплавам технологичность, пластичность при сохранении достоинств α-сплавов. Сплавы с низким содержанием алюминия (2-3 %) обрабатываются давлением в холодном состоянии и только при изготовлении деталей сложной формы подогреваются до 500—700 °С (ОТ4, ОТ4-1). На жаропрочность сплавов благоприятно влияют цирконий и кремний. Цирконий способствует увеличению растворимости β -стабилизаторов в α-фазе и повышает температуру рекристаллизации. Кремний повышает жаропрочность вследствие образования тонкодисперсных силицидов, трудно растворимых в α-фазе. Псевдо- α-сплавы легированные Zr, V, Mo, Nb, Si, используются в изделиях, работающих при наиболее высоких температурах. Недостатком этих сплавов является склонность к водородной хрупкости.
Двухфазные (α + β)-сплавы. Наибольшее упрочнение достигается при легировании титана эвтектоидообразующими β -стабилизаторами Fe, Сг, Мn и изоморфными Mo, V, Nb стабилизаторами. Ванадий и ниобий упрочняют сплавы слабее других, но и меньше снижают пластичность. Двухфазные сплавы упрочняются с помощью термической обработки закалки и старения. В отожженном и закаленном состояниях они имеют хорошую пластичность, а после старения приобретают высокую прочность и жаропрочность. Чем больше β -фазы содержится в структуре сплава, тем он прочнее в отожженном состоянии и сильнее упрочняется при термической обработке.
По структуре после закалки двухфазные сплавы подразделяют на два класса: мартенситный и переходный.
Сплавы мартенситного класса менее легированы и в равновесном состоянии содержат сравнительно немного β -фазы (5-25 масс. %). К этому классу относятся высокопрочные сплавы ВТ6, ВТ14, ВТ16 и жаропрочные сплавы ВТ8, ВТ9, ВТЗ-1. Сплавы переходного класса содержат больше легирующих элементов и соответственно больше β-фазы (25-50 масс. %). Наличие большого количества B-фазы обеспечивает сплавам переходного класса самую высокую прочность среди (α + β)-сплавов. Например, сплав ВТ22 (50 масс. % β-фазы) имеет после отжига такое же временное сопротивление, как сплав ВТ6 после закалки и старения. Двухфазные сплавы удовлетворительно обрабатываются резанием и свариваются. Двухфазные сплавы куются, штампуются и прокапываются легче, чем сплавы с α -структурой. Они поставляются в виде поковок, штамповок, прутков, листов, ленты.
Однофазные β-сплавы не имеют промышленного значения, так как для получения устойчивой β-структуры сплавы должны быть легированы большим количеством изоморфных β--стабилизаторов (V, Mo, Nb, Та), которые имеют высокую стоимость и обладающих высокой плотностью.
Псевдо-β-сплавы. Это высоколегированные в основном β-стабилизаторами сплавы. Суммарное количество легирующих элементов в них, как правило, превышает 20 масс. %. Наиболее часто их легируют Mo, V, Сг, реже Fe, Zr, Sn. Алюминий присутствует почти во всех сплавах в небольшом количестве (~ 3%). В равновесном состоянии они имеют в основном β-структуру и небольшое количество α-фазы. Наибольшее распространение в промышленности получил сплав ВТ15 (~3 % А1, ~8% Мо и 11 % Сг). Этот сплав выпускается в виде полос, листов, прутков, поковок и рекомендуется для длительной работы при температуре до 350 оС.
Литейные титановые сплавы. Небольшой температурный интервал кристаллизации обеспечивает высокую жидкотекучесть и плотность отливок из титановых сплавов. Они отличаются малой склонностью к образованию горячих трещин; линейная усадка в 1 %; объемная усадка 3 %. Плавку и заливку сплавов на основе титана осуществляют в среде нейтральных газов или в вакууме в связи с их высокой химической активностью при нагреве. Отливки изготовляют методом фасонного литья в чугунные, стальные и специальные формы. Для получения высококачественных сложных титановых отливок необходим комплексный подход к выбору оптимальных режимов литья как при плавке и заливке металла, так и при формировании отливки в литейной форме. Литейные сплавы обладают более низкими механическими свойствами, чем соответствующие деформируемые. Упрочняющая термическая обработка не применяется, так как резко снижает пластичность сплавов.
Порошковые титановые сплавы. Высокая стоимость изготовления и трудность механической обработки сплавов на основе титана являются серьезным препятствием на пути их широкого применения. Методы порошковой технологии позволяют повысить коэффициент использования металла путем уменьшения отходов при механической обработке и открывают потенциальные возможности получения готовых деталей для конструкций летательных аппаратов и двигателей.
Получение порошков из сплавов на основе титана является сложной проблемой вследствие вредного влияния различных примесей. Высокая химическая активность расплавленного титана исключает применение большинства огнеупоров в качестве материала для тиглей. Использование современных методов получения легированных порошков дуговой плавкой с вращающимся анодом и неподвижным вольфрамовым катодом, электроплазменной плавкой либо распылением в вакууме и других позволяет исключить загрязнения. Повышение качества полуфабрикатов и готовых деталей сложных форм может быть достигнуто в результате использования новых прогрессивных методов, таких, как горячее компактирование гранул, горячее изостатическое прессование легированных порошков (ГИП) с последующим спеканием в вакуума и др. Для изготовления деталей методами порошковой технологии используют сплавы ВТ5, ВТ5-1, ОТ4, ВТЗ-1.
Марки титановых сплавов.
Титановые литейные сплавы: ВТ14Л, ВТ1Л, ВТ20Л, ВТ21Л, ВТ3-1Л, ВТ5Л, ВТ6Л, ВТ9Л.
Титановые деформируемые сплавы: 14, 2В, 3М, 5В, АТ-6, АТ3, ВТ14, ВТ15, ВТ16, ВТ18, ВТ18у, ВТ20, ВТ20-1св, ВТ20-2св, ВТ22, ВТ23, ВТ2св, ВТ3-1, ВТ5, ВТ5-1, ВТ6, ВТ6С, ВТ6св, ВТ8, ВТ9, ОТ4, ОТ4-0, ОТ4-1, ОТ4-1св, ОТ4св, ПТ-1М, ПТ-3В, ПТ-7М, Пт-7св, СПТ-2, ТС6.
В качестве примера рассмотрен химический состав сплава ВТ15 "Марочник стали и сплавов (www.splav.kharkov.com)". Титановый деформируемый сплав для изготовления кавитационно стойких изделий; класс по структуре псевдо β. Химический состав в масс. % материала ВТ15 (ОСТ 1-90013 – 81).
Fe | C | Si | Cr | Mo | N | Ti | Al | O | H |
до 0.3 | до 0.1 | до 0.15 | 9.5- 11 | 6.8 - 8 | до 0.05 | 76.8 - 81.4 | 2.3 - 3.6 | до 0.12 | до 0.012 |
Области применения титана.
Титановые сплавы отличающиеся сочетанием ряда ценных свойств, перспективны для применения во многих областях современной техники высокая стоимость тина его сплавов во многих случаях компенсируется их большей работоспособностью, а в некоторых случаях они являются единственным материалом, из которого можно изготовить оборудование или конструкции, способные работать в данных конкретных условиях. Титановые сплавы широко применяют в авиационной технике. Титан и его сплавы применяют в химической, нефтехимической, целлюлозно-бумажной и пищевой промышленности, в цветной металлургии, энергомашиностроении, электронике, ядерной технике, гальванотехнике, при производстве вооружения, для изготовления броневых плит, опреснительных установок, деталей гоночных автомобилей, спортинвентаря (клюшки для гольфа), деталей ручных часов и даже украшений. Азотирование титана приводит к образованию его поверхности золотистой пленки, по красоте не уступающей настоящему золоту.
При существующих высоких ценах на титан его применяют преимущественно для производства военного оборудования, где главная роль принадлежит не стоимости, а техническим характеристикам. По мере снижения цен на титан и роста его производства области применения титана постоянно расширяются.
Авиация. В области самолетостроения и производства авиационных двигателей титан все больше вытесняет алюминий и нержавеющую сталь. С повышением температуры алюминий быстро утрачивает свою прочность. С другой стороны, титан обладает явным преимуществом в отношении прочности при температуре до 430°C, а повышенные температуры такого порядка возникают при больших скоростях благодаря аэродинамическому нагреванию. Преимущество замены стали титаном в авиации заключается в снижении веса без потери прочности. При постройке реактивных двигателей титан применяется преимущественно для изготовления лопаток компрессора, дисков турбины и многих других штампованных деталей. Здесь титан вытесняет нержавеющую и термически обрабатываемую легированную стали. Экономия в весе двигателя в один килограмм позволяет сберегать до 10кг в общем весе самолета благодаря облегчению фюзеляжа. Листовой титан применяется для изготовления всевозможных кожухов, защитных оболочек кабелей и направляющих для снарядов. Из листов легированного титана изготовляются различные элементы жесткости, шпангоуты фюзеляжа, нервюры.
Военно-морской флот. Малый удельный вес металла в сочетании с коррозионной стойкостью повышает маневренность и дальность действия кораблей, а также снижает расходы по уходу за материальной частью и ее ремонту. Применение титана в военно-морском деле включает изготовление выхлопных глушителей для дизельных двигателей подводных лодок, дисков измерительных приборов, тонкостенных труб для конденсаторов и теплообменников. По мнению специалистов, титан, как никакой другой металл, способен увеличить срок службы выхлопных глушителей на подводных лодках
Артиллерия. Проходят испытания, изготовленные из титана орудийные станки, крестовины лафетов и цилиндры противооткатных приспособлений. Широкое применение титан может получить при производстве управляемых снарядов и ракет.
Транспорт.Замена конструкционных материалов, потребляемых в настоящее время предприятиями транспортного машиностроения, титаном должна привести к снижению расхода топлива, росту полезной грузоподъемности, повышению предела усталости деталей кривошипно-шатунных механизмов и т. п. На железных дорогах исключительно важно снизить мертвый груз. Существенное уменьшение общего веса подвижного состава за счет применения титана позволит сэкономить в тяге, уменьшить габариты шеек и букс.
Химическая промышленность. При производстве оборудования для химической промышленности значение имеет коррозионная стойкость титана, а также то, что титан имеет невысокую плотность (4,5г/см3) и повышенную прочность.
Строительство. Благодаря высокой стойкости к солнечной радиации и воздействию атмосферы, даже в условиях жаркого влажного морского климата, титан и его сплавы считают выдающимся архитектурно-строительным материалом. При этом важное значение имеет то обстоятельство, что титан обладает самым близким из «строительных» металлов коэффициентом линейного термического расширения по отношению к аналогичной характеристике стекла, бетона, кирпича и камня.
Титановый прокат (титановый лист, титановая плита, титановая труба, титановый пруток, титановая проволока) применяют в строительстве и архитектуре для изготовления наружной обшивки, перегородок, покрытия крыш, облицовки колонн, козырьков, навесов, внутренней отделки зданий, а также для монументальной архитектуры. В Москве из титановых сплавов изготовлены два монументальных памятника: в честь запуска первого искусственного спутника Земли и первого космонавта Ю.А. Гагарина.
Биологические имплантантов. Титан является наилучшим материалом, биологически совместимым с тканями человека. Поэтому титан широко применяется в медицине для изготовления различного рода хирургических имплантантов (протезов суставов, стоматологических коронок и мостов, пластин и т.д.), а также хирургического инструмента (скальпелей, пинцетов и т.п.) и медицинской аппаратуры (центрифуг сепарации крови).
Прочие области применения титана. Применение титана целесообразно в пищевой, нефтяной и электротехнической промышленности, а также для изготовления хирургических инструментов и в самой хирургии.
Столы для подготовки пищи, пропарочные столы, изготовленные из титана, по качествам превосходят стальные изделия.
В нефте- и газобурильной областях серьезное значение имеет борьба с коррозией, поэтому применение титана позволит реже заменять корродирующие штанги оборудования. В каталитическом производстве и для изготовления нефтепроводов желательно применять титан, сохраняющий механические свойства при высокой температуре и обладающий хорошей коррозионной устойчивостью. В электропромышленности титан можно применить для бронирования кабелей благодаря хорошей удельной прочности, высокому электрическому сопротивлению и немагнитным свойствам. В различных отраслях промышленности начинают применять крепежные детали той или иной формы, изготовленные из титана. Дальнейшее расширение применения титана возможно для изготовления хирургических инструментов главным образом благодаря его коррозионной стойкости. Инструменты из титана в этом отношении превосходят обычные хирургические инструменты при многократном кипячении или обработке в автоклаве.
Медь и медные сплавы.
Медь (Cu) — широко применяемый в электротехнике и в машиностроении материал. Мировое производство меди растет и соизмеримо с объемами производства алюминия, хотя содержание меди в земной коре невелико (0,01%).
Медь характеризуется высокой электропроводностью, теплопроводностью, коррозионной стойкостью и хорошими пластическими свойствами при обработке давлением, способностью образовывать разнообразные сплавы с другими цветными металлами, обладающими многими ценными физическими и механическими свойствами. Существенные недостатки, свойственные меди: низкие литейные свойства, плохая обрабатываемость резанием, относительно невысокие прочностные характеристики.
Медь применяется в различных отраслях промышленности в виде полуфабрикатов (листов, лент, труб, прутков и проволоки) или фасонных отливок. В настоящее время общий объем выплавки меди занимает второе (после алюминия) место среди цветных металлов. Степень чистоты меди определяется способом её производства. Электролитическим рафинированием или огненным рафинированием получают медь с содержанием основного вещества не менее 99.99 % (табл. 4.8).
Около 50% всей выплавляемой меди расходуется электропромышленностью. Медь используется в производстве кабельных изделий, контактных проводов, электрогенераторов, моторов, распределительных устройств, телефонного и телеграфного оборудования и радиоаппаратуры. Многочисленные сплавы на медной основе используются в машиностроении, судостроении (25—35% всей производимой меди). Медь служит хорошим материалом для производства химической аппаратуры, вакуум-аппаратов, теплообменников. Медь используется также в строительстве. Соли меди применяются в приготовлении пигментов, препаратов для сельского хозяйства, а также в производстве искусственных кож и мехов. Значительное количество меди используется в промышленности в виде полуфабрикатов из меди и сплавов на медной основе.
Таблица. 4.8.
Способы получения меди, марки меди и содержание основных примесей.
Способ получения | Марка | Cu, не менее | Bi, не более | Sb, не более | As, не более | Fe,не более | Ni, не более |
Электролитическое рафинирование | МООк МОк М1к | 99,99 99,97 99,95 | 0,0003х 0,0005 0,001 | 0,0004 0,001 0,002 | 0,0005 0,001 0,002 | 0,001 0,001 0,003 | 0,002 0,001 0,002 |
Огневое рафинирование | МООб МОб | 99,99 99,97 | 0,0005 0,0005 | 0,001 0,001 | 0,001 0,001 | 0,001 0,003 | 0,001 0,002 |
Переплавка катодов | МОО МОО М1 | 99,96 99,93 99,90 | 0,0005 0,0005 0,001 | 0,001 0,002 0,002 | 0,001 0,001 0,002 | 0,001 0,004 0,005 | 0,001 0,002 0,002 |
Переплавка с раскислением | М1р М1ф М2р М3р | 99,90 99,90 99,70 99,50 | 0,001 0,001 0,002 0,003 | 0,002 0,002 0,005 0,05 | 0,002 0,002 0,01 0,05 | 0,005 0,005 0,05 0,05 | 0,002 0,002 0,2 0,2 |
Огневое рафинирование отходов | М2 М3 | 99,70 99,50 | 0,002 0,003 | 0,005 0,05 | 0,01 0,01 | 0,05 0,05 | 0,2 0,2 |
Примеси оказывают существенное влияние на физико-механические характеристики меди. Их можно условно разделить на следующие группы: снижающие прочность при горячей и холодной обработке давлением (О2, Pb, S, Se, Fe, Sb, Bi); улучшающие обрабатываемость резанием (Se, Pb, Те, Si); понижающие тепло- и электропроводность (Pb, As, Sb, Fe, Al, P); снижающие коррозионную стойкость (О2, Fe); повышающие коррозионную стойкость (Be, Al); повышающие прочность меди (Fe, P).
В зависимости от добавок к меди получают сплавы с различными свойствами (высокопрочные, антифрикционные, химически стойкие и др.). Сплавы на медной основе делятся на две большие группы: латуни и бронзы.
![]() | Рис.4.3. Фото силового кабеля, изготовленного из меди. Самое большое применение меди, производство кабелей и проводов. |
Латуни.
Латунями являются сплавы меди с цинком, в которых меди содержится от 60 до 90 масс %, а цинка от 40 до 10 масс. %.
Сплавы подразделяются на простые, состоящие только из меди и цинка, и специальные — многокомпонентные, с добавками алюминия, марганца, никеля, олова, кремния, железа и других элементов. Латуни характеризуются высокими технологическими свойствами: хорошо отливаются, прокатываются, штампуются и легко обрабатываются. Изготовляемые из латуни полуфабрикаты — листы, трубы и литые изделия – нашли широкое применение в машиностроении, военной технике, оптике и приборостроении, в целлюлозно-бумажной промышленности и др.
Специальные многокомпонентные латуни с различными добавками обладают повышенной пластичностью, более высоким пределом прочности и большей твердостью, чем простые латуни.
В зависимости от основного легирующего компонента различают алюминиевые, кремнистые, марганцевые, никелевые, оловянные, свинцовые и другие латуни.
Алюминиевым латуням свойственны повышенные механические характеристики и коррозионная стойкость. В деформируемых латунях содержится до 4 % алюминия, в литейных до 7 %. Характерные представители алюминиевых латуней: ЛА 85-0,5, ЛА 77-2, ЛА Мш 77-2-0,05.
Высокой коррозионной стойкостью в атмосферных условиях и в морской воде отличаются кремнистые латуни.
При содержании кремния до 3% они обладают высокими механическими свойствами и достаточной пластичностью: при увеличении содержания кремния свыше 4% повышается твердость сплавов, но уменьшается пластичность. В машиностроении применяют кремнистые латуни марок ЛК 80-3, ЛК С65-1,5-3 и другие.
Широкое применение в судостроении получили марганцевые латуни с высокими механическими свойствами, обрабатывающиеся давлением в горячем и холодном состоянии, стойкие к коррозии в морской воде, хлоридах и перегретом паре. При легировании марганцем структура сплава изменяется незначительно. Представители этой группы сплавов: ЛМц 58-2, ЛМцА 57-3-1.
Никелевые латуни наиболее стойки к растворению цинка из поверхностного слоя изделия, при котором он обогащается медью, образующей гальваническую пару с частицами деталей, объединенных цинком. Такие сплавы имеют высокие механические свойства, хорошо обрабатываются давлением в горячем и холодном состоянии. В машиностроении распространены никелевые латуни марки ЛН 65-5 и другие.
Оловянные латуни, обладающие повышенной коррозионной стойкостью в морской и пресной воде, широко применяют в судостроении. Эти латуни хорошо обрабатываются, имеют повышенные антифрикционные свойства. Типичные представители этой группы: ЛО 90-1, ЛО 70-1, ЛО 62-1.
![]() | Рис. 4.4. Фото лома латуни, сантехника. |
Свинцовым латуням свойственны повышенные антифрикционные свойства и обрабатываемость резанием. Свинец в этих сплавах присутствует в виде самостоятельной фазы, практически не изменяющей структуры сплава. В машиностроении применяют свинцовые латуни марок ЛС 63-3, ЛС 74-3, ЛС 60-1 и другие.
Латуни перерабатывают в изделия обработкой давлением, резанием, литьем. Некоторые свойства деформируемых и литейных латуней и область их применения приведены в таблицах 4.9. и 4.10.
Таблица 4.9.
Физические и технологические свойства простых деформируемых латуней.
Марка
| Л 96 | Л 90 | Л 85 | Л 80 | Л 70 | Л 68 | Л 62 | |
Температура плавления в 0C
| 1070 | 1045 | 1025 | 1099 | 950 | 938 | 905 | |
Плотность в Г/см3 | 8,85 | 8,78 | 8,75 | 8,06 | 8,62 | 8,60 | 8,43 | |
Модуль упругости в кгc/мм2 | мягкой латуни | - | - | - | 10600 | - | 11000 | 10000 |
твердой латуни | 11400 | 10500 | 10500 | 11400 | 11200 | 11500 | - | |
Коэффициент линейного расширения Х 106 1/0C | 17,0 | 17,0 | 18,7 | 18,8 | 18,9 | 19,0 | 20,6 | |
Удельная теплоемкость в кал/г×0C | 0,093 | 0,09 | 0,092 | 0,093 | 0,09 | 0,093 | 0,092 | |
Теплопроводность в кал/см×сек×0C
| 0,592 | 0,40 | 0,36 | 0,34 | 0,29 | 0,28 | 0,26 | |
Температура горячей обработки в 0C | 700-850 | 700-850 | 750-850 | 750-850 | 750-850 | 750-850 | 750-850 | |
Температура отжига в 0C | 450-650 | 450-650 | 450-650 | 450-650 | 450-650 | 450-650 | 450-650 |
Таблица 4.10.
Состав и назначение латуни разных марок.
Марка латуни | Состав | Назначение |
Л96 | 95-97% Cu, остальное Zn | Радиаторные трубки |
Л90 | 88-91% Cu, остальное Zn | Листы и ленты для плакировки |
Л80 | 79-81% Cu, остальное Zn | Проволочные сетки в целлюлозно-бумажной промышленности, сильфоны |
Л68 | 67-70% Cu, остальное Zn | Изделия, получаемые холодной штамповкой и глубокой вытяжкой |
Л63 | 62-65% Cu, остальное Zn | Полосы, листы, лента, проволока, трубы, прутки |
ЛА77-2 | 76-79% Cu, 1,75-2,5% Al, остальное Zn | Конденсаторные трубки |
ЛАЖ60-1-1 | 58-61% Cu, 0,75-1,5% Al, 0,75-1,5% Fe, 0,1-0,6% Mn, остальное Zn | Трубы и прутки |
ЛАЖМц66-6-3-2 | 64-68% Cu, 6-7% Al, 2-4% Fe, 1,5-2,5% Mn, остальное Zn | Литые массивные червячные винты, гайки нажимных винтов |
ЛАН59-3-2 | 57-60% Cu, 2,5-3,5% Al, 2-3% Ni, остальное Zn | Трубы и прутки |
ЛЖМц59-1-1 | 57-60% Cu, 0,6-1,2% Fe, 0,5-0,8% Mn, 0,1-0,4% Al, 0,3-0,7% Sn, остальное Zn | Полосы, проволока, прутки и трубы |
ЛН65-5 | 64-67% Cu, 5-6,5% Ni, остальное Zn | Манометрические трубки, конденсаторные трубы |
Л070-1 | 69-71% Cu, 1-1,5% Sn, остальное Zn | Конденсаторные трубы, теплотехническая аппаратура |
ЛС74-3 | 72-75% Cu, 2,4-3% Pb, остальное Zn | Детали часов, автомобилей |
ЛК80-3Л | 79-81% Cu, 2,5-4,5% Si, остальное Zn | Арматура, подвергающаяся действию воды, детали судов |
ЛКС80-3-3 | 79-80% Cu, 2,5-4,5% Si, 2-4% Pb, остальное Zn | Литые подшипники и втулки |
Бронзы.
Бронзами являются сплавы на медной основе, в которых основными легирующими компонентами являются олово, алюминий, кремний и другие металлы. Кроме того, к бронзам относят все другие сплавы меди, которые не являются латунями.
Бронзы подразделяются на оловянные и безоловянные, или специальные.
Оловянными бронзами называются сплавы меди с оловом, а также сплавы меди с оловом (содержание олова от 2 до 6%), легированные другими компонентами. Это наиболее распространенные литейные сплавы, известные с древнейших времен. Оловянные бронзыобладают высокими антифрикционными свойствами, хорошей коррозионной стойкостью, нечувствительны к перегреву, морозостойки, немагнитны. Главными недостатками оловянных бронз являются склонность к образованию пор в отливках (явление обратной ликвации) и поэтому невысокая герметичность отливок, малая жидкотекучесть.
Безоловянные бронзы, среди которых большой удельный вес занимают алюминиевые бронзы,— группа сплавов на медной основе, содержащих от 4 до 11 % алюминия. Алюминиевые бронзы также обладают высокими антифрикционными свойствами и коррозионной стойкостью, морозостойки и немагнитны. Положительные свойства алюминиевых бронз обеспечили широкое применение их в различных отраслях промышленности. Среди других сплавов на медной основе сплав меди с фосфором (до 10% фосфора) используется в качестве лигатуры при изготовлении фосфористых бронз и как раскислитель сплавов на медной основе; сплав меди с кремнием (содержание меди от 5 до 12%) используется в производстве метилхлорсиланов и других кремний полимеров.
В зависимости от технологии переработки и применения различают деформируемые, литейные и специальные бронзы.
Деформируемые оловянные бронзы содержат до 8 % олова. Эти бронзы используют для изготовления пружин и деформируемых деталей. Литейные бронзы содержат свыше 6% олова, обладают высокими антифрикционными свойствами и достаточной прочностью; их используют для изготовления деталей ответственных узлов трения.
Широкое применение получили специальные бронзы, в состав которых включены алюминий, никель, кремний, железо, бериллий, хром, свинец и другие элементы. В ряде случаев название бронзы определяется основным легирующим компонентом.
К числу наиболее распространенных сплавов рассматриваемой группы относятся алюминиевые бронзы, обладающие высокими механическими, антифрикционными и противокоррозионными свойствами. Для снижения усадки, окисляемости и склонности к газонасыщению алюминиевые бронзы легируют железом, никелем, марганцем. Их выпускают в виде слитков, деформированных полуфабрикатов. Основное применение алюминиевые бронзы нашли в изготовлении ответственных деталей машин, работающих при интенсивном изнашивании и повышенных температурах.
Сплавы меди с кремнием (кремнистые бронзы) характеризуются высокими антифрикционными, упругими свойствами, коррозионной стойкостью. Кремний образует с медью твердый α - раствор, обеспечивающий хорошую обрабатываемость сплава давлением и его пластичность. Дополнительное легирование кремниевых бронз другими элементами способствует улучшению эксплуатационных и технологических свойств бронз: цинк повышает литейные свойства, марганец и никель увеличивают коррозионную стойкость и прочность, свинец улучшает обрабатываемость резанием и антифрикционные свойства. Кремнистые бронзы применяют взамен оловянных для изготовления антифрикционных деталей, пружин, мембран приборов и оборудования.
Медь и свинец в твердом состоянии практически не растворяются друг в друге. Поэтому свинцовые бронзы после затвердевания состоят из кристаллов меди с включениями свинца. Образующаяся структура обеспечивает высокие антифрикционные свойства и теплопроводность сплава. Это позволяет использовать свинцовые бронзы в парах трения, эксплуатируемых при высоких относительных скоростях перемещения деталей. Для повышения механических свойств и коррозионной стойкости сплавы легируют никелем, оловом.
Среди медных сплавов бериллиевые бронзы отличаются высокими прочностными свойствами, износостойкостью и стойкостью к воздействию коррозионных сред. Бронзы этого типа используют для изготовления деталей ответственного назначения, эксплуатируемых при повышенных скоростях перемещения, нагрузках, температуре.
Для снижения стоимости бронзы легируют марганцем, титаном, никелем, кобальтом. По требованию потребителя в бронзе всех марок массовая доля сурьмы должна быть не более 0,4%, общая сумма примесей—не более 1,2%; массовая доля фосфора в бронзах марок Бр03Ц8С4Н1 и Бр03Ц13С4 — не более 0,05%; массовая доля кремния в бронзе марок Бр05Ц6С5 и Бр04Ц7С5 — не более 0,04%; в бронзе марок Бр03Ц8С4Н1 и Бр03Ц13С4 общая сумма примесей алюминия и кремния не должна быть более 0,02%, для деталей, не работающих под давлением, допускается массовая доля алюминия и кремния до 0,05% каждого; в марке Бр05Ц6С5 допускается увеличение массовой доли свинца и массовая доля цинка не более 7,0%. Массовая доля никеля в бронзах всех марок, кроме марки Бр03Ц8С4Н1, допускается за счет меди и в общую сумму примесей не входит. Примеси, которые не регламентируются настоящим стандартом, входят в общую сумму примесей (табл. 4.11.).
Таблица 4.11.
Марки и химический состав оловянных литейных бронз.
Бронзы оловянные литейные | ||||||
Марка | Химический состав, % | |||||
Основной компонент | ||||||
Sn | Zn | Pb | P | Ni | Cu | |
БрОЗЦ12С5 | 2,0-3,5 | 8,0-15,0 | 3,0-6,0 | - | - | Ост. |
БрОЗЦ7С5Н1 | 2,5-4,0 | 6,0-9,5 | 3,0-6,0 | - | 0,5-2,0 | Ост. |
БрО4Ц7С5 | 3,0-5,0 | 6,0-9,0 | 4,0-7,0 | - | - | Ост. |
БрО4Ц4С17 | 3,5-5,5 | 2,0-6,0 | 14,0-20,0 | - | - | Ост. |
БрО5Ц5С5 | 4,0-6,0 | 4,0-6,0 | 4,0-6,0 | - | - | Ост. |
БрО5С25 | 4,0-6,0 | - | 23,0-26,0 | - | - | Ост. |
Бро6Ц6С3 | 5,0-7,0 | 5,0-7,0 | 2,0-4,0 | - | - | Ост. |
БрО8Ц4 | 7,0-9,0 | 4,0-6,0 | - | - | - | Ост. |
Дата добавления: 2019-02-22; просмотров: 601; Мы поможем в написании вашей работы! |
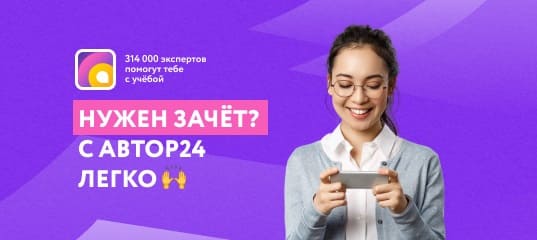
Мы поможем в написании ваших работ!