Виды обработки металлов давлением
Обработка металлов давлением — прогрессивный и экономичный технологический процесс. Такой обработке подвергаются около 90% выплавляемой стали, 60% цветных металлов и их сплавов и многие неметаллические материалы.
В промышленности обработка металлов давлением применяется для производства проката, различных видов заготовок, поковок и штамповок, также в ремонтном деле. Основными видами обработки металлов давлением являются:
- прокатка;
- волочение;
- прессование;
- свободная ковка;
- объемная и листовая штамповка.
Различают холодную и горячую обработку металлов давлением. Чистые металлы и некоторые сплавы железа, алюминия и меди имеют высокую пластичность и могут обрабатываться давлением без предварительного подогрева. В основном же заготовки металлов нагреваются, их пластичность повышается, что облегчает процесс обработки.
Пластичность металла характеризуется ковкостью и определяется относительным удлинением, поперечным сужением и степенью осадки без разрушения. На пластичность металла влияют температура, скорость деформации, химический состав и другие факторы. С увеличением температуры нагрева пластичность металлов повышается, а сопротивление деформации падает. Повышение в металлах содержания углерода, кремния, серы, фосфора и легирующих элементов снижает их пластичность. Установлено, что температура предварительного нагрева металлов должна быть строго определенной и равномерной по всему сечению заготовки. Рекомендуемые пределы горячей обработки для низкоуглеродистых сталей от 1200 до 850°С, для среднеуглеродистых – от 1150 до 820°С и для высокоуглеродистых сталей – от1050 до 800°С. Обработка сплавов цветных металлов производится при температуре 850–350°С.
|
|
Рис.7.1. Основные виды обработки металлов давлением
Прокатка (рис. 7.1, а) — один из основных способов обработки металлов давлением — является завершающим этапом полного металлургического цикла.
Цель прокатки — придание обрабатываемому материалу такой формы и размеров сечения, которые позволяют в последующем использовать металл с наибольшим эффектом.
При прокатке (рис.7. 1, а) металл пропускают между двумя валками, вращающимися навстречу друг другу. За счет силы трения, возникающей между валками и металлом, последний протаскивается между ними. При этом поперечное сечение металла уменьшается, а длина увеличивается. Отношение первоначальной длины заготовки к конечной длине за один проход заготовки называется коэффициентом вытяжки; он колеблется в пределах от 1,2 до 2 и зависит от рода материала и скорости прокатки.
Разность между толщиной материала до прокатки и после прокатки представляет собой величину абсолютного сжатия.
|
|
Прокатные валки могут быть гладкими, цилиндрическими или калиброванными, имеющими на поверхности различные углубления, которые по размерам и форме соответствуют поперечному сечению получаемого изделия. На гладких валках получают плоский прокат, а на калиброванных — изделия самого различного профиля. Прокатку производят в прокатных станах, а нагрев заготовок — в пламенных и электрических печах.
Прессование (рис. 7.1, б) — процесс обработки металлов давлением посредством выдавливания металла пуансоном из контейнера через отверстие в матрице. В зависимости от конфигурации отверстия в матрице металл может принимать круглую, квадратную или другую форму.
Волочением (рис. 7.1, в) называется процесс обработки металлов давлением, заключающийся в протаскивании заготовки через отверстие волоки, размеры которой меньше размеров сечения заготовки. Особенностью волочения является высокая точность получаемых изделий и чистота их поверхности. Волочением изготавливают проволоку, тонкостенные трубы и различные фасонные профили, производят калибровку различных горячекатаных профилей для повышения точности изделий.
|
|
Свободной ковкой (рис. 7.1, г) называется процесс свободного истечения металла под ударами молота или действия пресса.
Процесс пластического формирования нагретого металла давлением называется ковкой, а получаемые изделия — поковками. С помощью свободной ковки изготавливаются поковки различной массы и размеров.
Штамповка (рис. 7.1, е) — способ получения поковок с помощью специальных инструментов — штампов.
Штамп представляет собой металлическую разъемную форму, внутри которой расположена полость, называемая ручьем, соответствующая конфигурации получаемого изделия. При этом течение металла не свободное, а ограничено стенками штампа. Детали, полученные при штамповке, имеют более точные размеры, чем при свободной ковке, и могут не подвергаться последующей механической обработке.
Штамповка подразделяется на объемную и листовую. При объемной штамповке (рис. 7.1, 3) используются штампы, имеющие одну или несколько внутренних полостей; при листовой штамповке (рис. 7.1, е) изготавливаются тонкостенные изделия.
Объемная штамповка может быть горячей и холодной. Горячей объемной штамповкой получают крупногабаритные поковки, а холодной — небольших размеров и массы. Холодная объемная штамповка применяется при массовом производстве небольших поковок без последующей механической обработки. Листовая штамповка подразделяется на горячую и холодную, тонколистовую и толстолистовую.
Дата добавления: 2019-03-09; просмотров: 316; Мы поможем в написании вашей работы! |
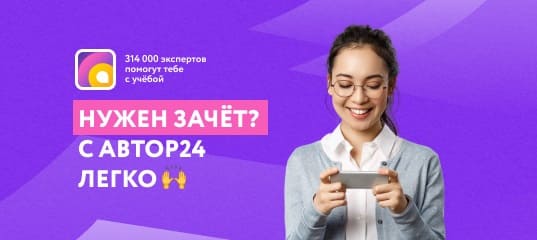
Мы поможем в написании ваших работ!