Краткая история развития бурения скважин
Начало бурения скважин для добычи нефти было положено в XIX ве-ке, а вообще история бурения насчитывает, по утверждению В. Е. Копыло-ва, десятки веков. Скважины бурились для разведки и добычи полезных ископаемых, водоснабжения, а также в других целях.
Многие страны историю своей нефтяной промышленности ведут с момента бурения первой нефтяной скважины, давшей нефть. Так, в Румынии отсчет ведется с 1857 г., в Канаде — с 1858 г., в США — с 1859 г., в Венесуэле — с 1863 г., а в России — с 1864 г. Последняя дата относится к скважине, сооруженной около города Анапы на берегу реки Кудако на Кубани под руководством А. Н. Новосельцева. Первый фонтан нефти из этой скважины получили в 1866 г. В 1964 г . на Северном Кавказе торжественно отмечалось столетие добычи нефти через скважину. В честь этого события возле этой скважины установлен обелиск с надписью « Первооткрывательнице нефти в России».
По выражению В. Е. Копылова, организаторов торжеств не смутило то обстоятельство, что еще в 1957 г. в книге А. А. Зворыкина « История горной техники» описывалось бурение нефтяной скважины в Баку намного аньше — в 1864 г. Упоминается имя В. Н. Семенова, который еще в 1844 г. предложил добычу нефти производить с помощью скважин.
В этой же книге есть сведения о промышленнике М. К. Сидорове, пробу-рившем нефтяную скважину на реке Ухте в 1855 г. Позже публиковались архивные материалы, доказывающие приоритет нашей страны в строи-тельстве первой в мире нефтяной скважины.
|
|
Тем же автором приводится документальное подтверждение об окон-чании бурения нефтяной скважины, имеющееся в докладной графа Ворон-цова от 14 июля 1848 г.: «Я разрешил произвести новые разведки на нефть в Бакинском уезде, на берегу Каспийского моря в урочище Бей-Бат по-средством земляных буров. ...Директор Бакинских и Ширванских мине-ральных промыслов доносил, что пробурена на Би-бе-Эйбате буровая скважина, в которой найдена нефть». Очевидно, что отсчет следует вести не с 1864 г., а на 16 лет раньше.
Ниже приводится краткое описание ударного и вращательного способов бурения скважин. Хотя ударное бурение при строительстве нефтяных и газовых скважин у нас в стране ныне не применяется, а за рубежом его применение в этих целях тоже ограничено, но с точки зрения истории развития технологии бурения будет полезно получить общие представления о технологии существовавших и проблемах ныне существующих способов бурения.
Ударное бурение
Ствол скважины создается периодическими ударами долота по забою (рис. 3.1) под действием собственного веса и тяжелой ударной штанги. Приподнимание долота и ударной штанги, прикрепленных к штангам (ударное штанговое бурение) или инструментальному канату ( ударное ка-натное бурение), осуществляется балансиром бурового станка. На рис. 3.1 изображена схема ударно-канатного бурения. Кривошипно-шатунный ме-ханизм 10, 12 приводит в движение балансирную раму 13, при опускании которой оттяжной ролик 14 натягивает инструментальный канат 11 и под-нимает долото 1 над забоем на 0,05–1,5 м. При подъеме балансирной рамы долото падает и разрушает породу. Лезвия долота имеют небольшую площадь контакта с забоем, что обеспечивает их значительное углубление при каждом ударе и разрушение даже очень твердых пород. Поражение всей поверхности забоя и получение цилиндрического ствола достигается прину-дительным проворачиваем инструмента после каждого удара с помощью канатного замка 6. После углубления всей площади забоя на достаточную величину на ту же величину удлиняется весь инструмент. Инструментальный канат 11 сматывается с инструментального барабана. Инструмент (буровой снаряд) канатного бурения кроме долота 1 ударной штанги 2 массой 1000–2000 кг, каната и канатного замка 6 для их соединения включает раздвижную штангу 5 (ясс, самопад) и расширитель 3. При штанговом бурении ясс предохраняет штанги от действия динамических нагрузок, допуская не-которое свободное перемещение штанг вниз после удара долота о забой; самопады допускают свободное падение долота и ударной штанги с высоты, близкой к длине хода головки балансира (балансирной рамы).
|
|
|
|
Конструктивно яссы представляют собой трубу в трубе как два звена цепи, имеющие свободное перемещение в пределах определенной длины. В самопаде предусматривается устройство, обеспечивающее захват ударной штанги, долота на забое и сбрасывание их после окончания хода балансира вверх. При канатном бурении яссы облегчают выбивание долота вверх при бурении в вязких породах.
Расширитель 3 обеспечивает увеличение диаметра скважины больше диаметра долота 1 и обсадной колонны 4, внутри которой он вместе со всем инструментом спускается. Поэтому расширитель при спуске и подъ-еме внутри обсадной колонны складывается, а в рабочее положение при-водится при выходе из-под ее башмака (основания).
Для удаления в процессе работы долота на забой подается вода, если она самопроизвольно не поступает из разбуриваемых или ранее вскрытых пластов. Очистка забоя скважины от шлама осуществляется по мере его накопления периодически с помощью устройства, называемого желонкой 8. Желонка состоит из цилиндра и поршня,оборудованных обратнымиклапанами 7, 9. Желонка спускается на относительно легком тартальном канате с высокоскоростного барабана (тартального). При достижении же-лонкой забоя поршень под действием собственного веса опускается вниз на дно колонки. При подъеме поршня его клапан закрывается, а клапан желонки остается открытым, обеспечивая поступление в желонку переме-шанного с водой шлама. При отрыве желонки от забоя под действием соб-ственного веса и веса шлама закрывается и нижний клапан. При ударном бурении скважина обычно не заполняется буровым раствором, поэтому для предотвращения обвалов спускается ( ходовая) обсадная колонна, пе-риодически продвигающаяся к забою по мере углубления скважины.
|
|
11
Рис. 3.1. Схема ударно-канатного бурения
Обсадная колонна спускается со специального барабана. Наращива-ние ее осуществляется трубами с резьбовыми соединениями ( редко на сварке). С увеличением выхода ( расстояния) башмака опускаемой колон-ны из-под башмака предыдущей ( ранее спущенной) затрудняется и нако-нец становится невозможным ее проталкивание к забою даже с помощью забивных снарядов. Тогда эта колонна оставляется в скважине в таком по-ложении, чтобы ее башмак находился в устойчивых породах. Далее вновь опускается следующая (ходовая) обсадная колонна, которая так же про-двигается к забою по мере углубления скважины. Поэтому число обсадных колонн при ударном бурении велико.
Для ударного бурения нефтяных скважин характерны следующие ос-новные особенности. Способ разрушения горных пород периодическими ударами с частотой от 10–20 до 100–150 в минуту при длительности собственного удара всего в десятые и сотые доли секунды дает возмож-ность сосредоточивать в контакте с породой большие мощности и разру-шать практически любую по твердости породу из осадочного комплекса при малой мощности привода бурового станка. Однако вследствие низкой частоты ударов невелики и скорости проходки — не более нескольких метров в час.
Отсутствие буровых насосов, очистных устройств, непрерывной про-мывки скважин облегчает буровую установку, требует сравнительно не-большой мощности привода и расхода электроэнергии или топлива. Энер-гоемкость бурения невелика, однако скорости проходки понижаются еще больше вследствие периодичности очистки забоя и больших перерывов в работе долота.
Из-за отсутствия бурового раствора в скважине не создается противо-давление на ее стенки и насыщающие пласты флюиды, что, с одной сторо-ны, улучшает качество вскрытия низконапорных пластов, исключает их загрязнение и пропуск при разведке, а с другой стороны — повышает опасность обвалообразований, вынуждает спускать большое число обсад-ных колонн, что, соответственно, требует больших затрат на строи-тельство скважин. Отсутствие регулируемого противодавления в скважине практически исключает вскрытие высоконапорных нефтяных пластов из-за опасности выбросов, открытого фонтанирования и пожаров.
Попытки усовершенствовать ударное бурение за счет применения не-прерывной циркуляции жидкости для очистки забоя приводили к сущест-венному усложнению оборудования и удорожанию его эксплуатации, ли-шали ударное бурение и другого преимущества перед вращательным — более высокого качества вскрытия продуктивных нефтяных пластов, по-этому выпускаемые у нас станки ударно-канатного бурения для других от-раслей промышленности не предусматривают непрерывную циркуляцию бурового раствора, имеют небольшую массу и предназначены для бурения на глубину менее сотни метров. В США есть опыт применения ударного бурения лишь для вскрытия нефтяных пластов, когда весь основной ствол бурится вращательным способом ( комбинированное последовательное ударно-вращательное бурение).
Однако и для этих целей оно было заменено более эффективным вра-щательным бурением с аэрацией пеной или продувкой газообразными агентами, промывкой растворами на нефтяной основе. В России ударное бурение применяется ныне в других отраслях.
Вращательное бурение
При этом способе бурения горная порода на забое разрушается вра-щающимся долотом, на которое передаются осевая нагрузка и крутящий момент. Разрушенная порода удаляется с забоя потоком жидкости, непре-рывно подаваемой по колонне бурильных труб. Крутящий момент на до-лото передается или с поверхности от вращателя ( ротора) через колонну бурильных труб (роторное бурение), или от забойного двигателя (турбобу-ра, электробура, винтового бура), установленного непосредственно над до-лотом. Осевая нагрузка создается в основном частью веса находящихся над долотом утяжеленных (толстостенных) бурильных труб, забойного двигателя. Используются гидравлические, гидроударные и другие способы передачи нагрузки. На долото диаметром 215,9 мм создается нагрузка око-ло 100–250 кН. Крутящий момент в процессе бурения в зависимости от ти-па долота (шарошечное, алмазное и т.д.) и свойств пород (твердые, мягкие, пластичные) при диаметре скважины 215,9 мм составляет от1 до 3 кН-м. Частота вращения долота при роторном бурении составляет 20–200 об/мин, при бурении винтовыми двигателями — 150–250 об/ мин, турбин-ном и электробурении без редуцирования — 250–800 об/мин, при бурении турбобурами и электробурами с редуктором — 200–300 об/мин. При об-щей установленной мощности буровых установок для бурения на глубину до 4500 м в 1000, 1500 кВт на долото передается около 50–200 кВт при из-менении глубины от 0 до 4500 м.
Несмотря на низкий коэффициент передачи мощности на забой, в среднем мощность на долоте в несколько раз больше, чем при ударном бурении, что обеспечивает гораздо более высокие скорости проходки, дос-тигающие 100 м в час при бурении пород средней твердости и мягких. Этому способствует и непрерывная промывка.
Подаваемый для очистки забоя буровой раствор совершает непрерыв-ный кругооборот-циркуляцию: буровой насос — нагнетательная линия — вертлюг — бурильная колонна — забойный двигатель — долото — забой — кольцевое пространство между бурильной колонной и стенками скважины — устье скважины — желоба и другие устройства очистки бу-рового раствора от шлама, газа — приемная емкость для очищенного рас-твора — подпорный насос, всасывающая линия бурового насоса.
В качестве бурового раствора используются вода, естественные рас-творы, образующиеся из шлама и подаваемой с поверхности воды, с добавлением химических реагентов, пластовых вод; глинистый раствор; нефтеэмульсионный раствор; раствор на нефтяной (углеводородной) осно-ве; вода, смешанная с воздухом ( аэрированная); пена; воздух; природные газы и их смеси с отработанными газами двигателей внутреннего сгорания (ДВС); утяжеленные растворы плотностью до 2400 кг/м3 и др.
Производительность буровых насосов при диаметре долота 215,9 мм составляет 20–40 дм3/с, давление на выкиде насосов 5–20 МПа, установленная мощность на приводе около 600 кВт. При глубоком бурении на буровой устанавливается до трех таких насосов.
Циркулирующий буровой раствор не только удаляет разбури- ваемую породу и частицы осыпающихся пород, но и охлаждает долото, иногда способствует более эффективному разрушению породы. Одновременно буровой раствор создает противодавление на стенки скважины, чем преду-преждается прорыв пластовых флюидов, обвалообразования, также он мо-жет закупоривать и укреплять стенки за счет гидродинамического и физико-химического взаимодействия с горными породами и пластовыми флюидами. Поэтому, в отличие от ударного бурения, в скважину спускает-ся меньше обсадных колонн, причем делается это после проходки всего интервала их спуска.
Для смены изношенного долота производится подъем бурильной ко-лонны, а затем ее спуск с новым долотом. Спуск и подъем бурильного ин-струмента, спуск обсадных колонн осуществляется с помощью подъемного оборудования — вышки, лебедки, полиспастовой (талевой) системы, подъ-емного крюка (рис. 3.2).
При спуско-подъемных операциях (СПО) используются ключи и другие приспособления для свинчивания и развинчивания труб и других элементов бурильной колонны, удержания колонны на весу в процессе свинчивания и развинчивания, захвата труб и подачи их к устью ( стволу ротора) или от устья для установки на специальный стол, называемый под-свечником, в слегка наклонном (1–3°) положении.
Для удобства изготовления, эксплуатации и транспортирования бу-рильные трубы выпускаются длиной не более 12 метров, для ускорения СПО в глубоком бурении целесообразно поднимать (опускать) инструмент, расчленяя его на части, включающие 2–4 трубы, называемые свечами. Это уменьшает также изнашивание резьб, труб, подъемного оборудования, ме-ханизмов. Расстановка свечей на подсвечнике в ( почти) вертикальном по-ложении повышает производительность труда, исключает многие операции, связанные с переводом труб в горизонтальное положение, осуществляемое лишь при разборке буровой после окончания бурения скважины.
В зависимости от объема СПО применяют свечи длиной 25 и 37 м, со-ответственно вышки высотой 41 и 53 м. Высота вышки определяется не только длиной свечи, но и возможностью размещения талевого ( подвиж-ного) блока, крюка, штропов и безопасного пути их торможения. Попереч-ные размеры вышки определяются глубиной бурения, диаметром труб, числом свечей, устанавливаемых на подсвечниках по обе стороны от стола ротора в пределах площади, ограниченной боковыми сторонами вышки.
При бурении на малые и средние глубины наибольшее распростране-ние получили удобные в монтаже и транспортировании мачтовые вышки, а при бурении сверхглубоких скважин чаще используются вышки башен-ного типа.
Масса инструмента изменяется по мере его спуска (подъема), а также с углублением скважины. Для более полного использования приводной мощности лебедки изготавливаются многоскоростными (4–6), предусмат-риваются также оснастка канатом от 2 до 6 шкивов талевого блока и от 3 до 7 шкивов кронблока (оснастки 2x3, 3x4, 4x5, 5x6, 6x7) по мере возрас-тания глубины скважины и массы колонны.
Грузоподъемность вышки и другого оборудования определяется мас-сой бурильной колонны с запасом на возможные осложнения, затяжки
и заклинивания инструмента в скважине. Вышки для бурения на 4500 м имеют грузоподъемность около 200 т.
Ротор необходим не только для передачи вращения бурильному инст-рументу. Он используется и при СПО как опора для установки бурильной колонны, удерживаемой клиновыми захватами или элеватором. Использу-ется ротор и для поворачивания бурильной колонны во время ориентиро-ванного спуска инструмента при наклонном бурении.
Для примера ниже приводится описание операции подъема инструмента.
Перед подъемом инструмента скважина промывается до выравнивания плотности подаваемой и выходящей из нее жидкости, что свидетельствует об отсутствии шлама, газа в скважине и косвенно — угрозы осложнений (сальников, выброса, обвала). Чаще скважина промывается более ограни-ченное время лишь для подъема шлама с забоя на такую высоту, чтобы ис-ключить забивание шламом насадок долота, турбобура и перелив промывочной жидкости из труб на устье вследствие разности плотностей зашлам-ленной жидкости в кольцевом пространстве и очищенной от шлама жидко-сти внутри полости бурильного инструмента. Инструмент, подвешенный на крюке, поднимают на длину ведущей трубы так, чтобы над столом ротора оказалось замковое соединение бурильных труб. Прекращают подъем, включают тормоз лебедки, убирают малые вкладыши ротора с квадратными вырезами под ведущую трубу и вместо него устанавливают клиновые захва-ты (встроенные в ротор либо съемные). Клинья поднимаются и опускаются с помощью пневматических домкратов, управляемых с пульта бурильщика.
Растормаживанием барабана лебедки опускают колонну чуть ниже, чтобы сработали клиновые захваты и она повисла бы на них. Отвинчивают ведущую трубу вместе с вертлюгом и с помощью автозатаскивателя под-водят ее нижний конец к шурфу и опускают с помощью талевой системы
в шурф. Шурф представляет собой горную выработку ( скважину) глу-биной 18–25 м, пробуренную на расстоянии 1,5–2 м от центра ротора на-клонно в сторону правого угла для размещения ведущей трубы на время СПО или наращивания.
Рис. 3.2. Схема установки для бурения глубоких скважин:
1 —долото; 2 —наддолотная утяжеленная бурильная труба; 3 —переводник; 4 — центратор; 5 —муфтовый переводник; 6, 7 —утяжеленные бурильныетрубы; 8 — переводник; 9 — предохранительное кольцо; 10 — бурильные трубы; 11 —предохранительный переводник; 12, 23 — переводники штанговые,нижний и верхний; 13 — ведущая труба; 14 — редуктор; 15 — лебедка; 16 — переводник вертлюга; 17 —крюк; 18 —кронблок; 19 — вышка; 20 —талевый блок; 21 —вертлюг; 22 —шланг; 24 —стояк; 25 —ротор; 26 — шламоотделитель; 27 —буровой насос
После спуска ведущей штанги в шурф отсоединяют крюк от серьги вертлюга, на штропы подвешивают элеватор. Элеватор закрывают под муфтой замка верхней трубы. Бурильщик, включив лебедку, поднимает подвешенную на элеваторе бурильную колонну на длину свечи так, чтобы после подвешивания бурильной колонны на клинья можно было ниже зам-кового соединения вновь установить элеватор.
Поднятую свечу отвинчивают от бурильной колонны с помощью пневмораскрепителей, пневматических или электрических ключей, редко — машинными ключами. Отвинченная свеча под действием пружины крюка поднимается, и ниппель замка немедленно, еще до включения ле-бедки, выходит из муфты замка, что предупреждает разрушение резьб.
Помощник бурильщика, захватив нижний конец свечи крючком, отводит свечу и ставит ее на подсвечник. Второй помощник бурильщика,
находящийся на площадке верхнего рабочего на уровне верхнего конца свечи, освобождает свечу от элеватора и заводит ее верхний конец за спе-циальную консольную балку- палец, закрепленную на вышке. Бурильщик опускает порожний элеватор для захватывания им бурильной колонны, и операция по подъему и установке следующей свечи повторяется.
Проводятся работы по облегчению труда рабочих буровой бригады. С этой целью продолжается совершенствование спуско-подъемного обо-рудования и механизмов. Разработан комплекс механизмов спуска-подъема ( МСП), в котором механизированы свинчивание-развинчивание, расстановка свечей при подъеме и подача свечей к оси скважины.
В автоматизированной установке АСП ( автомат спуско-подъемных операций) совмещаются во времени операции спуска-подъема колонны бурильных труб и незагруженного элеватора с операциями установки све-чи на подсвечник и выноса ее с подсвечника, отвинчивания и свинчивания. МСП, АСП ввиду их сложности эффективны при бурении глубоких сква-жин, если велико число отрабатываемых долот, большой объем СПО.
С их использованием выполняется и наращивание ( удлинение бу-рильного инструмента по мере углубления скважины). Обычно наращива-ние осуществляется по одной трубе ( одиночно). При бурении забойными двигателями на большой глубине, когда непрерывно вращать инструмент ротором не нужно, а реактивный момент полностью гасится трением бурильного инструмента о стенки скважины, возможно использование двух соединенных вместе ведущих труб и наращивание свечами.
Ускоряет работы и дополнительный второй шурф, пробуренный ря-дом с первым на той же диагонали , проходящей через ноги и центр вышки. Во время наращивания труба опускается во второй шурф. После того, как долото углубится так, что верхний конец ведущей трубы ока-жется в роторе, начинают операцию по наращиванию. Колонну подни-мают на длину ведущей трубы, подвешивают на клиньях, затем отвинчивают ведущую трубу и соединяют с помощью элеваторов с наращиваемой трубой, поднимают вместе с ней и затем наращиваемую трубу соединяют с бурильной колонной, далее закрепляют резьбовое соединение ведущей трубы с наращиваемой, включается промывка, и инструмент подается на забой.
При наращивании и СПО должны строго соблюдаться правила охра-ны труда, так как эти операции являются наиболее тяжелыми, трудоемки-ми и при больших глубинах очень длительными ( занимают много време-ни), утомительными, когда рабочие могут утратить осторожность. Перед началом работ проверяется исправность талевой системы, отсутствие неза-крепленных предметов, а также исправность бурового оборудования, осо-бенно ленточных тормозов лебедки, наличие надлежащего давления в пневмосистеме. Для предупреждения затаскивания талевого блока под кронблок должен быть установлен противозатаскиватель.
Пространство вокруг стола ротора, рабочее место каждого члена вах-ты должно быть свободно и содержаться в чистоте. Инструмент при подъ-еме должен промываться для удаления сальников на замковых элементах и визуального контроля с целью выявления трещин, промывов и других нарушений в бурильном инструменте.
При работе на буровой необходимо пользоваться индивидуальными средствами защиты ( брезентовым костюмом, рукавицами, текстолитовым шлемом и др.). Верхний рабочий должен иметь предохранительный пояс, закрепленный на вышке. Бурильщик должен видеть все приборы контроля хода СПО.
После проводки ствола скважины под очередную обсадную колонну механическое бурение прекращается, проводится геофизические исследо-вания вскрытых скважиной пластов на нефтегазоносность, изучаются ли-тология, коллекторские свойства пород — проницаемость, пористость, трещиноватость, глубина проникновения фильтрата бурового раствора, определяются температура, кривизна ствола и азимут искривления по ин-тервалам бурения, записывается размер и форма сечения ствола — профи-леграмма или кавернограмма, ствол скважины готовится к креплению.В скважину спускается обсадная колонна, и кольцевое пространство между обсадной колонной и стенками скважины цементируется.
После цементирования каждой колонны скважина проверяется на герметичность внутренним давлением (опрессовка), а иногда наружным давлением путем понижения уровня (откачкой) жидкости в колонне. На кондукторы (промежуточные колонны) после проверки скважины на гер-метичность устанавливается противовыбросовая арматура.
Эксплуатационная колонна, выдержавшая проверку на герметичность, соединяется с пластом путем простреливания или просверливания в ней отверстий. Устье скважины оборудуется эксплуатационной арматурой, после чего приступают к освоению скважины, вводу ее в эксплуатацию.В разведочных скважинах испытываются объекты ( пласты), которые при опробовании в процессе бурения показали возможную промышленную продуктивность. Составляется паспорт скважины, акт испытаний, готовит-ся другая документация, а скважина сдается промысловикам. Вся площадка скважины приводится в надлежащий вид.
Вращательное бурение от ударного отличается следующим:
1) высокой производительностью за счет передачи на долото большей мощности, непрерывного разрушения горной породы и удаления ее с забоя на поверхность циркулирующим промывочным агентом;
2) эффективностью применения для самых различных целей: универ-сальностью, возможностью вскрытия пластов с низким и высоким давлением, используя для промывки, в зависимости от условий, газо-образные агенты, облегченные, нормальные или утяжеленные буровые растворы; возможностью преодолеть многие виды обвалообразований, поглощений промывочной жидкости, не прибегая к дополнительному креплению ствола скважины, возможностью предупредить в большин-стве случаев проявления, выбросы и открытое фонтанирование;
3) большой мощностью привода буровой установки, сложностью буро-вого оборудования, КИП и системы управления, высокой начальной стоимостью ( покупная цена) и стоимостью эксплуатации, монтажа, транспортирования установки.
Экспериментальные буровые обеспечиваются ныне автоматами пода-чи долота, следящими устройствами, вычислительными машинами, физи-ко-химическими лабораториями контроля состава и качества буровых
и тампонажных растворов и пластовых флюидов. Каждая буровая установ-ка представляет собой довольно крупную автономную единицу, тре-бующую высококвалифицированных специалистов буровиков-технологов, механиков-вышкомонтажников, механиков по эксплуатации, обслужива-нию, ремонту бурового оборудования и инструмента, инженеров по КИП и автоматике.
Буровая техника и технология должны находиться в постоянном со-вершенствовании. Основной проблемой всегда являлись увеличение мощ-ности на забое, повышение скоростей проходки. Малопроизводительный ручной штанговый вращательный способ бурения с очень малой общей и очень низкой удельной мощностью (на единицу контактной поверхности инструмента) постепенно вытеснялся механическим ударно-канатным спо-собом, который был вытеснен роторным способом бурения.
Затем крупным шагом в развитии бурения было создание гидравлических забойных двигателей — турбобуров, при применении которых, в отли-чие от роторного бурения, бурильная колонна не вращается и не затрачива-ется на это мощность буровой установки, снижается аварийность и износ бурильных труб, промежуточных обсадных колонн. Первые одноступенча-тые турбобуры были созданы в 1923 г. М. А. Капелюшниковым, С. И. Волохом, И. А. Корнеевым. Однако ввиду недостаточной мощности, высоких оборотов и очень малого крутящего момента бурение ими не могло кон-курировать с роторным. В 1933–1940 гг. на базе разработанной П. П. Шумиловым теории осевых многоступенчатых (100 и более ступеней) турбин им совместно с Р. А. Ионнесяном, Э. И. Тагиевым, М. Т. Гусманом был создан турбобур достаточно мощный, с довольно большим крутящим моментом и износостойкой резинометаллической опорой. Советский Союз стал родоначальником нового прогрессивного метода бурения. Турбобур надежен и удобен в эксплуатации, может успешно работать в большинстве видов буровых растворов — на воде, аэрированных, глинистых и эмульсионных растворах. Особенностью турбобура является его мягкая рабочая ха-рактеристика. При разработке новых конструкций турбобуров и режимов бурения все еще остается не в полной мере решенной проблема оптималь-ного сочетания частоты вращения и крутящего момента на валу двигателя.
Важным условием успешного развития роторного и особенно турбин-ного бурения было создание в начале XX века в США шарошечных долот, требующих для своего вращения гораздо меньших крутящих моментов, чем лопастные долота, применявшиеся по аналогии с ударным бурением на заре внедрения вращательного способа. Совершенствование шарошеч-ных долот продолжается и поныне для достижения высоких показателей в очень твердых и высокоабразивных породах и при большом диаметре скважин.
Специалисты турбинного бурения ныне отказались от бытовавших в 50-е годы прошлого века взглядов на целесообразность высокооборотно-го (600–800 об/мин) бурения. Развитие бурения продолжается в направле-нии повышения крутящего момента и мощности на долоте за счет приме-нения редукторов, секционирования (соединения двух, трех и более турбобуров-секций).
Для дальнейшего улучшения показателей турбинного бурения необ-ходимо и далее повышать износостойкость его турбин, опор, улучшать моментную характеристику.
Другим направлением в совершенствовании гидравлических забойных двигателей является разработка объемного винтового двигателя, отличаю-щегося от турбобура принципом работы и более жесткой характеристикой, большим крутящим моментом, меньшей частотой вращения ( до 250 об/мин), меньшими габаритами, меньшим потребным расходом жидкости и меньшим перепадом давления. Винтовой двигатель имеет большую мощ-ность, большой крутящий момент при меньшей частоте вращения. К на-стоящему времени разработан ряд двигателей диаметром от 54 до 195 мм. Принципиальные особенности характеристики винтового двигателя позво-ляют рассматривать его как очень перспективный забойный двигатель, осо-бенно при необходимости иметь большие крутящие моменты при малых расходах, т.е. при бурении на больших глубинах в твердых абразивных и пластичных породах и бурении скважин уменьшенных и малых диаметров с промывкой хорошо очищенными от твердой фазы растворами.
1937–1940 гг. инженерами А. П. Островским, Н. В. Александровым, Н. Г. Григоряном и др. впервые разработан и с тех пор находит промыш-ленное применение электробур — забойный асинхронный электродвига-тель, выпускаемый ныне в 8–10-полюсном исполнении с частотой враще-ния 540–700 об/мин, диаметром от 164 до 290 мм, с мощностью 50–250 кВт. Относительно высокий коэффициент передачи мощности на забой, большая мощность и довольно большой крутящий момент позволяют при-менять электробур при разбуривании практически всех типов пород. На-личие кабеля внутри бурильных труб обеспечивает постоянный электриче-ский канал связи для контроля режимных параметров и направления ство-ла скважины. Преимуществом является и наличие двух каналов передачи энергии на забой: электрической по кабелю и гидравлической по трубам.
Благодаря возможности систематического контроля за направлением ство-ла скважины и отклонителя положительные результаты получены при на-клонном и горизонтальном бурении.
Проблемой при бурении электробуром остается организация его крупномасштабного применения на больших площадях, упрощающих ква-лифицированный контроль за его работой, осмотр, профилактику и ре-монт.
Следующим шагом в совершенствовании бурения электробуром мог быть переход на постоянный ток, обеспечивающий удобство регулирования крутящего момента и частоты вращения, надежность сети питания.
В ближайшее время, видимо, вновь расширится объем роторного бу-рения, что обусловлено, во-первых, возможностью иметь на долоте крутя-щий момент, больший, чем при других способах бурения, соответственно, большей может быть осевая нагрузка, возможно более эффективное раз-рушение пластичных пород, в том числе пород абразивных.
Вторым преимуществом роторного бурения перед гидравлическими забойными двигателями является наличие второго (гидродинамического) канала передачи (гидравлической) энергии на забой по бурильным трубам, более широкая возможность применения гидромониторной промывки, уменьшения расхода и увеличение перепада давления и скорости истечения через насадки долот. Однако ограничения по частоте вращения отрицательно сказываются при бурении долотами большого диаметра на малой и средней глубине (500–2000 м), когда механические скорости роторного бурения оказываются кратно ниже показателей турбинного бурения.
В роторном бурении бурильная колонна работает в напряженных ус-ловиях, быстрее наступает усталостное разрушение, скорее изнашивается, соответственно, выше требования к прочности и износостойкости, контро-лю всех элементов бурильной колонны.
Эти вопросы сейчас находятся в стадии решения, разработаны и нача-ли выпускаться трубы со специальными резьбами со стабилизирующими поясами и др. Проблемой, требующей скорого решения, является создание стальных труб, пригодных для работы в агрессивных средах, в условиях сероводородной агрессии, и легкосплавных труб, работающих в условиях магнезиальной коррозии и повышенных температур.
В процессе развития вращательного бурения совершенствовались и промывочные жидкости, технология вскрытия пластов и предупреждения осложнений, крепления скважин.
Дата добавления: 2019-02-22; просмотров: 757; Мы поможем в написании вашей работы! |
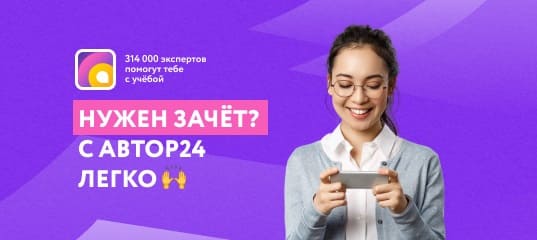
Мы поможем в написании ваших работ!