Для бронзы необходимо согласовать размер прутка по ГОСТ 1628-78.
Для проката стали - по ГОСТ 2590-2006.
Таблица №1
Припуски на чистовое подрезание торцов и уступов, мм
Диаметр заготовки | Общая длина заготовки | |||||
До 18 | 18-50 | 50-120 | 120-260 | 260-500 | Св.500 | |
До 30 | 0,4 | 0,5 | 0,7 | 0,8 | 1,0 | 1,2 |
30-50 | 0,5 | 0,6 | 0,7 | 0,8 | 1,0 | 1,2 |
50-120 | 0,6 | 0,7 | 0,8 | 1,0 | 1,2 | 1,3 |
120-300 | 0,8 | 0,9 | 1,0 | 1,2 | 1,4 | 1,5 |
Таблица №2
Припуск на диаметр при расчетной длине детали при различных операциях, мм
Номинальный диаметр | Операция | Припуск на диаметр при расчетной длине | ||||||||
До 25 | 25-63 | 63-100 | 100-160 | 160-250 | 250-400 | 400-630 | 630-1000 | 1000-1600 | ||
50-80 | Точение черновое | 4,0 | 4,0 | 4,0 | 4,5 | 4,5 | 4,5 | 5,0 | 5,5 | 6,0 |
Точение чистовое | 1,5 | 1,5 | 1,5 | 1,5 | 1,5 | 2,0 | 2,0 | 2,5 | 2,5 | |
Шлифование | 0,4 0,4 | 0,4 0,4 | 0,4 0,4 | 0,4 0,5 | 0,4 0,5 | 0,5 0,5 | 0,5 0,6 | 0,6 0,7 | 0,7 0,9 | |
80-120 | Точение черновое | 5,5 | 5,5 | 5,5 | 6,0 | 6,0 | 7,0 | 7,5 | 8,5 | 8,5 |
Точение чистовое | 2,0 | 2,0 | 2,0 | 2,0 | 2,0 | 2,0 | 2,5 | 2,5 | 3,0 | |
Шлифование | 0,5 0,5 | 0,5 0,5 | 0,5 0,5 | 0,5 0,6 | 0,5 0,6 | 0,5 0,7 | 0,6 0,7 | 0,6 0,8 | 0,8 0,9 | |
120-160 | Точение черновое | 6,0 | 6,0 | 6,0 | 7,0 | 7,0 | 7,5 | 8,0 | 9,0 | 9,0 |
Точение чистовое | 2,0 | 2,0 | 2,0 | 2,5 | 2,5 | 2,5 | 3,0 | 3,0 | 3,5 | |
Шлифование | 0,5 0,5 | 0,5 0,5 | 0,5 0,5 | 0,6 0,7 | 0,6 0,7 | 0,6 0,8 | 0,6 0,8 | 0,7 0,9 | 0,8 1,0 |
Примечание:
1. В числителе даны припуски для незакаленных деталей, в знаменателе – для закаленных.
2. При обработке с уступами припуск назначается по отношению к общей длине детали.
3. При закаливании деталей, изготовленных из сталей, подверженных значительным термическим деформациям (например, из стали 45), припуск под шлифование следует увеличить.
|
|
2. Оценка качества исходной заготовки производите по значению коэффициента использования материала:
Коэффициент использования материала КИМ = Мд / Мз,
где Мд – масса детали, Мз - масса заготовки
Результаты расчетов сведены в таблицу:
Габариты детали, мм | Ø140х90 | |
Габариты заготовки, мм | Ø160х92 | |
Масса детали, кг | 12,5 | Мд=140х0,09-0,67х0,14=12,5 кг |
Масса заготовки, кг | 14,7 | Мз=160х0,092=14,7 кг |
Коэффициент использования материала КИМ | 0,85 | КИМ= М детали/М заготовки=12,5/14,7=0,85 |
Практическая работа № 5
Тема 4.5. Точение.
Определение основного (машинного) времени при токарной обработке.
Исходные данные:
Операционный эскиз
Пример выполнения практической работы:
4. | Вал | 85 | 130 | Сталь 25 |
- Основное (технологическое) время (То) - это время, в течение которого происходит процесс снятия стружки. При работе на станке основное (технологическое) время может быть машинным и машинно-ручным.
- При токарной обработке машинное время может быть подсчитано по формуле
Тм= L·i/(n·s), мин
|
|
где L - величина пути инструмента в направлении подачи в мм;
n - число оборотов заготовки (шпинделя) в минуту;
s - подача в мм/об;
i – число проходов.
L = lр + lвр,
lр – длина резания, lвр – величина врезания и перебега инструмента,
L = l р + l 1 + l 2, где l р – длина резания, мм;
l 1 + l 2 – длина врезания и перебега резца.
l р=130 мм; l 1 = 3 мм; (перебег для данного эскиза отсутствует – l2 = 0 мм )
[9] прил.9л1стр.245
[9] Общемашиностроительные нормативы времени вспомогательного на обслуживание
рабочего места подготовительно-заключительного на работы, выполняемые на малогабаритных металлорежущих станках (мелкосерийное, серийное и крупносерийное производство) – М.: НИИ труда,1970. 280с, ил.
L=130+3=103мм; i чер=3 - число проходов
Режимы резания при черновой обработке по результатам расчетов практической работы №3:
t=3мм; s=0,8 мм/об; nст= 800 об/мин; Vф =352 м/мин, тогда
Тм=( L · i )/( n · s )=(102,5·3)/(800·0,8)=0,48 мин
Практическое задание №8
Тема 4.5. Точение.
Определение требуемой подачи при чистовом точении.
Исходные данные:
4 | 1,5 | 0,5 | 140 | 75 | 30 | 1,5 | 180 |
Пояснения к выполнению практической работы:
При чистовой обработке среднеуглеродистых сталей точением резцами марки Т15К6 среднее арифметическое отклонение профиля Ra можно определить по следующей формуле:
|
|
, мкм (1)
где t — глубина резания, мм;
S —подача, мм/об;
φ, φ1,— главный и вспомогательный углы в плане, град.;
V — скорость резания, м/мин;
r — радиус при вершине резца, мм;
НВ — твердость по Бринеллю.
Из формулы (1) определим S0,58:
, тогда Sрасч. = Х1/0,58= Х1,7
Выбрать ближайшее стандартное значение подачи по паспорту станка 16К20.
Для обработки детали выбираем самый распространенный широкоуниверсальный токарно-винторезный станок модель 16К20, позволяющий производить токарную обработку деталей наиболее широкой номенклатуры и наиболее типичных размеров.
Технические характеристики станка:
- Наибольший диаметр обрабатываемой заготовки над суппортом - 220мм.
- Наибольшая длина обрабатываемой заготовки - 710мм.
- Высота расположения центров - 215мм.
- Наибольший диаметр прутка в патроне - 53мм.
- Внутренний конус шпинделя - Морзе 6
- Частота вращения шпинделя - 12,5-1600об/мин. (12,5; 16; 25; 31,5; 40; 50; 63; 80; 100; 125; 160; 200; 250; 315; 400; 500; 630; 800; 1000; 1250; 1600)
- Подача продольная - 0,05-2,8мм/об. (0,05; 0,06; 0,075; 0,09; 0,1; 0,125; 0,15; 0,175; 0,2; 0,25; 0,3; 0,35; 0,4; 0,5; 0,6; 0,7; 0,8; 1,0; 1,2; 1,4; 1,6; 2,0; 2,4; 2,8)
- Подача поперечная - 0,025-1,4мм/об.
- Конус отверстия пиноли задней бабки - Морзе 5.
|
|
- Сечение резца - 25х25мм.
- Диаметр патрона - 250мм.
- Мощность электродвигателя - 11,0кВт.
- Габаритные размеры станка - 2505х1190х1500мм.
Вывод: записать значение подачи, скорректированной по паспорту станка 16К20
Практическое задание №9
Тема 4.5. Точение.
Разработка ТП изготовления деталей типа «вал»
Исходные данные:
1. Эскизы деталей типа «вал».
Рис.1 Разновидности деталей типа «вал»
1. Изучить главу 1 [11]
2. Составить типовой маршрут обработки деталь типа «вал» для единичного производства.
3. Валы и оси составляют 10-13% в общем объеме производства деталей машин. Они весьма разнообразны по своему назначению, конструктивной форме, размерам и марке конструкционного материала. Эти изделия делятся на гладкие и ступенчатые; цельные и пустотелые; валы с фланцами, шлицевые валы и валы-шестерни, а также комбинированные с разнообразными сочетаниями указанных на рис.1. По форме геометрической оси валы могут быть прямыми, коленчатыми, кривошипными и эксцентриковыми (кулачковыми).
4. Наибольшее распространение в машиностроении получили ступенчатые валы длиной от 150 до 1200 мм. По соотношению длины l и среднего диаметра d валы делят на жесткие (l / d 8…12) и нежесткие (l / d>12).
При конструировании деталей этого типа предъявляют следующие технологические требования:
2. Изделия должны обладать концентричными наружными и внутренними поверхностями, минимальной несоосностью отдельных обрабатываемых поверхностей и стабильностью положения оси вращения (для шпинделей).
3. Для упрощения изготовления, контроля и ремонта изделия предусматривают центровые отверстия в торцовых поверхностях.
4. Ступенчатые валы и оси должны иметь небольшие перепады диаметров, при этом на разных ступенях желательно иметь одинаковые перепады. Это особенно важно, если заготовка будет обрабатываться на многорезцовых станках.
5. При конструировании валов и осей со шпоночными пазами следует отдавать предпочтение пазам, образуемым дисковой фрезой, так как обработка концевой фрезой менее производительная.
6. При проектировании этих деталей со шлицами следует предусматривать возможность свободного выхода режущего инструмента. Поэтому диаметр вала, прилегающего к шлицевому участку, выполняют меньше внутреннего диаметра шлицев.
Практическое задание № 11
Дата добавления: 2019-02-22; просмотров: 130; Мы поможем в написании вашей работы! |
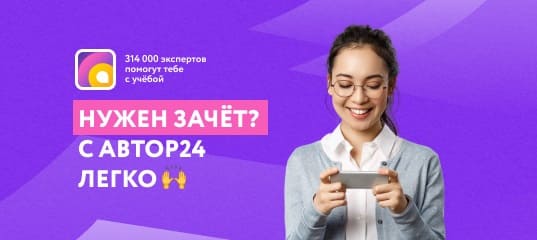
Мы поможем в написании ваших работ!