Портландцемент. Шикізат материалдары 19 страница
Шикізаттың минералдық құрамының әсері. Шикізат қоспасының реакцияға бейімділігі ең алдымен алюмосиликатты компоненттердің табиғатына байланысты. Бұлардың ішінен кварц, халцедон және опал реакцияға оңайлықпен түсе қоймайды. Кремний тотығының жоғары температуралы модификациясы – тридимит пен кристобалит – алдыңғыларға қарағанда жақсы әрекеттеседі, өйткені олар полиморфтық өзгерістерге ұшыраған. Сол себепті кристалл торлары бұзылған, әрі тығыз емес. Дала шпаттарының да белсенділігі төмен. Әрекеттесуге бейім минералдар – сазбалшық минералдары. Себебі сусызданғаннан кейін олардың құрылымы бейберекет өнімдер түзіледі. AI3+ ионының Mg2+ ионына ауысуы да олардың белсенділігін арттырады.
Табиғи сазды тау жыныстардың ішінде мергель, сазды сланец және бентониттің белсенділігі жоғары, ал лесс, сланец және биотитті саздың белсенділігі төмен. Сазды минералдардың ішінде монтмориллонит, галлуазит, гидрослюда, каолиниттердің белсенділігі жоғары, ал слюда, вермикулит, хлориттің белсенділігі төмендеу.
Табиғи кремнеземдардың белсенділігін келесі қатардан байқауға болады: яшма > кварц, опал, халцедон > тау хрусталі.
SiО2-нің полиморфты модификацияларын белсенділігі бойынша келесі қатарға орналастыруға болады: кристобалит > тридимит > кварц. Әр түрлі қосылыстардың құрамындағы SiО2-нің белсенділігі кварцтың белсенділігінен жоғары. Мысалы сазды компонент ретінде волластонитті тау жыныстарын (СаО∙SiО2 минералы), базальт, диабаздарды пайдаланғанда клинкер күйдірілу процестері төмен температураларда аяқталады.
|
|
Сусыздандыру нәтижесінде силикаттармен қатар түзілетін темір тотығы Fe2O3 пирит огаркасымен енген темір тотығына Fe2O3 қарағанда реакцияға оңай түседі.
Карбонаттардың ішінен реакцияға белсенділері бор, ұлутас және мергель. Майда кристалды әктастардың белгенділігі ірі кристалдылардан жоғары. Әктас құрамында қоспа ретінде саз-балшық болса, біл шикізаттың күйдірілу белсенділігі артады.
Егер шикізат құрамына карбонаттың орнына Ca(OH)2 енгізетін болса, оның белсенділігі өте жоғары болады. Себебі, Ca(OH)2 –ден алынатын СаО, кальциттен (СаСО3) алынатын СаО-ға қарағанда реакцияға бейім келеді. Қоспаға карбонаттың орнына сөндірілмеген әк қосылатын болса, оның белсенділігі кемиді, себебі жоғары температурада күйдірілген әк қайтадан кристалданып, реакцияға бейімділігі нашарлайды.
|
|
Құрамында шлак бар қоспалар. Түйіршіктелген шлактардың шынылы фазасында құрылымдық өзгерістер 400...600 оС және одан жоғары температурада байқалады. Бұл ликвационды микрозонаға алып келетін күрделі аниондардың деполимеризациялық процесі. 700...800 оС температура аралығында шлакты шыныларда кристалды өнімдер пайда болады, бастапқыда олар аз болады, бірақ температураның жоғарылауымен уақыт өте келе көбейеді. Шлакты шынының кристаллизациялану процесі 1000...1100 оС аралығында күрделі жүреді. Пайда болатын минералдардың түрі шынының құрамына байланысты. Негізді шлактарда β-C2S, C3S2, C2АS (геленит), CS пайда болады, ал қышқыл шлактарда CS, C2S, C3S2, CА2S (окерманит), C2АS, SiО2 (тридимит) түзіледі.
800 оС температурада шлакқа СаО қосқанда байланысу процесінің басталуы байқалады (1...3%). Бұл температурада сульфитті күкірттің (CаS, Fes, MnS) сульфатты күкіртке (СаSО4) тотықтану процесі басталады. 1000 оС температурада 7...8 % СаО байланысады, және бұл процесс ары қарай интенсивті жүреді. Құрамында магний бар байланыстар Mg2+ жәймен Са2+ ығыстырады, бұл байланыс шыныда жоғары температураға дейін болады. СаО-ның C2SA, CAS2, CMS2, CMS қосылыстарының байланысы сазды минералдарға қарағанда жәй өтеді. 1000...1200 оС температура аралығында C2S, C5А3, C3А, C4AF, FeO, Mn2O3, MgO түзіледі, және де 4СаО∙Al2O3(Fe,Mn)2О3 байланысының түзілуі мүмкін.
|
|
Портландцементте шикізат қоспасы ретінде сазды компонент орнына доменді шлакты қолдану 1200 оС температурада және көптеген шихта компонентінде минерал түзілу ерекшелігі көрсетілген. 800...1000 оС температурада құрамында шлак кездесетін қоспаларында, доменді шлактарда қиын еритін геленит, окерманит, монтичеллит, шпинель СаО мен байланысуының жәй жүруіне алып келеді. Эвтектикалық балқыма пайда болғанда СаО байланысу реакциясы осы қоспаларда тезірек жүреді, және 1300...1500 оС температурада құрамында шлак кездесетін шихтада бос кальций тотығы саны сазды әкті қоспадағыдай болады. Шлакты шихтадағы әктің толық байланысуы сазды-әктастық шихтаға қарағанда 30...50 0С жоғары температурада аяқталады. Негізгі доменді шлактар құрамында CS, C2S, C3S2 және кейбір кезде C3S болғандықтан қышқыл шлактарға қарағанда реакцияға түсу қабілеті жоғары. Бірақта доменді шлактармен саз-балшықтың бөлігін ауыстырса оның теріс әсер етуі практикада байқалмайды, ал шихта құрамындағы шлак 3...5 % мөлшерінде болса минерал түзілу реакциясы тез жүруі мүмкін. Құрамында фосфор, фтор, барий, марганец бар шлактарды шихтаға қосу кезінде катализатор ретінде минерал түзілу процесін тездетеді.
|
|
Айналмалы пешті ірі кристалды (1...7 мм) түйіршіктелген шлактармен қоректендірсе пештің өнімділігі жоғарлайтындығы тәжірибе жүзінде дәлелденген.
Әктасты-шлакты қоспалардың реакционды қабілеті құрамына кварцты құм қосқанда жоғарылайды. Кремнезем кварц түрінде СаО мен шлак құрамындағы кремнеземге қарағанда белсені әсер етеді. CaF2, CaSO4, CaCl2 қатысымында минерал түзілу реакциясы жылдам жүреді.
Белит лайы (шламы) негізінен екі кальцийлі силикаттан тұрады. C2S күйдіру процесі жай жүргенде қайтадан кристалдануға ұшырап, белсенділігі төмендейді.
Жалпы алюмосиликаттар мен карбонаттарды бір-бірінен бөліп қарауға болмайды. Себебі, алюмосиликаттардың ыдырау кезеңі карбонаттардың диссоциациялану кезеңіне сәйкес келсе, шикізат қоспасының реакцияға белсенділігі өте жоғары болады.
Шикізат компоненттерінің майдалығының әсері. Клинкердің түзілуіне шикізат компоненттерінің майдалылығы, ұнтақтығы өте үлкен әсер етеді. Жоғары дисперсиялы шикізат қоспасында әктің байланысуы дисперсиялығы төмен қоспаларға қарағанда жақсы жүреді. Себебі, дисперсиялылығы төмен қоспаларда байланыспаған СаО қалады. Шикізаттың ұнтақтығы клинкердің құрылымына да әсер етеді. Ірі бөлшекті шикізаттың клинкерінде минералдар әр жерге жиналып түзіледі, яғни минералдардың саны әр түрлі болады. Шикізат компоненттерінің қажетті майдалылығын олардың табиғатына, реакцияға белсенділігіне қарап анықтайды.
Сазды компонеттер көбінесе өлшемі 5 мкм кіші бөлшектерден тұрады. Сондықтан әктас - саз қоспасында басты назарды әктас компонентінің майдалығына аударады. Кальциттің түйіршіктері 100 мкм-ден аспауы керек, ал жоғары маркалы цементтер үшін кальцит түйіршіктерінің үлкендігі 50...60 мкм ғана болуы керек. Кварцты тау жыныстарды одан да ұнтақ майдалаған жөн.
Беріктігі жоғары цементтер үшін оның түйіршіктері 15 мкм, жалпы 30 мкм болады. Зауыттарда шикізат қоспасының ұнтақтығын електен өткізу арқылы анықтайды. Көбінесе шикізатты №008-електен өткізгенде қалатын қалдық 5...15 % аспайтындай етіп майдалайды. Өнімділігі жоғары пештерде күйдірілетін материал ұзақ уақыт болатындықтан шикізатты өте майдаламауы мүмкін. Шикізаттың ұнтақтығы жоғары болған кезде қатты фазалы реакцияның жылдамдығы артады, бірақ C2S –пен байланыспаған СаО жоғары температурада қайтадан кристалданып, олардың балқымадағы еру жылдамдығы баяулайды. Сондықтан кейбір зауыттарда шикізатты №008-електе 20 % қалдық қалғанша майдалайды.
Шикізат қоспада SiО2-нің ірі бөлшектері (>90мкм) 0,5...1 % аспауы керек. Шикізатта SiО2-нің бөлшектері ірі болса клинкерде C2S-ке байытылған алаптар (зона) пайда болады. Белиттің кристалдары SiО2-нің ірі бөлшектерінің айналасына орналасады. Сол себептен байланыспаған СаО-ның мөлшері жоғарылайды.
Әктастың ірі бөлшектері (>90мкм) клинкер күйдіру процесіне мұншалықты әсер етпейді. Ірі бөлшектердің мөлшері 5 % дейін болуы мүмкін. Себебі декарбонизация кезінде кальциттің кристалдары жарылып, кеуектігі жоғарылап, пайда болған СаО кристалдарының өлшемі майда болады.
Майда ұнтақталған шикізат қоспаларының клинкер кұйдірген кездегі белсенділігі келесі себептерге байланысты:
1) Майда бөлшектердің беттік энергиясы жоғарылайды, себебі химиялық байланыстары үзілген және иондардың бір-бірімен байланысы азайған;
2) Кристалдардың дефектілер саны жоғарылайды;
3) Кристалдардың бір-бірімен түйісу беті жоғарылайды;
4) Майда бөлшектер балқымада тез ериді;
5) Майда ұнтақталған шикізат қоспасының химиялық құрамы жоғары дәрежеде біртектіленеді.
Шикізат қоспасының үлестік беті 300-400 м2/кг болғаны жөн. Майда ұнтақталған, гранулометриялық құрамы оңтайлы, жақсы біртектелінген шикізат қоспалардың күйдіру процесі 30...50 оС төмен температурада аяқталады.
Күйдіру режимінің әсері. Клинкер күйдіргендеСаО-ның байланысу жылдамдығына ең зор әсер ететін ол температура. Аррениустың теңдеуі бойынша химиялық реакцияның жылдамдығының константасы температураға экспоненциалды байланысты. СаО-ның байланысу жылдамдығы (ν) диффузиялық процестердің кинетикасына байланысты. Сол үшін оның температураға байланыстылығы сипаты экспоненциалды болуы мүмкін:
ν = ν0е-Е/RT (4.21)
Реакцияның жылдамдығы температура жоғарылаған сайын және оның активация энергиясы төмендеген сайын өседі. Минералдар пайда болу реакциясының жылдамдау себебі ол температура жоғарылаған сайын иондардың диффузиясы қатты және сүйық фазада жеделдетіледі, балқыманың тұтқырлығы төмендейді, оның мөлшері көбейеді.
Күйдіру режимінің клинкердің түзілуіне тигізетін әсері зор. Шикізатты тез күйдіргенде карбонаттардың диссоциациялану реакциясы, саз компоненттерінің ыдырау кезеңі, силикаттардың түзілу реакциясы бірге, бір уақытта жүреді. Бұлармен бірге қатты фазалы реакция да жүруі мүмкін, себебі компоненттердің кристалл торлары бұзылып, реакцияға бейімділігі артады. Тез күйдіргенде сұйық фаза да материалдың әр жеріне әр түрлі түзіледі.
Материалды жайымен күйдірсе әк рекристалданып, яғни қайтадан кристалданып, қатты фазада клинкер түзілу реакциясы баяулауы мүмкін. Жайымен күйдірген кезде жентектелу кезеңі СаО мен С2S-тің сұйық фазада еру жылдамдығымен лимиттенеді. Қайтадан кристалданған әк пен С2S-тің өсіп кеткен кристалдары жай ериді. Сондықтан шикізат қоспасын күйдіргенде жентектеліп бірігу алабында клинкер түзілу реакциясын тездету үшін материалды кальцийлеу алабында азырақ ұстайды.
НИИЦементінің (цемент саласындағы ғылыми-зерттеу институты) зерттеулері бойынша, негізгі клинкерлік минералдардың кристалдануы мен қасиеттеріне жентектелу алабының ұзындығы мен оның пештің соңына жақындығы үлкен әсер етеді. Ұзын айналмалы күйдіргіш пештерде клинкердің жентектелу алабы да ұзын. Ал материал ұзын пеште де, қысқа пеште де бір жылдамдықпен қозғалғандықтан, ұзын пештің жентектелу алабында ұзағырақ болады. Сондықтан ұзын пештерде жентектелу алабының пештің соңына жақын болғаны дұрыс. Бұл сапасы жоғары клинкер алуға мүмкіндік береді. Ұзын пештермен салыстырғанда қысқа пештерде беріктігі жоғары, әрі тез қатаятын цемент алу оңай.
Жай күйдірілген клинкермен салыстырғанда тез күйдірілген клинкерден гидравликалық белсенділігі өте жоғары цемент алынады. Себебі, рентгенграфикалық зерттеулер көрсеткеніндей, тез күйдірілген клинкерде алиттің кристалдары ақауларға толы болады, соның әсерінен алиттің гидравликалық қасиеті жоғары.
Күйдіру процесіне температура да үлкен әсер етеді. Жоғары температурада сұйық фазаның тұтқырлығы азайып, мөлшері көбейіп алит түзіледі. Мәселен, 1600 0С-та клинкер минералдары 5...10 минуттың ішінде, 1700...1800 0С-та бірнеше секунд ішінде, 1900...2000 0С аралығында секундқа да жетпейтін уақытта түзіледі, оның үстіне кристалдар да тез өседі. Мысалы, 1900...2000 0С аралығында бірнеше секунд ішінде алиттің кристалдары 2...3 мм жетсе, ал кәдімгі күйдіру температурасында олардың үлкендігі 20...40 мкм аспайды. 1800...2000 0С аралығында С3S пен С3А минералды тұрақсыз, сондықтан балқыған клинкерді жай клинкерге қарағанда жайырақ суыту керек, сонда С3S пен С3А қайтадан түзілуге мүмкіндік алады.
Клинкердің түзілуіне отын да әсерін тигізеді. Клинкер фазалары қатты отынды пайдаланған кезде айқын емес, бұлыңғыр болып түзіледі. Минералдардың кристалдары да үлкен, мысалы, алиттің кристалдарының үлкендігі 65 мкм, белиттің кристалдарының үлкендігі 55 мкм тең. Егер дәл осы шикізатты күйдіруге сұйық емес газ тәріздес отынды пайдаланса, клинкердің минералдары айқын, әрі майда (30...45 мкм) болып кристалданады. Осыған байланысты цементтің беріктігі 6...8 МПа артады.
Күйдіру температурасы 1450 оС-ден 1750 оС жоғарылағанда клинкердің құрамында 5...10 % артық алит пайда болады (есепке салыстырғанда). Алиттің мөлшерінің жоғарылауы С3S-тің торына қосымша Mg2+, Al3+, Fe3+, Na+ еніп қатты ерітінділер пайда болу және С3А-мен С4АF термиялық ыдырап, олардан СаО бөлініп, ол С2S-пен әрекеттесіп қосымша С3S пайда болады.
Айналмалы пеште клинкердің сүйық фазалық жентектелуі 15...30 минут жүреді. Бұл айналмалы пештің жентектелу алабында материалдың жүретін уақыты. Бұл уақытта 1300...1450 оС аралығында материалда С3S-тің негізгі мөлшері пайда болады. Бүл алапта материал аз уақыт болса, онда бос СаО көп мөлшерде қалып кетеді. Сонымен пеште 1300...1450 оС өлшемі 10...50 мм гранулдарда С3S толық пайда болу үшін 20...30 минут керек. Практика жүзінде клинкердегі СаО толық байланысып үлгере алмайды, 1...2 % бос СаО қалып кетеді.
1350...1450 оС температурада клинкер 4 сағат бойы күйдірілсе құрамындағы алит мөлшері 3...7 % өседі, алюмоферрит фазасы 1...3 % жоғарылайды, ал С3А 4...5 % төмендейді. Белиттің де жалпы мөлшері кемиді. С3А азаюы ыдырауына байланысты, ал С6АхFу жоғарылауы – Fе3+ С3А торына еніп онда А13+ алмастыруымен байланысты.
Сөйтіп клинкердің күйдірілгіштігіне әсер ететін маңызды факторларға шикізат қоспасының химиялық және минералдық құрамы, оның түйіршіктік құрамы, қоспаның біркелкілігі, күйдіру жылдамдығы жатады.
Дата добавления: 2019-02-22; просмотров: 218; Мы поможем в написании вашей работы! |
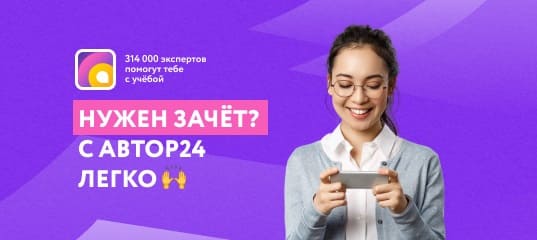
Мы поможем в написании ваших работ!