Наростообразование и его влияние на процесс резания
Ювенильность контактирующих поверхностей, высокие контактные давления и некоторые другие особенности трения при резании обусловливают высокую интенсивность адгезионных явлений, сопровождающих процесс стружкообразования. Одним из результатов этих явлений может быть задержка на передней поверхности частиц (или целых слоев) стружки. В результате образуется нарост.
Наростом называется связанное с инструментом тело (рис. 2.10), ко-торое при определенных условиях формируется на передней поверхности из материала срезаемого слоя. Дополняя режущий клин, нарост изменяет его геометрическую форму, контактные условия и тем самым влияет на процесс образования стружки, которая в этом случае частично или полностью скользит по поверхности нароста [42]. Периодически нарост частично или полностью срывается и уносится вместе со стружкой или, попадая под резец, переносится на обработанную поверхность.
При черновой обработке нарост играет положительную роль, так как увеличивает передний угол, что приводит к снижению сил резания. Кроме того, нарост защищает контактирующие поверхности инструмента от преждевременного износа.
При чистовой обработке частицы нароста, попавшие на обработанную поверхность заготовки, значительно уменьшают шероховатость обработанной поверхности.
Наростообразование зависит от пары режущий-обрабатываемый материал, режимов резания, смазочно-охлаждающей жидкости и т.д. Нарост образуется в определенном температурном диапазоне
|
|
(Θн = 60…600°С), проходя максимум при Θн = 250…300°С. Для выполнения качественной чистовой обработки температура в зоне резания должна быть либо меньше 60°С (скорость резания меньше 12 м/мин), либо больше 600°С (скорость резания больше 50 м/мин).
Для определения зоны резания без нароста за рубежом строят карты обрабатываемости для каждой пары режущий – обрабатываемый материал, по которым назначают режимы резания (рис. 2.11).
В последние годы в механообработке увеличивается доля инструмента (быстрорежущего и твердосплавного) с нанесенными покрытиями. Это позволяет в значительно увеличивать скорость резания и тем самым гарантированно работать за зоной наростообразования.
Износ и стойкость инструмента
Трение между стружкой и передней поверхностью инструмента и между поверхностью резания и главной задней поверхностью приводит к изнашиванию режущего инструмента. Высокие контактные давления и температура резания вызывают следующие виды изнашивания (рис. 2.12): адгезионный; усталостный; абразивный; термоусталостное разрушение; окисление; диффузионные процессы; высокотемпературная ползучесть.
|
|
В зависимости от режимов работы инструмента превалирует тот или иной вид износа.
Для эксплуатации режущего инструмента важно знать, как быстро режущая часть изменяет свою форму в результате воздействия на инструмент в процессе резания механических и тепловых нагрузок. Изменение формы режущей части инструмента происходит непрерывно. По истечении некоторого промежутка времени эти изменения становятся столь существенными, что инструмент либо вовсе теряет способность снимать срезаемый слой, либо не обеспечивает выполнение заданных технологических требований к обрабатываемой детали. Различают три вида износа:
· износ по передней поверхности;
· износ по задней поверхности;
· одновременный износ по обеим поверхностям (рис. 2.13).
Износ по передней поверхности характерен для быстрорежущих сталей. Износ по задней поверхности характерен для твердых сплавов. Одновременный износ по обеим поверхностям характерен для твердых сплавов при повышенных температурах.
При резании возможно хрупкое разрушение режущей части или пластическая деформация.
Хрупкое разрушение (рис. 2.14, а) – результат возникновения и развития трещин за счет развития микротрещин, которые нередко возникают в процессе получения лезвия инструмента, а также в процессе температурных, химических и других воздействий. Наиболее типично хрупкое разрушение для минералокерамических и твердосплавных (группа ТК) с малым содержанием кобальта материалов. Излом происходит при обработке с ударом, например, при точении вала со шпоночным пазом.
|
|
Для уменьшения трещин после заточки необходимо производить доводку инструмента абразивной пастой. Перед пайкой пластин необходим предварительный медленный разогрев тела резца и пластины, а затем медленное их охлаждение.
Пластическая деформация (рис. 2.14, б) возникает при недостаточной твердости инструментального материала. Устойчивость режущей части инструмента против пластического деформирования гарантируется при соблюдении условия:
Hи / Hф > 1,4,
где Ни – твердость инструмента, Нф – твердость стружки.
При повышении температуры резания твердость инструментального материала падает, а стружки остается практически неизменной. Течение режущей кромки характерно для твердых сплавов, работающих при температуре выше 1000°С.
Допустимое значение износа называют критерием износа. В большинстве случаев за критерий износа принимают износ инструмента h по главной задней поверхности. Для токарных резцов из быстрорежущей стали h=1,5…2 мм, для резцов, оснащенных пластинками твердого сплава h=0,8…1 мм. Допустимый износ соответствует определенному периоду стойкости инструмента.
|
|
Износ инструмента вызывает рост силы резания, что увеличивает деформацию заготовки и инструмента и еще более снижает точность обработки. Растут глубина наклепанного слоя на заготовке и силы трения между заготовкой и инструментом, а это приводит к увеличению тепловыделения при резании.
Для уменьшения влияния износа инструмента на точность и качество обработки применяют автоматические размерные подналадчики металлорежущих станков, либо делают принудительную замену инструмента через определенный промежуток времени.
Способность режущего инструмента сохранять работоспособными свои контактные поверхности и лезвия называют стойкостью инструмента, а время T, в течение которого это происходит, – периодом стойкости. Период стойкости равен времени работы инструмента между двумя заточками.
Период стойкости любого инструмента зависит от рода, механических и теплофизических свойств обрабатываемого и инструментального материалов, геометрических параметров инструмента, факторов режима резания и применяемой СОЖ. Так как стойкостные зависимости трудно прогнозировать, их устанавливают в настоящее время в основном экспериментально. На стойкость инструмента T наибольшее влияние оказывает скорость резания:
где С1 – некоторая постоянная; m1 – показатель степени, равный тангенсу угла наклона прямой к оси абсцисс, проведенной через опытные точки, нанесенные в двойной логарифмической сетке координат.
Стойкость инструмента выбирается по справочнику исходя из рассчитанной скорости резания. Если необходима определенная стойкость, то ее выбирают по справочнику, но скорость резания уже будет отличаться от рассчитанной. Значения стойкости обычно находятся в пределах 30, 40, 60, 90, 120, 180 мин. Меньшие значения для резцов, большие – для дорогостоящего инструмента: фрез, протяжек и др. За рубежом резание производят на более высоких скоростях, поэтому стойкость инструмента снижается. Так для точения часто выбирают стойкость равную всего 20 мин. Хотя при этом происходит интенсивный износ инструмента, но производительность выше и инструмент окупается.
В связи с тем, что стойкость инструмента даже в одной партии заметно отличается, то при обработке в автоматизированном производстве и на станках с ЧПУ производят принудительную замену инструмента через определенный промежуток времени (меньший, чем оптимальная стойкость инструмента).
Дата добавления: 2019-02-12; просмотров: 1563; Мы поможем в написании вашей работы! |
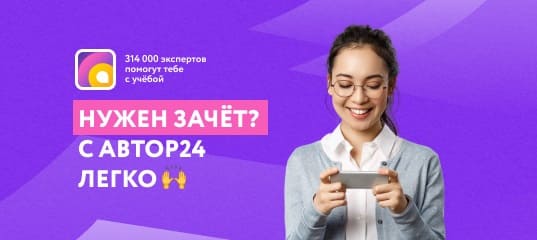
Мы поможем в написании ваших работ!